
книги / Современные и перспективные термолитические процессы глубокой переработки нефтяного сырья
..pdf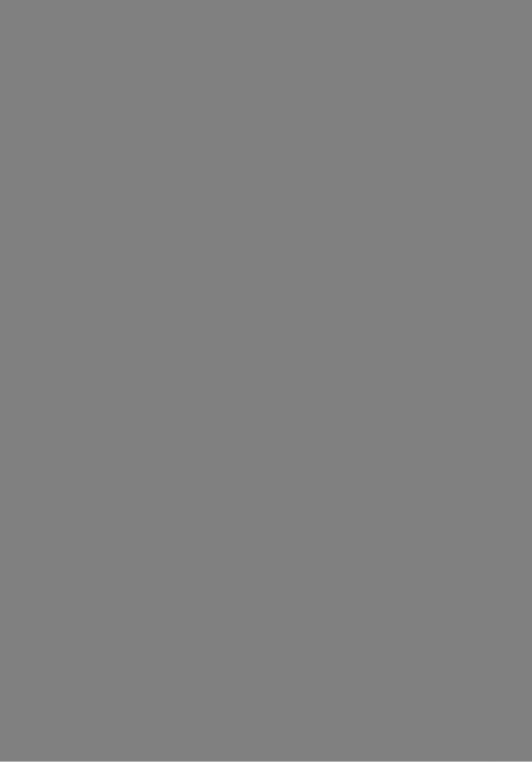
поверхности трубы — «Spalling» метод. Змеевики нагрева вторичного сырья оснаща ют термопарами, после пуска печи и вывода ее на режим следят за их показаниями. При повышении температуры стенки трубы на 50-60 °С приступают к чистке змее виков. Чтобы снижение производительности по свежему сырью было минимальным, данный метод используют на многопоточных печах (при наличии 2 потоков произ водительность упадет на 30-40 %). Очистка начинается в одном змеевике, второй работает в режиме максимальной производительности. К очистке приступают через 4-5 ч после постановки очередной камеры на режим коксования. Снижают расход сырья в очищаемых змеевиках и увеличивают расход воды или водяного пара, при этом необходимо следить, чтобы температура на выходе и давление на входе изме нялись в рамках технологического режима. Таким образом, расход сырья снижается до 0, расход воды до 3—4 т. Кокс начинает прогреваться, растрескивается и потоком пара выдувается по схеме в заполняемую камеру. На рис. 3.43 показана картограмма изменения температуры стенки труб в процессе эксплуатации установки, на которой видны периоды чистки труб от кокса. Процедура обычно проводится раз в 3-4 меся ца и, таким образом, пробеги установок достигают 2 и более лет, имеются сведения о пробеге установки в 4 года.
Рисунок 3.43 — Картограмма изменения температуры стенок труб печи одной из установок
замедленного коксования в процессе коксования и очистки змеевиков от кокса методом отслаивания 1
1 «Coker Process Training» — Presented by Evan Hyde, Becht Engineering Co. Jnc. March 10. 2008.
172
Недостатком метода является отсутствие контроля за чистотой очистки. И пос кольку после режима отслаивания коксовые частички удаляются не полностью, то существует необходимость через 4-5 чисток методом отслоения осуществить гид ромеханическую чистку.
3.10.Современные и перспективные печи установок замедленного коксования
От интенсификации работы печи в любом процессе зависит достижение макси мальной рентабельности технологической установки за счет снижения эксплуатаци онных затрат путем снижения расхода энергоносителей, обеспечение выполнения все более жестких природоохранных требований, обеспечение высокой надежности эксплуатации технологической установки.
Печь в процессе замедленного коксования (ПЗК) является основным аппаратом, определяющим межремонтный пробег установок, иногда печь называют «сердцем установки», поскольку при коксовании печи приходится останавливать всю уста новку. Конструкции печей первых установок имели низкий КПД, короткие меж ремонтные пробеги — 20-25 сут. Современные печи имеют КПД на уровне 90 %, и их межремонтные пробеги достигают 4 лет.
Одним из мировых лидеров по конструированию нефтезаводских печей, включая печи УЗК и висбрекинга, является фирма «Foster Wheeler», которая сконструировала и внедрила более 500 печей в 50 странах мира [71].
Несмотря на то что новых установок в России за последние 20 с лишним лет не строилось, научные и инженерные разработки проводились достаточно интенсивно (см. § 2.5.) и разработаны научные основы технологии конструирования печей УЗК и висбрекинга.
Технология включает разделы по тепловому и гидравлическому расчету зме евиков, выбору горелок, определению размеров топки, гидравлическому расчету змеевиков, общего КПД печи.
Расчет гидравлического и теплового режима включает:
—подъем температуры в змеевике от входа до выхода;
—измерение объема паровой и жидкой фаз с ростом температуры, включая изме нение соотношения жидкость : пар за счет испарения и химических реакций;
—расчет линейных скоростей по длине змеевика;
—перепад давления по длине змеевика;
—величину объемного газосодержания, структуру потока;
—рассчитывается внешний подвод тепла и температура стенки внешней поверх ности труб;
—рассчитывается время пребывания реакционной смеси по длине змеевика;
—рассчитываются режим течения газожидкостного потока и режим, исключающий возникновение дисперсной формы течения двухфазного потока.
Для проведения расчетов, разумеется, необходимо соответствующее програм
мное обеспечение.
Для разработки математических моделей и алгоритмов для проведения расчетов по перечисленным параметрам необходимо знать общие принципы работы печей.
173
Как работает печь установки замедленного коксования. Печь УЗК состоит из радиантной секции, в которой выделяется тепло, передаваемое нагреваемой среде за счет сжигания топлива в горелках и конвективной секции, в которой имеет место дополнительный нагрев за счет передачи тепла дымовых газов, выходящих из ради антной секции печи и перед выбросом в атмосферу проходящих через конвективную секцию. На зарубежных УЗК в большинстве случаев первичное сырье нагревается только в теплообменниках и через конвективную секцию не прокачивается. На оте чественных УЗК первичное сырье обычно после теплообменников дополнительно подогревается в конвективной секции печи. Оба решения имеют и преимущества, и недостатки. При дополнительном подогреве первичного сырья в камере конвек ции достигается более высокая температура подогрева и, как следствие, более высо кая температура в низу колонны и на входе в реакционную зону печи (температура вторичного сырья на входе в печь). Но при этом возможны случаи закоксовывания змеевиков первичного сырья. Если сырье поступает на установку в зависимости от уровня в основной ректификационной колонне и при повышении уровня в колонне подача первичного сырья уменьшится или даже прекратится, а поток тепла не сни зится, так как поток вторичного сырья не снижается и форсунки горят в обычном режиме, это может привести к закоксовыванию змеевика нагрева первичного сырья. Подогрев сырья только в теплообменниках обусловливает пониженную температуру в низу колонны и на входе в печь, что увеличивает размеры печи, создает более вы сокие перепады давления, более длительное время пребывания реакционной смеси.
Механизм теплопередачи. Механизм передачи тепла в каждой секции печи прин ципиально различен.
В радиантной секции печи тепло передается за счет излучения в соответствии с законом Стефана — Больцмана
Q = k b ( T 4- t 4),
где Q — тепло, передаваемое от единицы площади поверхности за один час (эта величина называется «тепловой поток»); к — постоянная Стефана — Больцмана, характеризующая излучение абсолютно черного тела; b — параметр, учитываю щий отличие теплового излучения от излучения абсолютно черного тела и прини мающий во внимание геометрию радиационной секции и состав дымовых газов; Т — средняя абсолютная температура дымовых газов в радиационной секции; t — средняя абсолютная температура теплообменных поверхностей в радиаци онной секции.
Как следует из приведенной формулы, для заданной геометрии радиационной секции тепловой поток весьма сильно зависит от разницы температур.
В конвекционной секции выходящие из радиационной секции печи дымовые газы охлаждаются в конвективной секции, где передача тепла технологической сре де осуществляется посредством механизма конвекции. Теплопередача описывается уравнением конвективного теплообмена:
Q = hc( T - t \
174
где Q — тепло, передаваемое от единицы площади поверхности за один час (теп ловой поток); hc— коэффициент конвективного теплообмена; Т — температура дымовых газов; t — температура металла труб.
Режимы работы печи. Тепло, выделяющееся при сжигании топлива (мазута или топливного газа), передается змеевику печи посредством радиационного или конвективного теплообмена, описываемых вышеприведенными уравнениями. На рис. 3.44 показано, как меняется давление дымовых газов внутри печи с естествен ной тягой. При правильной работе печи все ее внутренние компоненты находятся под отрицательным давлением. Такое отрицательное давление (разрежение) особенно важно с точки зрения обеспечения безопасности, так как в любом случае необходимо исключить возможность выброса пламени или раскаленных дымовых газов наружу. Если печь эксплуатируется в режиме с естественной тягой, то необходимую тягу для поддержания в системе надлежащего разрежения и преодоления перепада давления по всей длине тракта дымовых газов обеспечивает правильный выбор высоты дымо вой трубы. В печах, работающих с принудительной тягой, для создания требуемой тяги используется вытяжной вентилятор, однако профиль давления в них такой же, как и при естественной тяге.
Поскольку вся печь работает в условиях разрежения, с целью сведения к миниму му подвода воздуха на уровне свода печи обычно задается отрицательное давление порядка 3 мм водного столба. В этой точке печи уровень разрежения минимален. Давление в этой зоне регулируется либо установленным на выходе печи шибером, либо с помощью средств управления вытяжным вентилятором в зависимости от конструкции.
Горячие дымовые газы имеют меньшую плотность и поэтому стремятся под няться наверх, в связи с чем увеличивается тяга на уровне пода печи. Этот эффект используется для создания потока воздуха, необходимого для сжигания топлива через горелки.
Подъем дымовых газов обеспечивает хорошее перемешивание топлива с возду хом, что необходимо для нормального горения.
Перепад давления при проходе через конвективную секцию уравновешивается тягой, создаваемой дымовой трубой или вытяжным вентилятором, в зависимости от типа печи. Обычно он рассчитывается с запасом, чтобы печь могла работать с более высоким расходом дымовых газов.
Для нормальной работы печи необходимо отрегулировать положение шибера, на ходящегося на дымовой трубе либо на вытяжном вентиляторе, таким образом, чтобы обеспечить необходимую тягу на уровне свода, и установить воздушные регистры горелок так, чтобы поддерживать избыток воздуха горения на расчетном уровне.
Управлять расходом воздуха горения только с помощью шибера дымовой трубы небезопасно. Это связано с тем, что частичное закрытие шибера с целью уменьшения перепада давления на уровне горелок может привести к появлению положитель ного давления на уровне свода печи, в результате чего станет возможна протечка раскаленных дымовых газов через корпус печи, связанная с большим риском для персонала.
Всистемах со сбалансированной тягой (т. е. когда для выброса дымовых газов
ватмосферу применяется вытяжной вентилятор) печь работает по аналогичному
175
принципу. Необходимый для горения воздух подается нагнетающим вентилятором, который обеспечивает компенсацию перепада давления на горелках, в газоходах и в системе предварительного подогрева воздуха (если она применяется). Величина тяги на уровне свода поддерживается путем правильной установки регулирующего шибера вытяжного вентилятора.
Ш и б е р -------
|
Тяга на выходе |
|
радиационной |
х |
секции Ro 0,05-0,1 |
X |
дюйм вод.ст. |
о |
|
К |
|
X |
|
л |
|
X |
|
9
Рч
Горелки
Рисунок 3.44 — Изменение давления дымовых газов внутри печи с естественной тягой
КПД печи. Важной рабочей характеристикой печи является ее КПД (т|), который определяется как отношение
где Qa — полезное теплопоглощение; Qb— тепловыделение на горелках. Разница между Qaи Qbпредставляет собой потери тепла, которые, очевидно, будут выше для печей с более низким КПД (а — радиационные тепловые потери через стены печи; b — теплопотери, обусловленные уходом дымовых газов в атмосферу).
176
Нормальная величина тепловых потерь через стены печи обычно составляет 1,5-2,0 % общего тепловыделения. Унос тепла дымовыми газами гораздо значитель нее и зависит от эффективности работы печей. Для иллюстрации влияния парамет ров работы печи приведем пример оценки избытка воздуха на экономические пока затели. Мощность печи 52 Гкал/ч, в качестве топлива используется мазут с низшей теплотворной способностью 9500 ккал/ч. Печь работает с 20 % избытком воздуха, температура дымовых газов на выходе из печи — 400 °С. КПД такой печи 81,5 %. При увеличении избытка воздуха до 40 % КПД снизится до 78,7 %. Расчет экономики сведен в табл. 3.11.
Таблица 3.11 — Влияние избытка воздуха на экономику работы печи |
|
||
Показатель |
Ед. изм. |
Избыток |
Избыток |
воздуха 2 0 % |
воздуха 2 0 % |
||
Мощность установки |
т/год |
Около 4 000 000 |
|
Полезное теплопоглощение |
Гкал/ч |
52 |
52 |
Температура выходящих дымовых газов |
°С |
400 |
400 |
Потери в радиантной секции |
% |
1,5 |
1,5 |
Общий КПД |
% |
81,5 |
78,7 |
Чистый КПД |
% |
79,0 |
77,2 |
Тепловыделение |
Гкал/ч |
65,82 |
67,36 |
Разница значений тепловыделения |
Гкал/ч |
1,54 |
|
Экономия мазута |
кг/ч |
162 |
|
Ежегодная экономия (8000 ч работы в году) |
т/год |
1296 |
|
Стоимость топочного мазута |
евро/кг |
0 |
, 2 |
Ежегодная экономия |
евро |
259 200 |
Таким образом, количество подаваемого воздуха оказывает существенное влия ние на КПД печи. Обычно этот показатель характеризуется коэффициентом избыт ка воздуха, величину которого необходимо поддерживать на оптимальном уровне. Слишком низкий коэффициент избытка воздуха приведет к неполному сгоранию в радиантной секции и дожит будет проходить в конвекционной секции, что может привести к разрушению труб в камере конвекции, загрязнению теплообменной по верхности сажевыми отложениями. Весьма эффективным методом повышения КПД печи является подогрев воздуха. Результаты проиллюстрированы в табл. 3.12.
Таблица 3.12 — Влияние подогрева воздуха на режим работы печи |
|
||
Показатель |
Ед. изм. |
В отсутствие |
С воздухо |
воздухоподогревателя |
подогревателем |
Мощность установки |
бар./сут |
Полезное тепло |
Гкал/ч |
кпд |
% |
Тепло от сжигания топлива |
Гкал/ч |
52 |
70 000 |
52 |
|
72 |
90 |
72,22 |
57,78 |
177
Как видно из таблицы, наличие воздухоподогревателя приводит к значительному увеличению КПД и снижению расхода топлива.
Тепловой поток на единицу поверхности (теплонапряжение). Очевидно, что чем выше тепловой поток, тем меньшая площадь теплообменных поверхностей тре буется для работы печи и, следовательно, тем более экономична ее конструкция. Обычно расчетный тепловой поток зависит от типа нагреваемой среды и максималь но допустимой температуры поверхности.
Тепловой поток повышает температуру среды, контактирующей с внутренней поверхностью стенки трубы, в соответствии со следующей формулой:
где АТ — разность температур поверхности и основного объема среды; 0 — теп ловой поток; hjo— внутренний коэффициент теплопроводности нагреваемой среды.
Кроме повышения температуры поверхности АГ, повышение температуры труб обусловлено также тепловым сопротивлением металла змеевика. Оно описывается следующей формулой:
где АГ — разность температур металла на внутренней и наружной поверхностях трубы; 0 — тепловой поток; И— толщина стенки трубы, к — коэффициент теп лопроводности металла трубы.
Повышение теплового потока непосредственно ведет к повышению температуры поверхности основного металла трубы. Это может стать ограничивающим фактором, так как чрезмерно высокая температура может привести к разложению нагреваемой среды или повлиять на прочностные свойства труб.
Величина теплового потока, используемая в расчетах печей, влияет на среднюю температуру дымовых газов в радиационной секции и температуру перевальной стены, а следовательно, влияет и на эффективность радиационного теплообмена. К примеру, чем больше радиационный тепловой поток и чем более экономичной является конструкция радиационной секции, тем меньше будет ее тепловой КПД и наоборот.
Высокий общий КПД позволяет использовать больше тепла в конвективной сек ции. Высокий общий КПД означает меньшее различие температур поступающей нагреваемой среды и дымовых газов на выходе из конвективной секции, в связи с чем потребуется большая теплообменная поверхность. Эти дополнительные затраты, обусловленные монтажом дополнительных теплообменных элементов в конвектив ной секции, обычно с лихвой компенсируются экономией топлива.
Величина теплового потока играет большую роль при проектировании печи. Дело в том, что она зависит от целого ряда факторов, свойств нагреваемой среды, конструкции печи и типа подвода тепла (односторонний, двухсторонний режим), допустимой температуры нагрева и т. д. Влияние многих из этих факторов широко описано в литературе.
178
Гораздо меньше внимания уделяется решению так называемой «внутренней за дачи», особенно если процесс подъема температуры нагреваемой среды приводит к изменению ее фазового состояния и изменению структуры двухфазного потока. Изменение структуры нагреваемого газожидкостного потока приводит к значитель ному изменению процесса теплообмена и возникновению кризисных явлений при передаче тепла от стенки теплопередающей поверхности (см. раздел 2.5), где пока зано, что изменение коэффициента теплообмена в змеевиках УЗК может измениться в несколько раз. Поэтому величина теплового потока не должна быть постоянной по всему змеевику. Кроме того, змеевик необходимо конструировать таким образом, чтобы исключить возникновение кризисов теплообмена первого и второго рода. На пример, снижением скоростей в выходных трубах путем перехода на больший диа метр выходных труб или снижения теплового потока при нагреве быстро распадаю щихся продуктов, например асфальтов и гудронов с высокими коксовыми числами.
Закоксовывание внутренней поверхности змеевиков обусловлено целым ря дом факторов — наличием кризисных явлений теплообмена, перегревом пристен ного слоя при набросе пламени (зализывании) на поверхность труб, нагревом сырья
снизкой коллоидной стабильностью (обычно это сырье с высоким содержанием па рафинов) [39].
Печи старой конструкции часто проектировались с весьма низкой скоростью движения среды внутри змеевиков, так как это позволяет уменьшить перепад дав ления на печи. Этот принципиально неправильный подход стал главной причиной неэффективной работы печей, особенно в варианте эксплуатации при сниженной нагрузке. Во многих случаях повышение производительности смягчало остроту проб лемы, даже несмотря на увеличившуюся нагрузку.
Уменьшение объема выбросов в атмосферу. Производительность многих нефтеперерабатывающих и нефтехимических комплексов ограничивается общим объемом выбросов, которые разрешается выбрасывать в атмосферу в соответствии
сдействующим законодательством.
Снижение объема выбросов может быть достигнуто повышением КПД печи, так как при этом уменьшается тепловыделение и объем сжигаемого топлива, и заме ной имеющихся горелок более современными, с низким уровнем генерации окислов азота NOx.
Из всех выбросов особенно важны NOx и SOr Если объем выбросов S02 не посредственно зависит от качества топлива (и, следовательно, борьба с этим видом выбросов производится путем очистки топлива и не связана с применяемыми го релками), то количество образующихся при горении топлива NOx зависит от типа горелки.
Последние достижения в технологии сжигания топлив позволяют снизить объем выбросов NOx в сравнении с горелками старой конструкции более чем на 50 %. По вышение КПД печи также вносит вклад в дальнейшее уменьшение содержания NOx на выходе дымовой трубы. Пример сокращения объема выбросов NOx при работе печи прямого нагрева с тепловой нагрузкой 52 Гкал/ч после надлежащей реконст рукции приводится в табл. 3.13.
Наиболее распространенные и перспективные конструкции печей УЗК. Все
первые установки ЗК, построенные в СССР в 60-70-е гг. прошлого века, были обо
179
рудованы печами «шатрового типа». На рис. 3.45 представлены потоки первичного сырья (I с), вторичного сырья (II с) и место установки датчиков измерения парамет ров работы печей в период обследования. Некоторые результаты приводились выше (см. раздел 2.5).
Таблица 3.13 — Объемы выбросов NOx при работе печи |
|
||||
с модернизированной горелкой |
|
|
|||
|
|
|
Горелки |
Горелки |
|
Показатель |
Ед. изм. |
Обычные |
с низким уровнем |
||
с низким |
|||||
|
|
горелки |
уровнем NOx |
NOx с воздухопо |
|
|
|
|
догревателем |
||
|
|
|
|
||
Мощность установки |
бар./сут |
|
70000 |
|
|
т/год |
приблизительно 4 000 000 |
||||
|
|||||
Полезное теплопоглощение |
Гкал/ч |
52 |
52 |
52 |
|
кпд |
% |
77,2 |
79 |
90 |
|
Избыток воздуха горения |
% |
40 |
2 0 |
2 0 |
|
Тепловыделение |
Гкал/ч |
67,36 |
65,36 |
57,72 |
|
Количество дымовых газов |
кг/ч |
142790 |
119340 |
104750 |
|
Количество дымовых газов |
нм3/ч ** |
92142 |
90045 |
79040 |
|
Выбросы установки * |
мг/нмз ** |
600/250 |
350/75 |
400/90 |
|
Количество NOx |
кг/ч |
55,3 |
31,5 |
31,6 |
|
(при работе на мазуте) |
|||||
Количество NOx |
кг/ч |
23,0 |
|
7,9 |
|
(при работе на топливном газе) |
6 , 8 |
*Работа 100% на мазуте /100 % на топливном газе.
**В пересчете на сухие газы при содержании кислорода в дымовых газах 3 %>.
Печи «шатрового» типа обладают целым рядом недостатков: они имеют низ кий КПД, расположение форсунок способствует возникновению режима «наброса» пламени на трубы потолочного и фронтального экранов, трубы подового экрана ра ботают не эффективно. В процессе эксплуатации печи подвергались неоднократной реконструкции: изменялось количество потоков в печи, менялся угол наклона фор сунок, направление потока нагревательной среды, место ввода турбулизатора и т. д. В результате проведения большого объема исследований по оптимизации работы печей межремонтный пробег увеличен с 10-15 сут до одного года. На начальном периоде освоения в год менялось по 30-40 труб, в настоящее время на УЗК 21-10/300 ОАО «НОВОЙЛ» при коксуемости сырья на уровне 25-30 % в год заменяется 2-3 трубы. Печи «шатрового» типа до сих пор (с 1955 г.) эксплуатируются на УЗК «НОВОЙЛ», на НПЗ в Омске, Ангарске, Волгограде, Фергане.
Более совершенной является конструкция печей типа ГС с подовым располо жением и вертикально-факельным сжиганием топлива (рис. 3.46 — разработчик ВНИИНефтемаш).
180