
- •ИЗДАНИЕ ВТОРОЕ, ПЕРЕРАБОТАННОЕ И ДОПОЛНЕННОЕ
- •ОСНОВНЫЕ СХЕМЫ ПРОИЗВОДСТВА ГАЗА ДЛЯ СИНТЕЗА АММИАКА
- •ОСНОВЫ ПРОЦЕССОВ ОЧИСТКИ ГАЗОВ
- •Циркуляционные процессы
- •ОЧИСТКА ПРИРОДНОГО ГАЗА ОТ ВЫСШИХ УГЛЕВОДОРОДОВ
- •АБСОРБЦИОННЫЕ МЕТОДЫ ОЧИСТКИ ГАЗОВ ОТ ДВУОКИСИ УГЛЕРОДА И СЕРНИСТЫХ СОЕДИНЕНИЙ
- •Примеры расчета абсорберов МЭА-очистки
- •Катализаторы
- •Кинетика и механизм процесса гидрирования
- •Аппаратурно-технологическое оформление процесса
- •АБСОРБЦИОННЫЕ СПОСОБЫ ОЧИСТКИ ГАЗОВ ОТ СЕРНИСТЫХ СОЕДИНЕНИЙ
- •ОЧИСТКА ГАЗОВ ОТ ОКИСИ УГЛЕРОДА
- •КАТАЛИТИЧЕСКИЕ И АДСОРБЦИОННЫЕ МЕТОДЫ УДАЛЕНИЯ ИЗ СИНТЕЗ-ГАЗА КИСЛОРОДСОДЕРЖАЩИХ СОЕДИНЕНИИ
- •Катализаторы
- •Аппаратурно-технологическое оформление
- •Катализаторы
- •2. ТОНКАЯ ОЧИСТКА ОТ ДВУОКИСИ УГЛЕРОДА МЕТОДОМ АДСОРБЦИИ
- •ОЧИСТКА ГАЗОВ ОТ ОКИСИ АЗОТА И АЦЕТИЛЕНА
- •2. СПОСОБ ОЧИСТКИ ОТ ОКИСИ АЗОТА И АЦЕТИЛЕНА МЕТОДОМ КАТАЛИТИЧЕСКОГО ГИДРИРОВАНИЯ
- •АБСОРБЦИОННЫЕ МЕТОДЫ ОЧИСТКИ ГАЗОВ ОТ АЦЕТИЛЕНА
- •Очистка пирогаза от сажи
КАТАЛИТИЧЕСКИЕ И АДСОРБЦИОННЫЕ МЕТОДЫ УДАЛЕНИЯ ИЗ СИНТЕЗ-ГАЗА КИСЛОРОДСОДЕРЖАЩИХ СОЕДИНЕНИИ
Газ, полученный в результате конверсий углеводородов, содер жит значительные количества окиси и двуокиси углерода (от 10 до 35% и от 15 до 30% соответственно). Окись углерода, как изве стно, является потенциальным источником водорода, в результате ее каталитического взаимодействия с водяным паром образуются водород и двуокись углерода. Этот процесс можно рассматривать как грубую очистку от окиси углерода. Грубую очистку от двуокиси углерода осуществляют описанными выше абсорбционными мето дами. В результате очищенный газ может содержать от 50 см3/м3 до 7000 см3/м3 окислов углерода. Кроме того, в газе обычно при сутствуют незначительные примеси кислорода (до 500 см3/м3).
Присутствие кислородсодержащих веществ в азотоводородной смеси вызывает отравление железного катализатора синтеза ам миака, что резко снижает его производительность. Допустимое их содержание в газе, поступающем на катализатор синтеза аммиака, составляет 20 см3/м3. Причем в последнее время появилась тенден ция к ужесточению этих требований, особенно к содержанию дву окиси углерода. В схемах'синтеза аммиака всегда предусматривают тонкую очистку от кислородсодержащих примесей. Чаще всего это каталитическое гидрирование, возможно также применение адсорб ционных методов.
1. КАТАЛИТИЧЕСКИЕ МЕТОДЫ УДАЛЕНИЯ ОКИСЛОВ УГЛЕРОДА И КИСЛОРОДА
Методы каталитической очистки газа от кислородсодержащих веществ основаны на следующих экзотермических реакциях:
С0 + Н20 = С02+ Н 2 |
(V III,1) |
С0 + 1/202= С02 |
(V III,2) |
С0 + ЗН2= СН4+ Н 20 |
(VIII,3; |
С02 + 4Н2= СН4+ 2Н20 |
(VIII,4) |
0 2+ 1/2Н2 = Н20 |
(VIII,5) |
Образующуюся по реакциям (VIII,1) и (VIII,2) двуокись угле рода удаляют абсорбционным методом. Метан, который получается в результате гидрирования окислов углерода [реакции (VIII,3), (VIII,4)] остается в синтез-газе как балласт, влагу [реакции (VIII,3) —(VIII,5)] удаляют конденсированием. Преимуществом очистки но реакции (VIII,1) является образование водорода. При осущест влении. процессов по реакциям (VIII,3)—(VIII,5), напротив, рас
ходуется водород. |
|
|
|
|
|||
В табл. VIII-1 |
приведены тепловые эффекты, в табл. VIII-2— |
||||||
константы |
равновесия |
описываемых |
реакций |
[1]. |
|
||
Таблица |
VIII-1. |
Тепловой эффект реакций каталитической очистки |
|||||
Температура, К |
(VIII, 1) |
(VIII, 2) |
(VIII, 3) |
(VIII, 4) |
(VIII, 5) |
||
кД ж/моль* |
кДж/моль |
кДж/моль |
кДж/моль |
кДж/моль |
|||
0 |
|
|
40,4 |
279,3 |
192,1 |
151,7 |
239,1 |
298,16 |
|
|
41,2 |
283,2 |
206,3 |
165.1 |
242,0 |
300 |
|
|
41,2 |
283,2 |
206,4 |
165,2 |
242,0 |
400 |
|
|
40,6 |
283,7 |
210,8 |
170,2 |
243,0 |
500 |
|
|
39,9 |
283,9 |
214,7 |
174,8 |
244,0 |
600 |
|
|
38,9 |
283,9 |
218.0 |
179.1 |
244,9 |
700 |
|
|
37,9 |
283,7 |
220,6 |
182,8 |
245,8 |
800 |
|
|
36,8 |
283,5 |
222,8 |
185.9 |
246,6 |
900 |
|
|
35,8 |
283,2 |
224,5 |
188.7 |
247,4 |
1000 |
|
|
34,8 |
283,0 |
225,7 |
190,9 |
248,0 |
*1 Дж = 4,19 кал.
Таблица VIII-2. Константы равновесия реакций каталитической очистки
Темпе |
|
|
|
|
Реакция |
|
|
|
|
ратура, К |
(VIII,1) |
(VIII,2) |
(VIII,3) |
(VIII,4) |
(VIII,5) |
||||
|
|||||||||
300 |
8,975 |
• 10« |
5,492 • 1044 |
4,746 |
• 1024 |
5,288 • 1026 |
6,121 • 1039 |
||
400 |
1,475 |
• 103 |
2,562 |
• 1032 |
4,088 |
• 1016 |
2,760.1012 |
1,737-1026 |
|
500 |
1,260 |
• 102 |
1,013 |
• 1026 |
1,145 |
• 10Ю |
8,688 • 10? |
7,683 |
• 1022 |
600 |
27,08 |
|
1,161 • 1020 |
1,978 |
• 100 |
7,305 • 104 |
4,288 |
• 10Ю |
|
700 |
9.017 |
|
3,453.10Ю |
3.722 |
• 103 |
1,127.102 |
3,830 |
• 1016 |
|
800 |
4,038 |
|
7,848 |
• 1013 |
3.205 |
• 101 |
7,9365 |
1,943 - ЮН |
|
900 |
2,204 |
|
6,930. ЮН |
7,657 |
• 10-1 |
0,3473 |
3,146 |
• 10U |
|
1000 |
1,374 |
|
1,592. ЮЮ |
4,864 |
• 10-2 |
2,7405 - 10"2 |
1,151 |
• ЮЮ |
Из данных, приведенных в таблицах, следует, что все реакции могут* протекать с высокими степенями превращения, однако ско рости их ничтожно малы, поэтому реакции проводят в присутствии катализаторов. Все рассматриваемые процессы сопровождаются вы делением большого количества тепла, что вызывает резкое возраста ние температуры в зоне катализа.
Константа равновесия реакции взаимодействия окиси углерода с водяным паром невелика по сравнению с константами равновесия реакций гидрирования и окисления окиси углерода. Поэтому степень очистки, т. е. остаточное содержание окиси углерода, будет опреде ляться условиями термодинамического равновесия.
Повысить степень конверсии окиси углерода можно путем уве личения содержания в газе водяного пара, в результате промежуточ ного удаления двуокиси углерода или при снижении температуры процесса. Первый способ экономически невыгоден. Процесс конвер сии окиси углерода с промежуточным удалением двуокиси углерода применяют в схемах производства водорода в тех случаях, когда требуется получить водород с минимальным содержанием метана. Температура процесса определяется активностью используемых катализаторов.
До недавнего времени применялись катализаторы, активные при температуре выше 350—400 °С, остаточная концентрация окиси углерода составляла несколько процентов. В последние годы раз работаны низкотемпературные катализаторы, активные при 180— 250 °С. Их использование позволяет получить газ, содержащий менее 0,5% СО.
Катализаторы
Большое распространение в промышленности получили железо хромовые катализаторы [2—8], активные при температуре 350 °С и выше. Эти катализаторы очень близки по составу и содержат 80—90% окиси железа и 7—10% окиси хрома. Поэтому большин ство железохромовых катализаторов, выпускаемых в различных странах, независимо от способа приготовления близки по активности при работе в кинетическом режиме (т. е. на мелком зерне в отсутст вие диффузионного торможения)* Удельная поверхность невосстано вленных катализаторов различна, однако после проведения на них реакции она становится равной 25—30 м2/г, что и обусловливает одинаковую активность катализаторов в кинетической области при их близком химическом составе. Различная активность катали
заторов наблюдается в диффузионной области, при |
испытании их |
в целых зернах (табл. VIII-3). |
|
Промышленные катализаторы должны обладать |
оптимальной |
пористой структурой* обеспечивающей максимальное использование объема зерна при высокой прочности контакта и наименьшей насып ной плотности. Указанные свойства в значительной степени зависят от способа приготовления катализатора и условий проведения от дельных технологических стадий при его производстве [9—12].
В Советском Союзе железохромовый катализатор |
выпускают |
под маркой «482», содержащий 88% Fe (в пересчете на |
Fe20 3) и 7% |
Сг (в пересчете на Сг20 3), примесь сернистых соединений не превы шает 0,4—0,7% (в пересчете на S 0 3). Выпускают катализатор в та-
Таблица VII1-3. Сравнительная характеристика отечественных и зарубежных катализаторов
|
|
|
Размеры |
|
|
Активность (константа |
|||
|
|
|
гранул, мм |
|
|
скорости), см*/(л.с) |
|
||
|
|
|
|
|
|
в кинетическом |
на целом |
||
|
|
|
|
|
|
зерне при |
|||
Тип катализа |
|
|
Насыпная |
|
режиме |
380 °С |
|||
тора, фирма, |
|
|
плотность, |
|
|
|
|
||
страна |
диа |
вы |
кг/ма |
|
|
<0 |
В |
||
|
|
|
метр |
сота |
|
|
|
а |
■» |
|
|
|
|
|
|
о |
и |
в |
О |
|
|
|
|
|
|
о |
|
||
|
|
|
|
|
|
о |
о |
|
|
|
|
|
|
|
|
О |
о |
|
05 |
|
|
|
|
|
|
00 |
1ГЭ |
о |
|
|
|
|
|
|
|
со |
со |
03 |
|
482, формован |
7 - 9 |
5 - 2 0 |
1,15 • 10-8 |
2,2 |
1,0-1,3 |
0,98 |
5,26 |
||
ный, СССР |
|
|
|
|
|
|
|
||
482-М, табле- |
8 - 9 |
8 - 9 |
1.5 • 10-3— |
1,6 |
0,85—1,0 |
0,58 |
3,68 |
||
тированный, |
|
|
1.6 • Ю-з |
|
|
|
|
||
СССР |
|
|
|
|
|
|
|
|
|
Контакт |
1026, |
7 |
7 |
1,40 • Ю-з |
|
|
1,36 |
6,6 |
|
формован |
|
|
|
|
|
|
|
||
ный, ГДР |
6 |
|
|
|
|
|
|
||
Контакт |
1030, |
6 |
1,30 • Ю-з |
|
1,17 |
|
|
||
таблетиро- |
|
|
|
|
|
|
|
||
ванный, ГДР |
10-11 |
|
|
2,2- |
|
|
|
||
7374, |
|
формо |
5 -3 0 |
1,45 • Ю-з |
|
0,66 |
3,41 |
||
ванный, |
|
|
|
|
|
|
|
||
ЧССР |
|
|
|
1,20-Ю -з |
|
|
|
|
|
С-12-1, табло- |
9,3 |
4,8 |
|
1.2 |
0,86 |
|
|||
тированный, |
|
|
|
" |
|
|
|
||
ССЕ, США |
|
|
|
|
|
|
|||
|
|
1,23 • 10-» |
|
|
|
|
|||
15-4, таблети- |
8.8 |
12 |
■ |
0.82 |
|
|
|||
рованный, |
|
|
|
|
|
|
|
||
ICI, Англия |
|
|
1,31 • Ю-з |
|
|
|
|
||
15-5, таблети- |
4 |
4 |
|
1,15 |
|
|
|||
рованный, |
|
|
|
" |
|
|
|
||
ICI, |
Англия |
|
|
|
|
|
|
||
|
|
1,45 • Ю-з |
|
|
|
|
|||
BASF |
табдоти |
5,1 |
5,4 |
1,8 |
|
1,16 |
5,8 |
||
рованный, |
|
|
|
|
|
|
|
||
ФРГ |
|
|
|
|
1,25 • Ю-з |
|
|
1,02 |
5,2 |
G-3A таблети- |
6 |
6 |
|
|
|||||
рованный, |
|
|
|
|
|
|
|
||
Girdler, США |
|
|
|
|
|
|
|
t: и я 4
3 я
в W
о »
я Я
л о п si о а в « 0*0» 5 о
о
л Я
к н о а В „ ^ « н а
о с а
39
22
21
44
блетках и гранулах, причем мелкозернистый формованный катали затор обладает более высокой механической прочностью.
Катализаторы используют в промышленности как при атмосфер ном, так и при повышенном давлении до 29,4*10б Па (30 кгс/см2) в интервале 340—500 °С. Объемная скорость процесса при атмосфер ном давлении составляет 400—1000 ч“х и 2000—3000 ч-1 при повы шенном давлении. Соотношение пар : газ в зависимости от техноло гической схемы изменяется в пределах 0,4—1,0 : 1. При этом дости гается 95—98%-ная степень превращения СО (от степени превра щения в равновесных условиях).
24 Заказ 1460 |
369 |
Перед использованием катализатор восстанавливают. Восста новителями служат водород и окись углерода. Восстановление обычно проводят рабочим газом непосредственно в контактном аппа рате при температуре 350—450 °С. Восстановленный катализатор является пирофорным, поэтому перед выгрузкой его окисляют, так же как и низкотемпературный катализатор. Активной фазой катализатора является закись-окись железа (Fe30 4), образующаяся
впроцессе восстановления. Показано [13], что активность железо хромовых катализаторов связана с образованием твердого раствора Fe30 4—Сг20 3 шпинельного типа (происходит замещение трехва лентных ионов железа в кристаллической решетке Fe30 4 трехва лентными ионами хрома). Избыток окиси хрома, присутствующий
вкатализаторе в виде свободной фазы, снижает активность ката лизатора.
Наиболее распространенными и вредными каталитическими
ядами являются |
сернистые соединения. |
Сероводород реагирует с катализатором по уравнению: |
|
Fe30 4-f3H 2S + H2 |
3F eS + 4 Н 20 + 79,5 к Дж /моль (19 ккал/моль) (VI 11,6) |
Эта реакция обратима и в зависимости от соотношения пар газ и температуры процесса возможно или поглощение серы катализато ром, или выделение ранее поглощенной серы в парогазовую смесь. В равновесных условиях содержание серы не изменяется. Ниже
приведены |
константы |
равновесия |
указанной реакции Кр = |
|||
= [H2S]3 [Н2]/[Н20]4 |
при |
различных |
температурах |
[14]: |
||
°С |
. |
300 |
400 |
500 |
600 |
|
А'р |
2,66.10-12 |
1,78-10-ю 7,94.10-ю |
2,9 • 10-е |
Органические сернистые соединения в присутствии железо хромового катализатора реагируют с водяным паром с образованием сероводорода. Однако сероуглерод, если концентрация его в газе превышает 1%, конвертируется не полностью и необратимо отра вляет катализатор. Сульфид железа, образующийся при взаимодей ствии сероводорода с катализатором, так же как и Fe30 4, ката лизирует реакцию конверсии, но по сравнению с последним значи тельно менее активен.
Выпускают железохромовые катализаторы [3, 4] и кобальтмолибденовые наносные [15], которые могут работать в газах с по вышенным содержанием сернистых соединений.
Помимо сернистых соединений отравляющее действие на железо хромовый катализатор оказывают соединения фосфора, бора, крем ния, хлора [14]. Механические примеси, присутствующие в газе и паре, также снижают активность катализатора, забивая его по верхность, и уменьшают механическую прочность в результате эрозии. Снижение механической прочности происходит и При обра тимом отравлении, и в результате фазовых превращений.
Механические примеси попадают в парогазовую смесь, поступа ющую на железохромовый катализатор, из футеровки аппаратов
и |
из катализаторов, |
применяемых |
на |
предшествующих стадиях, |
а |
также из веществ, |
используемых |
для |
умягчения воды. Очень |
опасна конденсация водяного пара на катализаторе, так как на его поверхности адсорбируются все примеси, содержащиеся в паре; кроме того, происходит разрушение катализатора.
Свежие железохромовые катализаторы обычно содержат неболь шие примеси сульфатов, так как сырьем для производства катализа торов служит сульфат железа. При восстановлении катализатора происходит превращение сульфата в сероводород, который отра вляет низкотемпературный катализатор второй ступени конверсии. Сейчас разрабатывают катализаторы с небольшим содержанием серы [16] (менее 0,1%) или негенерирующие сернистые соединения при восстановлении и эксплуатации [3, 16].
Всхемах производства аммиака, в которых используют низко температурный катализатор, обязательно проводят обессеривание железохромового катализатора. Катализатор обрабатывают паро газовой смесью с повышенным содержанием пара (пар : газ при 440—450 °С. Обессеривание считается законченным, если газ
после железохромового катализатора содержит не более 0,5 мг/м3 сероводорода.
Впоследние годы довольно широко проводят исследования, направленные на повышение активности железохромовых катализа торов введением в них добавок, на создание катализаторов на основе других компонентов, а также на разработку бессернистых катали заторов.
Внастоящее время в промышленности широко применяют низко температурные катализаторы, позволяющие проводить процесс при температуре 180—250 °С [17—23].
Низкотемпературные катализаторы содержат соединения меди,
цинка, алюминия, иногда хрома. Известны двух-, трех-, четырех- и многокомпонентные катализаторы. В качестве добавок к указан ным выше компонентам используют соединения магния, титана, палладия, марганца, кальция, кобальта и др. В зависимости от способа приготовления в свежих катализаторах содержатся обычно окислы металлов либо шпинели, либо их смеси.
Содержание меди в |
катализаторах колеблется от 20 до 50% |
(в пересчете на окись). |
Наличие в низкотемпературных катализато |
рах соединений алюминия, марганца и магния сильно повышает их стабильность, делает более устойчивыми к повышенной темпе ратуре.
Отечественный низкотемпературный катализатор марки НТК-4 выпускают в виде таблеток 5 x 5 или 6 x 4 мм. Насыпная плот ность катализатора колеблется от 1,5• 10“ 3 до 1,8«10” 3 кг/м3. Меха ническая прочность катализатора, определяемая как усилие на раз давливание по торцу таблетки, составляет 250—400 кгс/см2 (но не меньше 170 кгс/см2).
По своей каталитической активности большинство известных катализаторов, в том числе и отечественный, не отличаются друг
от друга. Об этом свидетельствуют полученные в лабораторных условиях результаты (сравнение каталитической активности ряда образцов приведено в табл. VII1-4).
Таблица V II 1-4. |
Активность различных |
низкотемпературных |
катализаторов |
||||
|
|
|
(в ч-1) |
|
|
|
|
|
|
Размер |
Константа скорости при температурах (°С) *: |
||||
|
Катализатор |
|
|
|
|
|
|
|
таблетки, |
|
|
|
|
|
|
|
|
мм |
225 |
250 |
225^ |
175 |
225 |
НТК-4 (СССР) |
5X5 |
3,65 |
4,10 |
3,65 |
1.75 |
3,73 |
|
С-18-1 (США) |
3X6 |
3,80 |
3,65 |
3,11 |
1.79 |
3,11 |
|
52-1 |
(Англия) |
3,7 X 5,5 |
3,55 |
3,42 |
- 3,00 |
2.08 |
2,61 |
1960 |
(ГДР) |
4,4X5 |
3,63 |
4,08 |
3,14 |
— |
2.83 |
* Запись соответствует лорядк у изменения температуры во время опыта.
Об идентичности свойств различных катализаторов свидетельст вуют также условия их промышленной эксплуатации: температура
200—250 °С, объемная скорость 2000—3000 |
ч"1, соотношение |
пар: газ 0,4—0,7, давление 19,6 - 10б—29,4 • 10б |
Па (20—30 кгс/см2). |
При этом обеспечивается 90—95%-ная степень превращения окиси углерода (от степени превращения в равновесных условиях). "
Перед использованием низкотемпературный катализатор вос станавливают. Восстановителями служат окись углерода и водород. Восстановление окисью углерода протекает при более низкой темпе ратуре, однако в этом случае на восстановленном катализаторе начи нается реакция конверсии окиси углерода, а это вызывает последу ющее увеличение температуры.
Реакция постановления катализатора протекает с большим выделением тепла. Тепловой эффект восстановления катализатора в несколько раз больше теплового эффекта реакции конверсии. Поэтому при восстановлении, происходит увеличение температуры в слое катализатора. Многочисленными исследованиями, подтвер жденными на практике, показано, что при восстановлении низко температурных катализаторов температура не должна превышать 230—250 °С [3, 20]. Увеличение температуры в процессе восстано вления приводит к снижению активности и срока службы катализа тора. Чтобы предотвратить это, при восстановлении газ-восстанови тель разбавляют азотом, углекислым газом, природным газом, водя ным паром [3,24—26].
В качестве восстановителя чаще используют водород, что свя зано с наличием на большинстве заводов чистой азотоводород ной смеси. Процесс восстановления не рекомендуется проводить слишком быстро, так как в этом случае также возможна рекристалли зация активной поверхности, наиболее целесообразно проводить
восстановление при давлении, близком к атмосферному [27]. На восстановление 1 т катализатора НТК-4 расходуется около 130 м8 водорода. Если восстановление проводить с объемной скоростью газа около 200—300 ч"1 (как это часто бывает в производственных условиях), то первоначальное содержание водорода в газе должно составлять около 0,3—0,5%. Содержание восстановителя в газе по мере восстановления катализатора постепенно увеличивается до 1—1,2%, а в конце процесса до 5—10%.
В качестве газа-разбавителя при восстановлении чаще всего при меняют азот. Водяной пар, как разбавитель, в процессе восстано вления оказывает влияние на структуру катализатора и вызывает снижение его прочности [3, 28]. В работе [6] объясняют отрицатель ное действие пара присутствием в нем большого числа примесей. Двуокись углерода при определенных условиях (температура ниже 160 °С и парциальное давление 2,94• 105 Па, 3 кгс/см2) может реа гировать с окисью цинка, содержащейся в катализаторе, что при водит к снижению механической прочности. При действии Н 20 и СО2 на окиси цинка протекает процесс, аналогичный спеканию, только при более низких температурах [3].
Применять природный газ для разбавления водорода нежела тельно, так как в нем присутствуют примеси сернистых соединений, отравляющие катализатор. Влияние других содержащихся в природ ном газе примесей (тяжелые углеводороды) еще недостаточно изу чено, однако есть предположения о их вредном воздействии на ката лизатор.
Восстановленный катализатор пирофорен, поэтому перед вы грузкой из контактных аппаратов его необходимо окислять. Про цесс окисления сопровождается большим тепловым эффектом и осуще ствляют его, во избежание резкого подъема температуры, с соответ ствующими предосторожностями (постепенная дозировка окисли теля, сильное разбавление инертным газом и т. д.).
При восстановлении катализатора происходит формирование его активной поверхности. Окись меди и соединения меди, содержа щиеся в катализаторе, восстанавливаются с образованием мелкодис персной металлической меди. Многие исследователи считают, что с присутствием меди связана каталитическая активность катали затора [3, 5, 28—31]. Получены данные о прямой зависимости ката литической активности низкотемпературных катализаторов от удель ной поверхности меди [28, 32] (рис. VIII-1, VIII-2). Есть предполо жения, что роль основного активного компонента в низкотемпера турных катализаторах выполняет не 0-валентная медь [33—35].
В устойчивых и активных катализаторах дисперсность фазы
меди, по |
данным различных авторов, колеблется от 1*10“8 до |
4-10” 8 м |
[27, 30, 37]. Для катализатора НТК-4 эта величина соста |
вляет около 1,5 *10” 8 м.
Для целого ряда промышленных, опытных и лабораторных образцов катализаторов была определена зависимость каталитиче ской активности от величины поверхности меди по специально
разработанной методике [36]. Полученные данные приведены на рис. VIII-3, из которых видно, что активность медьсодержащих катализаторов повышается при увеличении медной поверхности.
I*
<!§■
1*8 |
|
|
|
|
|
|
|
|
сэ |
а, |
|
|
|
|
|
|
|
ся |
$ |
|
|
|
|
|
|
|
I I |
|
|
|
|
|
|
|
|
£ 441 |
|
|
|
|
|
|
|
|
|
О |
Ю 20 |
30 |
40 |
50 |
ПоОерхностьСи,м% катализатора |
||
|
ПодерхностьСи\м2/г катализатора |
|
|
|
||||
Рис. VIII-1. |
Зависимость |
между |
каталитической |
активностью |
катализатора |
|||
|
|
и поверхностью меди |
(по данным J. S. Campbell [3]). |
|||||
Рис. VIII-2. Зависимость между |
каталитической |
активностью |
катализатора |
|||||
и поверхностью меди |
(по данным |
N. Ray, |
S. К. Nath, A. Sarkar |
и др. [32]). |
Кроме металлической меди восстановленные катализаторы содер жат окислы и шпинели цинка, алюминия, хрома. В их состав входят
также и комплексные шпинели, |
содержащие медь, которые восста |
||||||||||||||
|
|
|
|
|
|
навливаются |
с выделением |
ме |
|||||||
|
|
|
|
|
|
таллической |
|
меди |
|
при |
более |
||||
|ц |
|
|
|
|
|
высокой |
температуре |
(400— |
|||||||
|
|
о |
|
|
600 °С). Эти |
|
соединения выпол |
||||||||
53^ |
|
|
X |
|
X |
няют |
у роль |
|
стабилизаторов. |
||||||
^ У |
|
X |
|
к |
|
КГним относятся |
ZnO, |
Сг20 3, |
|||||||
t i |
|
|
|
|
0-А12Оз, |
ZnGr20 4, |
Cu2Cr20 4, |
||||||||
|
□ |
|
|
|
|||||||||||
g а |
О |
|
|
|
|
Cu(Cr, |
А1)20 4, |
(Zn, |
Cu)Cr20 4. |
||||||
0 X |
|
|
|
Стабилизаторы |
препятствуют |
||||||||||
|
|
|
|
|
|||||||||||
Г |
|
|
|
|
|
р е к р и ст а л л и за ц и и |
м еди . |
||||||||
|
|
|
|
|
В табл. VIII-5 приведены данные |
||||||||||
|
10 |
20 |
30 |
40 |
50 |
по дисперсности |
стабилизиру |
||||||||
|
ющей фазы |
|
и меди, |
образовав |
|||||||||||
|
Меднаяпо6ерхность,м2/г |
|
шейся |
в ее |
присутствии. В от |
||||||||||
Рис. VIII-3. Изменение каталитической |
сутствие |
стабилизаторов |
медь |
||||||||||||
активности |
в |
зависимости от |
поверх |
очень |
быстро спекается и прак |
||||||||||
|
|
ности |
меди: |
|
|
тически катализатор полностью |
|||||||||
Л — НТК-1; |
|
X — Си—Mg; О — НТК-4; |
теряет |
активность. |
|
|
|
|
|||||||
|
|
□ — НТК-8 |
|
|
Для |
ряда |
промышленных |
||||||||
|
|
|
|
|
|
||||||||||
|
|
|
|
|
|
катализаторов и опытных образ |
|||||||||
цов при близких значениях медной |
поверхности наблюдается суще |
||||||||||||||
ственное различие в активности |
(табл. VIII-6). |
Это относится к ка |
тализаторам, содержащим различные немедные компоненты, а такж е приготовленным разными методами.
Таблица V III-5 . Данные по дисперсности отдельных компонентов низкотемпературных катализаторов, образующихся при их восстановлении
|
|
Температура, |
|
Размер) частиц |
|
|
|
нагревание до |
|
|
|
|
|
которой в восста |
|
|
металлической |
Стабилизирующая фаза |
новительной среде |
стабилизирующей |
|||
не меняет кри |
меди, образовав |
||||
|
|
сталличности |
фазы до указанной |
шейся в присут |
|
|
|
стабилизирующей |
температуры, м |
ствии стабилизи |
|
|
|
фазы, °С |
|
|
рующей фазы, м |
ZnO |
|
600 |
5 . 1 0 "» |
2 . 1 0 -е |
|
СГ2О3 |
|
550 |
Рентгеноаморфна |
1,9 • 10-е |
|
0 -AI2O3 |
|
^ 6 0 0 |
5 • 1 0 -е |
1,6 • 1 0 -8 |
|
ZnCr20 4 |
|
^ 6 0 0 |
1 |
• 1 0 -8 |
0,7 • 10-8 |
С112СГ2 О4-1-СГ2О3 |
400 |
1 |
• 1 0 -8 |
1,9-10-8 |
|
(Zn, Си) |
Сг20 4 |
500 |
1 |
. 1 0 -8 |
1 , 1 - 1 0 -8 |
Си (Сг, |
А1)20 4 |
400* |
1 |
. 1 0 -8 |
1,4 - 1 0 -8 |
* При данной температуре происходит восстановление с образованием Си0.
Таблица V IJI-6 . Активность различных медьсодержащих катализаторов
Тип ката |
Способ |
Основной состав катализа |
лизатора |
приготовления |
торов, моль |
НТК-1 |
Мокрым сме |
СиО • Сг20 3 • 4ZnO |
|
шением |
|
НТК-4 |
Мокрым сме |
СиО • 0,1Сг2О3 . 0,ЗА12О3 . |
|
шением |
• 0,2 ZnO |
НТК-8 |
Осаждением |
СиО • 0,7ZnO • 0,7А12О3 |
НТК-1М* |
Смешением |
СиО • 0,9ZnO • 0,7А12Оз |
С-18-1 |
Осаждением |
СиО • l,8ZnO • 0,9А12Оз |
(фирма ССЕ) |
Смешением |
СиО • 9MgO |
Си — Mg* |
Содержание меди % (масс.) в пере счете на СиО |
Поверхность меди, м*/г |
1Константа скоро сти в кин. обл. при 225 °С, см* •(г •с) |
12 |
14,1 |
3,8 |
54 |
13,1 |
5,5 |
35 |
12,7 |
9,0 |
35 |
11,7 |
12,0 |
25 |
13,0 |
6,0 |
18 |
14,9 |
2,9 |
* Опытные образцы.
Полученные данные указывают на различные каталитическиесвойства медной поверхности, что, видимо, обусловлено природой немедных компонентов и характером их взаимодействия с медью.
Измерения, выполненные в высокотемпературной рентгеновской камере на катализаторе НТК-4, показали, что при его восстановле нии происходит образование металлической меди. При подаче реак ционной смеси на восстановленный катализатор количество метал лической меди уменьшается примерно в два раза, но образование новой фазы не обнаруживается. На основании этих данных можно
предположить, что в реакционной среде часть металлической меди окисляется и образовавшаяся рентгеноаморфная фаза окисной меди является каталитически активной. Для объяснения данного явления можно представить также, что реакция протекает по окислительно восстановительному механизму, предложенному М. И. Темкиным; работающая часть поверхности непрерывно окисляется и восстанав ливается и не выявляется на рентгенограммах. Можно также предположить, что при протекании реакции конверсии происхо дит образование других соединений, например гидратного типа.
В процессе работы каталитическая активность низкотемператур ных катализаторов постепенно понижается. Обычно в промышлен ных условиях срок их службы не превышает 1,5—2 лет. Чтобы обес печить использование катализатора в течение такого времени, его загружают обычно в избытке (в 2—3 раза больше) по сравнению с количеством, соответствующим первоначальной каталитической активности. В промышленных конверторах зона реакции постепенно перемещается в направлении движения газового потока.
Свежевосстановленный или проработавший незначительное время катализатор имеет более высокую дисперсность и поверхность по сравнению с отработанным. Одной из причин дезактивации катали затора является его рекристаллизация под действием температуры и реакционной среды. Процесс рекристаллизации ускоряется при повышении температуры. Нагревание катализатора выше 500 °С в восстановительной среде приводит к быстрой и почти полной его дезактивации. Если отработанный катализатор окислить при 200— 250 °С, а затем снова восстановить, то его активность в значительной степени восстанавливается.
Ядами для низкотемпературных катализаторов конверсии окиси углерода являются соединения серы и хлора. Показано, что соединения кремния, фосфора, мышьяка, ненасыщенные угле водороды, аммиак и др. понижают каталитическую активность катализатора.
Вгазе, поступающем на катализатор, сера обычно присутствует
ввиде сероводорода, который послойно связывается катализатором. Содержащаяся в катализаторе окись цинка поглощает сероводород
собразованием сульфида цинка. Происходит также хемосорбция сероводорода медью (для образования сульфида меди необходимо, чтобы в газе при температуре 220 °С присутствовало около 3 см3/м3 сероводорода [27], что значительно превышает содержание серо водорода в промышленном газе). Рей и др. [37] наблюдали значи тельное уменьшение медной поверхности катализатора при содер жании в газе 6 см3/м3 сероводорода. Отравление катализатора серо водородом при небольшом его содержании (0,1—1 см3/м3 газа) — обратимый процесс.
Изучалось отравляющее действие на низкотемпературный ката лизатор других сернистых соединений [38]. По своему дезактивируй ющему действию их располагают в такой последовательности:
H 2S, S 0 2, CS2, C2H5SH, C4H4S.
Активность катализатора понижается, если содержание серы в нем превышает 0,1%. В разных по ходу газа слоях отработанного катализатора содержание серы различно; около 80% всей серы задер живается лобовым слоем (до 3% серы). Среднее содержание серы в от работанном катализаторе составляет около 1%. Чтобы обеспечить двухгодичный срок службы катализатора (при объемной скорости 3000 ч"1), концентрация сероводорода в газе, поступающего на ката лизатор, не должна превышать 0,2 мг/м3 [39].
В настоящее время установлено, что более сильнодействующим ядом, чем сероводород, для низкотемпературных катализаторов являются хлориды [3, 27, 28, 40]. Если в катализаторе содержится 0,02% хлора, его активность понижается на 30—50%. В отличие от сероводорода, который практически полностью связывается ката лизатором, хлор соединяется с катализатором частично. Катализа тор задерживает от 40 до 70% хлора, содержащегося в газе. Меха низм отравления катализатора хлором Кемпбел [3, 28] представляет как образование малоустойчивого хлорида меди, при разложении которого образуется медь с мепыпей дисперсностью, чем в свежем катализаторе. Юнг и Кларк [27] считают, что хлор реагирует о окисью цинка, образуя неустойчивый хлорид цинка. Разложение хлорида цинка сопровождается рекристаллизацией цинка, а это, в свою очередь, приводит к рекристаллизации меди.
Авторами установлено, что в газе недопустимо содержание хлора более 0,01 мг/м3. В работах [35, 40] показано, что катализатор, содержащий А120 3, более устойчив к хлору, чем содержащий только ZnO. Это связано с тем, что в первом случае дисперсность меди в ка тализаторе выше, чем во втором, и А120 3 в значительной степени препятствует рекристаллизации меди. Источниками хлора, попада ющего в газ, могут служить пар, конденсат, некоторые виды угле водородного сырья, воздух, другие катализаторы и футеровочные материалы, расположенные до низкотемпературного катализатора.
Каталитическая активность низкотемпературного катализатора понижается и цри попадании на него влаги. Это происходит в тех случаях, когда температура в слое катализатора ниже температуры точки росы. При конденсации влаги на катализаторе уменьшается и его механическая прочность. Понижение активности катализатора связано с тем, что все примеси, содержащиеся в парогазовой смеси, адсорбируются катализатором и уменьшают активную поверхность. Потеря механической прочности сопровождается разрушением ката лизатора и ростом гидравлического сопротивления конвертора. Поэтому к конденсату и пару, которые используются в процессе низкотемпературной конверсии окиси углерода, предъявляют жест кие требования по содержанию примесей. Газовый конденсат не должен содержать более 2 • 10” 3 мг/м3 солей, соединения хлора, серы, а также масло должны отсутствовать.
Для увеличения срока службы катализатора работу с ним целе сообразно начинать при возможно более низкой температуре. По мере снижения каталитической активности катализатора температуру
обычно увеличивают до 250—260 °С. Низкотемпературный ката лизатор конверсии СО можно регенерировать окислением его воздухом или паром при температуре 200—250 °С [30, 41, 42]. Раз работан также способ химической регенерации низкотемпературного катализатора конверсии СО [43].
Кинетика и механизм процесса
Изучению кинетики реакции конверсии окиси углерода на раз личных катализаторах посвящено большое число работ. Подробное обобщение кинетических данных приведено в работах [3, 23, 44]. Показано, что для большинства промышленных катализаторов в условиях, близких к производственным, протекает реакция пер вого порядка по окиси углерода и нулевого по водяному пару. Для расчета константы скорости при повышенном давлении обычно поль зуются указанной зависимостью.
Последними исследованиями М. И. Темкина с сотр. [45, 46] установлено, что для описания скорости реакции в кинетической области на среднетемпературном и низкотемпературном катализа торах может быть использовано одно уравнение:
к ( р с о р Н ' 0 - к р 1рп , р с о .) |
(V III,7) |
^ н 2о+ ^со, |
|
где Рс 0 , Рьь0, РНг, P QO2~~ паРЦиальные давления компонентов парогазовой |
|
смеси; к — константа скорости; А — постоянная величина, |
характеризуемая |
отношением констант скоростей элементарных реакции окисления поверхности.
За скорость реакции конверсии принимают объем СО (в см3), вступающий в реакцию за 1 с, отнесенный к 1 см3 катализатора.
Тогда к выражается в с"1: |
|
|
для железохромового катализатора в интервале |
температур |
|
400 -500 °С [45] |
|
|
lg к = — 34 000/4,577* +10.2; lg А = — 8800/4,577* + 2,32 |
||
для низкотемпературного катализатора НТК-4 |
в |
интервале |
температур от 200 до 250 °С lg к = —8253/4,57Т + |
4,690; lg А = |
=-4695,5/4,57 Т + 1,935.
Уравнение (VIII,7) переходит в уравнение первого порядка по
окиси углерода, если Р н2о -Рсо2> как это обычно бывает при проведении процесса в промышленности, при условии, что обратной реакцией можно пренебречь.
Относительно механизма реакции есть несколько точек зрения. М. И. Темкин при выводе кинетического уравнения исходил из представления об окислительно-восстановительном механизме про цесса:
Н2 О -f- □ = Н2 “Ь [О] СО -f-[О] = СО2 -f- □
С0 + Н20 = С 02+Г12
где [О] — атом кислорода на поверхности катализатора; □ — вакантное место, возникающее на поверхности катализатора при удалении атома кисло рода.
Согласно этой схеме, реакция протекает при попеременном окис лении и восстановлении поверхности катализатора (без возникнове ния новой фазы).
Прямыми экспериментальными измерениями указанный механизм подтвержден для железохромового катализатора [47]. Представле ния об окислительно-восстановительном механизме реакции при держиваются многие исследователи.
Для низкотемпературных катализаторов помимо окислительно восстановительного механизма многие авторы предлагают адсорб ционный механизм реакции [48, 49].
При проведении процесса конверсии окиси углерода в промышлен ных условиях большое влияние оказывает диффузионное торможе ние, характер которого изменяется в зависимости от пористой струк туры, размера, формы гранулы катализатора, а также от условий проведения реакции. В промышленных условиях процесс конверсии проходит во внутридиффузионной области. Влияние диффузионного
торможения возрастает при |
увеличении поверхности контакта [10, |
||||||||
50], а |
также давления процесса. |
|
|
|
|
||||
В табл. VIII-7 приведены значения относительной активности |
|||||||||
единицы |
объема |
|
формованного и |
таблетированного |
катализатора |
||||
№ 482 |
и таблетированного |
катализатора |
НТК-4 |
в |
зависимости |
||||
от размера гранулы и давления процесса. |
|
|
|
||||||
Таблица |
VIII-7. Относительная активность катализаторов № 482 и НТК-4 |
||||||||
|
|
|
|
|
|
Давление |
|
|
|
Размер гранулы |
0,9810е Па |
(1 кгс/см2) |
29,4*106 Па (30 кгс-см2) |
||||||
|
|
|
|
|
|
||||
катализатора, |
мм |
|
таблетнро- |
формован |
таблетиро- |
||||
|
|
|
|
формован |
|||||
|
|
|
|
|
ный |
ванный |
ный |
|
ванный |
|
|
|
|
|
№ 482 |
|
|
|
|
1 - 2 |
|
|
|
|
1 |
1 |
5 |
|
5 |
5 |
|
|
|
|
0,43 |
0,29 |
2,2 |
|
1,7 |
9 |
|
|
|
|
0,27 |
0,17 |
1,6 |
|
1,2 |
|
|
|
|
|
НТК-4 |
|
|
|
|
1,5X1,5 |
|
|
|
|
_ |
1 |
_ |
|
1,5 |
5X5 |
|
|
|
|
— |
0,4 |
— |
|
1,15 |
8X 8 |
|
|
|
|
— |
0,17 |
— |
|
0,78 |
Формованный катализатор отличается от таблетированного пори* стой структурой, а следовательно, кажущейся плотностью. Объем ная активность катализатора во внутридиффузионной области,
т. е. в промышленных условиях ведения процесса, пропорциональна
1/е(1—е) (где е — пористость).
Установлено, что значительное увеличение скорости реакции, как на железохромовом, так и на низкотемпературном катализато рах, наблюдается при увеличении давления до 9,8 • 10б—14,7• 10БПа {10—15 кгс/см2). Дальнейшее повышение давления практически не влияет на скорость процесса. Аналогичные зависимости получены и другими авторами.
Моделирование процесса конверсии окиси углерода
Чтобы выбрать оптимальные условия процесса (объемную ско рость и др. параметры), проводят расчет реактора конверсии окиси углерода с помощью математической модели.
Математическую модель строят, применяя иерархический прин цип [51] последовательного рассмотрения приведенных ниже стадий.
1. Элементарный акт химической реакции, суммарно выражае мой уравнением (VIII,1). Химическая реакция протекает на актив ном участке поверхности катализатора, имеющем размеры порядка диаметров молекул.
2.Процесс на одном зерне катализатора как совокупность элементарных актов с учетом подвода реагентов к активным участ кам и отвода продуктов реакции. Зерно катализатора предста вляет собой пористое образование с развитой внутренней поверх ностью.
3.Процесс в малом объеме слоя катализатора, который необхо
димо рассматривать как совокупность достаточного числа отдель ных зерен, что позволяет допускать квазигомогенную структуру.
4. Конверсия по всей длине слоя катализатора малой толщины как совокупности малых объемов с изменяющейся температурой
иконцентрацией.
5.Конверсия во всем объеме реактора как совокупности слоев малой толщины с изменяющейся температурой и изменяющимися объемами подводимой реакционной смеси. В этой стадии учитывают макрогидродинамические условия в аппарате и распределение потока сырья по слою катализатора.
Врезультате-определяют необходимый объем катализатора при заданных технологических параметрах входа и выхода, принципи альную конструкцию аппарата. Подобные модели можно использо вать для оптимизации и управления данной стадии, а также как блок при построении моделей целых схем.
Дальнейшими расчетами определяют гидравлическое сопроти вление аппарата, габариты, массу и некоторые конструктивные осо бенности реактора. Совокупность расчетов позволяет оценить тех ническую и экономическую эффективность аппарата.
Химическая реакция. Рассматривается кинетйка и равновесие
реакции (УШ,1) на среднетемпературном или низкотемпературном
катализаторе. В кинетическом уравнении (VIII,7) |
константы fc, К |
||
и А — функции температуры, выражаемые формулами |
|||
к = А;0’ехр](—E /R T ) |
(VIII,8) |
||
К = |
iiTo’exp’(— AH/RT) |
(VI11,9) |
|
А = |
Л0*ехр^( —a/RT) |
(VIII,10) |
|
где Е — энергия активации, |
кДж/моль; АН — тепловой |
эффект реакции, |
|
кДж/моль; а — температурный |
коэффициент, кДж/моль. |
|
Численные значения этих величин приведены в Справочнике [2]. Как уже отмечалось, уравнение (VIII,7) для большинства практи чески важных случаев можно аппроксимировать линейной зависи мостью вида
w = kpc0 ИЛИ w = k ( p c 0 - p c 0 ) |
(VI 11,11) |
(где рсо — равновесное парциальное давление) с погрешностью около 10%, что соответствует точности кинетических измерений.
Процесс на зерне катализатора. Для конверсии окиси углерода характерно, что диффузия компонентов к поверхности зерна из потока происходит значительно быстрее, чем реакция внутри зерна.- Поэтому процесс на зерне катализатора описывается уравнением внутренней диффузии с химической реакцией, которое для цилин дрической таблетки имеет вид
(дс . 1 дс , д*с\
(VIIТ, 12)
■ ° Ы + Т а 7 + агО+и,(с)=0
где DI— эффективный коэффициент диффузии, м2/с.
Необходимо отметить, что уравнение (VIII,12) следует рассматри вать вместе с уравнением теплопроводности, так как зерно катали затора в процессе реакции разогревается. Однако экспериментами и расчетами установлено, что эффективная теплопроводность табле ток промышленных катализаторов достаточно высока и ее разогрев можно не учитывать, полагая, что температура внутри зерна почти такая же, как и в потоке парогазовой смеси.
Часто для инженерных расчетов цилиндрическую таблетку заме няют эквивалентной сферой с равным отношением поверхности к объему. Тогда вместо уравнения (VIII,12) можно пользоваться более простым одномерным уравнением в сферических координатах
[(т)(I)+Ю]+ш(е)=0 |
(VIIIil3) |
||
с граничными условиями |
|
|
|
r = R |
с = сп |
(V 111,14) |
|
г = О |
д с /д г= о |
||
|
где R — наружный радиус зерна, м; сп — концентрация окиси углерода на поверхности зерна.
При решении уравнений (VIII,12) или (VIIIДЗ) можно опреде лить степень использования объема зерна катализатора, которая является мерой внутридиффузионного торможения реакции. Для шарового зерна и при реакции первого порядка эта величина равна
Гcth qR |
1 |
(V III,15) |
Л = з L l R ~ ~ |
(7 Л)2' ] |
|
где q = VkJD. |
|
|
Степень использования объема зерна возрастает, если уменьшать радиус зерна при прочих равных условиях, и максимально дости гает значения единицы (кинетическая область). Для создания эффек тивных реакторов конверсии окиси углерода необходимо применять мелкозернистые катализаторы.
Для расчетов необходимо знать коэффициенты внутренней диф фузии D. Перенос компонентов реакции внутрь зерна осуществляется посредством молекулярной и кнудсеновской диффузии, это описы вается уравнением
D = 6 |
-Р м -Р к н |
(V III,16) |
DM~\-^ к н |
где D Ml D K — коэффициенты молекулярной и кнудсеновской диффузии соот ветственно, м2/с; б — коэффициент, полученный по экспериментальным данным, б = о,1 -0 ,3 .
Значение б можно также оценить по формуле [52]
. |
N яЛ2 |
(V III,17) |
|
6 = |
~ ~ |
||
|
где h — средний диаметр пор, м; N — число пор на единицу поверхности, 1/м2; х — коэффициент извилистости.
Если процесс проводят под давлением 1,9•10е—2,9*10® Па (20—
30 кгс/см2), то DM<С В™ и
D ^ 6 D M (V III,18)
Коэффициент молекулярной диффузии рассчитывают по известным формулам, например Отмера и Чена для двойной смеси и Уилка для многокомпонентной смеси [53].
Процесс в малом объеме слоя. Рассматривая геометрические характеристики слоя катализатора, находят количество вещества, в кмоль/(м3-с), реагирующее в единице объема слоя за единицу времени
(1 —е) тр (с) |
(VIII,19) |
где е — пористость слоя, определяемая экспериментально. |
|
Конверсия в слое малой толщины. Здесь необходимо учитывать перенос вещества в свободном объеме слоя катализатора конвекцией и диффузией. Для радиального реактора, например, можно записать следующее уравнение переноса
д |
(VI П.20) |
* 3 7 r(vc + j) + gr = 0 |
где г — радиус слоя, м; v — скорость потока, кмоль/(с-м2); / — диффузионный поток (перемешивание), кмоль/(с*м2).
Экспериментально и расчетами показано [54], что перемешивание играет несущественную роль и им можно пренебречь. Уравнение (VIII,20) решают, полагая, что концентрации окиси углерода на входе и выходе из слоя катализатора заданы.
Конверсия во всем объеме реактора. Если поток сырья неравно мерно распределяется по слою катализатора (например, изменяется по высоте реактора z), то величины и, с, /, g — функции продольной координаты z. В этом случае, даже не учитывая явлений продоль ного переноса в слое катализатора, придется провести интегриро вание по координате z. Однако на практике конструктивными прие мами добиваются равномерного распределения потоков, что всегда принимают при построении математических моделей.
Тепловые явления. В приведенные выше уравнения входят вели чины, зависящие от температуры, которая меняется по длине или радиусу слоя катализатора вследствие выделения тепла реакции.
Рассмотрим тепловые явления, чтобы определить взаимосвязь
между |
температурой и концентрацией. |
|
|
|||
Уравнение теплопереноса имеет вид |
|
|
||||
|
|
|
- ^ r ( v H CM+ I ) - g r A H = 0 |
|
(VIII,21) |
|
где # См — энтальпия |
смеси, Дж/моль; |
/ — тепловой |
поток, обусловленный |
|||
эффективной теплопроводностью, Вт/(м2-с). |
|
|
||||
Не |
учитывая |
незначительную |
эффективную |
теплопроводность |
||
и диффузию |
в слое зерен и совместно решая |
уравнения (VIII,20) |
||||
и (VIII,21), |
получим: |
|
|
|
||
|
|
|
с0- с = ^ ( Т - Т 0) |
|
(V III,22) |
|
где со, |
То — соответственно концентрация окиси углерода и температура смеси |
|||||
на входе в слой катализатора; Ср — теплоемкость смеси, |
Дж/(моль • °С). |
В более точных математических моделях дополнительно учиты вают зависимость физико-химических и феноменологических кон
стант (например, |
АЯ , D и др.) от температуры и концентрации. |
|
Достаточно |
точная |
и подробная математическая модель изложена |
в работе |
[55]. |
|
Таким образом, при расчете реактора по математическим моделям задача сводится к нахождению надежных кинетических и фено менологических констант. Используя математическую модель, их можно определить из опыта работы промышленных реакторов, что
повышает надежность расчетов и устраняет |
ошибки, связанные |
с неучтенными действующими факторами. |
|
. Аппаратурно-технологическое |
оформление |
В схемах производства аммиака на основе парокислородной конверсии углеводородов при атмосферном и повышенном давлениях процесс конверсии окиси углерода проводят на железохромовом
катализаторе. В этом случае работают так называемые совмещенные агрегаты конверсии метана и СО, которые подробно описаны в лите ратуре [56—58],
В новых энерготехнологических схемах производства аммиака процесс конверсии окиси углерода протекает в две ступени на средне- и низкотемпературном катализаторах. Схема конверсии приведена
на рис. VIII-4. Процесс проводят под давлением |
19,6-10б—29,4 X |
X 105 Па (20—30 кгс/см2). Поступающий на конверсию газ содержит |
|
57% Н 2, 22-23% N „ 12,0-12,5% СО, 7,5-8,0% |
С 02, 0,25% Аг |
и 0,35% СН4, 0,55—0,75 объема водяных паров |
на 1 объем газа. |
Рис. VIII-4. Схема двухступенчатого процесса конверсии окиси углерода:
1 — увлажнитель; 2 — конвертор |
I ступени; 3 — котел-утилизатор; 4 — подогреватель |
газа; |
5 — конвертор II ступени. |
Донасыщение газа влагой происходит в увлажнителе 7, при впрыскивании в газ конденсата. Изменяя подачу конденсата, можно регулировать температуру на входе в конвертор.
В конверторе первой ступени процесс проводят на железохро мовом катализаторе при объемной скорости 2000—3000 ч-1 и тем пературе на входе 380 °С. По мере прохождения парогазовой смеси через катализатор температура увеличивается до 440—450 °С. Из конвертора газ поступает в котел-утилизатор 3, где выделяющееся тепло используют для получения пара давлением 104,4 -105 Па (106,5 кгс/см2), а затем в подогреватель 4 для нагревания газа, поступающего на метанирование. При этом парогазовая смесь охла ждается до 210—220 °С и поступает в конвертор СО второй ступени 5. Газ имеет следующий состав: 60,5—61% Н 2, 20,5—21% N 2, 2,5— 3,5% СО, 15—16% С 02, 0,23% Аг и 0,32% СН4. На низкотемпера турном катализаторе при 210—250 °С и объемной скорости 2000— 3000 ч” 1 происходит конверсия окиси углерода (остаточное содержа ние 0,3—0,55%). Газ после низкотемпературной конверсии поступает на очистку от двуокиси углерода. В схемах с МЭА-очисткой его тепло предварительно используют для регенерации раствора.
Температуру газа на входе во вторую ступень конверсии регу лируют с помощью байпасирования части газа мимо котла-утили-
затора. Есть схемы, где регулирование температуры осуществляют впрыскиванием конденсата в газ, поступающий в конвертор.
Для увеличения срока службы и надежности работы низкотем пературного катализатора конверсии окиси углерода во многих схемах предусматривают специальную очистку парогазовой смеси от сероводорода и соединений хлора. Очистку осуществляют или в специальных аппаратах, или на дополнительно загружаемых в кон вертор второй ступени слоях катализатора. Сероочистку проводят
Рис. VIII-5. Принципиальная схема очистки газа |
от СО методом конверсии |
с водяным паром: |
|
1 — са тур ац и о н н ая баш н я; 2 — огн евой п одогреватель; 3 — |
к он вертор СО; 4 — теплообм ен |
ник; 5 — водон агр евател ьн ая баш ня; в — к он ден сац и о н н ая баш н я .
обычно на цинковых или цинкмедных поглотителях, а от соедине ний хлора на специальных поглотителях [27]. Очистку проводят при тех же температурах, что и во второй ступени конверсии окиси углерода и при объемных скоростях порядка 10 000—20 000 ч“ \
Всвязи с тем, что в газе присутствует значительное количество пара
ипроцесс проводят при высоких объемных скоростях, сероемкость
ихлороемкость поглотителей не превышает 2%.
Для получения водорода высокой степени чистоты применяют, схемы конверсии окиси углерода с промежуточным удалением дву окиси углерода. Газ после среднетемпературной конверсии СО проходит грубую очистку от двуокиси углерода и поступает на ста
дию низкотемпературной конверсии |
(рис. VIII-5). |
Очищаемый |
газ |
содержит 83—88% Н 2, 4—5% (N2 + |
Аг), 3—5% |
С 02, 3—5% |
СО |
и 0,5% СН4. |
|
|
|
Сначала газ насыщается водяными парами в сатурационной башне 1, затем смешивается с паром до требуемого для конверсии СО соотношения пар газ. В ряде случаев ограничиваются только сатурацией. Парогазовая смесь подогревается до 190—210 °С в подо гревателе 2 и поступает в конвертор СО 3 на низкотемпературный катализатор. Тепло конвертированного газа используют в тепло обменнике 4 для подогрева конденсата, подаваемого в сатурационную
25 за к а з 1 46 0 |
385 |
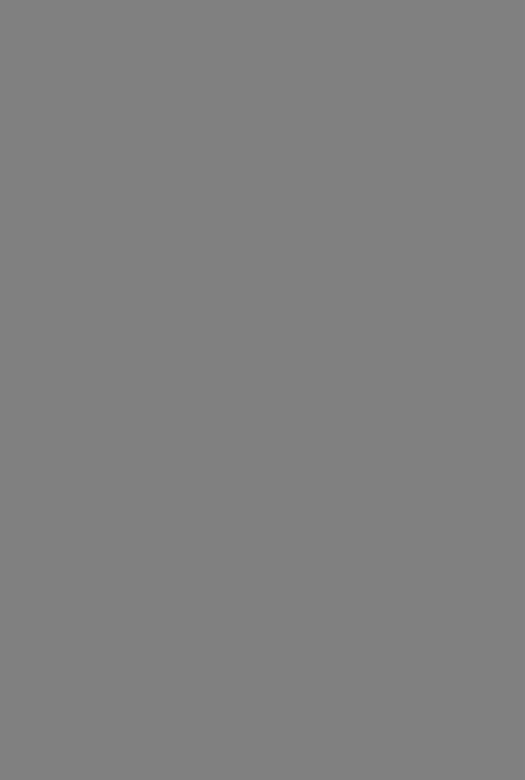
технические показатели работы катализатора (срок службы, сте пень конверсии, гидравлическое сопротивление и др.).
Если содержание мелких фракций превышает допустимый предел (—1%), катализатор рассеивают на специальной установке, оборудо ванной набором сит, вентилятором и циклоном для отсоса и сбора пыли. После загрузки определенной порции катализатора произ водят разравнивание слоя, необходимое для обеспечения более
Рис. VIII-7. Промышленные распределители:
ст — тороидального типа: 1 — корпус; 2 — распределитель; б — из трубы с вырезом: 1 — корпус; 2 — распределитель; з — защитно-распределительный слой; 4 — сетка; 5 — ката лизатор; в — из набора колец: 1 — корпус; 2 — распределитель.
равномерного распределения порозности по объему, которое нару шается остаточными мелкими фракциями.
Распределение парогазового потока по сечению аппарата. Важной проблемой для полочных реакторов является обеспечение равно мерного распределения парогазового потока по сечению аппарата. Предполагают, что в современных конструкциях можно достичь равномерного распределения с помощью различных распределите лей и защитно-распределительного слоя. Примеры промышленных распределителей приведены на рис. VIII-7. Кроме этих типов исполь зуют также распределительные решетки.
Основные требования, предъявляемые к распределителям, — это небольшие габариты и простота конструкции. Как правило, ука занные требования выполняются, однако следует отметить, что
большинство используемых в настоящее время распределителен не отвечают своему прямому назначению.
На рис. VIII-8 представлены результаты испытаний тороидаль ного распределителя а. Из рисунка видно: измеренный профиль скоростей потока существенно отличается от равномерного. Наблю-
|
|
|
|
|
|
дается |
возвратное течение в пе |
|||||
|
|
|
|
|
|
риферийной |
области. |
|
|
|||
|
|
|
|
|
|
_На |
рис. VIII-7, б |
показан |
||||
|
|
|
|
|
|
приблизительный |
характер те |
|||||
|
|
|
|
|
|
чения потока для |
распредели |
|||||
|
|
|
|
|
|
теля, состоящего из трубы с вы |
||||||
|
|
|
|
|
|
резом, наблюдаемый в промыш |
||||||
|
|
|
|
|
|
ленных условиях и существенно |
||||||
|
|
|
|
|
|
влияющий на эксплуатационные |
||||||
|
|
|
|
|
|
показатели реактора. Основной |
||||||
|
|
|
|
|
|
поток устремляется вниз к слою |
||||||
|
|
|
|
|
|
катализатора |
вдоль стенки ап |
|||||
|
|
|
|
|
|
парата, противоположной месту |
||||||
|
|
|
|
|
|
входа. |
На |
поверхности |
слоя |
|||
|
|
|
|
|
|
наблюдается |
возвратное |
тече |
||||
|
|
|
|
|
|
ние. В |
результате попадающая |
|||||
|
|
|
|
|
|
в катализатор |
пыль |
сдувается |
||||
|
|
|
|
|
|
в центральную |
зону |
сечения, |
||||
|
|
|
|
|
|
где она со временем уплот |
||||||
|
|
|
|
|
|
няется, |
превращаясь |
в |
слой, |
|||
|
|
|
|
|
|
практически непроницаемый для |
||||||
|
|
|
|
|
|
газа. |
|
|
|
|
|
|
|
|
|
|
|
|
На |
периферии вдоль стенок |
|||||
|
|
|
|
|
|
аппарата образуется |
серповид |
|||||
|
|
|
|
|
|
ная промоина, куда в основном |
||||||
Puc. VIII-8. Профиль скорости |
смеси |
и устремляется поток. Вовремя |
||||||||||
перед слоем катализатора, создаваемый |
работы это приводит к быстрому |
|||||||||||
распределителем |
тороидального |
типа: |
возрастанию |
гидравлического |
||||||||
w — ск орость |
г а за , |
м /с; |
w?cp — ср ед н я я |
с к о |
сопротивления |
аппарата, |
сни |
|||||
рость га за на |
п о л н ое сеч ен и е, м /с; х / В |
— |
к о |
жению |
степени |
конверсии, не |
||||||
|
орди н ата . |
|
|
|||||||||
|
|
|
|
|
|
обходимым остановкам для раз- |
||||||
равнивания слоя |
катализатора |
выгрузке накопившейся |
пыли |
ит. п.
Ваппарате с тороидальным распределителем (рис. VIII-7, а) образуется промоина в центральной части сечения, а область уплот нения на периферии; с распределителем из набора колец (рис.УШ-7,в)
—наоборот.
Одиночные распределительные решетки из перфорированных листов также не обеспечивают необходимого распределения потока. Поэтому лучше устанавливать систему решеток, расположенных на определенном расстоянии друг от друга [59]. Такой распредели тель занимает много места, конструктивно неудобен и редко приме няется.
Часто переоценивают и распределительные свойства верхнего защитно-распределительного слоя и делают его слишком коротким, не более 0,25 м. На самом же деле хорошее распределение обеспечи вают слои высотой в два-три диаметра аппарата [60]. В промышлен ных аппаратах это условие невыполнимо и, следовательно, распре делительное действие защитного слоя ограниченно.
Гидравлическое сопротивление. Полочные реакторы имеют отно сительно высокое гидравлическое сопротивление, создаваемое в ос новном слоем катализатора. Гидравлическое сопротивление посто янно увеличивается со временем вследствие разрушения катализа тора, а также по причинам, указанным выше.
В полочных аппаратах необходим постоянный контроль за вели чиной гидравлического сопротивления. Работа с реактором, где перепад давления выше допустимого, весьма опасна, так как могут обрушиться полки. В полочных реакторах применяют в основном крупнозернистые катализаторы. Расчет гидравлического сопроти вления (в Па) свежезагруженного катализатора производят по фор
муле [60]:
bp=(yw*/2g) [s (1 — е)/е3] f3h (VIII,23)
где у — удельный вес смеси, Па/м (Н/м3); w — скорость на полное сечение, м/с; 5 — удельпая поверхность грапул, м2/м3; е — порозпость слоя; / э — коэффи циент сопротивления; h — высота слоя, м.
Прочность опорной конструкции полок. При проектировании полочного реактора прочность опорной конструкции полок рассчи тывают, допуская, что нагрузка на нее состоит из веса катализатора, защитных слоев и решеток, а также усилий допускаемого гидравли ческого сопротивления. Поэтому установленный предел гидравли ческого сопротивления во время работы нельзя превышать. Однако это еще не дает полных гарантий.
Во время эксплуатации выполняют такие операции (например, быстрое открытие задвижек), в результате которых возникают и рас пространяются по технологической нитке сильные возмущения. Скорость распространения возмущений в слое катализатора^ осо бенно при повышенном гидравлическом сопротивлении, намного меньше, чем в пустом объеме. Из-за этого, например, при сбросах давления быстро опорожняется объем под слоем катализатора, в то время каК над ним находится практически невозмущенный газ.
Втаких случаях перепад давления на слое катализатора может достигать величины номинального давления в системе, и на опорную конструкцию будут действовать мощные кратковременные нагрузки.
Втаких условиях наблюдались случаи, когда катализаторные полки рушились. Это серьезная авария, которая надолго выводит всю технологическую систему из строя. Поэтому при работе с полочными
реакторам#» выполняя описанные операции, необходимо действо вать внимательно и осторожно.
Боковые нагрузки на катализатор вследствие изменений тем пературы. При разогреве реактора корпус его расширяется и про исходит усадка слоя катализатора.
При остановке и охлаждении корпус аппарата сжимается и ока зывает давление на катализатор. Расчеты (см. с. 320) показывают, что возникающие при этом нагрузки в десятки раз превышают вес слоя катализатора и вызывают разрушение наименее прочных гранул, образование мелких фракций, повышение гидравлического сопротивления и т. д.
Поэтому условием эффективной работы реактора является ста бильный технологический режим. Частые пуски и остановки реак тора быстро выводят катализатор из строя.
Безбалочные конструкции (рис. VIII-9). Безбалочная конструкция устраняет опас ность обрушения катализа тора, поскольку он распо лагается над слоем прочных металлических колец, кера мических шаров и т. п.
Таким образом, конструк ция полочного реактора при всей своей кажущейся про стоте содержит немало нега тивных моментов, которые необходимо учитывать при проектировании и эксплуа тации.
Радиальные реакторы (рис. VIII-10). В радиальных реакторах катализатор размещают в корзинах, образованных коаксиально расположенными центральной трубой и наружной обечайкой. Рабо чие поверхности корзины перфорированы и покрыты сеткой со сто роны катализатора. Между корпусом реактора и наружной обечай кой катализаторной корзины образуется кольцевой канал, по кото рому либо отводят продукты реакции, либо вводят сырье. Таким образом, в радиальном реакторе возникает сложное движение по
тока одновременно в |
осевом направлении (по |
кольцевому каналу |
и центральной трубе) |
и в радиальном — через |
слой катализатора. |
В соответствии с обозначениями И. Е. Идельчика [59] радиальные реакторы (рис. VII-11) могут быть двух типов: Z-образные (реак тор I) и П-образные (реактор И).
В Z-образном реакторе газ в центральной трубе и кольцевом зазоре движется в одном направлении, в П-образном — в противо положных. Число катализаторных корзин в реакторе обычно не превышает трех.
Распределение потока по слою катализатора. Эффективность работы радиального реактора в большей мере зависит от распреде ления потока сырья по высо.те слоя катализатора (по оси аппарата). Распределение потока сырья при некоторых соотношениях геометри ческих размеров аппарата и параметров структуры катализатора может сильно отличаться от равномерного. Однако в отличие от
полочных реакторов распределение потоков в данном случае под дается расчету, так как движение газа в радиальном реакторе сим метрично и организовано системой каналов. При расчете распреде ления потока сырья по слою катализатора в радиальном реакторе [61] исходили из рассмотрения движения газа или жидкости в пори стом канале.
Для решения этой задачи наиболее плодотворным оказался энергетический подход. Были получены расчетные формулы, не содержащие эмпирических коэффициентов [62—65].
5
л.'
с:
У |
У |
Рис. VIII-10. Радиальный конвертор окиси углерода:
1 — корпус конвертора; 2 — катализатор; з — катализатор для компенсации усадки.
Рис. VIII-11. Схемы радиальных реакторов:
1 — центральная труба; 2 — катализатор; 3 — кольцевой канал.
Ниже приведены дифференциальные уравнения для расчета рас пределения средней осевой скорости в центральной трубе по длине реактора:
Тип реактора |
Уравнения |
|
|
П-образный |
ипи'± аи'и -(- Ьи2 = О |
(VII1,24) |
|
Z-образный |
и”и*±a\u,u±a?ul (1— |
— а± (1—u)2 = 0 |
(VIII,25) |
з |
/ L V - |
_ _ b L - |
м f f V |
20 |
\ h ) |
’ “3 _ 4r00 ’ |
a4“ 2d3p V / J |
го, rlf d 9, l — радиусы центральной трубы, наружной обечайки корзины, экви
валентный диаметр кольцевого канала, длина рабочей (перфорированной) части корзины, м; л — коэффициент трения для промышленных трубопроводов
(от 0,015 до 0,022); £, <р, <рх — коэффициенты сопротивления и свободное се чение перфорации для центральной трубы и наружной обечайки корзин соот ветственно; /, / х — площадь поперечного сечения центральной трубы и кольце
вого канала, |
м2; |
е, х — свободный |
объем и |
коэффициент извилистости |
слоя; |
||||
s — удельная |
поверхность слоя, |
ма/м3; |
/ э — коэффициент трения |
в слое; |
и = |
||||
= w/wо — средняя безразмерная скорость в |
центральной трубе; |
WQ = |
q/f — |
||||||
м/с, где q — расход смеси, м3/с; |
у = |
хЦ — безразмерная координата; и', |
н е |
||||||
соответствующие |
производные |
по |
безразмерной |
координате; и* — скорость |
|||||
потока через слой катализатора, м/с, |
на полное |
сечение. |
|
|
|||||
П р и м е ч а н и е . При двойном |
знаке |
(± ) |
верхний знак |
относится к |
|||||
вводу смеси в центральную трубу реактора, |
а нижний — в кольцевой канал. |
||||||||
1,00 |
|
|
|
|
|
|
|
|
|
0,75
а0,50
0,25
О |
0,25 |
0,50 |
0,75 |
1,00 |
0 |
0,2 |
0,4 |
0,6 |
0,8 |
1,0 |
|
|
У |
|
|
|
|
|
У |
|
|
Рис. VIII-12. Распределение средней осевой скорости в П - и Z-образных реак торах (пунктирная линия — равномерное распределение):
1 |
— |
П -обравны й реак тор; <р = 0,16, f t |
> /; 2 |
— |
то ж е , <р =■ 0,16, Л < /; 3 — т о ж е , <р = 0,04, |
|
ft |
> |
/; 4 — Z-обр азн ы й р еак тор , |
<р *■ 0,04, Д |
> |
/ . Т очк и соответствую т различны м р а сх о д а м |
|
|
|
- |
|
га зо в о й |
см еси . |
|
Рис. V III-13. Распределение |
безразмерной скорости через слой катализатора |
|||||
|
|
по длине слоя |
в промышленном реакторе. |
Уравнения решают с граничными условиями:
у = 1 |
и = |
0 |
у = 0 |
и = |
1 |
На рис. (VIII-12 и VIII-13) представлены результаты экспериментов, полученные на моделях радиальных реакторов и в промышленных условиях.
На рис. (VII1-12) по оси ординат отложена безразмерная осевая скорость в центральной трубе, а по оси абсцисс безразмерная длина реактора (относи тельная скорость через слой катализатора v/vCp равна модулю производной и'). Сплошными линиями нанесены теоретические кривые, рассчитанные по урав нениям (V III,24)—(V III,25).
Точки на рис. VIII-12 — опытные данные. Пунктиром обозначена линия равномерного распределения. Как видно, на распределение потока существенно
влияет доля свободного сечения боковой поверхности центральной трубы. Уве личение ф от 0,04 (кривая 3) до 0,16 (кривая 1) приводит к резкому возрастанию неравномерности, что проявляется в значительном отклонении кривой 1 от пун ктирной линии. Таким образом, в радиальном реакторе всегда можно добиться практически равномерного распределения потока простым уменьшением доли свободного сечения перфорации центральной трубы или наружной обечайки.
Влияние высоты реактора I на характер распределения определяется вели чиной энергетических затрат на трение. При обычных для промышленных трубо проводов значениях X = 0,01—0,02 удлинение реактора, как правило, приводит
кусилению неравномерности в раздаче потока.
Вкоротком реакторе проблема распределения потока сырья менее важный фактор. Изменения диаметра центральной трубы или ширины кольцевого ка
нала в различной степени проявляются в реакторах типа П и Z. В П-образном реакторе можно довольно эффективно влиять на характер распределения, из меняй эти параметры. В Z-образном реакторе это влияние значительно слабее. Однако, если правильно выбрать геометрические размеры, можно добиться распределения потоков, очень близкого к равномерному. Например, об этом свидетельствуют данные рис. (VII1-13), полученные при обследовании промы шленного реактора.
Как видно из рисунка, на котором кривая рассчитана по уравнению (VIII,25), скорость парогазовой смеси через слой катализатора не более чем на 6% отли чается от средней. Таким образом, проблема распределения потоков в радиаль ном реакторе может быть полностью решена.
Расчет распределения потоков можно распространить на многокорзинчатые радиальные реакторы [61].
Гидравлическое сопротивление. Одним из достоинств радиаль ного реактора является небольшое гидравлическое сопротивление, что позволяет использовать мелкозернистые катализаторы и дости гать высоких объемных скоростей. Поскольку в радиальных реакто рах движение газа довольно сложно, то расчет гидравлического сопротивления отличается некоторым своеобразием. Полная потеря давления не может быть получена как результат суммирования перепадов давления отдельных элементов реактора, так как вели чины Дpi не являются аддитивными. Приходится пользоваться другими аддитивными величинами, такими как потери энергии (затраченная работа) на продвижение потока через различные эле менты реактора, выражаемые формулой:
М = 4 i & Pi
Тогда общее сопротивление радиального аппарата определится как
где qi — соответственно общий расход смеси и расход для отдельного эле мента реактора, м3/с.
Ниже приведены формулы для расчета составляющих общего сопро
тивления: |
|
|
|
1) |
работа, затраченная на |
преодоление входного участка |
|
|
|
= |
(VIII,26) |
где |
— коэффициент местного |
сопротивления |
входа; w x — скорость потока |
на |
входе, м/с* |
|
|
2) |
то же, для выходного участка |
|
|
|
|
а2= hpiw\ 72 |
(VIII,27) |
|
|
2 |
|
где |
£а — коэффициент местного сопротивления выхода; w 2 — скорость потока |
||
на |
выходе, |
м/с. |
|
3) работа, |
затраченная на продвижение газа но центральной трубе |
||
|
|
1 |
|
|
|
А э = (Xpl/4r0) fu>* J* «3 (у) dy |
|
|
|
О |
|
4) то же, |
в кольцевом зазоре |
|
|
|
|
1 |
|
|
|
Ai = (Xpl/2d3) h [(///,) ш0]3 Ju3 (у) dy |
|
|
|
о |
|
5) |
работа |
на преодоление трения в зернистом |
слое |
|
Л 5 = (л /8) р/э [S (1 — е ) / е З ] [f a — го)/^] (rjj/Z2) |
( u f)* d y |
|
|
|
|
1 |
6) работа на преодоление сопротивления перфорации центральной
трубы
0
А е = (я/8) гор (r0w0/2l) з ZJ £ fa )3 dy
1
7) то же для перфорации наружной обечайки катализаторной кор зины
|
о |
|
л 7= |
(л / 8) гг р (r0w0/2l)3 (r0/r i) 3.Jl (u')3dy |
|
|
\ |
|
Для вычисления |
работ As — ^17 необходимо знать закон |
изме |
нения средней скорости в центральной трубе по продольной |
коор |
динате. Соответствующие уравнения приведены выше. Поскольку радиальные реакторы проектируют всегда таким образом, чтобы
распределение парогазовой смеси было близким |
к равномерному, |
то для расчетов можно пользоваться формулами |
и = 1 — у; и' = |
= —1. Потери энергии на участках между корзинами вычисляют по формулам (VIII,26)—(VIII,27), в которых значения скорости, расхода и коэффициента сопротивления выбирают для соответст вующего участка.
Усадка катализатора и паразитные объемы. Катализаторы кон версии окиси углерода при восстановлении уменьшаются в объеме (до 7%). Кроме того, во время работы снижается порозность слоя
(в)вследствие усадки и разрушения части гранул. Все это приводит
кусадке катализатора. Для компенсации усадки приходится сверх
работающего слоя иметь в радиальной корзине затворные слои, в которых находится до 10—15% общего объема катализатора. Слои
катализатора, заполняющие днище корзины, также не участвуют
вработе. Эти дополнительные объемы катализатора являются для реактора паразитными. Определенную часть объема реактора зани мают и каналы, предназначенные для подвода и отвода потока паро газовой смеси.
Врезультате степень полезного использования объема аппарата
врадиальном реакторе ниже, чем в полочном.Если высота затвор ного слоя выбрана неверно или в результате неправильной эксплуа тации катализатор сильно разрушился, возможно образование бай пасного потока газа, который минует слой катализатора через освободившиеся отверстия пер форации.
Горизонтальные реакторы (рис. VIII-14). Горизонтальные реакторы по таким характери стикам, как гидравлическое со
противление и степень исполь |
|
||
зования |
полезного объема, |
за |
|
нимают |
промежуточное поло |
Рис. VIII-14. Горизонтальный реактор: |
|
жение |
между полочными |
и |
1 — катализатор; 2 — загрузочные люки; |
радиальными аппаратами. |
|
з — сетка; 4 — распределительные решетки; |
|
|
|
|
5 — разгрузочные люки. |
Преимуществом горизонталь ного реактора является возмож
ность использования коротких слоев катализатора, для которых требо вания к прочности гранул менее жесткие. Кроме того, не имеют осо бого значения и явления усадки катализатора. Однако без допол нительно принятых мер (например, футеровки корпуса или его обдува) горизонтальные реакторы могут работать с ограничен ным перепадом температур в слое катализатора. Иначе корпус аппарата и внутренние конструкции могут быть разрушены в ре зультате температурных деформаций. Поэтому в наиболее простом варианте горизонтальные реакторы применяют только для низко температурной конверсии окиси углерода.
Для горизонтальных реакторов характерны те же особенности движения и распределения потоков, что и для радиальных аппаратов.
Поэтому расчет распределения потоков и гидравлического сопро тивления в горизонтальном реакторе проводят по изложенной выше методике, учитывая специфическую геометрическую форму каналов и катализаторного слоя.
ОЧИСТКА ОТ ОКИСИ И ДВУОКИСИ УГЛЁРОДА И ОТ КИСЛОРОДА КАТАЛИТИЧЕСКИМ ГИДРИРОВАНИЕМ
Методы гидрирования СО, С 02 и 0 2 имеют много общего, по этому очистку от таких веществ методом гидрирования почти всегда совмещают в одном аппарате. Процессы гидрирования кислород содержащих примесей ускоряются одинаковыми или очень сход ными катализаторами. В промышленности процесс очистки от окиси
и двуокиси углерода методом гидрирования обычно называют метанированием. Степень очистки, которая может быть при этом достиг нута, определяется условиями термодинамического равновесия.
Вусловиях равновесия остаточная концентрация окиси углерода
вочищенном газе определяется уравнением:
Рн2орсн4
Рсо— ^,.3
КРц2
где К — константа равновесия; рНг0» Рен*» £со» Рн% ~ парциальные давле ния соответствующих компонентов в условиях равновесия, Па|
Расчеты показали, что при температуре ниже 400—450 °С реак цию можно рассматривать как необратимую; следовательно, прак тически может быть достигнута полная очистка газа от СО.
Равновесное парциальное давление двуокиси углерода выра жается уравнением
*Р>н,о14 Рс0* Рся41^Н*о]2
где К — константа равновесия; рНа, рСОа» Рен*’ ^HiO~ парциальные давле ния соответствующих компонентов, Па*
При температуре ниже 350 °С реакцию гидрирования двуокиси углерода в азотоводородной смеси следует рассматривать как необ ратимую.
При гидрировании кислорода в условиях термодинамического равновесия парциальные давления компонентов связаны соотно шением
^H2.Q •=к
^Н* V 'P O t
где К — константа равновесия; рНа0» Ро* — парциальные давления соответ ствующих компонентов в равновесных условиях, Па.
При стехиометрическом соотношении водорода и кислорода в исходной смеси равновесное парциальное давление кислорода можно определить по уравнению:
Р о 2 = ( Р н г о № К ) 2 / 3
При небольшом избытке водорода резко уменьшается равновесное парциальное давление кислорода. В таких условиях рог(равновесное) определяется по уравнению:
Р 0 2 ^ ( Р Н г О / Р н , К ) 2
На рис. VIII-15 приведена зависимость константы равновесия
иравповесного остаточного содержания кислорода от температуры
[66].Расчеты авторов показали, что при стехиометрическом соотно шении водорода и кислорода и температуре до 500 °С (а при неболь шом избытке водорода и температуре до 1000 °С) реакция взаимодей ствия О2 и Н 2 может рассматриваться как необратимая.