
книги / Надежность электрических машин
..pdf131
2. Заранее принимается решение об усечении (ограничении) последовательного анализа. При этом методика предполагает одновременное испытание всех образцов изделий с фиксацией отказов в моменты их возникновения. Параметры усечения rусеч и tусеч определяются по соответствующим таблицам
ГОСТ 27.410–87 «Методы и планы статистического контроля показателей надёжности по альтернативному признаку».
Если график последовательных испытаний r = f (t) достига-
ет отрезка АВ (см. рис. 15), то выносится решение о несоответствии надёжности партии техническим требованиям; если достигает отрезка ВС, то партия принимается.
132
VIII. УСКОРЕННЫЕ ИСПЫТАНИЯ ЭМ НА НАДЁЖНОСТЬ
8.1. Планирование исследований по определению коэффициента ускорения
Срок службы современных ЭМ составляет иногда десятки тысяч часов. Все испытания на надёжность, как определительные, так и контрольные, весьма продолжительны и дорогостоящи. Проблему сокращения длительности испытаний можно решить проведением ускоренных испытаний (УИ) на надёжность. УИ ЭМ проводятся в специальных условиях, которые характеризуются повышенным уровнем некоторых воздействующих факторов. Эти факторы называются факторами форсирования.
Кним относятся:
–повышенная температура;
–повышенная вибрация, частота вращения, частота пусков;
–повышенная влажность;
–удельное нажатие и плотность тока под щёткой;
–запылённость и др.
Ускоренным испытаниям предшествуют исследования по определению Kу. Как уже говорилось, коэффициент ускорения – это отношение времени работы машины в нормальных условиях ко времени работы в форсированных режимах при одинаковой вероятности безотказной работы. Из определения следует не-
обходимость соблюдения адекватности законов распределения в нормальных и форсированных режимах. Это означает, что при форсированных режимах не должна нарушаться физика процессов старения и износа материалов и конструкции ЭМ.
При УИ на надёжность количество факторов форсирования обычно варьируется от двух до четырёх. Для получения функциональных зависимостей коэффициента ускорения от факторов
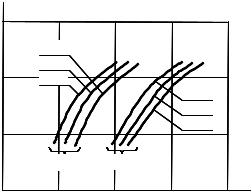
133
форсирования необходимо реализовать специальные планы, которые составлены согласно математической теории планирования экспериментов. Функциональные зависимости записываются
вполиномиальном виде:
–для планов первого порядка
y = b0 + ∑bi xi +∑bij xi xj , |
(86) |
– для планов второго порядка |
|
y = b0 +∑bi xi + ∑bij xi xj +∑bij xi2 , |
(87) |
где bi – коэффициенты искомого полинома; xi – факторные независимые переменные; y – коэффициент ускорения.
Зависимость коэффициентов ускорения от факторов форсирования Kу = f(xi) находится после математической обработки. Графическое изображение типичной зависимости Kу = f(xi) (для ДПТ от 1 до 10 кВт) показано на рис. 16.
K y
3600
4000
20 4260
4260
4000
3600
10
2A=130 2A=80
Θ,oС
0 |
50 |
100 |
150 |
Рис. 16. Зависимость Kу от факторов форсирования: температуры; вибрации; частоты вращения
Коэффициент ускорения является функцией трёх факторов: температуры Θ , частоты вращения и вибрации.

134
На рис. 16 показаны два уровня вибрации с двойной амплитудой 2А, равной 80 и 130 мкм, и три уровня частоты вращения: 3600, 4000, 4260 об/мин. Аналитическое выражение имеет вид
y = 0,0575 + 0,0112x1 + 0,0225x2 + 0,002x3, |
(88) |
где x1 – температура; x2 – вибрация; x3 – частота вращения; y – коэффициент ускорения (все величины переменных факторов xi переведены в относительные единицы).
Для проведения исследований по определению Kу должны быть решены следующие задачи:
1.Разбиение исследуемой системы на отдельные подсистемы.
2.Установление факторов, воздействующих на отдельные узлы ЭМ, и определение совокупности факторов, которые должны быть воспроизведены при УИ.
3.Установление предельных значений основных воздействующих факторов.
4.Выбор контрольных параметров и установление критериев работоспособности и отказа.
5.Разработка плана испытаний по определению Kу.
6.Реализация заданных уровней форсирования в соответствии с матрицей планирования эксперимента.
7.Обработка результатов.
Проанализируем приведённые положения на примере МПТ:
1.МПТ как систему можно разбить на отдельные подсистемы: подшипниковый узел, коллекторно-щёточный узел, обмотки статора и ротора.
2.В общем случае в зависимости от характера воздействия факторы можно разбить на три группы:
W – случайные факторы, к которым можно отнести отклонение геометрии магнитной системы, расстройство коммуникации, всплески токов, эксцентриситет коллектора, эллиптичность коллектора, ослабление коллектора, отклонение в технологии изготовления коллекторов и щёток, перекос щёток в щёткодержателях и др.;
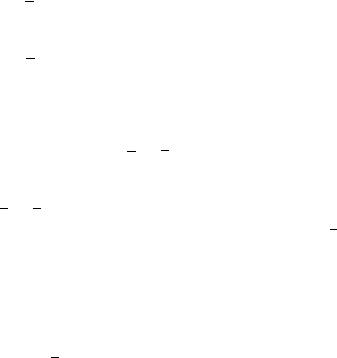
135
С – постоянные, не изменяемые в процессе исследования факторы, например конструкция коллекторного узла, применяемые материалы, марка щёток, конструкция щёткодержателя;
Х– переменные факторы, изменяемые и контролируемые
впроцессе проведения ускоренных испытаний: температура, влажность, кислотность и запылённость, вибрация, давление на щётку, плотность тока под щёткой, частота пусков, частота вращения, величина нагрузки, время непрерывной работы.
Факторы групп W и C в основном определяются конструкцией, технологией, настройкой машины, а также её эксплуатацией. При реализации планов теории эксперимента факторы групп
Wи C автоматически учитываются в уравнениях регрессии.
3.Основные воздействующие факторы группы Х могут изменяться в достаточно широких пределах. Для получения наи-
больших Kу режимы испытания должны быть жёсткими, но бесконечно увеличивать форсирование нельзя, так как нарушается физическая картина процессов старения. Опыт создания методик
УИ показывает, что Kу не должен превышать 12–15 (в отдель-
ных случаях 20). Выбор интервалов варьирования параметров
группы X является сложной задачей и основывается на данных ТУ, лабораторных испытаниях, анализе всего объекта в целом. После проведения предварительного эксперимента интервалы варьирования уточняются. Ориентировочно предельные значения для МПТ следующие: температура коллектора – до 150 °С; частота вращения – до 1,5 номинальной; влажность окружающего воздуха – до 98 %; двойная амплитуда вибрации – не более тройной от номинала; плотность тока под щёткой – до 12 А/см2.
4. Выбор контрольных параметров и установление критериев отказа – наиболее важные моменты, так как единого нормативного критерия, характеризующего работу узла, практически нет.
Например, критериями работоспособности коллекторного узла являются: биение (статическое и динамическое), искрение, величина и скорость износа щёток, температура коллектора, ширина безыскровой зоны, переходное сопротивление щёточного контакта, па-
136
дение напряжения в щётках; к критериям отказа относятся: превышение допустимого уровня искрения, скорость износа щёток или величина износа щёток, износ коллектора выше допустимого, существенное превышение допустимой температуры коллектора.
5. План испытаний по определению коэффициентов ускорения разрабатывают следующим образом. Функциональные зависимости, связывающие Kу и факторы форсирования, находят с помощью методов теории планирования эксперимента. При этом используются: планы первого порядка– полный факторный эксперимент (ПФЭ), дробный факторный эксперимент (ДФЭ) и планы второго порядка– рототабельное центральное композиционное планирование (РЦКП), аналогичное ортогональное планирование (ОЦКП). Планы первого порядка используются для описания линейных объектов (или близких к ним), планы второго порядка – для описания нелинейных объектов. Планы РЦКП и ОЦКП требуют использования вычислительной техники для расчёта коэффициентов полинома и проверки гипотез адекватности полученной математической модели искомой функции из-за сложных расчётных алгоритмов и больших временных затрат. В данном пособии методы планирования нерассматриваются.
Перед испытаниями должны быть осуществлены следующие процедуры: выбор параметра оптимизации (выходного параметра); выбор факторов форсирования (они не должны быть закоррелированы); выбор центра плана, уровней и интервалов варьирования факторов; выбор схемы планирования.
Задачи, поставленные выше в пунктах 6 и 7, решаются в соответствии с методами теории планирования экспериментов.
8.2. Краткая характеристика испытательного оборудования
При УИ значение Kу не должно превышать 20 (исключение составляет изоляция обмоток некоторых типов машин с большими значениями Kу), чтобы сохранить физическую сущность старения испытываемой машины в целом. Аппаратура, применяемая при испытаниях, должна соответствовать стандарту на общие методы испытаний (ГОСТ 11828–86).
137
Планирование испытаний ведётся с учётом закона распределения отказов, известного риска заказчика, ресурса двигателя и вероятности безотказной работы за ресурс.
Цель планирования УИ на надёжность – оптимальный выбор объёма выборки, времени испытаний и режима испытаний (испытательной температуры обмоток и подшипников, вибраций
инагрузки на подшипники) по рассчитанным коэффициентам ускорения.
Испытательное оборудование должно обеспечить необходимую частоту пусков, уровень вибрации, температуру отдельных узлов и нагрузку на подшипники. Испытания проводятся на специальных испытательных стендах.
Подготовка двигателей к УИ включает в себя: установку температурных индикаторов в лобовые части обмотки статора (ОС)
ина наружные обоймы подшипников для контроля температуры во время испытаний, закладку термостойкой смазки, установку регулируемого небаланса для обеспечения требуемого уровня вибрации, а также проведение приработочных испытаний в течение 100 ч при номинальном значении воздействующих факторов. Вышедшие из строя во время приработочных испытаний двигатели заменяются новыми, а отказ во время приработочных испытаний при обработке результатов испытаний не учитывается.
Иногда проведение испытаний предусматривается в два этапа. Первоначально двигатель подвергается форсированным воздействиям коммутационных перенапряжений за счёт увеличения частоты пусков, температуры, вибрации и механической нагрузки на подшипник в течение времени, эквивалентного одному году нормальной работы. Затем проводится увлажнение обмоток в камере влажности с последующим воздействием росы. Камера влажности, в которую помещаются двигатели после каждого цикла испытаний, должна обеспечивать автоматическое поддер-
жание влажности воздуха до 100 % при температуре 20–40 °С и достаточном для испытаний рабочем объёме. В камере влажности производится увлажнение обмоток в два этапа, для чего
138
двигатели сначала в течение 16 ч держат в камере при температуре + 30 °С и относительной влажности 94–98 %, а затем температура снижается до появления росы. В этих условиях двигатели выдерживаются в камере влажности ещё в течение определённого времени (обычно 8–10 ч).
Заданная частота пусков (реверсов) двигателя обеспечивается с помощью мультивибратора, программного устройства или реле времени. Испытательная температура может быть достигнута несколькими путями в зависимости от режима нагрузки испытуемой машины (ИМ). При непосредственной нагрузке ЭМ преимуществами обладает метод взаимной нагрузки, поскольку он позволяет одновременно испытывать две машины. При этом испытательная температура может достигаться за счёт выбора частоты пусков (реверсов), если это не противоречит предыдущему требованию. Если частота пусков (реверсов) не позволяет обеспечить заданную температуру, то воздействуют на схему вентиляции путём увеличения её гидравлического сопротивления. Расход охлаждающего агента при этом уменьшается, а температура при неизменных потерях возрастает.
Для машин со степенью защиты IP44 и выше уменьшают сечения отверстий в кожухе вентилятора, а у машин со степенью защиты IP23 уменьшают сечения отверстий для входа и выхода охлаждающего агента в корпусе и подшипниковых щитах.
Для некоторых машин могут использоваться схемы искусственной нагрузки, аналогичные приведённой на рис. 17. Испытание ведётся в режиме холостого хода (ХХ), пуск осуществляется при схеме соединения ОС в звезду.
После окончания пуска начало обмотки одной из фаз через регулируемое сопротивление нагрузки Rн соединяется с нулевой точкой. Регулированием величины нагрузочного сопротивления Rн добиваются требуемого в обмотках тока. Электрическая схема, показанная на рис. 17, б, сложнее схемы на рис. 17, а, но в ней отпадает необходимость в нагрузочных устройствах. Сопротивление нагрузки
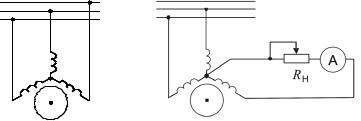
|
|
139 |
|
|
Rн = |
Uл |
|
− Rф, |
(89) |
2 I |
|
|||
|
н |
|
где Uл – линейное напряжение, В; Iн – номинальный фазный ток, А; Rф – активное сопротивление обмотки фазы, Ом.
а |
б |
Рис. 17. Электрические схемы испытаний двигателя:
а – в режиме холостого хода; б – с искусственной нагрузкой
Схемы искусственной нагрузки желательно применять при малом числе пусков. Если нельзя обеспечить требуемую температуру путём регулирования Rн, то изменяют схему вентиляции, как и в предыдущем случае.
Для машин, работающих в повторно-кратковременных режимах (режимах S3 – S5 по ГОСТ 183–74), добиться требуемого увеличения значения температуры обмоток, в сравнении с номинальным, можно при работе в режиме ХХ за счёт увеличения числа пусков (реверсов).
Получение заданной вибрации может быть осуществлено двумя путями: искусственным дисбалансом вращающихся частей ЭМ или применением специальных вибростендов. Первый способ применяется для машин средней и большой мощности. Если испытание проводится в режиме нагрузки, то дополнительный груз устанавливается на шкив, соединительную муфту и аналогичные им вращающиеся детали. Выбором груза добиваются требуемого класса вибрации. Если испытание проводится в режиме ХХ, то дополнительный груз устанавливается на внеш-
140
нем вентиляторе, а в случае его отсутствия – на роторе или на шкиве, с помощью которого осуществляется заданная нагрузка на подшипник. Применение искусственного дисбаланса позволяет получить заданный уровень вибрации, но изменяет её частотный спектр, поскольку указанный уровень будет обеспечиваться за счёт составляющей с частотой f = n /60, где n – рабочая частота вращения, об/мин. Кроме того, эта вибрация однокомпонентная, так как она содержит лишь радиальную составляющую.
Для машины небольшой мощности требуемый уровень вибрации устанавливается с помощью вибростенда, на котором можно одновременно разместить несколько машин. Под вибростендом понимается комплекс оборудования, включающий в себя возбудитель колебаний, пульт управления с контрольно-измерительной аппаратурой, устройства для регулирования или автоматического поддержания режима колебаний. По типу колебаний вибростенды бывают: механические (до 150–300 Гц), магнитомеханические, пьезострикционные, гидравлические (до 150–300 Гц), электрогидравлические, магнитогидравлические, магнитогидродинамические.
Применение вибростендов позволяет получить трёхкомпонентную вибрацию заданного частотного спектра. Однако на практике, как правило, ограничиваются однокомпонентной вибрацией. По виброграмме испытываемой в нормальных условиях машины определяют частоту, вносящую наибольший вклад в общий уровень вибрации, и усиливают при форсировании вибрации именно её. Указанные обстоятельства позволяют при использовании вибростенда добиться лучшего соответствия нормального и форсированного режимов.
Для машин небольшой мощности класс вибрации обычно не превышает 2,8, а при форсировании – 7,0. Последняя цифра соответствует уровню вибрации 103 дБ и виброускорению 42 м/с2. Уровень частоты вибрации доходит до 1–2 кГц. Анализ приведённых в литературе данных позволяет сделать вывод о применимости для УИ электродинамических вибростендов. Механические и гидравлические вибростенды обеспечивают заданный уровень вибрации, но имеют небольшую максимальную частоту (150–300 Гц).