
книги / Общий курс путей сообщения
..pdfта. Траверсы, представляющие собой короткие поперечные дамбы, препятствуют течению воды вдоль насыпи и предохраняют ее от размыва.
В горах, в местах возможных обвалов, сооружают специальные галереи, а в местах возможных грязекаменных (селевых) потоков – селеспуски.
При необходимости пропуска через путь потока воды (водовода) устраивают дюкеры, представляющие собой два колодца, расположенных с обеих сторон железнодорожного пути и соединенных трубой.
Трубы устраивают при пересечении железной дороги небольших водотоков или суходолов. По материалу различают каменные, металлические, бетонные и железобетонные трубы. Трубы требуют небольших затрат на содержание и устройство. В зависимости от высоты насыпи и предполагаемого расхода воды трубы бывают одно-, двух- и в отдельных случаях трехочковые. По форме поперечного сечения они могут быть круглыми, прямоугольными, сводчатыми.
2.4.2. Верхнее строение пути
Рельсы. Назначение рельсов и требования, предъявляемые к ним
Назначение рельсов – направлять колеса подвижного состава: непосредственно воспринимать и передавать нагрузки от колес на подрельсовое основание. На участках с автоблокировкой и электрической тягой рельсы, кроме этого, должны выполнять функцию проводников электрического тока.
Типы рельсов определяются массой рельса, длиной 1,0 м, значение которой округлено и проставляется после буквы Р. На главных путях железных дорог России эксплуатируются рельсы типов Р65 (87,7 % протяжения путей), Р75 (2,9 %), Р50 (8,8 %) и Р43 и легче (2,4 %).
В настоящее время прокатываются и укладываются в путь рельсы в основном Р65 (рис. 1).
41
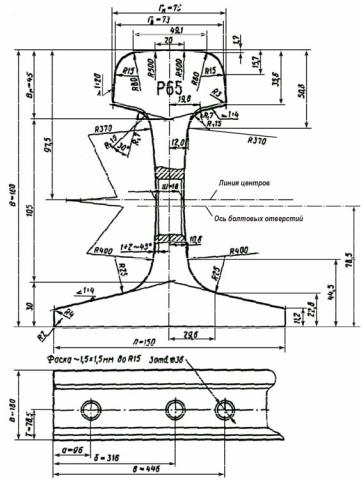
Рис. 1. Основные элементы рельса
Боковые грани головок выполняют с уклоном 1:20 (см. рис. 1). Это необходимо для размещения большего, по сравнению с рельсами, количества более легких типов металла в головке при сохранении ее предельной ширины поверху, связанной с шириной бандажей колес и допустимой величиной эксцентриситета передачи давления на рельс.
42
Переход от головки и подошвы к шейке рельса, через которую головка передает давление от колес подвижного состава на подошву, а подошва – на подрельсовые опоры, делается особенно плавным, а сама шейка имеет криволинейное очертание (см. рис. 1). Это обеспечивает минимальную концентрацию местных подголовочных напряжений и напряжений в зоне перехода шейки в подошву.
Если концы рельсов не сваривают друг с другом, то они соединяются накладками с помощью болтов. Нижние грани головки и верхние поверхности подошвы рельса имеют уклон 1:4, как и опорные поверхности стыковых накладок, что позволяет накладке при затяжке болтов входить в пазуху рельса, как клин, распирая головку и подошву, и создает условия для лучшей передачи вертикальных и горизонтальных сил от рельсов на накладку.
Стандартная длина рельсов на сети железных дорог России – 25 м. Для укладки на внутренних нитях кривых участков пути в плане изготавливают укороченные рельсы длиной 24,92 и 24,84 м. Для уменьшения числа стыков рельсы сваривают в плети. Длина коротких бесстыковых плетей на дорогах России – до 800 м, длинных – более 800 м. Длинные плети могут быть длиной, равной длине блок-участка, перегона или неограниченной длины.
Рельсы должны быть прочными, долговечными, иметь высокую контактно-усталостную выносливость. Масса рельса, его профиль, качество рельсовой стали и особенности изготовления находятся между собой в тесной взаимосвязи и в зависимости от нагрузок колесных пар подвижного состава на рельс, скоростей движения и грузонапряженности.
Типы, профили, длины рельсов
Основные характеристики применяемых типов рельсов приведены табл. 4. Поверхность катания головки нового рельса для центральности передачи нагрузки от колеса имеет выпуклое криволинейное очертание.
43
Таблица 4
Основные характеристики рельсов
|
Р75 по |
Р65 по |
Р50 по |
Р43 по |
Показатель |
ГОСТ |
ГОСТ |
ГОСТ |
ГОСТ |
|
16210–77 |
8161–75 |
7174–75 |
7173–54 |
Масса 1 м рельса, кг |
74,41 |
64,72 |
51,67 |
44,65 |
Масса одного рельса дли- |
1860 |
1618 |
1292 |
1116 |
ной 25 м, кг |
|
|
|
|
Высота, мм: |
|
|
|
|
рельса (В) |
192,0 |
180,0 |
152,0 |
140,0 |
головки (Вг) |
55,3 |
45,0 |
42,0 |
42,0 |
Ширина головки рельса, |
|
|
|
|
мм: |
|
|
|
|
вверху (Гв) |
72,0 |
73,0 |
70,0 |
70,0 |
внизу (Гн) |
75,0 |
75,0 |
70,0 |
70,0 |
Ширина подошвы (П), мм |
150 |
150 |
132 |
114 |
Ширина шейки в средней |
20 |
18 |
16 |
14,5 |
части (Ш), мм |
|
|
|
|
Расположение болтовых |
|
|
|
|
отверстий, размеры, мм: |
|
|
|
|
а |
96 |
96 |
66 |
56 |
б |
316 |
316 |
216 |
166 |
в |
446 |
446 |
356 |
326 |
Т |
80,4 |
78,5 |
68,5 |
62,5 |
d |
36 |
36 |
34 |
25 |
|
|
|
|
|
Рельсовая сталь
Материалом для рельсов служит рельсовая сталь. Рельсы изготавливают двух групп:
– I группа – из спокойной мартеновской стали, раскисленной в ковше комплексными раскислителями без применения алюминия или других раскислителей, образующих в стали вредные строчечные неметаллические включения;
44
– II группа – из спокойной мартеновской стали, раскисленной алюминием или марганец-алюминиевым сплавом.
Качество стали определяется ее химическим составом. С повышением в стали углерода повышаются общая прочность рельсов при изгибе, твердость и износостойкость. Марганец увеличивает твердость, износостойкость и вязкость рельсовой стали, а кремний – твердость и износостойкость. Фосфор и сера – вредные примеси. При низких температурах рельсы с большим содержанием фосфора становятся хрупкими, а серы – красноломкими (при прокате рельсов образуются трещины). Ванадий, титан и цирконий улучшают структуру и качество стали.
Марки стали имеют следующие обозначения: М76В, М76Т, М76ВТ, М74Т, М76Ц, М74Ц и т.д. В обозначении марки стали буква «М» указывает на способ выплавки стали (мартеновский); цифры обозначают среднее содержание углерода в сотых долях процента, буквы В, Т, Ц – соответственно относят к рельсам с ванадием, титаном и цирконием.
Механические свойства стали для рельсов I и II групп при испытаниях на растяжение должны соответствовать данным, приведенным в табл. 5. Эти данные соответствуют рельсам, изготовленным из мартеновской стали.
|
|
|
Таблица 5 |
|
|
Механические свойства стали |
|||
|
|
|
|
|
|
Марка |
Временное |
Относительное |
|
Типы рельсов |
сопротивление |
|||
стали |
удлинение, % |
|||
|
|
на разрыв, кПа |
|
|
Р75 |
М76 |
не менее 9000 |
не менее 4,0 |
|
Р65, Р50 |
М74 |
8600 |
5,0 |
Для обеспечения большей износостойкости и долговечности рельсы изготавливают из мартеновской высокоуглеродистой стали (типы Р75, Р65, Р50), подвергая их термической
45
обработке по всей длине путем объемной закалки в масле с последующим печным отпуском (ГОСТ 18267–82).
Рельсы, полностью удовлетворяющие техническим требованиям и стандартам, относятся к первому сорту. Рельсы, имеющие отклонение в химическом составе и механических свойствах, относятся ко второму сорту.
Объемно-закаленные рельсы имеют срок службы в 1,3– 1,5 раза выше, чем обычные.
Заводская маркировка рельсов, сроки службы рельсов и мероприятия по их продлению
Маркировка рельсов производится для правильной укладки их в путь и для определения места и времени изготовления каждого отдельного рельса. Она подразделяется на основную (постоянную), выполняемую во время прокатки клеймением (рис. 2), и дополнительную или временную, выполненную краской. Основная заводская маркировка указывает соответствие рельсов требованиям стандартов, а дополнительная отмечает особенности каждого рельса (укорочение, пригодность к укладке, сорт и т.д.).
Маркировка разделяется на общую для всех рельсов
ииндивидуальную для каждого рельса. Рядом со знаками инспекции МПС, определяющими сорт рельсов, наносится клеймо ОТК завода-изготовителя. На всех рельсах вдоль шейки примерно через 2,5 м выпуклыми буквами и цифрами указывают завод-изготовитель рельсов (начальной буквой – название завода): А – Азовсталь; Д – завод им. Дзержинского
ит.д. Кроме этого, на шейке рельса в 5–6 местах указывают номер плавки стали, время проката, тип рельса и т.д. (см.
рис. 2).
Для характеристики особенностей каждого рельса делают дополнительную маркировку. Например, если торец головки рельса по контуру обведен белой краской и выбит керн, то это значит, что рельс незакаленный первого сорта; если весь торец рельса окрашен синей краской, на обоих
46
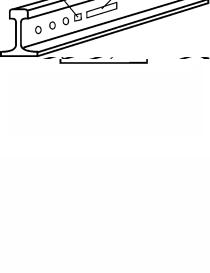
а
б
Рис. 2. Основная маркировка рельсов: а – на торце рельса; б – на боковой поверхности шейки; 1 – инспекторские клейма; 2 – клеймо ОТК завода; 3 – место нанесения номера рельса; 4 – место нанесения номера плавки стали; 5 – место указания порядкового номера рельса от головной части слитка; 6 – место выкатанной маркировки по длине рельса, повторяющейся примерно через 2,5 м и обозначающей завод-изготовитель, месяц и год проката, тип рельса
концах по 3 керна – рельс забракован, к укладке в путь непригоден и т.д.
Сроки службы рельсов определяются:
1)в кривых R = 250…650 м, как правило, боковым
иприведенным износом рельсов;
2)на прямых и кривых R > 650 м – интенсивностью нарастания их одиночного изъятия по дефектам.
Интенсивность одиночного выхода рельсов зависит от их наработки (пропущенного по ним тоннажа), конструкции пути, нагрузок на рельсы, плана и профиля пути, типа рельсов, качества стали и других факторов.
47
Волнообразная деформация головки рельса (длинные волны), как правило, возникает при прокате и правке рельсов на комбинатах, а в эксплуатации происходит дальнейшее развитие первоначальных дефектов.
Вследствие неоднородности механических свойств металла, получающейся при сварке рельсов, образуется местное смятие головки рельса. Смятие головки в виде седловины связано с особенностями динамического воздействия колеса на рельс при прохождении им зоны стыка.
При движении подвижного состава вследствие ряда причин (главным образом из-за разности в диаметрах кругов катания колесной пары) возникает периодическое проскальзывание колес, что вызывает сдвиги или повышенное истирание верхних слоев металла в местах проскальзывания и образование коротких неровностей – рифлей.
Эффективным мероприятием для восстановления дефектных рельсов является их шлифовка. Она подразделяется на два вида: профильная, при которой головка рельса шлифуется по всему ее периметру с целью удаления вертикальных и боковых неровностей, и поверхностная (в вертикальной плоскости), предназначенная для устранения волнообразного износа и коротких неровностей других видов на поверхности катания рельсов для уменьшения вибрационных воздействий подвижного состава на путь.
Рельсовые стыки и стыковые скрепления. Классификация стыков
Места соединения рельсов между собой называют стыками. По конструкции различают стыки болтовые, клееболтовые и сварные.
В болтовых стыках (рис. 3) между концами рельсов, прикрытых накладками, оставляют зазоры для возможности изменения длины рельс при изменении температуры. Стык – самое напряженное место в пути. Около 35–50 % затрат труда по выправке пути связано с наличием стыков. Стыки соз-
48
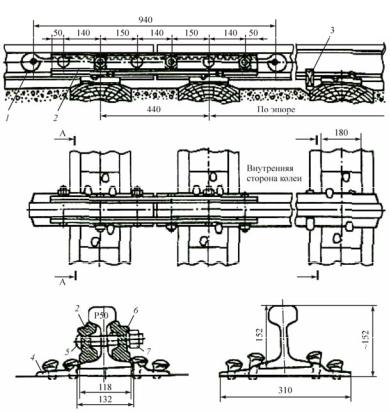
дают сопротивление движению поездов (около 5–7 % основного сопротивления).
В клееболтовых стыках накладки приклеиваются к рельсам и стягиваются болтами.
Рис. 3. Общий вид крепежа рельса к шпале
49

В сварных стыках обеспечена непрерывность рельсовых нитей. Однако если в сварном стыке рельсы примыкают друг к другу под углом или со ступенькой в плане и профиле, то ударно-динамические воздействия колес на путь в таком стыке могут быть такими же, как на болтовом стыке.
По отношению к опорам различают стыки на шпале (рис. 4, а), на весу (рис. 4, б) и на сдвоенных шпалах (рис. 4, в). Стык на шпале под колесной нагрузкой получается жестким, кроме того, наблюдается кантование (поворот относительно продольной оси) шпалы. Поэтому такой стык быстро расстраивается. Стык на весу более упруг, однако в его накладках реализуются более высокие напряжения. Основными недостатками стыка на сдвоенных шпалах являются: большая жесткость, трудность подбивки балласта под сдвоенные шпалы, дополнительный расход металла на стяжные болты.
а |
б |
в |
Рис. 4. Общий вид стыков
Всеобщее распространение получили стыки на весу. Изгиб рельсовых концов и накладок от колесной нагрузки при стыке на весу больше, чем при стыках на опоре. Для снижения изгибающего момента расстояние между осями стыковых шпал устраивают меньшими, чем между осями промежуточных шпал. На пути с рельсами Р50 стыковой пролет принят равным 440 мм, а при рельсах Р65 и Р75 – 420 мм, в то время как расстояния между осями промежуточных шпал приняты равными 550 мм при эпюре шпал 1840 шт. на 1 км и 500 мм при эпюре шпал 2000 шт. на 1 км.
50