
книги / Технология производства и методы обеспечения качества зубчатых колес и передач
..pdfМеханическая обработка цилиндрических зубчатых колес |
141 |
товки легче деформируются при закреплении и под давлением инструмента. Чтобы не до пустить попорота заготовки зубчатого колеса на зуборезном станке, необходимо жестко зажать ее на оправку между двумя дисками. Однако при этом под действием зажимного усилия вепец деформируется, и поверхность вершин зубьев приобретает бочкообразную форму. После снятия сжимающего усилия первоначальное положение венца восстанавли вается, в результате чего получаются вогнутые в осевом направлении профили зубьев. Это приводит к неравномерному распределению нагрузки по длине зуба. Уменьшение усилия сжатия заготовок, применение соответствующего инструмента, а также малые по дачи способствуют снижению этого нежелательного эффекта.
Низкая теплопроводность материала приводит к снижению скорости передачи тепла, образующегося в пластмассовом колесе при резании. Следствием этого является размяг чение материала или деструкция поверхности. Уменьшить количество выделяемого тепла можно с помощью хорошо заточенного инструмента, небольшой подачи, не слишком вы сокой скорости резания, а также благодаря хорошему охлаждению.
Таблица 3.48
Влияние вида механической обработки на точность пластмассовых зубчатых колес [4]
М а тер и ал
Fir
.
и степеней точности по Г О С Т 91 7 8 -8 1 (по д чертом)
/,,1,г |
| |
* |
1 |
Fn |
| |
Зубофрсзсровапис (ор-•53,5-125,5 м/мин; S - 0,238-0,589 мм/оборот заготовки)
Полиамил |
30-37 |
8-13 |
15-31 |
30-42 |
45-70 |
ПА 6 |
7 |
6-7 |
10 |
7-8 |
7-8 |
Полиамид |
30-46 |
6-16 |
23-36 |
31-50 |
41-68 |
ПА 610 |
7-8 |
5-8 |
10 |
8-9 |
7-8 |
Полиамил |
31-45 |
4-19 |
12-24 |
25-44 |
43-62 |
АК7 |
7 |
5-8 |
10 |
7-9 |
7-8 |
Зубодолбленис(ор- |
15-40 м/мип; S~■0,01-0,187 мм/двойиой ход долбяка) |
|
|||
Полиамид |
30-46 |
5-18 |
15-27 |
30-44 |
51-70 |
ПА 6 |
7-8 |
5-8 |
10 |
8-9 |
8-9 |
Полиамид |
37-49 |
1=Ш |
10-30 |
30-40 |
32-53 |
ПА 610 |
7-8 |
6-8 |
9-10 |
8 |
7-8 |
Полиамид |
37-57 |
10-16 |
15-28 |
26-44 |
30-70 |
АК7 |
7-8 |
7-8 |
10 |
7-9 |
7-9 |
Шевингование (ир- 9,54-23,8 м/мин; 5 - 0,021-0,104 мм/оборот изделия) |
|
||||
Полиамид |
- |
6-10 |
4-19 |
22-28 |
27-60 |
ПА 6 |
6-7 |
6-8 |
7-8 |
6-8 |
|
Полиамид |
- |
6-13 |
4= 15. |
15-27 |
18-43 |
ПА 610 |
6-8 |
6-10 |
6-8 |
6-7 |
|
Полиамид |
- |
3 - |
119-18 |
22-39 |
26-44 |
АК7 |
4 - |
97-10 |
7-8 |
6-7 |
Наиболее благоприятным является диапазон подач S - 1,5-3,5 мм/ч. При S < 1 мм возрастает колебание измерительного межосевого расстояния за оборот колеса в двухпро фильном зацеплении. Например, при обработке зубчатых колес из полиамида при
142 Г л а в а 3
S = 0,73 мм/ч образовывались заусенцы или наплывы на кромках головки зуба, которых нельзя было избежать даже при охлаждении заготовки маслом. При попутном фрезерова нии получены шестерни, имеющие лучшее качество поверхности, чем при встречном фре зеровании, так как стружка вначале ее образования не разрушалась [4]. При этом упроща ется также процесс удаления стружки.
Зубчатые колеса, полученные методом зубодолблсния, отличаются более низкой точ ностью по сравнению с зубофрезерованными колесами, особенно по показателям Fjn f pbr « V Шевингование повышает степень точности фрезерованных зубчатых колес по F'r и Fn примерно на одну степень и по F$r — почти на две-три степени (табл. 3.48).
При оптимальных режимах зубообработки (табл. 3.49) точность зубчатых колес соот ветствует 8, 9-й степени точности по ГОСТ 9178-81 при зубодолбленни, 7, 8-й — при зубофрезеровании и 6 ,7-й — при шевинговании. Для получения высокоточных пластмассо вых колес следует применять зубофрезерование или зубодолбление с последующим ше вингованием. Однако большое число проходов при шевинговании ухудшает качество рабочей поверхности зуба (появляются канавки глубиной до 20-30 мкм). В процессе зубонарезания червячными фрезами и зуборезными долбяками из-за снятия стружки очень малого сечения образуются трудноудалимые заусенцы, которые сравнительно легко уда ляются только при последующем шевинговании.
|
|
|
Таблица 3.49 |
Рекомендуемые режимы зубообработки мелкомодульных |
|||
|
зубчатых колес из полиамидов [4] |
|
|
|
Рскомсилусммс режимы зубообработки |
||
Механическая обработка |
Скорость резания ир, м/мпн |
Подача продольная (осепая) |
|
|
|||
|
|
S, м.м/оборот заготовки |
|
Зубодолбление |
20-30 |
0,03 |
-0,06 |
Зубофрезсропапис |
80-100 |
0,2 |
-0,4 |
Шевингование |
15-20 |
0,03 |
-0,05 |
Для получения качественной рабочей поверхности зубьев при шевинговании реко мендуется использовать специальные шеверы, перекрывающие обрабатываемую заготов ку по ширине.
Для шевингования характерна различная степень улучшения показателей точности (табл. 3.50). Недостаточно, но в большей степени, чем для металлических колес, исправ ляются погрешности, характеризующие кинематическую точность, — радиальное биение, накопленная погрешность шага и др., а также характеризующие плавность работы, — по грешности профиля и шага зацепления. Направление зуба можно исправить незначитель но, особенно у колес с большой шириной венца, но лучше, чем у металлических колес.
Повышение точности в большей степени зависит от коэффициента перекрытия при зацеплении шевера с пластмассовым зубчатым колесом, это объясняет существенное исправление погрешности косозубых колес. После шевингования шероховатость обрабо танной поверхности Rz улучшается до 0,80-0,63. Радиальная подача при шевинговании не вызывает характерного для металлических зубчатых колес значительного увеличения нагрузки, которое приводит к износу режущих кромок шевера. Поэтому радиальная подача при шевинговании пластмассового колеса может быть больше и достигать 0,OS- О.08 мм/ход.
Механическая обработка цилиндрических зубчатых колес |
143 |
||
|
|
Таблица 3.50 |
|
Значения показателей точности до и после шевингования [5] |
|
||
Показатель точности |
Погрешность при iiiciiiiiirooaiiiiii, мкм |
||
ло |
после |
||
|
|||
Накопленная погрешность шага Ft„ |
40-80 |
30-50 |
|
Радиальное биение зубчатого венца Fn, |
50-70 |
15-30 |
|
Колебание измерительного мсжоссиого расстояния за оборот |
60-100 |
20-40 |
|
зубчатого колеса F" |
|
|
|
Погрешность профиля зуба f/r |
20-70 |
10-20 |
|
Отклонение шага |
20-30 |
10-20 |
|
Колебание измерительного мсжоссвого расстояния па одном |
20-40 |
10-20 |
|
зубе /7' |
|
|
Тангенциальную подачу 5Тпри шевинговании выбирают в зависимости от необходи мой шероховатости поверхности зубьев, имея в виду, что величина 5, обратно пропорцио нальна шероховатости. Радиальная подача должна быть небольшой. Число калибровочных проходов для 8-й и 9-й степеней точности пластмассового зубчатого колеса составляет 2-3.
Проблемы износа и прочности шевсра при шевинговании пластмассовых зубчатых ко лес из ненаполнепных пластмасс практически не возникает. При шевинговании зубчатых колес из стеклонаполненных материалов заметен износ профиля зуба шевера, достигающий
0.01.0,05 мм по толщине зуба после обработки 100 зубчатых колес (ти = 2 мм, г - 26). При сравнении затрат на изготовление зубчатых колес механической обработкой н
литьем под давлением следует учитывать возможность получения колес требуемой точно сти и серийности изготовления. В соответствии с результатами исследований при средних показателях производства для зубчатых венцов, выполненных способом зубофрезерования, можно получить степень точности от 8 до 10, способом литья под давлением — не вы ше 10-12 [6].
Следует отметить, что в процессе обработки режущим инструментом могут возник нуть микротрещины даже на качественной поверхности, что сокращает срок службы зуб чатых колес. Для зубчатых колес, изготовленных способом литья под давлением, характе рен преимущественно аморфный рабочий слой на боковых сторонах зубьев, который бла гоприятно влияет на несущую способность передачи, поэтому литье под давлением следует рассматривать как наиболее надежный и экономичный способ изготовления зуб чатых колес в крупносерийном производстве.
Литература
1.Штучный Б. П. Механическая обработка пластмасс. М., 1974.
2.Стснанон А. А. Обработка резанием пысокопрочных композиционных полимерныхматериалов. Л.. 1974.
3.Кобаяши А. Обработка плас тмасс резанием. М., 1974.
4.Гуревич С. И., Ермаков D. А., Москалев М. А. Мелкомодульмыс зубчатые колеса из пластических масс. Применение пластмасс в промышленности. Вын. 10. М., 1962.
5.Беляев Б., Арнаудоп К., Козлова А. Зъбни нредавкн с нластмасоин колола. София, 1985.
6.Krause W. Plastzahnrâdcr. Berlin, 1985.
Глава 4
МЕХАНИЧЕСКАЯ ОБРАБОТКА КОНИЧЕСКИХ ЗУБЧАТЫХ КОЛЕС
4.1. Механическая обработка прямозубых конических колес
4.1.1. Методы обработки прямозубых конических колес
Принципиально все способы нарезания конических колес можно свести к двум техно логическим методам: обкатки и копирования.
При нарезании по методу обкатки сопряженные поверхности зубьев получаются в ре зультате зацепления нарезаемого зубчатого колеса с производящим колесом, роль которо го выполняют режущие кромки инструмента.
Метод копирования применяется при нарезании сравнительно грубых передач, так как имеются трудности изготовления точного инструмента с фасонным профилем.
В табл. 4.1 приведены сравнительные характеристики применения методов обкатки и копирования для нарезания конических колес с прямыми зубьями.
4.1.2. Нарезание конических колес с прямыми зубьями двумя зубострогальными резцами по методу обкатки
При данном методе нарезания резцы имеют профиль впадины зуба производящего колеса. В процессе обработки резцам и нарезаемому зубчатому колесу сообщается относи тельное обкатное движение, воспроизводящее зацепление нарезаемого и производящего зубчатых колес.
Профиль зубьев производящего колеса имеет форму равнобокой трапеции, как у зуб чатой рейки, и его зацепление с коническим колесом аналогично зацеплению рейки с ци линдрическим колесом.
Принципиальная схема станка для нарезания конических колес с прямыми зубьями двумя зубострогальными резцами по методу обкатки представлена на рис. 4.1, а.
Роль условного плоского производящего колеса 1 выполняет люлька 2 с двумя резца ми 3, повторяющими одну впадину такого колеса. Нарезаемое колесо 4 устанавливается в положение, идентичное его зацеплению с плоским производящим колесом.
|
Механическая обработка конических зубчатых колес |
145 |
||||
|
|
|
|
|
Таблица 4.1 |
|
|
Методы нарезания конических колес с прямыми зубьями |
|
||||
Метол |
|
Рекомендуемая |
Достигаемые показатели |
|
||
|
|
|
|
|
||
профнлм- |
Способ нарезания |
|
|
|
Модели |
|
область |
Произво |
Точность |
Шерохова |
|||
ропаиия |
|
применения |
станков |
|||
зуба |
|
дитель |
но ГОСТ |
тость Ra, |
|
|
|
|
|
ность |
1758-81 |
мкм |
|
Обкатка |
Строгание двумя зубо- |
Единичное |
25-100 |
6-8 |
3,2-1,6 |
5А26 |
|
етрогалы ii.iм11резцами |
и мелкосерий |
с/зуб |
|
|
5236П |
|
е прямолинейными |
ное производ |
|
|
|
5282 |
|
режущими кромками |
ство |
|
|
|
5А283 |
|
|
|
|
|
|
5286П |
|
Фрезерование двумя спа |
Серийное |
15-50 |
7-9 |
3,2-1,6 |
5230 |
|
ренными дисковыми фре |
и массовое |
с/зуб |
|
|
5С237 |
|
зами с прямолинейными |
производство |
|
|
|
5С267П |
|
режущими кромками |
|
|
|
|
5С277П |
|
|
|
|
|
|
5С27П |
Копиро |
Круговое протягивание |
Массовое про |
2-5 |
9-10 |
3,2 |
5С268 |
вание |
дисковой протяжкой |
изводство зуб |
с/зуб |
|
|
5С269 |
|
(способ «Рсвасайкл») |
чатых колес |
|
|
|
|
|
|
дифференциа |
|
|
|
|
|
|
лов cm до 8 мм |
|
|
|
|
|
Фрезерование дисковой |
Черновое на |
5-20 |
11-12 |
12,5-6,3 |
ЕЗ-11 |
|
модульной фрезой |
резание в мас |
с/зуб |
|
|
ЕЗ-40 |
|
|
совом произ |
|
|
|
|
|
|
водстве |
|
|
|
|
Люльке 2 и нарезаемому колесу придается согласованное вращение с помощью кине матической цепи 5 с оборотами, обратно пропорциональными числу их зубьев. Для обес печения процесса резцам сообщается возвратно-поступательное движение вдоль торца люльки. Таким образом, при возвратно-поступательном движении резцов происходит на резание зубьев конического колеса, а при одновременном вращении люльки с резцами выполняется обкатка зубьев, в результате чего резцами с прямолинейными профилями обрабатываются эвольвентпые профили колес. Последовательность расположения резцов относительно зубьев нарезаемого колеса представлена на рис. 4.1, б.
В связи с тем, что сразу нарезается только один зуб, люлька и колесо поворачиваются на угол, обеспечивающий полное нарезание зуба. Затем следует отвод колеса от резцов, поворот его и люльки в обратную сторону.
Станки, работающие по такому принципу, должны осуществлять движения: возврат но-поступательное (главное) — резцов; обкатки — согласованное вращение люльки и на резаемого колеса; подвода и отвода нарезаемого колеса к резцам; деления —периодиче ский поворот колеса для нарезания следующего зуба.
Точность нарезания зубьев колеса возможна лишь при правильной установке заго товки по отношению к центру станка О. Центром станка О называется точка, в которой пересекаются оси: люльки ООи шпинделя бабки изделия 00-, и вертикальная О, вокруг которой поворачивается стол 6 вместе с нарезаемым колесом. С центром станка О должна совпадать вершина начального конуса нарезаемого колеса и проходить через его плос кость, в которой движутся резцы.
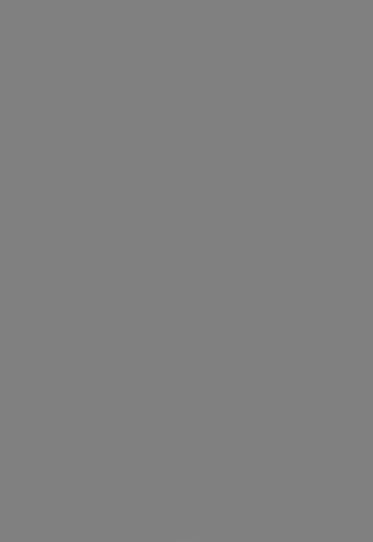
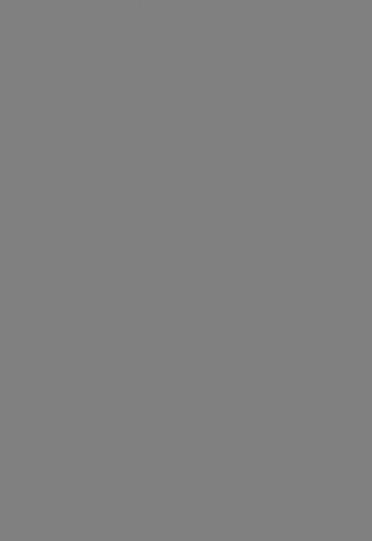
148 |
Г л а в а 4 |
|
Степень бочкообразности определяется величиной отвода на концах зуба, который |
может быть рассчитан по формуле |
A5= tg6(^/ô2/ 4+ rH —г„ ) .
где 5 — угол поднутрения.
Наладка станка для нарезания конических колес с прямыми зубьями по методу обкатки включает такие последовательно осуществляемые операции, как: настройка барабана подач, установка — углов поворота сегментов, угла люльки, положения фре зерных суппортов, угла поворота плиты бабки детали, осевой бабки детали; настрой ка — смещения стола, скорости резания, гитары деления, гитары обкатки и редукции.
У дисковых фрез, применяемых для нарезания конических колес с прямыми зубьями по методу обкатки, режущие кромки могут располагаться либо на плоскости, перпендику лярной оси вращения, либо на конической поверхности. При наличии угла поднутрения б,, режущие кромки располагаются на конической поверхности, что приводит к бочкооб разности формы зуба нарезаемых колес. Резцы головки имеют задний угол а - 10-12°, пе редний у = 20°. Заточка резцов производится по передней поверхности.
В комплекте, состоящем из двух фрез, одна должна быть праворежущей, другая — ле ворежущей.
Параметры дисковых фрез, применяемых для обработки колес на станках мод. 5С237, 5230 и 5С267П, приведены в табл. 4.2.
Таблица 4.2
Основные параметры дисковых фрез для нарезания конических колес
спрямыми зубьями
Мо д у л ь н ар е за ем о го к о л ес а, м м
П ар а м е т р ы |
М о д е л ь слипся |
0.5 |
0,8 |
1 |
1.5 |
2 |
3 |
4 |
6 |
8 |
|
|
|||||||||
Наружный диа |
5С237.5П23, |
150 |
150 |
150 |
150 |
150 |
150 |
150 |
150 |
150 |
метр фрезы, мм |
5С267П, 5230 |
275 |
275 |
275 |
275 |
275 |
275 |
275 |
275 |
275 |
Высота режущей |
5С237,5С267П, |
2,5 |
4 |
5 |
6,5 |
8 |
10 |
12 |
15 |
18 |
кромки, мм |
5230 |
|
|
|
|
|
|
|
|
|
Ширина носика |
5С237,5С267П, |
0.2 |
0,32 |
0,4 |
0,6 |
1 |
1.5 |
2 |
3 |
4 |
тезцов, мм |
5230 |
|
|
|
|
|
|
|
|
_ |
Угол поднутрения |
5С237, |
4° |
4е |
4е |
3°20' |
1°40' |
_ |
_ |
_ |
|
|
5С267П, 5230 |
- |
- |
- |
5° |
5° |
5° |
5° |
1°30' |
Г |
Режимы резания при обработке двумя дисковыми фрезами приведены в табл. 4.3. При этом для определения скорости резания выбирают поправочный коэффициент Kv по табл. 4.4.
|
|
|
|
|
|
Таблищ 43 |
|
Режимы резания при нарезании прямозубых конических колес |
|
|
|||||
|
двумя дисковыми фрезами |
|
|
|
|
|
|
|
|
Скорость реза |
Время обработки зуба t2,с/зуб. |
||||
Обработка |
Длина |
|
|
Модуль, мм |
|
||
зуба, мм |
ния, Vrofa. м/мип |
|
|
|
|||
|
|
|
|
|
|
||
|
|
|
4 |
5 |
6 |
7 |
8 |
Предварительная без обкатки |
20 |
35 |
_ |
_ |
12 |
15 |
16 |
|
30 |
|
_ |
_ |
15 |
18 |
20 |
|
40 |
|
- |
- |
18 |
20 |
22 |
Механическая обработка конических зубчатых колес |
149 |
Окончание таблицы 4.4
|
|
|
В ремя обработки зу ба tt,с /зу б . |
||||
О бр аб о тк а |
Д ли н а |
С корость реза |
М одуль, мм |
|
|
||
зуба, мм |
ния. |
м /м и н |
|
|
|||
|
|
|
|
|
|||
|
|
|
4 |
5 |
6 |
7 |
8 |
Однократная окончательная: |
|
|
|
|
|
|
|
простой способ с обкаткой (для колес |
20 |
45 |
10 |
12 |
16 |
24 |
28 |
с углом начального конуса 45°) |
30 |
|
12 |
16 |
20 |
28 |
32 |
|
40 |
|
16 |
20 |
24 |
32 |
33 |
Комбинированный способ (врезание |
20 |
45 |
- |
18 |
22 |
26 |
32 |
с последующей обкаткой для колесе уг |
30 |
|
- |
22 |
26 |
32 |
38 |
лом начального конуса 45е) |
40 |
|
- |
26 |
32 |
38 |
44 |
Окончательная обработка после фрезе |
20 |
45 |
- |
12 |
16 |
20 |
24 |
рования |
30 |
|
- |
16 |
20 |
24 |
28 |
|
40 |
|
- |
20 |
24 |
28 |
32 |
Окончательная обработка штампован |
20 |
35 |
- |
_ |
22 |
26 |
30 |
ного зуба |
30 |
|
- |
- |
26 |
30 |
34 |
|
40 |
|
~ |
- |
30 |
34 |
38 |
Примечания. 1. Режимы резания даны для колес нормальной точности при обработке в один про
ход. 2. Режимы резания рассчитаны на стойкость дисковых фрез Т„ - |
1500 мин. |
|
||
|
|
|
|
Таблица 4.4 |
Коэффициент скорости при нарезании прямозубых конических колее |
||||
|
двумя дисковыми фрезами |
|
|
|
О бр а б аты в ае м а я с та л ь |
18Х ГТ |
ЗОХГГ |
2 0 Х Н Р |
2 0Х Н М |
К.. |
0,9 |
0,8 |
0.9 |
1.0 |
4.1.4. Нарезание конических колес с прямыми зубьями по методу кругового протягивания
Данный способ разработан фирмой Глисон и назван «Ревасайкл» (рис. 4.4). Инструмент для нарезания представляет собой наборную фрезу-протяжку, составлен
ную из блоков по 4-5 резцов в каждом. Первые 10-13 блоков черновые, остальные 4-5 — чистовые. Каждая впадина нарезается отдельно, а затем производится деление на один зуб. При нарезании колесо остается неподвижным, а фреза вращается, совершая поступательное движение по направлению к образующей внутреннего конуса из положения 0 ( в 0 2 и об ратно. Черновые резцы имеют боковые и наружные режущие кромки и вырезают основную массу металла. У чистовых резцов режущие кромки только боковые, расположенные на пе ременном расстоянии от их средней диаметральной плоскости и образующие винтовую по верхность. Такое расположение режущих кромок при заданном перемещении оси фре зы-протяжки вдоль зуба позволяет сузить его от наружного конца к внутреннему.
За один оборот протяжки производится полная обработка впадины. Делительный по ворот нарезаемого колеса происходит в момент нахождения против колеса сектора фре зы-протяжки, свободного от резцов.
По сравнению со всеми известными способами нарезания конических прямозубых колес данный позволяет получить наиболее высокую производительность. Время обра ботки зуба составляет 1,5-6 с. Однако вследствие технологических затруднений профили зубьев фрезы-протяжки выполняются приближенно по дугам окружностей, вследствие чего данный метод применяется только в тех случаях, когда требования к точности наре заемых колес невысоки.
150 |
Глава 4 |
Рис. 4.4. Схема нарезания конических колес с прямыми зубьями по методу кругового протягивания
Режимы резания при обработке методом протягивания приведены в табл. 4.5.
|
|
|
Таблица 4.5 |
|
Режимы резания при нарезании прямозубых конических колес |
||||
методом кругового протягивания |
|
|||
Обработка |
Модуль, мм |
Скоростьреза |
Время обработки |
|
ния V, м/мин |
одногозубаГ2,с/зуб |
|||
|
|
|||
Однократная окончательная |
4 |
35 |
3 |
|
|
5 |
30 |
3,5 |
|
|
6 |
28 |
4 |
|
|
7 |
25 |
5 |
|
Окончательная после предварительной |
8 |
20 |
6 |
|
6 |
30 |
3,5 |
||
|
7 |
28 |
4 |
|
|
8 |
25 |
5 |
Примечания. 1. При недостаточной жесткости станка скорость резания нужноуменьшать на 20%, а время обработки одного зуба увеличивать на 20%. 2. При обработке на приведенных режимах резания нормализованной стали 20ХНМ стойкость Ти- 1000 мин.
Машинное время при нарезании конических прямозубых колес двумя дисковыми фрезами, двумя зубострогальными резцами или круговой протяжкой равно
Т » - & / 60,
где tz — время на обработку одного зуба, с.