
книги / Надежность электрических машин
..pdf31 |
|
|
Тип генератора |
ЕС |
ЕСС |
Количество исследованных машин |
520 |
230 |
Общее количество отказов |
329 |
89 |
Распределение отказов: |
|
|
обмотка ротора |
26 |
8 |
обмотка статора |
22 |
9 |
блок регулирования напряжения |
188 |
50 |
подшипниковый узел |
21 |
7 |
контактно-щёточный узел |
72 |
15 |
Вероятность безотказной работы генераторов |
ЕС и ЕСС |
в период 0–4000 ч соответствует распределению |
Вейбулла. |
В период 4000–12 000 ч распределение отказов является экспоненциальным. Основными причинами отказов являются: нарушение технологии изготовления, низкокачественная настройка и наладка систем регулирования напряжения, неправильная эксплуатация, а также конструктивные недоделки.
Статистика располагает сведениями о надёжности и ремонтопригодности некоторых типов синхронных генераторов ука-
занной мощности: |
|
|
|
|
Тип генератора |
ЕС-52-4 |
ДГС |
ПС-93-4 |
ЕСС |
Средняя наработка на отказ, ч |
3060 |
4660 |
4800 |
5100 |
Среднее время ремонта, ч |
12,5 |
21,0 |
33,5 |
10,0 |
Проведём анализ повреждаемости основных узлов крупных синхронных машин. Отказ СМ из-за повреждения обмотки статора, как правило, происходит в результате пробоя изоляции обмотки. Участки пониженной электрической прочности могут появляться в изоляции обмотки вследствие дефектов изготовления, повреждений при монтаже обмотки или в процессе эксплуатации, включая ремонтные работы.
Процесс разрушения изоляции ускоряют концентрации нагрузок: повышенные механические усилия при переходных процессах, перегрузки по току, перенапряжения, вибрации и др.
32
В этой ситуации наличие участков с пониженной электрической прочностью и приводит к повреждению обмотки, ибо амплитуды практически возможных перенапряжений недостаточны для пробоя доброкачественной изоляции.
При изготовлении обмотки возможно попадание на её поверхность ферромагнитных частиц, вибрация которых в магнитном поле приводит к постепенному разрушению изоляции.
Недостаточно надёжное крепление лобовых частей обмотки создаёт условия для повреждения изоляции преимущественно у выхода стержней из пазов. Со временем происходит опускание корзинки лобовых частей обмотки, в связи с чем появляются дополнительные напряжения, а лобовые части становятся более подверженными вибрациям и ударам под действием внезапных электродинамических усилий (короткие замыкания и несинхронные включения генераторов, пуски и реверсы двигателей). Серьёзной опасности изоляция обмотки подвергается также при тепловых перегрузках, вызванных причинами местного характера. Так, при разрушении изоляции листов и местном замыкании сегментов активных стальных листов температура в области замыкания достигает 200–300 °С. Повреждению изоляции обмотки статора способствует также проникновение в статор машины воды и масла.
Причиной повреждения активной стали является в основном ослабление её запрессовки. Прессовка стали должна производиться примерно через каждые 0,5 м, причём давление прессовки увеличивается с 80–100 до 170 Н/см2. При меньших давлениях не обеспечивается необходимая плотность прессовки, при больших возникает опасность повреждения лаковой пленки под вентиляционными распорками, где местные давления достигают 1000–1200 Н/см2.
Механические повреждения роторов происходят несколько реже, чем повреждения неподвижных частей машин, но приводят ктяжёлым авариям. Такие аварии характерны для турбогенераторов, роторыкоторыхобладаютбольшимзапасомкинетическойэнергии.
Относительно редкие, но тяжёлые аварии вызываются разрушением роторных валов. Причиной аварии может быть заклинивание ротора при разрыве бандажа, распространение трещин
33
от зубцов в глубину вала, а также температурные напряжения
втеле ротора, вызванные несимметричным распределением тепловых потоков в плоскости поперечного сечения. Например, разность температур поверхности большого зуба и внутренней области ротора у нейтральной оси в турбогенераторах с косвенным охлаждением достигает 90–100 °С. При этом напряжение разрыва, направленное вдоль оси ротора, может быть величиной порядка 16 000–18 000 Н/см2.
Повреждение обмотки ротора из-за её перемещения при изменениях температуры является одной из основных причин аварий у турбогенераторов с косвенным охлаждением. Применение непосредственного охлаждения обмоток ротора из легированной (с присадкой серебра) меди позволяет существенно уменьшить температурные деформации обмотки: если для чистой меди марки М1 предел текучести составляет 2000–3000 Н/см2, то для ле-
гированной – 15 000–20 000 Н/см2.
До 30–40 % отказов роторов вызывается повреждениями и не-
исправностями токопроводов и токосъёмных узлов. Внутренние токопроводы крупных турбогенераторов обладают высокой надёжностью, однако отмечались случаи нарушения изоляции токоведущих болтов, главным образом вблизи контактных колец, обусловленные дефектами изготовления или сборки. Значительно чаще наблюдаются повреждения внешних токопроводов турбогенераторов малой мощности, вызванные в основном усталостным изломом токоведущих пластин около крепления к контактному кольцу или истиранием изоляции на изгибах токопровода. Сравнительно часто
вявнополюсных машинах, в частности гидрогенераторах, происходят разрывы токопровода или междуполюсных соединений, а также перегрев и расплавление паек междуполюсных соединений при длительных форсировках возбуждения.
Распространённой неисправностью является снижение сопро-
тивления изоляции цепи ротора из-за загрязнения токопровода маслом и угольной пылью. Снижение сопротивления изоляции может произойти также вследствие загрязнения самой обмотки.
34
Чаще всего повреждения подшипников и подпятников со-
провождаются выплавлением баббита, повреждением вкладышей и цапф подшипниковыми токами и вытеканием масла. Выплавление баббита обычно происходит в результате нарушения работы системы маслоснабжения. При быстрой остановке агрегата повреждения цапф оказываются незначительными, так как расплавленный баббит играет роль смазки. Повреждённые вкладыши подлежат замене или перезаливке. Возникновение подшипниковых токов типично для крупных электрических машин. Весьма значительные токи протекают через подшипники при замыкании цепи возбуждения на корпус и наличии заземления во внешней цепи ротора. В этом случае повреждения шеек вала и вкладышей подшипников могут быть весьма серьёзными. Однако даже небольшие подшипниковые токи при длительном протекании приводят к повреждению вкладышей и шеек вала.
Весьма ответственным узлом гидрогенераторов является подпятник. Повреждения подпятников обусловливают существенный процент отказов электрических машин этого типа. Наиболее характерными повреждениями подпятников являются износ, задиры и расплавление баббитового слоя на поверхности сегментов, а также повреждения от подшипниковых токов. Повышенный износ может быть обусловлен чрезмерной удельной нагрузкой на определённые участки поверхности сегментов, вызванной их температурной деформацией или иными причинами.
Повышенная вибрация электрических машин свидетельствует оналичии недостатков конструкции, дефектов изготовления
исборки, а также о возникновении повреждений. Вместе с тем сама вибрация является источником серьёзных повреждений и аварий.
Врезультате повышенной вибрации происходит ослабление прессовки активной стали, нарушение плотности соединений, разрушение сварных швов и деталей вследствие усталости материала
иконтактной коррозии, снижение газоплотности, ускоренный износ изоляции, нарушение герметичности в системах водо- и маслоснабжения, повышенные потери и нагрев подшипников, расстройствоработыи износ контактных колец и щёточного аппарата и т. д.
35
Работа с повышенной вибрацией вредна не только для машины и её фундамента, но и для окружающих машин, контрольноизмерительных приборов и обслуживающего персонала. Действующие стандарты определяют следующие допустимые значения амплитуды вибрации: для турбогенераторов – не более 40 мкм, для синхронных компенсаторов – не более 80 мкм, для гидрогенераторов – не более 100–180 мкм в зависимости от частоты вращения. Однако регламентируется при этом только вибрация подшипников.
Отказы машин постоянного тока. На предприятиях, электро-
станциях, в судовых установках и на многих других объектах общего и специального назначения в эксплуатации находится большое количество электрических машин постоянного тока (МПТ) разных мощностей, напряжений и скоростей вращения, используемых для различных целей. В зависимости от назначения и характера установок на указанных объектах одни электрические машины в них работают генераторами, другие двигателями. Надёжная работа машин оказывает существенное влияние на снижение эксплуатационных расходов и сокращение вынужденных простоев производственных механизмов и разных устройств.
Надёжная работа машин постоянного тока в период их эксплуатации определяется конструкционной надёжностью и условиями эксплуатации. Анализ причин отказов МПТ общепромышленного и специального назначения на предприятиях и различных объектах показывает, что большинство этих отказов происходит по вине обслуживающего персонала, который не всегда обеспечивает необходимый уход за машинами или же качественное выполнение текущего ремонта.
Выше отмечалось, что наибольшая доля отказов в этих машинах приходится на коллекторно-щёточный и подшипниковый узлы. Согласно эксплуатационной статистике в среднем около 25 % отказов машин происходит из-за неисправности коллекторов. В некоторых случаях (например, на транспорте) эта цифра достигает 44–66 %. В тяговых двигателях электровозов одной из серьёзных причин отказов является возникновение кругового огня. Доля отказов коллекторов из-закругового огнясоставляет в среднем 70 %.
36
Исследование ряда двигателей постоянного тока прокатных станов показало следующее распределение отказов по узлам: коллекторный узел – 56 %, механические повреждения всех узлов – 34 %, обмотка якоря и полюсов – 10 %.
Анализ статистических данных об отказах тяговых электродвигателей постоянного тока большегрузных автомобилей ДК-717А показал, что наименее надёжными элементами являются обмотка якоря и коллекторно-щёточный узел. Доля отказов электродвигателей из-за неисправности коллекторно-щёточного узла колеблется от 21,6 % (по предприятиям Минчермета) до 37,8 % (по предприятиям Минудобрений) и в среднем по всем отраслям составляет 26,5 %; из-за неисправности обмотки якоря – от 19,6 % (Минцветмет) до 42 % (Минуглепром) и в среднем – 27,7 %.
Закон распределения отказов тяговых электродвигателей ДК-717АсоответствуетсуперпозициидвухзаконовВейбуллассоот- ветствующими весовыми коэффициентами. Усреднённая зависимость интенсивности отказов электродвигателей λ (1/тыс. км) от пробега τ (тыс. км) транспортных средств показала, что от 25 до 75 тыс. км пробега интенсивность отказов двигателей, обмоток якорей, коллекторно-щёточныхимеханическихузловоказываетсяпрак- тическипостоянной. Длямеханических узловинтенсивностьотказов от 0 до 100 тыс. км пробега не превышает 0,1. Для коллекторнощёточных узлов и обмоток якоря интенсивность отказов (различаясь незначительно) составляет около 0,3, а для двигателей она достигает максимальнойвеличины0,7 дляпробегаот25 до75 тыс. км.
Если представить интенсивность отказов электродвигателей ввиде функции λдв = kp f (xi ) (где kp – коэффициент, учитывающий
условия работы на предприятиях различных отраслей, хi – прочие факторы), то согласно статистическим данным коэффициент kp составляет: для горнодобывающих предприятий черной металлургии 0,837, для предприятий цветной металлургии 0,919, угольной промышленности1,166, химическойпромышленности1,137.
Рассмотрим характерные повреждения основных узлов машин постоянного тока. К характерным повреждениям коллектора относятся изменение его формы из-за неравномерного износа, наруше-
37
ние полировки поверхности с появлением на ней царапин, подгорание и оплавление пластин при неблагоприятной коммутации и круговых огнях. При возникновении одного из указанных повреждений машина должна быть остановлена для проведения соответствующего ремонта. В целях устранения возникшей неисправности коллектор обязательно подвергается проточке резцом.
В некоторых типах электродвигателей постоянного тока применяются коллекторы с пластмассовым корпусом. Отказы таких коллекторов в большинстве случаев связаны с пробоем или перекрытием дугой изоляционной части корпуса.
Повреждение обмотки якоря происходит по следующим причинам: из-за пробоя корпусной изоляции между обмоткой и пакетом стали якоря, межвитковых замыканий (в якорях с многовитковыми секциями), распайки соединительных петушков коллекторных пластин с обмоткой (в машинах большой мощности), разрушения бандажей, удерживающих обмотку якоря (в высокоскоростных машинах), и др.
Повреждения обмоток возбуждения, обмоток добавочных полюсов и компенсационных обмоток довольно редки. Они представляют собой обычно пробой корпусной изоляции между обмоткой и магнитной системой машины.
Из механических частей машин постоянного тока наиболее подвержены износу подшипники скольжения или качения и шейки вала. Типичными повреждениями этих частей являются: износ вкладышей, вытекание смазки, нарушение работы смазочных колец, поломка шариков или роликов, разрушение сепараторов, заклинивание шариков, заедание шеек вала во вкладышах подшипников и т. д. Щёточная траверса выходит из строя при поломке кольца траверсы, которое держит её в подшипниковом или другом устройстве; при расстройстве регулировки положения щёткодержателей на пальцах или бракетах траверсы; при повреждении пальцев или бракетов, служащих для удержания щёткодержателей на траверсе, и в других ситуациях. Любые вышеуказанные повреждения приводят к отказу машины, которая должна быть остановлена для проведения соответствующего ремонта.
38
Следует отметить, что по отдельным типам МПТ публикаций об отказах до сих пор ещё недостаточно, а приводятся только некоторые сведения о причинах отказов.
Например, наблюдения за работой 6 прокатных двигателей постоянного тока (ДПТ) типа ПКБ250/145 (мощностью 3320 кВт, с частотой вращения 50/120 об/мин) в составе приводов валков блюминга позволили обнаружить 22 полных отказа, произошедших за 6 лет совместной работы данных двигателей и прокатных установок (1958–1964 гг.). Средняя наработка до первых отказов при этом составила два года (17 520 ч) со средним временем между соседними отказами, равным 1,4 года (12 260 ч). В табл. 10 приведено количество отказов отдельных частей данного типа двигателей (в процентах от общего числа отказов).
Таблица 1 0
Отказы конструктивных элементов двигателей типа ПКБ250/145
|
Количество отказов от- |
Количество простоев цеха |
|||||
|
дельных частей двигате- |
из-за отказов отдельных |
|||||
Конструктивные элемен- |
частей двигателей, % от |
||||||
лей, % от общего числа |
общего времени простоев |
||||||
ты прокатных двигате- |
|
отказов |
|
||||
|
|
из-за отказов двигателей |
|||||
лей |
|
|
|
||||
Блю- |
Блю- |
Блю- |
Блю- |
Блю- |
Блю- |
||
|
|||||||
|
минг |
минг |
минг |
минг |
минг |
минг |
|
|
№ 1 |
№ 2 |
№ 3 |
№ 1 |
№ 2 |
№ 3 |
|
Обмотка якоря |
5,5 |
10,5 |
– |
29,4 |
33,3 |
– |
|
Обмоткаглавныхполюсов |
– |
– |
– |
– |
– |
– |
|
Обмотка добавочных полю- |
11,0 |
– |
– |
7,2 |
– |
– |
|
совикомпенсационная |
|||||||
Коллектор |
44,3 |
58,6 |
66 |
47,1 |
61,4 |
85 |
|
Различные механические |
|
|
|
|
|
|
|
повреждения элементов |
39,2 |
30,9 |
34 |
16,3 |
5,3 |
15 |
В табл. 10 виден высокий процент отказов данных типов прокатных двигателей из-за повреждений коллекторов, причём устранение этих отказов требует значительных трудовых и материальных затрат. Этообъясняетсятем, чтонеблагоприятнаякоммутацияуряда прокатных двигателей и питающих их генераторов при регулярных

39
кратковременных перегрузках требует проведения частых проточек и шлифовок коллекторов, тщательного и длительного подбора подходящих марок электрощёток, повторных перепаек в местах соединенияпетушковобмотоксколлекторнымипластинамиит. п.
Анализ отказов данных типов прокатных двигателей постоянного тока показывает, что около 80 % составляют конструкционные и технологические отказы и примерно 20 % – эксплуатационные отказы.
Если предположить распределение отказов по экспоненциальному закону, то легко определяется средняя интенсивность отказов данных ДПТ ( λ = 0,57 10−4 ч−1 ) и надёжность для любых реальных промежутков времени работы двигателей (например, для промежутков времени работы 1000 и 4000 ч надёжность со-
ставила 0,945 и 0,80).
В табл. 11 приведены данные о распределении удельного (относительного) числа отключений синхронных генераторов, вызванных отказами в работе их возбудителей, за семь лет (1949–1955 гг.), а также относительное число дефектов, обнаруженных в возбудителях при капитальных ремонтах. Под удельным числом отключений подразумевается число аварийных отключений в году, отнесённое к числу работающих генераторов, выраженное в процентах.
Таблица 1 1
Повреждения основных элементов возбудителей синхронных машин
|
Относительное число |
Относительноечисло |
||
|
отключений синхрон- |
дефектов, обнару- |
||
Вид повреждения возбудителя |
ных генераторов в год |
женныхприкапи- |
||
|
из-за повреждений |
тальныхремонтах |
||
|
возбудителей, % |
возбудителей, % |
||
|
Турбо- |
Гидро- |
Турбо- |
Гидро- |
|
генератор |
генератор |
генератор |
генератор |
Повреждение бандажей |
0,85 |
Нет |
0,2 |
0,18 |
Распайка петушков |
0,64 |
0,21 |
1,3 |
0,18 |
Пробой изоляции обмотки якоря |
0,35 |
0,28 |
0,9 |
0,18 |
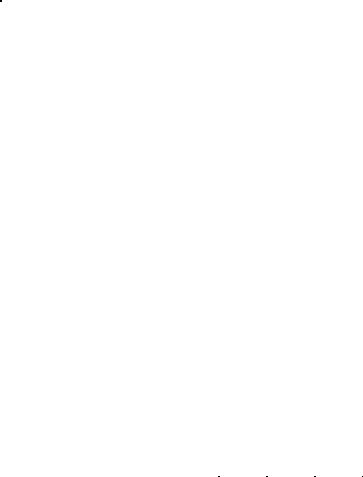
40
Окончание табл. 1 1
Вид повреждения возбудителя |
Относительное число |
Относительноечисло |
||
|
отключений синхрон- |
дефектов, обнару- |
||
|
ных генераторов в год |
женныхприкапи- |
||
|
из-за повреждений |
тальныхремонтах |
||
|
возбудителей, % |
возбудителей, % |
||
|
Турбо- |
Гидро- |
Турбо- |
Гидро- |
|
генератор |
генератор |
генератор |
генератор |
Потери контакта в цепи |
|
|
|
|
возбуждения |
0,30 |
0,07 |
– |
– |
Износ коллектора |
– |
– |
1,3 |
0,71 |
Прочие повреждения |
0,56 |
Нет |
2,1 |
1,95 |
Всего |
2,7 |
0,56 |
5,8 |
3,2 |
В табл. 11 видно, что наиболее частыми повреждениями возбудителей синхронных генераторов за указанный период являются повреждения бандажей обмотки якоря, нарушения пайки петушков и износ коллектора.
Как уже говорилось, в тяговых двигателях электровозов одной из частых причин отказов в работе является возникновение кругового огня на коллекторах. Имеющиеся статистические данные за 1964 г. показывают, что наибольшая интенсивность этого явления, а также других повреждений тяговых двигателей типа НБ-412М электровозов ВЛ60 приходится на летние месяцы
(табл. 12).
Таблица 1 2
Повреждения тяговых двигателей типа НБ-412М
Повреждение двигателя |
|
|
Месяц |
|
|
|
май |
июнь |
июль |
август |
сентябрь |
||
|
||||||
Круговой огонь на коллекторе |
42 |
76 |
71 |
112 |
78 |
|
Другие повреждения |
70 |
102 |
97 |
170 |
105 |
Основными причинами, вызывающими возникновение кругового огня на коллекторах тяговых двигателей данного типа, являются: буксование колёсных пар электровоза из-за неправильного подбора двигателей и неумелого управления электро-