
книги / Теория сварочных процессов
..pdf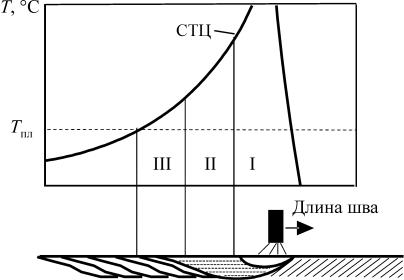
металла, а значит, металл дольше находится в расплавленном состоянии. В среднем вес металла электрошлаковой ванны составляет 450– 500 г. Температура в различных участках такой ванны одинакова и близка к температуре плавления металла. Условия протекания металлургических реакций в таких сварочных ваннах близки к равновесным и поэтому расчеты с использованием термодинамических данных не дают больших погрешностей.
2.3.Распределение температур в сварочной ванне
икапле электродного металла
Свойства различных зон сварного соединения во многом определяет термический цикл сварки (СТЦ) (рис. 2.3). Его основные параметры – максимальная температура СТЦ, скорость нагрева и охлаждения, время пребывания металла выше заданной температуры – влияют на структуру металла сварного шва и зоны термовлияния.
При ручной дуговой сварке, по данным И.К. Походни и И.И. Фрумина, существуют три температурные зоны. На рис. 2.3 показана схема распределения температуры по длине сварочной ванны.
Рис. 2.3. Схема распределения температуры по длине сварочной ванны: I – высокотемпературная зона, II – промежуточная зона, III – периферийная зона
На рис. 2.3 обозначены:
I – высокотемпературная зона вблизи столба дуги. Температура столба дуги – 5000…8000 °С, температура металла в этой зоне выше температуры его кипения (температура кипения для железа 3040 °С, для алюминия – 2460 °С, для титана – 3250 °С);
31
II – промежуточная зона с температурой 1800…2000 °С;
III – периферийная зона, температура в которой близка к температуре плавления металла. Средняя температура сварочной ванны при разных видах сварки приведена в табл. 2.2.
Таблица 2.2
Температура сварочной ванны и капель электродного металла для различных видов сварки
|
Свариваемый |
Температура |
Температу- |
Способ сварки |
сварочной |
ра элект- |
|
|
металл |
ванны, К |
родных |
|
|
капель, К |
|
Механизированная под |
Низкоуглеродистая |
1970…2130 |
– |
флюсом, пров.Св-08А |
сталь |
|
|
В аргоне, пров.Св-08 |
То же |
1900…2070 |
2830…3460 |
В СО2, пров.Св-08Г2С |
– » – |
2170 |
2860…2970 |
Порошковой проволо- |
Низколегированная |
1770…1880 |
2270…2970 |
кой рутилового типа |
сталь |
|
|
Электродами с кислым |
Низкоуглеродистая |
1870…2270 |
2380…2470 |
покрытием |
сталь |
|
|
Термический цикл сварки во многом определяет свойства различных зон сварного соединения, поэтому расчет его основных параметров (максимальная температура СТЦ, скорость нагрева и охлаждения, время пребывания металла выше заданной температуры представляет значительный практический интерес. Так, например, при сварке сталей при температурах более 1000 °С растет аустенитное зерно, что приводит к охрупчиванию стали. Степень роста зерна зависит от максимальной температуры СТЦ и времени пребывания стали при температуре выше 1000 °С. Структурное состояние стали (степень закалки) определяется скоростью охлаждения в интервале температур минимальной устойчивости аустенита (около 500 °С). Температура капель электродного металла на 500…800 °С выше средней температуры ванны. Температура сварочной ванны и капель электродного металла для различных видов сварки показана в табл. 2.2.
2.4. Перенос электродного металла в сварочную ванну
Характер переноса электродного металла в сварочную ванну влияет на полноту физико-химических процессов взаимодействия металлической, шлаковой и газовой фаз, а также на устойчивость процесса сварки.
32
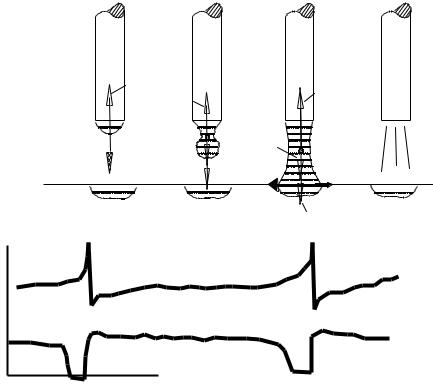
Существуют следующие виды переноса электродного металла:
–капельный (крупно- и мелкокапельный) с короткими замыканиями дугового промежутка;
–капельный без коротких замыканий;
–струйный;
–перенос через газовую фазу.
Наиболее благоприятным с позиций стабильности процесса горения дуги и качества формирования шва является мелкокапельный перенос. Рассмотрим факторы, способствующие получению мелкокапельного переноса электродного металла.
На рис. 2.5 представлена схема крупнокапельного с короткими замыканиями переноса электродного металла. На схеме показано измене-
ние напряжения дуги Uд и тока сварки Iсв в ходе процесса. По мере формирования капли напряжение дуги несколько снижается, так как капля растет и длина дуги уменьшается, сила тока немного увеличивается. В момент короткого замыкания каплей дугового промежутка напряжение равно нулю (Uд = 0), сила тока максимальна – ток короткого замы-
кания Iк.з. Далее процесс горения дуги возобновляется, начинается формирование новой капли электродного металла.
|
|
Nп.н Nп.н |
|
|
N′эд |
|
|
Р |
Р |
|
Р |
|
|
|
Nэд |
N |
|
N |
|
|
|
|
п.н |
п.н |
|||
|
|
|
|
|
||
Uд, |
I |
II |
|
III |
N"эд |
IV |
|
|
Iсв
Iсв
Uд
τ
Рис. 2.5. Схема крупнокапельного с короткими замыканиями переноса электродного металла в сварочную ванну
33
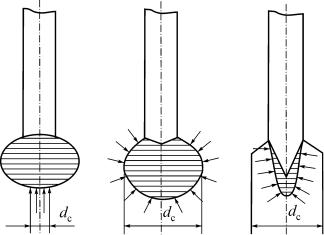
На этапах I–II на каплю действуют сила тяжести Р, сила поверхностного натяжения Nп.н и электродинамическая сила Nэд. Электродинамическая сила является результатом наличия электромагнитного поля вокруг электрода при протекании по нему тока. Она оказывает сжимающее действие на каплю. На этапе III в момент отрыва сила Nэд направлена от центра мостика вниз и вверх. В нижнем направлении эта сила больше, что способствует отрыву капли. В момент замыкания сила Nп.н стягивает каплю, что также способствует отрыву.
Размер капли определяется соотношением всех сил – и удерживающих, и отрывающих каплю. Из удерживающих сил основной явля-
ется сила поверхностного натяжения Nп.н. Она зависит от поверхностного натяжения электродного металла и температуры капли. Уменьшить эту силу можно введением поверхностно-активных веществ (щелочноземельных металлов, их углекислых солей), а также повышением тока сварки. Отрывающая электродинамическая сила Nэд возрастает с увеличением сварочного тока, и, следовательно, размер капли уменьшается. Увеличение напряжения также способствует измельчению капель. Чем
|
мельче |
капли |
электродного |
||
|
металла, тем больше суммар- |
||||
|
ная реакционная поверхность, |
||||
|
и тем полнее идут металлур- |
||||
|
гические |
реакции |
взаи- |
||
|
модействия компонентов. |
||||
|
Для сварки голой прово- |
||||
|
локой характерен |
крупнока- |
|||
|
пельный перенос с короткими |
||||
|
замыканиями, |
для |
сварки |
||
|
толстопокрытыми |
электрода- |
|||
|
ми – мелкокапельный пере- |
||||
Рис. 2.6. Схема перехода крупнокапельного |
нос с короткими замыкания- |
||||
ми, для сварки под флюсом – |
|||||
переноса металла в струйный |
мелкокапельный, |
для |
элек- |
||
|
трошлаковой сварки – мелкокапельный (при малых токах) и крупнокапельный (при больших токах).
Установлено значительное влияние на размер переносимых капель не только величины, но и плотности тока. При некотором критическом его значении капельная форма переноса переходит в струйную. Подобная форма переноса наблюдается при сварке в аргоне. В.И. Дятлов объясняет переход от капельного переноса к струйному увеличением раз-
мера dc столба (рис. 2.6), когда активное пятно охватывает боковую поверхность капли и увеличиваются сжимающие силы. Тогда конец
34
электрода заостряется, капля вытягивается в конус и возникает струйный перенос.
Размер переносимых капель оказывает существенное влияние на ход металлургических процессов. Чем мельче капли, тем больше суммарная поверхность соприкосновения их с окружающей средой, а значит, полнее взаимодействие с этой средой (растворение газов, процессы легирования, окисления и др.). Однако нельзя забывать, что в таком случае время существования капель уменьшается, а потому снижается и полнота протекания реакций.
2.5. Взаимодействие металла с газовой фазой при сварке
Несмотря на принимаемые защитные меры, полностью исключить попадание воздуха в зону сварки невозможно при любых методах. При сварке под флюсом, покрытыми электродами и электрошлаковой сварке воздух проникает через слой флюса или шлака. При сварке в СО2 и аргоне существует подсос воздуха вследствие турбулентности, а также примеси воздуха в самом защитном газе. Таким образом, в газовой атмосфере дуги содержится минимум 3 % воздуха. Взаимодействие расплавленной сварочной ванны с газами воздуха, неизбежное при сварке, влияет на состав металла шва и его свойства.
В состав газовой фазы входят:
–газы воздуха (азот, кислород, водород, пары воды);
–газы, образующиеся при плавлении и испарении покрытий электродов и флюсов;
–газы – продукты химических реакций в сварочной ванне;
–газы из адсорбированной влаги и загрязнений на металле;
–пары металла.
При взаимодействии газов с расплавленным металлом возможны следующие два случая:
1)растворение газа (т.е. образование растворов водорода, кислорода и др. в металле);
2)образование химических соединений (оксидов MeO, нитридов MeN гидридов MeH на поверхности и в объеме металла).
И тот, и другой тип взаимодействия с газами опасен и приводит
кпотере свойств металла сварного соединения.
Условно взаимодействие газов с металлами разделяют на следующие стадии:
–доставка молекул газа к поверхности металла;
–диссоциация молекулярного газа на атомы;
–адсорбция атомов на поверхности металла;
–растворение атомарного газа в металле;
35

– диффузия атомов в глубь металла.
Рассмотрим наиболее значимые стадии – диссоциацию и растворение – более подробно.
2.5.1. Диссоциация газов
Высокая температура в зоне сварки создает условия для диссоциации двух- и трехатомных газов. Диссоциацией называют распад молекулярных газов на атомы. В атомарном состоянии газы приобретают высокую химическую активность и легко взаимодействуют с жидким металлом электродных капель и сварочной ванны. Если атом газа теряет электроны с внешнего уровня и становится ионом, то процесс называют
термической ионизацией.
Диссоциация – процесс эндотермический, выражается уравнением химических реакций с соответствующими константами равновесия:
|
|
P 2 |
|
|
|
|
|
|
H 2H – Q |
K = |
H |
|
|
; |
|
|
|
|
|
|
|
|
|
|||
2 |
p |
PH 2 |
|
|
|
|
|
|
|
|
|
|
|
|
|
||
|
|
P 2 |
|
|
|
|
|
|
O 2O – Q |
K = |
O |
|
; |
|
|
||
|
|
|
|
|
||||
2 |
p |
PO2 |
|
|
|
|
|
|
|
|
|
|
|
|
|
||
|
|
|
P1/ 2 P |
|
||||
CO2 CO +1/2 O2 – Q |
Kp = |
|
O2 |
CO |
. |
|||
|
|
|||||||
|
|
|
PCO2 |
|||||
|
|
|
|
|
|
|
Количественной характеристикой процесса диссоциации является величина степени диссоциации α – это отношение числа диссоциированных молекул к числу первоначальных, т.е. α ≤ 1. Степень диссоциации связана с константой равновесия Kр реакции диссоциации и внешним давлением Р следующим соотношением:
|
K p |
|
α = |
|
. |
K p + 4P |
C увеличением внешнего давления степень диссоциации уменьшается. Степень диссоциации зависит также от температуры: α увеличивается с ростом температуры Т для любого газа из атмосферы дуги. Ориентировочная зависимость степени диссоциации водорода, кислорода
и азота от температуры приведена на рис. 2.7.
Таким образом, вблизи столба дуги в высокотемпературной зоне идет процесс диссоциации газов (азот и кислород диссоциированы поч-
ти полностью, αН2= 0,96 αО2 = 0,80). В сварочной ванне, где температу-
ра ниже, идет обратный процесс образования молекул из атомов, называемый рекомбинацией.
36
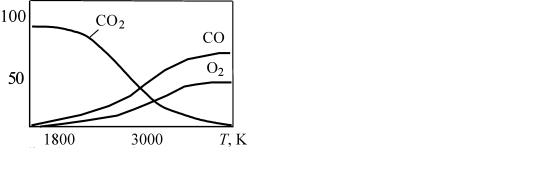
α |
CO2 |
H2 |
O2 |
N2 |
% |
1 |
|
|
|
|
|
0,5 |
|
|
|
|
|
|
2000 |
|
5000 |
Т, К |
Т, К |
Рис. 2.7. Зависимость степени диссоциа- |
Рис. 2.8. Содержание газовой фазы при |
|
ции азота, кислорода, водорода и |
уг- |
диссоциации углекислого газа в зависи- |
лекислого газа от температуры |
|
мости от температуры |
Содержание газовой фазы при диссоциации углекислого газа СО2 меняется в зависимости от температуры. При температуре Т > 4000 К углекислый газ полностью диссоциирован, а у поверхности сварочной ванны (2000 К) диссоциация СО2 незначительна.
Содержание продуктов диссоциации СО2 в зависимости от температуры можно определить по графику на рис. 2.8. При каждой температуре газовая фаза состоит из кислорода, угарного газа и углекислого в концентрациях, пропорциональных ординате соответствующей кривой, при этом суммарное содержание газов равно 100 %.
Таблица 2.3 Атомный вес Аi и потенциал ионизации веществ Ui
Вещество |
Аi |
Ui, эВ |
Вещество |
Аi |
Ui, эВ |
Водород (H) |
1,0 |
13,59 |
Железо (Fe) |
55,8 |
7,90 |
Азот (N) |
14,0 |
14,54 |
Алюминий (Al) |
26,9 |
5,98 |
Кислород (O) |
15,9 |
13,61 |
Медь (Cu) |
63,5 |
7,70 |
Водород (H2)) |
– |
15,40 |
Титан (Ti) |
47,9 |
6,80 |
Азот (N2) |
– |
15,80 |
Никель (Ni) |
58,7 |
7,63 |
Кислород (O2) |
– |
13,50 |
Кальций (Ca) |
40,0 |
6,11 |
Гелий (He) |
4,0 |
24,58 |
Литий (Li) |
6,9 |
5,40 |
Аргон (Ar) |
39,9 |
15,76 |
Натрий (Na) |
22,9 |
5,14 |
Оксид азота (NO) |
30,0 |
9,30 |
Калий (K) |
19,1 |
4,34 |
Фтор (F) |
19,9 |
16,90 |
Кремний (Si) |
28,0 |
7,94 |
Углекисл. газ (CO2) |
44,0 |
14,40 |
Марганец (Mn) |
54,9 |
7,40 |
Углерод(C) |
12,0 |
11,26 |
Магний (Mg) |
24,0 |
7,64 |
Вода (H2O) |
18,0 |
13,00 |
Вольфрам (W) |
183,8 |
7,93 |
|
|
37 |
|
|
|
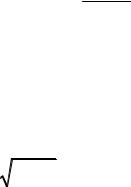
При дуговом нагреве одноатомные газы и пары металла подвергаются также термической ионизации, образуя плазму из заряженных ионов и электронов. Это облегчает стабильное горение дуги. Потенциалы ионизации ряда газов и паров приведены в табл. 2.3. Для щелочных металлов (калий К, натрий Na, калий К), кальция Ca, титана Ti и др. потенциал ионизации мал, составляет 4…6 эВ. Поэтому эти металлы являются стабилизирующими в составе сварочных материалов. От них резко отличаются аргон, потенциал ионизации которых достигает больших значений (15…24 эВ). При смешивании этих газов потенциал ионизации существенно снижается.
2.5.2. Растворение газов в металлах
Газы растворяются в металле только в атомарном виде. Реакцию растворения газа в жидком металле записывают в следующей форме:
{Г} [Г],
где {Г}– атомарный газ над поверхностью металла; [Г] – растворенный в металле газ.
Процесс растворения газов подчиняется закону Генри: содержание атомарного газа в металле [Г] пропорционально его парциальному дав-
лению в газовой фазе Р{Г}, т.е.
[Г] = KР{Г} (закон Генри),
где K – константа Генри, зависящая только от температуры и связанная с энергией Гиббса растворения газа ∆Gрас соотношением
ln K = − ∆GRTрас .
Если растворяется двухатомный газ, то реакцию его растворения в жидком металле записывают в следующей форме:
{Г2} 2[Г].
Процесс растворения двухатомного газа описывается законом Сивертса:
[Г] = K Р{Г2} (закон Сивертса),
где Р{Г2} – парциальное давление молекулярного газа над жидким ме-
таллом, ат.
Содержание газов в металле измеряют в кубических сантиметрах на 100 г либо в массовых процентах (мас.%): 1 см3/ 100 г = 0,001 мас.%.
Растворимость газов в металле зависит от температуры. С увеличением температуры содержание растворенного в металле газа растет:
38
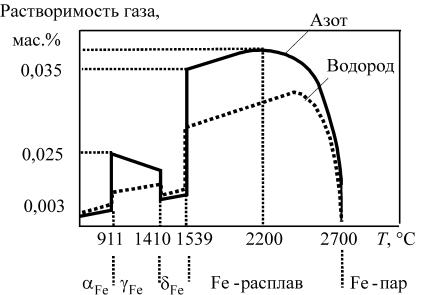
− |
Q |
|
|
RT , |
|||
[Г] = А e |
где [Г] – содержание газа в металле; А – константа, зависящая от рода газа; Q – теплота растворения газа; R – универсальная газовая постоянная.
Однако при температурах полиморфного превращения и температурах плавления растворимость газа изменяется скачкообразно – это так называемый скачок растворимости. Графики равновесных концентраций водорода и азота в железе, алюминии, никеле и меди при различных температурах (рис. 2.9 и 2.10) показывают, что в жидком металле концентрации газов значительны, а при кристаллизации железа (1539 °С) резко падают. Это создает риск образования пор при ускоренной кристаллизации. Особенно велик перепад растворимости для водорода в твердом и жидком алюминии, что объясняет его повышенную склонность к образованию пор в условиях дуговой сварки.
Рис. 2.9. Растворимость водорода и азота в железе при парциальном давлении РН2 = РN2 = 0,1 МПа
Растворимость газов зависит также и от структуры металла, что приводит к скачкообразному изменению растворимости при (α→ γ → → δ)-превращении и переходе от объемно-центрированной кристаллической решетки к гранецентрированной. Например, для растворения водорода и азота в железе (см. рис. 2.9) – при 911 и 1410 °С. Максимум
39
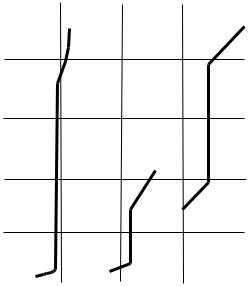
[H2], см3/100 г
|
|
Al |
|
|
40 |
|
|
Ni |
|
|
|
|
|
|
30 |
|
|
|
|
20 |
|
Cu |
|
|
10 |
|
|
|
|
|
|
Tпл = 660 °С |
Tпл = |
1453 °С |
|
|
Tпл = 1083 °С |
|
|
500 |
1000 |
Т, °С |
Рис. 2.10. Растворимость водорода в железе, меди и алюминии
растворимости азота в железе приходится на 2200 °С, водорода – на 2400 °С. При температуре кипения железа – 2700 °С растворимость газов в железе равна нулю.
2.5.3. Кислород в металлах при сварке
Характер окисления металлов при сварке различен.
Алюминий и магний практически не растворяют кислород ни
втвердом, ни в жидком состоянии. При их окислении образуются либо оксидные пленки на поверхности, либо частицы оксида, взвешенные
вжидком металле.
Железо, медь, никель, титан растворяют кислород ограниченно. Растворимость в жидкой фазе этих металлов больше, чем в твердой,
ис повышением температуры растет. Это означает, что взаимодействие с кислородом наиболее интенсивно идет в каплях электродного металла
именее – в хвостовой части ванны. Поглощенный кислород содержится в этих металлах в виде раствора (очень немного), в виде оксидов низ-
шей валентности – Ti2O, FeO, и в виде неметаллических эндогенных включений.
Окисление металла свободным кислородом газовой фазы идет по реакции:
2Ме + О2 2МеО.
40