
книги / Современные и перспективные термолитические процессы глубокой переработки нефтяного сырья
..pdfТаблица 2.22 — Характеристика нефтей, остатков и коксов |
|
|
|
|
|
|
|
|
|
|
|
|||||
|
|
Сырье |
|
|
Остаток > 500 °С |
|
|
|
|
|
Кокс |
|
||||
Нефть |
Плот- |
Содержание, % |
Выход |
Плот |
Коксуе- |
Содержание, % |
Выход |
|
Содержание, % |
|||||||
|
ность, |
S |
V |
Ni |
на |
ность, |
мость, |
S |
V |
Ni |
на |
|
S |
|
V |
Ni |
|
г/см3 |
нефть |
г/см3 |
% |
гудрон |
|
|
|||||||||
Западносибирская |
0,8395 |
0,45 |
|
|
16,2 |
0,9968 |
16,5 |
1,29 |
_ |
_ |
25,4 |
1,29 |
|
— |
||
малосернистая |
|
|
0 , 0 1 |
|||||||||||||
Смесь Сургут + |
0,8742 |
1,62 |
0,0055 0,00067 |
33,5 |
1,0014 |
16,6 |
3,00 |
0,0155 |
0,0023 |
26,6 |
3,42 |
0,06 |
0,0080 |
|||
южнобалыкская |
||||||||||||||||
Правдинская |
0,8523 |
0,72 |
0 , 0 0 1 1 0,00014 |
24,4 |
0,9731 |
13,8 |
1 , 8 6 |
0,0056 |
0 , 0 0 1 0 |
2 2 , 0 |
3,10 |
0,024 |
0,0036 |
|||
Смесь нижневартовских |
0,8410 |
1 , 0 2 |
0,0013 |
0,0008 |
16,3 |
0,9987 |
15,9 |
2,40 |
0,0090 |
0,0060 |
23,0 |
2 |
, 1 |
0 |
0,035 |
0,0180 |
Самотлорская |
0,8420 |
0,98 |
0,0017 |
0,0008 |
2 0 , 0 |
0,9993 |
13,5 |
2,25 |
0,0080 |
0,0045 |
2 1 , 8 |
2 |
, 1 |
0 |
0,035 |
0 , 0 2 1 0 |
Советско-соснинская |
0,8386 |
0,97 |
0,0008 |
0,0005 |
17,0 |
0,9990 |
15,0 |
1,95 |
0,0045 |
0,0030 |
23,0 |
1,80 |
0,019 |
0,0180 |
||
Смесь мегионской |
0,8378 |
1,09 |
0,0015 |
0,0009 |
18,7 |
0,9939 |
13,9 |
2,26 |
|
0,0050 |
|
2,16 |
0,042 |
0,0214 |
||
и ватинской |
0 , 0 1 0 0 |
2 2 , 6 |
||||||||||||||
Шаимская |
0,8270 |
0,45 |
— |
— |
18,0 |
0,9702 |
П , 2 |
1,26 |
0,0013 |
0 , 0 0 1 2 |
19,0 |
1,63 |
0,007 |
0,0060 |
||
Западносибирская |
0,8556 |
1,48 |
|
|
|
0,9811 |
_ |
2,23 |
0,0083 |
0,0035 |
|
2,40 |
0,040 |
0,0150 |
||
сернистая |
|
|
|
2 0 , 0 |
||||||||||||
Варьеганская |
0,8269 |
0,45 |
0,00053 0 , 0 0 1 0 |
13,7 |
,9924 |
13,6 |
1,30 |
0,0047 |
0,0051 |
22,7 |
1,42 |
0 , 0 2 0 |
0 , 0 2 1 0 |
|||
Ноябрьская |
0,8410 |
0,56 |
0 , 0 0 1 2 |
0 , 0 0 1 0 |
17,9 |
1,0074 |
17,8 |
1,52 |
0,0070 |
0,0052 |
26,0 |
1,67 |
0,025 |
0 , 0 2 0 0 |
||
Кулешовская |
0,8324 |
1 , 0 2 |
— |
— |
18,8 |
0,9947 |
17,5 |
2,31 |
— |
— |
26,0 |
3,03 |
0,030 |
— |
||
Мартышинская |
0,8881 |
0,36 |
— |
— |
26,0 |
0,9668 |
16,7 |
0,77 |
— |
— |
2 1 , 8 |
1,79 |
— |
— |
||
Восточно-украинская |
0,8045 |
0,7 |
— |
— |
— |
0,9894 |
15,5 |
1,40 |
— |
— |
24,3 |
1,64 |
— |
— |
||
Смеси сургутских |
— |
— |
— |
— |
— |
1,0014 |
16,6 |
3,00 |
0,0155 |
0,0023 |
— |
3,42 |
0,056 |
0,0080 |
||
Нижневартовская |
— |
— |
— |
— |
— |
0,9987 |
15,9 |
2,40 |
0,0090 |
0,0060 |
— |
2 |
, 1 |
0 |
0,035 |
0,0025 |
Мегионская |
— |
— |
— |
— |
— |
0,9939 |
13,8 |
2,26 |
0 , 0 1 0 0 |
0,0066 |
— |
2,16 |
0,041 |
0,0028 |
О 7
СО
2
О
в 5
2
1
О |
1 |
2 |
3 |
4 |
5 |
6 |
7 |
8 |
Содержание серы в сырье, % мае.
Рисунок 2.31 — Зависимость содержания серы в коксе от ее содержания в сырье коксования
Содержание V в коксе,ppm
■• о — нефти различного происхождения
■— остатки арланской нефти
Рисунок 2.32 — Взаимосвязь между содержанием серы и ванадия в сырых коксах
Общая тенденция — чем больше серы в сырье, тем больше ее в коксе. В частных случаях можно наблюдать ситуацию, когда содержание серы в коксе существенно выше содержания серы в сырье, и наоборот. Количественной оценки, которая бы надежно позволила оценить величину соотношения SctapM/ SKOKcaпока не существует, и можно надежно оценить это только экспериментально. По 3. И. Сюняеву это объяс няется различным соотношением реакции распада и уплотнения. Остатки с высоким
112
отношением С/Н склонны к реакциям термоконденсации, в результате которых обра зуется больше атомного водорода, что и приводит к эффекту «обессеривания» кокса.
Повышенное содержание серы в сырье всегда обусловливает повышенное со держание ванадия. Взаимосвязь между содержанием серы и ванадия в сырых коксах показана на рис. 2.32.
2.11.Производство специальных сортов кокса типа КНПС и игольчатого
Пожалуй, нет в системе Д. И. Менделеева элемента более удивительного, чем угле род. Алмаз — углерод, прочность которого такова, что он режет металл. Графит тоже углерод, но он пишет на бумаге. Алмаз — диэлектрик, графит — проводник электри чества на уровне металлов и т. д. Такое многообразие форм существования углерода и разнообразие его свойств объясняет огромный спектр применения углерода в различ ных областях науки и техники. Нефтяной кокс, который более чем на 90 % состоит из углерода, также значительно меняет свои свойства в зависимости от сырья и технологии его производства. Кокс может обладать высокой или низкой теплопроводностью, высо кой или низкой реакционной способностью к активным газам, анизотропией свойств по теплопроводности, электропроводимости вдоль и поперек оси приложения усилия. Эти свойства широко используются при производстве графитированной продукции. Так, для сокращения расхода электроэнергии при выплавке электростали для производства электродов используется кокс игольчатой структуры. При этом расход электродов на тонну стали снижается не на несколько процентов, а в разы. По другой технологии с использованием сырья определенного качества можно получить кокс изотропной структуры, у которого отсутствует изометрия по расширению, электропроводнос ти и теплопроводности, такой кокс используется в космической и ракетной технике.
Исследования по разработке технологии производства специальных сортов кокса начались во времена СССР. Большой вклад в разработку теоретических основ форми рования структуры игольчатого кокса внесли работы 3. И. Сюняева, Р. Н. Гимаева. Не менее важен вклад ученых, которые активно участвовали в разработке и внедрении на нефтеперерабатывающих и электродных заводах — В. В. Фрязинова, Б. М. Ежова, Р. X. Садыкова, С. М. Слуцкой, В. П. Запорина, Г. Ф. Давыдова, Б. Ш. Мордуховича. Не заменим труд работников заводов, на которых были организованы многочисленные пробеги с получением опытных партий, изготовление графитированных электродов и испытания в опытных плавках на электродуговых печах, А. Ф. Махова, Д. Н. Махтумова, В. И. Губанова, Г. Г. Теляшева. Нельзя не отметить большой вклад в разработку технологии работников бывшего Миннефтехимпрома СССР, которые способствова ли в организации и финансированию разработок — А. В. Рябова, А. Е. Злотникова, А. П. Смирнова, В. А. Ефимова. Окончательное апробирование технологии произошло в году, когда на ОАО «НУНПЗ» по отечественной технологии была наработана опытная партия в количестве 18 тыс. т, которая прошла полномасштабные испытания по всем переделам — получение кокса, изготовление электродов различных сечений и испы тание электродов в электродуговых печах с различной токовой нагрузкой. Результаты испытаний сопоставлены с результатами, полученными на импортных коксах лучших марок. Получены вполне сопоставимые, мало чем отличающиеся показатели по все му спектру и свойств графитированных электродов, и по расходам электроэнергии на
113
тонну стали, и расходу электродов. Результаты проведенной работы показали, что мы располагаем отечественной технологией производства кокса игольчатой структуры, надежно отработанной в промышленном масштабе.
Итогом явилась разработка технологического регламента и рабочего проекта многотоннажного производства кокса игольчатой структуры (рис. 2.33).
|
Продукты крекинга |
|
Продукты коксования |
М алосернистые |
|
|
|
дистилляты ТГК, |
|
|
КИС 120000 т/год |
ТГКК 43-102,1А -1М |
|
Крекинг-остаток |
(30 % на крекинг-остаток, |
1 200000 т/год |
Термический крекинг |
400 000 т/год, |
1 0 % на исходные |
100% |
3 0 % |
Замедленное дистилляты) |
|
(блок подготовки сырья |
|
коксование |
|
для производства КИС) |
|
||
|
|
||
Рисунок 2.33 — |
Отечественная технология производства КИС с содержанием серы 0,5-0,6 % |
||
|
на Красноводском НПЗ |
|
Этапы разработки технологии получения игольчатого кокса:
I. 1968-1969 — первые лабораторные эксперименты на кафедре ТНГ, УНИ. (Сюняев 3. И., Гимаев Р. Н., Давыдов Г. Ф.).
II. 1969 — первая партия КИС, полученная на промышленной установке ЗК на Крас новодском НПЗ (Махтумов Д. Н., Давыдов Г. Ф., Валявин Г. Г.) Подтвержден ма териальный баланс, содержание серы 0 ,5-0, 6 %, по структуре «человекообразная обезьяна».
III. 1969-1977 — проведен широкий спектр углубленных исследований по созданию теоретических основ и технологий производства КИС из различных видов не фтяного сырья:
—на Красноводском НПЗ организовано получение опытных партий КИС в объеме 2000-2500 т/год;
—на электродных заводах получены опытные партии графитированных элект родов и проведены испытания на электрометаллургических печах (3. И. Сюняев, В. Н. Гимаев, С. М. Слуцкая, В. П. Запорин, Б. Ш. Мордухович; МН-
ХП, Союзуглерод, КНПЗ, электродные заводы). IV. Опытная партия 20 т.
V.1977 — разработана отечественная технология — МНХП утвержден технологи ческий регламент на блок подготовки сырья для производства КИС (В. В. Фрязинов, Г. Г. Валявин, Н. И. Ветошкин, С. М. Слуцкая, В. П. Запорин).
VI. 1978 — Башгипронефтехим разработал проект блока подготовки сырья.
Хотя технологию производства фирмы скрывают, в настоящее время установле но, что конечная структура кокса зависит от скорости образования «мезофазы» — жидкокристаллического состояния вещества между жидкой и твердой формой сы рья и кокса. Если структура мезофазы выглядит так, как показано на рис. 2.34, то в результате получается кокс игольчатый анизотропной структуры (рис. 2.35). Если структура мезофазы имеет форму как на рис. 2.36, то при коксовании такого сырья образуется кокс изотропной структуры (рис. 2.37).
114
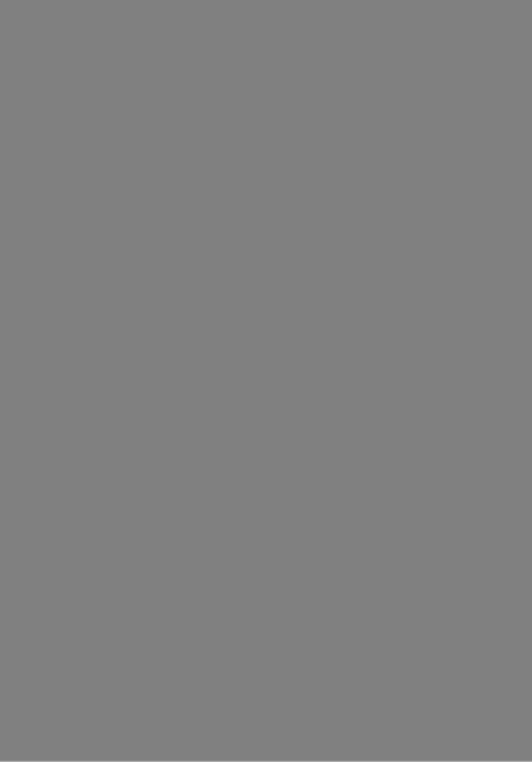
ГЛАВА 3. СОВЕРШЕНСТВОВАНИЕ КОНСТРУКЦИИ ОСНОВНЫХ АППАРАТОВ И ТЕХНОЛОГИИ УСТАНОВОК ЗАМЕДЛЕННОГО КОКСОВАНИЯ
3.1.Принципиальная технологическая схема установок замедленного коксования
Процесс замедленного коксования является непрерывным по подаче сырья, вы ходу газообразных и дистиллятных продуктов, но периодическим по выгрузке кокса из реакторов. Сущность процесса заключается в том, что предварительно нагретое до высокой температуры (495-520 °С) сырье закачивается в необогреваемые изоли рованные снаружи реакторы, где проводится коксование за счет аккумулированного сырьем тепла.
Коксовые реакторы (или камеры) представляют собой вертикальные полые ци линдры с люками вверху и внизу. Несколько реакторов объединены в один блок. Сырье нагревается в трубчатых нагревателях. Непрерывно выделяющиеся из реак тора горячие пары и газы подвергаются ректификации в колонне, а затем поступают в конденсаторы-холодильники.
На рис. 3.1 в самом общем виде показана схема установки замедленного коксо вания (УЗК).
газ+бензин
Рисунок 3.1 — Принципиальная схема установки замедленного коксования:
Р-1,2 — коксовые камеры; П — печь для подогрева сырья; К-1 — ректификационная колонна
Свежее (первичное сырье), подогретое в теплообменниках и конвекционной секции печи, поступает во фракционную колонну, туда же поступают продук
116
ты реакции. Первичное сырье контактирует с парами из реакторов, что приводит к конденсации части паровой фазы, образовавшиеся жидкие продукты стекают вниз колонны и рециркулируют по схеме колонна — печь — реактор — колонна. Смесь рециркулята и первичного сырья образует вторичное сырье и поступает после нагрева в радиантной секции печи в одну из подготовленных к работе ка мер. Продукты реакции поступают во фракционную колонну и разделяются на газ, бензин, легкий и тяжелый газойли. Современные высокопроизводительные уста новки мощностью до 6 - 1 2 млн т/год в своем составе имеют до 8 камер диаметром до 1 0 м.
После заполнения реактора коксом горячий поток сырья переключают в следую щий подготовленный реактор. Заполненный коксом аппарат после отключения про паривают с целью отгона от кокса дистиллятных нефтяных фракций. Пары направ ляются в колонну, а через 0,5 ч их сбрасывают в скрубер, соединенный вытяжной трубой. Затем кокс охлаждают водой. Кокс после охлаждения выгружают при помо щи струи воды, вводимой специальными устройствами (резаками) в пробуренную центральную скважину под давлением 150-250 кг/см2, в зависимости от диаметра камеры.
После выгрузки кокса реактор подготавливают к новому циклу коксования: про гревают вначале водяным паром, а затем парами продуктов коксования из работаю щего реактора. При этом во избежание заноса твердых частиц в колонну на выходе из реактора устанавливают сетчатый фильтр. Прогретый до 300-400 °С реактор может быть включен в работу. Кокс с площадки транспортируется на склад. Первая опытно промышленная УЗК производительностью 300 тыс. т/год по сырью была построена в 1955 г. на Ново-Уфимском НПЗ. В дальнейшем аналогичные установки были пос троены на НПЗ гг. Волгограда и Ферганы. Все 3 установки по состоянию на 2008 г. успешно эксплуатируются под индексом УЗК типа 21-10/300.
Наиболее интенсивное строительство УЗК в бывшем СССР велось с конца 60-х до середины 80-х гг. прошлого столетия. Было построено несколько модификаций установок типа 21-10/600,21-10/6,21-10/ЗМ мощностью 600 тыс. т сырья в год. Схе мы установок различались незначительно, были оснащены 4 камерами диаметром
5.5м. Самые крупные УЗК в СССР были введены в строй — установка мощностью
1.5млн т/год 21-10/5К на НПЗ гг. Баку и Новокуйбышевска.
В2008 г. УЗК НУНПЗ была реконструирована. Добавлена четвертая камера, внедрена система продувки и улавливания продуктов прогрева и охлаждения кок совых камер, внедрена технология коксования с выносной секцией колонны К-1 (см. §3.11).
Так как все установки работают в режиме — одна камера заполняется, вторая готовится к заполнению, большое влияние на эффективность работы установок ока зывает скорость оборачиваемости коксовых камер. Чем быстрее заполняется камера коксом и чем быстрее она подготовлена к новому циклу, тем эффективнее работа установки. В табл. 3.1 проанализированы графики работы камер коксования на раз личных режимах работы УЗК в США и России.
Из табл. 3.1 следует, что на зарубежных УЗК оборудование используется гораздо более эффективно, так как на подготовительные операции затрачивается гораздо меньше времени. Особо следует обратить внимание на длительность подготовитель
117
ных операций коксовых камер. Она значительно больше на отечественных УЗК. Это связано с меньшей автоматизацией трудоемких операций, некоторыми различиями в нормах по разогреву и охлаждению коксовых камер, отсутствием закрытых систем пропарки и охлаждения.
Таблица 3.1 — График работы камер коксования для УЗК НПЗ США и России
Время на операцию, ч
Наименование операций |
|
США |
|
Россия |
|
|
|
||
Заполнение реакторов коксом |
24 |
18 |
1 2 |
30 |
Пропарка в ректификационную колонну |
1 |
0,5 |
0,5 |
7 |
Пропарка в систему улавливания |
1 |
0,5 |
0,5 |
вЕ-91 |
Охлаждение «малой» водой |
3 |
3 |
1,5 |
|
Охлаждение «большой» водой |
4 |
3 |
|
6 |
2 |
|
|||
Дренаж воды |
2 |
2 |
2 |
2 |
Открытие люков |
1 |
0,5 |
0,5 |
2 |
Выгрузка кокса |
3 |
3 |
2 |
4 |
Закрытие люков |
1 |
0,5 |
0,5 |
1 |
Опрессовка |
1 |
1 |
0,5 |
1 |
Прогрев парами |
5 |
4 |
2 |
6 |
Общий цикл |
48 |
36 |
24 |
60 |
Отсюда следует, что ускорение оборачиваемости камер — это одно из важнейших направлений по интенсификации установок замедленного коксования.
3.2. Интенсификация УЗК ускорением оборачиваемости коксовых камер
Рабочий цикл коксовых камер включает время заполнения камер коксом и время проведения подготовительных операций к постановке камеры на режим коксования. Время заполнения коксовых камер определяется производительностью установок по сырью, выходом кокса в пересчете на исходное сырье, которое, в свою очередь, опре деляется коксовым числом (коксуемостью) свежего сырья. В табл. 3.2 показаны ре зультаты работы действующих установок на НПЗ России. Видно, что на установках с наименьшим временем заполнения эффективность использования реакционного объема коксовых камер наибольшая.
Особо следует отметить опыт работы УЗК ОАО НУНПЗ, где установка работает по 12-часовому режиму заполнения камер. В этом режиме установка работает в те чение длительного времени (более 2 лет), и при этом качество кокса соответствует существующим нормативам. Наиболее распространенным циклом оборачиваемос ти камер составляет 24-^48 ч на подготовительные операции и 24 ч на заполнение коксом (табл. 3.2). При таком режиме все операции по заполнению, переключению,
118
выгрузке кокса осуществляются в одно и то же время суток, что повышает надеж ность, обусловливает ритмичность работы установки, позволяет значительно со кратить количество обслуживающего персонала, так как достаточно иметь в штате одну бригаду специалистов по выгрузке кокса и на операции по закрытию-открытию люков коксовых камер. В последние годы все большее и большее распространение получает 24-часовой цикл оборачиваемости камер. При этом 12 ч камера заполня ется коксом и 12 ч отводится на подготовительные операции. Следует учесть, что некоторые операции, такие как разогрев и охлаждение камер следует осуществлять по строго определенному временному графику. Это связано с тем, что камера при нагревании от температуры окружающей среды до 500 °С «удлиняется» по высо те на 150-200 мм и на такую же величину уменьшается при ее охлаждении. При чрезмерно быстром нагреве и охлаждении в теле металла камеры могут возник нуть значительные напряжения, что приводит к сокращению сроков службы. Для обеспечения длительной работы камеры, скорости нагрева и охлаждения не долж ны превышать 60-70 °С в час. Прогрев камеры парами из работающего реактора начинается после ее опрессовки водяным паром, и температура стенки достигает 100-120 °С. Для достижения температуры в камере 320-350 °С при переключении ее на режим коксования достаточно 3-3,5 ч.Таким образом, суммарный разогрев камеры составляет 3,5^4 ч и это время является своеобразной «константой», которая оптимизации не подлежит.
Таблица 3.2 — Время заполнения и коксосъем с 1 м3 объема коксовых камер
Завод |
Суммарный |
Время |
Произведено |
Коксосъем, |
|
объем камер |
заполне |
кокса, |
т/м3 |
||
|
коксования, м3 |
ния, ч |
тыс. т |
||
|
|
||||
ОАО «Ново-Уфимский» |
1280 |
1 2 |
151 |
118 |
|
ООО «ЛУКОЙЛ-Волгоград- |
3861 |
>24 |
260 |
67,5 |
|
нефтепреработка» |
|||||
|
|
|
|
||
ООО «ЛУКОЙЛ-ПНОС» |
2168 |
24 |
237 |
109,3 |
|
ОАО «Новокуйбышевский НПЗ» |
3464/1732 |
>24 |
136 |
78,5/39,3 |
|
ОАО «Ангарская НХК» |
2168 |
>24 |
148 |
68,3 |
|
ОАО «Сибнефть-Омский НПЗ» |
2168 |
>24 |
174 |
80,3 |
|
ИТОГО |
15109 |
— |
1094 |
72,4 |
Несколько иная ситуация с режимом охлаждения кокса водяным паром и водой. Процесс охлаждения состоит из 3 этапов. На первом этапе в течение 1 ч осущест вляется пропарка кокса водяным паром в колонну К-1 и узел улавливания. В этот период происходит удаление недококсованных продуктов из камеры и частичное охлаждение кокса. На втором этапе подают воду. При этом необходимо помнить, что если вода будет подаваться в избыточном количестве, то может произойти рез кое снижение температуры стенки камеры и как следствие появление «отдулин» на стенке камеры и даже появление трещин. Поэтому для исключения возникновения
119
чрезмерных термических напряжений в корпусе камеры осуществляют так называе мую «дробную подачу воды» по специальному графику (табл. 3.3).
Таблица 3.3 — Ориентировочный график подачи воды на охлаждение коксовой камеры
Длительность, мин |
Расход воды, м3/ч |
0-30 |
5-10 |
30-60 |
2 0 |
60-90 |
30 |
90-120 |
40 |
120-150 |
50 |
150-180 |
60 |
После заполнения всей массы кокса водой, в принципе, процесс охлаждения кокса заканчивается и начинается следующий этап доохлаждения коксовой каме ры до такого уровня, чтобы температура в районе верхнего люка не превышала 60 °С (нормы надзорных организаций), она устанавливается в целях исключения травматизма при открытии верхнего люка камеры. Процесс доохлаждения доста точно длинный и занимает 3—4 ч. После открытия верхнего люка производится дренаж воды до полного опорожнения камеры, чтобы обеспечить безопасность при открытии нижнего люка. Операции доохлаждения и дренажа воды можно оптими зировать и значительно сократить время их проведения. Также можно оптимизиро вать операции по пропарке кокса в камерах и время выгрузки кокса из реакторов. Проведение подготовительных операций в оптимальном режиме позволит перей ти на 24-часовой цикл оборачиваемости коксовых камер: 12-часовое заполнение
и12-часовая подготовка (табл. 3.2). Операции по нагреву и охлаждению камер можно автоматизировать.
На рис. 3.2 представлена схема автоматического управления процессами разо грева и охлаждения камер коксования, основанная на эффекте увеличения линейных размеров камеры в процессе разогрева и охлаждения [57]. Схема была смонтирована
иуспешно испытана на НПЗ в г. Гурьеве (ныне г. Атырау), но до постоянного внед рения дело не дошло, так как цикл коксования на установке был более 90 ч и особой нужды в такой системе обслуживающий персонал не находил. В настоящее время при коротких циклах оборачиваемости камер проблема становится весьма актуаль ной, процесс охлаждения и разогрева необходимо автоматизировать, тем более что появились новые, более современные разработки.
Процесс доохлаждения можно сократить путем подачи воды на верх коксовой камеры. После заполнения камеры водой до уровня высоты кокса, можно начать подачу воды на верх, направив небольшой объем потока воды в низ коксового ба рабана. Подача воды на верх дает возможность раньше начать дренаж воды, так как возникновение вакуума при снижении уровня воды исключается. Схема подачи воды на верх камеры показана на рис. 3.3.
120