
книги / Современные и перспективные термолитические процессы глубокой переработки нефтяного сырья
..pdfтарелки, а исходное (первичное) сырье с температурой 320-330 °С — на каскад ные тарелки, где оно контактирует с парами из реакторов. Поскольку первичное сырье нагрето до температуры паров, происходит их конденсация, где образуется жидкая фаза, которая стекает по тарелкам в низ колонны, и образуется вторичное сырье (смесь исходного сырья и рециркулята). Формируется коэффициент рецир куляции — отношение количества вторичного сырья к первичному. Такая схема работы низа колонны обусловливает максимальные коэффициенты рециркуляции 1,5-1,7, и даже более 2. Все отечественные установки работали, а многие работают
и в настоящее время с высокими значениями К — 1,5 и выше. Это было связано
стем, что рециркулирующие продукты улучшают тепловой режим реакционных камер, что приводит к некоторому снижению летучих веществ и повышению ме ханической прочности кокса. Но высокий коэффициент рециркуляции значительно увеличивает расход энергоносителей на тонну переработанного сырья. Поэтому большинство современных установок работают с коэффициентом рециркуляции на уровне 5-10% . Исключение составляют установки по производству кокса игольчатой структуры, работающие с высоким рециклом — 200 % и более. Осо бенно нецелесообразно присутствие во вторичном сырье фракций, выкипающих до 380—400 °С. В табл. 3.4 приведен состав первичного и вторичного сырья при работе установки с коэффициентом рециркуляции 70 % (1,7). Производительность установки 600 тыс. т сырья в год (установка 21-10/6 КНПЗ). Наличие во вторичном сырье фракций, выкипающих до 400 °С, которые не участвуют в формировании
конечного материального баланса и являются «балластом», конечно, приводит к повышенным расходам энергоносителей и снижает технико-экономические по казатели установки.
газ+бензин
газ+бензин |
газ+бензин |
-------- ► |
|
К-1 легкий
газойль^
тяжелый J b . газой^
|
I сырье |
|
100 кг/ч |
3 |
пары из |
|
реакторов1 |
Ъсырье
170 кг/ч
н.к. =280°С
Рисунок 3.14 — Формирование продуктов рециркуляции при различных режимах работы К-1
При производительности установки по сырью 600 тыс. т/год и коэффициенте ре циркуляции 1,7 приходится перекачивать, нагревать, охлаждать 420 тыс. т/год рецирку лирующих фракций, в т. ч. выкипающих до 380-400 °С, в количестве 126,8 тыс. т/год.
131
Таблица 3.4 — |
Состав первичного сырья, вторичного сырья и рециркулята УЗК-З |
|||||
|
КНПЗ при работе с коэффициентом рециркуляции 1,7 |
|
||||
|
|
|
Выход, % мае. |
|
|
|
Компонент |
I сырье |
II сырье |
Рециркулят |
|||
|
Комп. |
£ |
Комп. |
£ |
Комп. |
£ |
190-220 |
— |
— |
0,61 |
0,61 |
1,48 |
1,48 |
220-240 |
— |
— |
0,54 |
1,15 |
1,30 |
2,78 |
240-260 |
— |
— |
0,43 |
1,58 |
1,04 |
3,82 |
260-280 |
— |
— |
1,38 |
2,96 |
3,34 |
7,16 |
280-300 |
— |
— |
0,62 |
3,58 |
1,50 |
8 , 6 6 |
300-320 |
— |
— |
1,49 |
5,07 |
3,63 |
12,29 |
320-340 |
— |
— |
1,94 |
7,01 |
4,72 |
17,01 |
340-360 |
— |
— |
2,30 |
9,31 |
5,58 |
22,59 |
360-380 |
0,94 |
0,94 |
3,68 |
12,99 |
7,59 |
30,18 |
380-400 |
0,37 |
1,31 |
2,57 |
15,56 |
5,70 |
35,88 |
400-420 |
0 , 6 6 |
1,97 |
3,80 |
19,36 |
8,29 |
44,17 |
420-440 |
1,75 |
3,72 |
4,05 |
23,41 |
7,33 |
51,50 |
440-460 |
2,67 |
6,39 |
8,29 |
31,70 |
16,32 |
67,82 |
460-480 |
2,45 |
8,84 |
6,90 |
38,60 |
13,26 |
81,08 |
480-500 |
3,58 |
12,42 |
9,80 |
48,40 |
18,69 |
99,77 |
>500 |
87,58 |
1 0 0 , 0 0 |
51,60 |
1 0 0 , 0 0 |
0,23 |
1 0 0 , 0 0 |
Коэффициент рециркуляции можно значительно уменьшить, исключив контакт паров с первичным сырьем (рис. 3.14б). Такая схема позволяет снизить рециркуля цию до 20-25 %, но при этом количество рециркулята сложно регулировать, и его величина постоянно меняется. Это связано с тем, что при переводе сырья на оче редную камеру температура внизу колонны падает, и рециркуляция увеличивается, при выходе на нормальный режим рециркуляция снова уменьшается, и такой цикл повторяется каждый раз при переключении камер.
Расчеты показывают, что циклическое увеличение коэффициента рециркуляции и как следствие этого периодическое снижение производительности установки по сырью в целом за год уменьшает производительность установки по свежему сырью - н а 1 0 0 тыс. т/год.
Количеством и качеством рециркулирующих фракций можно управлять, уста новив выносную секцию к основной ректификационной колонне (К-0, рис. 3.14в). Первичное сырье поступает не в основную колонну, а в секцию К-0, наличие ко торой позволяет четко регулировать количество рециркулята и даже работать без него с нулевым коэффициентом рециркуляции. Кроме того, необходимо организовать более четкую ректификацию продуктов рециркуляции. Для этого под аккумулято ром необходимо смонтировать эффективные контактные устройства и подать на них
132
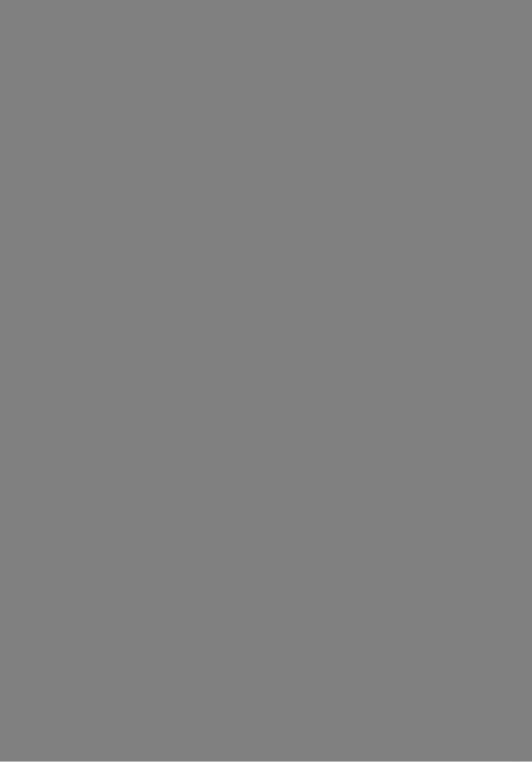
Использование сырьевой емкости К-0 позволило исключить контакт исходного сырья с продуктами коксования из камер Р-1-Р-4 и регулировать количество рециркулята в широких пределах (от 0 и выше) путем изменения его подачи в К-0. При производительности по свежему сырью 900 тыс. т/год и количестве рециркулята 10 % (90 тыс. т/год) загрузка печей вторичного сырья составит 990 тыс. т/год.
При модернизации установки были реализованы следующие основные техно логические решения:
—смонтирована и обвязана промежуточная емкость для вторичного сырья К-0;
—установлен и обвязан насос для перекачки нижнего циркуляционного орошения (НЦО) колонны К-1;
—установлены теплообменники на линии НЦО и тяжелого газойля коксования;
—смонтирован и обвязан горячий насос для откачки остатка с низа колонны К-1;
—увеличена поверхность конденсаторов-холодильников на дистилляте колонны К-1.
Втабл. 3.5 представлены сравнительные данные по материальным балансам установки до модернизации и после модернизации. Производительность установки по сырью была увеличена с 600 (по проекту фактически с 450) до 900 тыс. т/год, выработка кокса — со 126 до 171 тыс. т/год.
Таблица 3.5 — Материальный баланс процесса коксования гудрона до и после модернизации
|
Выход |
||
Продукт |
До модернизации |
После модернизации |
|
рециркуляция 60 %, |
рециркуляция 1 0 %, |
||
|
|||
|
тыс. т/год |
тыс. т/год |
|
|
Взято |
|
|
Сырье |
по проекту 600,0 |
900,0 |
|
фактически 450,0 |
|
||
|
|
||
|
Получено |
|
|
Газ по С4 |
58,2 |
79,0 |
|
Бензин (н.к. — 180 °С) |
79,8 |
108,0 |
|
Легкий газойль (180-350 °С) |
139,2 |
186,0 |
|
Тяжелый газойль (350 °С — к.к.) |
184,8 |
347,0 |
|
Кокс |
126,0 |
171,0 |
|
Потери |
1 2 , 0 |
9,0 |
|
Итого |
600,0 |
900,0 |
Все получаемые продукты полностью соответствуют требованиям, предъявляе мым к показателям качества, действующим на НПЗ. Рекламаций по качеству кокса в течение 4 лет эксплуатации установки по новой технологии ни по содержанию летучих, ни по другим показателям не было.
Технология запатентована [59,60], и в настоящее время ведется проектирование двух крупных установок мощностью 1,2 млн т сырья в год на ОАО «Уфанефтехим»
134
и ОАО «Уфимский НПЗ». Обе установки проектируются по технологии с выносной секцией, ректификацией продуктов рециркуляции и монтажом высокотехнологичной шиберной системы открытия-закрытия коксовых камер.
За рубежом также широко проводится работа по снижению рециркуляции. В ос новном они связаны также с модернизацией основной ректификационной колонны. На рис. 3.16 и 3.17 показаны схемы низа фракционирующей колонны по технологии фирмы «Foster wheeler» и «Conoco Phillips».
Надо отметить следующие недостатки схемы работы низа колонны по техноло гии «Foster wheeler»:
1.Маловероятно, что такая схема обеспечит снижение рецикла до 5-7 % (сверх низкий рецикл).
2.Рецикл формируется за счет подачи кулинга и естественного снижения темпера туры, кулинг — величина непостоянная, и рецикл будет меняться.
3.При переводе реакторов температура в колонне падает, что также приводит к из менению рецикла.
4.Схема не исключает возможности попадания коксовых частиц на прием печных насосов, что ускоряет закоксовывание печей.
5.При организации безотходной технологии (возврат продуктов с узла улавлива ния) произойдет снижение производительности по сырью или увеличение на грузки на печь и теплонапряженности поверхности трубного экрана.
Камера распыления промывного газойля
Промывной
газойль
Пары с верха кокс, камеры
Тепловой |
|
|
|
||
|
экран |
' |
Исключает |
|
|
|
|
|
|||
|
|
— |
разбрызгивание |
|
|
|
|
|
свежего сырья |
Свежее |
|
|
|
|
|
сырье |
|
Сырье |
|
|
Удаление |
||
|
|
коксовой мелочи |
|||
в печь |
■ |
С |
|||
„на ходу" |
|||||
|
|||||
|
|
|
Рисунок 3.16 — Схема работы низа колонны по технологии «Foster wheeler»
Схема фирмы «Conoco Phillips» (рис. 3.17) имеет все недостатки, присущие ко лонне фирмы «Foster wheeler». Наличие устройства для улавливания кокса проблемы не решает, так как объем его небольшой и нет условий для «отстаивания» кокса.
135
Рисунок 3.17 — Схема ректификационной колонны УЗК «Conoco Phillips»
В заключение отметим, что схема работы установки с выносной секцией К-0 позволяет:
—гарантированно регулировать количество и фракционный состав рециркулирую щих фракций;
—исключить попадание коксовых частиц на прием печных насосов;
—стабилизировать режим работы реакторного блока в период переключения кок совых камер;
—исключить колебания температурного режима печи и реакторов;
—осуществить возврат продуктов реакции в переработку без снижения произво дительности по свежему сырью;
—регулировать качество тяжелого газойля по концу кипения и коксуемости;
—обеспечить минимальный расход энергоносителей на тонну переработанного сырья;
—в перспективе позволяет вырабатывать два сорта кокса [60].
3.5.Углубление переработки нефти
коксованием остатков глубоковакуумной перегонки нефти
Ранее (§ 1.1.1) было отмечено, что целевым назначением современных и перспек тивных процессов замедленного коксования является производство кроме нефтяного кокса максимального количества дистиллятов — полупродуктов для последующей гидрокаталитической переработки в ценные компоненты моторных топлив, тем са мым существенное углубление переработки нефти.
По показателю глубины переработки нефти (ГПН) отечественная нефтеперера ботка (~72 %) существенно отстает не только от США (~93 %) и западноевропейских
136
стран (~87 %), но и от среднемирового уровня (~74 %). Необходимость дальнейшего повышения ГПН тесно связана с актуальнейшей глобальной проблемой экономики наступившего столетия — истощением извлекаемых запасов нефти. По оценкам эк спертов, в случае сохранения нынешнего уровня мировой добычи (~3,5 млрд т/г) истощение извлекаемых запасов нефти в мире (~140 млрд т) произойдет примерно за 40 лет, а в России — за 20 лет [1-3]. Запасы нефти (~7 млрд т) за последние два десятилетия (после распада СССР) у нас в стране практически не восполнялись. К тому же в ближайшие годы мы обречены работать с трудноизвлекаемыми и сильно обводненными запасами [2]. Таким образом, проблема дефицита нефти для нашей страны стала реальной. Но тем не менее, как и в годы «нефтяного бума», Россия продолжает экспортировать ее в больших объемах (более половины добычи), а не которые средства массовой информации уверяют общество, что нефти хватит на все столетие, и без долларов не останемся.
В условиях реально наступившего дефицита нефти и при наличии в достаточных количествах природного газа (в РФ Уз от мировых запасов) для сжигания в топках котлов, существующая практика нерационального расходования нефтяных ресурсов
и«мазутная» политика в энергетике не могут быть оправданы. Нефть должна пол ностью и без остатка перерабатываться с получением только высококачественных
иэкологически чистых нефтепродуктов, прежде всего моторных топлив, высокоин дексных смазочных масел и использоваться в качестве сырья для нефтехимии.
Опроблеме углубления переработки нефти официально говорится и прини маются решения более 20 лет. Однако результаты по их реализации исключитель но скромны. Здесь уместны слова бывшего министра Миннефтехимпрома СССР
В. Н. Лемаева: «В нашей стране утратили понимание, для чего добывается углево дородные сырье — нефть и газ. У руководства страны сложилось впечатление, что мы обладаем такими ресурсами нефти и газа, которые обеспечат нам десятилетиями безбедное существование. Мы не сделали ни одного шага в развитии новых техно логий в области нефтепереработки и нефтехимии».
Решение застарелой проблемы повышения ГПН для России невозможно без разработки и внедрения в производство технологических процессов переработки тяжелых нефтяных остатков (ТНО) — мазутов, гудронов и в перспективе битуми нозных нефтей, являющихся исключительно трудноперерабатываемыми видами сы рья по причине их высокой коксогенности и большого содержания в них металлов (никеля, ванадия и др.) — ядов для катализаторов. В этой связи каталитическая или гидрокаталитическая переработка ТНО рентабельно возможна лишь после их пред варительной деасфальтизации и деметаллизации известными в мировой нефтепере работке некаталитическими процессами, такими как сольвентные или термоконтак тные (термоадсорбционные). Однако сольвентные процессы типа «Демекс» фирмы «ЮОП», «РОЗЕ» фирмы «Керр-Макги» и отечественные пропановой деасфальти зации, применяемые в производствах смазочных масел) характеризуются высокой энергоемкостью, повышенными капитальными и эксплуатационными затратами; они приводят к образованию еще более тяжелого асфальтового остатка, чем гудроны. Термоконтактные процессы (APT, ЗД, АКО, ЭТКК и др. (см. § 1.3) в настоящее время в России не освоены и не рассматриваются в «Основных положениях энергетической стратегии страны» как перспективные для внедрения их в нефтепереработку.
137
В последние годы на ряде НПЗ страны начато строительство новых УЗК по переработке типовых вакуумных остатков, выкипающих свыше 500 °С. Однако на НПЗ ряда зарубежных развитых стран мира (например, в США) освоили техноло гию глубоковакуумной перегонки мазутов с получением глубоковакуумных газойлей с последующей их каталитической переработкой в моторные топлива, а гудроны, выкипающие свыше 500 °С (вплоть до 600 °С) стали подвергаться коксованию. В результате существенно возрастает ГПН и улучшаются технико-экономические показатели УЗК.
В табл. 3.6 приведены данные по качеству различных российских нефтей, вакуум ных остатков и получаемых из них коксов. Экспериментальные данные по коксуемос ти, выходу кокса на остаток и нефть, отношению выхода кокса на коксуемость и дру гим физико-химическим свойствам ТНО, выкипающим при температурах 480-590 °С, из западносибирской и арланской нефтей приведены в табл. 3.7. На рис. 3.18 представлены зависимости выхода кокса от коксуемости ТНО различных нефтей.
|
Коксуемость, % мае. |
|
|
• |
Мангышлак |
о Гюртянская |
■ щ аимская |
е |
-Арлан |
А Грозненская |
Смесь западносибирских |
х -Котур-Тепе |
• Самотлор |
Варьеганская |
|
о |
-Русская |
А Советско-Соснинская |
|
Рисунок 3.18 — |
Влияние коксуемости тяжелых нефтяных остатков различных нефтей |
||
|
|
на выход кокса из них: |
|
1 — остатки мангышлакской нефти; 2 — |
остатки арланской нефти; 3 — остатки западносибирских нефтей |
||
|
и малосернистых нефтей СССР |
138
Таблица 3.6 — Характеристика некоторых российских нефтей, остатков вакуумной их перегонки и коксов
Нефть
Наименование
показателей
Плотность, г/см3 Содержание, %:
S
V
Ni
Выход на нефть, % Плотность, г/см3
Коксуемость, % Содержание, %:
S
V
Ni
Выход на гудрон Содержание, %:
S
V
Ni
Западно масибирская лосернистая 0,8395
Смесь Сургут + южнобалыкская
0,8742
Правдинская |
Смесь нижневартов ских |
Самотлорская |
Советскососнинская |
Смесь мегионской и ватинской |
Шаимская |
Западно сибирская сернистая |
Варьеганская |
Ноябрьская |
0,8523 |
0,8410 |
0,8420 |
0,8386 |
0,8378 |
0,8270 |
0,8556 |
0,8269 |
0,8410 |
0,45 |
1,62 |
0,72 |
1 , 0 2 |
0,98 |
0,97 |
1,09 |
0,45 |
1,48 |
0,45 |
0,56 |
||||
— |
0,0055 |
0 , 0 0 1 1 |
0,0013 |
0,0017 |
0,0008 |
0,0015 |
— |
— |
0,00053 |
0 , 0 0 1 2 |
||||
— |
0,00067 |
0,00014 |
0,0008 |
0,0008 |
0,0005 |
0,0009 |
— |
— |
0 , 0 0 1 0 |
0 , 0 0 1 0 |
||||
|
|
|
|
|
Остатки (гудроны >500° С) |
|
|
|
|
|
||||
16,2 |
33,5 |
24,4 |
16,3 |
2 |
0 |
, 0 |
17,0 |
18,7 |
18,0 |
— |
13,7 |
17,9 |
||
0,9968 |
1,0014 |
0,9731 |
0,9987 |
0,9993 |
0,9990 |
0,9939 |
0,9702 |
0,9811 |
0,9924 |
1,0074 |
||||
16,5 |
16,6 |
13,8 |
15,9 |
13,5 |
15,0 |
13,9 |
1 1 , 2 |
— |
13,6 |
17,8 |
||||
1,29 |
3,0 |
1 , 8 6 |
2,40 |
2,25 |
1,95 |
2,26 |
1,26 |
2,23 |
1,30 |
1,52 |
||||
— |
0,0155 |
0,0056 |
0,0090 |
0,0080 |
0,0045 |
0 , 0 1 0 |
0,0013 |
0,0083 |
0,0047 |
0,0070 |
||||
— |
0,0023 |
0 , 0 |
0 |
1 0 |
0,0060 |
0,0045 |
0,0030 |
0,0050 |
0 , 0 0 1 2 |
0,0035 |
0,0051 |
0,0052 |
||
|
|
|
|
|
|
Кокс |
|
|
|
|
|
|
||
25,4 |
26,6 |
2 |
2 |
, 0 |
23,0 |
2 |
1 |
, 8 |
23,0 |
2 2 , 6 |
19,0 |
2 0 , 0 |
22,7 |
26,0 |
1,29 |
3,42 |
3,10 |
2 , 1 0 |
2 |
, 1 |
0 |
1,80 |
2,16 |
1,63 |
2,4 |
1,42 |
1,67 |
||
0 , 0 1 |
0,06 |
0,024 |
0,035 |
0,035 |
0,019 |
0,0420 |
0,0070 |
0,0400 |
0 , 0 2 0 0 |
0,025 |
||||
— |
0,0080 |
0,0036 |
0,018 |
0 , 0 2 1 |
0,018 |
0,0214 |
0,006 |
0,015 |
0 , 0 2 1 0 |
0 , 0 2 0 |
Таблица 3.7 — Характеристика глубоковакуумных остатков
западносибирской и арланской нефтей |
|
|
|
|||
Показатели |
Остатки нефтей, выкипающие выше, °С |
|||||
смеси западносибирских |
|
арланской |
|
|||
|
480 |
540 |
590 |
510 |
540 |
580 |
Выход на нефть, % мае. |
27,0 |
16,7 |
1 2 , 6 |
30,0 |
26,5 |
2 1 , 0 |
Плотность, кг/м3 |
986 |
1014 |
1029 |
1050 |
1051 |
1062 |
Коксуемость |
|
|
|
|
|
|
по Конрадсону, % мае. |
12,5 |
18,4 |
23,1 |
26,05 |
27,0 |
28,0 |
Зольность, % мае. |
0,04 |
0,05 |
0 , 1 2 |
0 , 1 2 |
0,13 |
0,17 |
Температура размягчения |
|
|
|
|
|
|
по КиШ, °С |
26 |
37 |
50,5 |
61 |
67,5 |
8 6 |
Вязкость кинематическая, |
|
|
|
|
|
|
сСт, при, °С |
|
|
|
|
|
|
150 |
— |
160 |
274 |
— |
1300 |
4796 |
2 0 0 |
— |
37 |
58 |
— |
150 |
334 |
Содержание металлов, |
|
|
|
|
|
|
% мае. • 1 0 ' 4 |
|
|
|
|
|
|
ванадий |
1 2 0 |
170 |
240 |
475 |
530 |
650 |
никель |
46 |
71 |
90 |
225 |
250 |
310 |
Групповой химический состав, |
|
|
|
|
|
|
% мае.: |
|
|
|
|
|
|
парафино-нафтеновые |
13,9 |
7,7 |
5,5 |
5,2 |
4,1 |
3,5 |
легкая ароматика |
11,5 |
1 0 , 0 |
8 , 0 |
7,0 |
5,9 |
4,6 |
средняя ароматика |
8 , 0 |
7,2 |
5,8 |
5,8 |
5,8 |
4,5 |
тяжелая ароматика |
35,2 |
35,3 |
36,5 |
34,5 |
34,0 |
33,0 |
смолы I |
10,9 |
12,4 |
12,4 |
12,5 |
12,4 |
13,5 |
смолы II |
16,0 |
19,9 |
2 1 , 8 |
17,8 |
19,8 |
20,9 |
асфальтены |
4,5 |
7,5 |
1 0 , 0 |
17,2 |
18,0 |
2 0 , 0 |
Выход кокса на остаток, |
|
28,9 |
31,5 |
— |
36,0 |
38,6 |
% мае. |
1 2 |
|||||
|
|
|
|
|
|
|
Отношение: выход кокса |
|
|
1,5 |
— |
1,37 |
1,37 |
к коксуемости |
1 , 8 |
1 , 6 |
||||
|
|
|
|
|
|
|
Выход кокса на нефть, % мае. |
3,2 |
4,8 |
4,0 |
— |
9,5 |
8 , 1 |
Из представленных данных вытекает следующий однозначный вывод: с повы шением глубины вакуумного отбора нефтяного остатка:
—симбатно возрастает коксуемость по Конрадсону;
—увеличивается выход кокса на остаток;
—снижается отношение выхода кокса к коксуемости ТНО;
—уменьшается выход остатка на исходную нефть (рис. 3.19).
140