
книги / Развитие химической промышленности в СССР (1917-1980). Т. 2 Развитие отдельных отраслей химической промышленности
.pdfразвития хлорной промышленности в СССР сопровождался разработкой технологии и организацией производства многих новых хлорпродуктов.
Вгоды первой пятилетки было организовано производство бертолето вой соли, хлористой серы, продуктов хлорирования бензола, начато строи тельство цехов хлористого алюминия, трихлорэтилена и др., расширено производство жидкого хлора, соляной кислоты.
Вгоды второй пятилетки вошли в строй новые цеха и увеличилась выработка хлора и каустической соды, пущены первые производства хло ристого алюминия, гипохлорита кальция и синтетической соляной кисло ты, новые установки сжижения хлора и производства хлорной извести.
Русские ученые и инженеры внесли большой вклад в развитие элек трохимической науки. Достаточно указать на работы академика В. В. Пет рова по электролизу воды, ряда неорганических и органических соедине ний, академика Б. С. Якоби по гальванопластике, инженеров Ф. Вощука
пН. Глухова, сконструировавших первые в мире электролизеры для по лучения хлора и каустической соды и др.
Из-за отсутствия подготовленных технических кадров в восстанови тельный период и в начале первой пятилетки развитие хлорной промыш ленности базировалось на использовании импортной техники. Электроли зеры Грисгейм—Электрон старой конструкции применялись в Советском Союзе на заводах в Славяпске и Рубежном до 1927 г., а затем были за менены электролизерами Сименс—Биллитера, после того как этот тип электролизеров был испытан на Березниковском содовом заводе.
Две установки для производства хлора были оборудованы в тот пе риод вертикальными электролизерами типа «Кребс» с диафрагмой.
Одновременно усиленно проводилась подготовка научных и инженер ных кадров в области электрохимии, развивались научно-исследователь ские, конструкторские и проектные работы по электрохимическим произ водствам в ГИПХе, Гипрохиме и других научно-исследовательских и проектных институтах. Исследовались электрохимические процессы, изу чались повые типы электродов и диафрагм, разрабатывались технология
иконструкции электролизеров.
В1925 г. был включен в работу цех электролиза в Самаре, оборудо ванный цилиндрическими электролизерами, модернизированными совет скими специалистами, и уже в начале 30-х годов была разработана со ветская конструкция электролизера Х-2 па нагрузку 1 кА, которая по своим показателям находилась на уровне наиболее экономичных в то время иностранных конструкций. Начппая с этого времени производство хлора и каустической соды в Советском Союзе в основном осуществлялось с использованием электролизеров советских конструкций. В 1930—1931гг. был введен в действие ряд хлорных заводов, оборудованных этими элект ролизерами.
Е дальнейшем была проведена работа по увеличению мощности элект ролизера Х-2 за счет установки в нем второго дополнительного катода. С 1937 г. на заводах начинает использоваться модернизированная конст рукция электролизера Х-3 на нагрузку 1,5 кА. Применение электролизе ров Х-3 вместо Х-2 позволило затем во время Великой Отечественной войны увеличить мощности действующих цехов электролиза на 30—50%. Интенсификация электролизера Х-3 продолжалась за счет установки до полнительных катодов без изменения габаритов аппарата. Эта работа полу чила свое завершение в конструкции электролизера БГК-12 на нагрузку
2,2 кА [13]. Новые электролизеры, а также усовершенствования других технологических стадий производственного процесса, разработанные со ветскими специалистами, были использованы для развития производства хлора и каустической соды в 30—40-х годах.
В середине 30-х годов в Советском Союзе* начались работы по произ водству графитированиых анодов. До того времени производство электро литического хлора основывалось на импорте анодов из США и Германии. Работы велись на Днепровском электродном заводе и завершились пол ным успехом. Уже с конца 30-х годов оказалось возможным на всех за водах постепенно внедрить советские графитировапные аноды, по каче ству пе уступавшие импортным образцам. В тот же период на Ярослав ском асбестовом заводе удалось добиться больших успехов в производстве листовой асбестовой диафрагмы.
В 1927 г. была ликвидирована устаревшая конструкция электролизе ров Грисгейм—Электрой, в 1928 г. прекращено производство хлора по химическому методу на Бондюжском заводе, а с внедрением новых кон струкций электролизеров Сименс—Биллитера, Кребса и отечественных цилиндрических осуществлен переход с периодического процесса на не подвижном электролите на непрерывный режим работы с проточным электролитом. Это обеспечило значительное повышение концентрации электрощелочи и выхода по току, снижение удельных затрат электроэнер гии и анодных материалов, облегчение труда рабочих по обслуживанию, улучшение санитарных условий в цехе и более эффективное использова ние площади цеха электролиза.
Переход от цементной диафрагмы на листовую асбестовую открыл воз можность конструировать более компактные цилиндрические электроли зеры со значительным уменьшением межэлектродного расстояния и более высокими показателями их работы. Новые типы электролизеров позволя ли получать более концентрированную щелочь и снизить затраты пара на упарку щелоков, благодаря большей компактности они экономили производственные площади. Так, при оборудовании цеха электролизерами Грисгейм—Электрой на мощность 1 т/сут хлора требовалось в цехе электролиза, включая проходы между электролизерами, 350 м2 площади пола, в то время как для отечественных конструкций цилиндрических электролизеров — только 39,3 м2. Применение новых типов электролизе ров обеспечило значительное сокращение капитальных вложении па строительство цехов электролитического хлора и позволило увеличить мощность хлорных цехов действующих заводов в Славяиске и Рубежпом. В электролизерах новых типов получали концентрированный хлор с меньшим содежанием углекислоты, что имело большое значение для по лучения хлорной извести с более высоким содержанием активного хло ра, а также* для производства жидкого хлора и других хлорпродуктов.
К 1941 г. в Советском Союзе уже была создана мощная хлорная про мышленность, выпускавшая электролитическую каустическую соду и хлор, а также широкий ассортимент хлорпродуктов, обеспечивающих удовлетворение потребностей народного хозяйства и обороны страны.
Во время Великой Отечественной войны хлорной промышленности был нанесен огромный ущерб. Более одной трети всех мощностей хлорной промышленности было выведено из строя. Часть предприятий была эвакуирована в восточные районы страны, где выпускали продукцию не обходимую для обороны. Была проведена работа по расширению про-
пзводства каустической соды, хлора и хлорпродуктов в восточных райо нах страны. Общая выработка хлорной промышленности в 1946 г. была несколько ниже довоенного уровня 1940 г.
В послевоенные годы хлорная промышленность развивалась быстры ми темпами. Это объясняется, тем, что се продукция находит широкое применение в отраслях техники, определяющих важные направления тех нического процесса. Чистая каустическая сода и разнообразные хлорпродукты широко используются в производстве синтетических полимер ных материалов, пластических масс, в реактивной технике, в производ стве ядохимикатов, растворителей и др. Динамика роста производства каустической соды (1 0 0 %-нощ в тыс. т) показана ниже [14]:
1913 г. |
51 |
1940 г. |
175 |
1970 г. |
1783 |
1928г. |
54 |
1950 г. |
299 |
1975 г. |
2395 |
1932 г. |
74 |
1960 г. |
704 |
1980 г. |
2755 |
Если в 1913 г. электролитическим методом получали только ~20% всего производства каустической соды, то к 1980 г. этим методом было выработано основное ее количество.
Продукция хлорной промышленности выросла как за счет расширения и реконструкции существовавших хлорных заводов, так и в результате строительства новых хлорных предприятий. Число действующих хлорпых заводов в десятой пятилетке достигло 30. Среди них крупные хлорные установки, вырабатывающие более* 250 тыс. т хлора/год: ПО «Капролак там» в Дзержинске, Калушское ПО «Хлорвинил», Стерлитамакское ПО «Каустик» и др. [15].
Быстрое развитие хлорной промышленности в послевоенпые годы ба зировалось на совершенствовании техники производства, увеличении мощности заводов и сопровождалось расширением ассортимента хлор продуктов. Этому способствовало создание в научно-исследовательских и проектных институтах, а также на основных предприятиях прикладной электрохимии творческих коллективов, успешно решавших задачи разви тия производства и совершенствования его технического уровня.
В период первых пятилеток типовые мощности хлорных заводов со ставляли 5 и 10 тыс. т каустической соды в год. В послевоенный период цехи диафрагменного электролиза строились мощностью в 65—70, а в по следнее время 200—300 тыс. т каустической соды в год. Непрерывно укрупнялись производственные* агрегаты и создавались новые типы элек тролизеров.
Для реконструкции действующих цехов и строительства новых в пер вые послевоенные годы были использованы цилиндрические электролизе
ры |
БГК-12 |
с четырьями катодами, листовой диафрагмой и нагрузкой |
2,2 |
кА, а с |
начала 50-х годов стали применяться новые электролизеры |
сосажденной диафрагмой.
Входе работ по созданию новой техники хлорной промышленности в
СССР проведены оригинальные исследовательские, конструкторские, проектные и опытные работы, обеспечившие переход хлорной промышлен ности на новую, более высокую ступень техники и технологии. Подготов лены, а затем стали успешно внедряться в промышленность новые кон струкции электролизеров и новые приемы работы на них.
В области электролиза с диафрагмой изучался метод нанесения на катод асбестовой диафрагмы с целью конструирования максимально уп-
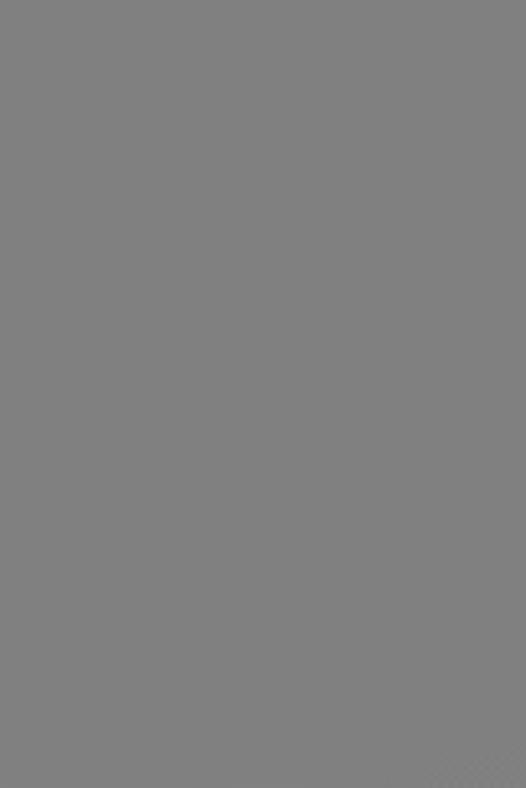
были установлены на Днепродзержинском химическом комбинате и на других предприятиях хлорной промышленности.
Крупным шагом в повышении уровня техники хлорного производства была разработка, а затем внедрение в промышленность малоизнашивающихся анодов (МИА) с активным слоем из смеси окислов рутения и ти тана, наносимых на титановую основу анода. Они получили название ОРТА [16]. Применение ОРТА позволило интенсифицировать процесс электролиза и осуществить дальнейшее увеличение мощности электроли зеров. Электролизеры с такими анодами па нагрузку 50 и 100 кА стали использоваться при строительстве всех хлорных производств, работающих но способу электролиза с фильтрующей диафрагмой. Этими электроли зерами оборудованы производства хлора на Калушском, Первомайском и других химических заводах. Интенсивно осуществляется также пере вод действующих цехов на новые аноды. В конце десятой пятилетки око ло 35% производимого хлора в нашей стране получали на электролизе рах с анодами ОРТА, доля которых в общем производстве хлора подни мется в одиннадцатой пятилетке до 70%. Применение мощных электролизеров с малоизнашпвающпмися анодами позволило снизить удельные затраты электрической энергии, резко сократить трудовые за траты на обслуживание и ремонт электролизеров и улучшить технико-эко номические показатели производства.
Работа по дальнейшему усовершенствованию техники электролиза про должается. Разрабатываются новые типы диафрагм с длительным сроком службы, проходят испытания конструкции электролизеров с проточной диафрагмой и биполярным включением электродов; разрабатываются конструкции электролизеров с ионообменными мембранами с целью получения чистой каустической соды без применения ртути с высокими технико-экономическими показателями.
Современные советские конструкции электролизеров успешно исполь зуются для развития производства хлора также в социалистических стра нах —в Румынии, Венгрии, Польше, Болгарии и др.
Ртутным методом в России в 1913 г. производилось около 60—65% общей выработки хлора. После Октябрьской революции производство хлора развивалось преимущественно по методу с диафрагмой. Единст венная установка по производству хлора и каустической соды по методу с ртутным катодом сохранялась на Донецком содовом заводе, оборудован ном стальными бетонированными электролизерами с платиновыми анода ми. Впоследствии платиновые аноды были заменены анодами из графи товых стержней и в таком виде производство действовало до 1941 г.; в связи с временной оккупацией Донбасса оно было прекращено.
После освобождения Донбасса производство па Донецком содовом за воде как морально устаревшее не было восстановлено, и развитие электро лиза с ртутным катодом шло в дальнейшем на более совершенной техни ческой базе.
Новые цехи ртутного электролиза, введенные в эксплуатацию после 1945 г., оборудовались стальными гуммированными электролизерами на пагрузку 15 кА при плотности тока 2,5—3,0 кА/м\ Большая работа, прове денная коллективом научных работников, конструкторов и проектиров щиков совместно с сотрудниками заводов, позволила успешно решить вопросы интенсификации производства и поднять нагрузку па электро лизеры до 30 кА, повысив плотность тока до 5—6 кА/м2.
Благодаря ряду технических усовершенствований интенсификация электролиза не сопровождалась увеличением расхода электроэнергии и напряжения па электролизере.
После окончания войны для оборудования вновь строящихся цехов были разработаны электролизеры Р-30 на нагрузку 30 кА с плотностью тока 5,0—6,0 кА/м2. Такими электролизерами было оборудовано несколь ко цехов в пашей стране и цех в Венгрии.
Большая потребность народного хозяйства, особенно вискозной про мышленности, в чистой каустической соде обусловила необходимость дальнейшего роста производства по методу электролиза с ртутным като дом. В 60-х годах для строительства была принята типовая мощность завода около 1 0 0 тыс. т каустической соды в год, п для оснащения таких заводов разработаны советские конструкции электролизеров с ртутным катодом на нагрузку в 100 кА. Этими электролизерами было оборудовано три цеха. В последние годы стали применять конструкцию электролизе ров СДМ па нагрузку до 200 кА, разработанных в СССР совместно со специалистами ГДР. На двух заводах было использовано оборудование фирм «Кребс» и «Де-Нора» [7, с. 184].
После окончания Великой Отечественной войны в стране не было про изводства чистой каустической соды, по благодаря вводу новых цехов доля электролиза с ртутпым катодом в электрохимическом производстве каустической соды возросла до 13% в 1958 г. и до 34% в 1965 г. В 1970 г. она составила 33,3% и снизилась в 1980 г. до 32%.
За прошедшие годы была разработана и применена новая техника для всех стадий производственного процесса получения хлора и каусти ческой соды и осуществлена перестройка производства на основе более совершенной технологии.
Новые хлорные производства, как правило, размещаются вблизи при родных запасов соли. Хлорная промышленность все в большей степени переходит на использование дешевого сырья в виде рассолов, получаемых подземным растворением соли, пли искусственных рассолов. Стоимость получаемых рассолов примерно в 1 0 раз дешевле, чем прп использова нии твердой соли. Резко сократилось число предприятий, работающих на привозной поваренной соли.
Подготовка и очистка рассола полностью переведены на непрерывный процесс с осветлением растворов в разного типа осветлителях, в том чи сле и со шламовым фильтром. Для интенсификации процесса осветлепия применяются флокулянты, в частности гидролизованпый полиакриламид. Фильтрация рассола проводится на автоматических насыпных фильтрах или на фильтрах Келли.,
Для охлаждения хлора стали широко применять титановые холодиль ники; для перекачки и компримирования —турбокомпрессоры и винто вые компрессоры на 0,3—1,2 МПа. Для очистки хлора от загрязняющих его аэрозолей широко применяется фильтрование влажного и сухого хло ра через фильтры из стекловолокнистой композиции, а также электро фильтры. Высокая степень осушки хлора до остаточного содержания не более 60—100 мг Н20 /м3 позволяет снизить процессы коррозии па ста дии компримирования, транспорта и потребления хлора. Разработаны и осуществлены в промышленности схемы двухступенчатого снижения хло ра с высоким коэффициентом сжижения, близким к 99%. Хлорные пред приятия оснащены современными мощными выпарными системами для
выпарки электролитических щелоков и для получения кристаллической соли для цехов электролиза с ртутным катодом пз рассолов подземного растворения. На выпарных установках автоматизированы основные про цессы.
Для изготовления трубопроводов, аппаратуры и арматуры применяют ся титан, гуммированная сталь, стеклопластики, что позволяет повысить надежность производственных схем и улучшить санитарные условия про изводства. Преобразовательные подстанции при хлорных заводах стали оборудовать современными мощными кремниевыми выпрямителями вме сто устаревших мотор-геиераторов и ртутных выпрямителей.
Широко используется автоматизация контроля и управления произ водством на многих стадиях технологического процесса, проводится заме на операций с ручным трудом на механизированные.
Хлорные предприятия все в большей степени переходят от автомати зации контроля и управления отдельных узлов производственной схемы к комплексной автоматизации технологического процесса. Начато внедре ние в хлорной промышленности автоматизированных систем управления технологическими процессами (АСУ ТП).
Весьма незначительное по размерам и отсталое по технике в прошлом электролитическое производство хлора превратилось в настоящее время в одну из важных отраслей социалистической промышленности, поставляю щей народному хозяйству все расширяющийся ассортимент разнообраз ных продуктов.
Большую роль в развитии техники хлорной промышленности сыграла творческая деятельность научно-исследовательских и проектных институ тов, конструкторских и экспериментальных групп и лабораторий в центре и на периферии, инженерно-технических коллективов предприятий, кото рые отдали свои знания, опыт и инициативу решению многих техниче ских проблем, возникавших в процессе развития этой отрасли промыш ленности. Большой вклад в развитие хлорной промышленности внесли, помимо перечисленных ранее, А. В. Блинов, Л. В. Гантман, Л. Ш. Генин, Н. Н. Иванов, Г. М. Камарьян, В. А. Новоселов, Ф. А. Орлова, В. И. Пыльнов, Т. В. Селезнев, 3. С. Смолян, В. И. Сучков, К. П. Титов, М. В. Хрулев, С. С. Шрайбман, С. Я . Файнштейи, В. Г. Флейшман и многие другие работники научно-исследовательских, конструкторских, проектных инсти тутов, а также предприятий прикладной электрохимии.
Расширялся ассортимент продукции, выпускаемой хлорной промыш ленностью. В связи с быстрым развитием нефтехимической промышлен ности более 80% всего хлора используется на хлорных заводах для производства различных полимерных материалов, хлороргаиических раст ворителей, продуктов хлорирования метана, бензола и других углеводоро дов, химических средств защиты растений, моющих средств, промежуточ ных органических продуктов и большого ассортимента неорганических хлорпродуктов.
В1956 г. на хлорных предприятиях выпускалось более 40 различных хлорпродуктов [15, с. 839], а в настоящее время —более 200 наимено ваний.
Вкрупных масштабах производятся следующие неорганические хлорпродукты: безводный хлористый алюминий, твердый гипохлорид каль
ция, бертолетова соль, четыреххлористый кремний, хлориды фосфора и серы, безводное хлорное железо и его водпые растворы, соляная кислой
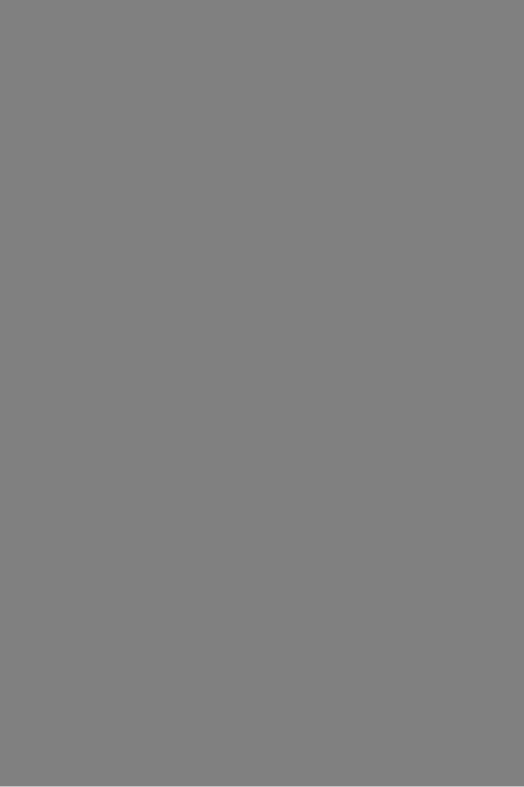
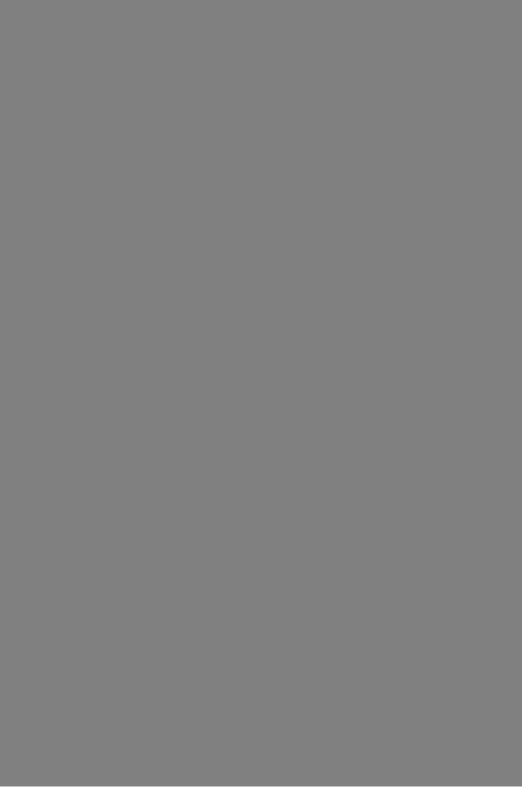
Электролиз воды в первой половине XX в. получил большое* развитие в странах, богатых гидроэлектроэнергией, для нужд производства синте тического аммиака и других целей. В СССР, Италии, скандинавских и других странах созданы крупные установки по электролизу воды [17]. Однако успехи в области производства водорода из природного газа и углеродсодержащего сырья привели к тому, что для крупных потреби телей водорода в химической и нефтехимической промышленности в на стоящее время применяют главным образом водород, полученный хими ческими способами или в процессе пиролиза нефтяных фракций.
Разработка процесса электролиза воды в нашей стране была начата в годы первых пятилеток в связи со строительством Чирчикского электро химического комбината для синтеза аммиака и производства азотпых удобрений. Для получения водорода было решено использовать электро лиз воды на базе электроэнергии гидроэлектростанций на реке Чпрчик. Предстояло создать самое крупное в то время в мире производство водо рода электрохимическим методом с потреблением 120 мВт электроэнер гии. К тому времени на различных заводах нашей страны имелись не большие установки электролиза воды мощностью по несколько киловатт, оборудованные устаревшими зарубежными конструкциями электролизе ров. Необходимо было заново разработать теорию и технологию, конст рукцию электролизера большой мощности и организовать производство оборудования на отечественных заводах.
Благодаря применению щелочных электролитов, разработке методов изготовления высокоустойчивых диафрагм, изоляторов, прокладочных ма териалов, конструкции электродов и других деталей электролизера, а так же способов защиты их от коррозии, удалось создать конструкцию фильтр-
прессиого биполярного электролизера, |
получившего индекс |
ФВ-500, |
из 160—170 последовательно включенных |
ячеек на нагрузку |
до 10 кА |
с мощностью до 3500—4000 кВт. В электролизерах были полностью автоматизированы схемы питания водой и регулирование давления, температуры и других параметров. Электролизеры работали без ремонта в течение 5—10 лет. Производство электролизеров было налажено на киевском машиностроительном заводе «Большевик».
Опытная модель электролизера из 56 ячеек была испытана в 1936— 1937 гг. па опытном заводе «Чирчикстрой», а в 1940 г. были включены под нагрузку первые серии электролизеров ФВ-500 в цехе электролиза Чирчикского электрохимического комбината. Во время Великой Отечест венной войны цех электролиза этого комбината бесперебойно снабжал производство аммиака водородом, азотной кислоты —кислородом, внеся свой вклад в общее дело победы над врагом. За разработку конструкции электролизера ФВ-500 и освоение процесса электролиза в промышленно сти группе специалистов (А. И. Колосков, Л. М. Якименко, Л. Ш. Генин, П. И. Соколов, В. Г. Хомяков) была присуждена Государственная пре мия СССР.
В 1940—1941 гг. был разработан проект организации производства тяжелой воды в цехе электролиза па одном из заводов. Тяжелая вода предназначалась для использования в иаучпых исследованиях. Мощность установки небольшая — 8 кг/год. В связи с началом войны проект не был реализован. В 1944 г. начались работы по организации производства тяжелой воды в промышленных масштабах. Была принята оригинальная отечественная схема [18] с пизкимп затратами тепловой энергии. Конст-