
книги / Современные и перспективные термолитические процессы глубокой переработки нефтяного сырья
..pdf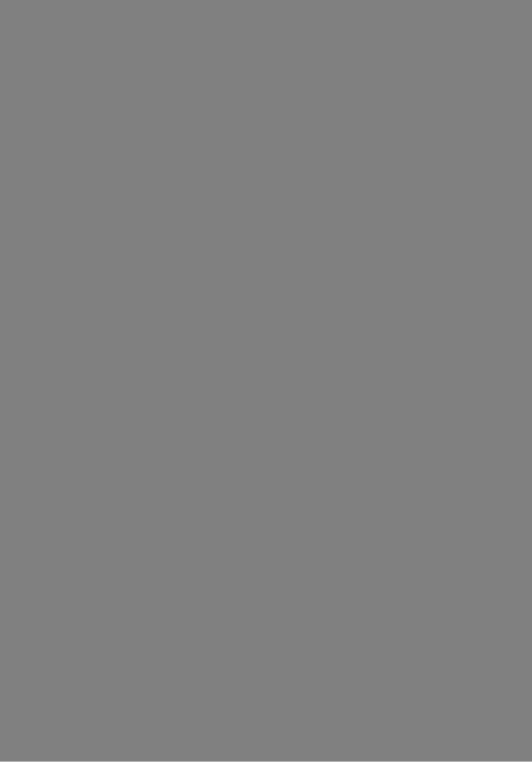
Кроме того, США является наиболее крупным потребителем и экспортером не только электродного кокса, но и топливного кокса для отраслей промышленности, традиционно использовавших каменный уголь. НПЗ США характеризуются наибо лее высокими показателями по насыщенности углубляющими нефтепереработку процессами, такими как коксование, КК (37,6%) и ГК (10,5 %), что позволяет перера ботать не только прямогонные газойли, но и в больших объемах газойли коксования, тем самым обеспечить самый высокий выход моторных топлив (73 %, а в России всего 48%) и глубину переработки нефти 97,6% (против 71,1 % в России).
Помимо США, ведущие позиции в мире по мощностям коксования занимают Китай (15,4 млн т, или 6,1 % от мировых мощностей), Венесуэла (соответственно 8,8 млн т и 3,5 %), Германия (5,7 млн т и 2,3 %), Япония (5,3 млн т и 2,1 %) и Россия (5,3 млн т и 2,1 %). Характерно, что в перечисленных выше странах, кроме России, мощности коксования сбалансированы мощностями КК и ГК, что обеспечивает прак тически безостаточную переработку нефти и, что особенно важно, существенную экономию сырой нефти.
Таблица 1.1 —
Страны
Показатели нефтепереработки развитых стран мира и РФ в 2005 г.
по мощностям (млн т/г) первичной переработки нефти (Аяя), |
|
|||||||
коксования (Л^), каталитического крекинга (NKK), |
|
|
||||||
гидрокрекинга (NrK) и глубине переработки нефти (ГПН) |
|
|||||||
|
|
оо |
N |
к |
100 |
N |
|
ГПН, |
|
|
|
■ ^•1 0 0 |
- ^ • 1 0 0 |
||||
|
|
|
ж—1 |
1WU |
|
|||
^ п п |
NK |
|
IX |
|
N ПП |
Nnn |
% |
|
|
|
|
|
|
|
США |
842,5 |
136,3 |
16,2 |
53,9 |
37,6 |
10,5 |
97,6 |
Китай |
232,1 |
15,4 |
6,6 |
6,1 |
31,4 |
4,6 |
— |
Венесуэла |
67,3 |
8,8 |
13,1 |
3,5 |
18,9 |
— |
— |
Германия |
117,3 |
5,7 |
4,9 |
2,25 |
18,9 |
11,7 |
93,1 |
Япония |
231,7 |
5,3 |
2,3 |
2,1 |
22,5 |
5,3 |
82,3 |
Россия |
268,6 |
5,3 |
2,0 |
2,1 |
6,7 |
0,5 |
71,1 |
Бразилия |
96,6 |
5,0 |
5,2 |
2,0 |
30,4 |
— |
— |
Великобритания |
91,1 |
3,8 |
4,1 |
2,0 |
25,2 |
14,4 |
84,3 |
Западная Европа |
752,3 |
18,7 |
2,5 |
7,4 |
15,8 |
7,5 |
— |
Всего в мире |
4115,7 |
252,9 |
6,1 |
100 |
27,8 |
8,1 |
88 |
Вотличие от ряда развитых стран мира, например США, где процессы коксо вания развиваются преимущественно для получения дистиллятов коксования с по следующей переработкой их в моторные топлива на установках КК или ГК, коксо вание в России до последнего времени рассматривалось и создавалось только для получения целевого продукта — нефтяного кокса для алюминиевой и электродной промышленности.
Вэтой связи УЗК строились только на тех НПЗ, где была доступна местная ма лосернистая нефть (Баку, Красноводск, Гурьев (ныне Атырау), Херсон, Волгоград,
12
Фергана) или была обеспечена поставка западносибирских малосернистых нефтей (Ангарск, Омск, Павлодар). Три УЗК — в Перми, Уфе и Ново-Куйбышевске — из восьми в России перерабатывают сернистую нефть с производством приемлемого по качеству кокса с содержанием серы до 3 % и выше и с повышенным содержани ем металлов. Однако, с учетом нынешней мировой тенденции развития технологии нефтепереработки, России следует переориентироваться на строительство и ввод мощностей коксования не только для обеспечения потребности в электродных кок сах, но и с целью решения актуальнейших проблем страны — углубления перера ботки нефти, повышения выхода и качества моторных топлив, соответствующим жестким экологическим требованиям ЕС-4 и ЕС-5 — путем блокировки установок коксования с углубляющими нефтепереработку каталитическими процессами КК
иГК. Как следует из табл. 1.1, отечественная нефтепереработка ныне значитель но отстает не только от развитых стран, но и от среднемирового уровня по пока зателям насыщенности НПЗ углубляющими переработку нефти и повышающими качество нефтепродуктов вторичными процессами и по выходу моторных топлив
иГПН.
Такую неэффективную и отсталую структуру отечественной нефтепереработ ки нельзя оправдать, как раньше, кажущимся богатством по сырьевым ресурсам, поскольку по извлекаемым запасам нефти (~5 % от мировых) Россия, при нынеш них темпах добычи и экспорта без восполнения ее запасов, обречена на истощение ресурсов нефти уже до середины нынешнего столетия с серьезными негативными последствиями для экономики последующего поколения россиян [2].
На начало 2009 г. на отечественных НПЗ находилось 8 УЗК общей мощностью 5,3 млн т/год (табл. 1.2). Как видно, средняя продолжительность эксплуатации УЗК в России составляет свыше 30 лет.
Таблица 1.2 — Типы и мощности (по сырью) УЗК на начало 2005 г.
НПЗ |
Коли |
Тип УЗК |
Год |
NKтыс. т/год |
|
чество |
ввода Проектная |
Установленная |
|||
|
УЗК |
|
|||
Новокуйбышевский |
1 |
21-10/5К |
1986 |
1500 |
1392 |
|
1 |
21-10/300 |
1963 |
300 |
351 |
Волгограднефтепереработка |
1 |
21-10-600 1966 |
600 |
658 |
|
|
1 |
21-10/7 |
1982 |
240 |
263 |
Пермнефтеоргсинтез |
1 |
21-10/ЗМ |
1970 |
600 |
1000 |
Омский |
1 |
21-10/ЗМ |
1970 |
600 |
600 |
Ангарская НХК |
1 |
21-10/ЗМ |
1971 |
600 |
600 |
Ново-Уфимский |
1 |
21-10/300 |
1955 |
300 |
430 |
Всего по РФ |
8 |
— |
— |
4780 |
5284 |
Комбинированная УЗК 21-10/5К Новокуйбышевского НПЗ — самая молодая и мощная. Она состоит из 4 секций (100 — вакуумной перегонки; 300 — ЗК; 400 — получение водяного пара; 500 — очистка газов) и транспортного блока. Сырьем уста новки является гудрон. Целевой продукт — кокс с содержанием серы ~3 %, летучих веществ ~8%, с выходом фракций более 8 мм -70% .
13
На 3 установках ЗК Волгоградского НПЗ перерабатывается смесь гудрона, ас фальта, экстракта процесса Дуосол. Выпускается электродный кокс с содержанием серы -1,5% .
На Пермском НПЗ эксплуатируется установка ЗК производительностью 1 млн т/год. Сырьем является гудрон. Производится кокс с содержанием серы -3 %.
На модернизированной установке ЗК Омского НПЗ перерабатывается смесь гудрона (70,8 %), тяжелого газойля КК (28,3 %) и тяжелого газойля коксования (1,6 %) с получением электродного кокса с серой -1,5%. Бензин ЗК на этом НПЗ направля ется на КК, а тяжелый газойль вовлекается во флотский мазут.
Установка ЗК на Ангарском НХК несколько отличается от рассмотренных вы ше аналогов: в ее состав дополнительно входят блок очистки газов от сероводорода и блок стабилизации и защелачивания при нагреве и пропарки реакторов. С 2004 г. на УЗК перерабатывается смесь гудрона (96,2 %), смолы пиролиза (3,8 %) и тяжелого газойля КК (0,02%) с получением электродного кокса с серой -1,5%. Бензин и ди зельная фракция направляются на гидроочистку.
На Ново-Уфимском НПЗ эксплуатируется построенная впервые в СССР
(1955 г.) установка ЗК проектной мощностью 300 тыс. т/год для переработки сер нистых и высокосернистых ТНО. В качестве сырья используется либо только гудрон или его смесь с остатком висбрекинга и газойлями КК с выработкой серы -2,5-4,0%. Таким образом, только на трех НПЗ (в Ангарске, Омске и Волгограде) производится малосернистый кокс с содержанием серы до 1,5%.
Как видно из приведенных в табл. 1.3 данных по материальному балансу УЗК, наибольшие выходы достигнуты по коксу на Ново-Уфимском НПЗ, а по сумме бен зина и легкого газойля — на Ангарском НХК.
Таблица 1.3 — Материальный баланс отечественных установок замедленного коксования за 2004 г., % от исходного сырья
Продукты УЗК
Газ
Бензин
Дизельная
фракция 350-400 °С Легкий газойль
Тяжелый
газойль
Кокс
Потери
Бензин + легкий газойль
Ново-Куйбы- шевский НПЗ |
Омский НПЗ |
11,4 |
8,3 |
10,2 |
8,7 |
——
——
31,1 18,3
14,6 34,1
31,1 28,3
1,6 2,3
41,3 27,0
Волгоградский НПЗ |
НовоУфимский НПЗ |
Пермский НПЗ |
|||
21-10/300 21-10/7 21-10/600 |
|||||
|
|
||||
13,2 |
8,7 |
9,3 |
8,0 |
9,6 |
|
8,3 |
11,0 |
14,1 |
4,0 |
14,9 |
|
— |
— |
— |
— |
— |
|
— |
— |
— |
— |
— |
|
25,6 |
27,4 |
35,0 |
19,0 |
22,5 |
|
25,5 |
25,4 |
14,1 |
35,0 |
26,4 |
|
26,7 |
26,8 |
26,8 |
33,0 |
25,7 |
|
0,7 |
0,7 |
0,7 |
1,0 |
0,9 |
|
33,9 |
38,4 |
49,1 |
23,0 |
37,4 |
Ангарский НХК
8,2
15,5
28,0
3,9
—
12,9
27,6
3,9
47,4
14
Втабл. 1.4 приведены сведения об оснащенности российских НПЗ установками
ККи ГК, откуда видно, что из НПЗ с коксовыми производствами лишь Ново-Уфим ский НПЗ и Волгограднефтепереработка не имеют в своей технологической струк туре процессов КК и ГК.
Таблица 1.4 — Мощности первичной переработки нефти (УУя/7), каталитического крекинга (Л^), гидрокрекинга (NrK)
на НПЗ РФ на начало 2005 г.
НПЗ |
млн. т |
млн т |
* кк |
млн т |
^ Г К |
|
% |
% |
|||||
|
||||||
Омский |
19,5 |
3,55 |
18,2 |
0 |
0 |
|
Рязанский |
19,04 |
2,5 |
13,1 |
0 |
0 |
|
Ярославнефтеоргсинтез |
15,20 |
1,25 |
8,2 |
0 |
0 |
|
Ангарская НХК |
13,40 |
1,76 |
13,1 |
0 |
0 |
|
Ново-Уфимский |
10,24 |
0 |
0 |
0 |
0 |
|
Московский |
12,15 |
2,0 |
16,5 |
0 |
0 |
|
Пермнефтеоргсинтез |
12,04 |
0,95 |
(7,9) |
3,52 |
29,2 |
|
Салаватнефтеоргсинтез |
11,71 |
0,6 |
5,1 |
0 |
0 |
|
Волгограднефтепереработка |
10,50 |
0 |
0 |
0 |
0 |
|
Новокуйбышевский |
9,56 |
0,71 |
7,4 |
0 |
0 |
|
Уфимский |
9,56 |
0,21 |
2,3 |
0 |
0 |
|
Уфанефтехим |
9,50 |
0,9 |
9,5 |
1,0 |
10,5 |
|
Куйбышевский |
7,0 |
0,89 |
12,7 |
0,5 |
7,1 |
|
Всего по РФ |
268,6 |
18,0 |
6,70 |
5,02 |
1,87 |
В большинстве стран мира процесс коксования используется для получения
вкачестве целевого продукта не нефтяного кокса, а газойлей коксования для пере работки их в автомобильные бензины и дизельные топлива на установках КК и ГК при существенном повышении глубины переработки нефти.
Это обстоятельство связано с тем, что наряду с получением ценнейшего продук та, каковым является кокс, в процессе реализуется целый ряд технологий, которые обеспечивают широкое его применение в производстве моторных топлив, улучшении экологической обстановки и санитарных условий на НПЗ:
1.В процессе ЗК обеспечивается высокоэффективная термодеасфальтизация неф тяных остатков. Если исходное сырье имеет коксовые числа 25-30% и более, то продукты коксования не более 0,3-0,5 %.
2.На установках ЗК происходит деметаллизация нефтяного сырья; при исходном содержании металлов до 300 и более ppm, в продуктах коксования содержание их не превышает 3-5 ppm, а 95-98% переходит в кокс.
3.Процесс ЗК является самым мощным «санитаром» на НПЗ. Образующиеся нефтешламы и другие отходы перерабатываются на УЗК, при этом получается топливный кокс, газообразные и жидкие продукты коксования, пригодные для производства моторных топлив.
15
4.Наличие УЗК высокой производительности в схеме завода позволяет наиболее быстро адаптироваться к изменению состава перерабатываемой нефти, посколь ку коксовые числа продуктов коксования и содержание в них металлов практи чески одинаковы как при переработке мазутов так и при переработке асфальтов, как малосернистых так и высокосернистых нефтей.
5.При использовании нефтяного кокса в качестве энергетического топлива резко снижается загрязнение окружающей среды. Например, при сжигании 6 млн т топочного мазута с содержанием серы 3 % мае. в окружающую среду выбрасы вается 180 тыс. т/год серы в виде сернистых соединений. При коксовании тако го же количества мазута образуется около 700 тыс. т/год нефтяного кокса с со держанием серы ~ 3,5 % мае., при сжигании которого образуется 49 тыс. т/год серы в виде сернистых соединений, что значительно ниже объема выбросов в окружающую среду при сжигании мазута. Это обстоятельство использу ется заводами, и многие строят собственные энергетические установки, ис пользуя кокс в качестве топлива. В США около 30 тепловых электростан ций переведено на сжигание нефтяного кокса в смеси с каменным углем, что полностью решает проблему сбыта нефтяного кокса, гарантирует круг логодичную бесперебойную работу заводов, так как кокс может храниться долго и проблема вывоза не столь актуальна по сравнению с проблемой вывоза мазута, когда при заполнении резервуарных парков приходится сни жать производительность завода. Для отгрузки можно организовать склад, обеспечивающий годичный объем хранения кокса. Все вышеперечисленное и делает процесс перспективным, наиболее дешевым и экономически при влекательным в производстве моторных топлив из тяжелых нефтяных остат ков.
Из опыта нефтепереработки США известно, что использование газойлей кок сования на установках КК и ГК позволило сэкономить 250 млн т/год нефти, что составляет 30% от переработанной в стране нефти. Между тем при слабой насы щенности процессами КК и ГК в отечественной нефтепереработке используется лишь 11,7% вакуумного газойля (см. табл. 1.1) от мощностей первичной перера ботки нефти, т. е. не вовлечено в каталитическую переработку более половины от потенциального его содержания в перерабатываемой нефти. В этой связи тяже лый газойль коксования используется на всех НПЗ России в качестве компонента котельного топлива.
На перспективу в соответствии с федеральной целевой программой России «Энергоэффективная экономика» и разделом «Модернизация нефтеперерабатываю щей промышленности» планируется к концу 2010 г. (если это не станет очередным неисполняемым намерением нефтяных компаний) строительство и ввод дополни тельных мощностей: по производству вакуумного газойля на 20 млн т/год; коксова нию (на Комсомольском, Ачинском, Туапсинском, Волгоградском НПЗ и Уфанефте химе); каталитическому крекингу на 2,9 млн т/год (в Рязани, Нижнекамске и Орске) и по гидрокрекингу на 18,4 млн т/год (в Киришах, Ярославле, Волгограде, НовоКуйбышевске, Ачинске, Комсомольске-на-Амуре и Туапсе). При этом использование газойлей коксования в качестве смесевого с вакуумным газойлем сырья для КК и ГК намечается на всех перечисленных НПЗ.
16
7.7.2.Особенности технологии производства игольчатого кокса
Сцелью интенсификации электросталеплавильных процессов в последние годы широко применяют высококачественные графитированные электроды, работающие при высоких удельных токовых нагрузках (30-35 Ом/см2). Зарубежный и отечест венный опыт показывает, что получить такие электроды возможно лишь на основе специального малозольного и малосернистого, так называемого игольчатого, кокса. Только игольчатый кокс может обеспечить такие необходимые свойства специальных электродов, как низкий коэффициент термического расширения и высокая электро проводимость. Потребности металлургии в таких сортах коксов за рубежом и в быв шем СССР непрерывно возрастают.
Игольчатый кокс по своим свойствам существенно отличается от рядового элект родного: ярко выраженной анизотропией волокон, низким содержанием гетеропри месей, высокой удельной плотностью и хорошей графитируемостью [10-12].
Наиболее традиционное сырье для производства игольчатого кокса — это мало сернистые ароматизированные дистиллятные остатки термического крекинга, газой лей КК, экстрактов масляного производства, тяжелой смолы пиролиза углеводородов,
атакже каменноугольной смолы. Аппаратурное оформление установки коксования для получения игольчатого кокса такое же, как на обычных УЗК. Температурный режим коксования при производстве игольчатого кокса примерно такой же, как при получении рядового кокса, только несколько выше кратность рециркуляции и давле ние в реакторах. Прокалка игольчатого кокса, по сравнению с рядовым, проводится при более высоких температурах (1400-1500 °С) [12].
1.2.Современное состояние непрерывных процессов коксования (флюидкокинг и флексикокинг)
В отличие отЗК коксование с псевдоожиженным слоем (флюидкокинг) [1] является непрерывным, высокопроизводительным, более автоматизированным
итехнологически универсальным, позволяющим перерабатывать исключительно разнообразные тяжелые остатки, такие как гудроны, асфальты, природные битумы (битуминозные пески) с плотностью 0,94-1,2 г/см3 и коксуемостью 12-50% мае. Целевым назначением флюидкокинга является получение из ТНО дистиллятных продуктов, направляемых на последующую гидрокаталитическую переработку в вы сококачественные моторные топлива. Получающийся в этом процессе порошкооб разный кокс является побочным малоценным продуктом, непригодным для изготов ления анодных и графитированных изделий, и используется в качестве топливного кокса на рынке твердых видов топлива.
Эта технология была впервые внедрена в 1947 г. в штате Монтана США произво дительностью всего 10тыс. бар./сут. В настоящее время в эксплуатации на НПЗ США
иКанады находится 8 установок флюид-коксования, в т. ч. 4 установки производи тельностью 95-110 тыс. бар./сут для переработки битуминозных песков в провинции Альберта в Канаде. Разработан проект отечественной промышленной установки, однако этот процесс до сих пор не внедрен на НПЗ нашей страны и за рубежом.
Флексикокинг [1] представляет собой модифицированный вариант флюидко кинга, дополненный блоком газификации балансового кокса и очистки низкокало
17
рийных топливных газов с получением углеводородных газов и жидких продуктов коксования. Топливный газ, получаемый газификацией (флексигаз) может сжигаться на собственном НПЗ или на соседних объектах.
Первая промышленная установка была введена в эксплуатацию в 1986 г. В настоя щее время в эксплуатации находится 5 установок (в Японии, Венесуэле, Нидерлан дах, в штатах Калифорния и Техас в США) суммарной производительностью свыше 1900 тыс. бар./сут.
Технология процесса флексикокинг получила дальнейшее развитие. В схему установки был включен второй реактор газификации. При этом в первом реакторе, куда подается только воздух, осуществляется частичное сжигание кокса, коксовый газ используется для нагрева рециркулирующего кокса в коксонагревателе; во втором газификаторе подачей водяного пара образуется синтез-газ.
Применение двух газификаторов позволяет примерно на 20% снизить выработку топливного газа и одновременно обеспечить производство водорода, количество ко торого значительно превосходит потребности в водороде для гидрооблагораживания жидких продуктов коксования.
Показатели работы промышленной установки флексикокинга производительнос тью 1 млн т/год приведены в табл. 1.5 и 1.6 [1].
Таблица 1.5 — Результаты работы промышленной установки «флексикокинг» производительностью 1 млн т/г
Показатель |
Данные |
||
Проектные |
Фактические |
||
|
|||
Сырье, м3/сут |
3387 |
3244 |
|
Плотность сырья, кг/м3 |
1038 |
1032 |
|
Коксуемость по Конрадсону, % мае. |
22,7 |
22,3 |
|
Содержание серы в сырье, % мае. |
4,3 |
5,0 |
|
Выход, % мае.: |
|
|
|
углеводороды С,-С2 |
6,8 |
6,0 |
|
углеводороды С3 |
3,2 |
2,1 |
|
углеводороды С4 |
2,1 |
2,2 |
|
фр. С5-182 °С, % об. |
16,2 |
19,5 |
|
фр. 182-510 °С,% об. |
5,04 |
49,3 |
|
Общий кокс, т/сут. |
1021,5 |
965,3 |
|
Кокс газифицированный, т/сут (%) |
928,1 (90,0) |
934,4 (96,9) |
|
Продуваемый кокс*, т/сут. |
93,4 |
30,9 |
|
Коксовый газ, м3 мазутных эквивалентов |
21200 |
23000 |
В продувочном коксе концентрируется более 99 %металлов, содержащихся в исход ном сырье.
18
Таблица 1.6 — Характеристика основных продуктов процесса флексикокинг
Показатель |
Данные |
|
Проектные |
Фактические |
|
|
до очистки |
после очистки |
Сырье |
|
|
Плотность сырья, кг/м3 |
1032 |
— |
Коксуемость по Конрадсону, % мае. |
21,8 |
— |
Содержание серы, % мае. |
5,6 |
— |
Продукты |
|
|
Бензин (после гидроочистки): |
|
|
бромное число |
—/1,0 |
0,4 |
содержание серы, % мае. |
3,5/0,01 |
0,00026 |
содержание азота, % мае. |
—/0,001 |
0,00003 |
Газойль коксования (после гидроочистки): |
|
|
содержание серы, % мае. |
5,3/0,1 |
0,05 |
содержание азота, % мае. |
—/0,13 |
0,03 |
Коксовый газ: |
|
|
содержание сероводорода, % об. |
—/0,002 |
0,0001 |
содержание серооксида углерода, % об |
—/0,0142 |
0,0134 |
низшая теплопроводная способность, ккал/м3 |
—/1148 |
1006 |
1.3.Современное состояние термоконтактных процессов деасфальтизации
идеметаллизации нефтяных остатков (APT, АКО, ЗД, ЭТКК, НОТ, ККИ)
Под термоконтактными подразумеваются процессы, осуществляемые термоли тически на поверхности твердых порошкообразных контактов, полученных либо специальным синтезом, либо из природных материалов. В литературе по нефтепе реработке встречаются термины-синонимы, такие как термоконтактный крекинг (ТКК), термоадсорбционный крекинг (ТАК), термоабсорбционная деасфальтизация и деметаллизация (ТАДЦ) [1]. Известен разработанный в СССР (Грозный) процесс ТКК, проводимый с использованием в качестве контакта гранулированного кокса по технологии, почти аналогичной каталитическому крекингу с движущимся слоем шарикового катализатора (типа 43-102). Флюидкокинг можно рассматривать как этап совершенствования технологии термоконтактного коксования, связанный с примене нием аппаратов с псевдоожиженным слоем, как это происходило ранее применитель но к процессам каталитического крекинга (отечественные установки 43-103,1А/1М, ГК-3). Следующий этап в совершенствовании каталитического крекинга был, как из вестно, связан с переводом реакционных аппаратов этих процессов на лифт-реактор- ные системы, в которых время контактирования сырья с катализатором на порядок
19
меньше по сравнению с реакторами с псевдоожиженным слоем (отечественные уста новки Г-43-107, КТ-1). Последнее достижение в этой области — процессы КК с ульт ракоротким временем контакта, так называемые миллисекундные процессы (ККМС).
Почти аналогичные эволюционные этапы происходят и применительно к процес сам коксования, но с использованием в качестве контактов не кокса, а специальных адсорбентов, не обладающих каталитической активностью (иначе катализаторы быст ро отравляются металлами, содержащимися в ТНО). Поэтому не удивительно, что вслед за этапом флюидкокинга были разработаны передовые технологии по конвер сии тяжелых нефтяных остатков (с последующей гидрокаталитической переработкой жидких продуктов), такие как APT, ЗД, АКО и др. Последние принято рассматривать как процессы облагораживания (подготовки) сырья для установок КК или ГК, имея в виду деметаллизацию и частичную декарбонизацию ТНО за счет осуществления адсорбции наиболее коксогенных и металлосодержащих компонентов — асфальто смолистых соединений и избирательного (легкого) термолитического их крекинга с образованием продуктов неглубокой конверсии — газойлевых дистиллятов. От сюда принято называть их в целом процессами термоадсорбционной деасфальтиза ции и деметаллизации (ТАДЦ) и рассматривать их как технологии, альтернативные сольвентным процессам деасфальтизации, находящие ограниченное применение для целей углубления переработки нефти [1].
Впроцессах ТАДЦ не образуется, в отличие от сольвентной деасфальтизации, такого трудноутилизируемого продукта, как асфальтит, а в отличие от флюидкокин га — малоценного топливного кокса, который полностью сжигается в регенераторе,
ивыделяющееся тепло используется для нагрева циркулирующего адсорбента и по лучения водяного пара. В отличие от флексикокинга в процессах ТАДЦ отсутствует блок газификации кокса и очистки флексигазов, требующих значительных капиталь ных и эксплуатационных затрат.
APT — процесс ТАДЦ ТНО с высокими коксуемостью и содержанием метал лов — разработан в США и пущен в 1983 г. в эксплуатацию мощностью 2,5 млн т/год. Процесс осуществляется на установке, аналогичной КК с лифт-реактором.
Адсорбент-теплоноситель имеет низкую удельную поверхность (10-15 м2/г), но большой диаметр пор (100-600 А); его готовят на основе каолиновых глин (арткат), относительно дешев (-800 $/т), выдерживает отложения металлов до 35 г/т. От работанный адсорбент можно регенерировать и извлечь никель и ванадий. В лифтреакторе процесса APT при температуре 480-530 °С и очень коротком времени контакта (0,5-5 с) сырья с адсорбентом наименее термостойкие асфальтосмолис тые и гетеросоединения — основные источники кокса и металлов — сорбируются на адсорбенте и крекируются. Закоксованный адсорбент восстанавливается в реге нераторе кипящего слоя, снабженном змеевиками для снятия избыточного тепла
ипроизводства водяного пара.
Впроцессе APT удаление металлов достигает свыше 95 %, а серы и азота — 50-85 %, при этом реакции крекинга протекают в минимальной степени. Примерный выход (в % об.) продуктов АЦТ при переработке гудрона составляет: газы С3-С 4 — 3-8, нафта — 13-17, легкий газойль (ЛГ) — 13-17, тяжелый газойль (ТГ) — 53-56
икокс 7-11 % мае. Смесь ЛГ и ТГ с незначительным содержанием металлов является качественным сырьем для КК или ГК [1].
20