
книги / Технология производства и методы обеспечения качества зубчатых колес и передач
..pdfЧАСТЬ I
ОБЩИЕ ТРЕБОВАНИЯ
КТЕХНОЛОГИЧНОСТИ
ИЭКСПЛУАТАЦИОННЫМ
ХАРАКТЕРИСТИКАМ ЗУБЧАТЫХ КОЛЕС
ИПЕРЕДАЧ
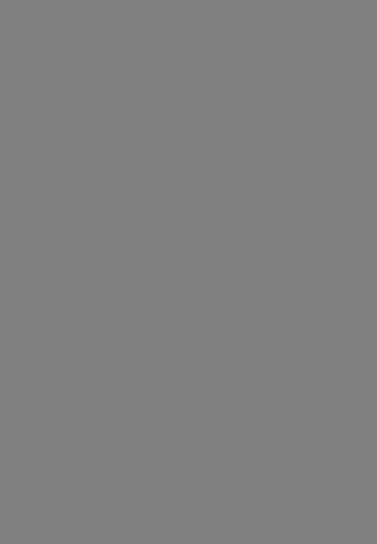
Глава 1
ОСНОВНЫЕ ТРЕБОВАНИЯ К ТЕХНОЛОГИИ ИЗГОТОВЛЕНИЯ ЗУБЧАТЫХ КОЛЕС МЕХАНИЧЕСКОЙ ОБРАБОТКОЙ
1.1.Общие принципы выбора технологического процесса изготовления зубчатых колес в условиях массового производства
Выбор технологического процесса изготовления зубчатых колес зависит от объема их выпуска, требуемой точности зубчатого венца, конфигурации и размеров, способа получе ния заготовок, термообработки, имеющегося оборудования и ряда других факторов.
Процесс изготовления зубчатого колеса включает следующие основные этапы: полу чение заготовок, их предварительную термическую обработку под зубонарезание, зубонарезание, термическую и финишную обработку зубчатых колес.
На этапах нарезания, зубозакруглення, снятия фасок и зубошевиигования происхо дит формообразование зубьев, причем нужно обеспечить максимально возможную точ ность по всем элементам профиля.
При термической обработке особое внимание необходимо уделять снижению дефор маций, так как от их характера в значительной мере зависит точность венцов термически обработанных нешлифованных зубчатых колес.
Снижение точности зубчатого венца в процессе термообработки следует компенсиро вать ужесточением примерно на одну степень норм точности на предшествующих опе рациях.
Наиболее распространенные автомобильные и тракторные зубчатые передачи, пере дачи сельскохозяйственных машин изготовляются, как правило, без зубошлнфования. Большинство из них для обеспечения эксплуатационных требований должно иметь 8-10-ю степень точности по ГОСТ 1643-81 и ГОСТ 1758-81.
Отсутствие при изготовлении этих передач процесса зубошлнфования объясняется малой его производительностью, а также возможностью возникновения при больших объ емах выпуска шлифовальных дефектов в виде прижогов, что приводит к резкому сниже нию работоспособности передач. В целом применение зубошлнфования для вышеуказан ных передач экономически нецелесообразно. Вследствие этого следует обращать особое внимание на уменьшение погрешностей изготовления передач на всех этапах. Для этого рекомендуется:
—с целью повышения точности установочных поверхностей шестерен со шлицевыми отверстиями их протягивание производить па вертикально-протяжных станках, а подрез ку торцов — на оправках, что исключает перекос;
—для повышения точности установочных поверхностен шестерен с гладкими отвер стиями их алмазную расточку осуществлять с подрезкой торцов;
24 |
Г л а в а 1 |
—базирование колес на операциях зубофрезерования (зубодолбления) и зубошевингования производить по одним и тем же установочным поверхностям;
—при нарезании зубьев под шевингование обеспечить максимально возможную сте
пень точности по накопленной погрешности окружных шагов и направлению зубьев;
— профиль червячной фрезы для нарезания колес под шевингование модифициро вать таким образом, чтобы глубина впадины была увеличена до (0,30-0,35)ш для обеспе чения радиального зазора при шевинговании, а ножка зубьев колес была подрезана так, чтобы в станочном зацеплении шевера обрабатывался полный рабочий участок профиля зубьев и не происходило касания головок зубьев шевера в зоне галтелей за пределами ра бочих участков профилей зубьев;
—начальный коэффициент перекрытия станочного зацепления зубьев шевера и коле са (с учетом среза головки и подреза ножки под шевингование) выбирать не менее 1,1;
—базирование обрабатываемого колеса на шевинговальном станке обеспечивать
сминимально возможным радиальным биением и перекосом нарезанного колеса относи тельно оси вращения;
—при газовой цементации колес применять специальные приспособления для их ус
тановки, препятствующие относительному смещению ступицы и венца;
—при закалке колес больших размеров использовать специальные закалочные штам пы, а для особо ответственных деталей — закалку в штампах на прессах с пульсирующей нагрузкой;
—для уменьшения деформации цементованных колес из сталей, не содержащих нике
ля, закаливать их с подстуживанием непосредственно после цементационного нагрева;
—при закалке колес без штампов обеспечить вертикальное положение деталей при расположении их на поддонах;
—для уменьшения влияния на работу передачи погрешностей деформации, возни кающей при термообработке, применять профили зубьев, модифицированные по высоте и длине;
—при использовании зубохонингования обеспечить зацепление хона и колеса с по люсом в зоне ножки за счет значительного отрицательного смещения исходного контура хона;
—при невозможности изготовления всей партии колес по заданным техническим ус ловиям подбирать зубчатые колеса парами.
1.2.Методы получения заготовок зубчатых колес
Наиболее распространенным методом получения заготовок зубчатых колес является штамповка на: паровоздушных штамповочных молотах, кривошипных горячештамповочных прессах и горизонтально-ковочных молотах с вертикальным разъемом матриц.
Получают развитие такие прогрессивные методы, как точная штамповка на многопо зиционных горячештамповочиых пресс-автоматах; штамповка заготовок с предваритель но и окончательно оформленным зубом, не требующая дальнейшей механической обра ботки; безоблойная штамповка заготовок в закрытых штампах на универсальном штампо вочном оборудовании; безуклонная штамповка на обрезных прессах; горячая накатка зубьев на зубопрокатиых станках.
Точная штамповка на многопозиционных горячештамповочных автоматах позволяет снизить расход металла на деталь до 20%, повысить производительность труда в 6—10 раз,
Требования к технологии изготовления зубчатых колес механической обработкой |
25 |
а также точность поковок за счет минимальных припусков на механическую обработку и кузнечных напусков.
При прокатке штампованных поковок цилиндрических зубчатых колес формуются зубья на нагретой заготовке с обжатием ее вращающимися зубчатыми валками. Процесс прокатки цилиндрических зубчатых колес производится с осевой подачей заготовки и ра диальной подачей валков. Изготовление цилиндрических зубчатых колес методом про катки на зубопрокатных станках позволяет сэкономить в объеме 15-20% металла (от веса заготовки), снизить трудоемкость обработки на 20-25%.
Горячее накатывание зубьев применяют вместо чернового зубонарезаиия при изго товлении зубчатых колес с модулем более 6 мм.
Производительность зубонакатных станков составляет в среднем 15-20 колес в час. Один стан может заменить до восьми зуборезных полуавтоматов и до пяти токарных по луавтоматов. Для горячего накатывания зубчатых колес применяются зубопрокатные ста ны мод. ЗПС-350, ЗПС-800 и ЗПС-1250 (350,800,1250 — ширина зуба колеса, умножен ная на модуль в мм). Заготовкой для горячего накатывания служит необработанная штам пованная поковка. Станы снабжены загрузочным устройством консольно-поворотного типа и секторными индукторами для нагрева поковок перед прокаткой.
Горячая накатка зубьев конических колес выполняется на зубопрокатных станах мод. 569. Станы оснащены индукторами для нагрева поковок перед накаткой. Рабочий цикл станов полностью автоматизирован. Недостаток этого процесса состоит в необходи мости предварительной токарной обработки поковок зубчатых колес перед накаткой.
Горячая штамповка конических зубчатых колес применяется для колес с модулем свыше 5 мм взамен операции чернового нарезания. Производительность достигает 300 де талей в час.
Штамповка поковок зубчатых колес в закрытых штампах осуществляется на горячештамповочпых кривошипных прессах двойного действия в разъемных матрицах с уси лием 6300, 10 000, 16 000 и 25 000 кИ. Отличительной особенностью таких прессов явля ется наличие внутреннего (деформирующего) и внешнего (прижимающего) ползунов, ки нематически связанных между собой.
Процесс штамповки поковок в закрытых штампах позволяет снизить расход металло проката на 5-30%, уменьшить трудоемкость механической обработки и расход энергоре сурсов на нагрев заготовок.
Методом порошковой металлургии изготовляются мало- и средненагруженные высо коскоростные зубчатые колеса с диаметром 30-200 мм. В качестве материала используют ся железные порошки, которые спекаются в закрытых штампах с усилием прессования до 500 кН при нагреве до 900-1100 °С. Для повышения твердости до 37 HRCBполученную заготовку нагревают до 430 °С, а до 61-66 HRC,, —азотируют в горячей соляной кислоте на глубину 0,02—0,03 мм.
Предварительную термическую обработку заготовок производят с целью улучшения структуры поковок, ее обрабатываемости резанием, снятия внутренних напряжений, сни жения мощности, затрачиваемой на резание. В отдельных случаях требуется, чтобы в про цессе предварительной термической обработки создавалась структура, которая обеспечи ла бы минимальные деформации при окончательной термической обработке. Хорошая об рабатываемость для средпеуглероднстых сталей в большинстве случаев достигается нормализацией при температуре 900-950 °С или отжигом при 900 °С.
Однако нормализация не обеспечивает стабильности структуры и твердости поковок, что приводит к широкому разбросу величин деформации и короблению зубчатых колес при химико-термической обработке.
26 Г л а в а 1
Рациональной является первичная термическая обработка (нормализация и отжиг) с использованием защитных атмосфер, что позволяет получить экономию металла за счет устранения процесса окалннообразования.
Более прогрессивный вид первичной термообработки — изотермический отжиг, кото рый дает возможность снизить деформацию при последующей термообработке, улучшить обрабатываемость резания, увеличить стойкость режущего инструмента. Такой метод наиболее эффективен при обработке зубчатых колес, требующих высокой точности при минимальной деформации. Кроме того, изотермический отжиг поковок позволяет увели чить скорость резания в процессе механической обработки до 20%.
Механическая обработка заготовок под зубопарезаиие производится с целью улучше ния качества подготовки базовых поверхностей, применяемых при зубонарезании и от делке зубчатых колес. При плохой обработке установочных баз невозможно обеспечить точность нарезания зубчатых колес.
Токарная обработка заготовок насадных зубчатых колес осуществляется в основном по трем схемам, в зависимости от объема выпуска, наличия оборудования и инструмента, а также технического уровня предприятия.
По первой схеме токарная обработка контура производится на многорезцовых полуав томатах и универсальных токарных станках. Базовое отверстие обрабатывается сверлением или зенкерованием на вертикально-сверлильных станках с последующим протягиванием на протяжных станках. Недостаток такой технологии — низкая производительность.
По второй схеме токарная обработка выполняется на многошпнпдельиых вертикаль ных и горизонтальных полуавтоматах (автоматах). Данная технология обеспечивает вы сокую производительность за счет совмещения операций на одном станке, сокращаются численность рабочих, количество межопсрацпонных перемещений деталей, высвобожда ются производственные площади и оборудование. Недостатком обработки по такой схеме является сложность автоматизации загрузки и выгрузки деталей.
По третьей схеме обработка осуществляется на токарных станках фронтального типа. При этом производится полная обработка контура зубчатого колеса, обеспечивается сво бодный доступ к заготовке загрузочных устройств, что позволяет полностью автоматизи ровать процесс токарной обработки.
Для получения требуемой точности базовых поверхностей применяются две основ ные схемы:
—обработка отверстий по 6-7-му квалитету точности, затем чистовая обработка опорных торцов на разжимной оснастке;
—одновременная обработка отверстий и торца.
По первой схеме отверстие обрабатывается протягиванием обычными быстрорежу щими протяжками либо протяжками с твердосплавными выглаживающими кольцами, ал мазным хонингованием или шлифованием.
Каждый из этих методов имеет свои достоинства и недостатки. Протягивание обыч ными протяжками дает высокую производительность, но требует точности их изготовле ния, соблюдения геометрических параметров при переточке, стабильности структуры ма териала заготовок. Протяжки с твердосплавными выглаживающими кольцами позволяют получить чистоту обработанной поверхности и размерную стойкость, но требуют выпол нения тех же условий, что и при использовании обычных быстрорежущих протяжек. Хо нингование отличается стабильностью процесса, но трудоемкость изготовления детали при этом увеличивается.
Чистовая обработка торцов по первой схеме производится на станках повышенной точности и, как правило, с применением разжимных оправок.
Требования к технологии изготовления зубчатых колес механической обработкой |
27 |
Хорошие результаты могут быть получены при использовании шестикулачных опра вок. Биение базового торца при обработке на этих оправках составляет 0,02-0,03 мм на диаметре 100 мм.
По второй схеме базовые поверхности обрабатываются на алмазно-расточных, токар ных (повышенной точности) и внутришлифовальных станках.
Алмазное растачивание и подрезка обеспечивают высокую точность по перпендику лярности отверстия и торца. Недостатками процесса являются нестабильность точности отверстия в пределах 6-го квалитета и частая подиаладка резцов.
В зависимости от типа и конструкции зубчатых колес, а также объема выпуска и имеющегося оборудования применяются различные технологические процессы механиче ской обработки заготовок под зубонарезание. Однако основным требованием к ним явля ется обеспечение необходимой точности базовых поверхностей, обусловленной точно стью операции зубопарезанпя и схемой базирования.
1.3.Выбор базовых поверхностей
Важнейший этан разработки принципиальной схемы технологического процесса - выбор базовых поверхностей.
По назначению базы подразделяются на конструкторские, технологические и измери тельные.
Конструкторские базы определяют положение зубчатого колеса в собранном узле. Технологические базы определяют положение заготовки зубчатого колеса в процессе из готовления. Измерительные базы служат для ориентации зубчатого колеса относительно средств измерений.
В механической обработке с каждой последующей операцией повышается точность формы, размеров и взаиморасположения поверхностей летали.
Таким образом, между черновыми и чистовыми операциями имеется ряд промежу точных, постепенно изменяющих форму детали. Следует стремиться к тому, чтобы для всех этих операций использовать те же базы, что и для финишных, однако практически это не всегда возможно. В связи с этим приходится изыскивать промежуточные базы.
Нужно иметь в виду, что смена баз всегда приводит к изменению взаимного располо жения поверхностей, обработанных от различных баз. Поэтому надо изыскивать такие по верхности для промежуточных баз, которые можно было бы использовать если не для всех промежуточных операций, то хотя бы для большинства из них.
На операциях рекомендуется совмещать технологические базы с конструкторскими посадочными поверхностями. Однако полное совмещение этих баз на всех операциях практически невозможно. При силах резания, возникающих в процессе нарезания и ше вингования зубьев, в качестве опорной технологической базы целесообразно использо вать один из торцов зубчатого венца, обработанный совместно с основными посадочными поверхностями.
При обработке зубьев шевингованием технологические базы должны совпадать с ба зами, использовавшимися при чистовом нарезании зубьев. Это обеспечивает нанвысшую точность шевингованных зубьев.
При изготовлении насадных зубчатых колес с цилиндрическим гладким или шлице вым отверстием в качестве технологических баз при зубообработке используются поса дочное отверстие и опорный торец. Благодаря симметричности формы таких зубчатых ко лес выбор базового опорного торца для зубообработкн в данном случае не имеет принци пиального значения.
28 Г л а в а 1
При изготовлении насадочных зубчатых колес со шлицевым отверстием в качестве центрирующей технологической базы рекомендуется принимать внутренний диаметр не зависимо от системы центрирования соединения в механизме. Это позволит сохранить единство технологических баз на протяжении всей обработки детали. Для наружного цен трирования шлицевого соединения это требует применения комбинированных протяжек с одновременной обработкой внутреннего и наружного диаметров шлицевого отверстия.
Если узкие зубчатые колеса устанавливаются на зубообрабатывающих станках паке том, оба торца, используемые в качестве опорной технологической базы, должны быть па раллельными между собой.
При изготовлении зубчатых колес с шейками в качестве центрирующей технологиче ской базы при зубонарезании рекомендуется использовать одну из посадочных шеек, а опорной базы — торец зубчатого венца.
Опорной технологической базой при зубообработке многовенцовых зубчатых колес обычно служит тот торец зубчатого венца, который обеспечивает возможность установки детали при обработке зубьев всех венцов.
Если в детали имеются отверстия разного диаметра, в качестве центрирующей техно логической базы при нарезании и шевинговании зубьев рекомендуется использовать от верстие меньшего диаметра.
Технологические базы при термической обработке зубчатых колес необходимо выби рать так, чтобы изменение положения зубчатого венца относительно оси посадочных по верхностей было минимальным.
При зубоотделочных операциях установочными базовыми поверхностями служат центровые фаски, шейки валов, посадочные отверстия насадных колес, шейки ступиц. По сле термической обработки технологические базы подвергаются специальной отделке или восстановлению.
В процессе восстановления технологических баз после термической обработки зубча тые венцы должны быть снова правильно сориентированы по отношению к этим базам.
Технологические базы и опорные поверхности должны обрабатываться за одну установ ку. Раздельная их обработка приводит к возникновению дополнительных погрешностей.
При отделке посадочного отверстия после закалки зубчатого колеса в качестве опор ного следует использовать тот торец, который служит технологической базой при предше ствующей обработке.
Торец венца или диска, используемый как опорная технологическая база при зубошлифовании закаленных колес, шлифуют после термической обработки только до устра нения черноты на площадках, равномерно расположенных по окружности. Поэтому на обра ботку этих поверхностей специальных припусков не оставляют. Последующую их обработку производят в пределах разности допусков на ширину зубчатого венца или толщину диска.
Наиболее точным методом восстановления взаимного положения установочных баз и зубчатого венца при шлифовании базовых поверхностей является базирование колеса по делительной окружности венца.
При шлифовании посадочных отверстий в конических зубчатых колесах применяется центрирование по трем стальным закаленным шарикам, помешенным между зубьями.
Исправленные фаски должны прилегать к центрам не менее чем на 70% своей поверх ности без разрыва по окружности.
Для зубчатых колес автомобилей и тракторов 7-9-й степеней точности ориентиро вочно можно назначать точность базовых поверхностей по табл. 1.1.
При назначении норм точности на базовые поверхности заготовок зубчатых колес следует исходить из того, что суммарная погрешность их базирования не должна превы шать 50-60% соответствующей погрешности зубчатого колеса. В табл. 1.2 приведены ре-
Требования к технологии изготовления зубчатых колес механической обработкой |
29 |
|
|
|
|
Таблица 1.1 |
|
Рекомендуемые нормы точности базовых поверхностей заготовок зубчатых колес |
|||||
Н а р у ж н ы й д и ам етр |
Ш и р и н а зу бч ато го |
Д о п у с к балопого |
П огреш н ость |
Н сп с р п с н л и к у л я р - |
|
и о сть б азового |
|||||
<|юрмм б азоного |
|||||
заго то п к и, м м |
псица, .мм |
о тв ер сти я, м км |
то р ц а к базо во м у |
||
о тиерстия, м км |
|||||
|
|
|
отверсти ю , м км |
||
|
|
|
|
||
До 25 |
До 25 |
8-15 |
5-8 |
8-13 |
|
Со. 25 до 100 |
4 |
13-25 |
5-13 |
10-20 |
|
« 100 « 200 |
4 |
20-30 |
5-15 |
15-30 |
|
4 200 « 300 |
4 |
25-38 |
5-18 |
25-50 |
|
|
Таблица 1.2
Соотношение точности базирования и допускаемого радиального биения для цилшщричсских зубчатых колес
С теп ен ь ки не м а ти ч еско й
то ч н о сти но Г О С Т 1 6 4 3 -8 1
Д о п у с к па ради альн ое б и ен и е |
|
|
зу бч ато го ценна, м км , п ри д е |
Р е к о |
|
л и тел ь н о м д иам етре |
||
М одуль, |
|
м ендуе |
мм |
|
м ая по- |
|
|
салка |
Си. 125 |
Си. 4 00 |
|
Д о 125 |
д о 8 00 |
|
до 4 00 |
|
Н аи б о л ьш ее зн а ч е н и е ради альн ого би ен и я, мкм, за с ч ет зазо р о в в систем е п о сад о к о т в е р с т и е - о п р ав к а п ри ди ам етр е п осад очн ого отверстия,
мм
Си |
. 10 |
С о. 18 |
С о. 30 |
С о. 50 |
Св. 80 |
д о |
18 |
до 30 |
д о 50 |
д о 80 |
до 120 |
6 |
1-3,5 |
25 |
36 |
45 |
Н5/Ь5 |
16 |
18 |
22 |
26 |
30 |
|
3,5-6,3 |
28 |
40 |
50 |
|
|
|
|
|
|
|
6,3-10 |
32 |
45 |
56 |
|
|
|
|
|
|
7 |
1-3,5 |
36 |
50 |
63 |
Н6/И5 |
19 |
22 |
27 |
31 |
37 |
|
3,5-6,3 |
40 |
56 |
71 |
|
|
|
|
|
|
|
6,3-10 |
45 |
63 |
80 |
|
|
|
|
|
|
8 |
1-3,5 |
45 |
63 |
80 |
Н7/Ь6 |
29 |
3 4 |
41 |
49 |
57 |
|
3,5-6,3 |
50 |
71 |
90 |
|
|
|
|
|
|
|
6,3-10 |
56 |
80 |
100 |
|
|
|
|
|
|
9 |
1-3,5 |
71 |
80 |
100 |
H 8 / h 6 |
38 |
46 |
55 |
65 |
76 |
|
3,5-6,3 |
80 |
100 |
100 |
|
|
|
|
|
|
|
6,3-10 |
90 |
112 |
125 |
|
|
|
|
|
|
10 |
1-3,5 |
100 |
112 |
125 |
Н9/Н6 |
54 |
65 |
78 |
93 |
109 |
|
3,5-6,3 |
125 |
140 |
140 |
|
|
|
|
|
|
|
6,3-10 |
140 |
160 |
160 |
|
|
|
|
|
|
И |
1-3,5 |
125 |
140 |
160 |
H9/h6 |
60 |
72 |
87 |
103 |
141 |
|
3,5-6,3 |
160 |
180 |
180 |
|
|
|
|
|
|
|
6,3-10 |
180 |
200 |
200 |
|
|
|
|
|
|
30 |
Г л а в а 1 |
Таблица 13
Соотношение точности по торцевому биению базовых поверхностей и допускаемой погрешности направления зубьев для цилиндрических зубчатых колее
Гт= 0,5d/bFP
|
|
Д о п у с к н а погреш н ость |
Д о п у с к ае м о е то р ц ев о е б и ен и е, |
||
С тепень то ч н о |
|
н ап р а вл е н и я зу ба, м км , Fp |
м км , н а 0 1 0 0 м м , F T |
||
сти норм ы к о н |
|
|
|
|
|
так та зу бьсо |
М одуль, мм |
|
Ш и р и н а зу бч ато го п сица, м м |
|
|
п о Г О С Т |
|
|
|
||
|
|
|
|
|
|
1 6 4 3 -8 1 |
|
|
|
Д о 40 |
С о . 4 0 д о 100 |
|
|
Д о 40 |
С о. 40 до 100 |
||
6 |
1-16 |
9 |
12 |
11 |
6 |
7 |
1-25 |
11 |
16 |
14 |
8 |
8 |
1 - 4 0 |
18 |
25 |
22 |
12,5 |
9 |
1-55 |
28 |
4 0 |
35 |
20 |
10 |
1-55 |
4 5 |
63 |
56 |
31,5 |
11 |
1-55 |
71 |
100 |
89 |
50 |
комендуемые посадки цилиндрических зубчатых колес в зависимости от степени кинема тической точности зубчатого венца, в табл. 1.3 — допускаемые значения торцевого биения базовых поверхностей с учетом допускаемой погрешности направления зубьев. Исходя из специфических требований к изготовлению зубчатых колес, в каждом конкретном случае должны быть рассчитаны соотношения соответствующих показателей точности зубчатого венца и базовых поверхностен, определяющих положение заготовки.
1.4.Методы обработки зубьев
Принципиально все виды обработки зубьев основаны на двух методах: копирования и обкатки.
Копирование заключается в том, что каждая впадина зубьев обрабатывается инстру ментом, имеющим профиль впадины (дисковая и пальцевая фреза, шлифовальный круг, протяжка). Во время обработки деталь не вращается, а по окончании она поворачивается на угол, равный 360°/z.
Этот метод имеет ограниченное применение при чистовой обработке зубьев вследст вие низкой производительности и трудности получения точных профилей инструмента. Более широко он применяется при черновой обработке зубчатых колес, а также при ис пользовании таких специальных способов нарезания, как полуобкатпый способ нарезания конических передач с круговыми зубьями, кругодиагональное протягивание цилиндриче ских зубчатых колес.
Обкатка заключается в том, что при зацеплении заготовки и инструмента ему необхо димо придать также дополнительное движение, обеспечивающее процесс резания, а при зацеплении пары сопряженных цилиндрических колес, одно из которых является инстру ментом — долбяком, — возвратно-поступательное.
При зацеплении зубчатого колеса с рейкой, являющейся инструментом, ей также при дается возвратно-поступательное движение резания.
В червячной передаче инструментом является червяк — червячная фреза. В осевом сечении ее зубья образуют рейку, которая при каждом обороте фрезы смещается вдоль ее