
755
.pdf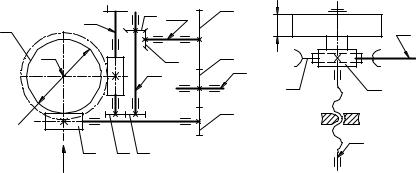
i1n i12i23...i n 1 n . |
(11.2) |
На рис. 11.1 представлена кинематическая схема лабораторной установки. При нарезании зубчатогоколеса инструменталь-
ным червяком И осуществляется станочное зацепление, ког-
да заготовка посредством согласующей кинематической цепи совершает вращательное движение по условию:
vxи = vtк, |
(11.3) |
где vxи – осевая скорость инструментального червяка; vtк – окружная скорость по делительной окружности нарезаемого колеса.
|
|
|
|
|
|
3' |
A |
|
Заготовка |
I |
|
2' |
III |
|
|
6 |
|
|
|
b |
V |
||
|
VI |
|
|
|
3 |
4 |
|
|
|
|
|
II |
|
IV |
|
|
|
|
И |
|
|
6 |
5' |
|
D |
|
|
|
|
5 |
|
|
|
|
|
|
|
|
|
|
|
5' |
1 |
2 |
|
|
VI |
|
|
|
|
|
|||
|
A |
|
|
|
|
|
|
(11.4)
(11.5)
где pxи – осевой шаг инструментального червяка, мм; zи – число заходов инструментального червяка; zк – число зубьев нарезаемого колеса; mи – осевой модуль инструментального червяка, мм; mк – модуль нарезаемого колеса; dк – делительный диаметр нарезаемого колеса; n1 – частота вращения инструментального червяка, об./мин, n6 – частота вращения заготовки.
Механизм согласования движений состоит из цилиндричес-
койпары z1/ z2,конической пары z2 / z3, цилиндрического ряда z3 / z4 /z5 и червячной передачи z5 / z6. Передаточное отношение от вала модульной червячной фрезы (инструментального червяка)дооси вращениязаготовки в соответствии сформулой (11.2):
141
|
i |
n1 |
i i |
i i |
z2 |
|
z3 |
|
z5 |
|
z6 |
, |
(11.6) |
|
|
|
|
|
|
||||||||
|
16 |
n6 |
12 |
23 35 56 |
z1 |
|
|
|
|
|
|
||
где z |
|
|
|
|
z2 |
|
z3 |
|
z5 |
|
|||
– число заходов приводного червяка. |
|
||||||||||||
5 |
|
|
|
|
|
|
|
|
|
|
|
|
|
Приравниваяправыечастиравенств(11.4)и(11.5),получаем:
mиzиn1 mк zкn6. |
(11.7) |
Отсюда передаточное отношение согласующей кинематической цепи с учетом равенства для станочного зацепления mи = mк:
|
|
n1 |
|
mкzк |
|
zк |
|
|
|
|
|
|
. |
(11.8) |
|||||
i16 |
|||||||||
|
|
n6 |
|
mиzи |
|
zи |
|
|
Результаты, рассчитанныепоформулам (11.6) и (11.8), должны совпадать.
11.1.3. Геометрия червяка |
|
Диаметр вершин червяка определяют по формуле |
|
da1 m(q 2). |
(11.9) |
Делительный диаметр: |
|
d1 mq. |
(11.10) |
Диаметр вершин инструментального червяка больше диаметра вершин червяка, находящегося в зацеплении, на величину радиальногозазора(0,2m):
daи m(q 2,4), |
(11.11) |
где m – осевой модуль червяка, равный окружному модулю колеса; q – коэффициент диаметра червяка.
Модуль нарезаемого колеса равен модулю инструментальногочервяка. Такимобразом, m= mи=m6. Величины mи qстандартизованы. Извлечение из ГОСТ 2166 приведено в табл. 11.1.
|
Таблица 11.1 |
Величины m и q (извлечение из ГОСТ 2166) |
|
|
|
Модуль m, мм |
1,6; 2; 2,5; 3,15; 4; 5; 6,3; 8; 10; 12,5; 16; 20 |
|
|
Коэффициент диаметра червяка q |
8; 10; 12,5; 16; 20 |
|
|
142
Высоту витка инструментального червяка определяют суммой двух высот головки витка и двух радиальных зазоров (ha = m):
hи = 2m + 2·0,2m = 2,4m. |
(11.12) |
Измеренная высота витка инструментального червяка hи позволит определить модуль m из формулы (11.12), а затем из формулы(11.11)вычислитькоэффициент диаметра червяка qпо измеренномудиаметрувершин инструментальногочервяка daи . Делительный угол подъема витка инструментального червяка:
arctg |
zи |
. |
(11.13) |
|
|||
|
q |
|
11.1.4. Контрольные параметры цилиндрического прямозубого колеса
Геометрические параметры нарезаемого цилиндрического колеса определяют модулем m и параметрами стандартного исходного контура по ГОСТ 13755: углом профиля = 20°; коэффициентом высоты головки зуба ha = 1; коэффициентом радиального зазора с* = 0,25; коэффициентом радиуса переходной кривой f = 0,38. В цилиндрических зубчатых колесах вычисляют четыре диаметра: делительный, основной, вершин и впадин.
Делительный диаметр: dк = mzк – формула (10.6) из лаб. работы № 10.
Основной диаметр: dbк dк cos mzк cos –формула (10.8). Диаметр вершин:
daк m z6 2ha m(z6 2). |
(11.14) |
Диаметрвпадин: |
|
dfк m zк 2ha 2c m(zк 2,5). |
(11.15) |
Модуль цилиндрического зубчатого колеса стандартизован. Извлечение из ГОСТ 9563 приведено в табл. 11.2.
|
|
Таблица 11.2 |
|
Модули цилиндрических колес m, мм |
|
|
|
|
1-й ряд |
|
1,5; 2; 2,5; 3; 4; 5; 6; 8; 10; 12; 16; 20 … 80 |
|
|
|
2-й ряд |
|
1,75; 2,25; 2,75; 3,5; 4,5; 5,5; 7 … 90 |
|
|
|
143
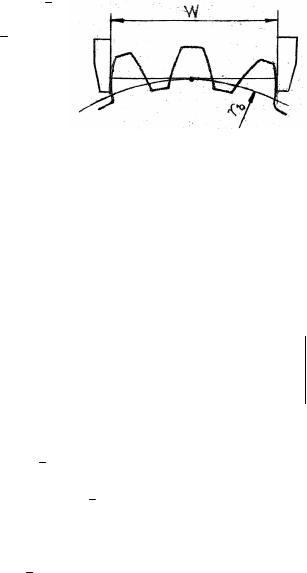
На чертежах деталей в таблице параметров указывают контрольные параметры зубчатых колес. Контроль зубьев при изготовлении колес осуществляют измерением размеров:
–длины общей нормали W;
–постоянной хорды sc ;
–высоты зуба до по-
стоянной хорды hc . ДлинуобщейнормалиW
(рис. 11.2) измеряют обхватом губками штангенциркуля определенного числа зубьев zw, зависящего от полного числа зубьев колеса z. Эта зависимость
связана с недопустимостью кромочного касания зубьев или штангенциркуля, т.е. губки штангенциркуля своими плоскостями должны касаться эвольвентной поверхности зубьев. Число охватываемых зубьев в длине общей нормали zw для прямозубых колес рассчитывают по зависимостям, приведенным в литературе, например, в [2], либо принимают из таблиц
(табл. 11.3)
Таблица 11.3
Число обхватываемых зубьев
Число зубьев |
12–18 |
19–27 |
28–36 |
37–45 |
46–54 |
55–63 |
64–72 |
73–81 |
|||||
колеса z |
|||||||||||||
|
|
|
|
|
|
|
|
|
|
|
|
||
Число обхватываемых |
2 |
|
|
3 |
4 |
5 |
6 |
7 |
8 |
9 |
|
|
|
штангенциркулем |
|
|
|
|
|||||||||
зубьев zw |
|
|
|
|
|
|
|
|
|
|
|
|
|
Длину общей нормали рассчитывают по формуле |
|
|
|
|
|||||||||
W = ( (zw – 0,5) – z inv ) mcos . |
|
(11.16) |
|||||||||||
Постоянную хорду |
s |
|
и расстояние до постоянной хорды |
|
|
||||||||
c |
hc |
(рис. 11.3) измеряют специальным инструментом — штангензубомером. Постоянная хорда sc — отрезок прямой, соединяющий две точки с разноименных профилей зуба, на пересечении профилей с нормалями к ним, проведенными из точки пересечения оси симметрии зуба с делительной окружностью d :
s |
c = 0,5 mcos2 . |
(11.17) |
144
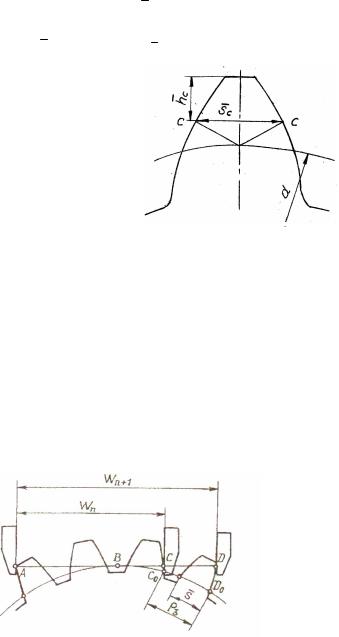
Высоту до постоянной хорды hc определяют как кратчайшее расстояние от вершины зуба до средней точки постоянной хорды: hc = 0,5(da – d – sc tg ). (11.18)
Для определения модуля нарезанного зубчатого колеса по длине общей нормали используют следующие свойства эвольвенты:
1) нормаль, проведенная из |
|
|
любой точки эвольвенты, явля- |
|
|
ется касательной к основной ок- |
|
|
ружности; |
|
|
2) отрезок нормали к эволь- |
Рис. 11.3. Схема измерения |
|
венте между точкой касания ее с |
||
постоянной хорды и высоты до |
||
основной окружностью и точкой |
постоянной хорды |
|
эвольвенты равен длине дуги ос- |
|
|
новнойокружности. |
|
Наиболее точным является метод определения модуля по разности длин общей нормали Wn и Wn +1. Схема измерений Wn и Wn +1 приведена на рис. 11.4. Величину Wn определяют обхватом zw зубьев, Wn +1 – обхватом zw +1 зубьев. Основной шаг рассчи-
тывают по формуле |
|
|
(11.19) |
pb Wn Wn 1, |
|||
искомый модуль m – по формуле: |
|
|
|
|
pb |
. |
(11.20) |
|
|||
m |
cos |
||
|
|
|
Рис. 11.4. Схема измерений основного шага
145
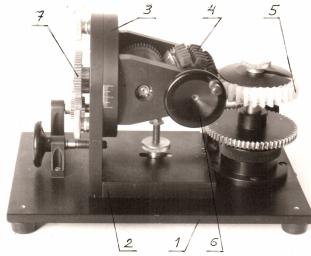
11.2.Описаниелабораторнойустановки
Общий вид лабораторной установки ТММ-СГУПС представлен на рис. 11.5. Она состоит из основания 1, по которому перемещается суппорт 2, поворотного устройства 3 с червячной фрезой 4 (инструментальным червяком) и заготовки 5. Ось червячной фрезыимеетвозможностьповорота относительнооси заготовки при помощи поворотного устройства на угол подъема винтовой линии инструментального червяка для нарезания прямозубых колес.
Рис. 11.5. Лабораторная установка ТММ-СГУПС
При вращении червячной фрезы 4 маховиком 6 при помощи согласующей кинематической цепи 7 приводится во вращение заготовкапри выполненииусловия(11.3).Дляповорота заготовки на один оборот необходимо повернуть маховик инструментального червяка на i16 оборотов. Для нарезания зубчатого колеса по всей ширине ось колеса-заготовки перемещается в вертикальномнаправлениипри помощиоднозаходноговинтасшагом p = 1,25 мм.
11.3.Порядок выполнения работы
1.Ознакомиться с теоретическими сведениями и устройством лабораторной установки ТММ-СГУПС.
2.Измерить диаметр D и ширину b заготовки.
146
3.Отвинтить винт, снять шайбу, установить заготовку из пластичного материала и закрепить ее винтом с шайбой.
4.Смазать машинным маслом режущие кромки червячной фрезы.
5.Сосчитать числа заходов инструментального червяка zи и
червяка привода заготовки z5 (смотреть на торцы червяков).
6.Сделать штангенциркулем пять измерений высоты витка инструментального червяка, рассчитать из формулы (11.11) модуль m и округлить его до стандартного (см. табл. 11.2).
7.Сделать штангенциркулем пять измерений диаметра вершин инструментального червяка daи , рассчитать из формулы (11.10) коэффициент диаметра червяка q' и округлить его до стандартного (см. табл. 11.1).
8.Рассчитать делительный угол подъема витка червяка по формуле (11.13).
9.Установить по круговой шкале инструментальный червяк под углом для нарезания прямозубого колеса.
10.Выполнить процесс нарезания зубчатого колеса на всю ширинувращениеммаховика.
11.Снять нарезанное зубчатое колесо с установки и сосчи-
тать его число зубьев zк. Стружку заготовки собрать в емкость дляповторногоиспользования.
12.Вычертить кинематическую схему привода заготовки
(см. рис. 11.1).
13.Рассчитать числа зубьев колес привода заготовки, пере-
даточное отношение i16 каждой ступени и общее передаточное отношениесогласующейкинематическойцепипоформуле(11.6).
14.Сделать штангенциркулем измерения длины общей нор-
мали Wn , приняв zw из табл. 11.3, затем, увеличив число охватываемых зубьев на единицу, сделать измерения Wn +1. В каждом случае сделать по 5 измерений и рассчитать средние значения.
15.Рассчитать основной шаг pb по формуле (11.19), модуль
m по формуле (11.20) и округлить его до стандартного (см.
табл. 11.2).
16.Вычертить схему измерений длины общей нормали (см.
рис. 11.4).
17.Рассчитать передаточное отношение согласующей кине-
матической цепи i по формуле (11.8).
16
147
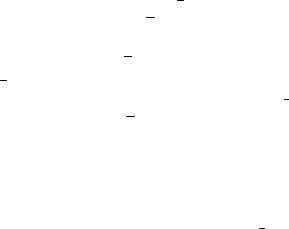
18.Рассчитать постоянную хорду sc по формуле (11.17) и
расстояние до постоянной хорды hc по формуле (11.18).
19.Установитьнавертикальной шкалештангензубомера рас-
стояние до постоянной хорды hc , сделать 5 измерений постоянной хорды sc и рассчитать среднее значение.
20.Вычертить схему измерений постоянной хорды sc и рас-
стояния до постоянной хорды hc (см. рис. 11.3). 21. Сделать выводы по следующим пунктам:
– соответствие модулей m и m , рассчитанных различными методами;
–соответствие общих передаточных отношений согласующей кинематическойцепиi16и i16 ,определенныхдвумяспособами;
–соответствие контрольных параметров Wn и sc , измеренных и рассчитанных; расхождение не должно превышать 5 %.
Вопросыкзащитеработы
1.Что такое эвольвента?
2.Какая окружность называется основной?
3.Что такое шаг зубчатого колеса?
4.Какая окружность называется делительной?
5.Опишите процесс нарезания цилиндрического зубчатого колеса червячной модульной фрезой.
6.Чем отличается инструментальный червяк (червячная фреза) от приводного червяка по форме и размерам?
7.Для обеспечения равенства каких параметров проектируется согласующая кинематическая цепь?
8.Почему для нарезания прямозубого колеса поворачивают суппортнуюголовку?
9.Как определяется передаточное отношение червячной передачи?
10.Как определяется общее передаточное отношение последовательно расположенных зубчатых колес?
11.Какустанавливаютштангенциркульприизмерениидлины общей нормали Wn?
12.Как определяют модуль при измерении длин общей нормали?
13.Что такое постоянная хорда?
148
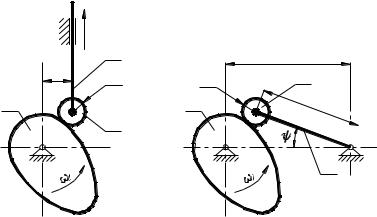
14. Какие свойства эвольвенты используют при расчете модуля по длине общей нормали?
Лабораторная работа № 12 Профилирование кулачка
Цель работы: построение профиля кулачка по заданной схеме кулачкового механизма и заданному закону движения толкателя.
Оборудование: прибор для профилирования кулачка ТММ21, бумажный круг.
12.1.Общие положения
Кулачковые механизмы дают возможность реализовать любой закон движения ведомого звена (толкателя) при равномерном движении ведущего звена (кулачка). Наибольшее распространение получили механизмы с вращающимся кулач-
ком (рис. 12.1, а, б).
|
|
S |
|
|
а) |
|
3 |
б) |
|
e |
|
rp |
rp |
А |
1 |
|
|
1 |
|
А |
|
|
||
|
2 |
|
|
|
O1 |
|
|
O1 |
|
|
|
|
а
2
l
O2
3
Рис. 12.1. Схемы кулачковых механизмов
В механизме с поступательно движущимся толкателем
(см. рис. 12.1, а) при вращении кулачка 1 толкатель 3 перемещается на величину линейного перемещения S = 0...Smax, занимая при любой угловой координате кулачка положения, задаваемые законом движения. Контакт толкателя с кулачком может осуществляться по высшей паре трения скольжения (грибовидный, плоский толкатель либо толкатель, оканчивающийся острием)
149
или для уменьшения потерь на трение — по высшей паре трения качения (ролик 2 на рис. 12.1, а, б, конструктивновыполняемый
ввиде подшипника качения).
Вмеханизме с качающимся толкателем (коромыслом)
вращение кулачка 1 дает угловое перемещение коромысла 3
= 0... max (см. рис. 12.1, б).
Исходные данныедля проектирования (синтеза) кулачкового механизма:
а) схема кулачкового механизма; б) закон движения толкателя;
в) максимальное перемещение толкателя Smax или max;
г) длина коромысла (для кулачково-коромыслового механизма);
д) максимально допустимый угол давления [ ] или минимально допустимый угол передачи [ ].
Синтез кулачкового механизма состоит из двух этапов:
а) определение основных размеров кулачка по допускаемо-
му углу давления (передачи): начального радиуса r0 и смещения e – для поступательно движущегося толкателя; начального угла0, межосевого расстояния а и начального радиуса r0 – для кулачково-коромыслового механизма;
б) профилирование, т.е. построение центрового (теоретического) и конструктивного (практического) профилей кулачка.
Цель данной работы – освоение второго этапа проектирования:построениепрофилей кулачка –профилированиекулачка.
12.2. Законы движения толкателя
Закон движения толкателя выбирают в зависимости от назначения кулачкового механизма (обеспечение заданной технологиилибоприемлемыхдинамическихнагрузок)ввидеаналитических или графических зависимостей одного из кинематических параметров (перемещения, скорости или ускорения) от времени t или угла поворота кулачка . Другие кинематические зависимости получают в результате интегрирования илидифференцированиязаданныхфункций.
Поскольку кулачковые механизмы большинства машин работают при высоких угловых скоростях кулачка, то для снижения инерционных нагрузок, действующих на звенья механизма,
150