
книги / Современные и перспективные термолитические процессы глубокой переработки нефтяного сырья
..pdf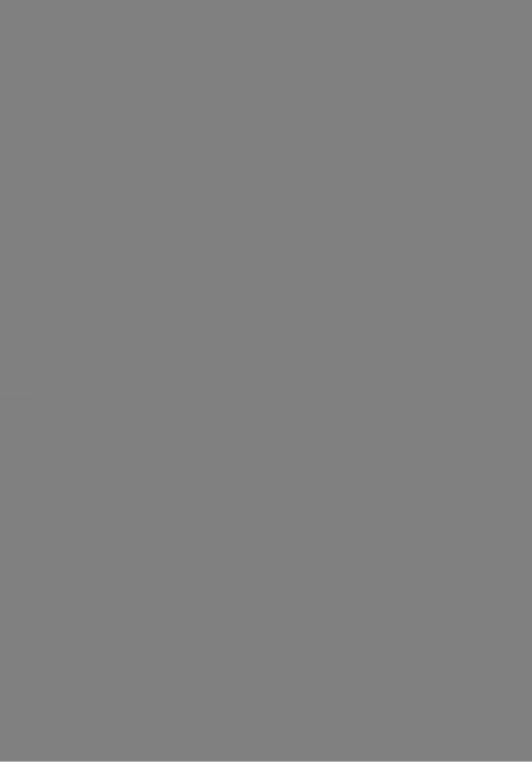
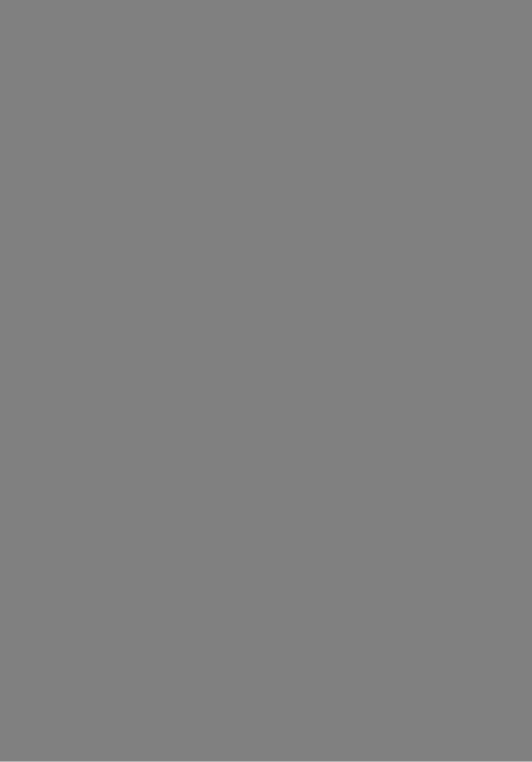
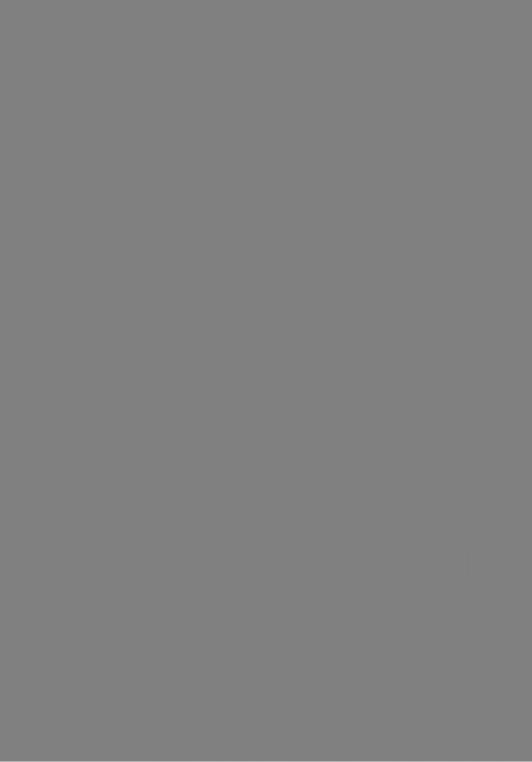
За рубежом шиберная система внедряется очень быстрыми темпами в течение последних 4-5 лет фирмой «Delta Valve», изготовлено и поставлено на НПЗ во многих регионах мира более 250 шиберов. Большой интерес к разработке обус ловлен целым рядом преимуществ перед существующими системами открытиязакрытия коксовых камер. Благодаря новой передовой технологии, устройство для открытия люков коксовых камер DeltaValve обеспечивает безопасные производс твенные условия эксплуатации УЗК. По дизайну DeltaValve представляет собой закрытую систему, которая устраняет риски внешнего воздействия, снижает расхо ды на содержание, увеличивает производительность и конкурентоспособность по цене. Кроме того, при использовании устройства для открытия люков DeltaValve отпадает необходимость в замене прокладок, крепежа и других регулировочных устройств. DeltaValve может быть скомпонована так, чтобы дренаж воды из камеры осуществлялся напрямую через задвижку. Эта особенность может значительно уве личить производительность путем уменьшения времени цикла и соответствующих эксплуатационных расходов.
3.3. Повышение эффективности использования реакционного объема коксовых камер применением антипенных присадок
Процесс коксования сопровождается вспениванием коксующейся массы в коксо вых камерах. Это обстоятельство приводит к снижению эффективности использова ния полезного объема камер, снижению производительности по сырью. Кроме того, чрезмерное неконтролируемое пенообразование может привести к перебросу коксую щейся массы в основную ректификационную колонну. Поскольку с пеной выносят ся не только жидкость, но и частицы кокса, попадание которых на прием печных насосов и далее в реакционные змеевики печи приводит к их быстрому закоксовыванию и преждевременной остановке всей установки, для контроля за уносом пены существует ряд методов с соответствующим приборным оснащением. Разработаны методы, позволяющие следить за уровнем пены от начала до конца цикла, методы, позволяющие следить раздельно за формированием массы кокса, жидкости и пены [58]. Самым простым способом контроля является метод с использованием радиа ционных источников, работающих в стационарном режиме на «просвет» (рис. 3.7). Контроль за уровнем пены осуществляется следующим образом. На одной стороне камеры устанавливается источник, на другой — счетчик радиоактивности. Чувстви тельность счетчика настраивается по интенсивности излучения: когда уровень пены достигает зоны действия источника, счетчик фиксирует резкое уменьшение интенсив ности. Обычно по высоте камеры датчики радиоактивности устанавливаются внизу и вверху камеры на 2-3 уровнях, например, на высотах 17, 19 и 21 м. При достиже нии пеной уровня нижней отметки начинается подготовка неработающей камеры к ее подключению на режиме коксования. При достижении пеной уровня верхней отметки производится переключение потока сырья в подготовленную к коксованию камеру.
Например, если уровнемер показал высоту пенного слоя 21 м, а после вскрытия камеры уровень кокса в ней окажется 17 м, то высота пенного слоя составит 4 м. Уровень пены зависит от режимных параметров — линейных скоростей в свободном сечении камеры, температуры верха камеры, качества сырья и т. д. Высота пенного
124
слоя может достигать 5-6 и более метров. Особенно важно следить за уровнем пены в период перевода камеры: если камера, в которую направляется поток сырья, недо статочно прогрета, то пена за считанные минуты может достигнуть самых верхних отметок.
Рисунок 3.7 — Расположение датчиков (1) и счетчиков (2) радиоактивности по высоте камеры
Для снижения пенообразования применяются антипенные присадки, в качестве которых используются реагенты с низкой величиной поверхностного натяжения. Процесс пенообразования чрезвычайно сложен из-за совместного влияния многочис ленных физико-химических, гидродинамических и других факторов и существенно зависит от условий применения в конкретном технологическом процессе. В настоя
125
щее время не существует единой теории, полностью количественно объясняющей поведение пены во времени. Тем не менее известно, что:
—устойчивость пенного состояния определяется величиной поверхностного на тяжения, поверхностной прочностью, диаметром пузырей элементарной пены;
—поверхностное натяжение зависит от поверхностной активности, концентрации жидких веществ в растворе и от степени гетерогенности поверхностного слоя;
—поверхностная прочность пленки на границе раздела жидкой и газо-паровой фазы зависит от свойств коллоидных веществ в растворе, от степени насыщенности ими поверхностного слоя, наличия и характера механических примесей в жидкости;
—диаметр пузырьков газа не зависит от физико-химических свойств раствора, а определяется главным образом гидродинамическими условиями образования и выделения газа [58].
Наиболее распространенным способом борьбы с пеной является введение спе циальных веществ — пеногасителей, подбор которых, как правило, осуществляют эмпирически с учетом целей и условий производства.
Вкачестве количественной оценки пеногашения используют так называемый коэффициент пеногасящей способности, представляющий собой отношение высоты столба пены без добавления антивспенивателя к высоте столба пены после добав ления пенной присадки. Эффективность антивспенивателей зависит не только от их физико-химической природы, но и от концентрации, способа введения, от свойств пенообразующего раствора и многих других факторов.
Антипенные присадки должны отвечать следующим основным требованиям:
—обладать высокой эффективностью, т. е. быстро гасить пену в малых концентра циях, длительное время препятствовать образованию новой пены;
—не должны изменять свойства продуктов и затруднять их последующую перера ботку;
—не оказывать токсического действия;
—не должны изменять свои свойства при хранении и термической обработке.
Вкачестве антипенных присадок широко используются кремнийорганические соединения. Они химически инертны, устойчивы и эффективны при высоких тем пературах, доступны и дешевы. При применении присадок на действующих УЗК используются растворы в легком или тяжелом газойле коксования. Пионером в раз работке технологии применения антипенных присадок был П. С. Седов, который разработал инструментарий для изучения параметров пенообразования, эксперимен тально изучил эффективность различных соединений [58]. Им было показано, что вспенивание существенно зависит от физико-химических свойств исходного сырья. На рис. 3.8 показано влияние продолжительности опыта на изменение объема вели чины коэффициента вспенивания К, который определяется по соотношению
к- yjyv
где F — текущая высота коксующейся массы; VQ— исходная высота свежего сы рья.
На рис. 3.8 приведены результаты экспериментов по вспениванию при коксова нии смесей гудрона и асфальта пропановой деасфальтизации.
126
Продолжительность опыта, мин
Рисунок 3.8 — Влияние продолжительности опыта на кратность увеличения объема смеси асфальта и гудрона при нагревании (температурара 440-450 °С):
1 — гудрон; 2 — асфальт деасфальтизации
Рисунок 3.9 — Влияние содержания асфальтенов или коксового числа на кратность увеличения объема прямогонных остатков при нагревании (температура 440-450 °С):
1 — коксовое число по Конрадсону, % мае.; 2 — содержание асфальтенов, % мае.
Из приведенных данных следует, что величина коэффициента вспенивания прак тически линейно изменяется в зависимости от содержания асфальтенов, что говорит о существенном их влиянии на пенообразование в процессе коксования. Эффектив ность пеногашения увеличивается с повышением молярной массы и вязкости. На рис. ЗЛО показаны результаты по влиянию вида присадок на эффективность пено гашения.
127
Время, мин
Рисунок 3.10 — Влияние вида присадки на вспенивание при карбонизации гудрона:
1 — без присадки; 2 — с присадкой ПМС; 3 — с присадкой СКТН; 4 — с присадкой «Софэксил-1165» (концентрация присадок — б %) в легком газойле коксования
Представленные данные однозначно свидетельствуют о предпочтительности ис пользования в качестве пеногасителя при коксовании силикона СКТН и «Софэксил», которые по сравнению с присадкой ПМС дают большее снижение высоты пенного слоя.
В лабораторных условиях изучалось влияние концентрации двух видов антипенных присадок отечественного производства в растворе легкого газойля на снижение пенообразования при коксовании гудрона.
Кривые изменения высоты пенного слоя в зависимости от количества добавляе мого силикона (его концентрации в растворе) представлены на рис. 3.11. Представ ленные кривые показывают, что увеличение концентрации обоих силиконов в рас творе, подаваемых непрерывно на слой пены, способствует эффективному снижению высоты слоя пены. Следует отметить, что эффект непогашения СКТН отечественной присадки и импортной «Софэксил» идентичен.
При выборе типа присадки и ее концентрации в растворе необходимо исходить из двух условий: эффективность антивспенивателя и его цены. То есть чем при меньшей концентрации присадки достигается больший эффект пеногашения, тем меньше ее расход и, соответственно, меньше затраты на ее приобретение. Кроме того, немало важным фактором выбора типа присадки является ее доступность. Как показал опыт работы УЗК НУНПЗ, расход присадки СКТН составляет 4,5-4,8 кг на одну камеру коксования. С учетом этого нам представляется целесообразным использовать при садку отечественного происхождения.
Ввод раствора присадки осуществляется с помощью специальных форсунок, обеспечивающих эффективное разбрызгивание за счет конструкции самой форсунки и организации оптимального перепада давления на форсунке.
На рис. 3.12 приведена схема организации подачи присадки на действующей установке. Схема включает емкость для раствора присадки; циркуляционный насос для приготовления и перемешивания раствора силикона в легком газойле; регулирую щие клапаны; расходомер (ротаметр); разбрызгивающие устройства (форсунки) (рис 3.13).
128
Рисунок 3.11 — Влияние концентрации присадки на изменение вспенивания гудрона:
1 — без присадки; 2 — концентрация присадки 2%; 3 — концентрация присадки 6 % ;— СКТН; х — «Софэксил»
Подача раствора присадки (расход — 40 л/ч на одну форсунку) начинается за 4-6 ч (в зависимости от качества используемого сырья и его склонности к вспенива нию) до прекращения подачи сырья в заполненную камеру. С целью исключения ве роятности переброса пены в колонну из-за возможных колебаний давления, раствор непрерывно подается в заполненную коксовую камеру в период переключения камер и в течение ~30 мин после отключения от потока во время пропарки кокса водяным паром. В остальное время к форсункам подается водяной пар с целью исключения засорения их коксом. Количество пара, подаваемого через форсунки, — одна тонна за цикл.
Рисунок 3.12 — Схема подачи раствора антипенной присадки:
1 — емкость для раствора присадки; циркуляционный насос; 3 — регулирующий клапан; 4 — ротаметр;
5 — форсунки; б — камера коксования
129
4 4 0 - 5
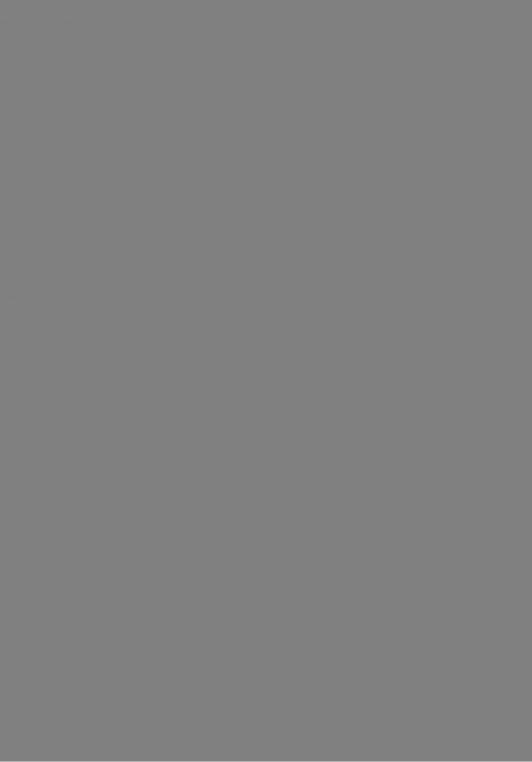