
книги / Развитие химической промышленности в СССР (1917-1980). Т. 2 Развитие отдельных отраслей химической промышленности
.pdfобслуживаппе. Все указанные недостатки в конечном итоге и обусловили весьма низкие технико-экономические показатели этих печей.
В 1948—1950 гг. возникла проблема расширения производства циан амида кальция для применения его в качестве дефолианта хлопчатника при машинной уборке хлопка. Страна еще не имела собственных дефо лиантов, их импортировали. Впервые в СССР на Кировакапском химиче
ском |
заводе группой |
инженеров |
(П. |
Е. |
Казарян, В. Н. |
Костин, |
Д. Е. |
Пюскуляп, А. П. |
Соболев) |
в 1949 |
г. |
был разработан и |
внедрен |
технологический процесс получения аэроцианамида кальция для постав ки хлопкосеющим райопам в качестве дефолианта. В 1950—1952 гг. были созданы новые конструкции циаиамидпых печей па Кировакапском химическом заводе, которые отличались своими геометрическими и тепло техническими параметрами, высокой производительностью и лучшими технико-экономическими показателями [17, с. 43].
Длительная экспериментальная проверка печи новой конструкции по казала ее высокую работоспособность и значительные преимущества в производственных условиях на Кировакапском химическом заводе [17, с. 45].
Исходя из полученных результатов испытания к впедрению была ре комендована печь новой конструкции, па базе которой осуществлена ре конструкция и расширение цеха цианамида кальция на Кировакапском химическом заводе п построены 1 1 0 печей па существующих производст венных площадках с минимальным объемом капитальных вложений, ко торые окупились в течение полугода. Это техническое мероприятие дало возможность обеспечить хлопкосеющие районы дефолиантом — топкомо лотым цианамидом кальция и создать крупнотоннажные производства дицпандиамида и меламина па этом заводе. Свыше 50 лет трудились в карбпд-цпанампдном производстве инженеры-технологи К. А. Меркпп,
А.Г. Хажакяд п А. С. Парилов, внесшие большой вклад в его развитие. Несмотря на то, что классический способ получения цианамида каль
ция в течение более трех четвертей века оставался незыблемым, этот про цесс в настоящее время уже отжил свой век, физически и морально устарел. Создание новых производств на базе существующего метода не целесообразно как по экономическим, так и по техническим соображе ниям. В связи с этим за последнее десятилетие ищут новые, более эко номичные пути и методы получения цианамида кальция и его производ ных. В частности, весьма перспективен комбинированный метод получения аммиака, цианамида кальция и свободного цианамида.
Цианамид кальция весьма ценный продукт. Он является непревзойден ным долгодействующим азотсодержащим щелочным удобрением для кис лых почв. Только при разработке нового метода его получения и значи тельном сокращении энергетических затрат (в условиях комбинированных схем) его производство может развиваться для использования в растение водстве в качестве высокоэффективного щелочного азотного удобрения.
ПРОИЗВОДСТВО
МИНЕРАЛЬНЫХ УДОБРЕНИЙ
ГЛАВА ВОСЬМАЯ
АЗОТНЫЕ УДОБРЕНИЯ*
АММИАЧНАЯ СЕЛИТРА
Аммиачная селитра (пытрат аммония) —один из самых многотоынажпых продуктов отечественной химической промышленности. В основном при меняется в качестве азотного удобрепия (содержит ~34% азота) и в относительно небольших количествах для производства промышленных взрывчатых веществ, используемых в горнодобывающей промышленно сти, при строительстве гидросооружений и т. д.
В начале нынешнего столетия аммиачная селитра производилась в не которых зарубежных странах в основном как компонент взрывчатых смесей.
Широкое развитие производства аммиачной селитры, как и других азотных удобрений, стало возможным лишь на базе синтеза аммиака.
За рубежом синтетический аммиак первоначально перерабатывали в малокопцентрированные удобрепия —сульфат аммония и известково-ам миачную селитру, содержащие 2 1 % азота, однако аммиачпую селитру не применяли в сельском хозяйстве из-за ее взрывоопаспостп (известен взрыв в Огшау в 1921 г., когда при разрыхлении с помощью взрывчатых веществ слежавшейся двойной соли сульфата-нитрата аммония произо шла детонация с катастрофическими последствиями). Еще в 1903 г. ака демик Д. Н. Прянишников, внесший большой вклад в изучение азотного питания растений, называл аммиачную селитру «удобрением будущего». В конце 20-х годов, когда в СССР только закладывался фундамент азот ной промышленности и необходимо было установить ассортимент азот ных удобрений, особое внимание было обращено на перспективность ис пользования в сельском хозяйстве аммиачной селитры, единица азота в которой оказывалась наиболее дешевой. В результате глубокого изучения свойств, в том числе взрывоопасности, аммиачной селитры и особенно благодаря полевым опытам в различных зонах в основу отечественной азотной промышленности с самого начала ее развития была положена переработка аммиака в аммиачную селитру.
Начало широкого промышленного производства аммиачной селитры в Советском Союзе относится к годам первой пятилетки, когда построили четыре цеха аммиачной селитры. Три из них были довольно крупными: один по отечественной схеме и на отечественном оборудовании в Горловке
*Раздел «Аммиачная селитра» написан А. И. Бруштенном и И. Н. Поляковым, раз дел «Карбамид» — В. В. Лебедевым.
(1933 г.) п два с использованием импортного оборудования в Березниках (1932 г.) и в Бобриках (1933 г.).
Сущность процесса получения аммиачной селитры с тех нор осталась прежней —нейтрализация азотной кислоты аммиаком с образованием вод ных растворов нитрата аммония, их упаривание и последующая кристалли зация с получением твердого продукта. Однако технологическая схема и аппаратурное оформление неузнаваемо изменились.
Первые установки отличались громоздкой схемой и низкой произво дительностью оборудования. Последнее изготавливалось преимущественно из углеродистой стали с футеровкой кислотоупорной плиткой или из алю миния, подверженного коррозии. В редких случаях применялась дорого стоящая импортная нержавеющая сталь.
Тепло нейтрализации азотпой кислоты аммиаком в первых отечествен ных цехах, как и за рубежом, в го время не использовалось; из-за опасения термического разложения и высоких потерь сырья процесс нейтрализации проводили с искусственным охлаждением. Образующийся в нейтрализаторах раствор циркулировал через выносные холодильники. Это усложняло узел нейтрализации, и вся поступающая с азотной кисло той вода оставалась в растворе, для упаривания которого приходилось расходовать большое количество пара (1 Гкал и более па 1 т продукта). Выпарпые аппараты применялись преимущественно периодического дей ствия.
Стадия кристаллизации решалась по-разному. В одних схемах раствор после упаривания до концентрации 82—83% охлаждался до насыщенно го состояния и кристаллы отделялись на центрифугах. По схеме Кестнера раствор упаривался до 94—95% и плав заливался в чашечные кри сталлизаторы периодического действия. За счет тепла кристаллизации и теплосодержания плава при медленном интенсивном перемешивании (операция длилась до 4 ч) удалялась остаточная влага и получался мел кокристаллический продукт. Несмотря на очень низкое содержание влаги (0 ,1 —0 ,2 %) мелкокристаллическая селитра слеживалась в прочную моно литную массу, что крайне затрудняло ее использование в сельском хо зяйстве.
Более совершеппой была схема непрерывной кристаллизации па охлаждаемом вальце, по которой упаренный до 97—98,5% плав аммиач ной селитры непрерывно поступал в корыто. Здесь плав охлаждался по груженным в корыто полым барабаном, заполнявшимся проточной холод ной водой. Образующаяся при вращении барабана на его поверхности тонкая корка закристаллизовавшегося плава срезалась пожами, получа лись чешуйки размером преимущественно от 2—3 до 5—6 мм и толщиной 1—1,5 мм. Чешуйчатая селитра также слеживалась, хотя и в меньшей степени, чем мелкокристаллическая.
К середине 30-х годов был пакоплеи значительный опыт производства аммиачной селитры, а также применения ее в сельском хозяйстве. Дей ствующие производства интенсифицировались —периодические процессы заменялись непрерывными, совершенствовалось оборудование, начала ис пользоваться отечественная нержавеющая сталь. С 1934 г. для упаковки продукта вместо бочек стали применять многослойные мешки из битумированиой бумаги, что позволило ежегодно экономить десятки тысяч кубо метров леса и сотни тонн обручного железа.
В 1937 г. было выработано около 270 тыс. т аммиачной селитры. Проектировщики Гинроазота и исследователи ГИА вместе с заводски
ми работниками продолжали совершенствовать технологический процесс. Основное внимание уделялось стадии нейтрализации и улучшению физи ческих свойств (снижению слеживаемости) аммпачпой селитры.
С расширением масштабов производства все более актуальной станови лась задача использования тепла нейтрализации. Еще в 1933 г. был раз работан (И. И. Гельперин и др.) и испытан комбинированный аппа рат ГЛ для получения концентрированных растворов аммиачной селитры с использованием не только тепла нейтрализации, но п тепла сокового пара. В конструкции аппарата были заложепы весьма прогрессивные идеп [1 ].
В 1935—1936 гг. па Чериоречеиском химическом заводе испытали разработанную Гипроазотом конструкцию нейтрализатора ИТР (исполь зование тепла реакции). Аппарат состоял из двух частей —реакционной (сатуратора) и испарительной. Нейтрализация в сатураторе осуществля лась под избыточным давлением 0,5—0,6 МПа с тем, чтобы не допустить кипения раствора в зоне реакции. Образовавшийся перегретый раствор нитрата аммония через редукционный вентиль непрерывно поступал в испарительную камеру, где кипел под атмосферным давлением. Азотпая кислота предварительно подогревалась соковым паром аппарата ИТР. В 1937—1938 гг. на Березниковском азотно-туковом заводе проводили испытания аппарата ИТН (использование тепла нейтрализации) более простой конструкции.
Улучшение физических свойств продукта осуществлялось путем обра ботки селитры гидрофобной добавкой (парафином) и освоения процесса гранулирования в башнях. Добавка парафипа применялась только в ча шечных кристаллизаторах. Гранулирование отрабатывали первоначально на лабораторной установке НИУИФа, а в 1934 г.—на Березниковском азотно-туковом заводе (А. М. Дубовицкпй, А. Г. Филинов и др.) в опыт ной башне высотой 15 м, в которой разбрызгивали 95%-иый плав при 145° С.
В предвоенные годы начался новый этап развития производства ам миачной селитры. До 1937—1938 гг. технический прогресс осуществлялся путем интенсификации установок, построенных в годы первой пятилет ки. В середине 30-х годов отечественное химическое машиностроение могло обеспечивать производство аммиачной селитры аппаратурой из нержавеющей стали, насосами из кислотоупорных сплавов и т. д.
На базе проведеппых работ и с использованием отечественного обору дования Гипроазот (А. К. Ковтун, Б. В. Козлов и др.) запроектировал че тыре цеха. До пачала Великой Отечественной войны были пущены три из них: цех гранулированной селитры в Кемерово (1937—1938 гг.), цехи в Днепродзержинске (1938 г.) и в Чирчике (1940 г.).
Вскоре после пуска аппараты ИТР удалось перевести на работу под атмосферным давлением, а мешалку для искусственной циркуляции раствора внутри сатуратора демонтировать; естественная циркуляция оказалась достаточно интенсивной, что заметно упростило обслуживание аппарата.
Аппарат ИТН, запроектированный для работы под атмосферным дав лением, первоначально был однопроходным, циркуляция раствора внутри аппарата пе предусматривалась. В последующем конструкция ИТН была
усовершенствована, ввод аммиака п кислоты перенесен вниз, в аппарате осуществлялась интенсивная циркуляция раствора между внутренним реакционным стаканом и наружной испарительной камерой. При проек тировании использовали результаты ранее проведенных исследований влияния температуры на процесс разложения нитрата аммония при осу ществлении реакции нейтрализации под атмосферным давлением [2 , 3], а также данные исследования упругости паров азотной кислоты и аммиа ка над водными растворами нитрата аммония [4].
Во всех проектах предусматривались многосекциоппые двухходовые горизонтальные трубчатые выпарные аппараты АС пленочного типа, рабо тавшие под разрежением, выгодно отличавшиеся простотой конструкции п повышенным паросъемом от старых громоздких аппаратов периодиче ского действия.
Поскольку на опытной установке в Березниках нельзя было получить исчерпывающих данных для проектирования грануляционных башен, пришлось до пуска Кемеровского азотно-тукового завода включить в пробную эксплуатацию грануляционные башни и отработать процессы выпаривания в аппаратах АС и гранулирования иа привозпой аммиачной селитре.
При пуске Кемеровского азотно-тукового завода, несмотря на новиз ну процесса, цех аммиачной селитры не испытывал неполадок и беспере бойно перерабатывал получаемое сырье, а в 1940 г. вышел иа первое место в стране по объему производства. В дальнейшем подобный метод пробных пусков на привозной селитре неоднократно применялся на дру гих предприятиях.
Накануне Великой Отечественной войны была создана крупная про мышленность по производству аммиачной селитры. Много селитры отгру жалось в хлопководческие районы Средней Азии, что заметно способство вало росту урожайности хлопчатника. Кроме того, аммиачная селитра (с промежуточным детонатором) иногда применялась при взрывных рабо тах на строительстве угольных шахт, при прокладке тоннелей, каналов,
строительстве |
плотин. При массовых |
взрывах использовались |
заряды |
до 2 тыс. т селитры. |
производимой в Советском |
Союзе |
|
К 1940 г. |
60% общего количества |
аммиачной селитры выпускали предприятия, расположенные в восточ ных районах страны. Это сыграло важную роль, когда на захваченной врагом территории оказались Горловский, Днепродзержинский азотно туковые заводы и Сталиногорский химический комбинат. Вся тяжесть но обеспечению страны аммиачной селитрой легла на Березниковский, Кемеровский азотно-туковые заводы и Чирчикский электрохимический комбинат.
Аммиачная селитра поставлялась для пужд фронта, она применя лась и в сельском хозяйстве (почти исключительно для хлопковод ства) . Ее использовали для производства так называемых динамонов — смесей аммиачной селитры с горючими добавками (древесной мукой, торфом и т. п.), которые заменили применявшиеся в довоенные годы в горно-рудной промышленности «классические» взрывчатые вещества.
В 1945 г. был достигнут, а в 1948 г. вдвое превзойден (без ввода новых заводов) довоенный уровень производства аммиачной селитры. Однако для дальнейшего развития сельского хозяйства требовалось зна чительное увеличение выпуска минеральных удобрений. За период
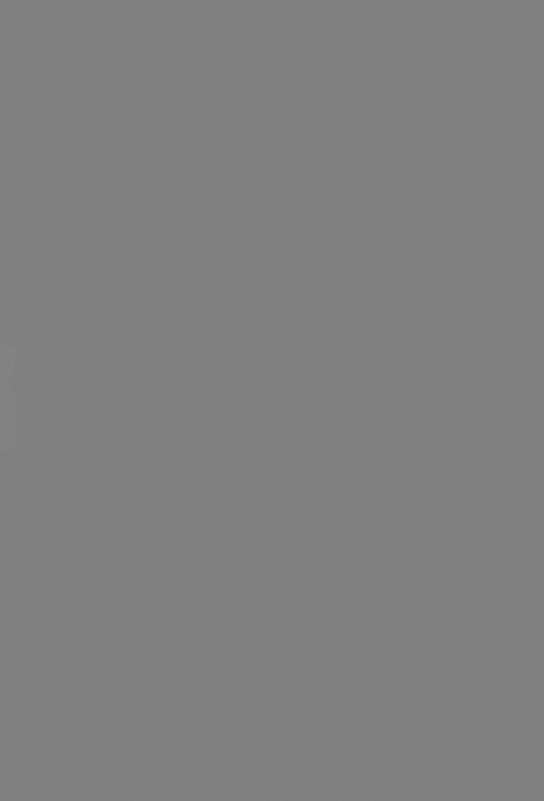
1951— 1955 гг. были введены три новых цеха аммиачной селитры: в Кировакане (1951 г.), в Лисичанске (1951 г.) и в Рустави (1955 г.).
По мере увеличения поставок удобрений росли требования и к их качеству. Между тем при хранении аммиачная селитра (даже гранули рованная) слеживалась в плотные глыбы, измельчение которых и просев через сита требовал значительных затрат труда. Работы, начатые еще в 30-е годы, показали, что устранению слеяшваемости способствует сни жение влагосодержапия, а также охлаждение и, особенно, введение кондпциопирующих добавок. В первые послевоенные годы охлаждение и сни жение влажности еще не были освоены, но удалось осуществить обработ ку селитры добавками.
Исследования кондиционирующих добавок были возобновлены в ГИАПе и в НИУИФе. В результате в 1948 г. Кемеровский азотно-туко вый завод и Сталипогорский химический комбинат начали применять предложенный сотрудниками НИУИФа [5] метод поверхностной обработ ки селитры гидрофобными (0,3—0,4% парафинистого мазута) и припуд ривающими (4—5% тоикоизмельченного известняка и др.) добавками во вращающихся барабанах. Однако в результате проведенных исследований [6 ] было выявлено повышение потенциальной взрыво- и пожароопасно сти селитры, вызываемое этими добавками. Особенно это было заметно при нарушениях дозировки и при увеличении содержания пылевидной фракции в чешуйчатой селитре. Поэтому уже в 1951 г. от использования этой гидрофобной добавки отказались.
Промышленность оказалась в затруднительном положении, нужно было в короткие сроки подобрать равноценную и безопасную замену. Следует отметить, что еще в 1947 г. были начаты исследовательские и опытные работы по изысканию неорганических добавок, уменьшающих слеживаемость аммиачной селитры. В результате этих работ были внед
рены две неорганические добавки1 условно названные |
РАП и |
ДЛМ. |
|
Добавка РАП —раствор, получаемый в результате |
разложения азот |
||
ной кислотой |
апатитового концентрата, содержащий в основном |
фосфор |
|
ную кислоту |
и нитрат кальция. Она была разработана Чирчикскпм |
||
электрохимическим комбинатом (М. Н. Набиев, А. И. Ильясов |
и др.) |
иАкадемией паук УзбССР и внедрена па Чирчикском электрохимическом
иСеверодонецком химическом комбинатах.
Добавка ДЛМ —раствор, получаемый разложением азотной кислотой доломита и содержащий в основном нитрат кальция и нитрат магния. Она была разработапа ГИАПом (М. А. Миниович и др.) и Кемеровским азотно-туковым заводом. Эту добавку стали применять на большинстве предприятий, выпускавших аммиачную селитру.
Разработка в сжатые сроки пеорганических добавок РАП и ДЛМ, кото рые начали использоваться в 1952—1953 гг., имела важное народнохо зяйственное значение.
В эти же годы был внедрен ряд других технических новшеств: авто матизация аппаратов ИТН, позволившая облегчить обслуживание и сни зить потери с соковым паром; машинная зашивка мешков для упаковки селитры вместо ручной завязки; использование тепла сокового пара для
1 Разработанная на Днепродзержинском азотно-туковом заводе добавка нитрата железа оказалась менее эффективной и применялась лишь несколько лет.
предварительного упаривания растворов. Почти па всех заводах приме
няли 44—48%-ную |
азотную кислоту и в аппаратах ИТН получали 60— |
6 8 %-ные растворы |
нитрата аммония, которые упаривали с затратой |
дорогостоящего пара. В то же время соковый пар, образующийся в аппа ратах ИТН, выбрасывали в атмосферу. Расчеты показали, что соковый пар пригоден для упаривания под вакуумом 65—68%-ных растворов селитры до 83%-ных. Однако эта идея оставалась неосуществленной, пока ГИАП в 1947 г. не запроектировал для Днепродзержинского азотно тукового завода устаповку двухступенчатого упаривания: в первой ступе ни (форвыпарка) —соковым паром, во второй —обычным промышлен ным паром давлепием 1),8 МПа. В качестве форвыпарки использовали одну секцию горизонтального аппарата АС, второй ступенью служил обычный многосекционпый аппарат АС.
Незадолго до этого обследование показало [7], что из-за значитель ного гидравлического сопротивления нижние секции (трубчатки) многосекционного аппарата АС работали не под вакуумом, как предусматри валось проектом, а под избыточным давлением. Результаты обследования оставались неиспользованными, пока при пуске форвыпарки в Днепро дзержинске не столкнулись с серьезными трудностями из-за повышенного гидравлического сопротивления [8 ]. В конце концов форвыпарку успеш но освоили и получили повые данные о гидравлическом режиме горизон тальных выпарных аппаратов АС. В проекты новых цехов стали закла дывать двухступенчатое упаривание, причем для первой ступени приме няли вертикальные аппараты с восходящей пленкой. Внедрение форвыпарки дало большую экономию промышленного пара. Уже в 1954— 1955 гг. ежегодно экономили сотни тысяч гигакалорий тепла.
За период 1946—1958 гг. выпуск аммиачной селитры возрос вчетверо, причем основной прирост был достигнут за счет интенсификации дей ствующих мощностей, введения технических усовершенствований, распро странения передового опыта лучших аппаратчиков М. И. Качкова, В. П. Хомяковой и др. С помощью Советского Союза было создано произ водство аммиачной селитры в социалистических странах.
Решения майского (1958 г.) Пленума ЦК КПСС об ускоренном разви тии химической промышленности послужили новым мощным стимулом роста производства азотных удобрений. Выпуск аммиачной селитры в 1965 г. почти в 2,5 раза превысил уровень 1958 г. За этот период было введено в эксплуатацию семь цехов аммиачной селитры.
Наиболее существенным в техническом прогрессе было внедрение способа охлаждения гранул в кипящем слое. Проводились также работы по интенсификации выпарпых аппаратов и по усовершенствованию гра нуляторов. Необходимость в охлаждении готового продукта была извест на, в отдельных проектах закладывали охлаждение гранул во вращаю щихся барабапах, но при крупиотонпажпых производствах этот метод был громоздким и трудноосуществимым. Требовалось принципиально новое решение. К началу 60-х . годов относится внедрение в производство аммиачной селитры разработанного в ГИАПе (Е. А. Казакова и др.) совместно с заводами метода охлаждения гранул в псевдоожижеппом слое [9].
В крупном промышленном масштабе охлаждение внедрили в 1960 г. на Днепродзержинском химическом комбипате в выносном (уста
новленпом после грапуляцпоппой башни) аппарате и па Лисичанском химическом комбинате в аппарате, встроеппом в конус грануляционной башни. В последующие несколько лет охлаждающие аппараты, преиму щественно встроенные, реже выносные, были смонтированы на всех заводах.
Несмотря на выявленное в 1946—1948 гг. высокое гидравлическое сопротивление, горизонтальные выпарные аппараты по-прежнему приме нялись для конечного упаривания до 98%. Поверхность нагрева отдель ных секций аппарата возросла от первоначальных 9 до 60 и 125 м \
В 1962 г., когда на Новомосковском химическом комбинате потребо валось увеличить производство аммиачной селитры, а дополнительный выпарной аппарат не размещался в надстройке над башней, было пред ложено использовать вертикальный выпарной аппарат с поверхностью нагрева 32 м2 с восходящей пленкой, предназначенной для цеха карба мида. В принципе конструкция аппарата не отличалась от используемых в цехах аммиачной селитры форвыпарок, обогреваемых соковым паром. Этот компактный аппарат-трубчатку с сепаратором легко разместили на небольшой свободной площади. При пуске неожиданно оказалось, что удельная производительность примерно втрое превышает производитель ность обычных горизонтальных аппаратов АС.
ГИАП разработал вариант переделки двухходовой трубчатки горизон тального выпарного аппарата АС в аппарат вертикального типа, и в те чение ближайших лет подобную реконструкцию провели все заводы. От использования горизонтальных выпарных аппаратов полностью отка зались.
На протяжении 1958—1965 гг. продолжалось совершенствование центробежных грануляторов. В прежние годы оно сводилось к экспери ментальному опробованию перфорированных корзин различной формы и с различными диаметром и шагом отверстий. С 1956—1957 гг. в централь ной лаборатории Лисичанского химического комбината было положено начало изучению и совершенствованию процесса гранулирования и кон струкции грануляторов (Б. Г. Холин). Однако в те годы новые конструк ции не получили еще широкого распространения.
Были приняты меры по снижению предельной влажности гранулиро ванной аммиачной селитры от 1,5 до 1,0%, по нормированию темпера туры затаривания и содержания гранул размером 1—3 мм, а также по улучшению рассыпчатости. Достигнутое улучшение качества продукта позволило потребителям начать производство гранулированных промыш ленных взрывчатых веществ (механическая смесь гранул аммиачной селитры с другими компонентами), отличающихся рядом преимуществ и
более низкой стоимостью |
по сравнению с порошковидными ВВ. |
В процессе переработки |
(механический транспорт, дозировка, смеше |
ние и др.) у промышленных потребителей происходило разрушение гра нул селитры. Это послужило стимулом к изучению влияния отдельных факторов, особенно режима охлаждения, на механическую прочность гра нул сначала на Лисичанском химическом комбинате [10], затем в ГИАПе и в других организациях.
Гранулированную аммиачную селитру начали применять и в горно добывающей промышленности для приготовления простейших взрывча тых веществ (пгданитов) непосредственно на месте взрывных работ.
В 1956—1957 гг. было организовано производство так называемой водоустойчивой аммиачной селитры, применяемой для технических целей, а в 1961—1962 гг. — ее производство в гранулированной форме.
За период 1966—1980 гг. выпуск селитры возрос в 2,2 раза, при этом произошли большие качественные изменения: удвоена мощность строя щихся агрегатов, освоено производство продукта, пригодного для бестар ного транспортирования и сухого тукосмешения. ГИАП, выполнив со вместно с промышленными предприятиями большой объем научно-иссле довательских и опытных работ, установил, что для получения такого продукта необходимо максимально снизить содержание в нем влаги, вы пуская его в форме плотных, однородных гранул, обладающих прочно стью, достаточной для предотвращения измельчения гранул при их транс портировке и хранении. Плав аммиачной селитры должеп содержать кондиционирующие добавки, устраняющие слеживаемость готового про дукта. И, наконец, гранулы селитры должны быть обработаны поверх ностно-активными веществами типа диспергатора НФ и др. (исключение составляет селитра с магиийсодержащими добавками).
Новые агрегаты мощностью по 225 тыс. т/год, пущенные в 1970— 1972 гг.2*в Череповце, Черкассах, Навои и др., в отличие от действую щих тогда агрегатов обеспечивались азотной кислотой повышенной кон центрации (57—59%-ной). Первоначально в проектах намечалась уста новка выпарных аппаратов для упаривания растворов в одну ступень от 80—84 до 98—98,5%. Однако уже в 1963—1964 гг. стала очевидной необходимость дальнейшего повышения концентрации плава и снижения влажности селитры по крайней мере до 0,3—0,4% против действовавшей тогда нормы до 1%. Между тем существующие вакуум-выпарные аппа раты не обеспечивали концентрацию плава выше 98,5—98,7%. Потребо валась коренная реконструкция выпарных установок на грануляционных башнях с монтажом (дополнительно к имеющимся вакуум-выпарным) новых аппаратов для последующего доупаривания 98%-пого плава до концентрации 99,5 %.
Таким образом, добавлялась еще стадия доупаривания. Изучение ва риантов доупарочных аппаратов в ГИАПе (М. Е. Иванов и др.) начали в 1963—1964 гг. на модельной установке и на Иевинпомысском химическом комбинате. На основе этих исследований была принята конструкция вер тикального кожухотрубного аппарата с падающей пленкой. Аппарат рабо тал под атмосферным давлением, противотоком к плаву в трубки пода вался горячий (180—190° С) воздух, уносящий выделяющиеся из плава водяные пары. Подобные аппараты с поверхностью нагрева 127 м8 были изготовлены для большинства действующих цехов (Невппномысский хи мический комбинат изготовил первый аппарат собственными силами и успешно освоил его в 1966 г.). Одновременно на Северодонецком хими ческом комбинате разработали новую конструкцию выпарного аппарата пенного типа, значительно более компактного, но менее мощного и тре бующего поступления плава концентрацией не ниже 98,0%.
Первоначально аналогичные аппараты пенного типа были изготов лены и установлены также в Чирчике и Кемерово, по в дальнейшем их заменили типовыми кожухотрубчатыми аппаратами конструкции ГИАПа,
2 Начиная с 1972 г. строили только крупные агрегаты типа АС-67 п АС-72 еди ничной мощностью по 450 тыс.т/год.