
книги / Теория сварочных процессов
..pdf
тем интенсивнее легирование кремнием и марганцем. Чем меньше это соотношение, тем легирование меньше. Именно по этой причине при сварке низкоуглеродистой стали проволокой Св08 под флюсом, содер-
жащим менее 10 % MnO и 15…20 % SiO2, марганец и кремний шов вообще не легируют. Кремний будет переходить в шов при содержании SiО2 во флюсе более 25 %, но при этом переход марганца из флюса в шов уменьшится из-за образования комплексов (MnO SiО2). Марганец будет переходить в шов с повышением основности флюса, в данном
случае это соотношение В = СaO+MgO . SiO2
При сварке под флюсом требуется надежное рафинирование металла как от серы, так и от фосфора. Источником серы является марган-
цевые руды, в которых сера находится в виде серного колчедана (FeS2). При температурах Т > 600 °С серный колчедан окисляется c образованием двуокиси серы по реакции
(FeS2) + O2 → [FeS] + SO2↑
При сварке под плавленными марганцовистыми флюсами удаление серы осуществляется оксидом марганца:
[FeS] + (MnO) → (MnS) + [FeO].
При высоком (более 25 %) содержании в марганцовистом флюсе оксида марганца (MnO) сера в металл шва практически не переходит.
При сварке под безмарганцовистыми или низкомарганцовистыми флюсами рафинирование от серы осуществляется оксидами Ca и Mg:
[FeS] + (CaO) → (CaS) + [FeO], [FeS] + (MgO) → (MgS) + [FeO].
Источником фосфора при сварке под флюсом являются марганцевые руды, которые загрязнены этим компонентом во много раз сильнее любых других руд. Удаление фосфора осуществляется традиционным путем с помощью обменных реакций с компонентами флюса (см. под-
разд. 2.9).
Металлургические процессы при сварке под керамическими флюсами имеют свои отличия по сравнению со сваркой под плавленными флюсами. Поскольку плавленные флюсы представляют собой системы неметаллических составляющих (оксидов, галогенидов), то легирование металла шва в этих случаях возможно только в результате диссоциации этих соединений на металлические составляющие. Вводить таким образом большое количество легирующих элементов в шов через флюс затруднительно и легирование составляет десятые доли процента. В кера-
81
мических флюсах легирующие вводятся в виде свободных металлических составляющих (ферросплавов и металлов). На этапе приготовления керамический флюс не подвергается нагреву, поэтому выгорания даже таких активных металлов, как титан и алюминий, не происходит. Таким образом, при сварке под керамическими флюсами осуществляется более широкий диапазон легирования металла шва. С увеличением напряжения дуги Uд легирование увеличивается, с увеличением тока сварки Iсв – уменьшается.
При сварке под керамическими флюсами кроме легирования возможно осуществлять модифицирование структуры металла сварного шва. Модифицированием называется измельчение зерна металла шва. В качестве модификаторов используются титан, кальций, алюминий. Механизм модифицирования заключается в том, что мелкодисперсные частицы этих металлов служат центрами образования зерен при кристаллизации металлической ванны. Модификаторы вводятся в виде FeTi, силикокальция и металлического алюминия в состав керамического флюса.
Раскисление при сварке под керамическими флюсами осуществляется ферросплавами – FeSi, FeMn, FeTi, введенными во флюс.
Рафинирование металла шва от серы и фосфора при данном виде сварки осуществляется через CaO и MgO, введенных в состав флюса.
Недостатком керамических флюсов с точки зрения металлургии процессов является неоднородность химического состава наплавленного металла, а также тот факт, что тугоплавкие металлы флюса могут не полностью растворяться в металле шва.
2.10.4. Металлургические процессы при сварке в среде защитных газов
Сущность способа заключается в том, что при сварке столб дуги, ванна и частично шов защищены струей газа от воздействия воздуха. Разновидностями способа являются сварки плавящимися электродами и неплавящимися электродами (с присадочной проволокой или без нее). Данный вид сварки применяется для соединения активных металлов – алюминия, титана (сварка в инертных газах Ar, He), кобальта, меди (сварка в азоте) и высоколегированных сталей (сварка в CO2).
Инертными называются газы, которые не образуют химических соединений с металлом в любых условиях. Для сварки применяют в основном два сорта аргона (табл. 2.13).
82
|
|
|
|
|
Таблица 2.13 |
|
|
Состав газов, об.% |
|
|
|
||
|
|
|
|
|
|
|
Сорт газа |
|
Ar |
O2 |
N2 |
|
H2O |
Высший |
|
99,993 |
0,0007 |
0,005 |
|
0,007 |
(для сварки Ti, Zr, Nb) |
|
|
|
|
|
|
Первый |
|
99,987 |
0,002 |
0,01 |
|
0,01 |
(для сварки Al, Mg, стали) |
|
|
|
|
|
Гелий выпускается трех сортов: особой чистоты (99,995 % Не); высокой чистоты (99,985 % Не); технический (99,80 % Не).
Металлургия при сварке в инертных газах имеет следующие особенности:
−хотя при сварке создается неокислительная среда, возможно непрямое взаимодействие с примесями защитного газа и с воздухом, который проникает в зону сварки вследствие турбулентности движения газовой струи;
−на каплях электродного металла нет пленки шлака, и поэтому имеет место повышенное испарение металла и угар легирующих элементов;
−в металле сварного шва возможна водородная пористость, если инертный газ не подвергается предварительной сушке.
Защитным считается газ, не являющийся инертным, но который
сданным металлом не образует устойчивых в условиях сварки химических соединений, ухудшающих свойства шва. Наиболее распространен-
ный защитный газ – углекислый СО2. Сварку в СО2 проводят только плавящимися электродами.
В преддуговой области идет высокотемпературная диссоциация углекислого газа:
2{CO2} 2{CO} + {O2} − Q.
(Как и любой процесс диссоциации, реакция идет с поглощением тепла).
Состав газовой фазы в различных точках зоны сварки меняется в соответствии с приведенной зависимостью долей СО, О2 и СО2 от температуры (рис. 2.28). Чем ближе расположен участок шва к зоне горения дуги, тем более диссоциирован в ней СО2, т.е. больше кислорода
игаза СО.
Ввысокотемпературной зоне идет окисление железа, углерода
илегирующих элементов по реакциям:
83
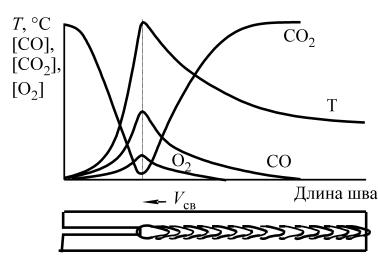
2[Fe] + {O2} → 2[FeO], 2[C] + {O2} → 2{CO}, [Si] + {O2} → (SiO2), 2[Mn] + {O2}→ 2(MnO).
Для предотвращения выгорания легирующих элементов необходимо использовать для сварки легированную марганцем и кремнием проволоку Св08ГС, Св08Г2С.
Рис. 2.28. Состав газовой фазы в различных зонах по длине шва при сварке в СО2
Вхвостовой части сварочной ванны идут процессы рекомбинации молекул СО2 и Н2О и раскисление.
Врезультате экзотермической реакции рекомбинации молекул СО2
2{СО} + {O2} → 2{CO2} + Q
увеличивается глубина проплавления шва, что необходимо учитывать при назначении режима сварки.
Раскисление марганцем и кремнием усиливается с понижением температуры металла шва:
[Mn] + [FeO]→ [Fe] +(MnO), [Si] + 2[FeO] → 2[Fe] + (SiO2).
Водород, образованный при диссоциации паров воды, связывается в молекулы при взаимодействии с углекислым газом:
{H2} + {CO2}→{H2O} + {CO}.
Вследствие протекания этой реакции металл шва менее загрязнен водородом, чем при других способах сварки.
84
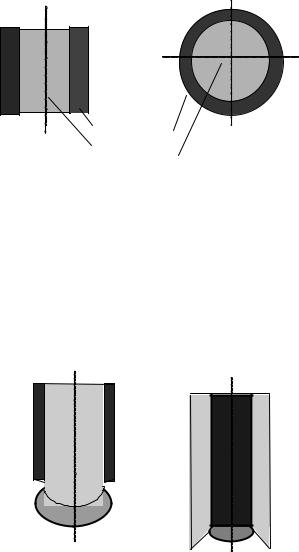
2.10.5.Металлургия сварки порошковой проволокой
Вданном способе сварку ведут, используя в качестве электрода специальную порошковую проволоку.
Порошковая проволока состоит из стальной оболочки и порошкового сердечника (рис. 2.29). Наружный диаметр порошковой проволоки – от 1,6 до 3 мм.
Получают порошковую проволоку по следующей технологической схеме:
|
− вальцовка стальной ленты |
|
|
|||||
диаметром 0,2…0,5 мм в трубку |
|
|
||||||
на специальных вальцах; |
Оболочка |
|
||||||
|
− засыпка в трубку порош- |
Сердечник |
|
|||||
кообразных компонентов – шла- |
Рис. 2.29. Схема строения порошковой |
|||||||
ко-, газообразующих, раскисли- |
проволоки |
|
||||||
телей и легирующих; |
|
|
|
|||||
|
− дополнительная обжимка порошковой проволоки; |
|
||||||
|
− свертывание в бухты. |
|
|
|||||
|
По способу защиты порошковые проволоки классифицируют на |
|||||||
самозащитные и проволоки для сварки в защитном газе. |
|
|||||||
|
По составу самозащитные проволоки бывают рутилорганические |
|||||||
и карбонатно-флюоритные, проволоки для сварки в СО2 бывают флюо- |
||||||||
ритные |
(ПП-АН6), |
рутиловые |
|
|
||||
(ПП-АН8) и рутил-флюоритные |
|
|
||||||
(ПП-АН8). Особенностью сварки |
|
|
||||||
порошковой проволокой являет- |
|
|
||||||
ся тот факт, что нагрев и плавле- |
|
|
||||||
ние сердечника отстает от нагре- |
|
|
||||||
ва и плавления оболочки. При |
|
|
||||||
сварке |
плавящимся |
электродом |
|
|
||||
(рис. 2.30), наоборот, плавление |
а |
б |
||||||
электродной проволоки опережа- |
||||||||
ет плавление покрытия, в резуль- |
Рис. 2.30. Неравномерность плав- |
|||||||
тате |
чего |
на |
торце |
электрода |
||||
образуется втулка из электродно- |
ления сердечника и оболочки по- |
|||||||
рошковой проволоки (а) и покры- |
||||||||
го покрытия. Природа этих явле- |
||||||||
тия и стержня электрода (б) |
||||||||
ний одинакова – в состав сердеч- |
|
|
||||||
ника порошковой проволоки, как и в состав электродного покрытия, |
||||||||
входят тугоплавкие компоненты с низкой теплопроводностью, которые |
||||||||
замедляют нагрев этих частей. |
|
|
85
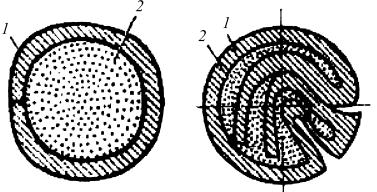
Для уменьшения отставания в нагреве усложняют конструкцию порошковых проволок, выполняя фигурную вальцовку (рис. 2.31).
Рис. 2.31. Конструкция порошковой проволоки: 1 – трубка, 2 – порошок
Основные проблемы металлургии сварки порошковой проволокой заключаются в том, что при использовании самозащитной проволоки
в шве много газовых примесей N2, H2, O2. Во избежание этого недостатка в сердечник проволоки вводят раскислители и нитридообразующие элементы – Ti, Al, Zr. Количество этих элементов сердечника не должно превышать 15–18 %, иначе начнется отставание плавления сердечника от плавления оболочки, так как все эти элементы – тугоплавки. Кроме того, увеличивается количество тугоплавких неметаллических включений в металле шва, что снижает его ударную вязкость.
2.10.6. Металлургические процессы при электрошлаковой сварке
К флюсам электрошлаковой сварки предъявляется ряд особых требований:
−высокая электропроводность флюса, для обеспечения быстрого начала электрошлакового процесса и его устойчивого прохождения.
Втвердом состоянии ток проводит только TiO2. Все остальные оксиды электропроводны только в жидком состоянии;
−обеспечение легкой отделимости шлаковой корки. В наибольшей
степени отделимость снижает оксид Al2O3;
−низкая температура плавления шлака и высокая температура ки-
пения;
−предупреждение дугообразования.
Для этого применяют флюсы с низкими стабилизирующими свой-
ствами – без CaO, MgO, К2O.
86
Все флюсы для ЭШС плавленные, не керамические. По химическому составу их разделяют на 4 основных класса:
1.Высококремнистые и высокомарганцовистые.
2.Низкокремнистые и низкомарганцовистые.
3.Бескремнистые.
4.Фторидные.
Особенности металлургии электрошлакового процесса заключаются в следующем:
−высоко- и низкотемпературные зоны имеют существенное различие в размерах: небольшая область вблизи торца электрода и весь остальной объем ванны соответственно;
−газовая атмосфера не контактирует с металлом, следовательно, основное значение приобретает взаимодействие металл–шлак. При дуговой сварке через шлак проходит, шунтируя дуговой разряд, лишь 12 % тока. При ЭШС весь ток идет через шлак, и, следовательно, сильнее идут электрохимические процессы между металлом и шлаком;
−при электрошлаковой сварке углерод выгорает слабее, чем при дуговой сварке, поскольку температура ЭШС меньше;
−необходимо организовывать замену флюса, так как состав шлака меняется в ходе сварки (увеличивается содержание FeO).
Контрольные вопросы
1.Перечислите группы металлургических процессов при сварке плавлением.
2.Охарактеризуйте основные типы сварочных ванн.
3.Характер распределения температур в сварочной ванне I типа.
4.Под действием каких сил осуществляется перенос электродного металла в сварочную ванну при ручной дуговой и автоматической сварке под флюсом?
5.Назовите виды переноса электродного металла через дуговой промежуток.
6.От каких факторов зависит размер электродных капель?
7. Как изменяются характер переноса электродного металла
сростом сварочного тока или напряжения на дуге?
8.Напишите уравнение диссоциации двух- и трехатомных газов, наиболее часто встречающихся в атмосфере дуги.
9.Каков механизм насыщения жидкого металла газами?
10.В чем проявляется влияние кислорода на свойства стали?
11.Как влияет азот на свойства стали?
87
12.Как влияет водород на свойства стали?
13.Какими путями попадают кислород, азот и водород в реакционное пространство при дуговой сварке?
14.В чем проявляется влияние оксидов углерода на свойства
стали?
15.Назначение шлаков при сварке.
16.Основы молекулярной и ионной теории шлаков.
17.Что такое основность шлаков?
18.Охарактеризуйте основные физические свойства сварочных
шлаков.
19.В чем различие длинных и коротких шлаков?
20.Дайте характеристику важнейших простых оксидов, входящих
всостав сварочных шлаков.
21.Назовите три основные системы сварочных шлаков.
22.В чем заключаются металлургические функции шлаков?
23.Перечислите три основных вида окисления составляющих металла и шлака.
24.Виды раскислительных процессов.
25.Приведите пример раскисления стали с получением конденсированных продуктов реакции.
26.Дайте характеристику основных раскислителей − Si; Mn; Ti; Al; подчеркните положительные и отрицательные свойства каждого из них.
27.Какие группы компонентов входят в состав электродного покрытия или флюса?
28.Каков механизм диффузионного раскисления стали шлаком?
29.Какими бывают сварочные флюсы по способу изготовления?
30.Пути легирования металла шва, их особенности, достоинства и недостатки.
31.Что такое коэффициент перехода элемента?
32.Каков механизм рафинирования стали от серы и фосфора?
33.В чем заключаются особенности металлургических процессов при дуговой сварке в углекислом газе?
34.Какие особенности у металлургических процессов при сварке порошковой проволокой?
35.Какие особенности у металлургических процессов при электрошлаковой сварке?
88
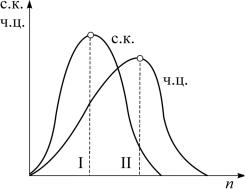
Глава 3 ПРОЦЕССЫ КРИСТАЛЛИЗАЦИИ МЕТАЛЛА ПРИ СВАРКЕ
3.1. Первичная кристаллизация металла
Переход металла из жидкого состояния в твердое сопровождается перегруппировкой атомов из неупорядоченного их расположения в упорядоченное, закономерное, определяемое кристаллической решеткой. Процесс образования кристаллов в металле при его затвердевании называется кристаллизацией. Как установил еще Д.К. Чернов, кристаллизация состоит из двух элементарных, одновременно протекающих процессов:
1)зарождения зародышей, или центров кристаллизации;
2)роста кристаллов из этих центров.
Первоначально вырастают оси кристаллов, характеризующиеся симметрией 1-го, 2-го и последующих порядков. Затем заполняются межосевые пространства и образуются кристаллы, скелет которых имеет дендритное, или древовидное, строение. На основе этих общих представлений сложились две теории кристаллизации металлов – непрерывной и периодической кристаллизации.
Теория непрерывной кристаллиза-
ции разработана Г. Тамманом на основе исследований кристаллизации органических веществ при различных температурах. Г. Тамман установил, что при переохлаждении жидкого расплава в нем самопроизвольно зарождаются центры кристаллизации и начинается рост кристаллов. В связи с этим скорость кристаллизации определяется как числом центров (ч.ц.) кристаллизации, зарождающихся в единицу времени, так и линейной скоростью роста кристаллов (с.к.) в единицу времени. Соотношение этих величин определяет размер образующихся кристаллов.
При переохлаждении п = 0 (рис. 3.1) значения ч.ц. и с.к. также равны нулю, т.е. кристаллизация невозможна из-за отсутствия переохлаждения. С появлением небольшого переохлаждения ч.ц. и с.к. вначале возрастают. На рис. 3.1 положению I соответствует относительно небольшое число центров при максимуме скорости роста кристаллов. В этом случае следует ожидать образования немногочисленных, но
89
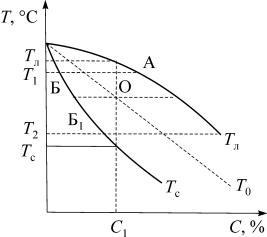
крупных кристаллов. Значительному переохлаждению жидкости в положении II отвечает максимальное число центров кристаллизации ч.ц., но относительно малая скорость роста кристаллов с.к. Тогда будет образовываться мелкое зерно.
Теория непрерывной кристаллизации Г. Таммана предполагает спокойное затвердевание жидкости – без перемешивания жидкого металла внутренними конвективными потоками, при равномерном распределении температур в кристаллизующемся объеме, тогда как в действительности таких условий обычно не бывает. Следовательно, теория непрерывной кристаллизации имеет ограниченное применение для реальных жидких металлов.
Теория периодической кристаллизации развита в работах советских ученых школы акад. Н.Т. Гудцова. Согласно этой теории кристаллизация металлов протекает с остановками вследствие периодического выделения скрытой теплоты кристаллизации, приостанавливающей равномерное течение процесса. Поскольку кристаллы растут с некоторыми остановками, т.е. слоями, центрами кристаллизации для каждого последующего слоя становятся различные неровности на поверхности предыдущего слоя.
Процесс кристаллизации имеет известную направленность: кристаллы растут в направлении, обратном теплоотводу, в глубь жидкости, причем внешняя форма их зависит от условий соприкосновения друг с другом.
В современных представлениях о кристаллизации сплавов особая роль отводится диффузионным процессам. Возьмем для примера
Рис. 3.2. Часть диаграммы состояния |
сплав концентрации С1 (рис. 3.2). |
|
При его переохлаждении от Тл до |
||
сплавов, образующих непрерывный |
||
ряд твердых растворов |
Т1 в жидкой фазе образуются заро- |
|
|
дыши твердой фазы, в которой |
растворенный элемент содержится в количестве, определяемом линией солидуса Тс при температуре Т1, т.е. точкой Б.
Непосредственно окружающая твердую фазу жидкость будет обогащаться растворенным элементом. Содержание его при температуре Т1, определится положением линии ликвидуса Тл, т.е. точкой А.
90