
755
.pdf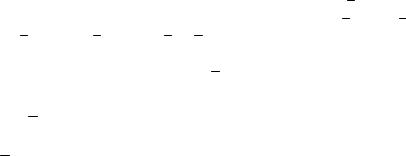
используют такой закон движения толкателя, чтобы его ускоре-
ния при работе механизма были минимальными. Поэтому при проектировании кулачковых механизмов обычно задают закон изменения ускорений, а диаграмму перемещений толкателя получают в результате двукратного интегрирования ускорений.
Безударная работа осуществляется при синусоидальном законе изменения ускорения (рис. 12.2, а). Кинематическую диаграмму можно разбить на четыре фазы, соответствующие углам поворота кулачка: у – угол удаления, на котором толкатель совершает прямой ход, например, открытие клапана двигателя внутреннего сгорания; д – угол дальнего стояния (выстой на максимальном перемещении); с – угол сближения (закрытие клапана); б – угол ближнего стояния (выстой в начальном положении). Весь цикл работы механизма соответствует одному обороту кулачка:
у д с б 360 . |
(12.1) |
Рабочий профильный угол включает первые три фазы:
1p у д с . |
(12.2) |
«Мягкий» удар соответствует следующим законам изменения ускорения: косинусоидальный закон (см. рис. 12.2, б), треугольный (рис. 12.2, в), прямоугольный (рис. 12.2, г).
12.3. Графическое интегрирование
Методика графическогоинтегрированиярассмотренана примерекосинусоидальногозакона изменения ускорения(рис. 12.3, а). Для правильного построения косинусоиды необходимо фазы удаления и сближения разбить на 6 равных частей.
Амплитудудиаграммыускорений принятьравной a =40...50 мм. Косинусоиду строят по 7 точкам с ординатами a ; 0,866a ; 0,5a ; 0; – 0,5 a ; – 0,866a ; –a . По оси абсцисс фазовые углы откладывают в масштабе (мм/град):
|
|
|
1p |
, |
(12.3) |
|
1p |
||||||
|
|
|
|
где 1p – длина отрезка на оси абсцисс, соответствующая рабочему профильному углу; рекомендуется принимать
1p = 150 мм.
151
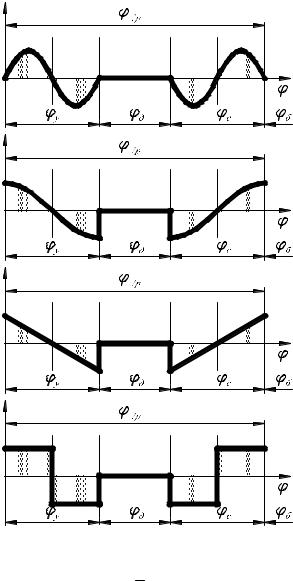
a) |
a |
б) |
a |
в) |
a |
г) |
a |
Рис. 12.2. Законы движения толкателя
Масштаб угла поворота , мм/рад:
|
|
|
|
1p |
. |
(12.4) |
|
|
|||||
|
|
1p |
||||
|
|
|
|
Слева от оси ординат откладывают отрезок интегрирования
Н1 = 25 мм.
152
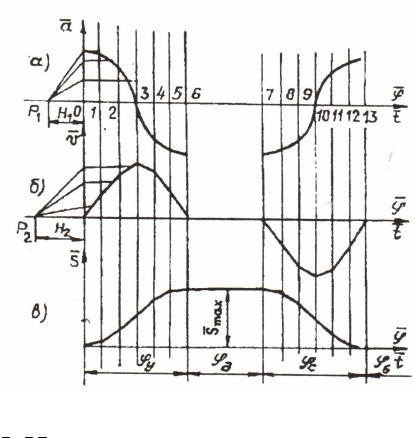
Рис. 12.3. Графическое интегрирование
Для выполнения графического интегрирования диаграмму a a заменяют ступенчатой таким образом, чтобы на каждом участке фигуры, образованные диаграммой, осью абсцисс и линиями, параллельными оси ординат, заменялись равновеликими прямоугольниками. Ординату прямоугольника назначают так,чтобыплощадки,расположенныевышеинижегоризонтали, проведеннойотординаты,были примерноодинаковойплощади.
СоединивполюсинтегрированияР1 сординатамипрямоугольников, получают лучи, которые параллельно переносят на диаграмму скоростей. На первом участке из начала координат проводят отрезок, параллельный первому лучу (рис. 12.3, б). На втором участке из конца первого отрезка проводят второй луч и т.д. Полученная ломаная линия представляет приближенно диаграмму
153
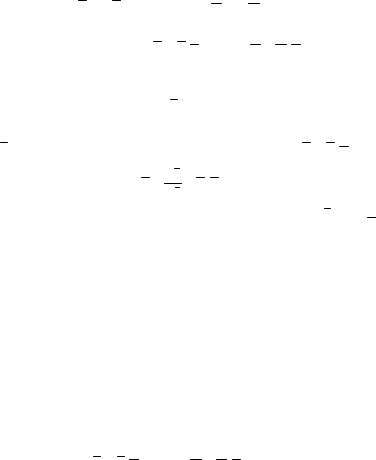
dS |
|
dS |
|
|
либо |
d |
|
|
d |
|
|
|
. |
|||||||
|
|
|||||||||||||||||||
|
|
|
|
|
|
|
||||||||||||||
d |
|
|
|
d |
|
|
|
|
|
d |
|
|
|
d |
|
|
|
|
|
Построение диаграммы S S либо выполняют аналогично. Для этого откладывают отрезок интегрирования Н2 (рис. 12.3, б). Масштаб диаграммы перемещений в мм/мм:
S |
|
Smax |
, |
(12.5) |
|
||||
|
|
Smax |
|
где Smax – максимальная ордината на диаграмме S S , мм.
Диаграмма скоростей v ds v на рис. 12.3, б одновре-
dt
менноявляетсядиаграммойаналоговскоростей |
|
|
|
ds |
|
|
|
|
|
|
. |
|||
v |
v |
|
||||||||||||
|
|
|
|
|||||||||||
|
|
|
q |
|
d |
|
|
|
|
q |
|
|
|
|
Масштаб последней диаграммы в мм/мм: |
|
|
|
|
|
|
||||||||
|
|
|
|
|
|
|
|
|
|
|
|
|||
vq |
s |
H2 . |
|
|
|
|
|
|
(12.6) |
|||||
|
|
|
|
|
|
|
||||||||
|
|
|
|
|
|
|
|
|
|
|
|
|
|
Для того, чтобы получить масштаб S = 1 мм/мм (М 1:1), задают vq = 1 мм/мм и из формулы (12.6) находят необходимый отрезок интегрирования Н2, мм:
H2 |
|
vq |
. |
(12.7) |
|
s |
|||||
|
|
|
|
Аналогичную зависимость можно записать для углового перемещения коромысла: при = 1 мм/град и d / d = 1 мм/град
Н2 = .
По диаграмме S S либо измеряют величины перемещений и с учетом масштаба определяют их модули (S, мм; , град) через 10…25° в соответствии с заданными фазовыми углами.
12.4. Профилирование кулачка
Профилирование выполняют по методу обращения движения, когда системе кулачок—толкатель задают вращениесугловойскоростьюкулачка 1,нонаправленнойвпротивопо-
ложную сторону. При этом кулачок остановится, а толкатель вместе со стойкой будет совершать вращательное движение со скоростью – 1.
154
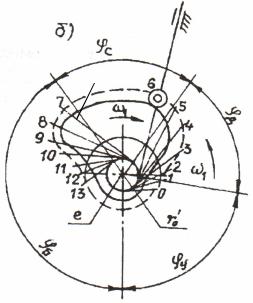
Профилирование кулачкового механизма с поступатель-
но движущимся толкателем выполняют в следующей последовательности.
Вмасштабе S вычерчивают окружность радиусами r0 (начальный радиус) и e (смещение, рис. 12.4). Окружность радиуса e делят на части в соответствии с заданными фазовыми углами
внаправлении против вращения кулачка. Дуги окружностей на
фазовых углах у и с делят на равные части в соответствии с кинематическими диаграммами (см. рис. 12.3).
Вточках деления проводят касательные. На касательных от
окружности r0 откладывают отрезки S1, S2 и т.д. и таким образом находят точки 1, 2 и т.д. центрового профиля (описываемого по методу обращения движения центром ролика), которые объединяют плавными кривыми и дугами окружностей. На рис. 12.4
показан отрезок S7. Конструктивный профиль располагают внутри центрового эквидистантно ему на расстоянии понорма-
ли, равном радиусу ролика rp. Для его вычерчивания проводят дугиокружностейрадиусомrp сцентраминацентровомпрофиле. Вычерчивая плавную огибающуюдугокружностей, получают конструктивныйпрофиль.
Профилирование кулачка при вращающемся толкателе
выполняют следующим образом.Описываютокружность радиусом а (межосевоерасстояние), которую делят на части в соответствии с заданными фазовыми углами
(рис. 12.5).
Дуги окружности на фазовых углах y и c делят на равные части. Из точек деления проводят лучи длиной l
S7
Рис. 12.4. Профилирование кулачка с поступательно движущимся толкателем
155
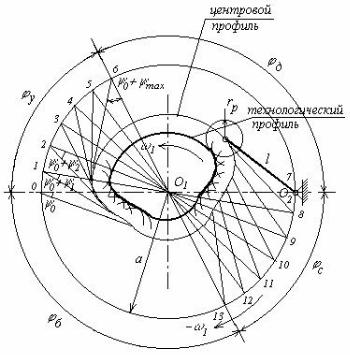
(длина коромысла) подуглами крадиусным прямым 0, 0 + 1,0 + 2 и т.д. Концы лучей соединяют плавной кривой, получая центровой профилькулачка. Технологический профиль кулачка расположен внутри центрового, эквидистантно ему на расстоянииrр.
Рис. 12.5. Профилирование кулачка с коромыслом
12.5. Описание прибора ТММ-21
При известном законе движения толкателя профиль кулачка можно вычертить с помощью прибора, схема которого представлена на рис. 12.6. На основании 1 установлен диск 2, имеющий деления через 1°. Диск может вращаться вокруг своей оси при помощи фрикционногомеханизма, управляемогорукояткой 3. Угол поворота диска отсчитывают по шкале диска 2.
На верхнюю плоскость диска 2 устанавливают круг из чертежной бумаги, служащий заготовкой кулачка. В правой части прибораустановленкорпус4,управляемыйрукояткой5,который
156
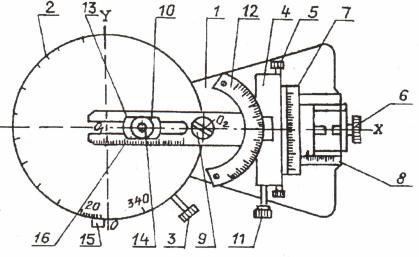
может перемещаться в направлении O1Y и от механизма, управляемого рукояткой 6, в направлении О1Х.
Рис. 12.6. Схема прибора ТММ-21
Перемещение корпуса 4 в направлении оси О1Y отсчитывают пошкале7,внаправлении осиО1Х–пошкале8.На оси9корпуса 4 установлена направляющая 10, представляющая собой толкатель. Вращение направляющей 10 осуществляют рукояткой 11, угол поворота направляющей можно определить по делениям секторной шкалы 12, установленной на верхней подвижной каретке. В пазу направляющей 10 может перемещаться ползун 13; величину перемещения отсчитывают по шкале, нанесенной на направляющей.
Вползуне13укреплены игла 14и приспособлениедля вычерчиванияокружностиролика(радиусроликапостоянный,равный 10 мм). При вычерчивании профиля кулачка для механизма с поступательно движущимся толкателем работу на приборе производят следующим образом: рукояткой 11 шкала 12 устанавливается на 0. По шкале 7 рукояткой 5 корпус 4 вместе с толкателем (направляющей 10) смещают на величину заданного эксцентриситета е.
Рукояткой 6 корпус 4 перемещается вправо до отсчета 12 по шкале 8, при этом отсчет 0 по шкале направляющей 10 будет
157
находиться точно над центром диска 2. После этого для каждого значения угла поворота кулачка ползуном 13 устанавливают величину перемещения толкателя S по шкале направляющей 10. Величину перемещения S для каждого угла поворота кулачка предварительно рассчитывают. Углы вводят поворотом диска 2, отсчет угла поворота производят по шкале 15 диска 2.
Для каждого угла и соответствующего ему значения S илис помощью иглы 14 и рукоятки 15 на заготовке диска 2 вычерчивают окружность радиусом rр (ролика). Геометрическое место центров роликов будет являться теоретическим профилем кулачка; внутренняя огибающая к окружностям роликов образует конструктивный (технологический) профиль кулачка.
При вычерчивании профиля кулачка для механизма с качающимся толкателем по шкале 7 рукояткой 5 корпус 4 устанавливают на нуль. По шкале 8 рукояткой 6 устанавливают межосевое расстояние О1О2 в соответствии с заданием. По шкале 16 направляющей 10 ползун 13 приводят в такое положение, чтобы размер АО2 был равен заданной длине толкателя (АО2 = l).
Диск 2 последовательно устанавливают на исходные углы пошкале, а направляющую(толкатель) 10—на углы пошкале 12. В каждом положении на заготовке диска вычерчивают окружность ролика. Геометрическое место центров роликов будет центровым профилем кулачка, внутренняя огибающая к окружностям роликов дает конструктивный профиль кулачка.
12.6. Аналитическое определение профиля кулачка
Для изготовления кулачка необходимо знать координаты отдельных точек его профиля. При профилировании кулачкового механизма задают полярную ось, от которой отсчитывают углыi, соответствующие радиусам-векторам ri, в направлении против вращения кулачка 1 (рис. 12.7).
Во внецентренном кулачковом механизме (e 0) с поступательно движущимся толкателем углы профиля кулачка i не равны соответствующим углам поворота кулачка i. В начале фазы удаления контакт кулачка и толкателя происходит в точке а.
Для произвольной точки кулачка b радиус-вектор ri = Ob составляет с радиусом-вектором точки a r0 = Оа угол i. При повороте кулачка в направлении 1 до контакта точки b с толка-
158
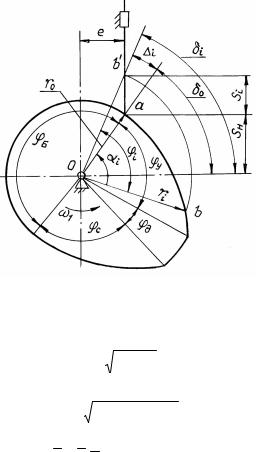
телем она займет положение b'. Точка b' находится на пересечениидугиокружностирадиусаri страекториейдвижениятолкателя (на рис. 12.7 — прямая ab'). Для того, чтобы точка контакта переместилась из точки а профиля в точку b, необходимо кулачок повернуть на угол i, отличающийся от угла i на величинуi = i – 0; углы профиля
i |
i i 0 ; |
(12.8) |
i |
arccos e/ri ; |
(12.9) |
0 arccos e/r0 . |
(12.10) |
Рис. 12.7. Схема к определению радиусов-векторов кулачкового механизма с поступательно движущимся толкателем
Координата нижнегоположения толкателя
S |
0 |
|
r2 |
e2 . |
(12.11) |
|
|
0 |
|
|
Текущий радиус-вектор
r |
e2 (S |
0 |
S |
)2 . |
(12.12) |
i |
|
i |
|
|
Величины Si, соответствующие углам поворота кулачка i, берут из диаграммы S S или рассчитывают по аналити-
159
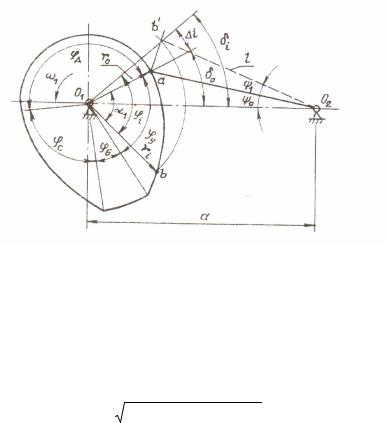
ческой зависимости S S . Последовательно рассчитывают координату S0, текущие радиусы-векторы ri, углы i, 0 и углы профиля i. Табличная функция ri r i определяет центровой профилькулачка.
Вцентральном (е=0)кулачковом механизмеспоступательно движущимся толкателем профильные i и фазовые i углы со-
впадают, так как i = i – 0 = 0, ri = r0 + Si.
При вращающемся толкателе (рис. 12.8) теоретические выкладкианалогичны.
Рис. 12.8. Схема к определению радиусов-векторов кулачково-коромыслового механизма
Точку b' находят на пересечении дуг радиусов ri и l (длина коромысла).Дляпрофилированиякулачкавначалепозаданному закону движения рассчитывают углы поворота коромысла i в функции угла поворота кулачка. Затем для ряда последовательных значений i вычисляют радиус-вектор (из O1b'O2 потеореме косинусов):
r |
a2 l2 2alcos |
0 |
|
, |
(12.13) |
i |
|
i |
|
|
где а — межосевое расстояние; 0 – начальный угол. По теореме синусов находят углы:
i |
arcsin lsin iri ; |
(12.14) |
0 |
arcsin lsin 0r0 . |
(12.15) |
160