
книги / Теория сварочных процессов
..pdf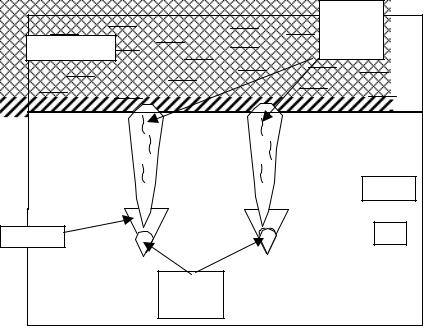
и фрактальным анализами морфологии пор при исследовании микроструктуры МДО-покрытия.
Причин образования пористости в покрытиях, полученных при микродуговом оксидировании, несколько. Во-первых, анализ тепловых условий процесса показывает, что при потенциалах микродуги электрические пробои в жидкостях вызывают локальное повышение температу-
ры до 20 103 К, а давления – до 100 МПа, что делает возможным термохимические реакции с участием как обрабатываемого металла, так и элементов электролита. В этих условиях вполне вероятно кипение металла основы на дне канала пробоя и образование вследствие этого пузырька пара этого металла. Второй причиной порообразования может явиться кипение электролита в порах при относительно большой плот-
ности тока (свыше 1 А/дм2).
Схема образования парового пузырька на границе раздела фаз в МДО-покрытии показана на рис. 4.37. С учетом того, что толщина оксидного слоя обычно составляет 50…200 мкм, пузырек пара должен выйти на поверхность и разряд приведет к появлению эффекта полого катода, вызывая образование наружной пористости и рыхлого поверхностного слоя. В то же время ускоренный теплоотвод и быстрая кристаллизация препятствуют выходу парового пузырька на поверхность анода, что вызывает образование микропор внутри слоя.
|
Газовый |
Электролит |
разряд |
в порах |
|
|
Al2O3 |
Расплав |
Al |
|
Паровой |
|
пузырек |
Рис. 4.37. Схема образования парового пузырька |
|
на границе раздела фаз в МДО-покрытии |
171

Условием кипения металла является равенство давлений внутри пузырька пара и снаружи:
P |
+ γ |
|
|
gh + γ |
|
gl + 2σ |
= P0 |
exp |
|
−2σM |
, |
|
Me |
эл |
|
|
|
||||||||
внеш |
|
|
r |
Me |
|
|
|
|||||
|
|
|
|
|
|
|
|
|
γMeRTr |
|
||
где Pвнеш – внешнее |
давление, Па; |
γMe и |
γэл |
|
– плотности металла |
и электролита, кг/м3; h – толщина оксидного слоя, м; l – глубина погружения электрода в электролит, м; σ – поверхностное натяжение жидкого металла, Дж/м2; r – радиус парового пузырька в момент заки-
пания, м; PMe0 – давление насыщенного пара металла, Па; M – атомная масса металла, кг/моль; R – универсальная газовая постоянная, Дж/моль К; T – абсолютная температура, К; g – ускорение свободного
падения.
При вычислении гидростатического давления на глубине расплавленного металла будем использовать значение толщины оксидного слоя h. Это упрощение не внесет серьезных ошибок в расчеты, поскольку выражение γMegh не является значащим членом в левой части урав-
нения.
Принимая во внимание, что внешнее давление при МДО остается постоянным и значащим членом в левой части уравнения является пока-
затель 2rσ , то основная зависимость радиуса парового пузырька наблю-
дается с изменением температуры.
Результаты расчетов радиуса пузырька пара металла при его кипении вблизи канала микродугового разряда при МДО алюминия и титана
взависимости от температуры и толщины оксидной пленки приведены
втабл. 4.7.
Таблица 4.7
Размеры пузырька пара алюминия и титана при их кипении вблизи канала микродугового разряда при МДО
Температура, К |
Толщина оксидной пленки, мкм |
r, мкм |
|
|
Алюминий |
|
|
2800 |
30 |
2,3 |
|
300 |
2,3 |
||
|
|||
3000 |
30 |
1,3 |
|
300 |
1,3 |
||
|
|||
3800 |
30 |
0,9 |
|
300 |
0,9 |
||
|
172
Окончание табл. 4.7
Температура, К |
Толщина оксидной пленки, мкм |
r, мкм |
|
Титан |
|
3600 |
100 |
Около10 |
3800 |
100 |
5,2 |
4000 |
100 |
3,0 |
Как показывают расчеты, изменения толщины оксидного покрытия не оказывают существенного влияния на размеры пузырька пара металла, т.е. при толщинах оксидного слоя в пределах от 30 до 300 мкм условия кипения остаются одинаковыми. Из таблицы видно, что с ростом температуры происходит уменьшение размера пузырька пара, однако даже максимальная расчетная его величина значительно ниже миллиметровых размеров пор наружного технологического слоя. В связи с этим можно утверждать, что паронаполненная сфера не всегда будет выходить на поверхность, чем и объясняется наличие микронной порис-
тости внутреннего слоя. Данное положение хорошо |
согласуется |
с экспериментальными результатами, полученными В.В. |
Баковцем, |
Э.С. Атрощенко, которые обнаружили поры-капилляры диаметром 0,05…0,5 мкм при толщине покрытия 15…50 мкм, а также с нашими исследованиями микроструктуры.
Выводы о паровой природе пор подтверждаются также морфологией пор, изученной при металлографических исследованиях (рис. 4.38).
Во-первых, это локализация пор не только в верхнем технологическом слое (там они возникают вследствие кипения электролита), но и в глубинном основном слое покрытия. Именно в основном слое создаются условия кипения металла в канале пробоя, максимум температуры и там вероятнее всего происходит формирование поры, образованной парами металла.
Количество и размер пор в верхнем технологическом слое увеличивается с ростом температуры электролита: при температуре электролита 20 °С их почти нет, а при температуре электролита 80 °С, когда идет активное его кипение, пор много и они достаточно большие.
Во-вторых, это форма и размеры пор. Поры в наружном слое МДОпокрытия имеют рваные края (рис. 4.39, а), форма пор далека от сферической. Внутренние поры, формирующиеся при парообразовании металла (рис. 4.40, а), имеют ровные края, форма поры близка к форме правильной сферы, что свидетельствует о том, что объем жидкой фазы при формировании поры был минимален – при разряде оплавляются лишь металл в поверхностном слое канала и его вершине, а прилегающие слои металла оказываются разогретыми, но нерасплавленными.
173
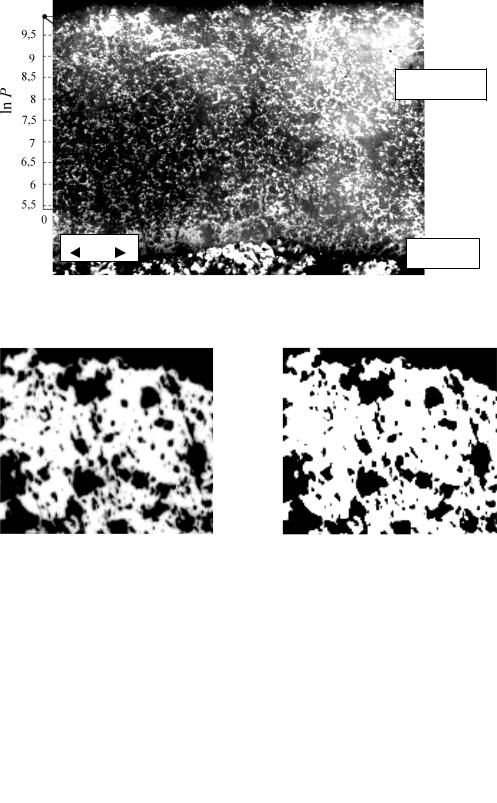
Покрытие
50 мкм |
Основа |
|
Рис. 4.38. Микроструктура покрытий, полученных при температур электролита 40 °С
|
|
|
а |
б |
в
Рис. 4.39. Микроструктура наружного слоя МДО-покрытия: а – реальное изображение; б – бинарное; в – зависимость мультифрактальной меры N от размерного фактора l и определение фрактальной размерности D
174
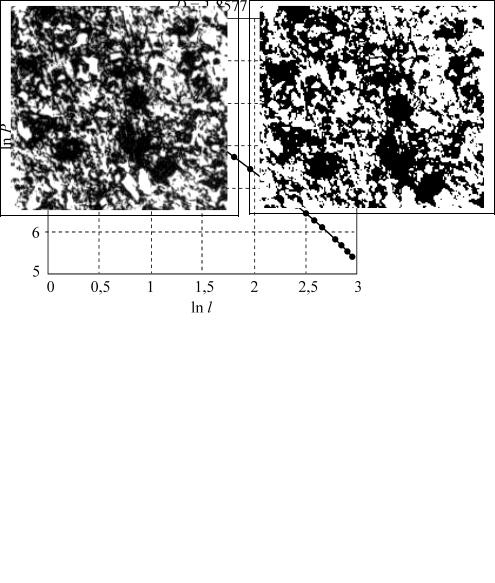
а |
б |
в
Рис. 4.40. Микроструктура внутреннего слоя МДО-покрытия: а – реальное изображение; б – бинарное; в – зависимость мультифрактальной меры N от размерного фактора l и определение фрактальной размерности D
Эволюция пористой структуры по глубине слоя прослеживалась
спомощью сравнительно нового для металловедения покрытий метода фрактального анализа, который позволил установить значения фрактальных размерностей Реньи D – показателя однородности и фрагментарности пористой структуры. Фрактальная, или мультифрактальная, мера характеризует распределение исследуемой структурной характеристики на соответствующем геометрическом носителе – наборе сеток
спрямоугольными ячейками. Предложено в качестве меры для пористой структуры МДО-покрытий принять плотность распределения участ-
175
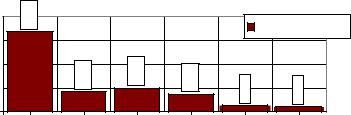
ков пористости на условной прямоугольной сетке, покрывающей поле шлифа. Плотность распределения пор N(Li) на каждой сетке связана с размером ячейки Li этой сетки степенным соотношением
N(Li) = const Li–D.
Из этого соотношения вычисляли фрактальную размерность структуры – D. Алгоритм реализован программными средствами Mathcad 2001 Professional, MATLAB 6.1
Фрактальная размерность внутренней пористой структуры для всех исследованных образцов выше, чем для наружной, что говорит о большей однородности и упорядоченности структуры внутреннего слоя покрытия и более равномерном распределении пор в нем
(см. рис. 4.39, 4.40).
Количество пор
80 |
67 |
|
|
|
Количество пор |
|
60 |
|
|
|
|
||
|
|
|
|
|
|
|
40 |
|
17 |
20 |
15 |
|
|
20 |
|
5 |
4 |
|||
|
|
|
|
|||
0 |
|
|
|
|
|
|
|
1-5 мкм |
5-10 мкм |
10-15 |
15-20 |
20-25 |
более |
|
|
|
мкм |
мкм |
мкм |
25 мкм |
|
|
Диапазоныразмеров пор, мкм |
|
Рис. 4.41. Гистограмма распределения пор по размерам
Реальные размеры пор, как видно на гистограмме рис. 4.41, от нескольких микрон до десятка микрон, что хорошо коррелирует с результатами расчета. Наибольшее количество пор имеют размеры до 5 мкм. Полученные результаты показывают, что важную роль в процессе формирования оксидного покрытия и образования внутренних дефектов типа пор играет парообразование металла. Фрактальный анализ структуры МДО-покрытия показал большую однородность и упорядоченность структуры внутреннего слоя покрытия и более равномерное распределение пор в нем.
4.10. Фрактальный анализ наноструктурированных материалов
Наноструктурированные (нанофазные) материалы представляют собой вещества с внутренней структурой, имеющей характерные размеры нанометрового масштаба. Структурированные композитные нанофазные материалы имеют характерные особенности и свойства, отлич-
176
ные от свойств веществ, находящихся в обычных объемных фазах. Основой наномасштабной структуры могут быть как наночастицы, так
имолекулярные кластеры, обладающие абсолютной идентичностью.
Внастоящее время при описании структурных свойств материала
он рассматривается как открытая нелинейная система. Свойства материала определяются процессами структурообразования при обмене энергией и веществом с внешней средой. При определенном характере взаимодействия могут формироваться устойчивые регулярные
истохастические самоподобные (фрактальные) структуры на разных масштабных уровнях.
Использование методов фрактального анализа и принципов мультифрактального формализма дает возможность ввести фрактальную параметризацию, характеризовать структурные особенности, отражающие топологию тонкой внутренней структуры рассматриваемых материалов, описать их свойства в понятиях меры и размерности, а также предсказывать физические эффекты, связанные с количественными изменениями фрактальных параметров среды.
Как известно, основным компонентам наноструктурированных наполненных полимеров-матриц, наночастицам и агрегатам частиц присущи фрактальные свойства. Наночастицы из-за их высокой реакционной способности чувствительны к примесям, агломерируют друг с другом при воздействии на систему. Повышение устойчивости наночастиц достигается применением стабилизаторов, в качестве которых используются низкомолекулярные органические соединения и синтетические полимеры.
Вработах А.В. Аксенова (ИРЭ РАН) опытные образцы наноструктурированных металлополимеров получали методом термодеструкции органических солей металлов в растворе-расплаве полимер–масло. На основе физической модели рассмотрены структурные свойства и исследованы электрофизические характеристики металлополимерных нанокомпозитов на основе наночастиц железа и кобальта в полиэтиленовой
ифторопластовой матрицах.
На основе исследования электропроводности наполненного полимерного нанокомпозита в зависимости от процентного содержания наночастиц металла продемонстрировано изменение механизма проводимости. Показано, что изменение диэлектрической проницаемости коррелирует с изменением плотности образцов в зависимости от концентрации наночастиц металла. Кроме того, измерения показали увеличение поглощающей способности наноструктурированного материала с увеличением плотности наночастиц металла в полимерной матрице.
177
В работах А.Н. Чехового показано, что способность металлического материала сопротивляться разрушению зависит не столько от его исходной структуры, сколько от той динамической структуры, которая формируется в процессе нагружения и обусловливает диссипацию энергии. Уникально высокий уровень прочности определяют нанофазы (ансамбли наночастиц), упорядоченные в пространственно-временной гетеросреде, – продукт неравновесных процессов взаимодействия коллективных систем, составляющих твердую фазу.
Информацию об объемном наноструктурировании природа закодировала на начальных этапах эксплуатации огромного количества деталей машин и инструментов в упругопластической области, где в микрообъемах с интенсивной пластической деформацией (ИПД) на структурных концентраторах напряжений идет процесс объемного наноструктурирования. ИПД в открытой неравновесной среде приводит к самоорганизации новых структурных состояний и новых химических соединений, которые, в свою очередь, оказывают определяющее влияние на физико-механические свойства макроструктуры, переводя ее из циклически разупрочняющегося в циклически упрочняющееся состояние.
Последовательность наносостояний можно представить иерархическим рядом: метастабильная матричная фаза кластер (наночастица)ансамбль наночастиц (нанофаза). Например, для мартенсита (М) при малоцикловом упругопластическом нагружении стали:
М→ Fe2,4C → Fe3С → (Fe, Mn)3 С → (Fe, Cr)7 С3 → (Fe, Cr)23 С6 →
→(Fe, W, Mо, Cr, V)6C
На этапе М → ε-фаза, где наблюдается обратное растворение кластеров размером ≈ 1 нм в матричной фазе, ориентационные соотношения несовместимы с классической кристаллографией. Это приводит к некоторой условности понятия когерентности для кристаллических структур, которое предполагает наличие на границах дислокационных стенок, что подтверждено экспериментально. В результате ненасыщенности связей на поверхностных дефектах возможна реконструкция и другой порядок расположения атомов. Скорость cегрегации на дислокациях на несколько порядков выше, чем на границах и это объясняет обратное растворение выделившихся в размерном масштабе ≈ 1 нм кластеров при высокой объемной плотности «свежих» дислокаций ИПД. Адсорбция атомов внедрения на случайно распределенных в матрице зародышах может быть описана универсальной моделью Хэма.
Процессом наноструктурирования можно управлять в точках бифуркации и получать новые структурные состояния с различной иерар-
178

хией самоорганизующихся ансамблей наночастиц не только на этапе эксплуатации, но и в условиях интенсивного силового воздействия на этапе производства. Каждому уровню иерархии присущи свои структурные мотивы, но одним из главных мотивов самоорганизации по принципу снизу–вверх является способность не совместимых по меркам классической кристаллографии фрагментов объединяться в сложные наноструктуры за счет эффектов когерентности на локальных участках ассоциации при целенаправленных воздействиях.
Это позволило в большей мере ис- |
|
|||
пользовать скрытые резервы металли- |
|
|||
ческого материала и на базе традицион- |
|
|||
но используемых получить уникальные |
|
|||
композиционные материалы с нано- |
|
|||
структурными элементами. Ресурс на- |
|
|||
ноструктурированных стали и металло- |
|
|||
керамики повышен до 500 % при ис- |
|
|||
ключительно малых |
энергетических |
|
||
затратах. |
|
|
|
|
Исследование топографии поверх- |
|
|||
ности |
кристаллов |
изоферроплатины |
0 300 600 900 1200 нм |
|
проводилось В.В. Дистлером (рис. 4.42). |
||||
Фрактальный анализ |
показывает, |
Рис. 4.42. Топограмма поверхно- |
||
что |
формообразующими |
элементами |
сти природной изоферроплатины |
пакета являются 3 типа полигональных наноблоков с линейными размерами 30, 50, и 100 нм. Для соотношения
характерных масштабов конкретных структур выполняется числовая последовательность Фибоначчи.
Кроме того, фрактальный анализ применим для оценки структурного состояния материалов, содержащих наноструктурные элементы: композиционных металлополимерных материалов, нанокерамических композиций на основе ZrO2, наноструктурных полупроводниковых материалов, наноразмерных ионно-плазменных покрытий Ti-Zr-N, Ti-Al-N, Ti-B-Si-N и др.
Контрольные вопросы
1.В чем преимущество использования теории фракталов в материаловедении?
2.Что изучает синергетика?
3.В чем отличие самоорганизации структур?
179
4.Что называется фракталом, что такое фрактальные структуры?
Вчем заключаются основные свойства фракталов?
5.Что такое фуллерены?
6.Что такое диссипативные структуры?
7.Классификация фракталов. Что такое геометрические и естественные фракталы?
8.Что такое фрактальная размерность. В чем ее отличие от геометрической размерности?
9.Приведите основное соотношение между геометрической характеристикой фрактала и фрактальной размерностью.
10.Приведите примеры известных геометрических фракталов.
11.Приведите примеры естественных фракталов.
12.Что делает структуру металла объектом фрактального анализа?
13.Чему равны евклидовы размерности d и энергии микроструктурных элементов: атомов, дислокаций, границ зерен?
14.Фрактальные мартенситные и дендритные структуры?
15.Приведите схему преобразования структуры чечевицеобразного мартенсита с использованием структурных параметров.
16.Как построить регулярный треугольный ковер Серпинского для моделирования процесса мартенситного превращения?
17.Как выглядит фрактальная модель высокодисперсных дендритных частиц железа?
18.Что такое фрактальная мера? Приведите основное соотношение между мерой и фрактальной размерностью.
19.Как осуществляется выбор меры для фрактального анализа структур металла сварных швов?
20.В чем заключается алгоритм метода сеток и метода точек?
21.Преимущества и недостатки алгоритмов расчета фрактальной размерности по методу сеток и методу точек.
22.Общая характеристика видманштеттовой структуры: морфологические признаки и температурный интервал образования.
23.Алгоритм фрактального анализа видманштеттовой структуры.
24.Взаимосвязь фрактальной размерности структуры с уровнем свойств металла шва.
25.Как может быть введена фрактальная размерность в задачи оптимизации состава электродного покрытия?
26.Преимущества применения фрактального подхода для анализа поверхности усталостного разрушения.
27.Особенности выбора меры для анализа трехмерных обьектов.
28.В чем заключается особенность обработки изображения поверхности усталостного разрушения?
180