
книги / Развитие химической промышленности в СССР (1917-1980). Т. 2 Развитие отдельных отраслей химической промышленности
.pdfВапреле 1944 г., т. е. через 7 месяцев после начала восстановитель ных работ, Горловскнй азотно-туковый завод стал производить кислород,
ав ноябре 1944 г. был пущен цех аммиака мощностью 65 т/сут, в марте 1945 г. была получена аммиачная селитра.
В1945 г. после восстановления разрушенных корпусов производства аммиака, цехов аммиачной селитры и азотной кислоты, котельной и дру гих коммуникаций вступил в строи Днепродзержинский азотно-туковый
завод.
Сельское хозяйство страны в 1945 г. получило всего 624 тыс. т мине ральных удобрений против 3159 тыс. т в 1940 г., и только в 1948 г. вы работка продукции азотной промышленностью страны достигла довоенно го уровня [40].
Потребность народного хозяйства в продуктах азотной промышленно сти возрастала. 21 декабря 1945 г. Совет Народных Комиссаров СССР
принял постановление «О мерах помощи по восстановлению п развитию химической промышленности», в котором выдвинул в качестве первооче редной задачи восстановление в короткие сроки производств азотных, фосфатных и калийных удобрений, ядохимикатов, соды и органических красителей и развития горно-химических производств для обеспечения сырьем химической промышленности [41].
Февральский (1947 г.) Пленум ЦК ВКП(б) принял постановление «О мерах подъема сельского хозяйства в послевоенный период», предопре делившее строительство одного из крупнейших предприятий — Лисичан ского химического комбината. В канун 1951 г. на комбинате была полу чена аммиачная селитра на привозном аммиаке, а в 1953 г. начато про изводство аммиака па базе газификации донецкого кокса.
В 1951 г. была введена в действие группа цехов по производству свя занного азота на Кироваканском химическом заводе, строительство кото рых началось еще в 1944 г., а эксплуатация отдельных цехов — в 1949 г. В 1950 г. производство аммиака в СССР превысило довоенный уровень и достигло 566 тыс. т.
В послевоенный период отечественная азотная промышленность раз вивалась высокими темпами. Это обеспечивалось большим объемом на учно-исследовательских и проектно-конструкторских работ. Еще во время Великой Отечественной войны, в апреле 1943 г., ГИА и Гипроазот были объединены в Государственный научно-исследовательский и проектный институт азотной промышленности — ГИАП. Большой вклад в развитие исследований в институте внесли его первый директор М. В. Быстров, Н. А. Конюхов, Н. А. Симулии, Б. П. Самарии.
ГИАП занял ведущее положение в научно-техническом обеспечении прогресса азотной промышленности. По проектам ГИАПа осуществлялось восстановление разрушенных войной заводов, а также строительство новых заводов. В 50-е годы были построены Лисичанский, Руставский. Иовокемеровский, Кироваканский химические заводы и комбинаты, а так же азотные заводы в социалистических и развивающихся странах (Бол
гарии, |
Румынии, Венгрии, Югославии, Польше, КНДР, Афганистане |
и др.) |
[42]. |
По мере увеличения объема работ ГИАПа были созданы его филиа лы — Лисичанский (1949 г.), Дзержинский (1952 г.), Днепродзержинский (1953 г.), Кемеровский (1954 г.), Новомосковский (1956 г.), Чирчикский (1959 г.), Гродненский (1973 г.) и Тольяттинский (1975 г.). Эти филиалы
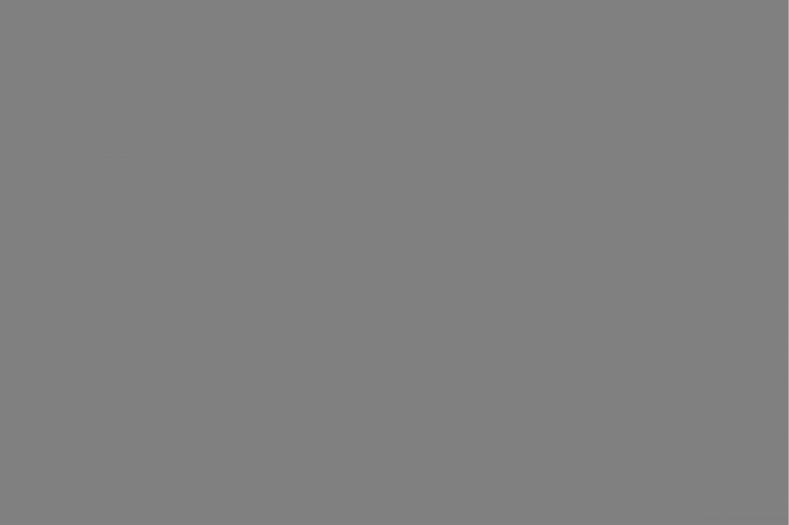
превратились в крупные специализированные организации, способные самостоятельно вести—научные исследования и проектирование крупных объектов на современном техническом уровне. В ГИАПе и трех его фи лиалах — Северодоиецком, Новомосковском и Дзержинском — были по строены опытные заводы.
В начале 50-х годов проводился большой объем исследовательских и проектных работ по освоению новых видов сырья для получения водо рода, методов очистки газов, синтеза аммиака и его переработки, в ре зультате чего отечественная азотная промышленность развивалась высо кими темпами.
Перед азотной промышленностью встала проблема технического пере вооружения. В новых проектах предусматривалось использование высоко эффективных агрегатов. Начали проектировать газогенераторы производи тельностью 35—50 вместо 16 тыс. м3/ч, а колонны синтеза аммиака — 180—200 вместо 50—60 т/сут.
Важное значение стали придавать правильному построению генераль ного плана новых предприятий и компоновке новых цехов. Так, произ водство аммиака проектировалось размещать в одном объединенном корпусе (вместо четырех-пяти). Отпала необходимость в установке колонн предкатализа в результате внедрения промывки газа жидким азотом вместо очистки его медноаммиачным раствором.
Создание укрупненных агрегатов с автоматическим и дистанционным управлением, объединение производственных цехов в крупные комплексы позволили предусмотреть в проектах 1956—1957 гг. снижение капиталь ных затрат на 15—20%.
Для обеспечения быстрого развития производства аммиака и азотных удобрений требовались новые технологические решения, которые позво лили бы увеличить производство с минимальными затратами. Требовалось изыскать надежные и дешевые источники водорода для синтеза аммиака. С этой целью были изучены и успешно освоены методы получения водо рода из природного газа конверсией метана.
В 1956 г. был пущен первый в нашей стране цех синтетического ам миака на базе конверсии метана коксового газа на Руставском азотно туковом заводе, а в 1959 г. на Сталиногорском химическом комбинате был осуществлен полный перевод аммиачного производства на природный газ. Впервые в Советском Союзе аммиак пз природного газа получен на этом комбинате в ноябре 1958 г.
Использование природного газа (каталитическая паро-кислородная конверсия при нормальном давлении) в производстве аммиака явилось значительным научно-техническим достижением. Успех был достигнут за счет укрупнения технологических агрегатов и прогресса энергетического и химического машиностроения, использования вторичных энергоресур сов. Применение природного газа в качестве сырья позволило снизить себестоимость аммиака на этих предприятиях на 40—50%, капитальные вложения на реконструкцию окупились за 2—3 года.
Объем производства синтетического аммиака является показателем научно-технического уровня химической промышленности. Создание более совершенных систем аммиачного производства требует объединенных уси лий работников различных областей науки и техники.
В послевоенный период в ГИАПе начались исследования, направлен ные на интенсификацию производства путем улучшения качества азото-
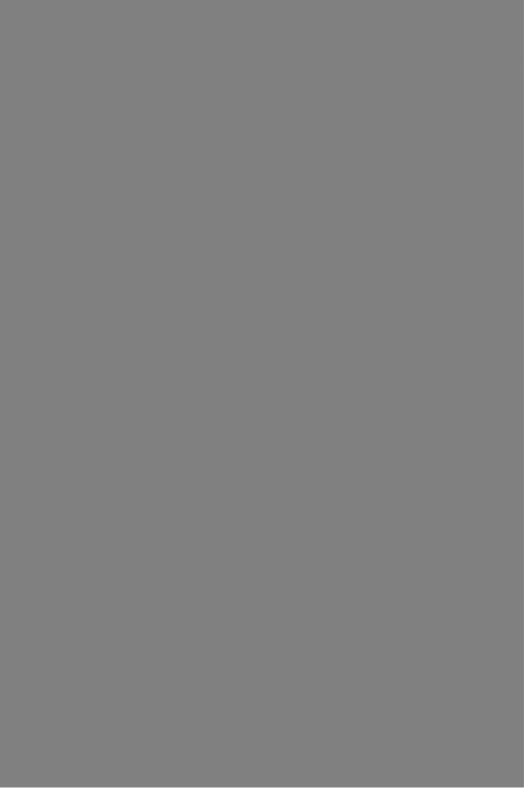
пзводптельностыо 1360 т/сут по энерготехнологической схеме при давле нии 32 МПа был пущен в эксплуатацию в 1973 г. в Невипномысске.
В 1959—1965 гг. были построены и пущены в ход промышленные агрегаты, использующие в качестве сырья природный газ, на Щекипском, Невпниомысском, Черкасском, Гродненском, Салаватском и Навоийском химических комбинатах, Ферганском и Иоиавском заводах азотных удоб рений. В 1965 г. производство аммиака в СССР превысило 3,8 млн. т и увеличилось по сравнению с 1958 г. в 3,15 раза.
Большой вклад в развитие отечественной азотной промышленности внесли крупные инженеры и организаторы производства, принимавшие участие в проектировании, строительстве и пуске первых советских заво дов, в восстановлении и реконструкции промышленности после Великой Отечественной войны: П. Г. Арутюнянц, И. М. Барский, М. Д. Батоев. Е. И. Бомштейн, М. В. Быстров, Г. И. Вилесов, В. Ф. Гогин, М. И. Гон чаров, И. В. Гусев, В. В. Добровольский, К. К. Килыптедт, А. М. Климахин, В. Е. Коваль, П. К. Ковтун, Н. А. Кошохов, С. В. Садовский, Б. П. Самарин, П. В. Сичков, Ю. Л. Севастьянов, А. И. Севцов, II. II. Со рокин, Д. Т. Трифонов, П. А. Чекии, Н. Ф. Юшкевич и многие другие.
В восьмой пятилетке (1966—1970 гг.) на развитие азотной промыш ленности было затрачено свыше 2 млрд, руб., что в 1,5 раза превышало объем капитальных вложений в 1959—1965 гг. При этом на производ ство новых заводов было направлено 15%, а на расширение и рекон струкцию действующих 85% капитальных вложений. За восьмую пя тилетку было построено и введено в строй четыре новых завода — Вахшский, Череповецкий, Ровеиский азотпо-туковые заводы и Новгородский химический комбинат.
По объему производства аммиака азотная промышленность СССР в 1970 г. находилась па втором месте в мире после США (табл. 2). Темпы роста производства были выше темпов ряда передовых в техническом отношении стран. Так, если в 1965 г. производство аммиака в США было в два раза выше производства СССР, то в 1970 г. только в полтора с
лишним раза.
Средняя мощность заводов по производству аммиака в 1969 г. была в
СССР в 1,5 раза выше, чем в США. Это свидетельствует о достигнутом к 70-м годам высоком техническом уровне советской азотной промышлен ности, а также химического машиностроения. Все оборудование для новых
ТАБЛИЦА 2. ПРОИЗВОДСТВО АММИАКА В РАЗВИТЫХ КАПИТАЛИСТИЧЕСКИХ И СОЦИАЛИСТИЧЕСКИХ
СТРАНАХ (В |
ТЫС.Т/ГОД) |
|
|
|
|
|
|
|
|
Страпа |
1965 г. |
1970 г. |
1975 г. |
1980 г . |
Страна |
1965 г. |
1970 г. |
1975 г. |
1980 г. |
США |
7806 |
11883 |
14 692 |
17 258 |
Болгария |
338 |
788 |
935 |
1009 |
СССР |
3813 |
7 638 |
11998 |
16 732 |
Венгрия |
210 |
503 |
624 |
966 |
Япония |
2162 |
3 220 |
3 636 |
2 572 |
ГДР |
533 |
585 |
1107 |
1436 |
ФРГ |
2023 |
2 220 |
2 416 |
2 493 |
Польша |
535 |
1445 |
2075 |
1882 |
Франция |
1562 |
1970 |
2 367 |
2 543 |
Румыния |
265 |
963 |
1895 |
2732 |
Италия |
1252 |
1548 |
1765 |
1704 |
|
|
|
|
|
и реконструируемых заводов было отечественного производства и частич но чехословацкого по разработкам и проектам ГИАПа.
В начале 60-х годов в научно-технической литературе стал обсуждать ся вопрос о повышении производительности агрегатов синтеза аммиака до 600—1000 и даже 2000 т/сут. Это позволяло перейти от поршневых к турбокомпрессорам для сжатия синтез-газа. Преимущества турбоком прессоров: более низкая начальная стоимость оборудования, дающая экономию 10% и выше, большой срок эксплуатации, меньшие эксплуа тационные расходы и меньшее количество вспомогательного оборудова ния, возможность применить в качестве двигателя паровую турбину вместо электромотора и тем самым снизить расход эпергии, меньше об служивающего персонала —все это дает значительное повышение произ водительности труда. Немаловажным обстоятельством является также отсутствие в синтез-газе паров смазочного масла, которыми сннтез-газ неизбежно насыщается при сжатии в поршпевых компрессорах, что ве дет к отравлению катализатора и снижению его активности и срока службы [43].
Для создания агрегата синтеза аммиака производительностью 400— 500 тыс. т/год необходимо было решить ряд сложных конструкторских и материаловедческих задач. Наиболее трудными из них были: разработ ка конструкции турбокомпрессора и паровой турбины в качестве привода к нему: разработка конструкции трубчатой печи для первой ступени кон версии метана с водяным паром и создапие материала для изготовления труб, работающих под давлением 3—4 МПа при температуре 850—900° С; разработка конструкции реактора для синтеза аммиака, которая обеспе чивала бы надежную работу агрегата при давлении 30—32 МПа в тече ние длительного времени; автоматизация отдельных процессов и агрегата в целом; создание высокоактивного катализатора для второй ступени (низкотемпературной) конверсии окиси углерода с водяным паром, обес печивающего достаточную скорость реакции при температуре 200—250° С.
В начале 50-х годов научно-исследовательские и опытно-конструктор ские работы для решения этих задач начали развиваться в ряде стран, в том числе в Советском Союзе. Работы по производству водорода кон версией метана с водяным паром в нашей стране были начаты профес сором В. А. Каржавиным и А. Г. Лейбуш еще в начале 30-х годов [44] и получили большой размах в ГИА в предвоенный период. По существу эти работы были научной базой для перевода в конце 50-х годов произ водства аммиака на новую сырьевую базу —природный газ. В ГИАПе для этой цели были разработаны три способа производства:
1.Паро-кислородо-воздушная конверсия природного газа с последую щей конверсией окиси углерода и очисткой азото-водородной смеси от остаточной окиси углерода абсорбцией медноаммиачпых растворов.
2.Паро-кислородная конверсия природного газа с промывкой конеч ной азото-водородной смеси жидким аммиаком.
3.Двухступенчатая паровая конверсия природного газа: первая сту
пень в трубчатых печах и вторая ступень в шахтной печи с добавкой воздуха.
Последний способ был испытай и под давлением 1,8—2,0 МПа.
Были разработаны высокоактивные катализаторы для второй ступени низкотемпературной копверсии окпси углерода с водяпым паром при тем пературах 190—250° С.
В начале 60-х годов на Невском машиностроительном заводе началась разработка опытного образца турбокомпрессора высокого давления. В се редине 60-х годов ГИАП вплотпую приступил к разработке агрегата син теза аммиака мощностью 1000—1500 т/сут.
Технико-экономическое сравнение, выполненное в ГИАПе примени тельно к производству 400 тыс. т аммиака в год на принятых в то время типовых агрегатах производительностью 200 т/сут н на одном агрегате производительностью 1250 т/сут, показало явное преимущество послед него.
Преимущества агрегата большой единичной мощности заключаются также и в том, что требуемая площадь застройки составляет 13,4 тыс. м2 тогда как для установки по типовой схеме — 61,5 тыс. м2. В табл. 3 приведены основные технпко-экопомпческие показатели для производства 400 тыс. т аммиака в год по типовой схеме, а также па установках из двух агрегатов по 200 тыс., т французской фирмы «ЭНСА» и установках из одного агрегата фирмы «УДЕ» (ФРГ) производительностью 400 тыс. т.
В апреле 1966 г. Министерство химической промышленности СССР
поставило вопрос об ускорении внедрения новой технологии синтетиче ского аммиака в азотной промышленности, в связи с чем была образова на Научно-техническая комиссия для подготовки рекомендаций по исполь зованию новейших достижений отечественной и зарубежной пауки и техники в производстве синтетического аммиака. В комиссию вошли вид нейшие ученые и инженеры, специалисты химической промышленно сти, металлургии и машиностроения. Возглавил комиссию академик Н. М. Жаворонков. В результате изучения вопроса комиссия пришла к выводу о необходимости внедрения в кратчайший срок в промышленность
СССР высонеэкономичной системы производства аммиака с агрегатами большой единичной мощности. Комиссия подготовила доклад, в котором
ТАБЛИЦА 3. ОСНОВНЫЕ ТЕХНИКО-ЭКОНОМИЧЕСКИЕ ПОКАЗАТЕЛИ АГРЕГАТОВ ПРОИЗВОДСТВА АММИАКА
|
|
Установка |
|
|
|
600 т/сут фир |
|
Показатель |
Типовой |
мы «ЭНСА» |
Установка |
проект |
для Черкас |
1200—1500т/сут |
|
|
|
ского хими |
фирмы «УДЕ» |
|
|
ческого ком |
|
|
|
бината |
|
Удельный расход природного газа в пересчете |
960 |
Н28 |
1142 |
на газ калорийностью 7800 ккал/м3, м3/т |
|
|
|
Удельный расход электроэнергии, кВт-ч |
1390 |
768 |
33,4 |
Удельный расход пара за вычетом отхода, |
0,65 |
0,6 |
— |
Мкал/т |
|
|
|
Расход охлаждающей оборотной воды, м3/т |
369 |
285 |
190 |
Заводская себестоимость в действующих ценах |
54 |
44 |
34 |
Новомосковского химического комбината, руб/т |
|
|
|
Удельные капиталовложения на промышленное |
150 |
108 |
77 |
строительство, руб/т |
|
|
|
В том числе стоимость оборудования, руб/т |
88,5 |
54 |
34 |
Сопряжеипые капиталовложения в топливную |
76 |
58 |
46 |
промышленность и энергетику, руб/т |
|
|
|
даы апализ состояния и перспектив развития отечественной и зарубеж ной азотной промышленности и сформулированы задачи создания комп лексного оборудования для крупных технологических систем производства аммиака и обеспечения их жаропрочными металлическими сплавами и высоколегированными сталями, а также другими материалами.
Решение поставленных задач было связано с преодолением многих трудностей, причиной которых являлась неподготовленность металлурги ческой промышленности и машиностроения. Однако эти трудности были успешно преодолены. На первых порах пришлось прибегнуть к импорту оборудования. В 1965 г. у фирмы «ЭНСА» была закуплена установка по производству аммиака, состоящая из двух липий по 600 т/сут каждая (мощность завода 400 тыс. т аммиака в год).
Вустановке были применены многие новые технологические процессы
иаппаратура: бескислородная каталитическая конверсия природного газа
сводяным паром в трубчатых печах под давлением 3 МПа, глубокая конверсия окиси углерода на низкотемпературном катализаторе, очистка азото-водородной смеси от кислородсодержащих соединений каталитиче ским гидрированием (метаиирование); использовались поршневые ком прессоры для сжатия синтез-газа до рабочего давления 30 МПа, так как фирма не располагала турбокомпрессорами. Оборудование было смонти ровано на Черкасском химическом комбинате и вступило в строй дейст вующих в 1970 г.
Первый агрегат большой единичной мощности на импортном оборудо вании производительностью 1360 т/сут был построен п сдан в эксплуата
цию в феврале 1973 г. на Невипномысском химическом комбинате. На этой установке производство аммиака было запроектировано в виде одной технологической линии.
Для получения всего продукционного аммиака в жидком виде с обес печением возможности его храпения в изотермическом хранилище при температуре —34° С без давлеппя предусмотрена установка компримиро вания и конденсации аммиака. Имеется возможность передачи части газо образного аммиака на другие предприятия в количестве, достигающем
25т/ч.
Вкачестве приводов для компрессоров, дымососов и большинства рабо чих насосов на Невипномысском комбинате установлены паровые турби ны. Получение необходимого количества пара для процесса и паровых приводов обеспечивается за счет утилизации тепла дымовых и техноло гических газов, а также за счет тепла сжигания природного газа во вспомогательном котле. Охлаждение технологических потоков на всех стадиях процесса, в том числе и конденсация отработанного па турбинах пара, осуществляется в холодильниках с воздушным охлаждением. Пита тельная вода для котлов-утилизаторов готовится в специальной установке деминерализации воды.
Управление основными стадиями процесса централизовано и осуществ
ляется из центрального диспетчерского пункта (ЦПУ). Автоматическое регулирование параметров процесса производится с помощью электронно пневматических и электрических систем. Отклонения параметров процес са и состояние оборудования фиксируются системой предупредительной сигнализации. Возникновение аварийных ситуаций предупреждается си стемами защиты (блокировки), которые автоматически ставят производ ство в положение безопасности. Остановка производства в целом и отдель-
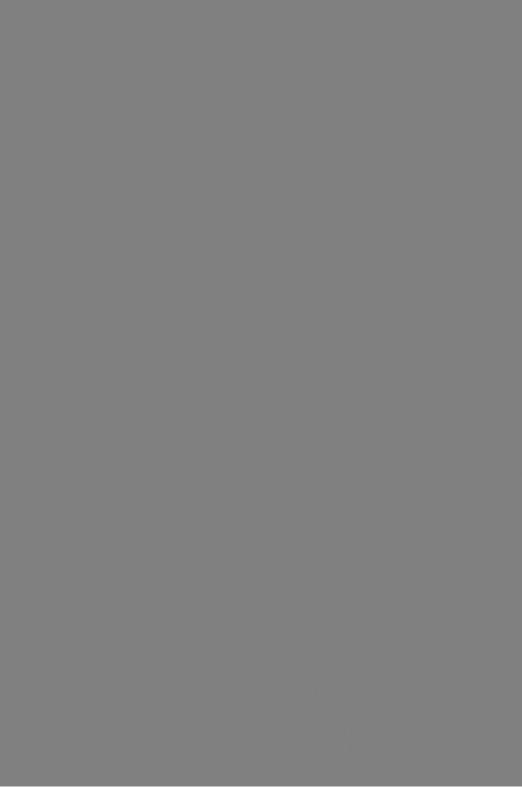
скую схему получения продукта. Различия состоят в конструктивном оформлении оборудования.
Опыт работы первого круппого импортного агрегата па Невинномысском и результаты эксплуатации первого отечественного агрегата на Новомосковском ПО «Азот» показали, что оборудование является работо способным и достаточно надежным. По состоянию на 1 января 1980 г. мощность крупных агрегатов синтеза аммиака составила 49,2% от общей мощности производства аммиака в СССР.
Ввод в действие первого крупнотоннажного агрегата синтеза аммиака позволил снизить его себестоимость в два раза, значительно сократить удельные капитальные вложения, резко повысить производительность труда. На Невпнномысском ПО «Азот» себестоимость 1 т аммиака, вырабо танного на крупном агрегате, в 1974 г. была в 2,3 раза ниже выработан ного на агрегатах меньшей мощности, а производительность труда соот ветственно в 7 раз выше.
Эиерготехнологические агрегаты по производству аммиака разработа ны с максимальным применением воздушного охлаждения. В результате использования тепла реакций и воздушного охлаждения потребление обо ротной воды снизилось в два раза. Технологическая схема агрегата харак теризуется глубокой рекуперацией тепла экзотермических стадий процес са. Низкопотенциальное тепло конвертированной паро-газовой смеси, отпариого газа разгонки конденсата использовано для получения холода на различных уровнях, а также для подогрева питательной воды котлов. Высокопотенциальное тепло технологического газа, дымовых газов труб чатой печи использовано для получения пара, необходимого для паровой турбины турбокомпрессора азото-водородной смеси. Пар применяется для технологических целей, приводов компрессоров природного газа и возду ха, дымососов и ряда центробежных насосов. Технологический процесс значительно автоматизирован с помощью электронных приборов и ЭВМ. Создание таких агрегатов явилось результатом прогресса пауки, творче ской инжепериой мысли и достижепий машиностроения и материалове дения.
Современное аммиачное производство представляет собой эперготехпологическин комплекс. Потребность в энергии полностью покрывается за счет сбалансированного использования тепловых отходов в процессах производства. Технический прогресс в производстве синтетического ам миака характеризуется следующими показателями: суммарный расход энергии на производство тоипы синтетического аммиака в агрегате боль шой единичной мощности (1360 т/сут) с применением в качестве сырья природного газа в 2,5 раза меньше, чем в старых агрегатах меньшей мощности с применением кокса или каменного угля для получения водо рода, и в 3 раза меньше, чем с использованием водорода, получаемого электролизом воды (табл. 4).
В первых установках 1928 г. производительность колонн синтеза ам миака с внутренним диаметром 400 мм составляла 8 т/сут и несмотря на экзотермичпость реакций, вследствие больших потерь тепла в окру жающую среду, приходилось непрерывно осуществлять электроподогрев азото-водородной смеси. В современных установках производительностью 1360 т/сут в колоннах синтеза с внутренним диаметром 2400 мм прихо дится отводить большое количество тепла, которое используется для подогрева воды парокотельпых установок.