
книги / Теория сварочных процессов
..pdf
|
|
|
|
|
|
|
|
|
|
Окончание табл. 4.5 |
||
|
|
|
|
|
|
|
|
|
|
|
|
|
|
|
Факторы оптимизации, мас.% |
|
|
Температурный |
Критерии оптимизации |
||||||
|
|
|
|
|
|
|
|
коэффициент |
|
|
|
|
|
Номер |
Х1 |
|
|
|
|
|
|
Число круп. |
Фракталь- |
||
|
элект- |
Х |
Х |
Х |
Х |
Иль- |
твердости β |
Ткр, °С |
неметал. |
ная раз- |
|
|
|
рода |
силико- |
2 |
3 |
4 |
5 |
менит |
(1серия/2 серия |
|
вкл. в поле |
мерность |
|
|
марганец |
слюда |
FeTi |
графит |
мрамор |
|
при несовпаде- |
|
структуры |
|
||
|
|
|
|
|
|
|
|
нии результатов) |
|
зрения |
Df |
|
|
|
|
|
|
|
|
|
|
|
|
||
|
1804 |
22 |
12 |
2 |
1 |
12 |
38 |
0,0331 |
–20 |
20 |
1,75 |
|
|
1805 |
6 |
12 |
2 |
1 |
12 |
54 |
0,0135 |
–50 |
5 |
1,87 |
|
|
1806 |
14 |
18 |
2 |
1 |
12 |
40 |
0,0129 |
–55 |
10 |
1,78 |
|
|
1807 |
14 |
6 |
2 |
1 |
12 |
52 |
0,0126 |
–55 |
10 |
1,84 |
|
161 |
1808 |
14 |
12 |
4 |
1 |
12 |
44 |
0,0133 |
–50 |
2 |
1,89 |
|
1809 |
14 |
12 |
0 |
1 |
12 |
48 |
0,0375/0,0244 |
–15/–30 |
30 |
1,82 |
|
|
|
|
|||||||||||
|
1810 |
14 |
12 |
2 |
3 |
12 |
44 |
0,0133 |
–50 |
1 |
1,87 |
|
|
1811 |
14 |
12 |
2 |
0 |
12 |
47 |
0,0133 |
–50 |
1 |
1,88 |
|
|
1812 |
14 |
12 |
2 |
1 |
18 |
40 |
0,0126 |
–55 |
10 |
1,83 |
|
|
1813 |
14 |
12 |
2 |
1 |
6 |
52 |
0,0131 |
–50 |
5 |
1,85 |
|
|
1814 |
14 |
12 |
2 |
1 |
12 |
46 |
0,0125 |
–55 |
13 |
1,82 |
|
|
1814 |
14 |
12 |
2 |
1 |
12 |
46 |
0,0133 |
–50 |
15 |
1,85 |
|
|
1814 |
14 |
12 |
2 |
1 |
12 |
46 |
0,0129 |
–50 |
10 |
1,85 |
|
|
1814 |
14 |
12 |
2 |
1 |
12 |
46 |
0,0133 |
–50 |
5 |
1,82 |
|
|
1814 |
14 |
12 |
2 |
1 |
12 |
46 |
0,0130 |
–50 |
10 |
1,82 |
|
|
1814 |
14 |
12 |
2 |
1 |
12 |
46 |
0,0134 |
–50 |
5 |
1,82 |
|
Примечание. Во всех составах вводились также тальк (10 %), целлюлоза (3 %). Жидкое стекло в количестве 27 % к массе сухой шихты.
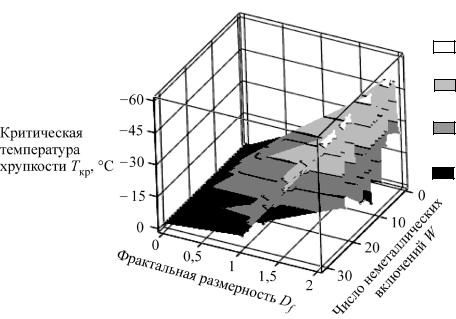
содержание слюды (Х2) в сочетании с мрамором, графитом и силикомарганцем загрубляет структуру: коэффициенты регрессии эффектов взаимодействия с Х2 всегда отрицательны.
Снижению загрязненности шва неметаллическими включениями в наибольшей степени способствуют ферротитан, совместно введенные ферротитан и силикомарганец (наиболее отрицательные коэффициенты регрессии –5 и –1,6), а также минимальное содержание слюды.
Наиболее полное представление о взаимосвязи критической температуры хрупкости, фрактальной размерности и загрязненности включениями получено с помощью тройной диаграммы взаимного влияния этих критериев (рис. 4.31). Область хорошей хладостойкости (вершина диаграммы, тонирована светлым тоном) находится на уровне высоких значений фрактальной размерности и низкого уровня загрязненности, область низкой хладостойкости – это нижняя часть диаграммы (темный тон) смещена в зону низкой фрактальной размерности и высокой загрязненности металла шва включениями.
Отличная хладостойкость
Хорошая хладостойкость
Удовлетворит. хладостойкость
Плохая хладостойкость
Рис. 4.31. Обобщенная диаграмма влияния фрактальной размерности и степени загрязненности неметаллическими включениями на хладостойкость металла сварного шва
Таким образом, исследование особенностей структурообразования сварных швов с использованием нового для металловедения сварки метода фрактального анализа позволило определить фрактальную размер-
ность Df – количественный показатель степени неоднородности и фраг-
162
ментарности структур сварных швов, а также установить критерии гомогенности структуры по значению фрактальной размерности. Выявле-
на связь структурной характеристики – фрактальной размерности Df – с уровнем вязкопластических свойств металла шва. Фрактальные размерности, наряду с критериями хладостойкости и чистоты шва, введены в задачи моделирования структурообразования, в результате реализации которых оптимизирован состав электродного покрытия.
4.8. Применение фрактального подхода для анализа поверхности усталостного разрушения
Усталость металлов остается важнейшей проблемой прочности материалов в связи с задачей повышения долговечности и надежности конструкций, работающих под действием различных видов циклических нагрузок.
Одними из наиболее сложных объектов являются сварные швы. При их испытании возникает ряд проблем, связанных с неоднородностью свойств материала, сложностью структуры, наличием конструктивных и технологических концентраторов напряжений, остаточных напряжений и т.д.
Наименее изученной областью исследования усталостных свойств металлов вообще и металлов сварных швов, в частности, является исследование их структурной зависимости.
Поэтому исследование структурной зависимости усталостных свойств с применением фрактального анализа и учетом фактора загрязненности шва неметаллическими включениями является весьма актуальным.
Сварные швы выполнялись электродами типа Э46 в канавку на полосах стали Ст.3 толщиной 6 мм за один проход. При таких условиях сварки существовали определенные ограничения по размерам образца. Из металла сварных швов изготавливали образцы Шарпи (ГОСТ 9454–78, тип 14). Вид концентратора – V-образный, длина L = = 55 мм, ширина t = 2,5±0,05 мм, высота W = 8±0,01 мм (рис. 4.32). Над-
рез ориентировали таким образом, чтобы трещина прошла через шов параллельно направлению сварки.
В ходе испытаний фиксировали кривые роста длины трещины l при увеличении числа циклов нагружения N. Вид кривых роста трещины для сварных швов представлен на рис. 4.33.
Для металла шва всех составов характерно достаточно плавное нарастание длины трещины с увеличением числа циклов нагружения без перегибов до длины примерно l = 5…6 мм. При этом пределе на кривых появляется перегиб, связанный с изменением схемы изгиба. При
163
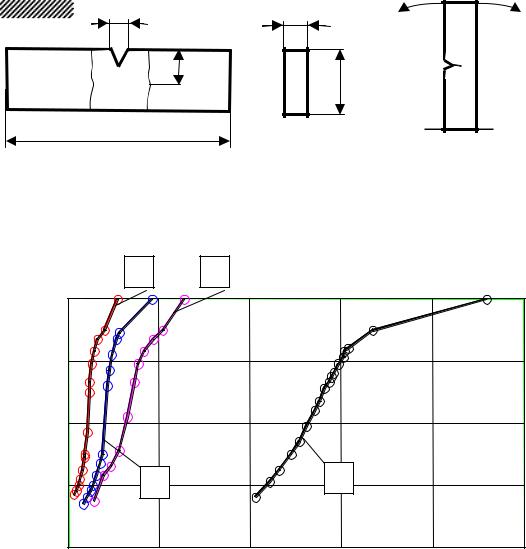
уменьшении рабочего сечения образца схема изгиба, выполняющаяся |
||||||||||||
в начале испытания, нарушается, деформирование становится возмож- |
||||||||||||
ным в нескольких направлениях и эффект сосредоточенности деформа- |
||||||||||||
ции исчезает, на кривых l = f(N) наблюдается замедление роста длины |
||||||||||||
трещины. Поэтому для сохранения корректности последующего анализа |
||||||||||||
характера усталостного разрушения ограничивались областью началь- |
||||||||||||
ных и средних длин трещин. |
|
|
|
|
|
|
|
|
|
|||
|
δ |
|
|
|
|
t |
|
σ |
|
|
σ |
|
|
|
|
|
|
|
|
|
|
|
|
||
|
|
l |
|
|
W |
|
|
|
|
|
||
|
|
|
|
|
|
|
|
|
|
|
||
|
L |
|
|
|
|
|
|
|
|
|
|
|
Рис. 4.32. Образцы для усталостных испытаний (штриховкой указано расположение |
||||||||||||
|
зоны сварного шва) и схема нагружения образца |
|
|
|
||||||||
|
1 |
|
|
3 |
|
|
|
|
|
|
|
|
8 |
|
|
|
|
|
|
|
|
|
|
|
|
6 |
|
|
|
|
|
|
|
|
|
|
|
|
L·10–3, м |
|
|
|
|
|
|
|
|
|
|
|
|
4 |
|
|
|
|
|
|
|
|
|
|
|
|
2 |
2 |
|
|
|
|
|
4 |
|
|
|
|
|
0 |
. |
|
5 |
. |
5 |
6 |
. |
5 |
. |
5 |
. |
6 |
|
|
|||||||||||
|
2 10 |
|
4 10 |
|
|
10 |
8 10 |
1 10 |
|
|||
|
|
|
|
|
|
N, циклов |
|
|
|
|
||
Рис. 4.33. Зависимость длины усталостной трещины L от числа |
|
|
||||||||||
циклов усталостных испытаний N для металла шва электродов: |
|
|
||||||||||
|
1 и 3 – 1805 (прогиб ∆ равен 1 и 1,5 мм); |
|
|
|
|
|||||||
|
2 и 4 – 1804 (прогиб ∆ равен 1 и 1,5 мм) |
|
|
|
|
164
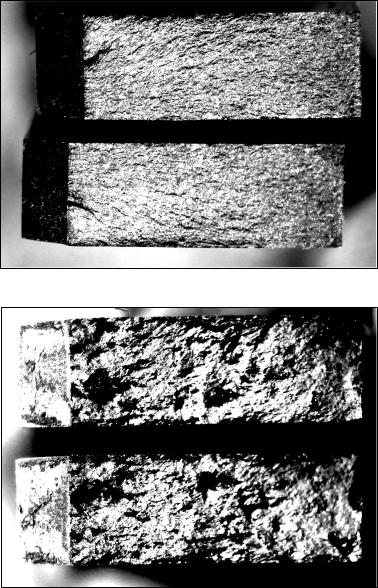
Этапу зарождения трещины предшествует инкубационный период, изменяющийся в зависимости от состава шва, структуры и величины изгибающего момента. Для прогиба ∆ = 1 мм инкубационный период составляет 2…3 105 циклов для швов с грубой структурой и 7…8 105 циклов для мелкозернистых швов. Эти трещины зарождаются тем раньше, чем выше уровень циклических напряжений и «грубее» структура металла шва.
На рис. 4.34 показаны макроструктуры изломов металла шва с мелкокристаллическим и крупнокристаллическим изломом.
а
б
Рис. 4.34. Макроструктура усталостного излома металла сварных швов. ×15
165
Дополнительную информацию о развитии усталостного разрушения металла сварных швов получили при использовании фрактального подхода к анализу усталостных изломов. Задачей данного этапа исследований является определение фрактальной размерности – структурной характеристики поверхности усталостного излома, и нахождение ее связи с динамическими характеристиками усталостного разрушения, например, со скоростью роста усталостной трещины.
Возможность и допустимость применения теории фракталов для анализа макроструктуры усталостных изломов объясняется следующим: фрактальный метод неоднократно успешно использовался при анализе фрактограмм усталостного разрушения в работах В.С. Ивановой, Г.В. Встровского [10].
Поскольку основным свойством фрактальных структур является инвариантность к масштабу, т.е. закономерности структуры, наблюдаемые при большом увеличении, должны сохраняться и при малом увеличении. Следовательно, целесообразным будет применение фрактального подхода к анализу макроизломов. Одной из особенностей применения метода фрактального анализа для исследования реальных усталостных изломов металлов является правильная идентификация объекта изучения. Если при исследовании видманштеттовой структуры объектом изучения являлось двумерное изображение структуры, то при анализе изломов имеем дело с трехмерным изображением.
Вуказанных выше работах объектом анализа являлись фрактограммы поверхности усталостного излома образцов молибдена, полученные на электронном микроскопе. При этом трехмерное изображение определенным образом обрабатывали, приводя к двумерному, что приводило к неизбежному упрощению или загрублению изображения. Для изучения изломов металла методом фрактального анализа предварительно получали «картинку», образующуюся в результате сечения поверхности излома секущей плоскостью и анализировали, в сущности, «след», остающийся на секущей плоскости. Таким образом, в качестве критерия однородности и скрытой периодичности структуры излома использовали показатель – фрактальную размерность, или набор фрактальных размерностей.
Внашем случае особенностью реального изображения макроизлома усталостного разрушения на цифровой фотографии является, вопервых, наличие тени на рельефе (даже при расположении источника света сверху), и, во-вторых, соответствие цветового тона каждого фрагмента на изображении высоте соответствующего фрагмента на реальном изломе.
166
Поэтому изображения изломов, полученные с помощью цифровой фотокамеры, подвергали предварительной обработке, реализуемой программными средствами Adobe Photoshop 7,0.
Основные этапы обработки:
–устранение тени на изображении;
–создание эффекта сечения на уровне 0,2 мм по глубине тона;
–контурирование рельефа.
Далее полученное изображение загружалось в программный файл фрактального анализа и по алгоритму, описанному в подразд. 4.7, проводился обсчет изображения, конечным результатом которого являлось определение фрактальной размерности макроизлома.
Исследования проводились для разных зон усталостного излома, соответствующих разным скоростям распространения трещины: на-
чальной зоны излома со скоростью 10–9 м/цикл и центральной зоны со
скоростью 10–7 м/цикл. Точное расположение зон устанавливалось при сопоставлении кривых роста трещины с кинетической диаграммой усталостного разрушения для каждого шва.
На рис. 4.35, 4.36 представлены последовательные этапы обработки изображения отдельных зон излома металла шва опытных электродов и фрагмент листинга программы фрактального анализа.
Количественные показатели разрушения и фрактальные характеристики приведены в табл. 4.6.
Таблица 4.6
Количественные показатели разрушения и фрактальные характеристики по зонам усталостного излома металла сварных швов
Номер |
Начальная зона излома |
Центральная зона излома |
||
Скорость роста |
Фрактальная |
Скорость |
Фрактальная |
|
электрода |
трещины, м/цикл |
размерность |
роста трещи- |
размерность |
|
|
Dfn |
ны, м/цикл |
Dfc |
1804 |
10–10…10–9 |
1,71 |
10–8…10–7 |
1,65 |
1805 |
10–8 |
1,67 |
10–7 |
1,54 |
1808 |
10–8 |
1,64 |
10–7 |
1,58 |
1809 |
10–9 |
1,68 |
10–7 |
1,59 |
167
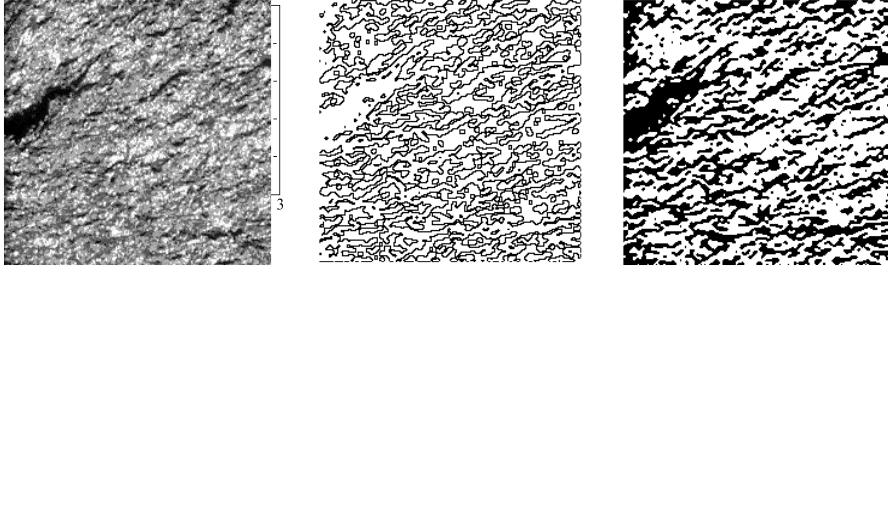
168
|
|
|
|
|
|
|
|
|
|
а |
|
б |
в |
Рис. 4.35. Последовательные этапы обработки изображения начальной зоны излома шва электрода 1804: а – реальное изображение; б, в – сечение излома с удалением тени и контурированием рельефа; г – зависимость ln P от ln L
и фрактальная размерность излома Df = 1,72
г
168
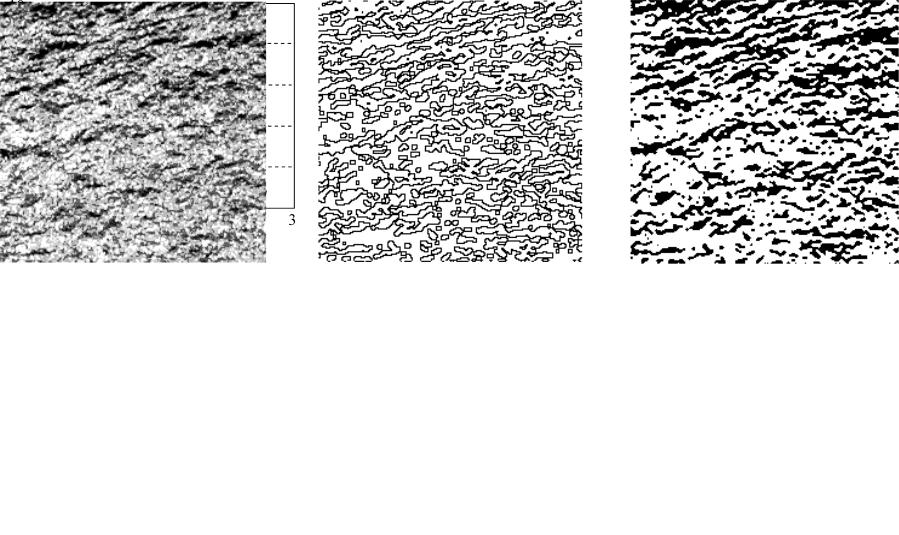
169
|
|
|
|
|
а |
б |
в |
Рис. 4.36. Последовательные этапы обработки изображения центральной зоны излома шва электрода 1804: а – реальное изображение; б, в – сечение излома с удалением тени и контурированием рельефа; г – зависимость ln P от ln L,
фрактальная размерность излома Df = 1,66
г
169
Итак, определена фрактальная размерность излома – структурная характеристика поверхности усталостного разрушения, исследована ее связь с динамической характеристикой процесса – скоростью роста усталостной трещины.
Анализ полученных данных позволяет заключить, что фрактальная размерность макроструктуры отдельных зон излома связана со скорость распространения усталостных трещин: при малой скорости роста усталостной трещины 10–10…10–9 м/цикл в начальный момент нагружения излом характеризуется фрактальной размерностью Dfn ≈ 1,70; при возрастании скорости до 10–8 м/цикл фрактальная размерность уменьшается до 1,67…1,64; центральной части излома со скоростью распространения трещины 10–7 м/цикл соответствует фрактальная размерность
Dfc = 1,60…1,55.
Таким образом, фрактальная размерность может рассматриваться как адекватный количественный показатель скорости распространения усталостной трещины, подобный такому показателю, как ширина бороздок на электронных фрактограммах. Вместе с тем, процесс проведения фрактального анализа усталостного излома значительно менее трудоемок, чем традиционная фрактография.
4.9. Фрактальный анализ пористости в покрытиях при микродуговом оксидировании
Другим примером использования фрактального подхода в металловедении служит анализ структурообразования покрытий, нанесенных методом микродугового оксидирования.
Формирование покрытий в режиме микродугового оксидирования происходит в условиях многократно повторяющихся дуговых пробоев образующегося оксидного слоя. Ввиду постоянно изменяющейся электропроводимости спонтанно изменяются количество и размеры образующихся кратеров и регулировать процесс их формирования не представляется возможным. Образование пор в МДО-покрытиях является результатом специфики механизма пробоя анодных пленок. Пористость анодных оксидных покрытий и анодных пленок является основной проблемой, приводящей к частичной или полной потере защитных свойств МДО-покрытий и, как следствие, снижению коррозионной стойкости, износостойкости и других эксплуатационных характеристик. В работе А.И. Горчакова исследованы причины образования пор в МДОпокрытиях. Выводы о паровой природе пор подтверждены физикохимическими расчетами условия кипения металла, металлографическим
170