
книги / FISMA and the risk management framework the new practice of federal cyber security
..pdf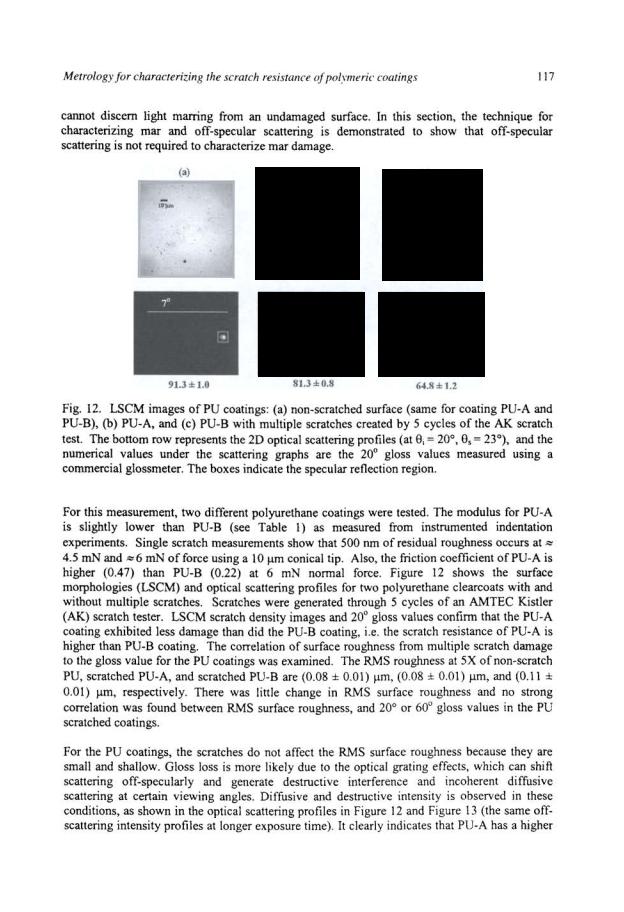
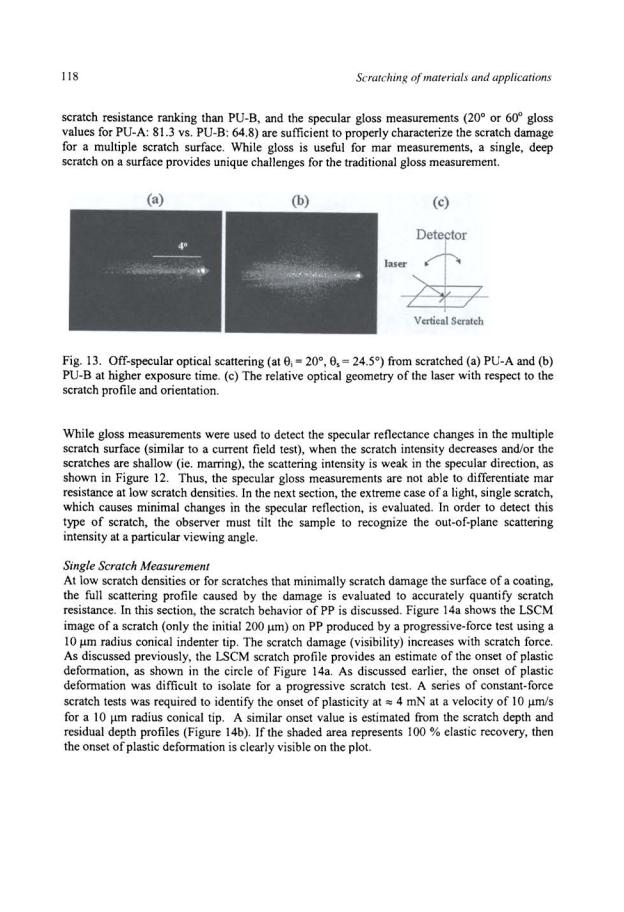
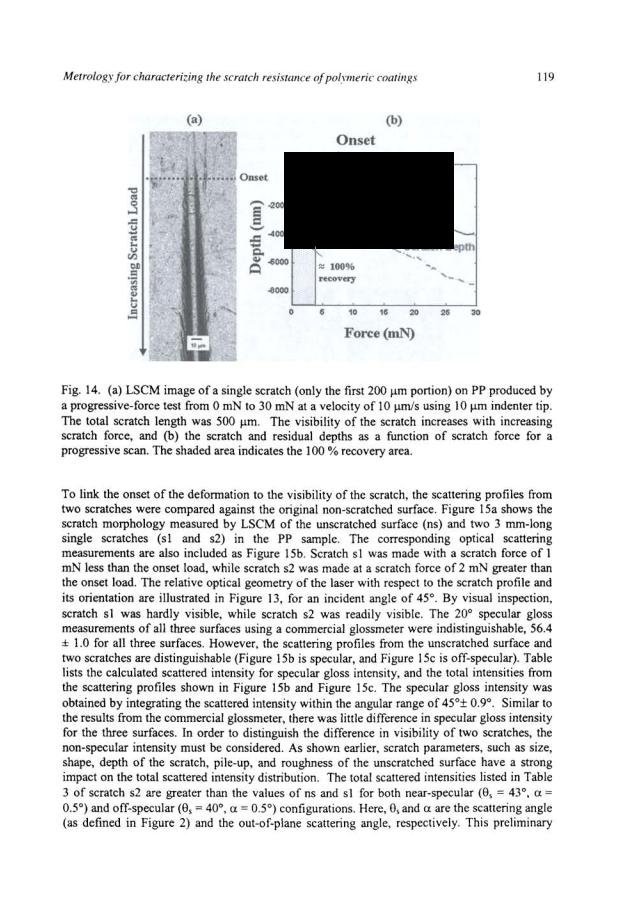
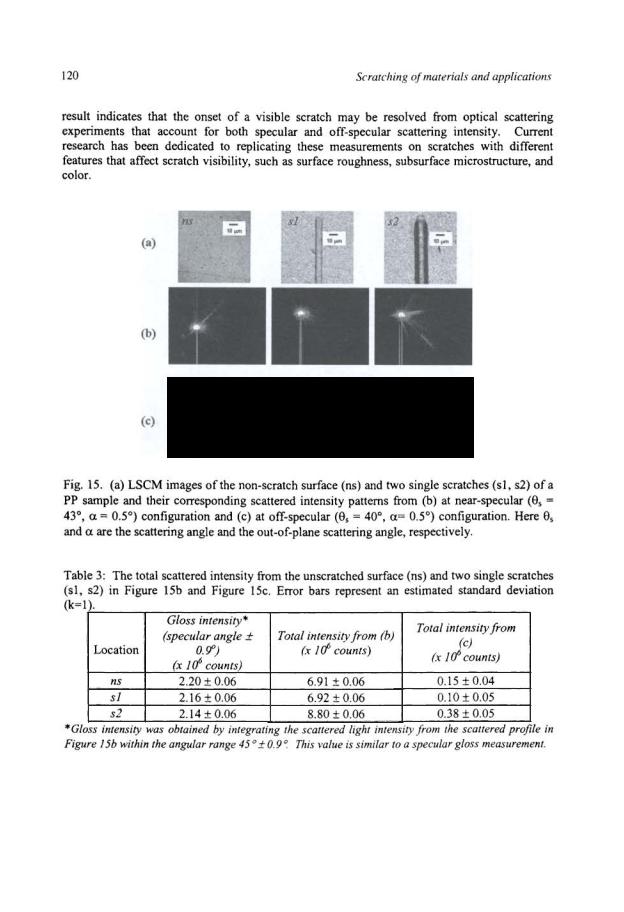
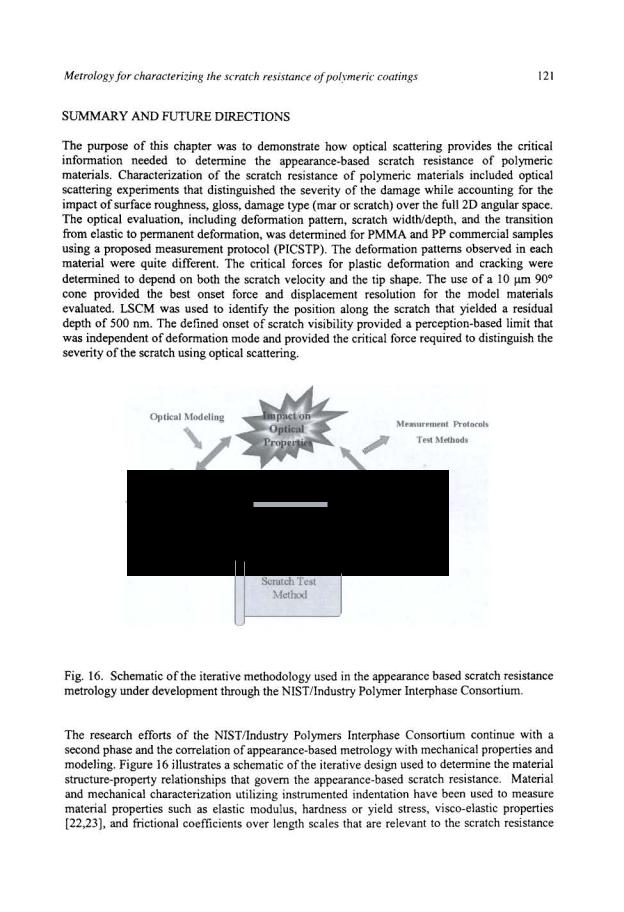
122 |
Scratching of materials and applications |
and material heterogeneity. These research results will be reported in the literature at a later date. Future research will expand to include polymeric materials and their appearance-based scratch resistance as a function of environmental aging.
ACKNOWLEDGEMENTS
The authors gratefully acknowledge funding support from the NIST-Industry Polymer Interphase Consortium (PIC). PIC Industrial members include: Visteon Corporation, Dow Chemical, PPG industries, MTS system Corporation, Arkema Inc., and Eastman Chemical. The authors give special thanks to PPG industries and Dow Chemical for providing the samples reported here.
REFERENCES
1.VanLandingham, M. R. (2005). In: Proceedings of3rd International Symposium on Service Life Prediction ofCoatings, pp. 305-330, Martin, J.W., Ryntz, R.A., and Dickie, R. A. (eds.), Federation of Societies for Coating Technology, Blue Bell, PA.
2.Betz, P. and Bartelt, A. (1993) Progress in Organic Coatings 22, pp. 27-37.
3.Ryntz, R.A., Abell, B.D., Pollano, G.M., Nguyen, L.H., and Shen, W.C. (2000) J. of
Coatings Technology 72 (904), pp. 47-53.
4.Lin, L., Blackman, G.M., and Matheson, R.R. (2001) Materials Science and Engineering A317, pp. 163-170.
5.Ryntz, R.A. and Britz, D. (2002) J. of Coatings Technology 14 (925), pp. 77-81.
6.Krupicka, A., Johansson, M., Wanstrand, 0., and Hult, A. (2003) Progress in Organic Coating 48, pp. 1-13.
7.Courter, J.L. (1997) J. ofCoatings Technology, 69 (866), pp. 57-63.
8.Rangarajan, P., Sinha, M., Watkins,V., Harding, K., and Sparks, J. (2003) Materials Engineering and Science 43 (3), pp. 749-758.
9.Fernholz, K., Sinha, M., Gardner, M., and Watkins, V. (2004). In: Proceeding of 7th
International Coatings for Plastics Symposium, June 7-9,2004, Troy, MI.
10.Sung, L., Drzal, P., VanLandingham, M. R., Wu, T.-Y., and Chang, S.-H. (2005) JCT Research 2 (8), pp. 583-589.
11.McKnight, M.E., Marx, E., Nadal, M., Vorburger,T.V., Barnes, P.Y., and Galler, M.A. (2001) Applied Optics, 40 (13), pp. 2159-2168.
12.Hunt, F.Y., Marx, E., Meyer, G.W., Vorburger, T.V., Walker, P.A., and Westlund, H.B. (2002). In: Service Life Prediction: Methodology and Metrologies, J. W. Martin and D. R. Bauer (eds.) ACS Symposium Series 805, Oxford University press.
13.ASME B46.1 (I 995) Surface Texture, Amer. Soc. Mech. Engrs., NY.
14.VanLandingham, M.R., Sung, L., Chang, N.-K., Wu, T.-Y., Chang, S.-H., and Jardret, V.D. (2004) JCT Research, 1 (4), pp. 257-266.
15.Corle, T.R. and Kino, G.S. (1996) Confocal Scanning Optical Microscopy and Related
Imaging Systems, Academic Press.
16.Sung, L., Jasmin, J., Gu, X., Nguyen, T., and Martin, J.W. (2004) JCT Research 1 (4), pp. 267-276.
17.Sung, L., Garver, J., Embree, E., Dickens, B., and Martin, J.W. (2005) NIST internal report.
Metrology for characterizing the scratch resistance ofpolymeric coatings |
123 |
18.NIST-Industry Polymer Interphase Consortium (PIC)- more details: visit consortium web site slp.nist.gov.
19.Briscoe, B. J., Pelillo, E., and Sinha, S.K. (1996) Polymer Engineering and Science 36 (24), pp. 2996-3005.
20.Jardret, V. and Morel, P. (2003) Progress in Organic Coatings 48, pp. 322-331.
21.Sung, L., Nadal, M.E., McKnight, M.E., Marx, E., and Laurenti, B. (2002)1. of Coatings Technology, 74 (932), pp. 55-63.
22.VanLandingham, M.R., Chang, N.K., Drzal, P.L., White, C.C., and Chang, S.-H. (2005)
J.Poly. Sci. B -Poly. Phys., 43 (14), pp. 1794-1811.
23.White, C.C., VanLandingham, M.R., Drzal, P.L., Chang, N.K., and Chang, S.-H. (2005)
J.Poly. Sci. B- Poly. Phys., 43 (14), pp. 1812-1824.
124
CHAPTER6
SCRATCHING OF POLYMERS: DEFORMATION MAPPING AND WEAR
MODELING
SUJEET K. SINHA
Department ofMechanical Engineering National University ofSingapore
9 Engineering Drive 1, 117576, SINGAPORE E-mail: mpesks@nus.edu.sg
ABSTRACT
Scratching as a material testing tool has been around for well over 180 years [1] but despite many advantages, this technique has only recently found general acceptance by the engineers. Often the problem lies not in the testing method but in the deconvolution of the test results due to a lack of proper understanding of the stress field around a scratching tip and the boundary condition between the tip surface and the material. In this chapter, we will present some of the successes in the application of scratching for bulk polymer where this technique has provided insight into the materials surface damage characteristics. Examples are drawn from this author and coworkers' current and past works on the scratching of mainly bulk solid polymers. The first application example is taken from the work on scratching maps for polymers. Scratching technique has shown that often materials' deformation behavior, when faced with a sharp tip, is a strong function of the tip attack angle, normal load, scratching velocity and temperature. The second part of this chapter will focus on more recent results on the use of nano-scratching to understand the wear debris generation process for polymers. It is shown that cyclic intersecting scratching provides a hitherto unknown clue as to why some polymers, despite their low tensile strength, are more wear resistant than other stronger polymers.
KEYWORDS: Scratching maps, intersecting scratching, polymers, abrasive wear modeling
INTRODUCTION
Scratching technique for (bulk) polymers has several advantages. For example, materials deformation characteristics for a range of imposed conditions (load, speed, temperature etc.) can be obtained by this simple test [2,3]. Scratching technique can also be used to understand the friction models such as plowing and sliding contributions to friction [4]. Recently, this technique has also been used to model abrasive wear of metals and polymers [5,6].
Although the stress field around a moving tip in a scratching event is very complex and requires the computational technique to understand and estimate stress [7], much of the materials specific data, for practical applications, can be obtained quite conveniently in a scratch test by simple measurements of the scratch force and post-scratch geometry of the groove. Historically,
Scratching ofpolymers: Deformation mapping and wear modeling |
125 |
the scratch hardness value has been obtained by a simple ratio of the load divided by the projected contact area [2). This way of calculating scratch hardness is quite similar to the calculation of indentation hardness, however, difficulty in scratching is that the calculation of the projected contact area is, at best, only an estimate. The scratching event is marred by elastic and plastic deformations and recoveries coupled with cracking, fracture and chip formation. These deformation and fracture events are directly related to parameters such as the material's mechanical properties, the indenter attack angle, applied load, scratching speed and the prevailing temperature. Thus, the actual projected contact area is difficult to estimate for scratching. Scratch hardness is useful as a surface property data when ductile metals or ductile polymers are involved, and also, the general material surface deformation behavior during scratching can be studied by this test.
In this chapter we will present two examples of the materials deformation and failure studies conducted by scratching. The examples are the scratch deformation mapping and the abrasive wear modeling. The studies mentioned here are related only to polymers, as metals and ceramics may present different set of trends.
SCRATCH DEFORMATION MAPPING FOR POLYMERS
The scratch deformation mapping study has been conducted to understand the condition under which a scratch would be damaging to the surface of a polymer. It is more related to the visual perception of a polymer surface than a real mechanical damage to its strength. Often many polymers are used for the appearance (such as transparency) or optical aesthetics of an engineering component and for such applications the quality of the surface is judged by visual appearance. The visual appearance can be quantified by measuring optical reflectivity or optical scatter of a surface [8,9). Thus, when a material deforms on its surface by only plastic deformation or by only brittle fracture, the optical reflectivity or scatter values of the deformed surface for these two extreme cases will be different. The other purpose of knowing the distinction between different deformation mechanisms is applicable in predicting failure as a result of surface damage. Whatever the purpose and intended final application, the main objective of this type of work is to understand the surface deformation characteristics, as perceived by some optical means, under a range of operational parameters such as the imposed strain, normal load, scratching speed and the ambient temperature. A change of any of these operational parameters, as will be seen later, brings a drastic change in the deformation characteristics of the polymers. It may be noted that the surface deformation characteristics of a material decide much of the other measured performances of the materials such as the coefficient of friction, wear rate and surface fatigue failure. Polymers are known to demonstrate a wide range of deformation behaviors for a slight change in the operational conditions. The variety in the materials responses has been shown schematically for a change in one factor, strain, characterized by the included angle of a conical tip; Fig. 1. This figure, though only a qualitative guideline, also provides an excellent definition of the nature of deformation encountered during scratching of polymers. Elastic deformation would be said when the scratching process does not leave behind an optically visible scratch mark. This is akin to pure elastic sliding often encountered when the imposed strain is extremely low coupled with low loading or stress condition. Ironing is the term used when we observe a type of mark on the surface of the polymer that is indicative of smoothening of the tall asperities on the surface but no observable plastic deformation on the real surface of the polymer. This type of deformation may be defined as a stage between the elastic deformation and the ductile plowing. Thus,
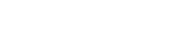
126 |
Scratching of materials and applications |
ductile plowing is defined as plastic deformation of the polymer surface by the scratching tip. The scratch groove does not show any presence of micro-cracks inside or along the scratch mark. Often a ductile polymer would show pile-ups or plastically deformed bulges formed on the sides of the scratch when the plowing is deep. Cracking would be encountered in and around the scratch if the material behaves in brittle manner. Lastly, brittle machining is recognized when there is the production of chips and loose debris as a result of crack initiation and propagation. Brittle machining is one important mechanism by which wear of the polymer material by hard asperities takes place. Often there is a combination of the above-mentioned deformation types which are recorded while constructing a scratch deformation map.
Response (Pictorial) |
Generic |
|
a |
|
|
|
|
|
|
~Lv |
|
180' |
||
Elulic |
|
|
||
- |
|
|
|
|
|
|
|
150' |
|
https://studfile.net/ |
|
ironing |
|
|
- |
|
|
|
|
|
|
|
120' |
|
-- |
|
Ductile |
||
|
|
|
||
---~ |
|
Ploughing |
|
|
-- |
|
|
90' |
|
|
Ductile |
|
|
|
~ |
|
llacl!lnlng |
|
|
|
+ Cracldng |
|
so· |
|
-- |
|
I |
|
|
|
|
|
||
~ |
|
30' |
||
~ |
|
Brittle |
|
o· |
- |
|
llachlnlng |
|
|
|
|
|
|
|
|
|
|
|
|
Fig. 1. A qualitative representation of the influence of cone angle upon the type of damage produced [4]. The figure only shows the effects and is not drawn to any scale. For clarity, the pictorial view does not show the change in the cone angle.
Figures 2 (a) and (b) show scratching maps for PMMA for different strains imposed at varying normal loads (Fig. 2 (a)) and temperatures (Fig. 2 (b)). The nominal strain was varied by changing the included angle of the conical indenter from 30° to 170°. The strain in this case is calculated by the parameter 0.2 tan 8; where 8 is the attack angle of the cone (8 = 90° - 0.5 x (included cone angle)). The map was constructed by observing the deformation patterns after scratching under a scanning electron microscope. It is seen that at normal temperature, PMMA starts to show brittle behavior at a strain of around 0.12 depending upon the normal load. Though not a very marked effect, high load has tendency to change the deformation mechanism to brittle machining and cracking. It is probable that both ductile deformation and brittle fracture can get pronounced at higher load just because deep penetration of the surface would create much higher stress field (both tensile and compressive) around the indenter than would be possible at lower load. Such change in the mechanism from ductile to brittle has been