
книги / Теория сварочных процессов
..pdf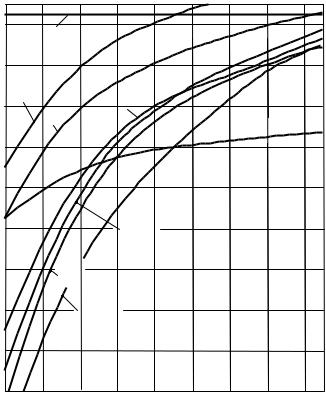
Обратная реакция – это реакция диссоциации оксида:
2МеО 2Ме + О2. Константа равновесия этой реакции
K |
|
|
a 2 |
P |
|
р |
= Me |
O2 , |
|||
|
|
aMeO2 |
|
||
|
|
|
где aMeO и aMe – активности (концентрации) металла и оксида металла; PO2 – парциальное давление кислорода, выделяющегося при диссо-
циации оксида МеО.
Металл и оксид являются конденсированными фазами постоянного состава, поэтому aMeO = aMe = 1. Тогда константа равновесия будет
определяться только парциальным давлением кислорода Kр = PO2 . Это
парциальное давление кислорода, выделяющегося при диссоциации оксида МеО, называется упругостью диссоциации оксида или сродством металла к кислороду.
Зависимость упругости диссоциации оксидов от температуры графически строится в логарифмических координатах lg PO2 – T (рис. 2.11).
lgPO2
|
воздух |
|
-6 |
|
|
-10 |
NiO |
MnO |
|
FeO |
CO |
-14 |
|
|
|
|
|
-18 |
|
|
-22 |
|
SiO2 |
|
|
-26
TiO2 -30 Al2O3
-34
-38
1000 |
1600 |
2200 |
2800 |
3400 T, К |
Рис. 2.11. Зависимость упругости диссоциации оксидов от температуры
41
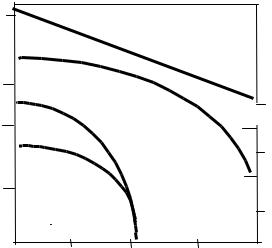
Там же отмечается горизонтальная прямая упругости диссоциации воздуха. Чем меньше PO2 , тем больше срoдство металла к кислороду, т.е.
тем легче металл окисляется.
Например, при 1600 К парциальное давление кислорода, выделяющегося из MnO, меньше, чем парциальное давление кислорода, выделяющегося из FeO. Следовательно, химические сродство к кислороду у железа меньше, чем у марганца. При 1600 К и равных молярных концентрациях марганец будет раскислять железо. Если линия упругости диссоциации оксида металла пересекает линию воздуха, то данный металл окисляться на воздухе не будет (например никель при температурах выше 2300 К).
С ростом температуры упругость диссоциации оксидов увеличивается, т.е. сродство металлов к кислороду уменьшается и, следовательно, стойкость оксидов уменьшается. Чем ниже расположена кривая lg PO2 ,
тем прочнее оксид и тем более сильным раскислителем будет металл. Таким образом, наиболее высоким сродством к кислороду обладают Al, Ti, Si и т.д.
При температурах выше 2400 К самым сильным раскислителем для металла сварочной ванны будет являться углерод. Сродство к кислороду у углерода при повышении температуры не убывает, как у металлов, а увеличивается. Таким образом, углерод является раскислителем только на стадии капли, а в центральной и хвостовой части сварочной ванны раскисляющая роль углерода незначительна.
Влияние кислорода на свойства стали всегда отрицательно
(рис. 2.12).
σВ, σ02, |
400 |
σB |
|
МПа |
|
||
|
|
σ02 |
KСV |
|
300 |
|
|
|
|
Дж/см2 |
|
|
200 |
KCV |
HB, МПа300 |
|
HB |
1000 |
|
|
|
200 |
|
|
|
|
800
100
100
0,010 0,020 0,030 |
[О], % |
Рис. 2.12. Влияние кислорода, содержащегося в низкоуглеродистой стали, на ее свойства
42

Кислород, находясь в стали в любых формах, снижает все ее механические свойства. Понижаются пределы прочности σB и текучести σ02,
твердость HB и, в особенности, ударная вязкость ak. Кроме того, уменьшается стойкость против коррозии, появляется склонность к хладноломкости, красноломкости и старению. У стали усиливается рост зерна при нагреве, ухудшается обрабатываемость резанием и ковкой, понижается магнитная проницаемость и увеличивается электрическое сопротивление.
Для снижения содержания кислорода в металле сварного шва применяют специальные меры (см. подразд. 2.7).
2.5.4. Взаимодействие металлов с водородом при сварке
Источникам водорода в газовой фазе зоны сварки могут служить атмосферная влага, влага покрытия электрода или флюса, кристаллизационная влага ржавчины на свариваемых кромках и т.д. В зависимости от температуры газовой фазы водород может находиться в ней в различных состояниях: молекулярном, атомарном и ионизированном. Из данных подразд. 2.5.1 следует, что в столбе дуги (температура Т = = 5000…6000 К) практически весь водород находится в атомарном состоянии.
По характеру взаимодействия с водородом металлы делятся на две группы:
–металлы, растворяющие водород, но не образующие гидридов.
Это Fe, Ni, Al, Co, Cu, Mo, Pt;
–металлы, образующие и твердые растворы, и гидриды. Это Zr, Ti, V, Ta, Th, Nb.
Растворимость атомарного водорода в металле при постоянной температуре в состоянии равновесия подчиняется закону Генри. Константа Генри растворимости водорода K зависит от температуры:
lg KН = −1745T −1,72 .
Растворимость водорода в железе с повышением температуры растет и изменяется скачкообразно при температурах полиморфных превращений (см. рис. 2.9). При температуре плавления растворимость водорода резко возрастает. Максимум растворимости наблюдается при температуре 2400 °С, таким образом наибольшее насыщение железа водородом при сварке происходит на стадии капли.
Водород существенно ухудшает свойства сварных соединений. Он уменьшает пластичность металла сварного шва, способствует хрупкому
43
разрушению. Это явление получило название «водородной хрупкости». Заключается оно в следующем. При охлаждении металла сварочной ванны растворенный атомарный водород не успевает выделится в атмосферу. Оставшийся в металле шва, он задерживается на микронесплошностях (дефектах кристаллической решетки, включениях) и воссоединяется в молекулы. Образуется водородное скопление с большим давлением. В металле шва возникает многоосное напряженное состояние, приводящее к снижению пластичности, вязкости и к хрупкому разрушению. Значительные напряжения приводят к появлению микронадрывов – флокенов.
Кроме того, распределение водорода в сварных соединениях неравномерно, локальные концентрации его во много раз выше допустимой. Водород скапливается на линии сплавления металлов, по зоне термовлияния, вызывает появление пор, трещин в этих областях. Особенно склонны к водородной хрупкости титановые сплавы и высокопрочные стали.
Для снижения содержания водорода в сварных соединениях принимают ряд определенных мер. Во-первых, необходимо удалить источники водорода при сварке, а именно прокаливать электроды, флюсы, зачистить кромки изделий перед сваркой и т.д. Во-вторых, следует связать водород в летучий фтористый водород добавкой флюорита в электродное покрытие или флюс. При этом последовательно осуществляются следующие реакции:
2CaF2 + 3 SiO2 SiF4 + 2 CaSiO3;
SiF4 + 3H SiF + 3HF↑.
И, в-третьих, к снижению содержания водорода приводит изотермическая выдержка при 20 °С. Данные табл. 2.4 свидетельствуют о том, что через 2–3 суток после сварки диффузионный водород из низколегированной стали практически выходит, а молекулярный водород остается в ней.
Таблица 2.4 Кинетика удаления водорода при 20 °С из металла сварного шва
Тип металла |
Содержание водорода в металле шва, см3/100 г |
|||||||
сразу по- |
|
после сварки через (ч) |
|
|||||
шва |
|
|
||||||
сле сварки |
5 |
20 |
45 |
75 |
120 |
840 |
||
|
||||||||
Ферритный на |
6,2 |
5,4 |
4,3 |
3,4 |
1,1 |
1,8 |
– |
|
стали Ст.3 |
|
|
|
|
|
|
|
|
Аустенитный на |
7,6 |
– |
7,6 |
7,4 |
– |
6,7 |
6,8 |
|
стали Х23Н18 |
|
|
|
|
|
|
|
44
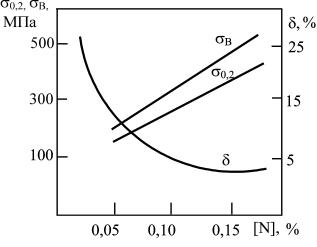
2.5.5. Взаимодействие металлов с азотом при сварке
Основной источник азота при сварке это воздух. Азот диссоциирует при более высокой температуре, чем водород и кислород (см. подразд. 2.5.1) и поэтому при сварке большая часть азота находится в молекулярной форме.
Азот нерастворим в таких металлах, как Au, Cu, Ag. В других металлах азот растворяется, образуя твердые растворы и нитриды.
Наиболее стойкие нитриды образуются при взаимодействии азота с титаном (TiN), молибденом, ниобием, хромом, марганцем. Железо также образует нитриды Fe2N, Fe4N. Указанные нитриды образуются в объеме зерен, увеличивают прочность, но резко снижают пластичность, ударную вязкость и коррозионную стойкость.
При кристаллизации железа растворимость азота скачкообразно уменьшается. Газ выходит из раствора и образует поры. Кроме того, скачок растворимости появляется и при температурах полиморфных превращений (см. рис. 2.9).
Рис. 2.13. Влияние концентрации азота в низкоуглеродистой стали на ее механические свойства
Азот, содержащийся в металле сварного шва, влияет на его свойства. На рис. 2.13 показано, что в результате повышения содержания
азота:
−повышается предел прочности, предел текучести, твердость;
−снижается ударная вязкость и пластичность;
−появляется склонность к старению, хладноломкости, синелом-
кости;
−увеличивается способность к закалке стального шва.
45
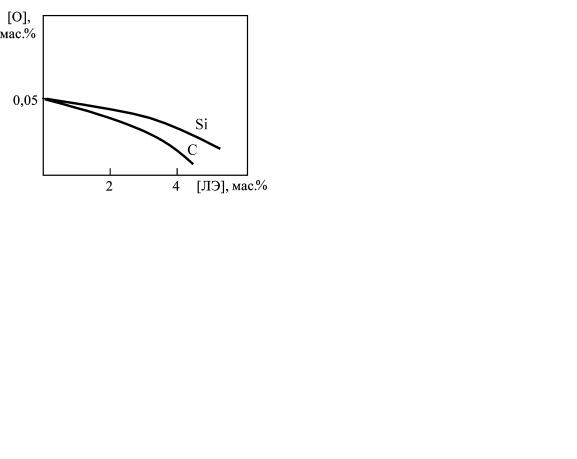
С этой точки зрения азот является нежелательной примесью. Однако положительное влияние азота на прочностные характеристики позволяет использовать его как легирующий элемент. Например, в стали 16Г2АФ содержится до 0,02 % азота. Кроме того, при сварке высоколегированных сталей азот повышает устойчивость аустенита и тем самым служит заменой никеля.
2.5.6.Влияние легирующих элементов на растворимость газов
вметалле сварного шва
Легирующие элементы стали способны существенно влиять на растворимость газов в основном металле.
Особенно сильно снижают растворимость азота в жидком железе такие элементы, как титан, углерод и кремний. Ванадий, ниобий и хром, наоборот, способствуют повышению растворимости азота в стали
(рис. 2.14, а).
а |
б |
в
Рис. 2.14. Влияние легирующих элементов на содержание: а – азота, б – водорода, в – кислорода в стали
46
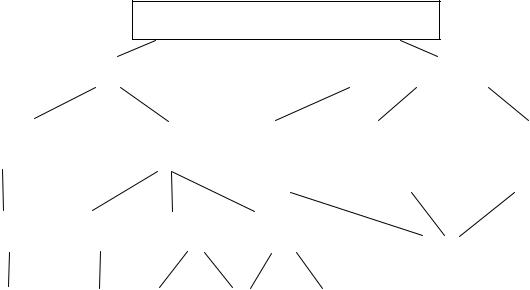
Снижению содержания водорода в стальном шве способствуют алюминий, углерод, также примесь кислорода. Титан, ниобий, марганец и другие повышают растворимость водорода в шве (рис. 2.14, б).
На снижение растворимости кислорода в стали при сварке благоприятно влияет увеличение содержания кремния и углерода
(рис. 2.14, в).
2.5.7. Защита металла сварного шва от взаимодействия с газами
Для предотвращения рассмотренных взаимодействий металла шва с газами в зоне дуги применяют защитные газовые, шлаковые, газошлаковые и вакуумные среды (рис. 2.15).
Способы защиты металла при дуговой сварке
|
|
|
|
физические |
|
|
|
|
|
|
|
|
|
|
|
физико-химические |
|
|
|||||||||||
|
|
|
|
|
|
|
|
|
|
|
|
|
|
|
|
|
|
|
|
|
|
|
|
|
|
|
|
|
|
|
|
|
|
|
|
|
|
|
|
|
|
|
|
|
|
|
|
|
|
|
|
|
|
|
|
|
|||
|
Удаление |
|
|
Вытеснение |
|
|
|
|
Уменьшение |
Усиление вы- |
|
Уменьшение |
|||||||||||||||||
|
воздуха |
|
|
|
|
|
воздуха |
|
|
|
растворимости |
деления [O] и |
|
вред. влияния |
|||||||||||||||
|
|
|
|
|
|
|
|
|
[O] и [N] в жид- |
[N] из жидкого |
|
[O]и [N] в твер- |
|||||||||||||||||
|
|
|
|
|
|
|
|
|
|
|
|
|
|
|
|
|
|||||||||||||
|
|
|
|
|
|
|
|
|
|
|
|
|
|
|
|
|
ком металле |
|
металла |
|
дом металле |
||||||||
|
|
|
|
|
|
|
|
|
|
|
|
|
|
|
|
|
|
|
|
|
|
|
|
|
|
|
|||
создание |
|
|
|
|
парами |
|
|
газами |
|
|
|
шлаками |
|
|
|
|
|
|
|
|
|
||||||||
|
вакуума |
|
|
|
|
|
|
|
|
|
|
|
|
|
|
|
|
|
|
|
|
|
|
|
|
|
|
|
|
|
|
|
|
|
|
|
|
|
|
|
|
|
|
|
|
|
|
|
|
|
|
|
Сварка открытой |
|
|||||
|
|
|
|
|
|
|
|
|
|
|
|
|
|
|
|
|
|
|
|
|
|
|
|
|
|
||||
|
|
|
|
|
|
|
|
|
|
|
|
|
|
|
|
|
|
|
|
|
|
|
|
|
дугой сплошны- |
|
|||
|
Сварка в |
|
|
Сварка в |
|
Сварка в |
|
|
Сварка по- |
|
Сварка |
|
|
ми проволоками |
|
||||||||||||||
|
вакууме |
|
водяном |
|
защитных |
|
|
|
крытыми |
|
|
под |
|
|
|
|
|
|
|
||||||||||
|
|
|
|
|
|
|
|
|
|
|
|
|
|||||||||||||||||
|
|
|
|
паре, па- |
|
газах, ар- |
|
электродами, |
|
флюсом |
|
|
|
|
|
||||||||||||||
|
|
|
|
рах ме- |
|
гоне, ге- |
|
порошковы- |
|
|
|
|
|
|
|
|
|
|
|
||||||||||
|
|
|
|
таллов |
|
лии, CO2, |
|
ми проволо- |
|
|
|
|
|
|
|
|
|
|
|
||||||||||
|
|
|
|
|
|
|
|
|
|
смесях |
|
|
|
|
|
ками |
|
|
|
|
|
|
|
|
|
|
|
Рис. 2.15. Способы защиты металла от вредного влияния воздуха при дуговой сварке
2.5.8. Газовые защитные среды при сварке
Газовая защита может быть струйной или камерной, когда сварка проводится в камере с контролируемой средой. Схема струйной газовой защиты приведена на рис. 2.16. Она состоит из паров и газов, генерируемых дугой, а также из защитного газа, поступающего из сопла горелки.
47
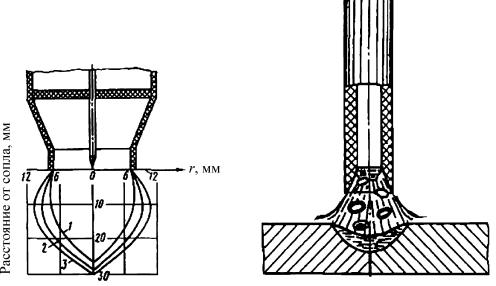
а |
б |
Рис. 2.16. Схемы струйной газовой защиты металла при дуговой сварке в газах (а) и электродом с покрытием (б): r – радиус струи и сопла
Высокая температура в зоне дуги, достигающая (6…8)·103 К, приводит к нагреву газа и его расширению более чем в 10 раз, а также к его диссоциации (см. рис. 2.8). Расширение газа способствует оттеснению воздуха и является самозащитным действием дуги. В том же направлении действуют пары металла в зоне анодного и катодного пятен, которые составляют до 10 % объема газов в зоне дуги. Наибольшее количество защитных газов создают электродные покрытия фтористо-каль- циевого и рутилового типов.
Струйная газовая защита имеет вид конусной прямолинейной, вихревой, кольцевой и комбинированной (двухслойной) струй.
Выходящая из сопла сплошная струя защитного газа смешивается с окружающим его воздухом, что сужает струю чистого защитного газа, который принимает вид конуса. Защитные свойства струи зависят и от плотности газа, что препятствует ее деформации при воздействии внешних потоков воздуха. Для прямолинейных газовых струй возможно ламинарное и турбулентное истечение газа. Режим движения газа оценивается числом Рейнольдса
Re = Dv IV,
где D – диаметр сопла, м; V – скорость истечения газа, м/с; v – коэффи-
циент кинематической вязкости газа, м2/с.
При Re > 3000 газовый поток переходит в турбулентный режим. Обычно применяемые скорости истечения обеспечивают заведомо ламинарный режим (за исключением аргона).
48
Однако сужение сопла за счет налипания брызг увеличивает скорость истечения и создает опасность перехода к турбулентному режиму. Наибольшее влияние на защиту от воздуха оказывают технологические факторы: длина дуги и расход газа. При струйной защите возможен подсос воздуха через зазор между кромками газами, поднимающимися от металла вследствие нагрева. Это исключается сваркой на подкладках, а также подачей газа через подкладки с каналами. Наряду с технологическими весьма эффективны и физико-химические способы защиты, заключающиеся в уменьшении растворимости газа в ванне путем снижения ее температуры и усиления выделения газов до начала кристаллизации либо в ослаблении их вредного влияния на свойства соединений.
Защитные газы, охлаждая дуговой разряд, снижают его стабильность, что особенно заметно при сварке в СО2. Другой вид воздействия на дуговой разряд – это влияние газов на характер переноса металла электрода (размер капель, степень разбрызгивания). Размер капель уменьшается с увеличением силы сварочного тока, повышением содержания углерода, уменьшением диаметра электродной проволоки и поверхностного натяжения в металле капли. В этом плане весьма эффективно добавление к аргону СО2 или кислорода, поскольку окисление поверхности капли снижает поверхностное натяжение.
При сварке в аргоне каждому диаметру электродной проволоки соответствует определенный критический ток, выше которого капельный перенос с сильным разбрызгиванием переходит к более благоприятному струйному.
При сварке тонколистового металла, когда увеличение тока недопустимо, добавка к аргону 20 % СО2 или 2...5 % О2, а также нанесение активаторов на электрод уменьшают критический ток и улучшают перенос металла.
Однако это увеличивает окислительную способность газов. Степень окисления металла пропорциональна температуре, поверхности
ивремени контактирования металла с газом. При радиусе капли 0,5 мм
итемпературе ее –3000 К, относительная удельная поверхность капель больше поверхности ванны в 20 раз.
Выбор защитного газа в решающей степени зависит от физикохимических свойств основного и электродного металлов и его взаимодействия с газами, что определяет возможность получения плотного металла шва.
Из инертных одноатомных газов используют аргон и в меньшем объеме гелий, а также их смеси преимущественно при сварке неплавящимся вольфрамовым электродом цветных, активных и тугоплавких
49
металлов (медь, алюминий, титан, молибден) и высоколегированных сталей.
Применяют аргон трех сортов (высший, № 1 и 2) по ГОСТ 10157–73, а также гелий трех-четырех сортов (особой чистоты, высокой чистоты, технический) по ТУ 51-689–75.
Смесь аргона с гелием состоит из 65 % Аг и 35 % Не. Такая смесь обеспечивает преимущества обоих газов: глубокое проплавление и хорошее формирование шва.
При сварке плавящимся электродом в инертных газах для получения мелкокапельного переноса и предотвращения пор применяют до-
бавки окислительных газов в смесях (в процентах): 80 Аr + 20 СО2;
80 Аr + 20 О2; 75 Аr + 22 СО2 + 3 О2.
При сварке низкоуглеродистых и низколегированных сталей применяют преимущественно в качестве защитного газа СО2 (ГОСТ 8050–76). Сварку в СО2 из всех механизированных способов применяют более часто. В результате диссоциации (см. рис. 2.7) СО2 обладает окислительным действием, а состав газов существенно различен вдоль зоны сваривания. Наибольшее окисление претерпевает металл при наиболее высоких температурах (стадия капли), что приводит к выгоранию углерода, несмотря на наличие раскислителей: кремния и марганца. Однако на стадии ванны, когда температура приближается к «кристаллизационной», окисление металла нейтрализуется раскислителями, которые могут быть введены в зону сваривания лишь в составе сварочной проволоки. Для сварки в СО2 низкоуглеродистых сталей рекомендованы проволоки по ГОСТ 2246–70. Состав этих проволок приведен в табл. 2.5.
Таблица 2.5 Состав проволок для сварки в СО2 низкоуглеродистых сталей, мас. %
Марка |
Углерод |
Кремний |
Марганец |
Тип раскисления |
проволок |
||||
|
|
|
|
|
Св-08ГС |
До 0,1 |
0,6...0,85 |
1,4...1,7 |
Среднераскисленный |
Св-08Г2С |
0,05...0,11 |
0,7...0,95 |
1,8...2,1 |
Высокораскисленный |
Для сварки низколегированных сталей в СО2 лучшими оказались проволоки Св-10ХГ2СМА, Св-08ХЗГ2СМ, Св-08Х14ГТ и др.
Для уменьшения разбрызгивания при сварке в СО2 применяют активированные проволоки и смеси защитных газов Аr + 20 % СО2. Свар-
50