
книги / FISMA and the risk management framework the new practice of federal cyber security
..pdf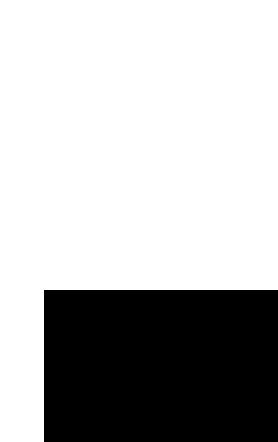
Mechanical analysis of the scratching of metals and polymers at moderate and large strains |
37 |
We observe very similar results in scratching (Fig. 9) with two main differences: first as noticed previously the material piles up for close to X> 10 and not 30, and for the same value of the indentation index the frontal edge is higher and very much steeper. In addition we see that the elastic recovery of the material in the scratch symmetry plane (x=O) is significant for X.$ 30, but the initial slope of the profile behind the indenter tip is not sufficiently high to maintain the contact between the tip of the indenter and the material for X> 1. Notice however that the calculation of the elastic recovery for higher values of X is not very accurate. Nevertheles the residual groove comprises always two shoulders more or less marked and their distance is very near the contact width: b-bc (Fig. 1). We describe in§ 7 the profile of the groove under load in plane y=O.
2 |
z |
|
|
|
|
|
|
|
|
|
|
|
|
····X=1 |
|
|
|
|
|
|
- |
X=5 |
|
|
|
|
|
|
- |
X=10 |
|
|
|
X=1 |
|
|
- |
X=20 |
|
1 |
|
|
|
|
-·X=30 |
||
|
|
|
|
|
|||
|
!••·"••v.•"•-••/\, •• r•"• ••·• |
|
|
- |
X=60 |
||
|
|
|
|
·-·X=80 |
|||
|
|
|
|
|
|
||
|
|
|
|
|
|
-X= 100 |
|
|
|
|
|
|
- |
X=200 |
|
|
|
|
|
|
|
--X= 1000 |
|
|
|
|
|
y |
|
|
|
|
|
|
|
|
|
|
|
|
|
-10 |
0 |
10 |
|
|
|
Fig 9. Scratching elastic perfectly plastic solids with a 70.3 deg cone under zero friction: Evolution with the indentation index X of the indent profile along the symmetry plane x=O (29].
2r----------------------------- |
, |
c |
scratch |
Fig 10. Indentation and scratching of elastic perfectly plastic solids with a 70.3 deg cone under zero friction: Evolution of the shape ratio c with the indentation index X.
38 |
Scratching ofmaterials and applications |
The evolution with X ofthe shape ratio in indentation and scratching is reported in Fig. 10. This figure states precisely that the shape ratio is higher in scratching than in indentation; in addition we see two interesting points:
+for X=1, c~0.75 a value already significantly higher than the value c=2ht-0.636 related to a full elastic contact (see below);
+for X=lOOO, c attains a high value c~l.78, but it is not sure that it is the limiting value related to the RPP solid.
The evolution with the indentation index X of the shape ratio in scratching can be fitted by a polynomial regression in two steps (similar equations have been proposed for indentation in [30]):
c = {0.74052 +0.1658L- O.ot 118L2 +0.12741L3 |
1 ~X~ 30 |
0.26092 + 0.98257L- 0.15885L2 |
with L =log X (19) |
30~X~103 |
The first relation must be used with some caution for X<5 because we have simulated only the cases X=1 and X=5. Nevertheless extrapolations for X<1 suggest that the value c=2/rt could be retained for X-().3 and so the contact geometry would be totally similar to the elastic theory
X~0.3. Some further calculations in this range of values of the indentation index are required in order to validate definitively this conclusion, but at present time our calculations suggest that because the rear contact angle decreases only for X:2:0.8, there would exist a range of values of the indentation index, 0.3 ~X~ 0.8, where the contact is limited by a full circle (quasi-elastic contact), but where in fact some plastic strain of the material occurs and where the contact radius is greater than its elastic value, for a given penetration depth. This quasielastic contact regime could be due to the gradual increase in size of the plastic core around the indenter tip.
Volume Average Plastic Strain and Scratch Hardness
All these previous results suggest that scratching induces higher plastic strain than indentation. In order to state more precisely this point we have estimated the average plastic strain Ev in the deformation volume V:
&v =..!.. Jc dV |
(20) |
Vv |
|
The numerical procedure is described in details in [33]. We see in Fig. 11 that in first approximation for 2 ~X~ 200, Ev increases in direct relation with logX and that it is 66 % about higher in scratching than in indentation. For higher values of the indentation index, &v becomes constant despite the fact that the contact geometry is not yet steady and it attains in scratching 0.936 a value very close to the value of 1.12 suggested by the 2D analogy for RPP solids(§ 3). Notice however that for low elasticity materials with high indentation index, Ev for indentation and scratching is much higher than the representative value 0.071 for indentation pressure suggested by Johnson (relation (2)).
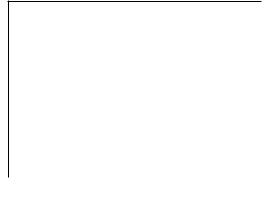
Mechanical analysis of the scratching of metals and polymers at moderate and large strains |
39 |
£. = 0.936
0.&
0.6
0.4
0.2
Fig 11. Indentation and scratching of elastic perfectly plastic solids with a 70.3 deg cone under zero friction: Evolution of the volume average plastic strain Ev with the indentation index X
Finally, Fig. 12 presents the evolution with the indentation index X of the indentation hardness H (true average contact pressure W/(7ti)) and the scratch hardness Hs and Hsl/2· At first sight we observe that all these quantities have similar evolution with X, but in fact:
+ the indentation hardness H is an increasing function of X and as expected tends toward a limiting value -2.6 cr0 which corresponds to the limiting value of the constrain factor C3 (70.3 deg)-2.6 (§ 2);
+ the (true) scratch hardness Hs increases in a first time, attains a maximum Hr;a-x -2.5 cr0 for
X-20, then decreases slowly toward 2.25 cr0 for X=I03; so the ratio HJH is a slowly decreasing function of X varying from 1.22 toward 0.87 about as X increases from I to I03, the value 1 being obtained for X-22;
•the evolution of the apparent scratch hardness H.112 is very similar to that of H•. Because the
area of the semi-disk with diameter the groove width b underestimates in all cases the real contact area, Hsl/2 is always greater than Hs, but Hs1121Hs is first a quick decreasing function of X from 1.57 (X=1) to I (X=10) because the rear contact angle decreases quickly (Fig.6); for X~ 20 it is about constant - 1.1 because the frontal edge is a little higher than the lateral edge (Fig. 5b): in the range X~ 10 under zero friction the apparent scratch hardness H,1;2 is a rather good estimation of the true contact pressure H,. It is interesting to notice that for
X~30 the relative difference between Hand H.u2 is lower than 6% and so in this large range of values of the indentation index the indentation hardness is very close to the apparent scratch hardness as it is commonly observed in testing at 20°C metals with high melting temperature [4].
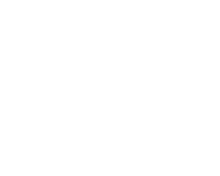
40 Scratching of materials and applications
|
|
H/cro |
|
0 |
0 |
)( |
|
X |
|
|
|
|
|
~ |
! 0~~ |
|
|
||
|
|
|
() |
0 |
~ |
|
|||
|
|
0 |
|
AAA |
A |
|
|||
|
|
|
|
|
|
||||
|
|
)( |
|
|
|
|
|||
2 |
A |
|
|
|
|
|
|
|
|
|
|
|
|
|
|
|
|
|
|
|
|
)( |
|
|
|
|
|
|
|
|
1p |
|
|
|
X H |
|
|||
|
|
~ |
|
|
|
|
|||
|
|
|
|
|
0 |
Hs112 |
|
||
|
|
|
|
|
|
|
|||
|
|
|
|
|
X |
A |
H. |
|
|
|
|
|
|
|
|
|
|
|
|
|
|
|
|
|
|
|
|
|
|
|
0 |
1 |
10 |
|
100 |
|
1000 |
Fig 12. Indentation and scratching of elastic perfectly plastic solids with a 70.3 deg cone under zero friction: Evolution of the indentation hardness H, the scratch harness Hs and H.112 with the indentation index X.
These results confirm the great similarity between scratching and indentation commonly observed especially for X> 10, i. e. for common metals, the difference in scratch and indentation hardness becoming rather high for X<lO as for some polymers. An unexpected difference however is the decrease of the scratch hardness at high values of the indentation index. This decrease is limited and so this result would require some additional work for confirmation. But from a physical point of view we think that it is real and due to the increase with X of the slope of the free surface of the edge (Fig. 9):
+the contact pressure for the equivalent wedge scratching (§ 3) is p-2.45 cro, a value very close toHr:ax -2.5 cr0 obtained for X-20 where the slope of the edge is very close to the slope of the indenter, as in the 2D scratching;
+for higher values of X the slope of the edge increases and for the 2D scratching this produces a decrease in the contact pressure.
FRICTION EFFECTS IN LOW STRAIN SCRATCHING AN ELASTIC PERFECTLY PLASTIC SOLID
Here we study the effect of the friction in the scratching of a work hardened steel (table 2) with the same conical indenter (8=70.3 deg). This material does not work harden and its indentation index is X= 100; the friction coefficient J.1 increases from 0 to 0.2 in steps of0.05.
Contact Geometry and Volume Average Plastic Strain
For this value of the indentation index the material is in contact only with the frontal part of the
indenter (see§ 5). As J.1 increases, the flow remains of the ploughing type and Fig. 13 describes
schematically the evolution of the contact geometry with friction for a given penetration depth:
in first approximation the contact width be and the contact height he remain constant. an
unexpected feature. On the contrary the frontal height hJe increases significantly (Fig. 14). So
Mechanical analysis of the scratching of metals and polymers at moderate and large strains |
41 |
|
Rear part |
Frontal part |
|
Increase
in!l
-t--+-1~ . - . - . .I.
bcl2-
1.53h tane
Fig. 13. Influence of the friction coefficient 11 on the contact surface (top view) in scratching an elastic perfectly plastic material (Ee-0.35 %) with a conical indenter (9=70.3 deg~ X-1 00)- h constant.
the top view of the contact is about halfofan elliptic disk whose eccentricity increases with the
friction (Fig. 13). So the friction produces an accumulation of the material on the frontal surface of the indenter and in addition we see on Fig. 14 that the slope of the frontal edge increases, a feature very similar to what occurs in 2D scratching [21, 24]. Unfortunately we have not observed more in details the flow field in the frontal edge in order to see if the increase in friction promotes the formation of a dead zone as in the SLF models of ploughing under high friction proposed by Petryk [24] and in the 2D numerical simulations [28]. So for 3D scratching this point requires further work.
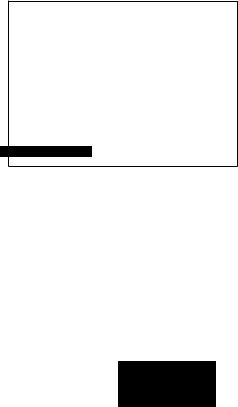
42 |
Scratching of materials and applications |
z
2
1
y
0 |
10 |
Fig. 14. Influence of the friction coefficient 1.1 on the profile of the frontal edge (side view, plane x=O) in scratching an elastic perfectly plastic material (Ee-0.35 %) with a conical indenter (9=70.3 deg-7 X-100).
2.2 |
|
|
|
hlh |
|
|
|
|
|
|
|
|
|
|
|
||
|
|
|
|
|
|
|
|
|
|
|
|
|
1/,/ |
.r;y- |
|
|
|
2 |
|
|
|
fc |
|
|
|
|
|
|
|
|
|
|
|
|
|
1.8 |
|
|
|
_,Y |
|
|
|
|
|
|
|
|
|
|
|
|
|
|
|
~ |
h /h |
|
|
|
|
|
|
|
|
|
|
|
|
|
|
1.6 |
|
|
|
c |
|
|
|
|
|
|
|
|
|
|
|
|
|
1.4 |
|
|
|
Ev |
|
|
|
|
1.2 |
|
|
|
\o. |
|
|
|
|
|
|
|
|
|
|
|
|
|
0.8 |
|
|
|
|
|
|
~ |
|
|
|
|
|
|
|
|
|
|
0 |
0.05 |
0.1 |
0.15 |
0.2 |
Fig.15. Influence of the friction coefficient 1.1 on the volume average plastic strain Ev and the frontal and lateral edge height hrc and he in scratching an elastic perfectly plastic material (e.-0.35 %) with a conical indenter (8=70.3 deg-7 X-1 00)
As a first approximation the frontal height to the penetration depth ratio hrclh is a linear function of the friction coefficient 1.1 (Fig. 15). The analogy with the 2D scratching suggests that such an evolution corresponds to a reduction in the depth of the strained volume(§ 3.2) and an increase in the average plastic strain in the material. We observe effectively that the volume average plastic strain Ev increases markedly with 1.1 from 0.95 to 1.61 as 1.1 increases from 0 to 0.2 (Fig.l5) and this increase is very similar to that of the frontal edge height hrc·
Apparent Friction Coefficient and Scratch Hardness
As expected, the apparent friction coefficient J.lo increases with the (real) friction coefficient 1.1 (Fig. 16): This increase is linear as commonly assumed and is well described in first
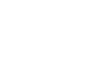
Mechanical analysis of the scratching of metals and polymers at moderate and large strains |
43 |
approximation by the classical relation of Bowden and Tabor for modelling the friction between solids [3]:
|
2 |
(21) |
||
|
|
|
Jio =-cote+ Ji |
|
|
|
|
7r |
|
0.45 |
|
|
, ----- . --- , . ---- , ---- , |
|
|
|
|||
|
|
|
J.lo |
|
0.4 |
|
|
|
|
0.35 |
|
|
\ |
|
|
|
(2in)coi8+1JI |
|
|
|
|
|
|
|
0.3 |
|
|
|
|
0.25 |
|
|
I |
|
|
|
|
|
0.2 L ______L______l_____L __ _,_J.I____JI
0 |
0.05 |
0.1 |
0.15 |
0.2 |
Fig. 16. Influence of the friction coefficient Jl on the apparent friction coefficient llo in scratching an elastic perfectly plastic material (Ee-0.35 %) with a conical indenter (9=70.3 deg~ X-1 00).
So our numerical simulation validates the model of Bowden and Tabor for 3D asperities similar to blunt cones or spheres with small penetrations. This model is different from the model proposed by Goddard and Witman for acute cones [35] where the adhesion term is pondered by 2/(7tsin9) and which is based on three main assumptions:
+the contact pressure is uniform: in fact it is sufficient in first approximation that the lines of equal contact pressure are parallel to the contact boundary (Fig. 5b) and it is effectively the case in the numerical simulation;
+the contact is limited on the frontal part by half of a circle and the flow lines at the contact surface are contained in planes parallel to the initial material surface. In fact the increase in frontal edge height produces only a slight increase in the ploughing term; therefore the form of the adhesion term suggests that the flow lines at the contact surface are contained in planes paraiiel to the plane x=O: it is not surprising in fact that this blunt cone does not induce a very significant sliding velocity component perpendicular to the scratch speed.
An unexpected result is that for a given penetration depth the normal force W does not vary significantly with the friction; as the contact width bc-b is also constant, it implies that the apparent scratch hardness Hs112 and the residual groove profile is quasi-independent on the friction for a given value of the normal force. This surprising result is in fact in agreement with experiments: the apparent scratch hardness of metals does not depend on the conditions of lubrication [4] and the residual groove profile does not vary significantly with the apparent friction coefficient [36].
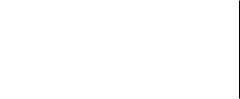
44 |
Scratching of materials and applications |
|
3 , ------- , ----- · - , ------- . ------- . |
|
other simulation |
|
|
|
Hs/o0 |
' |
|
|
|
|
I |
1.5 |
|
j···-...____ |
~ |
|
|
|
|
|
|
|
|
p/cr |
(20 scratching) • • • |
[ |
|
|
0 |
|
|
1 L _______ j _______c______l_____.I.I_Ji |
||||
0 |
0.05 |
0.1 |
0.15 |
0.2 |
Fig.17. Influence of the friction coefficient Jl on the scratch hardness H5 in scratching an elastic perfectly plastic material (E0-0.35 %) with a conical indenter (8=70.3 deg~ X-100); Comparison with the contact pressure p in 2D equivalent scratching.
It is interesting to note that for such a blunt indenter and a less elastic solid (X= 1rf), the indentation force also does not vary significantly with friction, but the increase of friction from
0 to the maximal value (friction stress equal to the yield shear stress =a0 I J3) produces a decrease of the shape ratio c from 1.25 to 1.16 and an increase of the contact pressure from 2.6 cro to 3.12 cro [30]. On the contrary, in scratching, because the frontal edge height increases, the (true) scratch hardness decreases as friction increases (Fig. 17): this decrease is initially limited, but becomes more marked for Jl:?: 0.1. Such an evolution is in agreement with the theory of the junction growth of Tabor [3]. It is easy to deduce from the current SLF model of ploughing [21] the evolution of the true scratch hardness for the equivalent wedge and the corresponding line is reported on Fig. 17 as p/o0: The decrease of p with 1.1 is linear and so it appears a shift between this line and the numerical results for Jl :<::; 0.1, but for Jl:?: 0.1, the slope of the p line is very close to the slope of the line passing through the numerical values ofH5 •
COMPARISON OF SCRATCHING OF WORKHARDENED STEEL AND POLYCARBONATE AT LOW AND HIGH STRAINS
Here we study the scratching ofworkhardened steel and polycarbonate (Table 2) performed with cones whose semi-apical angle 8 decreases from 70.3 to 20 (or 30) deg. One of the main objectives is to state precisely a transition from a ploughing flow to a cutting flow.
Scratching ofWorkhardened Steel
As expected in § 3 we observe such a transition for scratching of steel under zero friction (Fig. 18). For 8=70.3 and 60 deg, the material piles up on the frontal surface of the indenter, the reduction in e producing only a significant increase in the frontal edge height. But for 8= 45 and 30 deg, this frontal edge becomes clearly a chip whose thickness decreases with the cone angle.
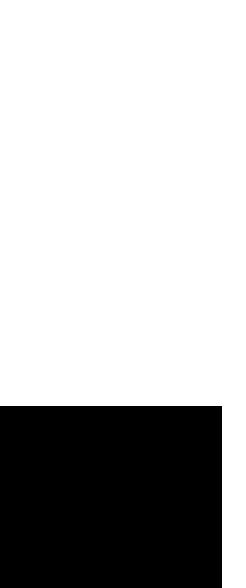
Mechanical analysis ofthe scratching of metals and polymers at moderate and large strains |
45 |
In all cases as expected the elastic recovery is small and the contact remains restricted on the frontal part of the indenter inside about half of a circle. So despite the change in the flow pattern the apparent friction coefficient llo is well predicted by the relation (7).
|
|
|
|
|
|
0 |
2 |
4 |
6 |
8 |
Fig. 18. Influence of the semi-apical angle 9 of a conical indenter on the scratch geometry (side view; plane x==O) an elastic perfectly plastic solid (Ee-{).35 %) (!J.=O).
The apparent scratch hardness H5112 is always greater than the (true) scratch hardness H5 (Fig. 19). But Hs decreases steadily with the cone angle and attains for 9=30 deg a value -1.12 cr0 , a little greater than the flow stress; H5112 decreases in a first time, but remains constant and equal to -1.6 cr0 for 9= 45 and 30 deg where a chip is formed (Fig. 19). Brookes et. al. [4] observed such an evolution for workhardened metals and reported that some chip is formed for 9 :::;45 deg. It is interesting to see that to a first approximation the evolution ofHsu2 is very close to the evolution of the contact pressure p for the equivalent wedge scratching (relations (10) and ( 13)) for 9 ~ 45 deg (Fig. 19).
3,----,-----,-,---,-----.----~
Cuttingploughing
2.5
2
1.5
40 |
50 |
60 |
70 |
80 |
Fig. 19. Influence of the semi-apical angle 9 of a conical indenter on the scratch hardness of an elastic perfectly plastic solid (Ee-0.35 %) (!J.==O); Comparison with the contact pressure p in 2D equivalent scratching.
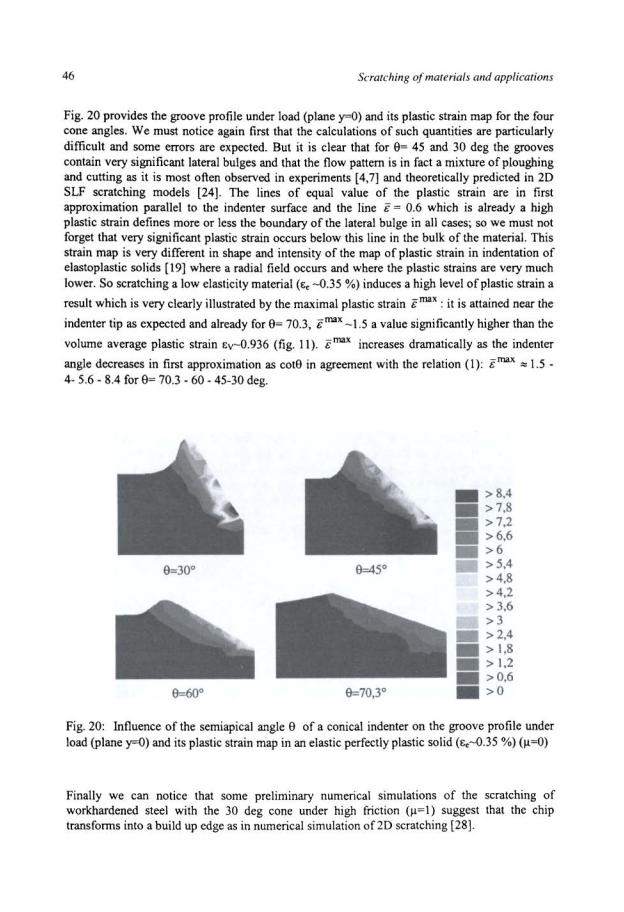