
книги / Теория сварочных процессов
..pdf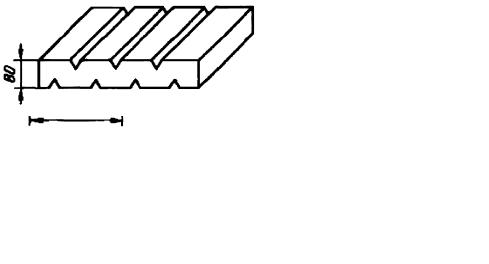
для дуговой сварки и 10...40 мм для лучевой независимо от толщины. Особенность сварки образцов заключается в том, чтобы закрепление входных и выходных планок не препятствовало раскрытию зазора. Сварка начинается с образцов большей ширины и заканчивается на образцах, в швах которых образуются ГТ.
а |
б |
в |
г |
Рис. 5.12. Схемы конструкции образцов технологических проб: а – с круговым швом; б – таврового; в – с переменной шириной пластин; г – со швом в канавку
Образец с канавками (см. рис. 5.12, г) изготовляют из пластин толщиной >40 мм. При толщине <60 мм он приваривается к жесткой плите по флангам швом с катетом 20 мм. Канавки выполняют с шагом 100 мм, при толщине образца >70 мм – с двух сторон. Они могут иметь V- и U-образную форму пазов.
При наличии ГТ металл сварного соединение считают склонным к образованию трещин. Относительную степень склонности к ГТ (см. рис. 5.12, а, б) оценивают суммарной длиной трещин по длине шва или в трех сечениях шва. При испытании образцов с переменной шириной (см. рис. 5.12, в) склонность к ГТ определяют по максимальной ширине образцов, в которых образуются трещины. При испытании пробы с канавками (см. рис. 5.12, г) за критерий склонности к ГТ принимают максимальную скорость сварки, при которой в швах начинают образовываться трещины.
Проба Холдкрофта (рис. 5.13) («рыбья кость») оценивает (качественно) сопротивляемость образованию горячих трещин при сварке тонких листов.
Образцом является пластина с боковыми прорезями увеличивающейся длины. На образец производится наплавка или проплавление
201
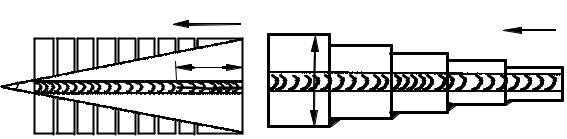
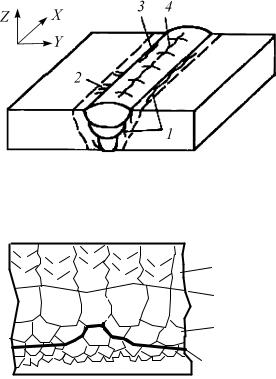
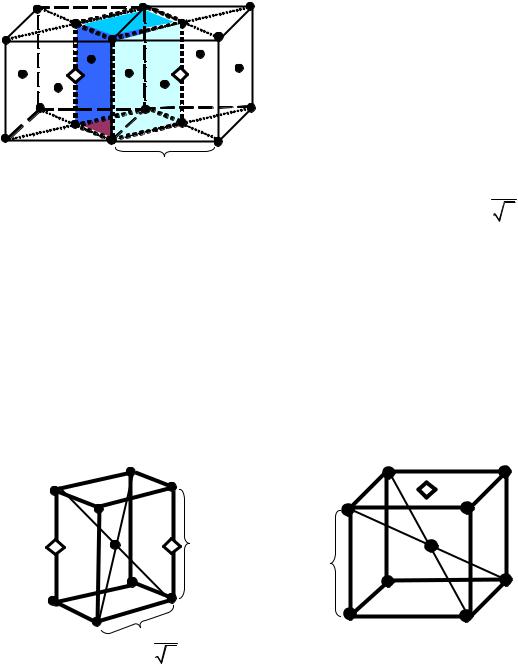
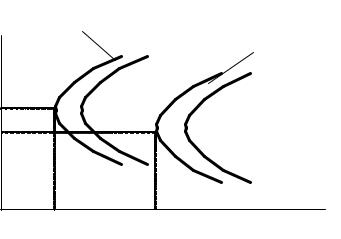
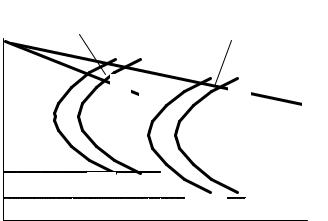
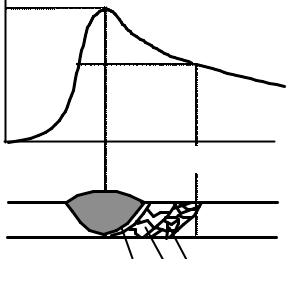

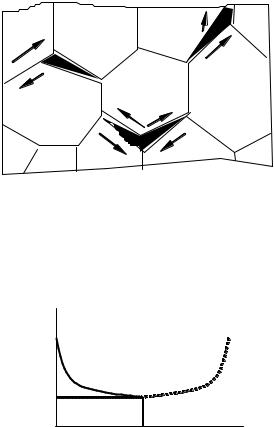
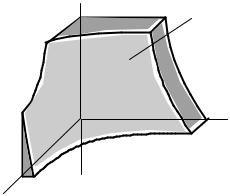