
книги / Развитие химической промышленности в СССР (1917-1980). Т. 2 Развитие отдельных отраслей химической промышленности
.pdfнения из-за недостатка материалов, таких, как гранит, легированная сталь, кислотоупорный цемент и др., были преодолены в короткий срок, н объем производства крепкой азотной кислоты значительно увеличился. Одновременно проводились усовершенствования производства слабой азотной кислоты. Например, впервые применили отбросный кислород для обогащения аммначно-воздушиой смеси, что позволило иа 2—3% повы сить степень конверсии аммиака и значительно улучшить стадию абсорб ции окислов азота.
На Кемеровском АТЗ были выполнены крупные работы, имевшие большое значение для увеличения выработки крепкой и слабой азотной кислоты. При пуске цеха крепкой азотной кислоты в постоянную экс плуатацию выявилось, что увеличение производства сверх проектной мощности лимитируется недостаточной производительностью отделения переработки отработанной серной кислоты в купоросное масло. Для устранения диспропорции группа инженеров предложила способ интен сификации существующих топок и концентраторов. Были расширены сечения газоходов, изменены кислотоперетоки, применен новый тепловой режим и т. д. В результате этого выработка купоросного масла увеличи лась в 2,5—3 раза, а выпуск крепкой азотной кислоты—в 1,5 раза [8]. За разработку и внедрение этого способа были удостоены Государствен ной премии СССР А. И. Кирш, Н. И. Беляев, А. Ф. Иванова, И. А. Казарцев, В. Г. Бахуров, И. П. Сорокин, А. Я. Рябеико, П. В. Спчков, A. А. Голубов.
Вторая работа, выполненная на Кемеровском АТЗ, связана с изыска нием нового катализатора для окисления аммиака в окись азота. Вслед ствие острой дефицитности и высокой стоимости родия (ои в 5 раз дороже платины), входившего в состав катализатора, во время войны и, частично, в послевоенный период применялись катализаторные сетки из платины без добавки 7—10% родия. При этом степень конверсии аммиа ка была ниже на 3—4%, а потери платины выше на 15—20%, чем в слу чае работы с платинородиевыми катализаторами.
В результате исследований был изыскан новый катализатор ГИАП-1, содержавший 93% платины, 4% палладия и только 3% родия. Многолет няя эксплуатация этого катализатора показала, что по механической прочности, сроку службы и потерям он не уступает платииородиевому катализатору, а по активности превосходит его иа 0,8—1%. Катализатор ГИАП-1 был разработан М. А. Миниовичем при участии В. А. Клевке, B. С. Ясиповского, И. М. Розенфельда и В. А. Немилова, которым за эту работу была присуждена Государственная премия СССР.
Вначале 1943 г. закончилось восстановление производств азотной кислоты на Сталиногорском химическом комбинате. При восстановлении цеха крепкой азотной кислоты осуществили ряд усовершенствований, увеличивших выпуск готового продукта.
Впроизводстве азотной кислоты во время Великой Отечественной войны было проведено много нововведений, увеличивших выпуск продук ции (повышена напряженность катализатора окисления аммиака на 15— 20%, внедрены новые приемы сборки концентрационных колонн, повы шены температуры подогрева слабой азотной кислоты и купоросного масла и т. д.).
Впериод Великой Отечественной войны для увеличения выпуска сла бой и крепкой азотной кислоты много творческой инициативы проявили,
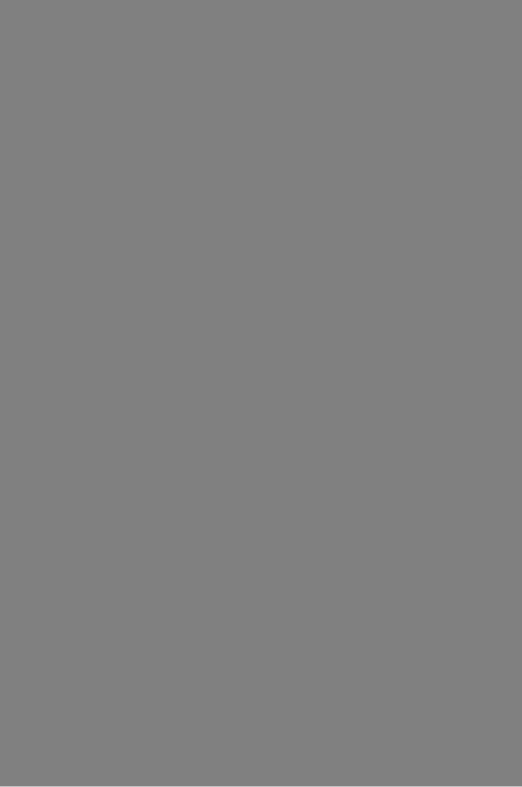
тонкой очистки аммиачно-воздушной смеси, получение пара с давлением 4050 кПа, применение в стадии абсорбции ситчатых тарелок и др. Метод обеспечивает высокую конверсию аммиака (не менее 97%) и низкие за траты платпноидного катализатора (0,028—0,40 г/т НЖ)з). Недостатка ми системы являются повышенный расход электроэнергии и небольшая мощность агрегата (45—50 тыс. т/год). Разработчики системы по произ водству азотной кислоты комбинированным методом с давлением 355 кПа в абсорбционной части: В. М. Попов, С. Н. Сороко, В. И. Коивисар, К. В. Михайлов, И. Н. Червенко, Л. И. Тюляев, П. А. Платонов,
Б.П. Самарин и др.
Впервой половине 60-х годов ГИАП и его Днепродзержинский фи лиал в содружестве с Харьковским политехническим институтом, Днепро дзержинским химическим комбинатом и Невским машиностроительным заводом разработали энерготехнологическую схему производства азотной кислоты под единым давлением 740 кПа [13, 14]. Мощность такого агре
гата в 3 раза превышает мощность агрегата комбинированной системы с давлением при абсорбции 355 кПа. Особенностями этой схемы являют ся газотурбинный привод, компенсирующий затраты энергии на техноло гические нужды производства, высокотемпературная очистка отходящих газов на катализаторе, содержащем 2% палладия на окиси алюминия, до концентрации в них окислов азота 0,005 об.%. Установка не потреб ляет энергии со сторопы. В 1976 г. на таких агрегатах производилось 43% всей выпускаемой слабой азотной кислоты [13]. По мере накопле ния опыта в систему вносились некоторые изменения, улучшившие пока затели ее работы.
За создание этой системы производства азотной кислоты Государствен ная премия СССР была присуждена Л. И. Чериомордику, В. Е. Горфункелю, В. И. Атрощенко, В. В. Святухину, Г. А. Систеру, И. Ф. Балан дину, Н. И. Беляеву, Е. И. Добровольскому, М. А. Бочару, Г. М. Ко вальчуку и X. Т. Черняку.
Кроме высокотемпературной каталитической очистки отходящих газов от окислов азота, был предложен способ их очистки с помощью аммиака на алюмованадиевом катализаторе. Этот способ [15], разработанный Днепродзержинским филиалом ГИАПа (Г. А. Скворцов, А. И. Поджарский и др.), внедрен на агрегатах комбинированной системы с давлением 355 кПа в стадии абсорбции.
Однако удовлетворить возрастающие потребности в азотной кислоте на основе известных систем ее производства было невозможно вследствие недостаточной мощпости агрегатов, больших трудовых затрат, сравни тельно высокого расхода вспомогательных материалов, сырья и др.
Выполненные ГИАПом предпроектные проработки показали, что луч шими по сравнению с другими установками технико-экономическими по казателями обладает агрегат АК-72 с комбинированным давлением 425— 476 кПа в отделении конверсии и 1114—1276 кПа в отделении абсорб ции. В такой системе в качестве привода машинного агрегата служит газовая рекуперативная турбина. Существенными преимуществами уста новки АК-72 являются возможность ее комплексной автоматизации, ката литическая очистка газа, получение 60%-ной азотной кислоты, высокая степень конверсии аммиака, сравнительно небольшие потери катализато ра и др. Впесеиные в схему АК-72 дополнительные усовершенствования позволят примерно вдвое повысить производительность труда. В разра
ботке агрегата АК-72 приняли активное участие М. Л. Ферд, А. А. Солоха, В. В. Харламов, И. И. Яшугин, В. М. Азаренко и др.
При разработке новых систем производства азотной кислоты широко использовались данные исследований, выполненных ГИАПом, его филиа лами, кафедрами технологии неорганических веществ Харьковского по литехнического института (ХПИ) им. В. И. Ленина, Ленинградского тех нологического института, Московского и Днепропетровского химико-техно логических институтов и других институтов и организаций, связанных с практикой работы азотпой промышленности [14, 16—18]. К таким ис следованиям относятся: детальное изучение процесса окисления аммиака в окись азота, изыскание новых катализаторов для этого процесса, оцен ка факторов, интенсифицирующих абсорбцию окислов азота растворами азотной кислоты различной концентрации, определение закономерностей образования азотной кислоты в случае применения перфорированных тарелок, выявление особенностей массопередачи в процессе пленочной абсорбции и т. д.
Вследствие постоянного возрастания мощностей по производству сла бой азотной кислоты значительно увеличиваются потребности в катали заторах для окисления аммиака в окись азота. ГИАП в содружестве с Днепродзержинским и Северодоиецкпм химическими комбинатами раз работал новые композиции катализаторпых сплавов, содержащих пони женное количество платипы и родия по сравнению со стандартным ката лизатором ГИАП-1. Новые композиции содержат примерно 80% платины, 15% палладия, небольшое количество родия, а в сплаве № 5 —и добавку рутения. По степени конверсии аммиака катализаторы с пониженным содержанием платины и родия не отличаются от стандартного сплава, но по сравнению с ним более устойчивы к каталитическим ядам, имеют на 7—9% меньший вес и используются с пониженными на 15—25% по терями платиноидов [18].
В разработке и виедрепии этих катализаторов участвовали А. Л. Шнеерсон, В. А. Молчанов, М. Т. Ивахнепко, И. Н. Олейник, В. А. Арутюнян, Д. А. Алексеенко, Е. Т. Моргунова, 3. Ф. Харитонова, Б. М. Блох,
Н.В. Добровольская, А. Н. Зугап и др.
Одновременно для работы под повышенным давлением испытываются
двухступенчатые* катализаторы с целью замены части платппоидных сеток иа неплатиповые катализаторы. Эти исследоваппя проводят ГИАП, ХПИ, Северодонецкий химический комбинат и другие предприятия азотной промышленности. К настоящему времени в эксплуатации находится ряд контактных аппаратов с двухступенчатым катализатором, работающих под давлением 608—740 кПа. Одпой из задач, которую следует решить для двухступенчатого метода, является разработка более совершенной конструкции контактного реактора.
В 60-х годах ГИАП разработал уникальный способ производства особо чистой 70%-пой азотной кислоты, широко применяемой в полупро водниковой, радиотехнической промышленности и в других отраслях науки и техппкп. Особо чистую азотную кислоту получают в аппарату ре, выполненной из горного хрусталя пли материалов, по качеству близ ких к нему. Содержапие каждой из 20 апализируемых примесей в особо чистой кислоте составляет миллионные доли процента и ниже.
В довоенные годы |
по прямому |
синтезу крепкой |
азотпой кисло |
ты были выполнены |
лабораторные |
исследования. |
Построенная на |
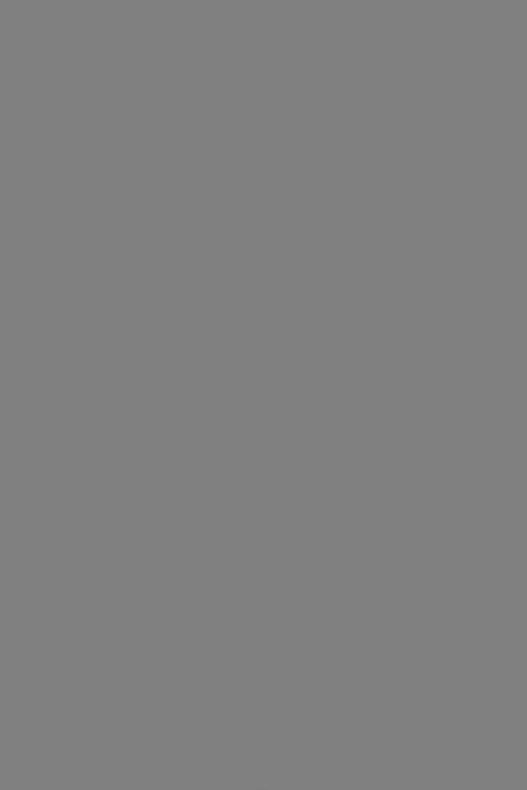
Горловском ГАТЗ небольшая опытная установка в связи с нача лом войны была разобрана. В 50—60-е годы было выполнено большое число исследований по прямому синтезу азотной кислоты. Кроме* того, проводились работы, посвящепные вопросам интенсификации процессов, протекающих при прямом синтезе крепкой азотной кислоты и при обра зовании слабой кислоты. Отметим следующие из этих исследований: абсорбция окислов азота концентрированной азотной кислотой, окисление окиси азота азотной кислотой, поглощение окислов азота в колоппах с ситчатыми тарелками, интенсификация процесса окисления окиси азота, определение условий образования азотной кислоты, процесс непрерывно го автоклавирования крепкой азотной кислоты, физико-химические свой ства растворов азотной кислоты, содержащих окислы азота, равповесие между окислами азота л раствором азотной кислоты, кинетика абсорб ции окислов азота и др.
Производство крепкой азотной кислоты с помощью концентрирован ной серной кислоты (купоросного масла) в послевоенный период почти не претерпело изменений. Выполненные А. В. Тихоновым фундаменталь ные исследования по этому способу и до настоящего времени не утратили своего значения [19].
Ужесточение норм отвода отработанных газов в окружающую среду вызвало необходимость изыскания новых способов производства крепкой азотной кислоты, главным образом с водоотнимающими веществами [20]. Одним из таких способов является применение* в качестве водоотиимающего средства 72—74%-пого плава нитрата магния или его смеси с нитра том кальция. Данный способ, разработанный ГИАПом, по сравнению с использованием купоросного масла экономически более выгоден, проще в аппаратурном оформлении и, что весьма важно, исключает выброс вред ных газов в окружающую среду.
ГИАП разработал также совмещенный способ одновременного полу чения в одном технологическом процессе слабой и крепкой азотной кис лоты. Проводятся исследования получения азотной кислоты промежуточ ной концентрации (80—90%-ной). В связи с переходом на работу с крупными агрегатами, с большими массами аммиака, природного и дру гих газов разработан ряд новых технических решений, обеспечивающих взрывобезопаспость и безаварийность в производствах азотной кислоты.
Выполненные за последние годы работы по развитию производств азотной кислоты н азотсодержащих продуктов подробно освещепы в ис точниках [21, 22]. Здесь только отметим, что в одиннадцатой пятилетке продолжается освоение ряда крупнотоннажных агрегатов азотной кисло ты, работавших по схеме АК-72, и намечено ввести в эксплуатацию еще 4 таких агрегата.
НИТРАТНЫЕ СОЛИ
В народном хозяйстве СССР применяют около тридцати солей азотной кислоты —нитратов. Они используются во многих отраслях промышлен ности, а некоторые из них и как удобрения в сельском хозяйстве.
В дореволюционной России, за исключением небольших количеств нитрата аммония (аммиачной селитры)2 нитраты не производились.
2 См. гл. 9 в настоящем томе, раздел «Аммиачная селитра».
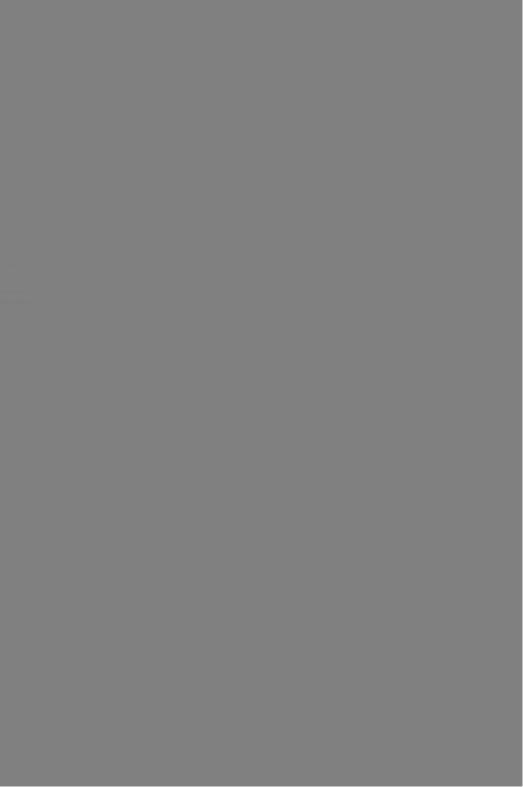
В данной главе кратко освещаются возникновение, современное со стояние и перспективы развития в ближайшие годы производств нитра тов калия, кальция и натрия, широко применяемых в промышленности и, в относительно небольших количествах, в сельском хозяйстве.
Нитрат калия. К о н в е р с и о н н ы й м е т о д [23, 26—28]. В настоя щее время нитрат калия применяется в разных отраслях промышленно сти (в производствах порохов и пиротехнических средств, в виде добавки при производстве стекла, для консервирования пищевых продуктов ит. д.). Как удобрение нитрат калия применяется для садовых, цветочных, цит русовых и других культур, па которые отрицательно действуют хлорсо держащие удобрения.
В сравнении с другими солями калия и азотной кислоты нитрат калия имеет преимущество, так как одновременно содержит азот и калий, в которых нуждаются растения. По физическим свойствам нитрат калия также имеет преимущества —он долго сохраняет сыпучесть, практически негигроскопичен и т. п. К недостаткам нитрата калия как удобрения относят «неуравновешенность» в нем питательных элементов (на 46,5% окиси калия приходится только 13,7% азота). В связи с этим рекомен дуют применять нитрат калия одновременно с фосфорными удобрения ми: при этом его агрохимический эффект значительно выше.
В дореволюционной России и примерно до 30-х годов нитрат калия приходилось импортировать и получать нейтрализацией слабой азотной кислотой остро дефицитных щелочей —поташа или гидроокиси калия. В небольшом количестве нитрат калия добывали в Средней Азии. Отсюда его доставляли на завод для очистки от примесей путем перекристалли зации. На одном из предприятий в начале 30-х годов работала небольшая установка, на которой получали нитрат калия обменным разложением чилийской селитры и хлористого калия.
В 1932 г. на Сталинском азотном заводе группой исследователей были проведены лабораторные и полузаводскпе опыты по получению нитрата калия из растворов синтетического нитрата патрпя и твердого хлористого калия. Был найден оптимальный режим конверсии псходпых солей с целью максимального выделения в донную фазу образующегося хлори стого натрия, определены зависимости между составами маточных раство ров и содержанием хлоридов в первичных кристаллах нитрата калия при их кристаллизации, найдены условия для разрушения примесей нитритов путем добавки небольших количеств аммиачной селитры.
Накопленные экспериментальные данные позволили силами инжене ров Сталинского азотного завода разработать проект крупного для того времени производства нитрата калия (5 тыс. т/год). По качеству полу чаемый питрат калия был близок к продуктам реактивной чистоты.
Исследования, проектирование, строительство цеха по производству нитрата калия и его освоение запяли около трех лет (с 1932 по 1934 г.). Присланная на Сталинский азотпый завод, по указанию Г. К. Орджони кидзе, комиссия Наркомтяжпрома высоко оценила работу коллектива завода по организации производства нитрата калия.
В настоящее время вопросу развития производства нитрата калия придается большое значение. Завершается освоеппе крупнотоннажного производства нитрата калия, построенного вместо двух производств мень шей мощности.
К а т и о н н ы й м е т о д . ГИАП разработал метод получения нитрата калия катионным обменом [29—31] в творческом содружестве с Берез никовским АТЗ.
По проекту ГИАПа на Березниковском АТЗ в 1960 г. был построен и пущен в эксплуатацию крупный опытно-промышленный цех получения нитрата калия методом катионного обмена. Процесс производства нитра та калия катионным методом прост по технологии и аппаратуре, не тре бует дефицитных щелочей или крепкой азотной кислоты и т. п.
Катионный метод имеет значительные потенциальные возможности для увеличения выработки нитрата калия за счет замены катионита с малой емкостью на катионит большей емкости и установки в стадии катпонирования современных конструкций катионовых реакторов. Недо
статком |
катионного |
метода получения |
нитрата калия (или |
нитрата |
|||
натрия) |
является образование сточных вод, содержащих хлориды. |
|
|||||
П р я м ы е м е т о д ы [23, |
32—3 5 ] —получение |
нитрата |
калия |
из |
|||
азотной |
кислоты или |
окислов |
азота и |
хлористого |
калия — много |
лет |
привлекают внимание исследователей и инженеров, работающих в облас ти связанного азота. Однако применение этих методов связано с трудно стями, с которыми столкнулись исследователи при переработке образую щихся при прямых методах газов, паров и побочных растворов.
Всоставе газовой фазы обычно содержатся хлористый нитрозил, молекулярный хлор, окислы азота и пары азотной и соляной кислот; полученные растворы содержат нитрат калия, азотную и соляную кисло ты, хлористый калий и примеси, вносимые с сырьем.
Много затруднений выявилось и при конструктивном оформлении аппаратуры из-за высокой коррозиопиой среды, в которой протекают процессы прямых методов.
Внашей стране проведены обстоятельные исследования по разным
вариантам прямых методов, выполненные в лабораторных условиях. В 1942 г. на Кемеровском АТЗ была построена опытная установка по
получению нитрата калия по одному из вариантов прямого способа. Край не необходим был нитрат калия в связи с временной потерей цеха на Сталинском азотном заводе.
На установке Кемеровского АТЗ нитрат калия получали из 45% -ной азотной кислоты и твердого хлористого калия при 75°С и избытке азот ной кислоты (10—20% по сравнению со стехиометрией). Установка работала без использования газов, которые отводились в атмосферу. Часть маточных растворов сбрасывалась после нейтрализации в заводскую канализацию. За время войны на установке методом прямого синтеза было выработано около 1,5 тыс. т технического нитрата калия.
Опыт работы на этой установке показал, что без использования маточных растворов выход нитрата калия не превышает 70—72%. После восстановления цеха нитрата калия на Сталинском азотном заводе уста новка Кемеровского АТЗ как нерентабельная и временная была демон тирована.
На Березниковском АТЗ небольшое количество нитрата калия при шлось получать нейтрализацией весьма дефицитной гидроокиси калия сла бой азотной кислотой. При этом часть маточных растворов отводилась в канализацию.
В 60-х годах в Северодонецком филиале ГИАПа начаты исследова тельские и предпроектные работы по одновременному получению прямым
методом нитрата калия в качестве удобрения и товарного жидкого хлора. После отработкп намеченного технологического и конструктивного оформления процесса по получению калиевой селитры будет выдана проектная документация на создание головного крупнотоннажного произ
водства нитрата калия по схеме прямого спитеза.
Нитрат кальция [27, 28, 36]. В последние годы нитрат кальция стал применяться не только как щелочное удобрение, но и в промышленности для получения повых веществ в сочетании с другими солями.
Несмотря на неудовлетворительную характеристику нитрата кальция (низкое содержание азота, сильная гигроскопичность и др.), многие агрохимики считают его универсальным удобрением, весьма полезным для почв нечерноземной зоны, бедных известью. По своему агрономиче скому действию па некоторые сельскохозяйственные культуры нитрат кальцин в ряде случаев не только не уступает натриевой селитре, но даже превосходит ее.
Раньше нитрат кальция как удобрение широко применялся за рубе жом. В настоящее время доля его в мировом выпуске азотпых удобре ний не превышает 1%.
В нашей стране нитрат кальция в виде товарного продукта получают только поглощением окислов азота низкой концентрации известковым молоком.
Еще в начале 30-х годов на Сталинском азотном заводе были смон тированы две полузаводские установки для исследования процессов полу чения нитрата кальция. На одной установке в качестве сырья применялся кусковой известняк и азотная кислота, а на другой —окислы азота (ГТО+ГЮо до 1,2%) н известковое молоко. На первой установке опыты проводились сотрудниками Государственного института азота (ГИА), на второй —сотрудниками Сталинского азотного завода. На обеих установ ках были получены данные, отсутствующие в литературе и необходимые для проектирования процессов производства нитрата кальция по двум вариантам: с применением известняка п известкового молока.
В 1951—1952 гг. на полузаводской установке, построенной на Днепро дзержинском АТЗ были проведены опыты по накоплению новых данных, касающихся оптимального режима работы при улавлпвапии окислов азота известковым молоком разной концентрации. Получепные резуль таты были использованы при проектировании для Днепродзержинского АТЗ изменений в ранее построенном промышленном цехе питрата каль ция. В дальнейшем это производство было частично модернизировано.
Из-за громоздкости абсорбционной части производства, ее низкой про изводительности, особенно в летнее время, и других недостатков системы поставлена задача вторично модернизировать существующее или строить
новое производство |
нитрата кальция с |
учетом возросших потребностей |
в этом продукте. |
[28, 36] используется |
для получения ряда нитратов |
Нитрат натрия |
(калия, бария, стронция и др.), как одпп из видов сырья п как добавка в производствах некоторых взрывчатых веществ, составов для чистки металлов или их закалки и т. д.
В сельском хозяйстве нитрат натрия (натриевая селитра) применяет ся в несколько большем количестве, чем другие щелочные питраты, яв ляясь быстродействующим высокоэффективным удобрением, особенно полезным на кислых почвах.