
книги / Основы конструирования авиационных двигателей и энергетических установок. Т. 4 Динамика и прочность авиационных двигателей и энергетических установок
.pdf/. I0. Модели упруго-пластических деформаций. Метод переменных параметров упругости
модель идеального упруго-пластического тела (кри вая 2), в которой пренебрегают упрочнением мате риала при пластической деформации. По мере на гружения при напряжениях менее предела текучести < Тдеформация упругая, она увеличивается пропор ционально напряжению (кривая 1). При дальней шем нагружении деформация увеличивается без увеличения напряжений. Благодаря своей простоте модель используется для оценки эффектов пласти ческой деформации в аналитических расчетах. Эта модель позволяет получать количественные резуль таты с достаточной для практики точностью лишь для весьма пластичных материалов (низкоуглеро дистых нелегированных сталей, например). Далее в порядке увеличения точности следуют модели ли нейного (кривая 3) и степенного (кривая 4) упроч нения. Последние наиболее близки к реальной кри вой упрочнения материала. При использовании современных численных методов обычно использу ются модели того уровня точности, который обес печивается экспериментальными данными о плас тической деформации материала.
Система уравнений, описывающая упруго-пла стическое напряженно-деформированное состоя ние тела, отличается от системы уравнений теории упругости только соотношениями между деформа циями и напряжениями. Она включает в себя урав нения равновесия (1.4), условия совместности де формаций (1.13), физические уравнения для упру го-пластического тела (1.34), а также соотношение (1.37) для параметра пластичности \|/. Решение дол жно, кроме того, удовлетворять граничным усло виям в перемещениях и напряжениях.
Рассмотрим предложенный И.А.Биргером метод расчета упруго-пластического напряженного состо яния - метод переменных параметров упругости. Он сводит упруго-пластическую задачу к цепочке уп ругих задач и реализации процесса последователь ных приближений. В основе метода лежит исполь зование обобщенного закона Гука, в котором модуль упругости и коэффициент Пуассона зависят от на пряжений и поэтому имеют разные значения в раз ных точках тела.
Уравнения обобщенного закона Гука записыва ются в виде:
Параметры ZT, G*и |Г зависят от отношения ин тенсивностей напряжений и деформаций. В част ном случае, когда пренебрегают сжимаемостью материала:
£ * = 3 G - = ^ - n * = 0,5 |
(139) |
bi |
|
Процесс последовательных приближений реа лизуется следующим образом. В первом прибли жении принимается, что переменные параметры ZT, G* и \1 равны параметрам упругости, и реша ется упругая задача, в результате чего определяют ся компоненты напряжения и деформации перво го приближения схУ ...., ..., у^,,,... По этим величинам в каждой точке тела вычисляются интенсивности напряжений и деформаций в пер вом приближении а., ив, . В координатах а, - е. (см. рис. 1.13) напряженное и деформированное со стояние некоторой точки тела изображается точкой 1, лежащей на луче, тангенс угла наклона которого пропорционален Е*: в соответствии с (1.39) она при нимается равной отношению интенсивности напря жений a* j к интенсивности деформаций E.J по ди аграмме a - & (см. рис. 1.13). Параметры Е *и G* будут различными в разных точках тела. Таким об разом, возникает задача определения напряжений в условно неоднородном теле, параметры упругос ти в различных точках которого различны. Далее ре шают эту задачу, определяют компоненты напряже ния и деформации с х2> ..., тп2, ..., ег2,..., у^,...
е , = - ^ , - И * ( к + < 0 } - а Г ’- 4 r - = ] S -
е.- = Jr[cf.,-H * (r,+ C T v)]+a r ' =
(1.38) |
Рис. 1.13. Метод переменных параметров упругости |
21
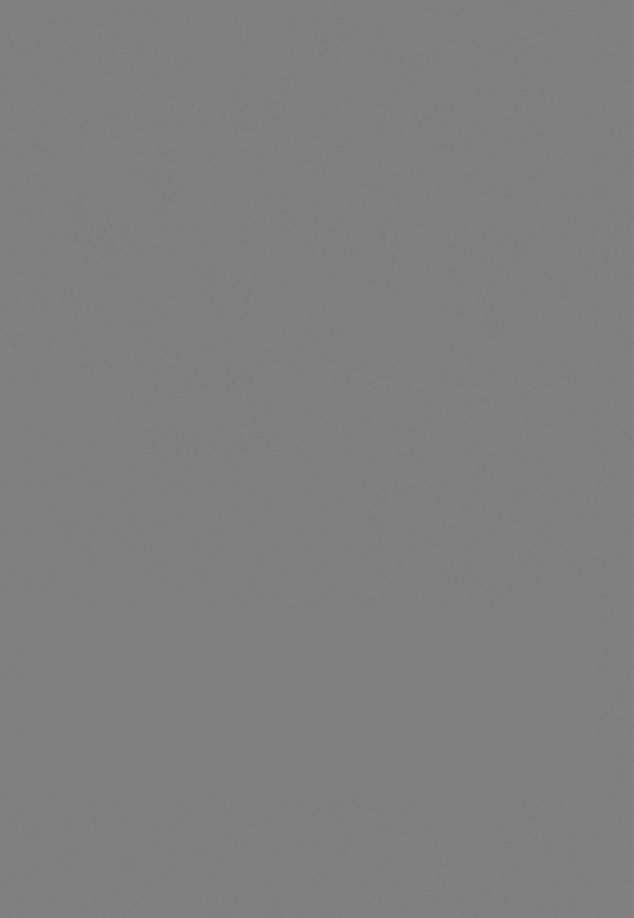
1.12. Ползучесть. Релаксация напряжений. Длительная прочность
Отсюда видно, что с увеличением изгибающе го момента пластическая зона постепенно увели чивается, и при некотором предельном значении изгибающего момента М ред все сечение стержня переходит в пластическое состояние (см. рис. 1.14, д). Дальнейшее увеличение изгибающего момента в рамках принятой модели идеального упруго-пла стического материала невозможно: образуется так называемый пластический шарнир. Предельный изгибающий момент Мпреддает оценку предельной несущей способности стержня, его значение вы текает из (1.43) при hx= 0: Мпред = GTbh2/4.
При разгрузке уменьшение напряжений пропор ционально уменьшению деформаций. В случае сложного напряженного состояния эта же зависи мость формулируется в отношении интенсивнос тей напряжений и деформаций:
а /разгр = Е г./разгр |
(1.44) |
Напряжения и деформации разгрузки могут быть определены из решения задачи теории упру гости для внешних сил, равных разностям сил при нагружении и остающихся после разгрузки. В слу чае полной разгрузки решается задача теории уп ругости для внешних сил, нагружающих тело. Это справедливо в том случае, если при разгрузке ма териал не выходит вновь за пределы упругости.
Поле остаточных напряжений удовлетворяет уравнениям равновесия и граничным условиям по напряжениям, соответствующим нагрузкам, остав шимся после разгрузки. В случае полной разгруз ки поле остаточных напряжений должно быть самоуравновешенным. Остаточные напряжения и деформации определяются как разность напря жений и деформаций, достигнутых на стадии на грузки, и напряжений и деформаций разгрузки:
а |
ij ост |
= а |
ij |
- а.. |
|
|
|
|
ij разгр; |
|
|||
£у ост |
= £ij - £ ij разгр |
(1.45) |
Вернемся к ситуации, когда в стержне под дей ствием изгибающего момента М возникла пласти ческая зона размером h - h xи рассмотрим процесс разгрузки. Напряжение разгрузки, получающееся из решения упругой задачи для изгибающего мо мента М, изменяется по высоте сечения стержня линейно:
, . М |
12М |
|
° ра„р( у ) = -] |
-у = ~ъё у |
(L46) |
где I - момент инерции сечения стержня. Остаточное напряжение определяется как раз
ность напряжения, определяемого соотношением
(1.41) и напряжения разгрузки:
^ ( у ) = о (у )-а ^ (у ). |
(1.47) |
Поле остаточных напряжений показано на рис. 1.14, в. Видно, что на верхней поверхности, в волокнах которой под нагрузкой возникает рас тягивающее напряжение, остаточное напряжение - сжимающее и составляет:
GOCT(/Z/2) = а т - 6M/bh2. |
(1.48) |
На нижней поверхности остаточное напряжение имеет такую же величину, но противоположный знак. Из рис. 1.14, в видно, что поле остаточных напряжений - самоуравновешенное: сумма проек ций всех напряжений на ось х равна нулю. Кроме остаточных напряжений в стержне возникают ос таточные деформации и перемещения (прогиб). В рассматриваемой задаче остаточный прогиб на правлен вверх, что и определяет знаки остаточных напряжений - сжатия в верхних волокнах и растя жения - в нижних.
При последующем нагружении остаточные на пряжения складываются с напряжениями от новой нагрузки. На рис. 1.14, г показано распределение напряжений в стержне при повторном нагружении моментом М,, величина которого несколько мень ше первоначально приложенного Л/, но больше момента Мг Суммарные напряжения при повтор ном нагружении оказываются меньше, чем при первом нагружении такого же момента Л/,.
Результирующие напряжения могут оказаться меньше или больше, чем в конструкции, не под вергавшейся пластической деформации. Поле ос таточных напряжений с этой точки зрения может быть благоприятным или неблагоприятным. В пер вом случае говорят о приспособляемости конструк ции и ее упрочнении (автофретировании) путем предварительной деформации. В частности, благо приятные поля остаточных напряжений возника ют при предварительной пластической деформа ции дисков ГТД.
1.12. Ползучесть. Релаксация напряжений. Длительная прочность
Напряжения и деформации, возникшие при на гружении деталей, изменяются во времени, даже если нагрузки остаются постоянными. Это явле ние называется ползучестью материала. Одна сто рона этого явления — изменение во времени де формаций — называется собственно ползучестью или последействием, а вторая — изменение напря
23
Глава L Основы анализа прочностной надежности двигателей
жений — релаксацией. Ползучесть может приво дить к недопустимому увеличению необратимой деформации детали или конструкции, и ее разру шению при напряжениях ниже предела прочнос ти. Примером негативного проявления ползучести может служить постепенное необратимое удлине ние лопаток ротора газовой турбины, которое мо жет привести к задеванию лопаток о статор и зак линиванию ротора.
Задачами расчета конструкций на ползучесть яв ляются определение деформаций, накапливаемых в конструкции во время работы, и определение вре мени до разрушения детали.
На рис. 1.15 проиллюстрирован процесс ползу чести, происходящий при одноосном растяжении стержня под действием постоянного во времени напряжения.
Деформация, возникшая мгновенно при прило жении нагрузки (отрезок ОА на рис. 1.15), упругая: она равна G /E. С течением времени при постоянной нагрузке появляется и постепенно увеличивается пластическая деформация - деформация ползучес ти (кривая А-А3). При этом наблюдаются три харак терных участка. На первом (А-Ах) деформация рас тет относительно быстро, затем замедляется и на участке А х-А2растет с постоянной скоростью. Учас ток Ах-А, называют участком установившейся пол зучести. На третьем участке (А0-А3) скорость дефор мации снова возрастает, и в точке А3 происходит разрушение.
Рассмотренную зависимость деформации от вре мени при постоянном напряжении называют кри вой ползучести. Семейство кривых ползучести, по лученных при разных напряжениях и температурах, является основной характеристикой ползучести материала и определяется экспериментально.
Если в момент времени, соответствующий точ ке В (см. рис. 1.15), снять нагрузку, происходит уменьшение деформации. Сначала деформация скачкообразно уменьшается на величину упругой деформации (участок ВС), а в дальнейшем падает постепенно (кривая CD). Это явление называется обратным последействием или обратной ползуче стью.
Ползучесть проявляется при напряжениях, меньших предела текучести материала. Кривые ползучести при постоянном напряжении для боль ших значений напряжений располагаются выше, что соответствует более высокой скорости дефор мации ползучести и меньшему времени до разру шения t3<t2< tx(см. рис. 1.16, а).
Существенное влияние на процессы ползучес ти оказывает температура. В металлах ползучесть проявляется при высоких температурах, начиная приблизительно с 35 % абсолютной температуры плавления. В полимерных материалах ползучесть проявляется при комнатной температуре. Ско рость ползучести всех материалов при более вы соких температурах выше, а время до разрушения меньше, чем при более низких температурах (см. рис. 1.16,6).
Одно из важных в практическом отношении проявлений ползучести - релаксация напряжений. Она проявляется в ситуации, когда тело нагруже но и зафиксировано таким образом, что суммар ная деформация его не может изменяться. Напри мер, растянутый и закрепленный в растянутом положении стержень. Другой пример - растянутый при затяжке болт, соединяющий две детали. Пол ная деформация, не изменяющаяся во времени, представляет собой сумму упругой деформации Ее
и пластической деформации ползучести Ес (индекс
с- начальная буква английского «creep» -ползу честь):
е = 8 + в |
с |
= const |
(1-49) |
|
е |
|
' |
' |
|
Рис. 1.16. Кривые ползучести: |
|
Рис. 1.15. Ползучесть при постоянном напряжении и в цик |
а - при различных напряжениях а х<а,<о3; |
|
б - при различных температурах Т(<Т2<Т3 |
||
ле нагрузка-разгрузка |
||
|
24
1.12. Ползучесть. Релаксация напряжений. Длительная прочность
В момент нагружения t = 0 деформации ползу чести еще нет, суммарная деформация равна упру гой. Напряжение определяется из закона Гука: а(0) = £а(0). Подставляя в (1.49) получаем:
Е |
Е |
cl ' |
(1.50) |
|
Из (1.50) следует, что при увеличении с течени ем времени пластической деформации напряжение будет постепенно уменьшаться (см. рис. 1.17). Ре лаксация напряжений может иметь негативные по следствия, выражающиеся, например, в ослаблении затяжки болтовых соединений. Другим примером негативного проявления релаксации является посте пенное снижение остаточных напряжений, создан ных в конструкции с целью ее упрочнения.
Релаксация проявляется также в постепенном снижении напряжений и увеличении пластических деформаций в зонах концентрации напряжений.
Таким образом, ползучесть проявляется в том, что напряжения и деформации в теле при заданной нагрузке зависят не только от пространственных координат, но и от времени.
Важной характеристикой сопротивления мате риала ползучести является предел ползучести. Так называется напряжение, при котором пластическая деформация за заданный промежуток времени до стигает заданной величины. При обозначении пре дела ползучести указывают величину деформации, время и температуру. Например, для жаропрочно го никелевого сплава ХН77ТЮР для предельной деформации 0,2 % при температуре 700° С и вре мени 100 часов предел ползучести
< 2/их, =400МПа
Математические модели ползучести опирают ся обычно на следующие согласующиеся с экспе риментальными данными положения.
а
Деформацию, вызываемую действующей на грузкой и нагревом, представляют как сумму де формаций упругости, пластичности, ползучести и теплового расширения. Аналогичным образом представляют приращение полной деформации:
dz=dz +dt +dz +Ш |
(1.51) |
||
е р |
с |
' |
' |
В трехмерном напряженно-деформированном состоянии приращение отдельных компонент де формаций ползучести принимается в виде:
dExc = 0 dt(ax - a o), |
|
dixyc!2 = 0 -d t-x ^ .... |
(1.52) |
где t - время;
Ф - функция ползучести, определяемая на основании экспериментальных данных;
а 0 - среднее напряжение (а0 = ( а + а + а , )/3). Существует несколько гипотез (иногда их на
зывают теориями) ползучести, различающихся видом этой функции. В теории течения прини мают Ф = Ф(а. , Т t) в теории упрочнения Ф = Ф( а . , Т, е ,с) , (здесь а -интенсивность на пряжений, е ,с- интенсивность накопленной дефор мации ползучести).
Остановимся подробнее на теории старения. Согласно этой теории предполагается, что при за данной температуре между напряжением, деформа цией и временем существует постоянная зависи мость Ф(а, е, /) = 0 . Для сложного напряженного состояния вместо напряжений и деформаций в этой зависимости записываются их интенсивности.
Эта зависимость представляет собой поверх ность в координатах а, е, t (см. рис. 1.18). Данные для ее построения определяются из семейства кри вых ползучести при разных напряжениях и темпе ратурах (см. рис. 1.16). Рассекая ее плоскостью
Рис. 1.17. Релаксация напряжений |
Рис. 1.18. Поверхность Ф(а, Е, т) = 0 в теории старения |
25
Глава 1. Основы анализа прочностной надежности двигателей
о= const, получаем кривые ползучести, е = const - кривые релаксации, t = const - изохронные (при одинаковом времени) кривые деформации.
Для момента 1= 0 изохронная кривая представ ляет собой диаграмму а - е, получаемую при обыч ных кратковременных испытаниях. Для последу ющих моментов кривая проходит ниже (см. рис. 1.18), что можно интерпретировать как посте пенное снижение сопротивления материала дефор мации (отсюда название «старение»). Когда изох ронные кривые найдены, задача сводится к расчету деформаций в упруго-пластическом теле по дефор мационной теории.
Модели ползучести, основанные на теории ста рения, позволяют описывать процессы ползучести при постоянном напряжении, монотонном нагруже нии, релаксацию. Один из основных недостатков теории старения состоит в том, что не учитывается история нагружения. От этого недостатка свобод ны теории течения и упрочнения, несколько более сложные в реализации. Более подробные сведения
оних можно найти в специальной литературе (см., например [14]).
Эффект ползучести, как отмечалось выше, про является при напряжениях, ниже предела текучес ти материала, и при таких напряжениях может при водить к разрушению конструкции. В отличие от обычных кратковременных испытаний на растяже ние, ползучесть приводит к разрушению не сразу, а по прошествии некоторого, возможно длительно го, периода времени. Это явление характерно для разрушения деталей горячей части авиационных двигателей. Его опасность состоит в том, что крат ковременные (например, сдаточные) испытания двигателя не позволяют выявить дефекты, связан ные с ползучестью, и разрушение детали может произойти через несколько лет эксплуатации.
Прочность материала при высоких температу рах характеризуется пределом длительной прочно сти. Пределом длительной прочности называется напряжение, которое может выдержать материал без разрушения в течение заданного времени при данной итемпературе. Предел длительной прочно сти не следует путать с пределом ползучести. При обозначении предела длительной прочности указы ваются температура и время. Например, для жаро прочного никелевого сплава ХН77ТЮР при темпе ратуре 700° С и времени 100 часов предел длительной прочности a J^oo = ЪЪОМПа (для сравнения - пре дел ползучести пр^той же температуре и времени несколько выше CJ 0 2| 100 = 400М77я;при той же тем
пературе при кратковременных испытаниях предел прочности ав = 830 МПа).
Зависимость предела длительной прочности от времени (см. рис. 1.19) представляют в виде степен ной зависимости:
ст'”)71 = С,откуда t = Cc~,,\h , |
(1.53) |
где С и AW- экспериментально определяемые характеристики материала, зависящие от температуры.
Показатель степени т для различных материа лов лежит в пределах 4...20, поэтому даже незна чительное изменение напряжения приводит к суще ственному изменению долговечности. С увеличени ем температуры предел длительной прочности заметно снижается (см. рис. 1.19).
Другой вариант представления зависимости предела длительной прочности от времени и тем пературы - обобщенная кривая Ларсона-Миллера [11] (см. рис. 1.19, б): если по оси абсцисс откла дывать не время, а параметр Ларсона-Миллера Р = 71(20 + Igt), кривые для различных температур с некоторым рассеянием ложатся на одну кривую. В расчетах принимают статистически минималь ное значение, как показано на рис. 1.19, б.
При обеспечении прочности авиационной тех ники принято оперировать коэффициентами запа са прочности. При постоянном по времени напря жении G и времени нагружения t определяют запасы прочности по напряжениям па и по долго вечности п0 равные, соответственно:
где ар и tp - разрушающее напряжение и время до разрушения.
Пользуясь соотношением (1.53), связывающим долговечность с напряжением можно получить связь между этими коэффициентами запаса:
П , = <
а |
б |
Рис. 1.19. Зависимость предела длительной прочности от
времени и температуры. Г, < Т2 < Ту
а - в логарифмических координатах; б - в форме
обобщенной кривой Ларсона-Миллера
26
Учитывая, что для конструкционных материа лов т = 4.. .20, оказывается, что запас по долговеч ности должен быть во много раз больше, чем по напряжениям, так, например, пятикратный запас по долговечности соответствует при т = 4 неболь шому запасу по напряжениям па= 1,5.
1.13. Усталостное разрушение элементов конструкций
Усталость - процесс постепенного накопления повреждений в материале, обусловленный цикли ческим действием нагрузок. Именно усталость яв ляется основной причиной разрушения элементов машиностроительных конструкций, в частности, авиационных двигателей. Особенность усталост ного разрушения состоит в том, что оно может иметь длительный инкубационный период, состав ляющий иногда годы эксплуатации изделия, в те чение которого выявление признаков приближаю щегося разрушения затруднительно. Механизмы усталостного разрушения для разных материалов
иусловий многообразны и чувствительны к мно жеству случайных факторов, что затрудняет рас четы, требует проведения большого объема экспе риментальных работ.
Выделяют малоцикловую и многоцикловую усталость, имеющие совершенно различные меха низмы и закономерности разрушения. Для мало цикловой усталости (МЦУ) характерно появление пластических деформаций в макроскопических (в несколько миллиметров и более) объемах мате риала в каждом цикле нагружения. Такой механизм разрушения реализуется при значительных цикли ческих нагрузках, и деталь выдерживает до полом ки не более 104... 105 циклов нагружения. МЦУ свя зана с изменением режима работы двигателя во время эксплуатации, что приводит к изменению статических напряжений в деталях; при длитель ной эксплуатации количество циклов изменения напряжений доходит до десятков тысяч, а ампли туда может превышать предел текучести. Накоп ление повреждений при МЦУ часто определяет ресурс работы деталей, работающих при повышен ных температурах, например, дисков, рабочих
исопловых лопаток турбины, элементов камер сгорания ГТД. Процессы разрушения при МЦУ рассмотрены в следующем разделе, здесь мы ос тановимся на закономерностях многоцикловой ус талости.
Многоцикловая усталость обычно связана с виб рациями. Переменные напряжения имеют сравни тельно небольшую амплитуду (значительно ниже предела текучести), но количество циклов нагру жения за время эксплуатации достигает миллиар
У.УЗ. Усталостное разрушение элементов конструкции
дов. Характерная особенность такого разрушения
-отсутствие макроскопических пластических де формаций в материале. Многоцикловая усталость
-определяющий процесс разрушения для многих деталей ГТД (лопатки, валы, шестерни).
Процесс усталостного разрушения принято де лить на две стадии. На первой под действием пе ременных напряжений происходят необратимые изменения в структуре металла, связанные с пере мещением микродефектов вследствие локальной концентрации напряжений на случайных неодно родностях исходной структуры материала. При слиянии микродефектов образуются микротрещи ны, объединяющиеся при дальнейшем цикличес ком нагружении в макроскопическую магистраль ную трещину, размеры которой соизмеримы
сразмерами зерна и составляют десятые доли мил лиметра. На второй стадии процесса усталостно го разрушения происходит рост макроскопической трещины, заканчивающийся окончательным раз рушением детали. Процессы, связанные с разви тием макроскопических трещин, рассмотрены ниже в разд. 1.15.
Упрощенно переменные напряжения представ ляют изменяющимися во времени по простому си нусоидальному циклу, который характеризуется
максимальным а max и минимальным а mm значениями, а также частотой/ = 1//ц (см. рис. 1.20). Чаще для характеристики переменных напряжений ис
пользуют амплитуду а д, среднее напряжение с т и коэффициент асимметрии цикла R:
а |
а |
= 0,5(а |
max |
- а |
|
); |
|
|
|
|
’ v |
|
m in7 ’ |
|
|
||||
а |
т |
=0,5(о |
mix |
+ о |
.); |
(1.55) |
|||
|
’ v |
|
|
|
min7’ |
v |
' |
Рис. 1.20. Характеристики цикла переменных напряжений
27
Глава 1. Основы анализа прочностной надежности двигателей
Если среднее напряжение цикла нулевое с т= О, цикл называют симметричным, для него R = -1. Цикл с Gmin = 0 и R = 0 называют пульсирующим.
Для определения характеристик усталостной прочности материалов проводят специальные ис пытания. Образцы нагружают переменным напря жением с заданными амплитудой и коэффициен том асимметрии и определяют количество циклов до разрушения N?. Если образец не сломался до некоторого базового числа циклов NB(обычно это 20 или 100 миллионов циклов), испытание прекра щают. Количество циклов до разрушения одина ковых образцов при одном и том же напряжении может различаться в несколько раз, или даже в де сятки раз вследствие рассеяния свойств материа ла; в связи с этим говорят о статистической приро де усталости.
По результатам испытаний серии образцов стро ят график зависимости числа циклов от амплиту ды (см. рис. 1.21). В логарифмических координа тах он состоит из двух прямолинейных участков. Точка перелома соответствует значению N0 при мерно равному 107 циклов.
Некоторые материалы имеют физический пре дел выносливости (предел усталости), под которым подразумевается максимальное напряжение, не вы зывающее разрушения детали при любом количе стве циклов нагружения. В этом случае правая ветвь кривой усталости параллельна оси абсцисс. Для симметричного цикла с R = -1 предел выносливос ти обозначают а Ц в е т н ы е металлы и сплавы фи зического предела выносливости не имеют, и пра вая ветвь кривой усталости не горизонтальна, но имеет меньший наклон, чем левая. В этом случае под a j подразумевают условный предел выносли вости при базе Nb.
В логарифмических координатах левую ветвь кривой усталости обычно аппроксимируют прямой:
Рис. 1.21. Кривые усталости по результатам испытаний
c mNp = C, |
(1.56) |
где / и и С - характеристики материала; обычно т = 4...12.
Для обеспечения усталостной прочности детали необходимо, чтобы рабочая амплитуда вибронапря жений о а была ниже предела выносливости а а< а г Предел выносливости весьма чувствителен к вли янию конструктивных, технологических и эксплу атационных факторов. В реальных деталях он су щ ественно ниже значения, получаемого при испытаниях образцов.
Наличие в детали концентраторов напряжений существенно снижает ее усталостную прочность. Для оценки этого снижения используют эффектив ный коэффициент концентрации, равный отноше нию предела усталости гладкого образца а , к пре делу усталости о 1Jt образца с концентратором:
*„=<*,/О U |
О '57) |
Как показывают результаты испытаний, этот ко эффициент заметно ниже теоретического (получа емого из решения задачи теории упругости) коэф фициента концентрации а а :
K = l+ q(ag- l) , |
(1.58) |
где q - коэффициент чувствительности к концен трации напряжений.
Для хрупких материалов q близок к единице и эффективный коэффициент концентрации бли зок к теоретическому, для пластичных материа лов q < 1. Для литых материалов q = 0,1.. .0,2, для малоуглеродистых сталей и жаропрочных нике левых сплавов q = 0,2.. .0,4, для титановых спла вов - д о 0,8... 0,9.
Весьма существенно влияние на предел вынос ливости состояния поверхностного слоя детали, характеризующегося чистотой поверхности, накле пом, остаточными напряжениями. Отношение пре дела выносливости стандартного образца а , с эта лонным поверхностным слоем (обычно образцы полируют) к пределу выносливости образца а ш с такими же характеристиками поверхностного слоя, как у детали:
Р = о , / о ш |
(1.59) |
отражает влияние технологических факторов на усталостную прочность. Он может быть представ лен произведением коэффициентов, отражающих влияние отдельных факторов: чистоты поверхнос ти, поверхностного упрочнения, коррозии.
28
йестно, что предел выносливости крупных деталей ниже, чем у стандартных образцов. Это - масштабный эффект, который объясняется боль шей вероятностью наличия микроскопических де фектов материала в большем объеме. Иэффициент масштабного фактора:
e, = o , / o -w > |
0.60) |
где с Ad - предел выносливости образца с диа метром d.
Предел выносливости при наличии среднего ра стягивающего напряжения цикла заметно снижа ется по сравнению со случаем симметричного на гружения. Влияние асимметрии цикла определяют экспериментально, проводя специальные испыта ния образцов при несимметричном цикле нагру жения. Результаты этих экспериментов можно представить в виде диаграммы предельных напря жений (см. рис. 1.22, а) или в виде диаграммы пре дельных амплитуд (см. рис. 1.22, б). На первой при водятся максимальное и минимальное напряжения цикла в зависимости от среднего, на второй - амп литуда. Диаграмму предельных амплитуд часто ап проксимируют линейной зависимостью (кривая 2):
=W m.
(1.61)
где \|f - коэффициент влияния асимметрии цикла; <5Ь- предел прочности материала.
Для материала реальной детали предел вынос ливости оЛдвт с учетом перечисленных факторов равен:
Ре |
f 1 |
а т Л |
|
-1 дет |
1- |
— |
(1.62) |
|
|
GbJ |
|
Рис. 1.22. Влияние среднего напряжения цикла на характе
ристики усталостной прочности. Диаграммы пре
дельных напряжений (а) и предельных амплитуд
(б)
1.13. Усталостное разрушение элементов конструкции
Коэффициент запаса усталостной прочности вво дится как отношение предела выносливости с уче том влияния конструктивных, технологических и эксплуатационных факторов к амплитуде пере менных напряжений, возникающих в детали во вре мя работы:
* v = < W < V |
(1.63) |
|
Следует отметить, что расчет коэффициента за паса по соотношениям (1.62), (1.63) с использовани ем справочных данных о значениях предела вынос ливости стандартных образцов при симметричном цикле нагружения может привести к значительным погрешностям. В соотношении (1.62) учтены не все факторы, влияющие на предел выносливости: ра бочая температура, форма цикла напряжений, час тота нагружения и т.д. Данные о влиянии этих фак торов приведены в многочисленных литературных источниках (см., например [11]). Поправочные ко эффициенты, входящие в (1.62), сами зависят от марки материала, термообработки, температуры и других факторов. Для правильной оценки пре дела выносливости эти коэффициенты (а не толь ко предел выносливости при симметричном цик ле) необходимо определять на образцах, имеющих тот же химический состав, структуру, что и натур ная деталь, при рабочей температуре. Для того, чтобы учесть влияние конструктивных и техноло гических факторов, в ряде случаев при проведе нии испытаний в качестве образцов используют на турные детали и проводят испытания в условиях, максимально приближенных к эксплуатационным. В частности, именно так определяют пределы вы носливости лопаток компрессоров и турбин ГТД.
Как отмечалось, результаты усталостных испы таний имеют значительное рассеяние. Поэтому чис ло циклов до разрушения при заданном напряже нии и предел выносливости являются величинами случайными и должны характеризоваться не толь ко средним значением, но и законом распределения. Если провести испытания большого количества об разцов так, чтобы на каждом уровне напряжений было испытано их несколько десятков, можно по лучить кривые усталости для разных значений ве роятности разрушения (см. рис. 1.23). Такие кривые позволяют статистически обосновать нормативное значение запаса усталостной прочности (1.63). Обычно принимают К^> 3...5, что значительно больше коэффициентов запаса по статическим на пряжениям.
Смысл статистического подхода проиллюстри рован на рис. 1.24. Кривые плотности распреде ления двух случайных величин - амплитуды пе ременных напряжений и предела выносливости пересекаются. Это означает, что существует ве-
29
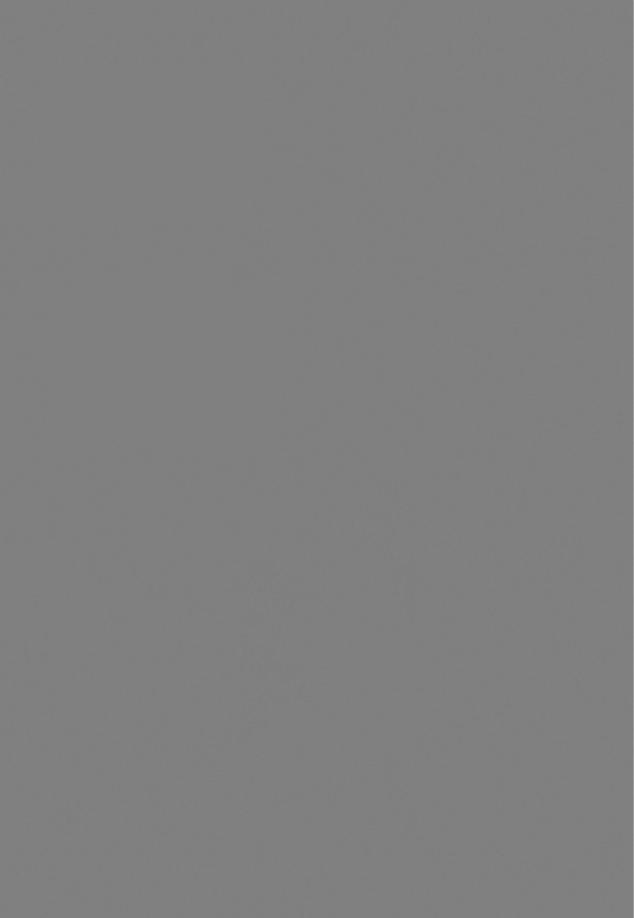