
книги / Теория сварочных процессов
..pdf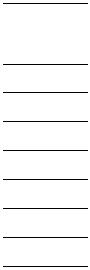
101
Таблица 3.1
Состав шлака и шлаковых включений в металле при дуговой сварке
|
Электорд |
|
Состав шлака, % |
|
|
|
Шлаковые включения |
|
|
||||||
|
|
|
|
|
|
|
|
|
|
|
|
|
|
|
|
|
|
|
|
|
|
|
|
|
|
|
|
состав, % |
|
||
|
или флюс |
SiO2 |
MnO |
TiO |
FeO |
CaO |
Al |
O |
|
Характеристика |
колич., % |
|
|
||
|
3 |
|
|
|
|
||||||||||
|
|
|
|
|
|||||||||||
|
|
|
|
2 |
|
|
2 |
|
|
|
SiO2 |
MnO |
FeO |
Al2O3 |
|
|
|
|
|
|
|
|
|
|
|
|
|
||||
|
Ц-3 |
37 |
14 |
12 |
18 |
8,1 |
– |
|
Крупные |
0,02 |
46 |
20 |
28 |
4 |
|
|
|
|
|
|
|
|
|
|
|
0,03 |
|
|
|
|
|
|
ОММ-5 |
27 |
29 |
15 |
13 |
3,6 |
– |
|
Крупные |
23 |
32 |
14 |
5 |
||
|
|
Дисперсные |
0,08 |
52 |
9 |
8 |
1 |
||||||||
|
|
|
|
|
|
|
|
|
|
||||||
|
|
|
|
|
|
|
|
|
|
0,02 |
|
|
|
|
|
|
УОНИ-13/55 |
31 |
4,5 |
2,2 |
7,9 |
42 |
– |
|
Крупные |
40 |
28 |
14 |
8 |
||
|
|
Дисперсные |
0,01 |
27 |
28 |
28 |
7 |
||||||||
|
|
|
|
|
|
|
|
|
|
||||||
|
|
|
|
|
|
|
|
|
|
|
0,04 |
|
|
|
|
|
ОСЦ-45 |
38 |
43 |
– |
4,7 |
1,8 |
1,4 |
|
Включения флюса |
74 |
11 |
11 |
2 |
||
|
|
|
0,03 |
|
|
|
|
||||||||
|
|
Включения шлака |
68 |
10 |
15 |
2 |
|||||||||
|
|
|
|
|
|
|
|
|
|
|
|
|
|
|
|
|
|
|
|
|
|
|
|
|
|
|
|
|
|
|
|
101

1)способности шлаковых частиц к коагуляции, т.е. укрупнению путем слияния;
2)скорости всплывания шлаковых частиц в жидком металле. Способность шлаковых частиц к коагуляции в свою очередь за-
висит от температуры металла, поверхностного натяжения на границе шлаковая частица – жидкий металл, вязкости как включений, так и жидкого металла, и др. Чем выше температура металла и поверхностное натяжение частиц, меньше их вязкость, тем легче протекает их коагуляция. Тугоплавкие включения, имеющие повышенную вязкость, плохо коагулируют и поэтому распределяются в металле в дисперсном
виде (SiO2; А12О3).
Скорость всплывания шлаковых частиц зависит от их размера, вязкости жидкого металла, разницы в удельном весе частицы и металла и др. Эту скорость приближенно можно определить с помощью формулы Стокса:
V = 2r 2 (γж.м − γш ) g , 9η
где r – радиус частицы; (γж.м − γш) – разность в плотности жидкого ме-
талла и шлаковой частицы; η – вязкость жидкого металла; g – ускорение силы тяжести .
Как видим, скорость всплывания частиц тем больше, чем крупнее частица, меньше ее плотность и вязкость металла, в котором она движется. С этой точки зрения нежелательны мелкодисперсные слабокоа-
гулирующие включения (SiO2; А12О3), обладающие малой скоростью всплывания и загрязняющие металл.
На скорость всплывания шлаковых частиц заметно влияет наличие конвективных потоков в металле, выделение из металла пузырей, перемешивающих металл и увлекающих шлаковые частицы к поверхности металлической ванны. Значительная часть шлаковых частиц выталкивается к поверхности сварочной ванны растущими кристаллитами металла шва.
Распределяются шлаковые включения в металле по-разному. Эвтектики, образуемые этими включениями с металлом или между собой, располагаются по границам зерен в виде прослоек или точечных скоп-
лений (рис. 3.13, а).
Шлаковые включения в виде самостоятельных фаз (рис. 3.13, б) могут иметь различную форму: 1 – групповые дисперсные включения глобулярной формы; 2 – игольчатые включения различной величины; 3 – отдельные крупные включения – глобулярные, веретенообразные и др. По внешнему виду (форме, окраске) шлаковые включения могут быть отнесены к тому или иному типу (рис. 3.14, табл. 3.2).
102
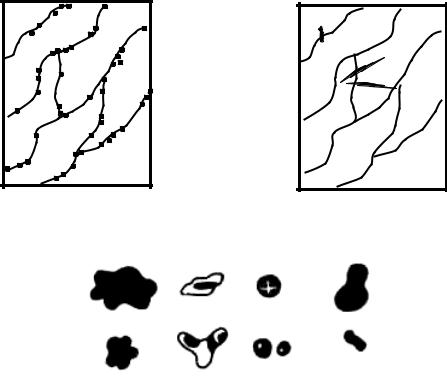
3
2
1
a |
б |
Рис. 3.13. Схема распределения возможных шлаковых включений
а |
б |
в |
г |
Рис. 3.14. Типы неметаллических включений в сварных швах: а – силикаты (изотропные); б – силикаты железа (анизотропные); в – силикаты с преобладанием марганца (изотропные, внутри светящийся крест); г – сульфиды, оксиды и пр. (изо-
тропные)
|
|
Типы включений |
Таблица 3.2 |
||
|
|
|
|||
|
|
|
|
|
|
Включения |
|
Характеристика включений |
|
||
Форма |
Цвет в отраженном свете |
Изменение |
|||
|
|
|
обычном |
поляризованном |
свойств |
Силикаты |
с пре- |
Непра- |
Черные или |
Светящиеся раз- |
Изотроп- |
обладанием железа |
вильная |
прозрачные |
личных цветов |
ное или |
|
|
|
|
|
|
анизо- |
|
|
|
|
|
тропное |
Силикаты марганца |
Круглая |
Черные |
Темные, внутри |
Изотроп- |
|
|
|
|
|
светящийся |
ное |
|
|
|
|
крест |
|
|
|
|
|
|
|
Сульфиды, |
оксиды |
Непра- |
– » – |
Черные |
– » – |
и др. |
|
вильная |
|
|
|
|
|
|
103 |
|
|
Форма и величина шлаковых включений оказывают заметное влияние на механические и физические свойства металла.
Крупные остроугольные включения (> 5 мкм) снижают выносливость металла – предел усталости. Мелкие включения (> 5 мкм) округлой формы не влияют на предел прочности и пластичности при статических испытаниях, а также на предел усталости металла, но увеличение их сопровождается некоторым снижением ударной вязкости и повышением склонности швов к кристаллизационным трещинам.
Выделение включений FеО, FеS и других по границам зерен, особенно в виде сплошных прослоек, придает металлу хрупкость, иногда красноломкость. Посторонние включения заметно уменьшают коррозионную стойкость металла. Однако мельчайшие, субмикроскопические включения, равномерно распределенные в металле (например ТiO2; А12О3), могут быть и полезными, так как они становятся дополнительными центрами кристаллизации и способствуют измельчению структуры.
3.4. Ликвация в металле сварного шва
Ликвацией называется неравномерное распределение элементов, химических соединений и других составляющих в металле. К числу сильно ликвирующих элементов относятся углерод, сера и фосфор.
В металле шва наблюдаются преимущественно два вида ликвации – дендритная и зональная. В свою очередь д е н д р и т н а я л и к в а ц и я может быть двух видов – внутри- и межкристаллитная.
Природа внутрикристаллитной |
ликвации связана |
с наличием |
у сплава интервала кристаллизации |
и с различной для |
центральной |
и периферийной частей кристалла степенью обогащения ликвирующими элементами. Началу кристаллизации сплава заданного состава А–А отвечает температура Тл. В первую очередь кристаллизуется металл вдоль осей будущих кристаллов, содержащий минимальное количество примесей и близкий по составу к исходному (точка Б). При снижении температуры оси обрастают кристаллизующимся металлом. Эти участки постепенно обогащаются примесями, которые особенно сильно насыщают последние порции металла (точка В). Поэтому центральные части (темные) образовавшихся столбчатых кристаллов, имеющих дендритное строение (рис. 3.16, б), близки по своему составу к чистому металлу, а периферийные (светлые) обогащены примесью. Такое строение шва – проявление внутрикристаллитной ликвации.
Степень m развития внутрикристаллитной ликвации зависит от скорости охлаждения металла (рис. 3.17).
104
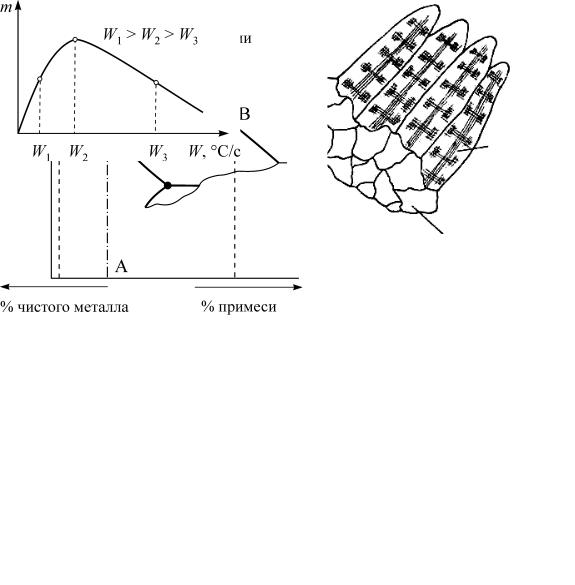
Металл
шва
Основной
металл
а |
б |
Рис. 3.16. Схема возникновения внутрикристаллитной ликвации (а) и дендритное строение металла шва (б)
В диапазоне малых скоростей их нарастание до определенного предела вызывает увеличение ликвации, протекающей по законам диффузионной кристаллизации. С дальнейшим ростом скорости охлаждения внутрикристаллитная ликвация снижается, так как процесс кристаллизации приобретает бездиффузионный характер. Если принять скорость диффузионного роста кристалла рав-
ной величине порядка ~103 см/мин, то при скорости роста столбчатых
Рис. 3.17. Зависимость скорости W охлаждения сплава при кристаллизации от степени m развития внутрикристаллитной ликвации
кристаллов в большей части объема ванны порядка 10…102 см/мин будет действовать, по-видимому, главным образом механизм бездиффузионной кристаллизации, приводящей к уменьшению внутрикристаллитной ликвации. Поэтому следует считать, что в общем случае в сварных швах эта ликвация выражена слабо.
Межкристаллитная ликвация |
является |
результатом оттеснения |
к границам растущих кристаллов |
различных |
легкоплавких эвтектик |
и примесей, создающих межкристаллитные прослойки. Последние препятствуют перемещению диффундирующих атомов и тем самым сохра-
105
няют дендритную неоднородность металла шва. Особую опасность представляют располагающиеся здесь легкоплавкие эвтектики типа сернистых.
З о н а л ь н а я л и к в а ц и я вызывается неодновременной кристаллизацией периферийной и центральной частей шва. По мере роста кристаллитов остающаяся жидкость оттесняется в центральную область шва и оказывается наиболее загрязненной различными вредными примесями. Этот участок шва называется зоной слабины. Здесь при неблагоприятных условиях могут появляться трещины.
Весьма заметна зональная ликвация в однослойных швах большого сечения в сварочной ванне первого типа. В меньшей мере это касается металла ванны II типа: несмотря на большое сечение однопроходных швов и крупностолбчатое строение металла, в них можно устранить плоскость встречи торцов кристаллитов (транскристаллизацию), т.е. избежать ликвации. Однако в таких швах наблюдается дендритная ликвация.
Ликвация в сварных швах (особенно зональная и межкристаллитная дендритная) снижает механические свойства металла, так как ослабляет связь между кристаллитами и служит одной из причин появления кристаллизационных трещин.
3.5. Методы регулирования первичной кристаллизации сварных швов
Первичная структура шва оказывает большое влияние на многие свойства наплавленного металла, особенно если в последующем он не подвергается термической обработке, прокатке или ковке. Поэтому важно, чтобы первичная структура была мелкозернистой и по возможности равноосной, с незначительной химической неоднородностью. Тогда свойства металла будут достаточно высокими и без последующей обработки. Рассмотрим пути регулирования процессов первичной кристаллизации.
1. Для уменьшения химической неоднородности и повышения стойкости металла к образованию кристаллизационных трещин нужно правильно подбирать соотношения между глубиной Н и шириной В сварочной ванны.
Коэффициент формы ванны
ψ = В/Н
зависит от многих факторов – способа и режима сварки, состава металла, сварочных материалов и т.д.
Узкая и глубокая ванна I типа (ψ < 2) создает неблагоприятную для кристаллизации металла схему (рис. 3.18, а). Здесь кристаллы, растущие
106
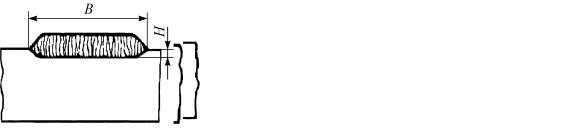
по нормали к поверхности охлаждения, неизбежно встречаются в центральной части шва, образуя зону слабины. Поэтому швы, кристаллизующиеся по указанной схеме, склонны к образованию кристаллизационных трещин. Из такой ванны посторонние примеси удаляются труднее. Наоборот, в широкой и неглубокой ванне (ψ > 2) условия для кристаллизации значительно лучше, так как последние порции жидкого металла, наиболее загрязненные примесями, оказываются вытесненными растущими кристаллами в самую верхнюю часть шва и не создают в металле опасной зоны слабины (рис. 3.18, б).
а |
б |
в |
Рис. 3.18. Влияние формы ванны I типа на расположение в шве ликвирующих примесей
Однако дальнейшее увеличение ширины ванны, т.е. увеличение ψ = В/Н (рис. 3.18, в), вновь усиливает опасность образования кристаллизационных трещин вдоль шва. Это объясняется большой абсолютной величиной поперечной усадки широких швов, концентрацией деформаций в средней части валика и неблагоприятным расположением дендритов. В сварочной ванне II типа (рис. 3.19) столбчатые кристаллы, растущие в радиальном направлении, в зависимости от коэффициента формы встречаются друг с другом торцами (а), под тупым (б) или под острым (в) углом. Но кристаллы могут расти и в осевом направлении и, изгибаясь, встречаться только боковыми гранями (г). Первым двум случаям (см. рис. 3.19, а, б) отвечает малое значение коэффициента формы (ψ > 0,8…1,5). Такие швы более склонны к образованию кристаллизационных трещин и больше загрязняются неметаллическими включениями.
Швы, где кристаллы встречаются друг с другом под острым углом (см. рис. 3.19, в), имеют средний коэффициент формы (ψ = 2) и обладают более высокой стойкостью к образованию кристаллизационных трещин. Лучшая форма ванны – чашеобразная (ψ = 3). В ней кристаллы растут в осевом направлении (см. рис. 3.19, г) и не встречаются друг с другом торцами. Ориентируясь на оптимальную форму ванны, а значит, и сечения шва, можно получить наиболее благоприятное расположение столбчатых кристаллов.
107
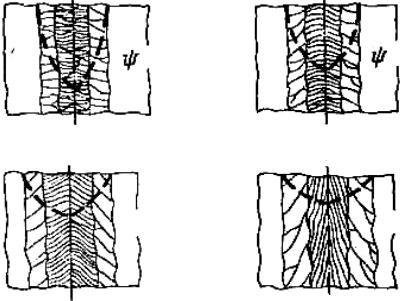
|
|
ψ = 1,5 |
ψ = 0,8 |
||
|
|
|
|
|
|
а |
б |
ψ = 2,0 |
|
ψ = 3,0 |
|
|
|
в |
г |
Рис. 3.19. Изменение направления роста столбчатых кристаллов в зависимости от коэффициента формы сварочной ванны второго типа
2. Чтобы получить металл высокой прочности и пластичности, стойкий к возникновению кристаллизационных трещин, нужно измельчать его грубую столбчатую структуру. Этого достигают различными способами. Рассмотрим некоторые из них:
а) введение в сварочную ванну элементов-модификаторов (B; Ti; V; Nb; Zr и др.). Эти поверхностно-активные вещества снижают энергию образования зародышей – центров кристаллизации – и повышают их устойчивость. Одновременно, располагаясь на поверхности кристаллов, они снижают их поверхностную энергию, что также ограничивает рост кристаллов;
б) введение в сварочную ванну элементов, способствующих образованию избыточных фаз типа твердого раствора (α-фаза);
в) воздействие на сварочную ванну ультразвуковых колебаний, механических вибраций или электромагнитное перемешивание металла ванны;
г) измельчение структуры металла швов путем искусственного повышения скорости охлаждения кристаллизующейся ванны.
108
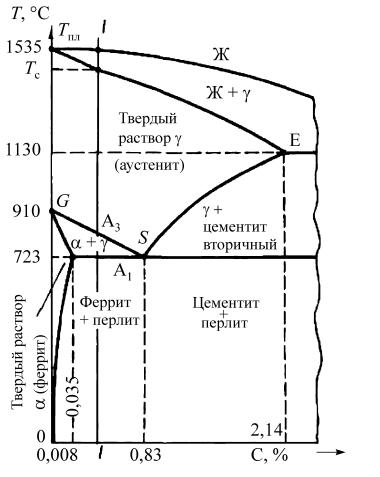
3.6.Процессы вторичной кристаллизации в металле шва
ив основном металле
Вторичная кристаллизация в металле шва. Как установлено ранее,
процесс первичной кристаллизации в сварочной ванне сплава 1–1 (малоуглеродистая сталь) заканчивается достижением температуры Тс (рис. 3.21). Металл приобретает аустенитную структуру γ-Fе, но аустенитные зерна образуются в пределах первичных столбчатых кристаллов.
Рис. 3.21. Упрощенная диаграмма состояния железо–углерод (левый угол)
Сдальнейшим понижением температуры структурные изменения
вметалле не наблюдаются вплоть до температуры, отвечающей началу
перекристаллизации (точка А3). Последующие структурные превращения в твердой фазе относятся к процессам вторичной кристаллизации металла. Как видно на рис. 3.21, для сплава 1–1 вторичная кристаллизация металла начнется при температуре ТА3 и будет протекать до темпе-
ратуры ТА1, отвечающей эвтектоидному превращению. В соответствии
109
с равновесными превращениями при температуре, отвечающей точке А3, начинается выделение из аустенита ферритной составляющей α-Fe (в результате полиморфного превращения γ → α). По мере выделения феррита оставшийся аустенит будет обогащаться углеродом в соответствии с кривой GS и при температуре ТА1 произойдет распад его на ме-
ханическую смесь феррита (α-Fe) и цементита (Fe3C), содержащую 0,83 % С и известную под названием перлита.
Высокие скорости охлаждения, свойственные сварочному циклу, влияют на характер превращений в наплавленном металле, и поэтому конечные структуры отличаются от равновесных. Можно отметить следующие общие особенности вторичных превращений в наплавленном металле:
1)избыточный феррит успевает выделиться из аустенита не весь
ипоэтому к моменту эвтектоидного превращения последний содержит
< 0,83 % С;
2)в результате эвтектоидного превращения образуется несколько большее количество перлита с меньшим содержанием углерода, чем при равновесных превращениях;
3)перлит имеет более тонкое строение.
Скорость охлаждения металла шва во времени — величина крайне непостоянная. В начальный момент, после прохождения дугой исследуемого участка металла, скорость охлаждения достигает 200–300 °С/с, а с течением времени быстро снижается. Наибольшее влияние на структуру металла шва оказывает скорость охлаждения в интервале температур наименьшей устойчивости аустенита. Принято считать, что она примерно равна мгновенной скорости охлаждения при средней температуре данного интервала. В частности, для малоуглеродистой стали эта температура 550 °С.
Рассмотрим на примере, как влияет скорость охлаждения металла шва на его структуру, а следовательно, и свойства.
Автоматической сваркой под флюсом были выполнены два шва, причем шов № 1 охлаждался очень медленно, а шов № 2 – быстро. Для металла с содержанием 0,22 % С, охлаждаемого в соответствии с равновесной диаграммой состояния Fe–Fe3C, количество перлита должно составлять примерно 12 %. По-видимому, для шва № 1 были созданы условия охлаждения, близкие к равновесным, так как он также содержит примерно 12 % перлита (рис. 3.22, а). Шов № 2, остывавший с большей скоростью (более типичной для сварки), содержит около 50 % перлита (рис. 3.22, б) и с более тонким строением. В обоих случаях металл шва сохранил столбчатую направленность кристаллитов и дендритов, однако особенно характерно это для шва № 2. Благодаря увеличению пер-
110