
книги / Развитие химической промышленности в СССР (1917-1980). Т. 2 Развитие отдельных отраслей химической промышленности
.pdfВ СССР изучение методов производства нитрата натрия было начато в 1924—1925 гг. одновременно с организацией иа Сталинском азотном заводе первой установки по производству нитрита натрия, который в то время импортировался из Германии. Накопление маточных растворов в этом производстве и «свежих» нптрит-нитратпых растворов привело к изучению стадии их переработки в нитрат натрия. Почти все исследо вания по нитрату натрия (например, по ииверсин нитритов в нитрат) были выполнены лишь после строительства отделений щелочного погло щения окислов азота в производствах азотной кислоты, работающих при атмосферном давлении (1930—1934 гг.).
Напомним, что нитрат натрия можно получать нейтрализацией азот ной кислотой пли окислами азота кальцинированной соды или, в виде исключения, гидроокиси натрия; прямым методом из азотной кислоты промежуточной концентрации и хлористого натрия; катионным обменом из кальциевой селитры и хлористого натрия, а также некоторыми кон версионными методами. Однако шесть действующих производств нитрата натрия до недавнего времени базировались только на поглощении раство ром кальцинированной соды окислов азота низкой концентрации (до 1— 1,2%). При этом из получаемых нитрнт-питратных растворов сначала выделяется примерно 40% товарного нитрита натрия, а остальное его количество инвертируется до нитрата натрия. С учетом того, что азотнокислотные производства, работающие при атмосферном давлении, по ряду причин намечается демонтировать, окислы азота низкой концентрации не будут применяться в производствах нитрита и нитрата натрия. Для про изводства этих продуктов предусматривается строительство крупнотон нажных агрегатов с применением концентрированных окислов азота (9,5—10% N0). Один из таких агрегатов построен в десятой пятилетке и эксплуатируется. Переработка получаемых нитрит-нитратных раство ров в крупнотоннажных агрегатах в отношении нитрата натрия мало от личается от указанной выше. Крупнотоннажные агрегаты по производ ству нитрита и нитрата натрия позволят снизить себестоимость этих продуктов.
ГЛАВА ТРЕТЬЯ
СЕРНАЯ КИСЛОТА
Области применения серной кислоты настолько широки, что часто об общем состоянии химической промышленности судят по масштабу вы пуска этой продукции. Основным ее потребителем является производство минеральных удобрений, где расходуется ~50% всей вырабатываемой кислоты.
Еще в 1900 г. Д. И. Менделеев отмечал, что серная кислота употреб ляется преимущественно для производства бездымного пороха, очпщенпя нефтяных продуктов и получения суперфосфата [1]. В настоящее же время области ее применения очень широки, они представлены па рисунке.
Для выработки серной кислоты используется довольно широкий ассортимент сырья. Наряду с серным колчеданом применяют серу, отхо дящие серусодержащие газы цветной металлургии, сероводород и др. Все возрастающее значение приобретает сера, с 1965 по 1980 г. производство серной кислоты из серы в СССР повысилось с 28,2 до 49,3%.
Промышленное производство серной кислоты осуществляется двумя способами: контактным и нитрозпым. При коптактпом способе серпнстый ангидрид, образующийся при сжигании серусодержащего сырья, окис ляют до серного ангидрида кислородом воздуха с применением катали затора; при нитрозиом способе передатчиком кислорода служит нитроза (раствор окислов азота в серной кислоте). Ранее существовало два нитрозных способа: камерный и башенный. Камерным способом в настоящее время серную кислоту не получают, производство продукта башенным методом постоянно сокращается.
Контактным методом вырабатывают концентрированную серную кис лоту (92,5—94,0%-ную) и олеум, содержащий 19,0—24,0% свободного серного ангидрида, а башенным —75%-иую серную кислоту.
Развитию контактного метода способствовал все возрастающий спрос на концентрированную серную кислоту высокого качества, в которой пуждались производство химических волокон и ряд отраслей органиче ского синтеза.
Стадия катализа требует тщательной очистки обжигового газа, что связано с дополнительными затратами. Экономичность переработки при родной серы при контактном методе, а также возможность более тща тельной очистки отходящих газов в контактном процессе по сравнению с башепным способствовали преобладанию контактного метода.
Дореволюционная Россия по производству серпой кислоты занимала одно из последних мест. Выработка серной кислоты в 1913 г. составляла лишь 121 тыс. т (в пересчете на моногидрат —100%-пую Н230 4). Перт вая мировая война потребовала значительного увеличения производства серной кислоты для изготовления взрывчатых веществ, для текстильной промышленности и др. В связи с этпм за годы войны было построено 28 крупных для того времени контактных и камерных сернокислотных установок. Всего в этот период в России серпая кислота вырабатывалась па 57 заводах. Производственная мощпость всех сернокислотных пред приятий в 1917 г. достигла 432 тыс. т в моногидрате. В годы граждан ской войпы многие сернокислотные заводы вышли из строя и выпуск серпой кислоты значительно снизился. В 1921/22 г. началось восстанов-
ление разрушенной химической промышленности. В 1928/29 г. производ ство серной кислоты достигло 242 тыс. т [2].
Потребности сельского хозяйства в минеральных удобрениях и спрос на серную кислоту в других отраслях промышленности стимулировали дальнейший рост ее выпуска. Успехи машиностроительной и металлурги ческой промышленности обеспечивали возмояшости строительства круп ных башенных систем и интенсификации их работы, а затем и развитие контактного способа.
В годы первой пятилетки в СССР производство серной кислоты суще ственно увеличилось и в 1932 г. составило 0,54 млн. т. Все сернокислот-
ные заводы работали на уральском рядовом серпом колчедане. К концу пятилетки увеличилась доля использования колчеданных флотационных хвостов, которые сернокислотной промышленности поставляла цветная металлургия. В эти годы 46% серпой кислоты изготовляли еще на камер ных установках, 19% —на башенных и 35% —на контактных.
Первая башенная система в СССР была введена в строй в 1927 г. на Урале. В первой пятилетке были построены башенные заводы в Ленинграде, Подмосковье, на Украине, в Донбассе и Приуралье. К концу пятилетки в эксплуатацию были введены крупные установки на Нев ском и Воскресенском суперфосфатных заводах. В 1931 г. профессор В. И. Шульц провел исследования по интенсификации башенных систем, результаты которых позволили увеличить съем башенной кислоты до 35—37 кг с 1 м3 объема башен.
Одновременно с башенным методом развивался и контактный. Пер выми контактными системами в СССР были «тентелевские», так как схе ма технологического процесса и аппаратурное оформление, применяемые на Тентелевском заводе, были признаны в то время наиболее рациональ ными. Поэтому тентелевские установки получили широкое распростране
ние не |
только в |
России, но и за рубежом. |
Так, в 1917 г. |
в России |
таких |
установок |
было 20, во Франции —18, |
в Англии —8, |
США — 3 |
и в Японии — 2. |
|
|
|
Однако тентелевские системы не позволяли увеличить объем произ водства серной кислоты в соответствии с возраставшими потребностями страны. Поэтому в годы первой пятилетки их заменяли более совершен ными и мощными системами Герресгоффа—Байера производительностью до 10 тыс. т/год. К этому времени относится разработка профессором Н. Ф. Юшкевичем метода изготовления ванадиевого катализатора, кото рый к началу второй пятилетки целиком вытеснил платину.
В1931 г. советскими учеными (И. Е. Ададуров и др.) была установ лена возможность получения серной кислоты путем каталитического окисления сернистого газа, содержащего пары воды. Этот процесс, на званный методом мокрого катализа, применяли при получении серной кислоты из сероводорода сначала в Германии, а затем в других странах. Однако приоритет в разработке метода мокрого катализа принадлежит советским ученым.
В1930-е годы строили башенные и контактные системы. Основным
сырьем для получения серной кислоты служили колчеданные флотацион ные хвосты —отходы медеплавильной промышленности. Сера еще не при менялась в связи с относительно небольшой ее добычей (в районах Сред ней Азии и на Волге).
В 1936 г. состоялось совещание работников сернокислотной промыш ленности, где были намечены мероприятия по внедрению опыта лучших заводов, повышению производительности труда, интенсификации суще ствующих предприятий и строительству новых.
Для повышения производства зерна и технических культур требова лось большое количество удобрений и, следовательно, серной кислоты для расширения их производства. Перед сернокислотной промышленностью стояла задача строительства новых заводов, главным образом на базе использования отходящих газов цветной металлургии.
Доля башенной кислоты составляла в 1939 г. 70% от всей вырабаты ваемой кислоты. В предвоенные годы советские ученые продолжали пс-
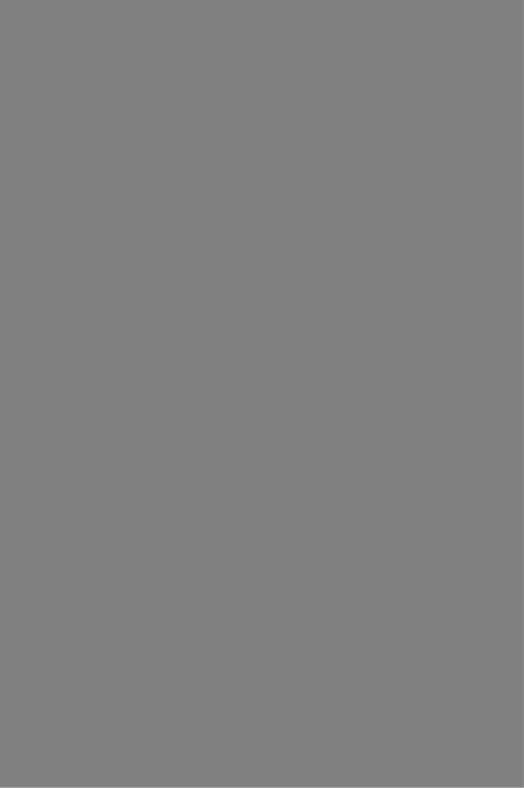
серной кислоты вследствие немецко-фашистской оккупации снизились до ~77%, развернулось строительство новых заводов в восточной и средне азиатской частях СССР; некоторые из них использовали в качестве сырья серу.
С повышением спроса па концентрированную серную кислоту разви вался контактный метод и интенсифицировалась работа установок для концентрирования кислоты. Мощность контактных заводов увеличива лась за счет строительства новых и коренной реконструкции старых, интенсификации всех операций производства серной кислоты, основан ной па глубоком теоретическом изучении процесса. В 1942 г. за успехи в развитии контактного процесса советским ученым Г. К. Борескову и А. Г. Амелину была присуждена Государственная премия СССР.
Послевоенный период (1946—1958 гг.) характеризуется дальнейшим ростом сернокислотного производства. К 1946 г. были восстановлены все заводы и их мощность превышала довоенную. В 40-е годы создаются печи с кипящим слоем для обжига сульфидного сырья и продолжаются работы по усовершенствованию ванадиевой контактной массы. В начале 50-х годов новый ванадиевый катализатор прошел испытания в промыш ленных условиях на Воскресенском химическом комбинате.
в |
На основе исследований по кинетике окисления сернистого ангидрида |
|
серный |
была разработана методика расчета контактных аппаратов |
|
[3, |
с. 273] |
и созданы контактные аппараты с промежуточным теплооб |
меном мощностью до 240 т/сут. Работы по исследованию катализа, коптактных масс и контактных узлов велись советскими учеными Г. К. Ве ресковым, М. Г. Слипько, И. П. Мухлеиовым, В. В. Илларионовым, Д. Ф. Терентьевым и др.
Проводилось изучение процессов очистки, осушки и абсорбции газов в контактной системе; установлен ряд кинетических зависимостей для процесса абсорбции серного ангидрида моногидратом и олеумом, изучены условия образования тумана, что позволило предотвратить или снизить образование тумана серной кислоты, который связывался с мышьяком и селеном в промывпом отделении и увеличивал потери серы в процессе абсорбции. Эта работа в 1951 г. была удостоепа Государственной премии
СССР [4]. На основании получеппых результатов были разработаны новые методы очистки обжигового газа, оптимальный режим абсорбции влагосодержащего газа («горячий режим»), позволявший снизить до ми нимума образование тумана, изучалась конденсация паров серной кисло ты, оптимальный режим концентрирования серной кислоты и др.
Несмотря па рост масштабов производства, серной кислоты в стране нехватало. Директивы XIX съезда КПСС предусматривали высокие тем пы увелпчепия выпуска минеральных удобрений —основного потребите ля серной кислоты [5].
Кроме колчедапа и колчеданных флотационных хвостов, в качестве сырья для производства серпой кислоты стали широко использовать газы металлургических печей и серу. На западе Украины была организована добыча элементной серы, что дало возможность строить контактные заво ды по так называемой короткой схеме. На этих предприятиях применяли «горячий» режим абсорбции, предотвращающий образование тумана в связи с наличием в природной сере битумов.
С развитием нефтеперерабатывающей и коксохимической промышлен ности появилась необходимость использовать для производства серной
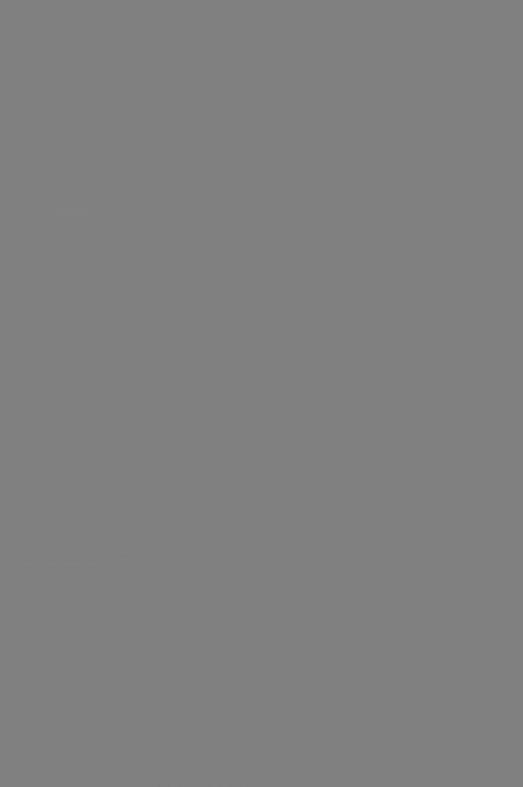
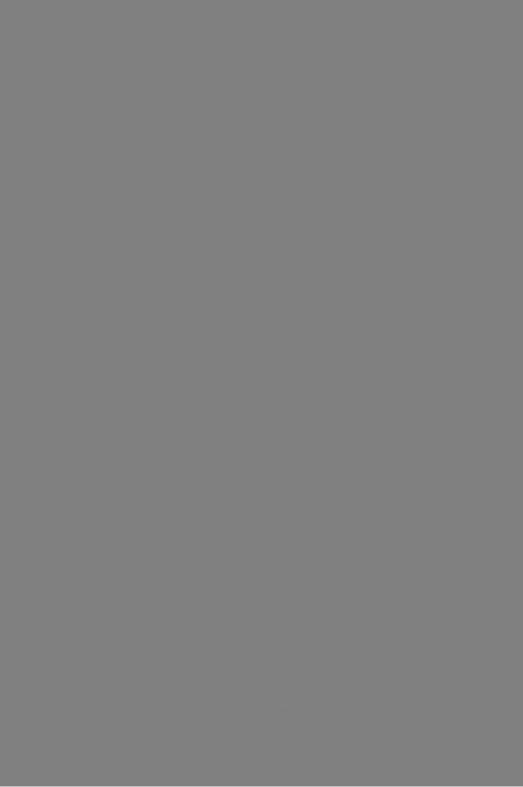
С 1972 г. действовала только одна промышленная установка под дав лением 506 кПа [7], которая использовала существующий способ с от дельными усовершенствованиями непринципиального характера; в этом направлении проводятся исследования [8]. Таким образом, первый опыт пока не получил широкого распространения.
Преимущество процесса под давлением состоит в том, что при этом увеличивается интенсивность основных аппаратов пропорционально по вышению давления, снижается расход катализатора, улучшаются усло вия отвода выделяющегося тепла и др. Однако применение давления не устраняет недостатки существующего способа, и основной из них заклю чается в том, что степень использования выделяющегося в процессе теп ла с получением энергетического пара составляет около 60%. Таким образом, остальное тепло не только не используется, но на его вывод из процесса затрачивается энергия со стороны в виде охлаждающей воды. Так же, как и при существующем способе, при работе под давлением объем отходящих газов составляет около 2000 пм^т'"1 и, следовательно, велик выброс вредных примесей в атмосферу. При работе под давлением значительно затрудняется создание автоматизированного производства.
Основное достоинство производства серной кислоты по циклической схеме с применением кислорода состоит в том, что процесс осуществ ляется на основе замкнутого технологического цикла. При этом практи чески полностью используются сырье и выделяющееся тепло, а объем отходящих газов сокращается в 40—50 раз и соответственно уменьшает ся выброс вредных примесей в атмосферу. Малое число аппаратов, а так же отсутствие насосов и холодильников для циркуляционной серной кис лоты облегчает ведение процесса под давлением и обеспечивает возмож ность создания автоматизированного производства.
В настоящее время в Советском Союзе ведутся лабораторные, полузаводские и опытпо-промышленные работы по освоению каждого из ука занных направлений; результаты этих исследований позволят определить пути развития производства серной кислоты на период до 1990 г.
ГЛАВА ЧЕТВЕРТАЯ
ФОСФОР И ФОСФОРСОДЕРЖАЩИЕ ПРОДУКТЫ
Фосфор и его многочисленные соединения широко применяются в раз личных отраслях народного хозяйства: в металлургии, нефтехимии, при органическом синтезе, для водоочистки в качестве аптнпакипипов и анти пиренов, для защиты металлов от коррозии, образования дымов, как само воспламеняющиеся и сигнальные средства. Фосфорные соединения эффек тивно используются в сельском хозяйстве и в некоторых пищевых и био химических производствах, в медицине, при получении средств для борь бы с вредителями и болезнями растений и животных.
О начале производства фосфора в России можно судить по времени возникновения спичечных фабрик, которые являлись единственными по
требителями фосфора. Производство спичек в |
России началось в |
||
1837 г. [1]. |
|
|
|
В конце XIX столетия в стране действовало уже более десятка фос |
|||
форных заводов. До 1901 г. Россия вырабатывала |
около |
183 т |
фосфора |
в год кислотно-термическим способом и, занимая |
третье |
место |
в мире, |
не только полностью удовлетворяла внутреннюю потребность в фосфоре, но и экспортировала его.
В 1891 г. за рубежом появился новый, более экономичный и менее вредный, электротермический способ производства фосфора, быстро вы теснивший несовершенный кислотно-термический. Однако старый способ применялся до 1926 г. После прекращения выпуска фосфора в начале первой мировой войны его получение этим способом было возобновлено в 1915 г. в Троицке в связи с необходимостью обеспечить военные нуж ды. В том же году у нас в стране было организовано товарищество «Русский фосфор», начавшее в 1916 г. производство фосфора иа ст. Померанья (Петроградская губерния). Вскоре после Февральской револю ции завод в Померанье был закрыт, а завод в Троицке проработал до 1926 г. [2], когда было начато производство фосфора электротермическим способом.
В 1921 г. в Москве в Научном институте по удобрениям (НИУ) С. И. Вольфкович и Е. И. Жуковский под руководством Э. В. Брицке выполнили исследования электровозгопки фосфора из дробленого куско вого фосфорита [3]. Применение в качестве сырья фосфоритов явилось прогрессивным шагом в новой технологии фосфора. В этих опытах были установлены технологические параметры процесса, использованные для проектирования иа Чериоречепском химическом заводе первого электро термического цеха по производству фосфора.
Вто же время в Ленинградском технологическом институте (ЛТИ)
В.Я. Курбатов и Е. И. Богоявленский завершили аналогичные исследо вания. Результаты были переданы ГИПХу. Иа опытном заводе ГИПХа сооружались две однофазные печи для электровозгопки фосфора. В каче
стве сырья в проекте предполагалось использовать обожженную кость. В 1926 г. вошли в строй два электротермических фосфорных цеха:
один иа Чернореченском химическом заводе, другой -- па опытном заводе ГИПХа в Ленинграде. В фосфорном цехе Черноречепского завода перво начально были установлены две одпофазные электропечи мощностью