
книги / Развитие химической промышленности в СССР (1917-1980). Т. 2 Развитие отдельных отраслей химической промышленности
.pdfрукцпя электролизера ФВ-500 была модернизирована, и уже в начале 1945 г. включена под нагрузку первая очередь производства тяжелой воды в цехе электролиза.
В дальнейшем процесс электролиза воды был широко использован в нашей стране для получения водорода для нужд синтеза аммиака и од новременно для производства тяжелой воды. До пуска первой установки получения тяжелой воды методом низкотемпературной ректификации жидкого водорода основное количество тяжелой воды практически цели ком получалось на установках электролиза воды.
Электролитический способ получения водорода и кислорода в послед ние десятилетия широко применяется также для удовлетворения потреб ности в водороде и кислороде большого количества сравнительно неболь ших его потребителей, предъявляющих высокие требования к чистоте газов. Электролитический водород широко используют для гидрогенизации жиров и получения других органических и неорганических продуктов, в системах охлаждения мощных электрических генераторов, в металло обработке для создания восстановительной атмосферы, в производство искусственных драгоценных камней и др.
Для большинства мелких потребителей водорода и кислорода особый интерес представляют электролизеры, работающие под избыточным дав лением. Впервые эта задача была решена в нашей стране.
В конце 30-х годов в СССР группой специалистов разработана конст рукция электролизеров типа ЭФ для получения водорода и кислорода под давлением до 1,5 МПа. Первые электролизеры такого типа были установлены перед Великой Отечественной войной на Ленинградском фарфоровом заводе, и затем они стали широко применяться в различных отраслях народного хозяйства. После войны была создана конструкция электролизеров типа СЭУ для работы под давлением до 1 МПа. Сейчас на предприятиях страны действует более 1 0 0 0 электролизеров для работы под давлением; завершается работа по созданию более совершенного электролизера большой мощности (Ф. 3. Серебряискнй и др.).
Электролитическое производство водорода для крупных его потреби телей не может конкурировать с получением водорода из природного газа или нефтяных фракций, однако в связи с ограниченностью запасов при родного газа, нефти и угля электролиз воды в будущем получит новое развитие как одни из возможных путей производства больших количеств водорода из воды, для нужд химической промышленности и для замены природного газа. В связи с этим в нашей стране начаты исследования по совершенствованию существующего процесса электролиза воды, а так же по разработке высокотемпературного электролиза водяного пара и электролиза с ионообменными мембранами.
*
«Основные направления экономического и социального развития СССР
на 1981—1985 годы и на период до 1990 года», утвержденные на XXVI съезде КПСС, выдвигают большие задачи перед электрохимической про мышленностью и наукой. Помимо быстрого роста объема производства, не обходимо обеспечить увеличение ассортимента и качества выпускаемой продукции с целью более полного удовлетворения всех запросов народно го хозяйства страны.
ГЛАВА ШЕСТАЯ
КАЛЬЦИНИРОВАННАЯ СОДА
Содовая промышленность была представлена в России в начале XX в. тремя предприятиями —Березниковским. Донецким и Славянским содо выми заводами. Они выпускали продукцию по аммиачному способу, со зданному в последней четверти XIX в. Этот способ основан на реакции взаимодействия раствора хлористого натрия, аммиака и углекислого газа с образованием бикарбоната натрия, выпадающего в осадок, и раствора хлористого аммония с последующим прокаливанием бикарбоната натрия для получения углекислого натрия (кальцинированной соды) и углекис лого газа, возвращаемого в процесс. Раствор хлористого аммония после отделения бикарбоната натрия обрабатывается известковым молоком для регенерации возвращаемого в процесс аммиака. При этом образуется раст вор хлорида кальция.
Необходимые для содового процесса известь и углекислый газ полу чаются при обжиге известняка или мела в известково-обжигательных печах.
В мировой практике аммиачному способу предшествовал процесс по лучения соды по методу Леблана, основанный на реакции взаимодейст вия сульфата натрия (природного или полученного из хлористого патрия при разложении его серной кислотой) с известняком и углем при высо кой температуре. Этот способ не получил сколько-нибудь значительного распространения в России [1, с. 141].
Развитие производства соды аммиачным методом происходило преиму щественно на осиове аппаратурного оформления непрерывного процесса, разработанного бельгийской фирмой «Сольвэ».
Фундаментальные научные исследования процесса были выполнены выдающимся русским химиком П. П. Федотьевым. В своей работе «Аммиачно-содовый процесс с точки зрения ученых о фазах», опублико ванной в 1903—1904 гг., он теоретически определил оптимальные усло вия ведения процесса (см. [2, с. 15; 3]).
Березниковский содовый завод оспован и введен в эксплуатацию в 1883 г. в бывшей Пермской губернии на реке Каме на проектную мощ ность 6 тыс. т/год, а в 1900 г. в результате расширения производства и совершенствования технологии она достигла 24,6 тыс. т/год [1, с. 136, 141].
В 1897 г. на заводе создано производство каустической соды химиче скими методами [3, с. 22]. Первоначально применялся известковый метод получения продукта, который в дальнейшем был заменен ферритным ме тодом.
Сущность известкового метода заключалась в обработке раствора кальцинированной соды известью, а ферритного —в прокаливаппп каль цинированной соды при высокой температуре- с окпсыо железа с образо ванием феррита натрия, из которого при последующем выщелачивании водой получались раствор каустической соды и возвращаемая в процесс окись железа.
В конце 1891 г. был оспован второй, более крупный, Донецкий содо вый завод. В 1896 г. на заводе было выработано 22,6 тыс. т кальцини рованной соды. В 1900 г. выпуск продукта достиг 37,3 тыс. т [1, с. 145]. Иа этом же заводе в 1892 г. было создано производство каустической со
ды по ферритному способу п в 1899 г.—по электролитическому ртутному методу Сольвэ [1, с. 142]. В 1901 г. па заводе был введен в действие цех очищенного пищевого бикарбоната натрия [4, с. 151].
Третье содовое предприятие —Славянский содовый завод —был вве ден в эксплуатацию в 1898 г. на базе метода Гоннгмана, применившего па ряде стадий производства кальцинированной соды в отличие от метода Сольвэ менее совершенные периодические процессы. В последующие годы (1899 п 1900) на заводе был построен цех каустической соды по извест ковому методу и цех бикарбоната натрия.
Выбор места для создания содовых предприятий определялся в основ ном наличием сырьевых ресурсов, необходимых для производства содопродуктов. Поваренная соль на Березниковском и Славянском содовых заводах поступала на производство в виде местных естественных рассо лов, па Донецкий содовый завод завозилась по железной дороге со стан ции Деконская, карбонатное сырье —известняк или мел — доставлялись по железной дороге или водным транспортом.
Суммарный выпуск кальцинированной соды на всех трех предприя тиях в 1900 г. составил 76,5 тыс. т, а вместе с Барнаульским заводом, работавшим по методу Леблана,—82,5 тыс. т [1, с. 145].
Созданию и развитию в России в последней четверти XIX в. содовой промышленности способствовало снятие в 1880 г.—под давлением науч
ной и технической |
общественности |
и |
после |
выступления |
в |
печати |
|||
Д. И. Менделеева —акциза |
на |
соль, |
а |
также |
увеличение пошлины |
на |
|||
ввозимую в страну |
соду [3, |
с. |
И ]. |
В оезультате к началу |
XX |
в. |
оте |
чественное содовое производство удовлетворяло потребности рынка, вы теснив ввозимую ранее продукцию.
Вместе с тем участие в строительстве заводов иностранного капита
ла —бельгийского и немецкого — создавало |
условия для утечки за гра |
ницу прибыли в виде дивидендов [3, с. 29]. |
|
С 1900 г. и до начала первой мировой войны производство содопродуктов продолжало развиваться и составило в 1913 г. около 160 тыс. т кальцинированной соды [1, с. 205]. Основное количество соды — 92,3 тыс. т —было выработано на Донецком содовом заводе. Здесь к тому времени было осуществлено укрупнение оборудования с установкой но вого, более мощного элемента абсорбции —дистилляции производитель ностью 260—280 т/сут; было создано производство хлористого аммония.
Наряду с этим существенно улучшилось обеспечение завода сырьем. Так, для снабжепия солью были организованы подземное растворепие каменной соли на месторождении «Карфаген» и подача рассола на завод по 38-кплометровому трубопроводу, в то время наиболее протяженного в мире [1, с. 204]. Мел стал поступать па завод непосредственно с карьера на верхнюю площадку известково-обжигательных печей.
Березниковский содовый завод за время с 1900 по 1913 г. подвергся значительной реконструкции. Паровой привод был заменен электрическим, вместо периодических аппаратов для кальцинации установлены вращаю щиеся содовые печи непрерывного действия, осуществлено расширение главного корпуса с наращением его на высоту до 46 м и заменой дере вянных конструкций па металлические, организована собственная сырье
вая база карбонатного |
сырья —Всеволодо-Вильвенский |
известковый |
карьер. Выработка соды в |
1913 г. возросла до 40,8 тыс. т |
[1, с. 205]. |
На Славянском содовом заводе к 1913 г. были введены в действие новые агрегаты, что позволило увеличить выработку кальцинированной соды с 14,6 до 26,8 тыс. т/год [1, с. 205].
Первая мировая война привела к уменьшению выработки соды на всех предприятиях, а в годы гражданской войны и интервенции они были остановлены. Первым был пущен в эксплуатацию Березниковский содо вый завод —в 1919 г., затем Донецкий содовый завод —в 1921 г., Сла вянский содовый завод —в 1926 г. [1, с. 206].
Довоенный уровень производства кальцинированной соды достигнут на Донецком содовом заводе в 1926 г., на Березниковском —в 1927 г. и на Славянском —в 1928 г. Суммарная выработка соды в 1928 г. со ставила 207 тыс. т [1, с. 206]. В целях подготовки квалифицированных рабочих кадров для содовых и смежных производств в 1924—1925 гг. на Березниковском, Донецком и Славянском содовых заводах были созданы школы фабрично-заводского ученичества (ФЗУ).
Наряду с восстановлением и развитием народного хозяйства разраба тывались и осуществлялись планы дальнейшего подъема содовой промыш ленности. Б 1925 г. па Донецком содовом заводе возобновились начатые до войны работы по установке третьего элемента абсорбции —дистилля ции, который был введен в действие в 1927 г. [1, с. 207]. С 1925 г. начата эксплуатация нового Секмеиевского мелового карьера с воздушноканатной дорогой. В 1927 г. организовано всестороннее научно-техниче ское обследование завода с участием профессоров П. П. Федотьева, Е. И. Орлова, И. А. Тищенко и привлечением молодых специалистов, приобретших производственный опыт для работы в содовой промышлен ности [5]. Особое внимание было уделено нормализации технологическо го режима и разработке мероприятий по устранению недостатков, вызы вающих потери производительности п сырьевых ресурсов.
На Березниковском содовом заводе в 1920 г. приступили к расшире нию производства кальцинированной соды с увеличением его мощности по сравнению с довоенным 1913 г. в 2 раза. Была расширена металли ческая высотная часть здания, в которой смонтирован второй элемент абсорбции—дистилляции и установлено другое дополнительное оборудо вание —карбонизационные колонны, содовые и известково-обжигатель ные печи, современные для того времени ротационные компрессоры «Иегер» для подачи углекислого газа в карбонизационные колонны, а также построена силовая станция. Выработка соды в результате вы полненных работ в 1928 г. составила 41 тыс. т [1 , с. 206].
Славянский содовый завод в 30-х годах подвергся значительной ре конструкции: часть аппаратуры была заменена более совершенной (по типу сольвеевской), в том числе периодически действующие нутч-фильт- ры — вращающимися фильтрами непрерывного действия; в отделении кальцинации вместо двухступенчатых агрегатов для переработки бикар боната натрия в кальцинированную соду установлены вращающиеся содовые печи; частпчпо механизирована работа известково-обжигатель ных печей, увеличена высотная часть здания, в котором установлен но вый элемент дистилляции. В дальнейшем все старые элементы абсорбции
идистилляции заменены на новые [1, с. 207].
В1928 г. по опыту Донецкого завода на Славянском содовом заводе было произведено обследование всех основных отделений цеха кальци-
нпрованиой соды п намечены мероприятия по дальнейшему развитию и усовершенствованию содового производства. Выработка соды в этом году составила 24,3 тыс. т [1, с. 206].
Модернизация аппаратуры цеха кальцинированной соды на Славянском
содовом заводе обеспечила к |
1930 г. увеличение |
выработки соды до |
40 тыс. т и превысила довоенный уровень на 48% |
[1, с. 207]. В 1935 г. |
|
выпуск соды достиг 58 тыс. т |
[1, с. 208]. К этому |
времени были уста |
новлены новые, более мощные элементы абсорбции—дистилляции, порш невые компрессоры с электрическим приводом и более мощные компрес соры КПС-2 с паровым приводом, изготовленные Сумским машинострои тельным заводом, а также ротационные компрессоры фирмы «Демаг». В отделении карбонизации установлены две дополнительные системы карбонаторов, в отделении кальцинации —три содовые печи и декарбонатор для обеспечения содовым раствором цеха каустической соды и производ ства бикарбоната натрия. Реконструировано и расширено энергетическое хозяйство завода.
В 20-х годах, наряду с производством кальцинированной соды амми ачным методом, было организовано получение в небольших количествах соды из природных содовых озер Петуховского и Михайловского место рождений в Западной Сибири. Сода озерной рапы получалась в процессе ее концентрации в летних условиях, вымораживания десятиводного уг лекислого натрия в зимний период и его кальцинации в подовых печах с получением кальцинированной соды. Выработка природной соды в 30-х годах достигла 8 тыс. т/год [6 ]. Суммарный выпуск кальцинирован ной соды в 1932 г. в стране составил 273 тыс. т.
Развитие содовой промышленности в период 1928—1940 гг. было на правлено на обеспечение все возрастающей потребности в содопродуктах. С этой целью расширялись и реконструировались все три действующих содовых завода, закончилось строительство новосодового завода в Славянске.
На Донецком содовом заводе в этот период были установлены четвер тый, а в дальнейшем пятый элементы абсорбции—дистилляции и дру гая аппаратура содового производства с одновременным расширением сырьевой базы, энергетического и вспомогательного хозяйства. В резуль тате производство кальцинированной соды на заводе в 1935 г. достигло 267 тыс. т [1, с. 208]. При реконструкции высотная часть здания цеха была расширена и в ней размещены абсорбционные и дистилляционные колонны, установлены дополнительные карбонизационные колонны, ком прессоры с электрическим приводом для подачи углекислого газа и содо вые печи; в цехе известково-обжигательных печей сооружены новые печи и гасители извести. На раесолопромысле введены в действие дополнитель ные рассольные скважины и проложен к заводу новый рассолопровод большего диаметра, увеличена мощность перекачивающих станций. Осу ществлена реконструкция подвесной дороги с Секменевского карьера для обеспечения подачи увеличенного количества мела на завод [5, с. 71].
На Березниковском содовом заводе в 1932 г. была дополнительно рас ширена высотная часть здания цеха, в которой установлен третий эле мент абсорбции—дистилляции, смонтированы вакуум-фильтр, газовый компрессор и вакуум-насосы, сооружены новые рассольные скважины. Были проведены мероприятия по расширению мощностей на отдельных участках производства и ликвидации «узких мест» на заводе [3, с. 71—
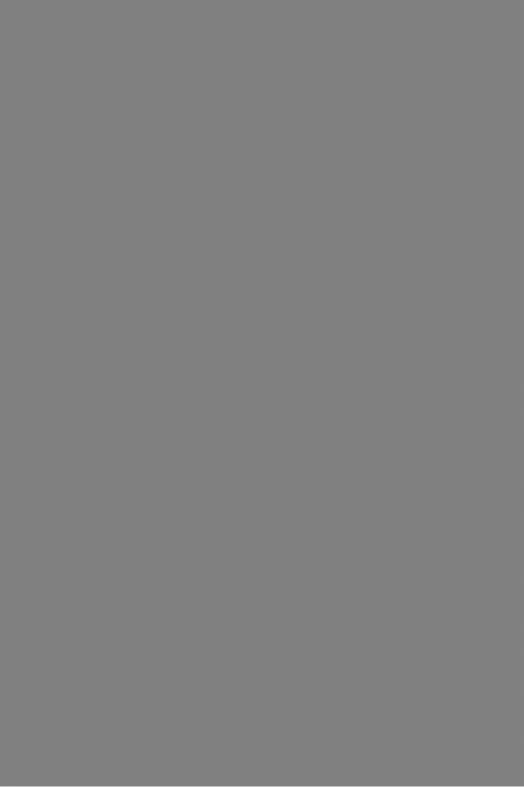
минералогии (Н. Ф. Юшкевич, И. Н. Шокпи п др.) по изучению стадий аммиачио-содового производства [1, с. 209]. Всесоюзный институт содовой промышленности (с 1956 г. Научно-исследовательский институт основной химии) выполнил ряд работ, связанных с изучением физико-химической сущности содового производства и совершенствованием производственных процессов: очистки рассола, интенсификации работы аппаратуры (из вестковых печей, дистилляцноииых колони, вакуум-фильтров), автомати ческого регулирования и контроля работы карбонизационных колонн и др.
Во время Великой Отечественной войны содовой промышленности был нанесен огромный ущерб. В результате временной оккупации прекрати лось поступление кальцинированной соды с содовых заводов Украины. Производство продукции продолжалось лишь на Березниковском содовом заводе. Небольшое количество природной соды получали на Михайлов ском содовом заводе в Алтайском крае. Оборудование Славянского ново содового завода было эвакуировано в Стерлптамак на площадку, предназ наченную для строительства содового завода на базе разведанных место рождений соли и известняка. Туда же было направлено оборудование нового цеха каустической соды по ферритному методу с Донецкого содо вого завода. Этот цех был введен в эксплуатацию в 1944 г.
Усилия работников содовой промышленности были сконцентрированы на преодолении трудностей военного времени и обеспечении нормальной работы производственных цехов Березниковского содового завода. В 1943 г. для ликвидации трудоемких работ в цехе известковых печей была смон тирована канатная дорога для подачи известняка со склада.
Для увеличения ресурсов кальцинированной соды был разработан и осуществлен проект расширения производства природной соды на Михай ловском содовом заводе и соответствующего развития общезаводского и транспортного хозяйства.
В послевоенный период перед содовой промышленностью встала зада ча восстановить разрушенные войной южные содовые заводы и ввести в
действие Славянский новосодовый и Стерлитамакскнй содовый заводы.
Восстановление Донецкого и |
Славянского содовых заводов было начато |
в 1943 г. сразу же после |
изгнания немецко-фашистских оккупантов. |
8 марта 1944 г. было введено в эксплуатацию производство кальциниро ванной соды в Славянске и вслед за ним 9 мая 1944 г.— на Донецком содовом заводе [4, с. 155].
В 1946 г. в стране было выработано 244 тыс. т кальцинированной соды.
Славянский новосодовый завод па реэвакуированном из Стерлитамака оборудовании был пущен в 1946 г., к 29-й годовщине Великой Октябрь ской социалистической революции [4, с. 155]. В 1948 г. он был объединен со старым содовым заводом в Славянский содовый комбинат.
В1950 г. довоенная производительность содовых предприятий была значительно перекрыта и составила 711 тыс. т кальцинированной соды.
Впослевоенный период осуществлялось форсированное строительство
Стерлптамакского |
содового |
завода. Пуск завода состоялся в ноябре |
1951 г., в 1955 г. |
он достиг |
проектпой мощности по производству каль |
цинированной соды 500 тыс. т/год. В соответствии с разработанным пла ном дальнейшего расширения завода мощность цеха кальцинированной соды к концу 1958 г. составила более 600 тыс. т/год.
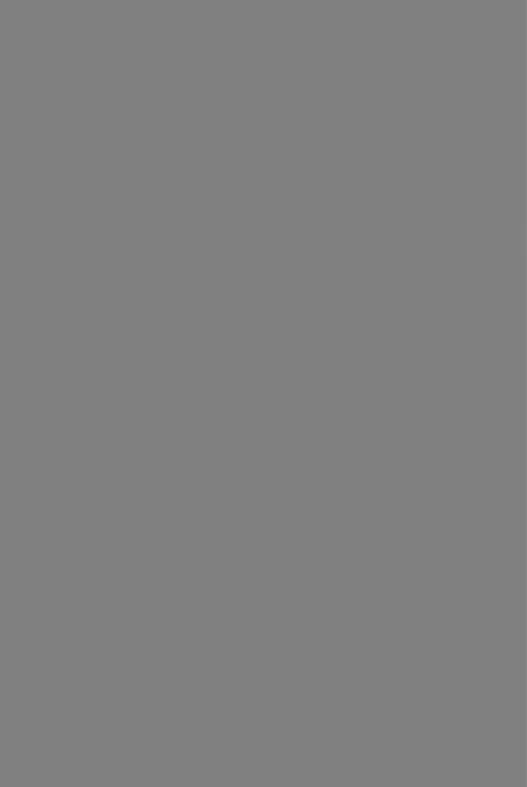
В 1957 г. па базе содового, цементного и шиферного заводов был соз дан Стерлнтамакскпй содово-цементный комбинат. Это позволило более рационально использовать сырьевые и энергетические ресурсы, укруп нить вспомогательное хозяйство п сократить административно-управлен ческий аппарат предприятия.
Усовершенствованные технологические процессы содового производ ства внедрены на действовавших до войны и восстановленных предприя тиях.
На основе исследований, проведенных Всесоюзным научно-исследова тельским и проектным институтом алюминиевой, магниевой и электрод ной промышленности (ВАМИ) в предвоенные годы, па Волховском алю миниевом заводе в 1950 г. был освоен новый метод производства содопродуктов на основе комплексной переработки нефелинового сырья на глинозем, кальцинированную соду, поташ и цемент. С этой целью была осуществлена реконструкция завода, работавшего до этого временп на традиционном сырье — боксите — п выпускавшего только глинозем.
В пятой пятилетке комплексная переработка нефелинового концентра та, получаемого, наряду с апатитовым концентратом, при переработке апатито-нефелиновой руды Кольского полуострова, в более крупном мас штабе была реализована на Пикалевском глиноземном заводе.
Метод предусматривает спекание с известняком во вращающихся пе чах нефелинового концентрата, в состав которого входят окислы алюми ния, натрия, калия и кремния. В результате спекания получают алюминаты натрия и калия. Образующийся спек после охлаждения выщелачивают с получением раствора алюмината натрия, калия и дикальцийсиликата. Алюминатпый раствор путем карбонизации разлагают на гидроокись алюминия, которая образует прп кальцинации глинозем и раствор карбонатов натрия и калия. Из этого раствора при выпаривании выделяют соду и поташ. Шлам дикальцийспликата перерабатывают на цемент. При реализации данного процесса достигается значительный эко номический эффект по сравнению с получением глинозема, содопродук тов и цемента из традиционных видов сырья (снижение эксплуатацион ных затрат —около 17%, удельных капитальных вложений —до 8%).
За разработку и промышленное освоение метода комплексной перера ботки нефелинового сырья в 1957 г. группе инженерно-технических и научных работников: И. Л. Талмуду, О. Н. Захаржевскому, В. П. Почпвалову, Н. И. Влодавцу, В. А. Крочевскому, Ф. Н. Строкову присуждена Ленинская премия [7].
В 60-е годы продолжалось расширение Стерлитамакского содово-це ментного комбината п Березниковского содового завода.
На Стерлитамакском содово-цемеигпом комбинате, наряду с расшире нием и реконструкцией, было осуществлено и строительство новых кор пусов. В них установлена высокопроизводительная колонная аппаратура абсорбции—дистилляции и карбонизации (по типу, освоенному в новом цехе на Славянском содовом комбинате) с превышением мощности по сравнению с проектной в 1,9 раза. Достигнутая к тому времени мощность элемента абсорбции—дистилляции составила 625 т соды в сутки. Парал лельно с реконструкцией и строительством производственных корпусов выполнялись работы по расширению сырьевой базы — известкового карь ера и рассолопромысла —прокладке дополнительного рассолопровода и
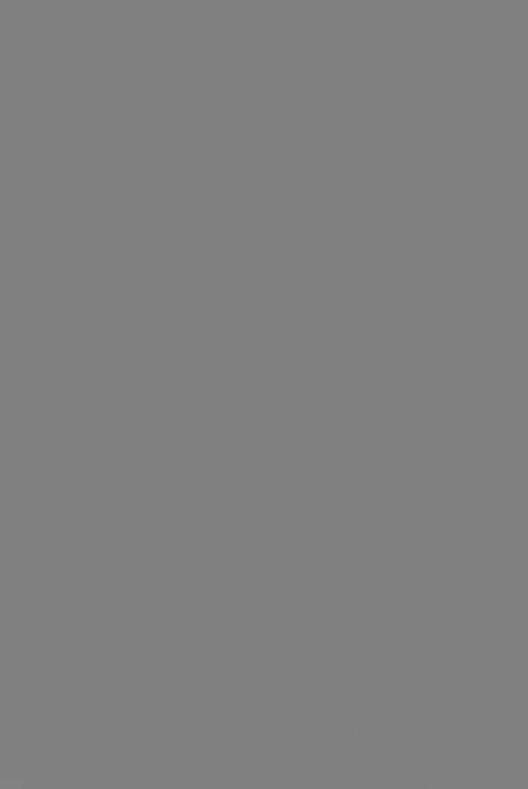