
книги / Технология производства и методы обеспечения качества зубчатых колес и передач
..pdfМеханическая обработка конических зубчатых колес. |
161 |
Н
Рис. 4.8. Направление смещений на контрольно-обкатном станке
Нужное положение пятна контакта обеспечивается путем внесения поправок к осе вой установке и гипоидному смещению, выявленному на контрольно-обкатном станке (табл. 4.11), в зуборезный станок с теми же абсолютными значениями, но с обратным знаком. Этот способ следует применять при смещениях, не превышающих 0,021. Если они более 0,021, рекомендуется величины изменения осевой установки и гипоидного смещения рассчитывать с учетом поправки к передаточному отношению обкатки, ради альной и угловой установки резцовой головки.
Основные причины погрешностей, возникающих при нарезании конических колес с круговыми зубьями, приведены в табл. 4.12, а достигаемая точность станков для нареза ния таких колес — в табл. 4.13. При назначении норм точности на оснастку можно пользо ваться данными табл. 4.14.
Номинальные режимы резания приведены в табл. 4.15. В зависимости от обрабаты ваемого материала используются поправочные коэффициенты (табл. 4.16). В результате скорость резания и время обработки одного зуба определяются по формулам
^ —^таГм в (г тайл ^ tz •
Машинное время при нарезании конических спиральнозубых колес по методу обкат ки или кругового протягивания равно
T„-t2z/60,
где tz — время на обработку одного зуба, с.
Форму и высоту пятна контакта изменяют путем регулирования профильной кривиз ны за счет гипоидного смещения в наладке станка, внесения поправок в передаточное от ношение обкатки, осевой установки и др.
162 |
|
|
|
Глава 4 |
|
Н а п р а в л е н и е см е щ е н и я |
Н а п р а в л е н и е сп и р а л и |
С то р о н а зу ба |
С м е щ е н и я н а к о н т р о л ь н о -о б к а т н о м |
||
п я т н а к о н т а к т а |
п а ш ес тер н е |
н а ш естерне |
с та н к е |
||
|
Регулирование пятна контакт а по высоте за счет осевом установки |
||||
С головки к ножке |
Правое |
|
Выпуклая |
Увеличить монтажный размер |
|
|
|
Левое |
|
Вогнутая |
|
С ножки к головке |
Правое |
|
Выпуклая |
Уменьшить монтажный размер |
|
|
|
Левое |
|
Вогнутая |
|
|
Регулирование пятна контакта но длине за счет гипоидного смещения |
||||
От носка к пятке |
Правое |
|
Выпуклая |
Гипоидное смещение вверх (- ) |
|
|
|
|
|
Вогнутая |
Гипоидное смещение вниз (+) |
|
|
Левое |
|
Выпуклая |
Гипоидное смещение вниз (+) |
|
|
|
|
Вогнутая |
Гипоидное смещение вверх ( - ) |
От пятки к носку |
Правое |
|
Выпуклая |
Гипоидное смещение вниз (+) |
|
|
|
|
|
Вогнутая |
Гипоидное смещение вверх ( - ) |
|
|
Левое |
|
Выпуклая |
Гипоидное смещение вверх ( - ) |
|
|
|
|
Вогнутая |
Гипоидное смещение вниз (+) |
|
|
|
|
|
Таблица 4.12 |
Погрешности, возникающие при нарезании конических колес с круговыми зубьями |
|||||
|
|
|
|
П о гр еш н о сть |
|
|
станка |
|
|
и н стр у м ен та |
наладки |
Накопленная погрешность шага Fpr отклонение шага f m биение зубчатого венца F„ |
|||||
Недостаточное усилие зажима |
Неточная |
установка резцовой |
Радиальное н торцевое биение |
||
Радиальное |
и осевое |
биенне |
головки — отсутствие плотной |
заготовки |
|
шпинделя резцовой головки |
посадки на посадочный конус с |
Увеличенный припуск под чис |
|||
Неточность |
кинематической |
упором па торец |
товое нарезание |
||
цепи взаимосвязанного порога |
|
|
Касание вершинами чистовых |
||
шпинделя изделия и люльки |
|
|
резцов дна впадины |
||
(цепи обкатка — деление) |
|
|
Неточность н нестабильность |
||
|
|
|
|
|
установки каретки до жесткого |
|
|
|
|
|
упора |
|
|
|
|
|
Неточная установка оправки |
|
|
|
|
|
изделия с плотной посадкой |
|
|
|
|
|
на посадочный конус с упором |
|
|
|
|
|
в торец |
|
|
Погрешность обката зубцовой част оты / сг |
|||
Радиальное и торцевое биение |
Неточность установки режу |
Неправильный угол профиля |
|||
шпинделя резцовой головки |
щих кромок резцов резцовой го |
резцов |
|||
|
|
|
ловки в одной плоскост и (бие |
Неполное профилирование зу |
|
|
|
|
ние, «веер») |
ба из-за недостаточного угла об |
|
|
|
|
|
|
ката |
|
|
|
|
|
Несовпадение середины угла |
|
|
|
|
|
качания с серединой цикла |
|
Механическая обработка конических зубчатых колес |
163 |
|
|
|
Продолжение таблицы 4.12 |
|
|
Погрешность |
|
|
станка |
инструмента |
| |
наладки |
Повышенная шероховатость па боковой поверхности зубьев в виде срезов за каждый оборот резцовой головки
Неточная установка резцовой головки (отсутствие плотной посадки на посадочный конус с упором в горец)
Нежесткое крепление резцовой головки Неточность установки режу
щих кромок резцов резцовой голоокн после установки головки на станке Режущие кромки резцов распо
ложены пол разными углами относительно оси вращения («веер»)
Различная высота резцов в рез цовой головке
Повышенная шероховатость па боковой поверхности зубьев в виде беспорядочных срезов
Забоины на сменных шестернях обкатки и деления Зазоры в подшипниках налов
сменных шестерен деления и обкатки
Недостаточно жесткая оправка детали
Различная высота резцов в рез цовой головке Недостаточный зазор в зацеп
лении сменных шестерен деле ния, обкатки и качания люльки Ослабление тормозного дейст вия вчервячном колесе нлюльке
Таблица 4.13
Точность, достигаемая при нарезании конических колес с круговыми зубьями на зуборезных станках (по ГОСТ 9152-83)
|
|
|
|
Допускдля станков классов точности, |
|
Проверяемый параметр |
Наибольшийдиаметробраба |
|
мкм |
||
тываемыхзубчатыхколее, мм |
|
|
|||
|
|
|
п |
|
|
|
|
|
|
В |
|
Точность |
положения |
профилей |
До 125 |
65 |
40 |
соседних зубьев, с |
|
Си. 125 до 200 |
40 |
25 |
|
|
|
|
« 200 « 320 |
32 |
20 |
|
|
|
«320 «500 |
25 |
16 |
|
|
|
« 500 « 800 |
20 |
12 |
Точность |
положения |
профилей |
До 125 |
160 |
100 |
зубьев на всей окружности, с |
Св. 125 до 200 |
100 |
65 |
||
|
|
|
«200 «320 |
80 |
50 |
|
|
|
« 320 « 500 |
65 |
40 |
|
|
|
«500 «800 |
50 |
32 |
Шероховатость обработанной по |
До 500 |
2 |
1,25 |
||
верхности зуба Ra, мкм |
|
Св. 500 до 1600 |
2,5 |
1.6 |
164 |
Г л а в а 4 |
Таблица 4.14
Нормы точности и износа базовых поверхностей приспособления жесткого типа для нарезания конических зубчатых колее, мкм
|
Проверяемый параметр |
Оснастка при установке на станок |
Оснастка, находящаяся |
|
и при нолналалкс ее на станке |
в эксплуатации |
|
|
|
||
Радиальное биение посадочной |
15 |
25 |
|
повспхпости оправки |
10 |
20 |
|
Торцевое биение по опорной |
|||
IIOBCDXHOCTH на радиусе 100 мм |
|
|
|
Величина износа посадочной |
|
|
|
поверхности при диаметре, мм: |
5 |
5 |
|
От 30 до 50 |
|||
Св. 50 « 80 |
10 |
10 |
|
4 |
80«120 |
10 |
10 |
4120 4180 |
15 |
15 |
|
4180 4 220 |
20 |
20 |
|
4 220 4 260 |
25 |
25 |
Таблица 4.15
Режимы резания при нарезании конических колее с круговыми зубьями
|
а. Обработка ведущих колее |
|
|
|
|
|
||
|
|
|
|
Степеньточности |
|
|
||
|
Скорость резания |
|
6-7 |
|
|
7-8 |
|
|
|
м/мин |
Время обработки зуба ttiafa,с; с модулем, мм |
||||||
|
|
|||||||
|
|
4 |
5 |
6 |
8 |
9 |
10 |
|
Предварительная |
45 |
18 |
20 |
25 |
30 |
35 |
40 |
|
Окончательная |
55 |
25 |
30 |
35 |
32 |
37 |
43 |
|
|
б. Обработка ведомых колее |
|
|
|
|
|
||
Характер обработки |
Скорость резания |
Время обработки зуба Сг таГ(л,с/зуб; для модуля, мм |
||||||
«яйри/мии |
4 |
5 |
6 |
8 |
9 |
10 |
||
|
||||||||
|
|
|||||||
Предварительная: |
|
|
|
|
|
|
|
|
с обкаткой |
40 |
12 |
15 |
20 |
25 |
30 |
35 |
|
без обкатки |
40 |
5 |
5 |
8 |
15 |
20 |
25 |
|
Окончательная после предвари |
|
|
|
|
|
|
|
|
тельной: |
|
|
|
|
|
|
|
|
с обкаткой |
50 |
18 |
20 |
25 |
30 |
32 |
35 |
|
без обкатки |
50 |
10 |
12 |
15 |
17 |
|
|
|
Окончательная |
8 |
3,5 |
4 |
5 |
7 |
8 |
9 |
|
(протягиванием) |
|
|
|
|
|
|
|
Примечания. 1. Режимы резания даны для ведущих колее с числом зубьев меньше 10. Для других значений время обработки одного зуба следует уменьшать в пределах 10%. 2. При нарезании зубьев на станках недостаточной жесткости время обработки одного зуба нужно увеличивать на 20%. 3. Для окончательной обработки зубьев ведущих колее указано время нарезания одной стороны зуба. 4. Для ведомых колее приведены режимы для работы двусторонними резцовыми головками. При работе трех сторонними головками скорость должна быть увеличена на 20%, а время обработки зуба уменьшено на 20%. 5. Режимы резания рассчитаны на стойкость обычных резцовых головок Ти- 500 мин, для одноцикловых резцовых головок (протяжек) Ти- 800 мин.
Механическая обработка конических зубчатых колес |
165 |
Таблица 4.16
Поправочные коэффициенты при нарезании конических колее
скругоимми зубьями
О брабаты ваемая сталь
К оэ(|и |)|щ и с 1т |
>1 |
|
|
|
18ХГТ |
ЗОХГГ |
20Х Н М |
К |
0 .9 |
0 ,9 |
1.0 |
к1; |
1.1 |
1.0 |
1.0 |
Диагональпость контакта можно устранить двумя способами:
а) изменением передаточного отношения обкатки и осевой установки, внесением обу словленных им поправок;
б) дополнительным гипоидным смешением и изменением осевой установки с внесе нием зависящих от этого исправлений.
Длина пятна контакта меняется при изменении образующих радиусов резцовых голо вок за счет изменения толщины прокладок под установку резцов.
Поведение пятна контакта регулируется для ответственных передач и для передач с нежесткими опорами. Для этого шестерне сообщается гипоидное и осевое смещение с це лью перемещения пятна контакта в крайнее положение к малому и большому модулям. Сопоставление полученных значений АН и AV с рекомендуемыми позволяет определить чувствительные передачи, погрешности монтажа и деформации под нагрузкой.
При термообработке пятно контакта корректируется с учетом последующих деформа ции. Кроме того, следует иметь в виду, что в процессе термообработки:
а) угол спирали на обеих сторонах зуба уменьшается, что приводит к смещению пятна контакта на выпуклой стороне к большему модулю, а на вогнутой — к меньшему;
б) высота пятна контакта, особенно па выпуклой стороне, несколько уменьшается; в) на обеих сторонах зуба возможно возникновение дополнительной диагональности
нормального типа.
Последовательность корректировки пятна контакта для конических передач с круго выми зубьями приведена в табл. 4.17.
|
Таблица 4.17 |
Порядок корректировки пятна контакта конических передач с круговыми зубьями |
|
О п ераци и |
Д еистами при получении исж слаем ого п ятна контакта |
1. Расчет наладочных пашмст|юв станка |
- |
2. Зубопарсзаннс |
- |
3. Контроль пятна контакта |
Определение поправок к наладке, повторение |
|
операций 1,2 |
4. Химико-термическая обработка |
- |
5. Контроль пятна контакта |
Определение поправок к наладке, повторение |
|
операций 1,2,3,4 |
6. Притирка |
- |
7. Контроль пятна контакта и уровня шума |
Определение поправок к наладке, повторение |
|
операций 1,2,3,4,5,6 |
8. Монтаж конической передачи в узле и опреде |
Внесение поправок, повторение операций 1,2,3, |
ление пятна контакта с учетом погрешностей |
4.5,6.7 |
монтажа и нагрузки |
Внесение поправок, повторение операций 1,2,3, |
9. Стендовые и эксплуатационные испытания, |
|
определение достигнутых характеристик нагру |
4.5,6,7 |
зочной способности и уровня шума |
|
166 |
Г л а в а 4 |
Корректировка пятна контакта заключается в следующем: после первичного расчета наладок производятся зубонарезание и контроль фактического пятна контакта. В случае его несоответствия заданному корректируется расчет наладок и производится повтор ное нарезание. Процедура длится до тех пор, пока не будет получено заданное пятно контакта, затем производятся термообработка зубчатых колес передачи, их спаривание и притирка. Если полученное пятно контакта не соответствует заданному, корректиру ются наладки. Процедура повторяется до достижения желаемого положения и формы пятна контакта в спаренной передаче. После этого осуществляется монтаж передачи в узле и испытание ее под нагрузкой, определяется поведение пятна контакта в передаче, при неудовлетворительном пятне контакта корректируются наладки.
В табл. 4.18 приведены наиболее часто встречающиеся погрешности пятна контакта конических передач с круговыми зубьями.
Таблица 4.18
Погрешности пятна контакта конических передач с круговыми зубьями
Пятно контакта при проверке на контрольно-обкатном станке
|
сторона зуба |
Характеристика пятна контакта |
|
|
|
выпуклая |
|
вогнутая |
Е 2 С Л
Г© [
t o
г - |
Г - / |
I |
|
Не занимает нужного положения, а смещено в продольном или поперечном, либо одновременно в обоих направлениях так, что выходит на край зуба у одного из торцов или на его головку или ножку. Работа передачи в этом случае при но минальных монтажных расстояниях невозможна Пятно контакта слишком узкое, вследствие недостаточ
ной величины коэффициента профильного перекрытия нарушается плавность зацепления и может повыситься уровень шума при работе передачи Пятно контакта слишком широкое, что может привести к
его разрыву по высоте (мостовой контакт)
При малейшем изменении взаимного положения шестерни и колеса (особенно при изменении осевой установки шес терни) пятно выходит на головку или ножку зуба Пятно контакта слишком короткое. Снижаются нагрузоч
ная способность передачи и коэффициент продольного пе рекрытия. Если же одновременно уменьшается ширина пятна, то это влечет за собой снижение плавности зацепле ния и возникновение шума Пятно контакта слишком длинное. При малейшем измене
нии взаимного положения шестерни и колеса пятно сме щается на край зуба у наружного торца, т. е. снижается не чувствительность передачи к небольшим погрешностям монтажа и де(|юрмациям под нагрузкой Пятно контакта располагается с перекосом по диагонали зу
ба. При такой форме пятна в зацеплении не участвует значи тельная часть рабочих поверхностей зубьев, нарушается плавность и появляется шум в зацеплении. При изменении взаимного положения шестерни и колеса пятно смещается на его головку или ножку Пятно контакта имеет нужные размеры, форму и располо
жение, но при изменении взаимного положения шестерни и колеса оно смещается с перекосом — на головку или нож ку зуба При изменении взаимного положения шестерни и колеса
пятно контакта смещается вдоль зуба, но его форма при этом нарушается
Механическая обработка конических зубчатых колес |
167 |
4 .2 .5 . Резцовые головки для нарезания конических колес с круговыми зубьями
У резцовых головок (табл. 4.19) для нарезания конических колес с круговыми зубья ми режущие кромки резцов располагаются по конусной поверхности.
Таблица 4.19
Номинальные диаметры зуборезных голонок для конических и гипоидных зубчатых колес с круговыми зубьями (по ГОСТ 11902-77)
Номинальный диаметр |
Параметры конических и гипоидных зубчатых колес, мм |
|||
наибольшая иненшяи |
наибольший модуль |
|||
ГОЛОВКИ,мм |
||||
|
пмеотазуба |
RHCH1IH1H окружном |
нормальный |
|
|
|
|||
20 |
3 |
- |
0.8 |
|
25 |
3 |
- |
1,0 |
|
32 |
4 |
- |
1,25 |
|
40 |
5 |
- |
1,5 |
|
50 |
6 |
- |
2,0 |
|
60 |
7 |
- |
2,25 |
|
80 |
8 |
- |
2,50 |
|
100 |
9 |
4.0 |
3,0 |
|
125 |
10 |
4,5 |
3,5 |
|
160 |
13 |
5.0 |
4,0 |
|
200 |
16 |
6,0 |
5.0 |
|
250 |
20 |
8,0 |
6,0 |
|
315 |
24 |
10,0 |
8,0 |
|
400 |
30 |
13,0 |
10,0 |
|
500 |
36 |
16,0 |
12,0 |
|
630 |
45 |
20,0 |
16,0 |
|
800 |
60 |
26,0 |
20,0 |
|
1000 |
70 |
30,0 |
25.0 |
Вершины режущих кромок наружных и внутренних резцов находятся на различных радиусах от оси головки. Разность этих радиусов называется разводом резцов. Их средняя величина является средним номинальным радиусом резцовой головки. Головки с номи нальными диаметрами от 20 до 80 мм выполняются цельными, от 100 до 1000 мм —сбор ными.
Цельные головки применяются в основном для нарезания мелкомодульных колес и выполняются только двусторонними.
Двусторонние чистовые головки применяются главным образом для чистового наре зания колес.
Двусторонние резцовые головки имеют два типа резцов — наружные и внутренние. Наружными обрабатывается вогнутая сторона зубьев, а внутренними — выпуклая. Под каждым резцом есть клин и подкладка, которые служат для регулировки резцов в ради альном направлении. Кроме того, у двусторонних чистовых резцовых головок имеются два нерегулируемых эталонных резца —наружный н внутренний, по которым и регулиру ются все остальные резцы.
Односторонние чистовые головки имеют только наружные либо внутренние резцы и применяются для чистовой обработки лишь одной стороны зубьев. У односторонних рез цовых головок нет развода. Они различаются по образующему радиусу.
168 Г л а в а 4
Двусторонние черновые головки имеют нерегулируемые наружные и внутренние рез цы и применяются в массовом и крупносерийном производстве для чернового нарезания по методу обкатки.
У трехсторонних черновых головок три тина резцов: наружные, внутренние и сред ние. Наружные резцы обрабатывают вогнутую сторону зуба, внутренние — выпуклую, средние — прорезают дно впадины.
Наружные и внутренние резцы трехсторонних головок такие же, как и резцы с дву сторонними головками. Применение таких головок позволяет повысить производитель ность, стойкость инструмента и особенно эффективно при черновом нарезании зубьев по методу врезания.
Чистовые резцы имеют затылованную рабочую и нерабочую стороны профиля резцов. Для расширения возможностей регулировки пятна контакта резцы цельных и сбор
ных головок изготовляют с различными профильными углами, величина которых опреде ляется номерной поправкой к номинальному углу.
Номер наружных и внутренних резцов указывает на величину их профильных углов а жи a oi:
а,к. = а л - Да; а,„= а„ + Да, |
|
где Да “ 10N — угол искажения, мин; N — номер резца (для |
чистовых головок — |
0-2-4-6-8-10-12-14-16-18-20-22-24-30-36-42; для черновых - |
0-4-8-12-6-20-24); |
а,* — угол профиля рабочей стороны чистового и чернового наружных резцов; а п — но минальный угол профиля; а,„ — угол профиля рабочей стороны чистового и чернового внутренних резцов.
Цельные головки и резцы сборных головок изготовляют из быстрорежущей стали ма рок Р18, Р9 и Р6М5 (по ГОСТ 19265-73) с карбидной неоднородностью рабочей части не более 3-го балла и твердостью 63-66 HRC3, корпуса чистовых сборных головок — из ста лей 12ХНЗА или 20ХН2М с последующей цементацией и термообработкой поверхно стей до твердости 57 -63 HRC,, корпуса черновых сборных головок — из сталей 40ХН2МА с термообработкой до твердости 41-46 HRCa. Допускается также изготовле ние корпусов черновых и чистовых головок нормальной точности из сталей 40Х или ХВГ. Для клиньев и прокладок используют стали марок X, ХВГ, У7, У8, У9 или У10.
Требования к точности и шероховатости основных поверхностей приведены в табл. 4.20.
Таблица 4.20
Нормы точности зуборезных головок для конических и гипоидных колес
скруговыми зубьями (по ГОСТ 11906-77)
а.Допуски параметров
|
|
|
Д о п у с к , м км , д л я го л о и о к |
|
П р о в е р я е м ы й п ар а м е тр |
Н о м и н а л ь н ы й |
|
|
|
д и а м е т р го л о о к и, мм |
|
ч и с то вы х н о р м а л ь |
ч и с т о в ы х п о в ы |
|
|
Ч ерновы х |
|||
|
|
н о й т о ч н о с ти |
ш е н н о й то ч н о с ти |
|
|
|
|
||
Биение опорного и переднего |
100-125 |
- |
10 |
2 |
торнов на наибольшем диаметре |
160-250 |
10 |
10 |
2 |
или по контрольному пояску |
315-400 |
15 |
15 |
3 |
|
500 |
20 |
20 |
5 |
|
630-1000 |
— |
25 |
- |
Отклонение посадочного |
|
|
|
+2 |
отверстия |
|
|
+2 |
|
058,23 и 0127,0 |
160-400 |
— |
-5 |
-5 |
0215,8 и 0330,0 |
500-1000 |
Н5 |
Н5 |
Н5 |
Механическая обработка конических зубчатых колес |
169 |
Продолжение таблицы 4.20
|
|
|
|
Д опуск, м км, д л я голопок |
|
П р о в ер я ем ы м пар ам етр |
ди ам етр головки, мм |
черпоиых |
чистовы х нормаль |
чистовы х повы |
|
|
|
||||
|
|
|
ной точности |
шенном точности |
|
|
|
|
|
||
Погрешность профиля рабочей |
|
|
|
|
|
стороны резцов на длине, мм: |
100-125 |
|
6 |
3 |
|
9 |
|
10 |
|||
10 |
|
160-200 |
6 |
3 |
|
15 |
|
250-320 |
16 |
10 |
4 |
25 |
|
400-500 |
20 |
16 |
5 |
35 |
|
630 |
— |
25 |
— |
60 |
|
800-1000 |
— |
40 |
|
Торцсиос биение по вершинам |
|
|
|
|
|
резцов: |
|
100-126 |
|
10 |
5 |
от резца к резцу |
|
25 |
|||
|
|
160-200 |
12 |
7 |
|
|
|
250-320 |
25 |
15 |
10 |
|
|
400-500 |
30 |
20 |
10 |
в пределах одного оборота |
630-1000 |
— |
25 |
— |
|
100-125 |
— |
30 |
16 |
||
|
|
160-200 |
50 |
30 |
20 |
|
|
250-320 |
55 |
35 |
25 |
|
|
400-500 |
60 |
40 |
30 |
|
|
630-1000 |
_ |
50 |
— |
Радиальное биение резцов посе |
100-320 |
30 |
25 |
1,6 |
|
редине режущих кромок |
400-500 |
40 |
4 |
2,5 |
|
Отклонение режущих |
кромок |
630-1000 |
— |
6 |
— |
100-125 |
- |
40 |
30 |
||
резцов от плоскости, |
проходя |
160-200 |
80 |
50 |
40 |
щей через ось головки |
|
250-320 |
100 |
60 |
50 |
|
|
400-500 |
20 |
80 |
60 |
|
|
630-800 |
|
100 |
|
|
|
1000 |
|
120 |
|
6.Шероховатост ь поверхностей
Шероховатость, м км, д л я головок
|
Поверхность |
|
чистовы х норм альной |
чистовы х п овы ш енной |
|
|
|
|
черновы х |
точности |
точности |
|
|
|
Цельные головки |
|
0,32 |
Посадочные отверстия R„ |
_ |
0,32 |
|||
Опорный торец Ra |
рабочей |
- |
0,63 |
0,32 |
|
Задняя |
поверхность |
— |
3,2 |
1,6 |
|
стороны профиля резца Rz |
— |
3,2 |
1,6 |
||
Передняя поверхность резца Rz |
|||||
Задняя |
поверхность нерабочей |
— |
6,3 |
3,2 |
|
стороны профиля резца Rz |
|
|
|
||
|
|
|
Сборные головки |
|
0,25 |
Посадочные отверстия R0 |
0,32 |
0,32 |
|||
Опорный торец Ra |
рабочей |
0,63 |
0,63 |
0,25 |
|
Задняя |
поверхность |
1.6 |
1.6 |
0,8 |
|
стороны профили резца Rt |
3,2 |
3,2 |
1,6 |
||
Передняя поверхность резца Rz |
|||||
Задняя |
поверхность |
нерабочей |
6,3 |
6,3 |
3,2 |
стороны профиля резца Rt
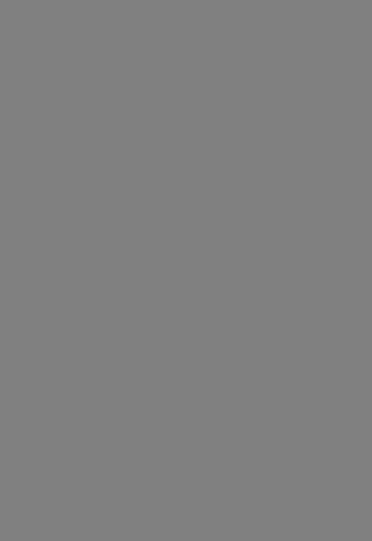