
книги / Технология производства и методы обеспечения качества зубчатых колес и передач
..pdfМеханическая обработка конических зубчатых колес |
171 |
Заточка резцовых головок производится по передней поверхности резцов, после чего обязательно контролируется передний угол. Проверяются также заданные перепады рас положения режущих кромок между соседними зубьями.
Ф ирмой Глисон разработана конструкция чистовой резцовой головки «Хардак». Эта конструкция отличается лучшим центрированием на шпинделе станка и повышенной точностью изготовления базовых поверхностей резцов и подкладок. Винты для крепления резцов расположены под углом 10° к поверхности опорного торца, что улучшает базирова ние резцов на опорной поверхности.
4 .2 .7 . Зуборезные станки для конических колес с круговыми зубьями
Наиболее распространенные модели станков для нарезания конических колес с кру говыми зубьями приведены в табл. 4.21.
4 .2 .8 . Подбор пар и притирка конических зубчатых передач
В результате деформации в процессе термической обработки зубчатых колес возни кает рассеяние параметров по пятну контакта, боковому зазору и уровню шума в собран ных передачах. Поэтому для конических передач с круговыми зубьями обязательным условием качественного их изготовления является подбор в пары с соответствующей притиркой. В дальнейшем при эксплуатации подобранные пары остаются сопряженны ми друг с другом, и замена одного из зубчатых колес в них не допускается.
Подбор в пары производится после термической и окончательной обработки базовых поверхностей. Как правило, перед подбором в пары колеса проверяет ОТК по геометриче ским параметрам.
Пары подбирают на контрольно-обкатных станках, которые рекомендуется устанавли вать в помещении, защищенном от постороннего шума.
Подобранные конические зубчатые колеса устанавливают на номинальном базовом рас стоянии. На их зубья наносят тонкий слой краски. Колеса приводятся во вращение в обе сто роны под низкой нагрузкой, создаваемой тормозом контрольно-обкатного станка. Вначале выявляют по шуму и удаляют забоины с поверхности зубьев с помощью ручной шлифоваль ной машинки или абразивным бруском. Затем увеличивают или уменьшают базовое расстоя ние шестерни и находят нанлучшее рабочее положение по пятну контакта, уровню шума и боковому зазору. Если подобранные пары предназначены для последующей притирки, то от клонения от номинального базового расстояния, полученные на контрольно-обкатном станке (фактическое базовое расстояние, гипоидное смещение), и порядковый номер пары временно маркируют па зубьях шестерни и колеса или прикрепляют бирку.
Если во время подбора пар перед притиркой выявлена резкая разница в расположении зоны касания, их сортируют по группам с различным расположением зоны касания или по величине полученного базового расстояния шестерни. Для каждой группы пар производят специальную наладку притирочного стайка или его подналадку. Если базовое расстояние или гипоидное смещение отличаются от номинального более чем на 0,25 мм, такие колеса прити рать не рекомендуется.
Если пары не подвергаются притирке, их подбор осуществляется путем замен шестерни и колеса до тех пор, пока не будут обеспечены требуемые пятно контакта и уровень шума.
|
|
|
|
|
|
|
|
|
|
|
|
|
|
|
|
|
Таблица 4.21 |
|
|
|
|
|
Зуборезные станки для конических колес с круговым зубом |
|
|
|
|
|
|||||||||
|
|
|
|
|
|
|
|
|
|
М о д ел ь ста н к а |
|
|
|
|
|
|
|
|
|
Основные |
|
|
|
|
ш |
В |
|
|
в |
m |
|
|
|
|
|
|
|
х а р а к т е р и с т и к и |
С |
|
В |
|
2 |
|
|
|
С |
|
|
В |
|
|||||
|
|
|
е |
2 |
й |
S |
2 |
|
й |
ш |
I |
|
|
|
|
со |
1 |
|
|
|
|
о |
g |
о |
О |
а |
< |
и |
|
о |
|
и |
< |
||||
|
|
|
щ |
|
|
|
|
|
||||||||||
|
|
|
|
|
|
|
|
|
|
|
|
|
|
|
|
|
|
|
Наибольший диаметр наре |
125 |
320 |
320 |
320 |
320 |
320 |
500 |
500 |
500 |
500 |
500 |
500 |
800 |
800 |
800 |
1600 |
||
заемых |
колес |
при переда |
|
|
|
|
|
|
|
|
|
|
|
|
|
|
|
|
точном отношении 10:1 |
|
|
|
|
|
|
|
|
|
|
|
|
|
|
|
|
||
и угле спирали 30е, мм |
|
|
|
|
|
|
|
|
|
|
|
|
|
|
|
|
||
Наибольший модуль наре |
2,5 |
8 |
8 |
8 |
10 |
10 |
10 |
12 |
10 |
10 |
12 |
12 |
14 |
16 |
16 |
30 |
||
заемых колее, мм |
|
|
|
|
|
|
|
|
|
|
|
|
|
|
|
|
||
Наибольшее конусное рас |
65 |
150 |
150 |
195 |
140 |
140 |
260 |
250 |
230 |
307 |
265 |
265 |
390 |
420 |
400 |
800 |
||
стояние нарезаемых колес |
|
|
|
|
|
|
|
|
|
|
|
|
|
|
|
|
||
при угле спирали 30°, мм |
|
|
|
|
|
|
|
|
|
|
|
|
|
|
|
|
||
Наибольшая |
ширина зуб |
20 |
50 |
50 |
50 |
|
|
65 |
65 |
80 |
80 |
80 |
80 |
110 |
100 |
125 |
235 |
|
чатого |
венца |
нарезаемых |
|
|
|
|
|
|
|
|
|
|
|
|
|
|
|
|
колее, мм |
|
|
|
|
|
|
|
|
|
|
|
|
|
|
|
|
|
|
Число зубьев нарезаемых 5-100 |
5-75 |
5-75 |
5-150 |
20-80 |
20-80 |
5-100 |
5-150 |
5-150 |
5-150 |
5-150 |
5-150 |
20-75 |
4-100 |
5-150 10- |
||||
колес |
|
|
|
|
|
|
|
|
|
|
|
|
|
|
|
|
|
150 |
Диаметры применяемых |
20-80 |
60- |
60- |
60- |
125- |
125- |
160- |
160- 100-4 |
100- |
160- |
160- |
90- |
250- |
160- |
450- |
|||
резцовых головок, мм |
|
250 |
250 |
400 |
250 |
250 |
315 |
400 |
00 |
400 |
400 |
400 |
500 |
500 |
500 |
900 |
||
Частота вращения шпинде |
110- |
3 0 - |
30- |
26- |
26- |
8-30 25- |
20- |
19- |
20- |
20- |
20-15 |
6,6- |
21- |
гО- |
8,3- |
|||
ля резцовой головки, мин"1 |
550 |
200 |
200 |
265 |
166 |
|
325 |
140 |
210 |
210 |
155 |
5 |
200 |
300 |
125 |
62 |
||
Время обработки одного 7-50 |
9-80 |
9-80 |
- |
2-10 |
2-7,5 |
5-80 |
10- 6-130 |
6-130 10- |
10- |
3-42 135- |
12- |
49- |
||||||
зуба, с |
|
|
|
|
|
|
|
|
|
120 |
|
|
120 |
120 |
|
240 |
200 |
1270 |
Мощность главного приво |
1,2 |
3 |
3 |
4,2/ |
5,5 |
3,0 |
4,5 |
4 |
4 |
4,2/ |
4 |
4 |
И / |
10 |
7,5 |
13 |
||
да, кВт |
|
|
|
|
|
7.1 |
|
|
|
|
|
7,1 |
|
|
13 |
|
|
|
Габаритные размеры, мм: |
1845 |
2607 |
2940 |
2920 |
2670 |
2670 |
2200 |
3140 |
2940 |
2920 |
3140 |
3235 |
4980 |
2600 |
3235 |
5600 |
||
длина |
|
|
||||||||||||||||
ширина |
|
1335 |
1925 |
2090 |
2565 |
2370 |
2370 |
1600 |
1900 |
2090 |
2505 |
1975 |
2180 |
3725 |
2100 |
2180 |
4000 |
|
\ высота |
|
1560 |
1870 |
2050 |
1995 |
2055 |
2055 |
1600 |
2200 |
2050 |
1995 |
2200 |
2200 |
2990 |
1950 |
2200 |
3200 |
|
\ Масса, кг |
|
3000 |
8800 |
9000 |
11300 |
7920 |
7920 |
6200 |
13500 |
9000 |
11100 |
13500 |
13500 |
15105 |
12200 |
15500 |
42900 |
Механическая обработка конических зубчатых колес |
173 |
|
|
|
Таблица 4.22 |
Зубопритирочные станки для конических колес с круговыми зубьями |
|||
|
|
М одель станка |
|
O c iю ш иле х арактер 11стик 11 |
|
|
|
|
5П 725М |
5П 725Е |
5 П 720Ф З |
Наибольший диаметр обрабатываемого зубчатого |
500 |
500 |
800 |
колеса, мм |
|
|
|
Модуль, мм |
2,5-8 |
2,5-10 |
5-16 |
Расстояние от оси ведомого шпинделя до торца |
150-300 |
150-300 |
200-450 |
ведущего, мм |
|
|
|
Расстояние от оси ведущего шпинделя до торца |
145-250 |
145-250 |
200-400 |
ведомого, мм |
|
|
|
Угол между осями шпинделей, фал |
90 |
90 |
90 |
Гипоидное смещение оси ведущего шпинделя |
|
|
|
относительно оси ведомого, мм: |
70 |
100 |
160 |
вверх |
|||
вниз |
70 |
100 |
160 |
Число двойных (осциллирующих) ходов за одни |
8 |
8-20 |
2-99 |
цикл |
|
|
|
Частота вращения ведущего шпинделя, мни"' |
1365 |
12-1500 |
1500 |
Продолжительность цикла притирки, с |
20-180 |
2-20 |
0,7-40 |
Моищость главного привода, кВт |
3,0 |
5,5 |
6,5 |
Габаритные размеры, мм: |
1945 |
1540 |
2185 |
длина |
|||
ширина |
1490 |
1480 |
2132 |
высота |
1870 |
1810 |
1860 |
Масса, кг |
4100 |
4800 |
7120 |
Притирка осуществляется на специальных станках (мод. 5П725М, 5П725Е, 5П726ФЗ), обеспечивающих совместное вращение сопряженных зубчатых колес с легким торможением, автоматическое изменение взаимного положения шестерни и колеса и подачу абразивной смеси в зону зацепления (табл. 4.22). Станок мод. 5П726ФЗ выполнен с числовым программ ным управлением и имеет более широкие технологические возможности. При изменении вза имного положения шестерни и колеса обеспечивается притирка на всей поверхности зуба. Обычно происходят следующие движения: вертикальное — шестерни или колеса для про дольного перемещения пятна контакта; горизонтальное вдоль оси шестерни — для перемеще ния пятна контакта по высоте зуба; осевое в направлении оси колеса — для сохранения боко вого зазора в передаче.
Величины перемещений определяют опытным путем. В качестве абразива при при тирке применяют карбид кремния, карбид бора и электрокорунд зернистостью 3-6. Жид костью служит масло СЭЛ-1, которое поддерживает абразив во взвешенном состоянии и легко смывается при последующей мойке. Применяют состав из 45% абразива и 55% мас ла. Припуск на операцию притирки обычно не оставляют. Время процесса составляет 4-12 мин и подбирается опытным путем. Так же определяется величина тормозного мо мента. Существенным фактором для качественной притирки является поддержание одно
174 Глава 4
родного состава абразивной жидкости. Для этих целей применяют специальные агрегаты, обеспечивающие смешивание абразива и жидкости, подогрев и подачу смеси к притироч ным станкам.
Фирмой Глисон разработан усовершенствованный метод притирки «периметрнк», за ключающийся в том, что притирка происходит путем чередования четырех различных циклов, выполняемых по заданной программе. Вначале происходит притирка вдоль зуба по двум разным циклам, а затем в зоне головки и ножки зуба. При каждом цикле автома тически изменяются гипоидное смещение, монтажные расстояния, тормозной момент и число ходов. Метод «периметрнк» удовлетворяет практически любым требованиям при тирки.
После притирки снова подбирают пары на контрольно-обкатном станке. У подобран ных пар маркируют отклонения от номинального базового расстояния или фактическое базовое расстояние на шестерне, а на колесе — величину бокового зазора. Порядковый но мер пары помечают на колесе и шестерне или на бирке. Иногда детали связывают прово локой. Зубья колеса и шестерни, используемые при измерении бокового зазора, также маркируют (чаще всего знаком «X»).
Основные характеристики контрольно-обкатных станков для конических передач приведены в табл. 4.23; нормы точности контрольно-обкатных станков — в табл. 4.24.
|
|
|
|
|
|
Таблица 4.23 |
|
|
Контролыю-обкатныс станки для конических передач |
|
|||||
Основные |
|
|
М о д е л ь с та н к а |
|
|
||
|
|
|
|
|
|
||
характеристики |
5 Б 7 2 0 |
5В 7 2 2 |
5Г725 |
5 Д 7 2 5 |
5 Б 7 2 6 |
5 А 7 2 7 |
|
|
|
||||||
Наибольший диаметр |
125 |
200 |
500 |
500 |
800 |
1600 |
|
проверяемых колес, мм |
|
|
|
|
|
|
|
Наибольший модуль |
2,5 |
8 |
10 |
10 |
16 |
30 |
|
проверяемых колес, мм |
|
|
|
|
|
|
|
Наибольшее |
расстояние |
|
|
225 |
|
550 |
880 |
между осями при контро |
|
|
|
|
|
|
|
ле цилиндрических пере |
|
|
|
|
|
|
|
дач. мм |
|
|
|
|
|
|
|
Угол между осями |
45-180 |
90 |
45-180 |
90 |
0-180 |
0-180 |
|
шпинделей, град. |
|
|
|
|
|
|
|
Наибольшее |
гипоидное |
|
|
|
|
|
|
смещение оси ведущего |
|
|
|
|
|
|
|
шпинделя относительно |
|
|
|
|
|
|
|
оси ведомого, мм: |
|
|
|
|
|
|
|
вверх |
|
32 |
50 |
125 |
125 |
200 |
400 |
вниз |
|
32 |
60 |
125 |
125 |
110 |
250 |
Расстояние от оси ведо |
0-140 |
65-160 |
120380 |
150300 |
100560 |
230-1100 |
|
мого шпинделя до торца |
|
|
|
|
|
|
|
ведущего при мсжоссвом |
|
|
|
|
|
|
|
угле 90°. мл! |
|
|
|
|
|
|
|
Наименьшее |
и наиболь |
0-100 |
50-160 |
0-180 |
100-200 |
0-1260 |
0-760 |
шее расстояния от оси ве |
|
|
|
|
|
|
|
дущего шпинделя до тор |
|
|
|
|
|
|
|
ца ведомою при мсжосс |
|
|
|
|
|
|
|
вом угле 90°. мм |
|
|
|
|
0153, ко |
0153, |
|
Конус ведущего и ведо |
Морзе |
Морзе 6 |
Метриче |
Метриче |
|||
мого шпинделя |
0,2,4 |
|
ский 100 |
ский 100 |
нусность |
конус |
|
|
|
|
|
|
|
1:20 |
ность 1:20 |
Механическая обработка конических зубчатых колес |
175 |
||||||
|
|
|
|
|
Продолжение таблицы 4.23 |
||
Осноинмс |
|
|
Модельстанка |
|
|
||
характеристики |
5Б720 |
50722 |
5Г725 |
5Д725 |
5Б726 |
5Л727 |
|
|
|||||||
Частота вращения веду |
600-1000 |
1200/800 |
630/1260 |
300-3000 |
220/450 |
200/400 |
|
щего шпинделя. мшГ1 |
Бесступен |
|
|
|
|
625/1250 |
800 |
Регулирование числа |
Двухско- |
Двухско- |
Бессту |
Шкивами |
Шкивами |
||
оборотов ведущего |
чатое |
|Х)СТПММ ростным пенчатое идвухско- |
идвухско- |
||||
шпинделя |
|
двигате |
двигате |
|
ростмым |
ростным |
|
|
|
лем |
лем |
|
двигате |
двигате |
|
|
0.9 |
|
2,2/3,6 |
6,5 |
лем |
лем |
|
Мощность главного |
1.8/2,1 |
6,0/9,0 |
7,5/14 |
||||
привода, кВт |
|
|
|
|
|
|
|
Габаритные размеры, |
|
|
|
|
|
|
|
мм: |
1000 |
1540 |
2160 |
2330 |
2990 |
3600 |
|
длина |
|||||||
ширина |
850 |
1100 |
1750 |
1725 |
2640 |
2950 |
|
высота |
1380 |
1550 |
1900 |
1900 |
1905 |
2000 |
|
Масса, кг |
990 |
1700 |
4500 |
6290 |
6550 |
7100 |
|
|
|
|
|
|
|
Таблица 4.24 |
|
Нормы точности контрольно-обкатных станков для конических колес |
|||||||
|
(по ГОСТ 16473-80) |
|
|
|
|||
|
а. Геометрические нормы |
|
|
|
|||
|
|
Н аибольш ий диам етр |
|
Д опуск, мкм, |
|||
|
|
дли стайкой к ласса точности |
|||||
О тк л о нен ия |
|
контролируемого зубчатого |
|
|
|||
|
|
|
колеса, мм |
|
п |
В |
|
|
|
|
|
|
|
||
Торцевое биение ведущего и ведомого |
До 200 |
|
|
4 |
3 |
||
шпинделей |
|
Св. 200 до 500 |
|
5 |
4 |
||
|
|
« |
500 « |
800 |
|
6 |
4 |
Радиальное биение конического отвер |
До 125 |
|
|
5 |
3 |
||
стия ведущего и ведомого шпинделей: |
Св. 125 до 200 |
|
5 |
3 |
|||
а) у торца |
|
< |
200 « |
500 |
|
6 |
4 |
б) па расстоянии, мм: |
|
« |
500 « |
800 |
|
8 |
5 |
75 |
|
До 125 |
|
|
6 |
4 |
|
150 |
|
Св. 125 до 200 |
|
8 |
5 |
||
150 |
|
« |
200 « |
500 |
|
10 |
6 |
150 |
|
« |
500 4 |
600 |
|
12 |
8 |
Перпендикулярность осей ведомого |
|
|
|
|
|
|
|
и ведущего шпинделей (для станковс по |
|
|
|
|
|
|
|
стоянным углом между осями, равным |
|
|
|
|
|
|
|
90°) на расстоянии, мм: |
|
До 125 |
|
|
6 |
5 |
|
75 |
|
|
|
||||
100 |
|
Св. 125 до 800 |
|
12 |
10 |
||
Параллельность направления перемеще |
|
|
|
|
|
|
|
ния шпинделей соответствующим осям |
|
|
|
|
|
|
|
горизонтальной и вертикальной плоско |
|
|
|
|
|
|
|
стей на расстоянии, мм: |
|
До 125 |
|
|
12 |
8 |
|
75 |
|
|
|
||||
150 |
|
Св. 125 до 200 |
|
16 |
10 |
||
200 |
|
« |
200 4 500 |
|
20 |
12 |
|
300 |
|
4 |
500 4 800 |
|
25 |
16 |
176 |
|
Г л а в а 4 |
|
|
|
|
|
|
|
Продолжение таблицы 4.24 |
|
|
|
б. Нормы шума |
|
|
|
Отклонения |
Суммарная номинальная мощность |
|
Норма ip, дБЛ |
||
|
|
||||
|
прпполои, кВт |
П |
В |
||
|
|
||||
|
|
|
|
||
Скорректированный |
До |
1,5 |
4 |
82 |
79 |
уровень звуковой |
Св. 1,5 до |
90 |
87 |
||
мощности, дБ |
« |
4 « |
12,5 |
96 |
93 |
|
« 12,5 « |
40 |
102 |
- |
4.3. Зубошлифовальные станки для конических колес
Основные характеристики зубошлифовальных станков для конических колес пред ставлены в табл. 4.25.
Таблица 4.25
Зубошлифовальные станки для конических колес
Основные характеристики |
|
Модель станка |
|
|
|
|
|
|
|
|
|
|
5 8 П 7 0 В |
5А 871 |
| 5 8 К 7 0 В | |
5 А 8 7 2 В |
| 5 8 К 7 1 А |
Тип зубьев конических колес |
Прямые |
|
Круговые |
|
|
Наибольший диаметр |
320 |
500 |
425 |
500 |
800 |
обрабатываемых колес, мм |
|
|
|
|
|
Наибольший модуль |
8 |
10 |
6 |
14 |
140 |
обрабатываемых колес, мм |
|
|
|
|
|
Наибольшая ширина венца |
32 |
80 |
50 |
125 |
|
обрабатываемых зубчатых |
|
|
|
|
|
колес, мм |
|
|
|
|
|
Число обрабатываемых |
15-100 |
- |
10-100 |
5-150 |
|
зубьев |
|
|
|
|
|
Режим шлифования |
10-530 м/с |
2250-3150 мин-1 |
10-30 м/с |
10-30 м/с |
|
Диаметр шлифовального |
275 |
250,315 |
100-250 |
160,200 |
|
круга, мм |
|
|
|
400.500 |
|
Мощность главного привода, |
3 |
4 |
3 |
4 |
|
кВт |
|
|
|
|
|
Габаритные размеры, мм: |
3515 |
|
|
3460 |
|
длина |
2690 |
3515 |
|
||
ширина |
1970 |
1750 |
1970 |
2600 |
|
высота |
1715 |
2100 |
1715 |
2115 |
|
Масса, кг |
8500 |
10500 |
8500 |
13300 |
|
Глава 5
МЕХАНИЧЕСКАЯ ОБРАБОТКА ЧЕРВЯЧНЫХ КОЛЕС И ЧЕРВЯКОВ
5.1. Основные конструктивные особенности червячных передач
Различают цилиндрические и глобоидные червячные передачи.
Червяк цилиндрической червячной передачи. Теоретическая поверхность витка чер вяка — винтовая, образована с осью, совпадающей с осью червяка.
Различают следующие разновидности цилиндрических червяков.
Копволютный червяк ZN, или цилиндрический геликоидный червяк, теоретический торцовый профиль витка которого является удлиненной или укороченной эвольвентой. Обычно применяются червяки, теоретический торцовый профиль которых является уд линенной эвольвентой.
Существует три вида конволютных червяков: конволютный червяк ZN\ с прямоли нейным профилем витка, конволютный червяк ZN2 с прямолинейным профилем впади ны, конволютный червяк ZN3 с прямолинейным нормальным профилем витка (рис. 5.1).
Архимедов червяк ZA, или цилиндрический геликоидный червяк. Теоретический тор цовый профиль витка червяка является архимедовой спиралью, теоретическая поверх ность архимедова червяка может быть образована при винтовом движении прямой, пере секающей ось червяка (рис. 5.2).
Эвольвентный червяк Z1, или цилиндрический геликоидный червяк, теоретический торцовый профиль витка которого является эвольвентой окружности. Эвольвентный чер вяк представляет собой частный случай конволютного червяка, у которого прямая, обра зующая поверхность витка, касательная к винтовой линии, находится на соосной цилинд рической поверхности (рис. 5.3).
ё=А
Рис. 5.1. Конволютный червяк ZN |
Рис. 5.2. Архимедов червякZA |
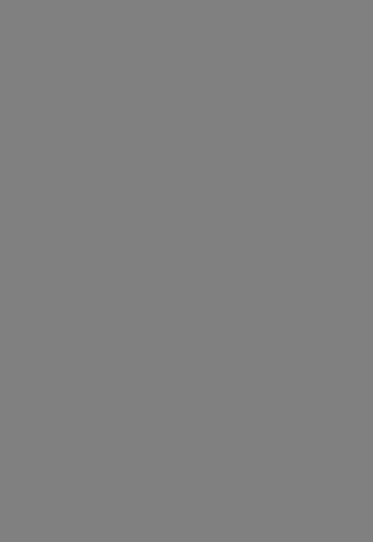
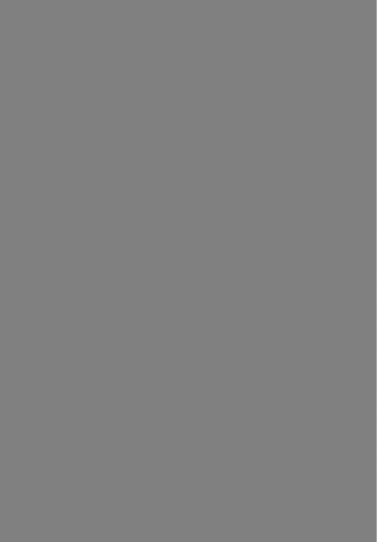
180 |
Г л а в а 5 |
5.2. Нарезание цилиндрических червяков
В зависимости от масштаба производства нарезание червяков может производиться профильными резцами на токарных станках, дисковыми и пальцевыми фрезами на уни версально-фрезерных станках, обкаточными резцами типа долбяков на специальных чер вячно-долбежных станках. Для окончательной обработки применяют шлифование про филя, притирку и полирование.
Нарезание червяков методом фрезерования является более производительным, чем нарезание их профильными резцами на токарных станках. Однако при фрезеровании чер вяк не получается с прямолинейным профилем витка, так как ось производящего конуса фрезы повернута на угол подъема витка по делительному цилиндру червяка и образует криволинейную поверхность витка. Поэтому при фрезеровании получаются отклонения профиля витка от прямолинейности, которые возрастают при обработке многозаходных червяков и требуют специальных фрез для обработки зубьев колес.
5.2.1. Нарезание цилиндрических червяков дисковыми фрезами
При нарезании цилиндрических червяков дисковыми фрезами фреза должна устанав ливаться так, чтобы средняя точка фрезы А была в горизонтальной осевой плоскости чер вяка, а ось вращения фрезы — наклонена на угол, равный углу подъема у линии витка чер вяка (рис. 5.10). При такой установке червяк профилируется в нормальном сечении по впадине. В процессе фрезерования фасонной дисковой фрезой профиля витков червяка возможно получение следующих видов червяков, имеющих сечения с прямолинейным профилем витков, которые представлены на рис. 5.11.
Архимедов червяк А имеет прямолинейный профиль в осевом сечении АА и криволи нейный профиль в нормальном сечении. Торцовое сечение червяка — архимедова спи раль; дисковая фреза должна иметь криволинейный профиль.
|
Рис. 5 .11 . Сечения цилиндрических червяков: |
|
A4 — осевое сечение; ББ — нормальное сече |
Рис. 5 .1 0 . Установка дисковой фрезы |
ние по впадине; ВВ — нормальное сечение |
по витку; ГГ — нормальное сечение по боковым |
|
при нарезании цилиндрических червяков |
поверхностям |