
книги / Развитие химической промышленности в СССР (1917-1980). Т. 2 Развитие отдельных отраслей химической промышленности
.pdfболее мощными п пригодными для упаривания менее концентрированных растворов.
Установка дополнительных доупарочных аппаратов в действующих цехах оказалась возможной благодаря тому, что при замене миогосекционных горизонтальных вакуум-выпарных аппаратов вертикальными (см. выше) освободилась площадь в надстройках грануляционных башен. И все же при реконструкции выпарных установок встретились серьезные трудности, тем более что строительно-монтажные работы на большой высоте приходилось выполнять на ходу, останавливая поочередно на минимальное время по одной грануляционной башне.
В 1966—1970 гг., когда доупарочные аппараты внедрили повсеместно, влажность селитры удалось резко снизить, качество существенно улуч шилось.
В результате длительных испытаний, проведенных ГИАПом и Грод ненским химическим комбинатом, с 1970 г. в промышленность была внед рена также добавка раствора сульфата аммония, вводимая в селитру из расчета содержания в готовом продукте 0,4% (ГШ4) 2 8 0 4 (гранулы селитры с этой добавкой опрыскиваются раствором диспергатора ЫФ). Еще ранее промышленные испытания подтвердили эффективность до бавки раствора нитрата магния3 получаемого разложением каустиче ского магнезита азотной кислотой, которая была впервые внедрена на Куйбышевском азотно-туковом заводе.
Совершенствование грануляторов продолжалось. Сумский филиал Харьковского политехнического института организовал изготовление центробежных секционных грануляторов, внедренных в Невинномысске (1970 г.), Днепродзержинске (1971 г.), Ангарске, Чирчике и т. д., а в дальнейшем —вращающихся виброгрануляторов, освоенных впервые в Невинномысске и в Гродно в 1977 г. [12]. Невинпомысский и Гроднен ский химические комбинаты в 60—70-е годы внесли наибольший вклад в совершенствование технологии аммиачной селитры. Аммиачная селит ра, выпускаемая Гродненским химическим комбинатом, в 1974 г. аттесто вана по высшей категории качества. Знак качества присвоен в 1976 г. аммиачной селитре ПО «Куйбышевазот». В 1972—1973 гг. этим заводом успешно проведены испытания длительного хранения аммиачной селитры насыпью в крупных буртах (до 1200 т), а в 1974 г. опробована пере возка селитры в саморазгружающихся вагонах типа хоппер-цементовоз. Однако бестарные отгрузки для сельского хозяйства до 1979 г. широкогоразвития не получили.
Потребители оценили преимущества бестарного метода, позволяющего экономить дефицитную тару и полностью механизировать разгрузочные работы. С 1972 г. Гомельский химический завод начал хранить селитру,, поставляемую насыпью.
Систематические наблюдения центральной лаборатории Гомельского химического завода [13] за состоянием буртов незатаренпой селитры, выработапной Днепродзержинским ПО «Азот» (с добавкой ДЛМ), в за крытом складе на протяжении двух месяцев показали отсутствие слеживаемости и сохранность гранул. С августа 1977 г. Днепродзержинское
ПО «Азот», а с декабря 1978 г. и Кемеровское |
ПО «Химпром» |
начали |
|
3 Первые отечествеппьте |
работы по изучепию влияния |
добавки магния |
относятся |
к концу 40-х годов (см. |
[11]). |
|
|
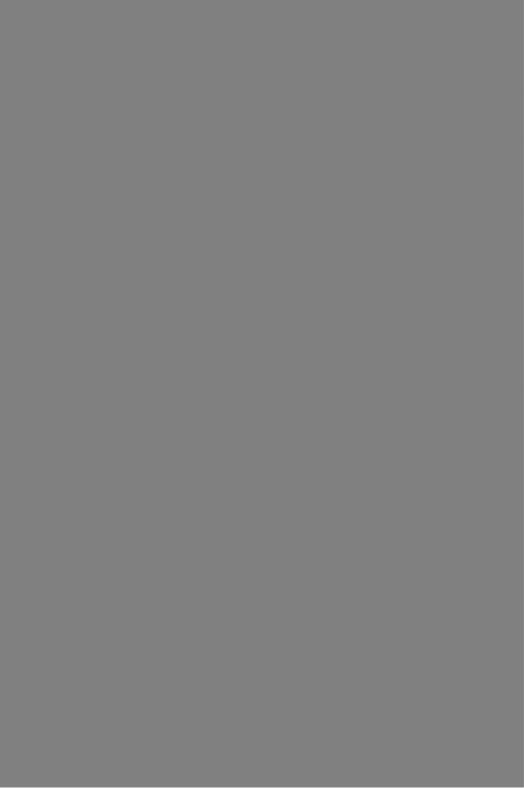
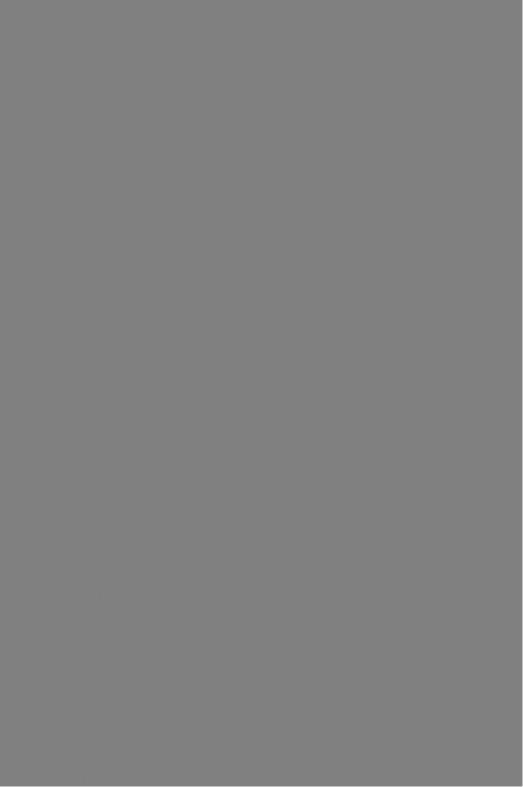
-секционный промывной скруббер. Секционное устройство охлаждающего аппарата и скруббера позволяет регулировать процесс охлаждения, а так же расход воздуха на гранулирование. На башнях установлено по шесть грануляторов, преимущественно акустических вибрационных конструк ций НИИхиммаш —ГИАП, которые в сочетании с интенсивными охлаж дающими аппаратами обеспечивают отличпый гранулометрический состав.
В агрегате АС-67 применяется |
|
|
|
|
|
||||||||
сульфатная добавка, в агрегате АС-72 |
|
|
|
|
|
||||||||
наряду |
с |
сульфатной —фосфатно |
|
|
|
|
|
||||||
сульфатная |
добавка, |
разработапная |
|
|
|
|
|
||||||
ГИАПом |
совместно |
с Невшшомыс- |
|
|
|
|
|
||||||
ским |
химическим |
комбинатом |
[14], |
|
|
|
|
|
|||||
представляющая собой раствор суль |
|
|
|
|
|
||||||||
фата и фосфата аммония, вводимых |
|
|
|
|
|
||||||||
соответственно в |
количестве 0,1—0,2 |
|
|
|
|
|
|||||||
и 0,3% (в пересчете на Р20 5) от веса |
|
|
|
|
|
||||||||
селитры. |
|
После |
охлаждения |
до |
|
|
|
|
|
||||
~45° |
С |
|
гранулы |
опрыскиваются |
|
|
|
|
|
||||
раствором диспергатора НФ. В обоих |
|
|
|
|
|
||||||||
агрегатах АС-67 и АС-72 управление |
|
|
|
|
|
||||||||
основными процессами автоматизиро |
1940 |
1950 |
1960 |
1970 |
1980 |
||||||||
вано и осуществляется с центрально |
|
|
Годы |
|
|
||||||||
го пульта. |
|
|
|
|
|
|
|
|
|
|
|||
К |
началу |
1980 г. на долю круп |
РОСТ ОБЪЕМА ПРОИЗВОДСТВА АММИАЧНОЙ |
||||||||||
СЕЛИТРЫ |
|
|
|
|
|||||||||
ных |
агрегатов |
приходилось 37% об |
|
|
|
|
|||||||
В скобках указано количество действую |
|||||||||||||
щей мощности по производству ам |
|||||||||||||
щих цехов |
|
|
|
||||||||||
миачной |
|
селитры. |
Продолжалось |
|
|
|
|
|
строительство новых агрегатов АС-72
иодновременно разрабатывался третий вариант крупного агрегата АС-85. Процесс интенсификации и совершенствования, непрерывно осуществ
ляемый в основных технологических стадиях производства, особенно крупных агрегатов, в меньшей степени коснулся конечных, наиболее трудоемких стадий —упаковочного и складского хозяйств.
В 1968 г. в связи с ростом объема производства была увеличена до пустимая емкость заводских складов до 15 тыс. т (два склада из трех отсеков по 2,5 тыс. т каждый) \ Однако использование складской пло щади затруднялось из-за отсутствия эффективной механизации. Основ ным средством механизации стала впервые изготовленная Невиииомысским химическим комбинатом трехзвеиная погрузочная машина, позво ляющая подавать мешки с селитрой в любую точку вагона. При непрерывной подаче вагонов погрузочная машина сводила к минимуму затраты труда. При отсутствии вагонов продукт приходилось хранить на складе. Аккумуляторные погрузчики не позволяли полностью механизи ровать складские работы —мешки на поддоны укладывались вручную.
Во второй половине 60-х годов пачали применять полиэтиленовые мешки, обеспечивающие по сравнению с битумпрованными бумажными лучшую сохранность селитры.
В 1969 г. ввели в эксплуатацию крупный склад для хранения 82%-ного раствора селитры емкостью 10 тыс. т на Ангарском нефтехи-
4 До 1961 г. строились склады до 500 т, а с 1961 г.— до 1500 т.
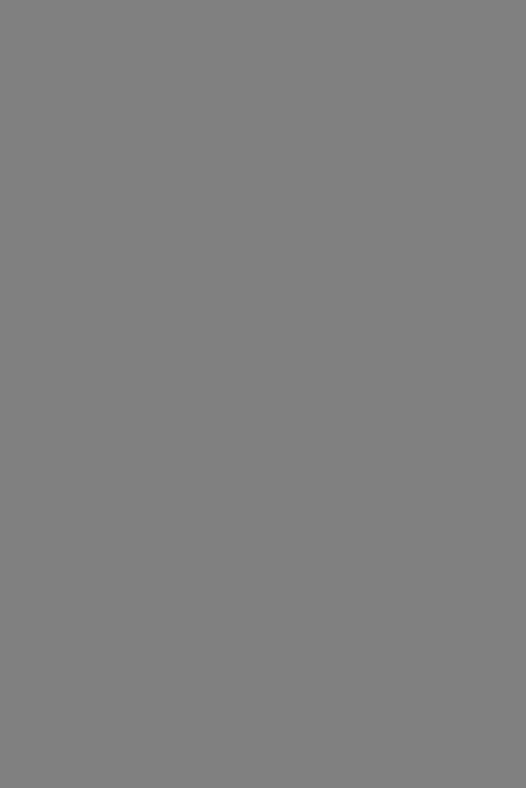
В. Я. Соболева, Г1. И. Сысоев, Г. Ф. Ткаченко, В. М. Халепа, Г. С. Храпунов и др.
Претворяя в жизнь решения XXVI съезда КПСС, строители, монтаж ники и эксплуатационники в одиннадцатой пятилетке вводят и осваи вают крупные агрегаты по производству высококачественной аммиачной •селитры в различных районах Советского Союза, чем вносят весомый вклад в выполнение Продовольственной программы СССР.
КАРБАМИД
Карбамид —продукт взаимодействия двуокиси углерода с аммиаком — широко применяется в различных отраслях народного хозяйства.
Вземледелии карбамид используется в качестве эффективного высококонцентрированного азотного удобрения и основного сырья для полу чения медленнодействующих мочевиноформальдегидных удобрений (МФУ). В животноводстве карбамид применяется как кормовая добавка для жвачных животных.
Впромышленности карбамид является основным сырьем для произ водства мочевиноформальдегидных смол, меламина и циапуровой кисло ты, которые в свою очередь используются при получении аминопластов
иклеевых веществ, применяемых в автомобиле- и судостроении, жилищ ном строительстве и т. д.
Карбамид используется также для приготовления лекарственных и
косметических |
средств, |
пищевых препаратов, препаратов для борьбы |
с обледенением. |
впервые синтезирован Ф. Вёлером в 1828 г. из |
|
Карбамид |
(мочевина) |
хлористого аммония и циановокислого серебра, в 1870 г. он был получен А. И. Базаровым из аммиака и двуокиси углерода.
Промышленное производство карбамида стало возможным лишь через столетие после опытов, проведенных Ф. Вёлером, благодаря развитию науки и техники. С 20—30-х годов нынешнего столетия начинается быстрое развитие производства карбамида во многих странах.
В дореволюционной России карбамид и его производные не выраба тывались. Первые опыты по производству карбамида в СССР были осу ществлены в 30-х годах, с 60-х годов наблюдается подъем его выработки с использованием отечественного и зарубежного оборудования.
Научно-исследовательские работы в области получения карбамида из аммиака и двуокиси углерода были начаты в СССР в середине 20-х годов (первые сообщения были опубликованы в 1928 г.). Фундаментальные физико-химические и технологические исследования по синтезу карбами да были проведены в Государственном институте высоких давлений (ГИВД) в начале 30-х годов под руководством Б. А. Болотова [15—17]. При этом было установлено, что реакция получения карбамида из аммиа ка и двуокиси углерода протекает в две стадии: образование карбамата аммопия (экзотермический процесс) и его дегидратация в карбамид (эндотермический процесс).
Суммарная реакция экзотермична. Если первая стадия протекает почти мгновенно при давлении 9,8 МПа и температуре 150° С, то де гидратация — процесс равновесный. Степень превращения карбамата аммония в карбамид возрастает с повышением температуры и давления, но при стехиометрическом соотношении компонентов она не превышает
53%. Избыток аммиака благоприятствует повышению степени конверсии карбамата до 70—75%. Наличие воды в исходных компонентах снижает степень конверсии карбамата.
Выходящий из реакционной аппаратуры плав содержит карбамид, не прореагировавший карбамат аммония, избыточный аммиак и воду, обра зующуюся в результате конверсии карбамата. Выделяют карбамид из плава дросселированием и подогревом, при этом карбамат аммония раз лагается на исходные вещества, которые вместе с избыточным аммиаком и парами воды переходят в газовую фазу. Водный раствор карбамида направляется на выделение товарного продукта.
В 1935 г. на Чериореченском химическом заводе была смонтирована модельная установка, пуск которой показал, что обычные аппаратурные конструкции и материалы не пригодны для промышленного осуществле ния синтеза карбамида. Поэтому в начале 1936 г. на опытной установке
С Ф ЕРА ПРИМЕНЕНИЯ КАРБАМ ИДА
мощностью 240 кг/сут отрабатывались технологические параметры и была создана оригинальная конструкция колонны синтеза с корпусом н крышкой из низколегированной углеродистой стали [18]. Внутри колон ны размещали два полых цилиндра (стаканы) из хром-никель-молпбде- новой стали, рекомендованной Ф. Ф. Химушиным [19] и А. И. Красильщиковым [20] на основе испытаний коррозионной устойчивости материа лов в условиях сиптеза карбамида. В пространство между стаканами нагнетали жидкий аммиак, предохраняющий корпус и крышки от сопри косновения с плавом. Двуокись углерода подавали непосредственно во внутренний стакан, где происходило ее смешение с аммиаком. Требуемая температура поддерживалась введением избыточной нормы аммиака.
В 1939 г. установка была реконструирована в полупромышленный цех мощностью 1 т/'сут. Схема синтеза, протекавшего под давлением 19,6 МПа, включала колонну для дистилляции под атмосферным давле нием, вакуум-выпарной аппарат периодического действия, шнековый кри сталлизатор, центрифугу и абсорбер для получения водного раствора углеаммонисвых солей. В этот период на Сталиногорском химическом ком бинате при активном участии И. П. Белоусова была смоптнрована установка большой мощности, на которой непрореагировавший аммиак перерабатывали в аммиачную селитру. В период Великой Отечественной войны (1941—1945 гг.) цех карбамида на Сталиногорском химическом комбинате был ликвидирован и до 1953 г. функционировала лишь полу промышленная установка на Чериоречеиском химическом заводе, мощ ность которой была доведена до 4 тыс. т/год.
В 1958 г. на Сталиногорском химическом комбинате был пущей но вый цех мощностью 10 тыс. т/год, где карбамид вырабатывали на двух, агрегатах, работающих по схеме с так называемым разомкнутым цик лом и переработкой всего непрореагировавшего аммиака в аммиачную селитру. Аналогичный цех, запроектированный Дзержинским филиалом ГИАПа, был пущен в 1958 г. на Лисичанском химическом комбинате. Технологические схемы этих цехов оставались на довоенном уровне, так как систематических научно-исследовательских и опытных работ в обла сти получения карбамида в послевоенные годы не проводилось и разви тие промышленности азотных удобрений ориентировалось на производства аммиачной селитры.
Следует отметить, что попытки усовершенствовать схему производства карбамида предпринимались. Так, в 1950—1951 гг. на Чериоречеиском химическом заводе проводились испытания запроектированного ГИАПоу узла дистилляции под давлением 1,7 МПа, включающего отгонную колон ну и конденсатор и предназначенного для отгонки избыточного аммиака с целью возврата в цикл. Руководил работой В. И. Заграничный. Однако опыты были прекращены, так как аммиак отгонялся вместе с двуокисью углерода, что вызывало быстрое забивание конденсатора углеаммониевы ми солями.
В 1949 г. был предложен способ селективного разделения газов дистил ляции раствором поташа [21]. Испытания модельной установки в цехе карбамида Чериореченского химического завода показали перспектив ность метода [22]. В 1950 г. В. А. Кикут и др. предложили проводить на заводе пассивацию хром-пикель-молпбденовых стаканов в колонне синтеза эпизодической подачей перекиси водорода в поток жидкого ам миака [18], а в 1955 г. И. П. Белоусов и К. К. Килынтедт разработали
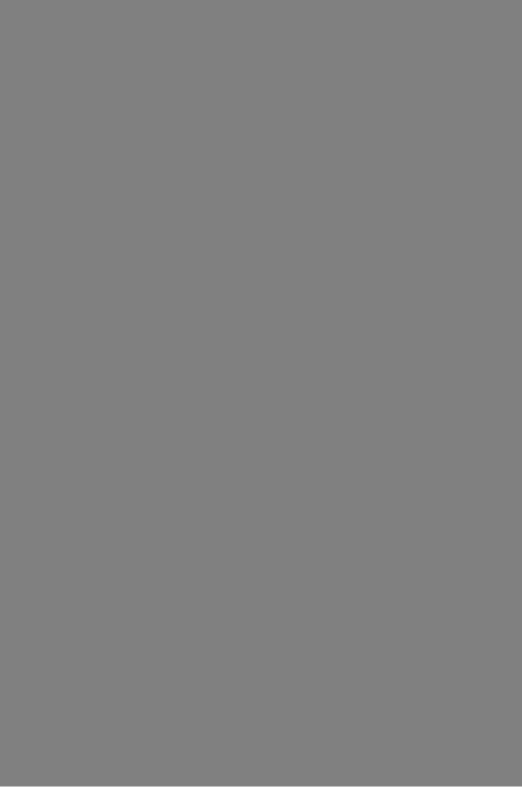
В результате изучения этих процессов был разработан проект типо вого агрегата по получению карбамида мощностью 100 т/сут, работаю щего но схеме с частичным рециклом аммиака п с возможностью пол ного рецикла при разделении газов. При этом газоообразиая двуокись
.углерода, в которую дозируется 0,5—0,8% кислорода, нагнетается пяти ступенчатым компрессором, а жидкий возвратный аммиак —плунжер ным насосом во внутренний стакан колонны синтеза. Свежий аммиак насосом подается в зазор между внешним стаканом и корпусом колонны, предохраняя последний от соприкосновения с плавом. Оба стакана изго товлены из хром-пикель-молпбденовой стали. Смешение реагентов проис ходит в нижней части внутреннего стакана, оснащенного тарелками.
Выделение карбамида из плава и частичный возврат аммиака в цикл ■осуществляются в системе двухступенчатой дистилляции. При этом отго няется почти весь избыточный аммиак. Карбамат аммония частично раз лагается, что приводит к загрязнению газовой фазы двуокисью углерода. Во избежание коррозионно-эрозионного износа оборудования (конденсато ров и насосов) газообразный аммиак очищается от С02 и сушится в ко лонне фракционирования, орошаемых концентрированной аммиачной во дой (~90% N N 3 ) . после чего сжижается. Первый по ходу конденсатор аммиака имеет трубки из хром-ннкель-молибденовой стали, так как в га зовой фазе содержится 0,02—0,05% С02. Этим же обусловлена необходи мость раздельного возврата в колонну синтеза циркуляционного и свеже го аммиака.
Во второй ступени дистилляции практически полностью разлагается карбамат аммония и отгоняются аммиак, двуокись углерода и пары воды ■в газовую фазу, которая направляется в скруббер-нейтрализатор для получения раствора аммиачной селитры или в систему разделения газов, откуда аммиак и двуокись углерода обособленными потоками возвраща ются в цикл. Водный раствор карбамида (70—80%) перерабатывается в кристаллический или гранулированный продукт.
По этому проекту с частичным рециклом амхмпака в 1961—1964 гг. были введены в эксплуатацию пять цехов мощностью 70 и 105 тыс. т/год на Новомосковском, Лисичанском, Новокемеровском и Гроднепском химических комбинатах и на Ангарском нефтехимическом комбинате и цех мощностью 140 тыс. т/год с разделением газов на Щекинском химическом комбинате, где возможность переработки аммиака в аммиачную селитру отсутствовала. Эти цехи, за исключением Новокемеровского и Щекинского, эксплуатируются до настоящего времени и производят кристалли ческий карбамид для технических целей со Знаком качества. На Ново кемеровском химическом комбинате цех ликвидирован, а на Щекинском химическом комбинате реконструирован по схеме с полным жидкостным рециклом, технико-экономические показатели которой были значительно лучше, чем в схеме с разделением газов.
Промышленное производство карбамида в СССР в дальнейшем разви валось в направлении внедрения более прогрессивной технологической схемы, основанной на рецикле раствора углеаммониевых солей.
Первый цех по получению карбамида по новой технологии мощностью 180 тыс. т/год (два агрегата) был введен в эксплуатацию на Щекпп* ском химическом комбинате в 1963 г., а на Чирчикском электрохимиче ском комбинате, Салаватском нефтехимическом комбинате и Северодонец ком химическом комбинате — в 1964—1965 гг.