
книги / Развитие химической промышленности в СССР (1917-1980). Т. 2 Развитие отдельных отраслей химической промышленности
.pdfции в сторону повышения концентрации аммиака. В 1901 г. он предпри нял экспериментальную проверку своего принципа, однако опыты были прерваны вследствие взрыва установки. Основываясь на проведенных опытах, А. Ле Шателье взял патент на способ получения аммиака путем взрыва сжатой смеси водорода и воздуха под давлением 10,1 МПа.
В1903 г. к изучению реакции прямого синтеза аммиака приступил
Ф.Габер. Задача эта была поставлена перед немецкими учеными про мышленностью. В 1904 г. Ф. Габер опубликовал первое сообщение о рав новесии реакции синтеза аммиака при атмосферном давлении и темпера
турах 700—1020° С [10]. Немного позднее В. Нерист вычислил, исходя из термодинамических данных, константы равновесия этой реакции [11]. Они существенно отличались от констант Ф. Габера. Тогда вновь были предприняты экспериментальные работы по изучению равновесия реак ции. В. Нерпст и Г. Пост провели исследования при 5,1—7,1 МПа и
685—1040° С [12], |
Ф. Габер и Р. Ле-Россипьоль — при 3 МПа и |
561— |
|
974° С. |
Результаты |
этих исследований были опубликованы в |
1908— |
1910 гг. |
[13]. |
|
|
На основе результатов исследований Ф. Габера, К. Боша, а также не мецкого ученого А. Митташа п их сотрудников были определены опти мальные условия синтеза аммиака при давлении 20,2 МПа и температуре около 550° С, сконструирован и пспытаи опытный реактор, па котором в 1910 г. была доказана принципиальная возможность промышленного про изводства синтетического аммиака. В 1912 г. в Людвигсгафепе (Герма ния) была построена и пущена в эксплуатацию опытная установка про изводительностью около 1 т аммиака в сутки.
В 1913 г. было закончено строительство завода в Оппау, который пачал производить 25 т аммиака в сутки. В конце 20-х годов производство было доведено до 400 т/сут. Второй большой завод синтетического ам миака Лейпа-Верке в Мерзебурге был построен и введен в действие в 1916 г. Первоначальная мощность завода составляла 400 т/сут, а к концу 20-х годов она была увеличена до 800—1000 т/сут.
До окончания первой мировой войны Германия была единственной страной, осуществившей промышленное производство синтетического ам миака. Однако научные изыскания в этой области продолжались во мно гих странах. Вскоре после окончания войны интерес к проблеме фикса ции азота и, в частности, к синтезу аммиака из элементов вспыхнул с повой силой, в том числе и в России. Однако гражданская война, интер венция нпостраниых государств и разруха задержали развитие научных исследований и создание промышленного производства синтетического ам миака в нашей стране.
В результате напряженных научно-исследовательских, проектно-кон структорских и опытных работ в ряде европейских стран и США в тече ние 5 лет после окончания первой мировой войны были созданы новые
системы синтеза аммиака и построены заводы. |
|
Производство синтетического аммиака интенсивно |
развивалось: |
за 8 лет (1929—1937 гг.) оно возросло с 1121,8 тыс. до |
3574,73 тыс. т, |
т. е. почти в 3,2 раза. Первое место по мощности производства занимали установки по методу Габера—Боша и его модификации (43,5% от обще мирового производства). С начала 20-х годов появились и другие методы синтеза аммиака, отличающиеся друг от друга в основном давлением, катализатором, сырьем для получения азото-водородной смеси и др. Из
новых методов наиболее быстро развивались система Казале (15,0%), система Клода (11,5%) и почти одинаково системы Фаузера (10,5%) и фирмы «Иайтроджеи» (9,0%).
В начале 30-х годов в иаучпо-техпической литературе состоялась дис куссия о том, какое давление предпочтительно в установках синтеза аммиака. Вопрос был решен с учетом опыта эксплуатации установок в пользу среднего давления. В последующие годы темпы строительства уста новок по системам высокого давления Казале и Клода замедлились, а по системам Фаузера и Найтроджеиа увеличились.
В эти же годы большие усилия ученых и инженеров были направле ны на разработку технически совершенных и экономичных методов про изводства чистых азота и водорода для синтеза аммиака [14—22]. Пер вые аммиачные заводы работали на азото-водородной смеси, получаемой из полуводяиого газа методом конверсии окиси углерода с водяным па ром, т. е. фактически сырьем были кокс и каменный уголь. Вскоре после первой мировой войны были разработаны промышленные методы произ водства водорода из коксового газа глубоким охлаждением его до темпе ратуры —200° С. При этом конденсируются все газообразные компоненты коксового газа — этилен, этап, метан, окись углерода, а остающийся нескоидепсированным водород промывается жидким азотом для освобож дения от следов окиси углерода. Были созданы совершенные электроли зеры с униполярными электродами, а также высокопроизводительные электролизеры филътр-прессного типа с биполярными электродами для электролиза воды, которые нашли широкое применение в Норвегии, Ита лии и Японии. В небольшом масштабе стал применяться железопаровой способ получения водорода, использовался побочный водород других про изводств, например производства хлора электролизом раствора поварен ной соли. Наконец, был разработан метод производства водорода конвер сией метана и углеводородов нефти с водяным паром при атмосферном давлении и под давлением 2—5,1 МПа. Последний метод оказался наи более экономичным, получил большое распространение после второй ми ровой войны и начал постепенно вытеснять другие.
В табл. 1 показано изменение удельного веса различных видов сырья
и методов производства |
водорода в |
мировой |
азотной |
промышленно |
||||||
сти [23]. |
|
|
|
|
|
|
|
|
|
|
ТАБЛИЦА 1. |
ИЗМЕНЕНИЕ |
СЫРЬЕВОЙ |
И ТОПЛИВНОЙ |
БАЗЫ |
МИРОВОЙ АЗОТНОЙ |
ПРОМЫШЛЕННОСТИ |
||||
(В %) |
|
|
|
|
|
|
|
|
|
|
Исходное технологическое |
.1929 г. |
1939 г. |
1949 г. |
1959 г. |
1962 г. |
1967 г. 1963 г. |
1969 г. |
|||
и энергетическое сырье |
||||||||||
Природный п попутный газы |
|
1 |
18 |
46 |
49 |
57 |
56 |
62 |
||
нефтепереработки |
|
|
|
|
|
|
|
|
|
|
Жидкое |
топливо |
(бензин, |
|
|
3 |
5 |
18 |
16 |
25 |
20 |
нефть, мазут) |
|
|
|
|
|
25 |
|
15 |
|
|
Уголь, кокс п коксовый газ |
81 |
81 |
69 |
41 |
21 |
14 |
||||
Электроэнергия (электролиз |
18 |
16 |
7 |
6 |
6 |
4 |
2 |
2 |
||
воды) |
|
|
1 |
2 |
3 |
2 |
2 |
2 |
2 |
|
Прочие виды сырья |
|
|
Накануне второй мировой войны производство синтетического аммиа ка в мире составило около 4,5 млн. т. Война задержала рост производ ства синтетического аммиака. Многие заводы в европейских странах были разрушены и восстановлены после окончания войны. Мировое произ водство синтетического аммиака в 1950 г. составило 5,25 млн. т.
В последующие годы производство синтетического аммиака развива лось весьма быстро. Главным стимулом быстрого развития производства аммиака был рост потребностей сельского хозяйства в азотных удобре ниях. Мировое производство синтетического аммиака в 1980 г. составило 67,5 млп. т, т. е. за 30 лет увеличилось в ~13 раз.
Каким бы впечатляющим ни был количественный рост продукции ам миака, не менее замечательными являются качественные изменения, про исшедшие в технике производства и вызвавшие снижение энергетических затрат и удельных капиталовложений на единицу установленной мощно сти. Достигнутый успех не является результатом каких-либо выдающихся изобретений и открытий, а обусловлен реализацией в промышленности достижений современной науки, что позволило модифицировать и усовер шенствовать уже известные технологические процессы, создать более эф фективное оборудование, повысить единичную мощность установок, пере вести заводы на новое сырье, а также внедрить в практику большое число изобретений и рационализаторских предложений. Необходимо под черкнуть, что усовершенствование известных технологических процессов и создание новых стало возможным благодаря прогрессу пауки и творче ским усилиям инженерной мысли.
Увеличение мощности агрегатов было достигнуто благодаря лучшему пониманию механизма реакции синтеза аммиака, изучению кинетики процесса и разработке методов быстрого отвода тепла из зоны реакции. Достижения в области металлургии и машиностроения позволили изгото вить более крупные корпуса колони сиптеза аммиака и оборудование бо лее высокого давления, чем это было возможно несколько лет назад.
На основе результатов многочисленных исследований разработаны бо лее совершенные методы и созданы высокопроизводительные аппараты для получения водорода каталитической конверсией метана с водяным паром с последующей конверсией окиси углерода. Наиболее экономичным оказался метод конверсии метана под давлением 4 МПа и при темпера туре 900° С. Он получает широкое распространение. Современный конвер тор метана представляет собой батарею трубок, заполненных катализато ром, обогреваемых пламенем газа, сжигаемого в межтрубном пространстве. Для изготовления трубок, которые должны работать в очень жестких условиях давления и температуры, применяются сплавы с высоким со держанием никеля и хрома.
Переход к агрегатам синтеза аммиака большой единичной мощности и применение конверсии природного газа под давлением открыли воз можность замены поршневых компрессоров для сжатия газа до конечного давления турбокомпрессорами с применением в качестве приводов паро вых турбин.
Большим успехом химиков является разработка процесса низкотемпе ратурной конверсии окиси углерода при 200—250° С. Это стало возможно в результате создания высокоактивных катализаторов. При осуществле нии конверсии метана с водяным паром образуются водород и окись угле рода по реакции СН4Ч-Н20 = ЗН2+ С0. Этот газ, содержащий избыточный
водяной пар, направляется на конверсию окиси углерода, которая осу ществляется в две стадии —первая при 450—500° С и вторая при 200— 250° С. При этом остаточное содержание окиси углерода в конвертирован ном газе не превышает 0,4%, что позволяет применить для очистки азотоводородной смеси каталитическое метапирование окиси углерода и тем самым исключить из технологической схемы медно-аммиачную очистку или промывку жидким азотом.
СОЗДАНИЕ И ПРОГРЕСС ПРОМЫШЛЕННОСТИ СИНТЕТИЧЕСКОГО АММИАКА В СССР
В дореволюционной России единственным источником технического свя занного азота был коксохимический аммиак, производство которого было далеко недостаточным для покрытия потребностей в нем. Эти потребно сти, возросшие во время первой мировой войны, удовлетворялись за счет импорта чилийской селитры. В Европейскую Россию, где былп располо жены заводы порохов и взрывчатых веществ, она поступала через Влади востокский порт. Из чилийской селитры разложением ее серной кислотой получались сульфат натрия и азотная кислота, необходимая для процес сов нитрования органических веществ.
Азотная проблема, естественно, волновала умы русских ученых, и они внесли весомый вклад в ее решение. Профессор А. И. Горбов и академик В. Ф. Миткевич в 1907—1909 гг. разработали оригинальную конструкцию электродуговой печи для окисления азота кислородом воздуха. Дуговой процесс привлекал внимание многих ученых своей простотой. В частно сти, в дальнейшем фундаментальные исследования процесса окисления азота в низкотемпературной плазме былп выполнены Я. Б. Зельдовичем с сотрудниками [24] и Л. С. Полаком и В. С. Щппачевым [25]. Этп исследования очень интересны в научном отношении. Однако этот про цесс весьма существенно уступает по расходу энергии и себестоимости методу синтеза аммиака.
Для молодой Советской Республики создание азотной промышленно сти было жизненно необходимой задачей, и поэтому уже в августе 1918 г. при Высшем Совете народного хозяйства (ВСНХ) была создана Комиссия по связанному азоту, в состав которой вошли видные ученые того време ни: В. II. Ипатьев, А. А. Яковкпн, В. Ф. Миткевич, А. В. Сапожников, И. И. Андреев, А. Е. Маковецкий и др. Комиссия организовывала лабора торные исследования, заслушивала доклады о состоянии производства азотных удобрений в зарубежных странах, разрабатывала проекты буду щих заводов.
В1918—1919 гг. в химической лаборатории Артиллерийской академии
В.Н. Ипатьев в аппарате собственной конструкции провел ряд экспери
ментов по изучению действия различных катализаторов на смесь азота и водорода. В начале 1918 г. на урановом катализаторе были получены следы аммиака, а в феврале 1919 г. на смешанном катализаторе воль фрам—молибден—окись алюминия иод давлением 7,5 МПа и прп тем пературе 605—470° С была достигнута концентрация N113 в газовой смеси 6,55%. Эти опыты проводились в период, когда сведения о производстве синтетического аммиака в Германии еще не были опубликованы. Однако из-за отсутствия газа п перебоев с электрической энергией эксперименты были прекращены [26].
Впервые годы Советской власти среди ученых не было единого мне ния при выборе метода фиксации атмосферного азота 127]: предлагалось получать аммиак нз цианамида кальция или цианида натрия и даже по строить промышленную установку, работающую по дуговому методу для получения кальциевой селитры. В. Н. Ипатьев, И. Ф. Юшкевич и др. предлагали освоить метод синтеза аммиака из элементов. И только Вто рой съезд технических работников основной химической промышленности (20—26 января 1925 г.) постановил в своей резолюции обратить внима ние ВСНХ на необходимость организации в СССР производства синтети ческого аммиака [28].
Всередине 1925 г. было принято решение о строительстве первой уста
новки синтетического аммиака на Черпоречеиском химическом заводе. В этом же году при Президиуме ВСНХ был создан Комитет по связан ному азоту под председательством В. II. Ипатьева. По поручению Коми тета группа специалистов выехала за границу для ознакомления с про изводством и закупки оборудования.
Торжественная закладка фундамента первого цеха синтеза аммиака на Чериореченском химическом заводе произошла в день восьмой годов щины Великого Октября и в преддверии XIV съезда ВКП(б), состоявше гося в декабре 1925 г. В течение 1926—1927 гг. был построен и введен в эксплуатацию цех по производству аммиака, а 9 февраля 1928 г. наша страна впервые получила синтетический аммиак.
Синтез аммиака осуществлялся под давлением 76 МПа и при темпе ратуре 450° С на железном катализаторе. Водород производился железо паровым способом в генераторах системы Пинча, азот —сжижением и ректификацией воздуха в аппаратах Лпнде. Генераторы водорода были загружены пористыми брикетами из окислов железа. Производство водо рода осуществлялось чередованием процессов восстановления окислов до металлического железа водяным газом и последующего окисления железа водяным паром. Восстановитель железа — водяной газ —получался гази фикацией кокса в газогенераторах. Первая очередь установки синтеза аммиака состояла из трех реакторов с внутренним диаметром колонны 400 мм, производительность каждого агрегата составляла 8 т/сут жидко го аммиака, общая мощность установки —около 7,5 тыс. т/год.
В течение первого же года работы цеха кокс, использовавшийся в ка честве сырья для получения водяного газа, был заменен на антрацит, а вместо импортных брикетов в генераторах водорода стали применять отечественные брикеты из уральского сидерита. В результате производи тельность генераторов поднялась на 10—15%. В процессе освоения произ водства и внедрения рационализаторских предложений производитель ность агрегата превысила 9 т/сут. Позже годовая производительность завода была доведена до 17—19 тыс. т путем установки в 1931 г. допол нительных четырех реакторов с внутренним диаметром 450 мм про
изводительностью 10 т/сут. |
В 1928 г. на заводе было произведено |
|
2,8 тыс. |
т синтетического |
аммиака, в 1930 г.— 6,5, а в 1932 г.— |
15,6 тыс. |
т. |
|
В 1930 г. на Чериореченском химическом заводе был введен в строй цех по производству цианамида кальция методом азотирования карбида кальция. Часть получаемой продукции предполагалось перерабатывать в аммиак, обрабатывая ее водой, для чего в Германии была закуплена, смонтирована и опробована специальная установка. Однако этот процесс
оказался громоздким и нерентабельным, и в 1933 г. от него полностью отказались, а оборудование было использовано в других целях.
В1927 г. Совет Труда и Обороны утвердил проект гидроэлектростан ции и карбидного завода в Закавказье [29]. Строительство предприятия началось в Караклисе весной 1930 г., а в 1934 г. завод был сдан в экс плуатацию.
Всоответствии с планом химизации страны, выдвинутом в постанов лении. Совета Народных Комиссаров СССР «О мероприятиях по химиза ции народного хозяйства Союза ССР» 28 апреля 1928 г. [30], были по вышены темпы строительства предприятий химической промышленности для удовлетворения потребностей страны в важнейших химических про дуктах. Придавая важное значение созданию промышленности минераль ных удобрений, XV съезд ВКП(б) утвердил курс «...на скорейшее осу ществление плана электрификации, развитие черпой и цветной металлур гии, в особенности в части качественных металлов, развитие химических производств, в особенности в части производства искусственных удобре ний...» [31].
Несколько ранее, в августе 1926 г., была создана проектная организа ция «Химстрой». В первые годы ее деятельности было разработано тех нико-экономическое обоснование строительства Березниковского и Горловского азотно-туковых заводов, а также Бобриковского химического комбината. С помощью иностранных фирм были выполнены проекты пер вой очереди этих заводов. Азотная секция Химстроя в результате реорга низации в феврале 1932 г. была выделена в самостоятельный Государст венный институт по проектированию предприятий азотной промышленно сти (Гипроазот).
Уже с 1934 г. Гипроазот поставил перед собой задачу разработать
проекты по расширению существующих п строительству новых комбина тов, основываясь исключительно на опыте эксплуатации отечественных азотных заводов.
Большое внимание в те годы было уделено созданию промышленности химического машиностроения и получению специальных материалов — хромоникелевых и высокохромистых сталей для аппаратуры, работающей под высоким давлением, и материалов высокой жаростойкости и кислото упорности.
Развитие отечественного химического машиностроения дало возмож ность быстрыми темпами увеличивать мощность предприятий азотной промышленности в последующих пятилетках. В Ленинграде в 1931 г. был создай Гипроазотмаш, внесший большой вклад в конструирование, проектирование, разработку технологии и организацию производства ма шин, аппаратуры и оборудования для. азотной промышленности. В ко роткие сроки при использовании зарубежного опыта были разработаны конструкции компрессоров высокого давления, колонн синтеза (реакто ров) и налажен их серийный выпуск машиностроительными заводами. Производство корпусов реакторов и другого оборудования высокого дав ления, в том числе компрессоров, было быстро освоено на отечественных машиностроительных заводах. Много энергии и творческого труда внесли в деятельность Гипроазотмаша его первый директор Н. В. Беляев, глав ный инженер института Н. А. Долежаль, инженер В. Б. Николаев и мно гие другие. В 1946 г. на базе Гипроазотмаша был создан ЛенНИИхпммаш.
В целях ускорения строительства предприятий азотной промышлен
ности требовалось создание организации, которая бы в централизованном порядке осуществляла руководство их сооружением и эксплуатацией. После обсуждения этого вопроса во Всехимпроме, ВСНХ и в ЦК ВКП(б) было принято решение об организации в 1932 г. треста «Союзазот».
Главными объектами строительства предприятий азотной промышлен ности в первой пятилетке стали Березниковский и Горловский азотно туковые заводы, а также Бобриковский химический комбинат.
С середины 1929 г. начались подготовительные работы к строительству Березниковского азотно-тукового завода. К зиме 1930 г. основные строи тельные работы были закончены и начато сооружение фундаментов под оборудование и аппаратуру; в мае 1931 г. был завершен монтаж газоге нераторного отделения аммиачного цеха. А через год были полностью закончены монтажные строительные работы и состоялся пуск завода в эксплуатацию. В течение мая—июля были проведены гарантийные испы тания оборудования всех цехов, и в 1932 г. завод был принят в эксплуа тацию.
Производственная мощность первой очереди Березниковского азотно тукового завода составляла 30 тыс. т/год. Завод был оснащен оборудова нием фирмы «Найтроджен», включающим четыре агрегата с колоннами синтеза с внутренним диаметром корпуса 700 мм и проектной производи тельностью агрегата 25 т/сут. Синтез аммиака осуществлялся под давле нием 30 МПа. Для производства азото-водородной смеси был принят метод получения водорода каталитической конверсией полуводяиого газа с во дяным паром с последующей очисткой от углекислого газа, отмывкой водой в скрубберах под давлением 1,6 МПа и очисткой от окиси угле рода абсорбцией водными растворами комплексных аммиакатов однова лентной меди под давлением 12 МПа. Производство азотоводородной сме си было более прогрессивным в сравнении с железопаровым способом, принятым на Чернореченском заводе.
В 1932 г. на Березниковском азотно-туковом заводе было выработано 4898 т аммиака. Общий выпуск продукции и доля в нем синтетического аммиака характеризовалась в нашей стране в то время следующими данными (в тоннах) [32]:
|
1928/29 г. |
1929/30 г. |
1930 г. |
1931 г. |
1932 г. |
Произведено аммиака |
11069 |
14033 |
15 780 |
22 995 |
33 680 |
В том числе синтетического |
2 827 |
5 214 |
6 480 |
11157 |
19 503 |
В последующие годы на Березниковском азотно-туковом заводе было расширено производство синтетического аммиака путем строительства второй и третьей очередей, и выпуск продукции к 1940 г. был доведен до 100 тыс. т/год. Наряду с производством аммиака были построены так же цехи азотной кислоты и переработки аммиака и азотной кислоты в аммиачную селитру и другие азотные удобрения. Все оборудование вто рой и третьей очередей было полностью изготовлено на отечественных машиностроительных заводах.
Параллельно с Березниковским заводом велось строительство Бобриковского химического комбината. В марте приступили к пуску оборудова ния, а в июле 1933 г. страна получила первый бобриковский синтетиче ский аммиак. Официальное открытие комбината состоялось в декабре 1933 г. В последующие годы были построены вторая и третья очереди ком-
бипата, и производство синтетического аммиака к 1940 г. было доведено до 100 тыс. т/год. Аммиачный завод был полностью укомплектован оте чественным оборудованием. Большую роль в подготовке квалифицирован ных инженеров и рабочих кадров сыграли первенцы азотной промышлен ности —Чериореченский химический и Березниковский азотно-туковый заводы. Именно там проходили практику специалисты вновь строящегося Бобриковского химического комбината, который впоследствии сам стал кузницей кадров для вновь вводимых объектов химической промышлен ности.
В 1933 г. вступил в строй Горловский азотно-туковый завод в Дон бассе производительностью 52 тыс. т/год жидкого аммиака. Проект за вода был разработан группой инженеров Гипрококса (Харьков) при уча стии итальянских специалистов. В основу проекта был положен процесс синтеза аммиака по методу Фаузера. Источником водорода служил кок совый газ, который поступал с близлежащего коксохимического завода. Водород выделялся методом глубокого охлаждения в аппаратах Линде. Азот получался сжижением и ректификацией воздуха. На заводе были установлены четыре колонны синтеза аммиака конструкции Фаузера с
внутренним |
диаметром |
800 мм |
с проектной |
производительностью |
40 т/'сут каждая. Синтез |
аммиака |
осуществлялся в колонном реакторе |
||
в режиме |
падающей температуры |
(600—450° С) |
под давлением 30— |
33МПа.
В1938 г. вошли в строй еще два аналогичных завода в Днепродзер жинске и Кемерово производительностью по 75 тыс. т/год синтетического аммиака каждый. И, наконец, в 1940 г. был закончен и пущен в эксплуа
тацию Чирчикский электрохимический комбинат, включающий завод син тетического аммиака производительностью 80 тыс. т/год на водороде, получаемом электролизом воды. Днепродзержинский, Кемеровский заво ды и Чирчикский электрохимический комбинат были полностью оснаще ны оборудованием отечественного производства.
К этому времени в стране было освоено производство установок глу бокого охлаждения для получения чистых кислорода и азота из воздуха и разделения коксового газа для получения водорода. При проектирова нии Чирчпкского электрохимического комбината параллельно с разработ кой отечественных электролизеров ФВ-500 велись переговоры с зарубеж ными фирмами о поставке электролизеров для комбината. Одпако при этом выяснилось, что конструкция советского электролизера по показате лям работы не только не уступает лучшим зарубежным образцам, но име ет некоторые преимущества в простоте их промышленного изготовления. Это позволило отказаться от импорта дорогостоящего оборудования п сэкономить 15—20 млн. рублей валюты [33]. Конструкцию отечественных электролизеров фильтр-прессного типа с бпполярпыми электродами ФВ-500 в 40-х годах разработали инженеры А. И. Колосков, Л. М. Яки менко, Л. Ш. Генпп, П. И. Соколов и В. Г. Хомяков. На Чирчпкском комбинате применили также оригинальную колонну снптеза аммиака, конструкцию которой разработали сотрудники Гипроазота и ГИА.
В конце 30-х годов азотная промышленность заняла ведущее место в химической индустрии СССР. Народнохозяйственным планом было пред усмотрено строительство ускоренными темпами важных объектов хими ческой промышленности. Одним из них был Лисичанский комбинат, строительство которого шло полным ходом. К 1941 г. были закончены
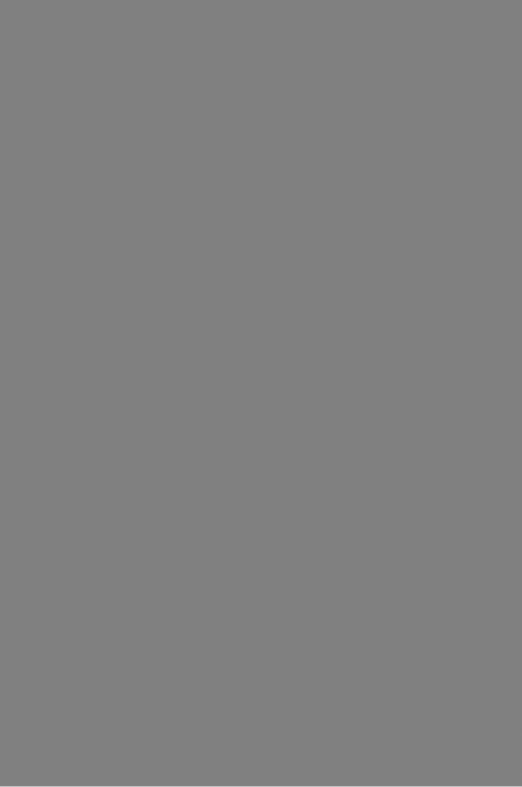
увеличении выпуска продукции. На Березниковском и Кемеровском заво дах и Чирчикском комбинате были увеличены мощности по производству синтетического аммиака, азотной кислоты, аммиачной селитры, и выпуск химической продукции, необходимой для обороны страны, стал непрерыв но возрастать. Так, выработка аммиака в апреле 1942 г. увеличилась на 50% по сравнению, с мартом того же года, а производство азотной кисло ты удвоилось [38].
Во время войны продолжалось строительство новых производств. Ши роко развернулись работы по строительству и монтажу цехов и отделе ний второй очереди Чирчикского электрохимического комбината, введен ной в строй в 1944 г. В 1942 г. началось строительство третьей очереди цеха азотной кислоты в Березниках, а в январе 1943 г. Центральному Комитету партии был направлен рапорт о том, что заводом освоен вы пуск четырех новых продуктов. Эта работа проводилась одновременно с установкой и освоением эвакуированного оборудования.
Непрерывно реконструировались и расширялись цехи, наращивались мощности, создавались новые производства па Кемеровском азотно-туко вом заводе. Его коллектив в максимально короткие сроки справился с пуском цехов азотной кислоты и за годы войны выработал для нужд обороны страны сотпи тысяч тонн продукции. В короткий срок была успешно решена задача расширения п модернизации аммиачного произ водства.
Сотрудники ГИА и Гнпроазота, направленные в Чирчнк и Березники, на Губахинскнй химический и Кемеровский азотно-туковый заводы, про вели ряд работ по ннтенснфШацин установок производства аммиака, азотной кислоты, аммиачной селитры. В ГИА в Москве было организо вано производство малотоннажных химических продуктов, необходимых для обороны.
На Березниковском заводе производительность агрегатов синтеза ам миака была увеличена до 40 т/сут при проектной мощности 25 т/сут. Большая заслуга в этом принадлежит инженерам И. И. Гельпернну,
С.П. Челобовой, И. П. Сидорову, Ф. П. Ивановскому, директору завода
В.С. Уварову. На Кемеровском заводе производительность агрегатов син теза аммиака была доведена до 80 т при проектной 40 т/сут, т. е. удвое на. Большой вклад в это внесли директор завода Н. П. Сорокин, инжене ры А. Я. Рябенко, П. В. Сичков, А. А. Голубев и многие другие.
Большой творческий труд в интенсификацию технологических про цессов па Чирчикском электрохимическом комбинате вложили его дирек тор С. В. Садовский и инженеры А. П. Милованов, 10. Л. Севастьянов,
Л.А. Ахпазаров и др.
Всвязи с успешными действиями советских войск на фронтах Великой
Отечественной войны уже в апреле 1942 г. началось восстановление Сталипогорского химического комбината в условиях прифронтовой полосы. Специалисты бригады проектировщиков Гнпроазота обеспечивали свое временную выдачу документации по восстановлению цехов аммиака, азотной и серпой кислот, аммиачной селитры, п 1 января 1943 г. это предприятие выдало первые тонны продукции.
В восстановление Сталипогорского химического комбината и совер шенствование технологических процессов много творческой инициативы и самоотверженного труда вложили инженеры В. Е. Коваль, Н. А. Копюхов, К. К. Кильштедт, А. И. Севцов [39].