
книги / Современные и перспективные термолитические процессы глубокой переработки нефтяного сырья
..pdfРисунок 3.45 — Схема расположения труб, материальных потоков, установки датчиков и место отбора проб в печи для нагрева вторичного сырья УЗК НУНПЗ (Ново-Уфимский) (а), ННПЗ (Надворнянский) (б) и ВНПЗ (Волгоградский) (в).
Датчики: Л — температура продукта; □ — температуры поверхности металла труб; * — температуры дымовых газов; О — давление; А — расход сырья; ф — радиоактивные индикаторы; 0 — место отбора проб
181
Вход вторичного сырья
Рисунок 3.46 — Схема расположения труб, материальных потоков, установки датчиков и место отбора проб в печи для нагрева вторичного сырья УЗК ФНПЗ.
Датчики: Д — температура продукта; □ — температуры поверхности металла труб; * — температуры дымовых газов; О — давление; А — расход сырья; ф — радиоактивные индикаторы; 0 — место отбора проб
Печами типа ГС оборудованы установки 21-10/6 на НПЗ в гг. Туркменбаши, Фер гане, Атырау, Павлодаре. Печи более надежны, имеют достаточно высокий КПД, за брос пламени факела на поверхность трубного экрана исключается. Но схема нагрева сырья и конструкция печи не позволяют организовать чистку змеевика без остановки всей установки. На рис. 3.47 представлены конструкции печей (разработка «АлитерАкси» и УГНТУ) для УЗК ООО «ЛУКОЙЛ-Волгограднефтепереработка».
182
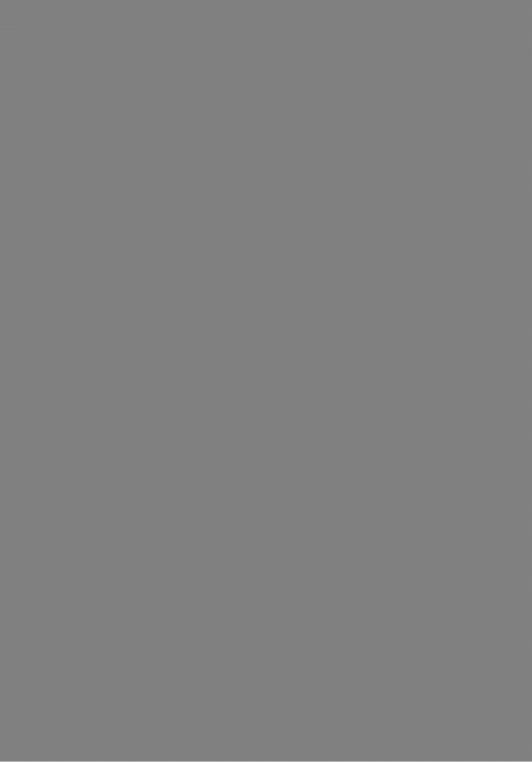
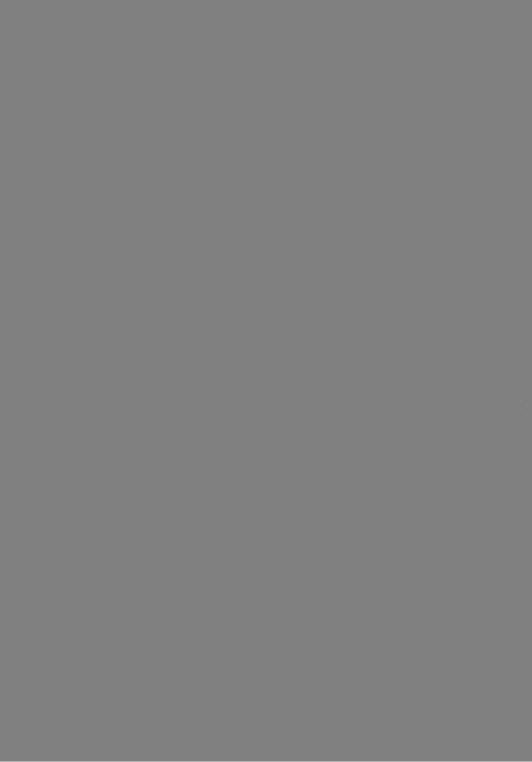
модернизированные аппараты и передовые технологии процессов ЗК. Современные системы бурения кокса позволяют выгружать кокс из камер диаметром 9 м за 2-3 ч, высоконапорные насосы на установке производительностью 6 млн т сырья в год оборудуются одним насосом без резерва, который работает без остановки 4-5 лет. Го рячие печные насосы также работают практически без резерва. Создана уникальная система открытия-закрытия люков камер (см. § 3.2.), позволяющая осуществлять эту операцию за несколько минут — это в буквальном смысле революция в технологии ЗК. Разработаны конструкции нагревательно-реакционных печей, позволяющих про водить удаление кокса из змеевиков без остановки всей установки, продлевая пробег до 4-5 лет. Усовершенствованы системы подготовительных операций циклы коксо вания сокращены до 12 ч (12 ч заполнение, 12 ч подготовка камеры к новому циклу).
Сопоставляя работу отечественных УЗК с современными установками, работаю щими по новым технологиям, оптимальным вариантом модернизации коксового про изводства на НПЗ России приходится признать снос всех существующих установок
истроительство новых. Расчеты показывают, что, например, при замене камер (а это надо делать уже сейчас и практически на всех установках) период простоя длится бо лее года. За это время завод за счет сокращения выработки продукции понесет огром ные убытки. При строительстве новой установки старая будет работать и к запуску новой УЗК ее строительство окупится практически полностью. Но такая стратегия требует значительных свободных средств, времени на проектирование, изготовление
ипоставки оборудования, поэтому весьма актуальной является задача модернизации действующих установок при минимальной затрате средств.
Наиболее перспективным направлением по увеличению производительности установок по сырью и коксу является снижение величины коэффициента рециркуля ции продуктов реакции К (см. § 3.4). Поскольку все установки работают с высоким Кр — 40-100 % и более, то его снижение до 10 % приведет к значительному увеличе нию производительности практически без изменения работы установки по основным аппаратам. Такая технология разработана в УГНТУ [59, 60]. Впервые технология внедрена на НПЗ г. Туркменбаши (Туркменистан), где установка типа 21-10/600, мощностью по проекту 600 тыс. т сырья в год с фактической производительностью не более 450 тыс. т, после внедрения технологии с низкой рециркуляцией перера батывает 0,9-1,0 млн т сырья в год. Установка эксплуатируется с 2003 г. За 5 лет эксплуатации от потребителей не поступало ни одной рекламации на качество кокса.
Особо следует отметить работу самой первой установки, построенной в Уфе в 1955 г., которая на протяжении всех лет эксплуатации имела высокие показатели по производству кокса и являлась всесоюзным испытательным полигоном по разра ботке новых видов кокса, нефтяного пека и специальных нефтепродуктов. Так, на установке проведен целый ряд опытных пробегов и наработано несколько опытных партий игольчатого кокса, на базе которых разработана отечественная технология производства этого вида кокса. На базе жидких продуктов освоено производство профилактических средств типа «Северин» и «Ниогрин».
За время эксплуатации мощность УЗК была доведена до 400-450 тыс. т/год. В 2008 г. она была реконструирована и переведена в режим работы с регулируемым Кр, и была установлена четвертая камера коксования. Схема УЗК после реконструк ции представлена на рис. 3.49.
185
КХ-1.Х-1
Рисунок 3.49 — Схема УЗК 21-10/300 ОАО «Ново-Уфимский НПЗ» после реконструкции. Производительность по сырью 700-750 тыс. т/год
Сырье коксования (I сырье) подается в змеевики первичного сырья печи П-1
инаправляется в колонну формирования вторичного сырья К-0. В колонну К-0 также подается рециркулят — тяжелый газойль из аккумулятора основной ректификацион ной колонны К-1. Первичное сырье смешивается с рециркулятом, образуя вторичное сырье коксования. Вторичное сырье из куба колонны К-0 забирается насосами и дву мя параллельными потоками прокачивается через змеевики реакционно-нагрева тельной печи П-1, где нагревается до 490-500 °С. Нагретое сырье подается в камеры коксования. На каждый поток вторичного сырья установлено по 2 камеры коксования Р-1-Р-4. Предусмотрена возможность работы камер как по двухпоточной схеме, так
ипо однопоточной. Кокс аккумулируется в камерах, а пары направляются в колонну
К-1 на ректификацию. С верха К-1 газ, пары бензина и водяной пар охлаждаются в конденсаторах-холодильниках КХ-1, Х-1 и разделяются в газосепараторе Е-2. Газ используется в качестве топлива, а избыток выводится с установки. Бензин из Е-2 подается в К-1 в качестве острого орошения, а балансовое количество выводится с установки. Легкий газойль с 9-й тарелки К-1 забирается насосом и после охлажде ния выводится с установки. Тяжелый газойль накапливается в аккумуляторе колонны К-1, откуда забирается насосом и разделяется на два потока. Первый поток подается в К-0 в качестве рециркулята. Второй поток после охлаждения в Х-8 также делится на два: один поток направляется в узел улавливания продуктов пропарки и охлажде ния кокса, а балансовое количество выводится с установки. Остаток с низа колонны К-1 прокачивается насосом через фильтр Ф-1 и после охлаждения вместе с тяжелый газойлем откачивается с установки. Тепловой баланс колонны и качество получае мых продуктов регулируется за счет циркуляционного орошения.
Образовавшийся в камере кокс пропаривается водяным паром и охлаждается во дой. Продукты пропарки и охлаждения улавливаются на блоке улавливания, который состоит из абсорбера Е-9, конденсатора-холодильника АВО-5, сепаратора С-1.
Основные технические решения реконструкции:
—монтаж 4-й камеры коксования;
—монтаж узла формирования вторичного сырья (К-0);
—реконструкция реакционно-нагревательной печи;
—монтаж закрытой секции улавливания продуктов прогрева камер, пропарки и охлаждения кокса;
—реализация схемы подачи воды на верх камер коксования для охлаждения кокса;
—монтаж схемы подачи антипенной присадки;
—реконструкция схемы сброса предохранительных клапанов из камер в К-1.
До реконструкции Кр находился в пределах 30-40 %, после реконструкции К поддерживается на уровне 10 %, что естественно привело к увеличению производи тельности. Производительность увеличилась и за счет изменения режима подачи сы рья в печь. При переключении реакторов (особенно это относится к трехреакторной схеме) пары не до конца прогретого реактора поступают в низ колонны, температура в низу реактора падает, что ведет к понижению температур на входе в печь и требует регулировки режима горения. Кроме того, снижение температуры в низу колонны приводит к временному росту Кр и, как следствие, снижению производительности по сырью, а поскольку переключений несколько сотен в году, производительность по сырью снижается значительно, применительно к УЗК НУНПЗ эта цифра составляет
187
около 100 тыс. т/год. При включении в схему выносной секции К-0 основной ректи фикационной колонны К-1 эти негативы исключаются, загрузка насосов с низа К-0 постоянна с постоянной температурой, температурный режим печи постоянный.
Следует также особо отметить, что производительность 700-750 тыс. т/год до стигается использованием одной печи, построенной 55 лет назад.
Кроме повышения производительности после реконструкции коренным образом изменилась экологическая обстановка на установке.
Вместо воды в Е-9 подается газойль коксования и установлены тарелки клапанно го типа. Замена воды на газойль позволила исключить попадание высококипящих уг леводородов в воду, они растворяются газойлем и возвращаются в процесс, уходящие с верха Е-9 пары бензина и воды охлаждаются и легко разделяются в аппарате С-1.
До реконструкции установка работала по 12-часовому циклу заполнения камер, при этом на подготовительные операции отводилось 24 ч. При переходе на 4-ка- мерный вариант камера заполняется за 16 ч и 16 ч отводится на подготовку камеры к новому циклу. График работы установки показан в табл. 3.14.
Таблица 3.14 — График работы камер коксования после реконструкции
УЗК ОАО «Ново-Уфимский НПЗ»
|
Наименование операций |
Продолжительность операции, ч |
1. |
Заполнение камер коксом |
16 |
2. |
Переключение камер и пропарка |
1.0 |
|
в основную ректификационную колонну |
|
|
|
|
3. |
Пропарка в систему улавливания |
1.0 |
4. Охлаждение водой |
4,0 |
|
5. Дренирование воды |
1,5 |
|
6. |
Выгрузка кокса из камер |
3,5 |
7. |
Установка крышек и опрессовка |
2,0 |
8. |
Разогрев камер |
3,0 |
9. |
Резервное время |
0 |
10. Итого |
16 |
Высокоавтоматизированная установка замедленного коксования ОАО «Уфанефтехим». На НПЗ России первой автоматизированной установкой, на ко торой не будет использоваться тяжелый ручной труд при выполнении трудоемких операций, будет установка ЗК на ОАО «Уфанефтехим», где внедрены многие со временные достижения в технологии и реализованы передовые инженерные раз работки.
Проект установки разработан институтом ГУП «Башгипронефтехим» по ли цензии УГНТУ. При проектировании установки учитывались все современные достижения в области инженерных разработок, закуплено самое современное высокоэффективное оборудование, которое не выпускается отечественным машино строением или его аналоги значительно уступают зарубежным.
188
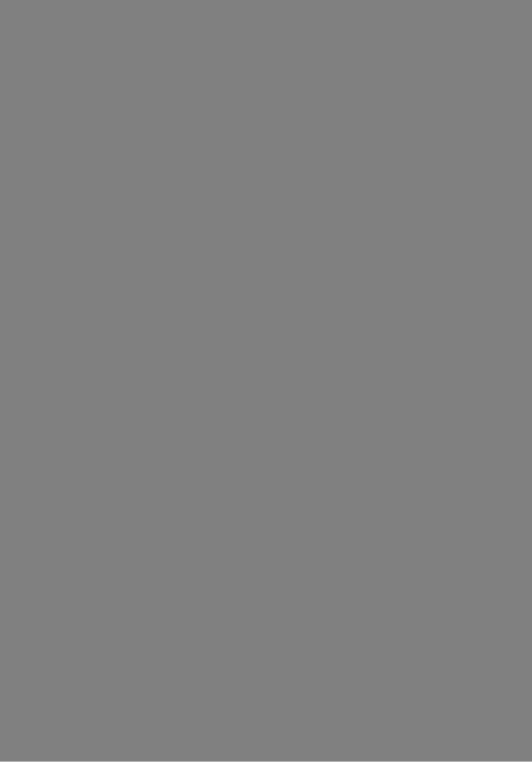
и разделяются в газосепараторе Е-103. Газ используется в качестве топлива, а избы ток выводится с установки. Бензин из газосепаратора подается в К-101 в качестве острого орошения, а балансовое количество выводится на стабилизацию. Легкий газойль из аккумулятора легкого газойля колонны К-101 поступает в отпарную ко лонну легкого газойля, прокачивается через холодильник и после охлаждения вы водится с установки. Тяжелый газойль накапливается в аккумуляторе К-101, откуда поступает в отпарную колонну тяжелого газойля. Тяжелый газойль из отпарной колонны делится на три потока. Первый поток подается под нижний аккумулятор колонны К-101 в качестве горячего орошения, второй направляется в К-100 в качест ве рециркулята. Третий поток после охлаждения также делится на два: один поток направляется в узел улавливания продуктов прогрева камер коксования, пропарки и охлаждения кокса, а балансовое количество выводится с установки. Остаток с низа колонны К-101 прокачивается через фильтр Ф-101 и после охлаждения откачивается с установки. Часть кубового остатка из колонны К-101 через фильтр Ф-102 возвраща ется в колонну для предотвращения засорения куба колонны коксовыми частицами. Тепловой баланс колонны и качество получаемых продуктов регулируется за счет двух циркуляционных орошений.
Образовавшийся в камере кокс пропаривается водяным паром и охлаждается во дой. Продукты пропарки и охлаждения улавливаются на блоке улавливания, который состоит из абсорбера К-104, конденсатора-холодильника Х-107, сепаратора С-101.
Технология имеет целый ряд преимуществ перед традиционной:
—она позволит регулировать величину Кр в широких пределах, начиная от 0;
—исключает попадание коксовых частиц на прием горячих печных насосов, что снижает скорость закоксовывания змеевиков печи;
—при переводе реакторов снижение температуры в низу основной ректификаци онной колонны не влияет на режим работы печи, не требуется изменять режим горения, производительность установки в момент переключения камер не умень шается;
—на установке можно производить два различных по качеству кокса — сернис тый и малосернистый; малосернистый и игольчатый; сернистый и игольчатый. График работы камер представлен в табл. 3.15, где приведены два режима работы
установки применительно к переработке остатка висбрекинга или к вакуумированному остатку висбрекинга.
Следует отметить так же, что установка может работать по 12-часовому циклу заполнения камер.
Кроме особенностей технологии на установке установлено самое современное оборудование. Прежде всего, следует отметить шиберную систему открытия и за крытия верхних и нижних люков коксовых камер и шиберных задвижек (разработ чик и поставщик фирма «Delta Valve») для переключения реакторов по парам на верху коксовых камер. Переключение камер при переводе камер с режима на режим осуществляется шаровыми кранами (поставщик фирма «Flowserve»). Внедрение пе речисленного оборудования позволило исключить тяжелый и даже не безопасный физический труд.
Раньше на эти операции в штате предусматривалось 3-4 человека в каждой вах те, новое оборудование полностью оснащено системой гидро- и электроприводов
190