
книги / Технология производства и методы обеспечения качества зубчатых колес и передач
..pdf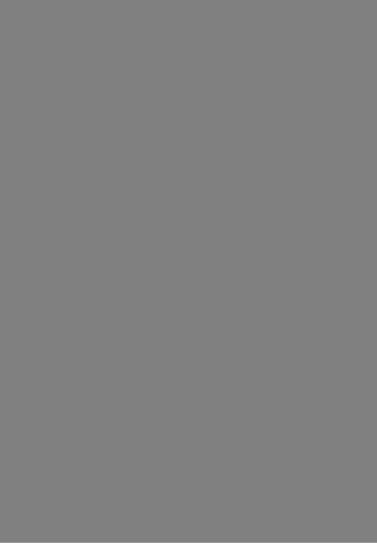
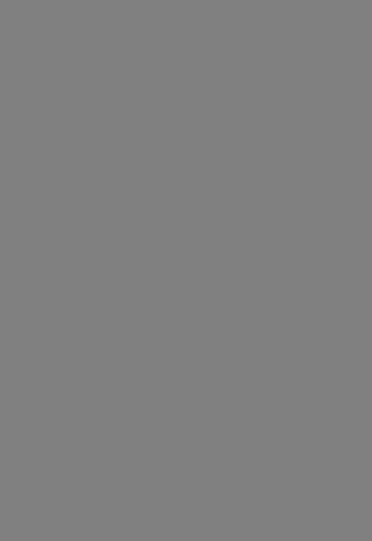
Механическая обработка цилиндрических зубчатых колес |
113 |
Рис. 3.19. Облегающий шевер
Рис. 3.20. Шевер для колес внутреннего зацепления
зубчатых колес по профилю получается несколько ниже, чем при использовании диско вых шевсров обычной конструкции.
Шеверы для колес внутреннего зацепления (рис. 3.20) отличаются тем, что боковая поверхность их зубьев не является эвольвентой. Это отличие тем больше, чем меньше раз ность числа зубьев колеса и шевера и чем больше угол скрещивания осей. С внешней сто роны зубья шевера бочкообразны, и практически его расчет для колес внутреннего зацеп ления сводится к определению величины бочкообразности как разницы в толщине зубьев в среднем и крайнем торцевых сечениях.
Однопроходные шеверы отличаются от обычных тем, что их зубья с одной стороны выполнены конусными и имеют три зоны: заходную, режущую и калибрующую. Шевин гование однопроходным шевером осуществляется при постоянном межосевом расстоя нии, что упрощает кинематику стайка. Кроме того, режущие зубья шевера вступают в ра боту последовательно, что позволяет более равномерно распределять припуск между ни ми. Цикл обработки однопроходным шевером состоит из одного рабочего и одного калибрующего хода.
114 |
Г л а в а 3 |
3.5. Калибрование зубьев цилиндрических колес
Калибрование осуществляется без снятия стружки при пластическом деформирова нии металла на боковой поверхности зуба. В результате повышается первоначальная твердость профиля, снижается уровень шума работающих зубчатых колес. Кроме того, обеспечивается шероховатость профиля с высотой микронеровностей 1-5 мкм.
Калибрование производится одним, двумя или тремя инструментами-накатниками. На станках с двумя или тремя инструментами-накатниками усилие накатки распределя ется между ними таким образом, что ось обрабатываемого колеса остается разгруженной. На станках с одним инструментом-накатником создаются значительные усилия, в связи с чем обрабатываемое колесо должно надежно поддерживаться специальными опорами. Пе ред чистовым накатыванием необходимо соблюдать большую точность и более узкий до пуск на припуск, чем перед шевингованием, так как в противном случае на боковых про филях зубьев образуются закаты и местные скопления металла. Для обеспечения одина ковых условий обработки обеих сторон зуба рекомендуется во время рабочего цикла осуществлять реверс.
Для массового производства эффективным является калибрование по методу «Моноролл». Обработка осуществляется свободным обкатом при параллельных осях обрабаты ваемого колеса и инструмента. Инструмент-накатник выполняется в виде шевера. На бо ковых поверхностях его зубьев нанесены поперечные канавки, которые расположены со смещением на определенную величину по длине каждого зуба, а на поверхности накатни ка канавки образуют винтовую линию. Благодаря этому при обкатке последовательно де формируются отдельные участки боковых поверхностей зубьев, что позволяет уменьшить ее усилие и повысить точность обработки. Число зубьев и групп в накатнике не должно быть равным или кратным числу зубьев обрабатываемого колеса. В процессе калиброва ния зубья инструмента под действием усилия деформации входят в металл на глубину припуска и вытесняют его из зоны контакта. Поскольку оси инструмента и обрабатывае мого колеса установлены параллельно, то, в отличие от процесса шевингования, отсутст вует эффект резания. Металл, вытесняемый при накатывании, перемещается к головке или ножке зуба. Накатник в течение цикла вращается в одном направлении. Обработка производится за один двойной ход стола станка при постоянном межосевом расстоянии. Обрабатываемое колесо выдерживается без реверса в конечном положении, а затем вме сте с поперечными салазками автоматически возвращается в исходное положение.
Накатники изготовляют из быстрорежущей стали той же твердости, что и шеверы. Средняя стойкость между переточками — 50 тыс. деталей при трех возможных переточ ках. Каждая сторона профиля зуба накатника выполняется с различной корректировкой, исходя из условий течения металла на ведущей и ведомой сторонах зуба обрабатываемого колеса и непостоянства величины прогиба на разных участках по длине зуба при обработ ке косозубых колес. Отношение ширины выступов к ширине канавок составляет 3:2, при пуск под калибрование — 0,02-0,03 мм, продолжительность обработки — 9-12 с для зуб чатых колес диаметром до 120 мм и модулем до 2,5 мм. Увеличение модуля и соответст венно габаритов обрабатываемых колес требует значительно больших пластических деформаций и перемещения поверхностных слоев металла, чем при обработке зубчатых колес с небольшим модулем. В связи с этим применение данного метода для более круп ных модулей зубчатых колес сопряжено со значительными трудностями.
Промежуточное место между калиброванием и шевингованием занимает метод обра ботки зубчатых колес «финишер». При этом методе инструмент по внешнему виду напо
Механическая обработка цилиндрических зубчатых колес |
115 |
минает зубчатое колесо. На одном нз его торцов расположены режущие кромки зубьев с очень малыми задними углами. Оси инструмента и зубчатых колес скрещены под углом 15-20°. Вращающийся инструмент находится в дпухпрофильном зацеплении с обрабаты ваемым колесом и одновременно вдоль его зубьев. Инструмент полностью обрабатывает колесо за один проход вдоль его зубьев. В отличие от шевингования, процесс идет с при нудительным обкатом. Скорости вращения инструмента и колеса строго синхронизирова ны кинематической цепью станка. Применяется инструмент либо из быстрорежущей ста ли, либо твердосплавный. В станки, работающие по методу «финишер», встроен механизм для перезаточки инструмента по передней грани.
Вследствие того, что процесс идет с принудительным обкатом, точность обработки су щественно выше, чем при шевинговании. При изготовлении колес т - 3-4,5 мм достига ется погрешность профиля в 0,01-0,02 мм, погрешность направления зуба — 0,04/100 мм, радиальное биение — 0,02-0,03 мм.
Фирма Landis Machine Со and Michigan Tool Со (США) создала серию станков для хо лодного калибрования зубчатых венцов колес для автомобилестроения и авиационной промышленности.
Фирма Lorenz (ФРГ) создала станки модели «Микрофло» (лицензия фирмы Michigan, США). Колеса с числами зубьев 31 и модулем зацепления 2,1 мм обрабатываются в течение 6 с (с учетом времени загрузки и выгрузки). Обработку ведут двумя кинематически связан ными валками (накатниками). Заготовку вращают накатники. Калибруют колеса диамет ром 25-125 мм при модуле 125-5 мм. Припуск на калибрование не превышает 0,02-0,03 мм. В станке используется высокоточный инструмент. При калибровании заготовок из сталей с HRC-18 усилия составляют 15-25 к11 на каждые 25 мм ширины венца при модуле 1,5-4 мм. Для сталей с HRC-21 усилия равны 20-40 кН. Точность колес после калибрования не по вышается, однако значительно возрастают класс шероховатости поверхности и контактная прочность зубьев. Производительность при калибровании в несколько раз выше, чем при шевинговании. Стойкость инструмента составляет около 1 млн. колес. .
Фирма Hurth (ФРГ) создала станок модели ZRA7, работающий одним накатником (процесс «Моноролл»). Производительность станка такая же, как и у «Микрофло». Инст румент выполнен с канавками на зубьях, что позволяет значительно снизить усилия нака тывания. Из-за высокой стоимости инструмента применение станка оправдано лишь при изготовлении не менее 1 тыс. однотипных колес в смену.
3.6. Хонингование зубьев цилиндрических колес
3 .6 .1 . Технология хонингования
Хонингование представляет собой процесс окончательной доводки зубьев цилиндри ческих колес с помощью зубчатого абразивного колеса — хона. Оно используется для до водки зубьев термически обработанных колес.
Различают схемы зубохоиинговання:
—при двухпрофилыюм зацеплении зубчатого хона с обрабатываемым колесом и ра диальной нагрузке «в распор» (рис. 3.21, а);
—при однопрофильном зацеплении зубчатого хона с обрабатываемым колесом и тор мозном моменте на колесе (рнс. 3.21, 6).
—«коронарное» зубохонингование при использовании в качестве инструмента «охватыва ющего» хона — колеса с внутренним зацеплением —с обрабатываемым колесом наружного за цепления (рис. 3.21, в).
116
Зубохонингование позволя ет устранить небольшие заусен цы и забоины, повысить качест во пятна контакта и плавность передачи, уменьшить шерохова тость рабочих поверхностей зу ба и уровень шума передачи.
В процессе зубохонингования обрабатываемое колесо и хон устанавливаются на скре щивающихся осях. При этом происходят движения: враща тельное — хона и колеса; осевое возвратно-поступательное — хо
на или колеса; осциллирующее возвратно-поступательное — хона для некоторых типов станков с целью увеличения производительности.
Припуск под хонингование зубьев обычно составляет не более 0,02-0,03 мм на сторо ну зуба. Для улучшения качества обработки колеса в каждом конкретном случае следует устанавливать оптимальную величину припуска, так как повышенный съем его при зубохонинговании приводит к возникновению дополнительных погрешностей.
В качестве инструмента применяются алмазные или абразивные хоны. Алмазный хон представляет собой зубчатое колесо, на профильную поверхность зубьев которого нанесен гальваническим методом алмазный слой. Абразивный хон изготавливается литьем в пресс-форму смеси белого электрокорунда с эпоксидными акриловыми и полиуретановы ми связками.
Жесткими являются эпоксидные и акриловые связки, упругими — полиуретановые. Жесткие связки обеспечивают равномерный съем припуска и более точную обработку. Эластичные связки способствуют ускорению процесса и некоторому повышению произ водительности.
В качестве СОЖ используется сульфофрезол или веретенное масло.
Благодаря высокой производительности процесс зубохонингования получил широ кое распространение в качестве отделочной операции при массовом производстве шесте рен, для снятия забоин и заусенцев, улучшения шероховатости зубьев.
3.6.2. Зубохонинговальные станки
Модели хонинговальных станков приведены в табл. 3.27.
|
|
Таблица 3.27 |
|
Зубохонинговальные станки |
|
|
|
Основные характеристики |
Модель станка |
||
5Б913 |
5А915 |
||
|
|||
Диаметр обрабатываемых колес, мм: |
320 |
500 |
|
наибольший |
|||
наименьший |
30 |
140 |
|
Наибольший модуль обрабатываемых колес, мм |
8 |
12 |
|
Наибольший угол наклона зуба обрабатываемых колес, град. |
45 |
30 |
Механическая обработка цилиндрических зубчатых колес |
117 |
||
|
Продолжение таблицы 3.27 |
||
Осноииысхарактеристики |
Модель станка |
||
5Б913 |
5А915 |
||
|
|||
Наибольшая ширима зубчатою немца обрабатываемых колес, мм |
125 |
150 |
|
Наибольшая длина устанавливаемого изделия, мм |
500 |
600 |
|
Диаметр хона, мм |
250 |
250 |
|
Ширина хона, мм |
40 |
40 |
|
Расстояние между осями хона и изделия, мм |
130-285 |
150-420 |
|
Наибольшее перемещение хонинговальной головки в каждую сторону |
60 |
80 |
|
от среднего положении, мм |
|
|
|
Величина радиального нагружения, Н |
630 |
800 |
|
Величина окружного нагружения, Н-м |
160 |
160 |
|
Частота вращения, мин-1 |
160-1000 |
160-500 |
|
|
(хона) |
(изделия) |
|
Число двойных ходов за цикл |
1-5 |
- |
|
Мощность главного привода, кВт |
3,0 |
3,2 |
|
Габаритные размеры, мм: |
1600 |
2260 |
|
длина |
|||
ширина |
1000 |
1450 |
|
высота |
2200 |
1930 |
|
Масса, кг |
3150 |
4300 |
3.7. Обкатка и притирка зубьев цилиндрических колес
Обкатка представляет собой процесс совместного вращения обрабатываемого колеса и одного или нескольких рабочих колес под распорной или окружной нагрузкой. Рабочие колеса обычно имеют высокую твердость, так как нагрузка при обкатке достигает 5-10 МПа. Время ее, как правило, составляет 1-2 мин. В результате на рабочих поверхно стях зубьев образуется наклепанный слой, снижается шероховатость, устраняются заусен цы и забоины. В качестве СОЖ применяется сульфофрезол или веретенное масло.
Притирка — это процесс искусственного изнашивания рабочих поверхностей зубьев с помощью абразивной массы. Притирка применяется для ответственных передач с целью уменьшения шума, повышения их плавности и улучшения пятна коитакга.
Притирку осуществляют на специальных станках чугунным зубчатым колесом или с парным колесом при усилии 100 Н на 1 см длины зуба. В зависимости от типов станков при притирке происходят: вращение притира и колеса; осевое перемещение притира или колеса; возвратно-поступательное перемещение притира или колеса в радиальном направ
лении.
Процесс притирки может осуществляться как при параллельном расположении осей притира и колеса, так и при скрещивающихся осях, причем в последнем случае повышает ся производительность.
Припуск под притирку обычно составляет не более 0,05 мм. Материалом для прити ров служит мелкозернистый серый чугун СЧ-21 с твердостью НВ 170-241 или СЧ-15 с НВ 163-229 и микроструктурой мелкопластннчатого графита. Для закрепления зерен аб разива в притире необходимо, чтобы они были немного больше пластинок графита.
118 |
Г л а в а 3 |
В качестве притирочной смеси применяется состав из 40% корунда или электроко рунда зернистостью 25-16 и 60% вазелиновой смазки.
Число зубьев притира не должно иметь общих множителей и быть кратным числу зубьев притираемого колеса. Обычно притирка производится при номинальном меж осевом расстоянии, поэтому толщина зубьев притира должна быть уменьшена на 0,05-0,08 мм.
Следует отметить, что в каждом конкретном случае для улучшения качества прити раемого колеса нужно установить оптимальную величину снимаемого припуска, так как при ее превышении (обычно свыше 0,05 мм) возникают дополнительные погрешности зубьев.
3.8. Шлифование зубьев цилиндрических колес
3 .8 .1 . Технология шлифования
Зубошлифование производится в основном при изготовлении колес повышенной точности, термически обработанных до твердости свыше 40 HRCa.
Различают два метода шлифования: копирования и обкатки. При шлифовании по первому методу шлифовальный круг повторяет профиль впадины обрабатываемого зуб чатого колеса, а по второму — боковые поверхности круга воспроизводят зуб рейки в заце плении с обрабатываемым колесом.
Наиболее производительными и точными являются станки, работающие по методу обкатки с использованием в качестве инструмента абразивного червячного круга. Высо кой производительностью характеризуются также станки, работающие по методу копиро вания, однако наладка их довольно сложна, и применяются они в основном для обработки прямозубых колес.
Величина припуска на сторону зуба под шлифование составляет для модулей: до 2 мм — 0,05-0,15 мм; 2 -5 мм — 0,15-0,20 мм; свыше 5 мм — 0,2-0,3 мм.
Зубошлифование позволяет обеспечить высокую точность зубчатого венца, устранить погрешности предварительной и термической обработки. Однако шлифование ухудшает качество поверхностного слоя и его физико-механические свойства. Выделяемое при шлифовании тепло вызывает структурные изменения в поверхностном слое в виде прижогов и внутренние растягивающие напряжения. При превышении этими величинами на пряжений предела прочности появляются шлифовочные трещины.
Прижоги в зависимости от схемы шлифования могут быть в виде пятен, чередующих ся полос или отдельных мелких штрихов. Глубина дефектного слоя может достигать 0,1 мм.
Прижоги и трещины образуются на деталях с низкой теплопроводностью, неоднород ной структурой, наличием поверхностных дефектов.
С целью предотвращения появления прижогов и шлифовочных трещин рекомендует ся применять: прерывистое шлифование либо шлифовать партиями детали из одной плавки; СОЖ с хорошими моющими и смазывающими свойствами; подачу СОЖ при больших давлениях (порядка 1,2-1,5 МПа); стали с более высокой теплопроводностью; площадку контакта детали с кругом в виде узкой длинной полоски; рациональные режи мы резания на черновых и чистовых проходах.
На образование прижогов большое влияние оказывают качество шлифовальных кру гов, своевременность их правки и балансировки. Дисбаланс вызывает колебания круга,
Механическая обработка цилиндрических зубчатых колес |
119 |
неравномерный съем металла за один оборот круга и, следовательно, образование цикли ческих прижогов.
Наилучшпе результаты при шлифовании цементованных сталей получают при при менении кругов марок ЭБ20СМ2К, ЭБ25СМ2К, ЭБ25СМ1К, а для станков с компенса торными устройствами — более мягких кругов с твердостью М3. Устранению прижогов способствует также совершенствование технологии химико-термической обработки, на правленное на уменьшение припуска на зубошлифоваиие. Она должна обеспечить необ ходимое упрочнение при наименьших температуре нагрева, времени выдержки и мини мальном количестве операций нагрева и охлаждения.
Рекомендуется также применять электрохимическое шлифование с использованием
ш лифовальных кругов из эльбора на токопроводящих металлических связках
Л016М 013 и Л025М 013. Деталь является анодом, а шлифовальный круг — катодом. Они подключаются к источнику постоянного тока. Электролит подается в зону резания гидроаэродинамическн м способом.
3 .8 .2 . Зубошлифовальные станки.
Точность, достигаемая при зубошлифовании
В табл. 3.28 приведены основные характеристики зубошлифовальных станков.
|
|
|
|
|
Таблица 3.28 |
||
Зубошлифовальные станки для цилиндрических колес |
|
||||||
Основные характеристики |
|
|
М одель с танка |
|
|
||
5В 832 |
| 5В 835 |
| 5М 841 |
5А 842 |
|
| 584 М |
||
|
| 5843 |
||||||
Тип применяемого |
А бразивны й черияк |
Конический круг |
|||||
инструмента |
|||||||
|
|
|
|
|
|
||
Диаметр обрабатываемого колеса, мм |
20-200 |
50-500 30-320 |
До 500 |
80-800 |
До 500 |
||
Модуль обрабатываемого колеса, мм |
0,3-3 |
1,5-6 |
1,5-8 |
До 10 |
До 12 |
2-10 |
|
Наибольшая длина зуба шлифуемого |
100 |
200 |
160 |
220 |
220 |
180 |
|
прямозубого колеса, мм |
|
|
|
45 |
|
45 |
|
Наибольший угол наклона обрабатывае |
45 |
30 |
45 |
45 |
|||
мых зубьев, i-рад |
|
16-250 10-200 |
10-200 10-200 |
8-150 |
|||
Число зубьев обрабатываемого колеса |
12-200 |
||||||
Расстояние между центрами, мм |
65-220 |
330-485 175-400 |
250-600 250-600 200-464 |
||||
Диаметр шлифовального круга, мм |
330-400 |
330-400 260-350 |
До 400 |
До 400 |
180-260 |
||
Ширина шлифовального круга, мм |
63 |
100 |
32 |
_ |
32 |
- |
|
Частота вращения шлн(|ювалыюго кру |
1500 |
1500 |
1920 |
1670 |
1670 |
2200 |
|
га, мии-1 |
|
|
|
|
1.5 |
U |
|
Мощность электродвигателя главного |
3 |
5.5 |
1,5 |
1.1 |
|||
привода, кВт |
|
|
|
|
|
|
|
Габаритные размеры, мм: |
2110 |
2770 |
2740 |
3079 |
3280 |
2535 |
|
длина |
|||||||
ширина |
2650 |
2700 |
2315 |
2450 |
2780 |
2260 |
|
высота |
1985 |
2345 |
2085 |
2300 |
2525 |
2300 |
|
Масса, кг |
7180 |
9500 |
7600 |
10400 |
11200 |
6000 |
120 |
|
|
Г л а в а 3 |
|
|
|
|
|
|
|
|
|
|
|
|
Продолжение таблицы 3.28 |
|||
|
|
|
|
М о д ел ь с та н к а |
|
|
|
||
хар ак тер и с ти к и |
5А 851 |
5 852 |
5 853 |
5891 |
| 5892А |
I 5 8 9 3 | |
5 А 8 9 3 |
5 8 6 |
| 5 8 6 0 Б |
|
|||||||||
Т и п п р и м е н яе м о го и н |
Т ар е л ьч аты й кр у г |
|
П л о ск и й кр у г |
|
Ф а с о н н ы й кр у г |
||||
стр у м ента |
|
|
|||||||
|
|
|
|
|
|
|
|
|
|
Диаметр обрабаты |
85-360 |
65-500 |
150-800 |
10-125 |
20-250 |
100-320 |
40-320 |
25-500 |
75-800 |
ваемого колеса, мм |
|
1,5-12 |
2-12 |
1-6 |
1-8 |
2-12 |
2-16 |
1-10 |
2-12 |
Модуль обрабаты- |
12 |
||||||||
васмого колеса, мм |
250 |
290 |
290 |
28 |
50 |
70 |
55 |
200 |
250 |
Наибольшая длина |
|||||||||
зуба обрабатывае |
|
|
|
|
|
|
|
|
|
мого прямозубого |
|
|
|
|
|
|
|
|
|
колеса, мм |
|
45 |
45 |
30 |
|
|
35 |
0 |
0 |
Наибольший угол |
45 |
45 |
45 |
||||||
наклона обрабаты |
|
|
|
|
|
|
|
|
|
ваемых зубьев, шал. |
|
|
|
|
|
|
|
|
|
Число зубьев обраба |
5-120 |
10-180 |
12-210 |
7-100 |
4-120 |
8-120 |
10-180 |
10-300 |
10-130 |
тываемого колеса |
|
|
|
|
|
|
|
|
|
Диаметр шлифоваль |
170- |
165- |
165- |
100- |
100- |
400- |
400- |
250- |
280- |
ного круга, мм |
275 |
275 |
275 |
300 |
400 |
500 |
500 |
350 |
400 |
Частота вращения |
1900- |
1900- |
1900- |
2000- |
1420 |
ИЗО |
1150 |
1900- |
950- |
шлифовального |
2660 |
2660 |
2660 |
2500 |
|
|
|
2660 |
2450 |
KDvra. мин- ' |
|
|
|
|
|
|
|
|
|
Мощность электро |
0,75x2 |
0,75x2 |
0,75x2 |
0,75 |
4,5 |
2.8 |
U |
7 |
10 |
двигателей главного |
|
|
|
|
|
|
|
|
|
привода. кВт |
|
|
|
|
|
|
|
|
|
Габаритные размеры, |
|
|
|
|
|
|
|
|
|
мм: |
|
|
|
|
|
|
|
|
|
длина |
2780 |
3490 |
3340 |
1590 |
1840 |
1840 |
2545 |
3350 |
2930 |
ширина |
2200 |
2170 |
2165 |
1500 |
1620 |
1620 |
1770 |
2260 |
3370 |
высота |
2210 |
2100 |
2340 |
1820 |
1990 |
2080 |
2190 |
2140 |
3017 |
Масса, кг |
7000 |
7030 |
7500 |
2800 |
3000 |
3870 |
3500 |
8500 |
9370 |
В табл. 3.29 приведены сведения об областях применения различных моделей зубо шлифовальных станков.
|
|
|
|
|
|
Таблица 3.29 |
|
|
Области применения основных моделей зубошлифовальных станков |
||||||
|
|
для цилиндрических зубчатых колес |
|
||||
|
П р и м е н я е м ы й |
Д ости гае м а я |
Д о сти гае м а я |
|
|
|
|
С та н о к |
то ч н о с ть |
ш срохоиатость |
О б р а б аты в ае м ы е к о л ес а и |
Р е к о м е н д у е м ы й т и п |
|||
и н стр у м ен т |
н о Г О С Т |
п о Г О С Т 2 7 8 9 - 7 3 |
м ето л о б р аб о тк и |
п р о и зв о д с т в а |
|||
|
|||||||
|
|
1 6 4 3 -8 1 |
R a, м км |
|
|
|
|
5В832 |
Абразивный |
5 |
0,63-0,32 |
Прямозубые и косозубые Серийное |
|||
5835 |
червячный круг |
|
|
цилиндрические колеса и крупносерийное |
|||
5В836 |
|
|
|
наружного |
зацепления, |
|
|
|
|
|
|
обрабатываются по мето |
|
||
5831 |
|
|
|
ду непрерывной обкатки |
|
||
Конический |
5-7 |
1,25-0,63 |
Прямозубые и косозубыс Мелкосерийное |
||||
5841 |
двусторонний |
|
|
колеса наружного зацеп и серийное |
|||
5842 |
круг |
|
|
ления, обрабатываются |
|
||
584М |
|
|
|
по методу |
обкатки при |
|
|
|
|
|
|
|
единичном делении