
книги / FISMA and the risk management framework the new practice of federal cyber security
..pdf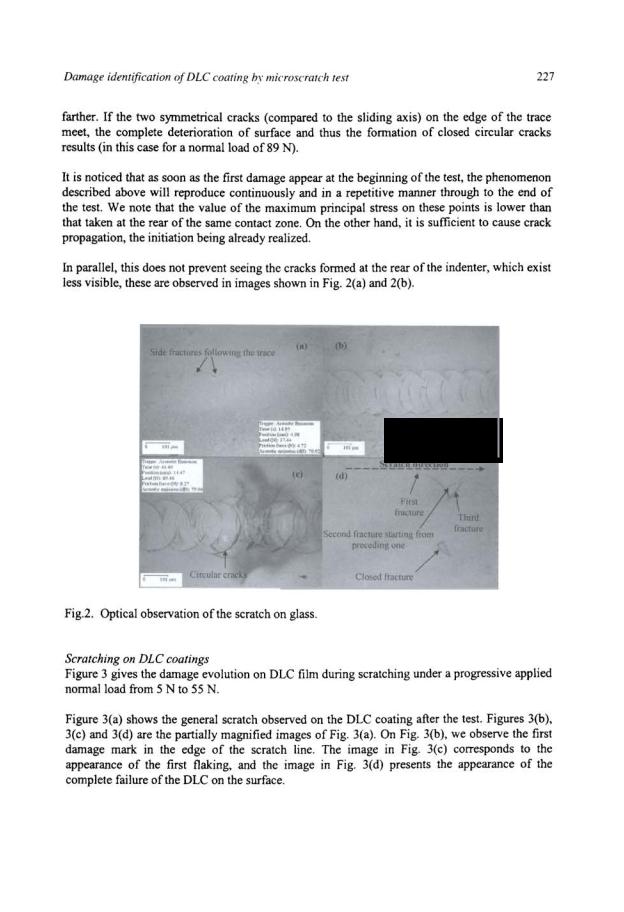
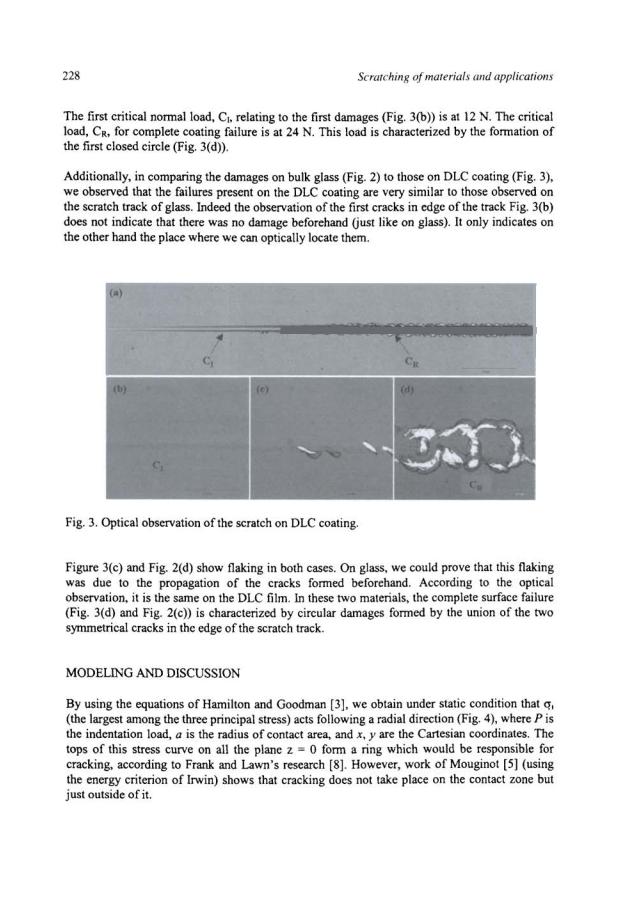
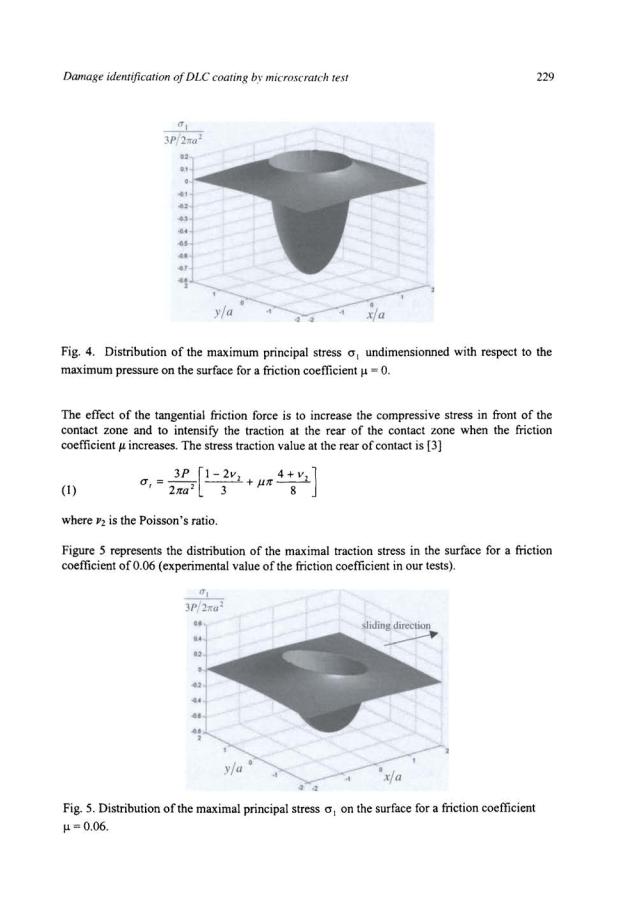
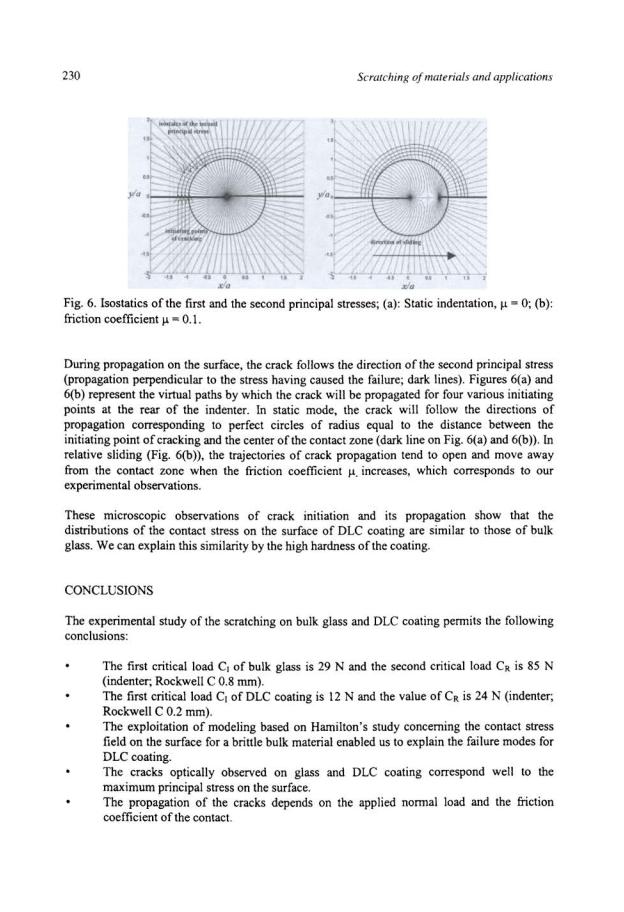
Damage identification of DLC coating by microscratch test |
231 |
The propagations of the cracks observed on DLC coating are similar to those observed on bulk glass.
REFERENCES
1.Bachmann, P. K., Leers, D. and Lydtin.H. (1991), Diamond Relat Mater.. 1. p. I.
2.Barquins, M. And Maugis, D. ( 1982), J Mecanique Theor Appli. I, p. 331.
3.Hamilton, G. M. and Goodman, L E. (1966), J Appl. Mech. 33, p. 371-376.
4.Lawn, B. R. (l967),Proc R. Soc. vol299,, p. 307-316.
5.Mouginot, R. (1988), Fracture offragile elastic materials under indentation ofplane and spherical punches. Thesis, University Paris 6.
6.Mathia, T. G. and Encrenaz, E. (1981), Wear. Vol. 73, No 1, p. 77-81.
7.Zeng, K. and Breder, K. (1992), Acta metal. Mater. vol40, No 10, p. 2601-2605.
8.Frank, F. C. and Lawn, B. R. (1967), Proc. R. Soc. London, Vol. 299, p. 292-306.
232
CHAPTER 12
CORRELATION BETWEEN ADHESION AND WEAR BEHAVIOUR OF
COMMERCIAL CARBON BASED COATING
Originally published in Tribology International vol 39. February 2006
K.H. LAU and K.Y. LI
Advanced Coatings Applied Research Laboratory (A CARL)
Department ofManufacturing Engineering and Engineering Management
City University ofHong Kong, Tat Chee Avenue, Kowloon, Hong Kong SAR, China.
E-mail: mekhlau@yahoo.com.hk
ABSTRACT
Adhesion and wear behaviour of hard coatings are two important properties that concern researchers. We need to use different tests to obtain these two values and the correlation between adhesion and wear is not always obvious. The purpose of this chapter is to find the relationship between the wear rate and the critical load for commercial hard coatings.
Commercial carbon based coatings were deposited on M42 high speed steel by magnetron sputtering. Different lengths of pre-sputtering time were used to change the properties of the coatings. Single pass scratch tests and multi-pass bi-directional wear tests were used to obtain the critical load and wear rate values, respectively. Results showed that there was a correlation between wear and adhesion. It was found that adhesion increases and wear rate decreases when the pre-sputtering time increases. It was also observed that adhesion strength varies with pre-sputtering time in a step function manner. To a large extent, the adhesion behaviour is related to the wear behaviour as far as the commercial carbon based coating is concerned. However, as different coatings have different microstructure and properties, further work should be done to decide whether a similar relationship can be applied in other cases.
KEYWORDS
Adhesion; wear; scratch tests; pre-sputtering time
Correlation between adhesion and wear behaviour of commercial carbon based coating |
233 |
INTRODUCTION
Adhesion and wear behaviour of hard coatings are two major properties that always concern researcher and several studies have been done on them. Adhesion of the coatings is an important property. The greater the adhesion between the film and substrate, the more difficult it is to break the coating. As drastic coating failure, such as spallation, will occur if the adhesion is poor [1], many researchers also focused on studying the adhesion of coatings [2- 4], Wear behaviour [5, 6] is an important factor also, as it can help us to determine some specific coating properties such as durability.
There are various methods for assessing the adhesion of hard coatings to a substrate [7, 8], but most researchers agree that the scratch test is the most practical approach [9]. The result of scratch test can be identified by the critical load (Lc1 and Lc2, which is defined as the load where initial coating failure is detected and total delamination of the coating from the substrate respectively). Due to the high reliability of scratch test, many researchers use this method to assess the adhesion of coating, see Refs [3, IOJ. As far as wear performance of coating is concerned, a hard counter-body material (e.g. tungsten carbide) is commonly used to carry out sliding wear. One common test is Pin-on-disc wear test [11]; in this paper a multi-pass bidirectional wear test is used.
Sometimes it is not feasible to carry out both the adhesion and wear test for a given coating sample due to the availability of machine, time and cost, etc. Therefore, if it is possible to find a general relationship between the two tests, one less test could then be used to identify the basic mechanical properties of the film. Up to now, few papers pay close attention to this topic, and even those researchers involved cannot observe any obvious relationship between them. For instance, S. J. Bull [12] had done similar work using TiN coatings deposited on 304 stainless steel, and he found that the correlation was poor. His results showed that when the critical load (Lc) increased, the wear resistance of some samples increased, but generally there was no change. Therefore, he concluded that the correlation between adhesion and wear was poor as there were many other factors which influenced the wear performance. The aim of this paper is to investigate the correlation between wear and adhesion of a commercial carbon based coating by using scratch tests and multi-pass bi-directional wear tests.
EXPERIMENTAL DETAILS
Deposition
A Teer UDP450 closed field unbalanced magnetron sputter ion plating (CFUBMSIP) system was used to deposit the coatings onto silicon wafer, as well as hardened (hardness-8 GPa) and
234 |
ScratchinK of materials and applications |
non-hardened (hardness-2.5 GPa) M42 high speed steel. The steel substrates were polished to roughness (Ra) about 0.03p.m. DC power and pulsed DC were used on the targets and the substrate respectively. To obtain coatings with different properties, five different pre-sputtering times [13] (3, 10, 20, 35 & 60 minutes) with -450V bias voltage on the substrate were used before depositions. Afterwards, -80V bias voltage with a frequency of 50 kHz was used on the substrate during deposition for two hours. The coating thickness was around 2p.m for all samples (see figure 1).
Scratch test
The scratch tests were carried out using a Teer ST-3001 scratch tester. A Rockwell C diamond tip (120°, 200p.m radius) was used as an indenter. During the test, the indenter was drawn over the coated surface as the applied normal load increased continuously until coating failure occurred. The load was increased from I0 N to 80 N by I00 N/min and sliding speed was constant at 10 mrnlmin. The scratch tests were performed in air at temperatures between 22 ·c and about 68% relative humidity (RH).
The scratch tracks were observed under microscope attached to the scratch tester and scanning electron microscope (SEM). The failure modes of the scratch tracks on different samples were obtained and the critical loads were determined by locating the position at which the coatings started to fail.
Wear test
Besides testing adhesion, the ST-3001 was employed to perform the reciprocating wear (multi-pass) test. In this test, a 5 mm diameter tungsten carbide (WC-6% Co) ball applied a constant load to the sample. Once the initial load was reached the sample moves backwards and forwards over a pre-selected distance until the pre-determined number of cycles was completed (one cycle means one complete reciprocating movement). The ambience conditions were around 22 ·c and 68% RH.
As the samples have different wear behaviour, depending on the pre-sputtering time, the number of cycles for each of the sample was carefully selected to ensure the indenter will not wear through the coating and reach the substrate and therefore lead to an incorrectly wear rate calculation. Parameters of the test are shown in Table I. After each test, a Talysurf profilometer was used to measure the cross sectional area of each wear track in order to calculate the wear rate.
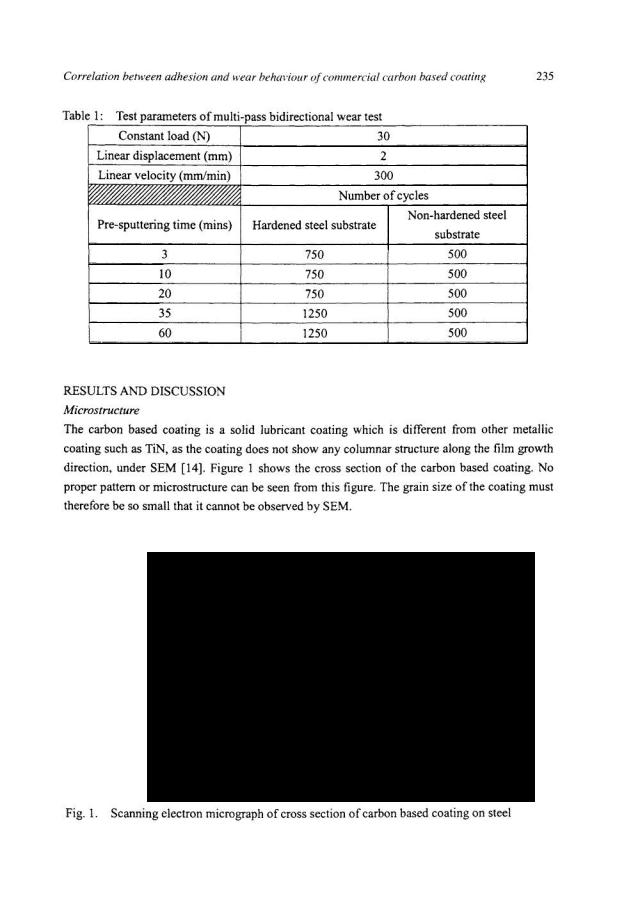
