
- •ИЗДАНИЕ ВТОРОЕ, ПЕРЕРАБОТАННОЕ И ДОПОЛНЕННОЕ
- •ОСНОВНЫЕ СХЕМЫ ПРОИЗВОДСТВА ГАЗА ДЛЯ СИНТЕЗА АММИАКА
- •ОСНОВЫ ПРОЦЕССОВ ОЧИСТКИ ГАЗОВ
- •Циркуляционные процессы
- •ОЧИСТКА ПРИРОДНОГО ГАЗА ОТ ВЫСШИХ УГЛЕВОДОРОДОВ
- •АБСОРБЦИОННЫЕ МЕТОДЫ ОЧИСТКИ ГАЗОВ ОТ ДВУОКИСИ УГЛЕРОДА И СЕРНИСТЫХ СОЕДИНЕНИЙ
- •Примеры расчета абсорберов МЭА-очистки
- •Катализаторы
- •Кинетика и механизм процесса гидрирования
- •Аппаратурно-технологическое оформление процесса
- •АБСОРБЦИОННЫЕ СПОСОБЫ ОЧИСТКИ ГАЗОВ ОТ СЕРНИСТЫХ СОЕДИНЕНИЙ
- •ОЧИСТКА ГАЗОВ ОТ ОКИСИ УГЛЕРОДА
- •КАТАЛИТИЧЕСКИЕ И АДСОРБЦИОННЫЕ МЕТОДЫ УДАЛЕНИЯ ИЗ СИНТЕЗ-ГАЗА КИСЛОРОДСОДЕРЖАЩИХ СОЕДИНЕНИИ
- •Катализаторы
- •Аппаратурно-технологическое оформление
- •Катализаторы
- •2. ТОНКАЯ ОЧИСТКА ОТ ДВУОКИСИ УГЛЕРОДА МЕТОДОМ АДСОРБЦИИ
- •ОЧИСТКА ГАЗОВ ОТ ОКИСИ АЗОТА И АЦЕТИЛЕНА
- •2. СПОСОБ ОЧИСТКИ ОТ ОКИСИ АЗОТА И АЦЕТИЛЕНА МЕТОДОМ КАТАЛИТИЧЕСКОГО ГИДРИРОВАНИЯ
- •АБСОРБЦИОННЫЕ МЕТОДЫ ОЧИСТКИ ГАЗОВ ОТ АЦЕТИЛЕНА
- •Очистка пирогаза от сажи
может применяться и в циркуляционных способах. Области приме нения разных схем абсорбции описаны ниже.
Применение рециркуляции позволяет увеличить скорость аб сорбции в тех случаях, когда коэффициент массопередачи зависит от плотности орошения; увеличить поверхность массообмена (если в схеме на рис. И-5, а насадка смачивается не полностью) и, следо вательно, уменьшить высоту абсорбера. Кроме того, при такой схеме можно полнее использовать хемосорбент, если реакция про текает медленно. Однако, если равновесное давление растворенного газа над насыщенным раствором не равно нулю (обратимая реакция), то схема на рис. Н-5, а не позволяет полностью извлекать примеси из газовой смеси, так как очищенный газ вверху абсорбера контак тирует с «грязным» абсорбентом.
Циркуляционные процессы
Циркуляционные (или абсорбционно-десорбционные) процессы отличаются от разомкнутых процессов наличием замкнутого цикла абсорбента. Простейшая характерная схема абсорбционно-десорб- ционного цикла приведена на рис. II-6 . Растворитель, насыщенный
6
Рис, II.6 . Технологические схемы циркуляционных процессов при абсорбции под давлением:
а — регенерация |
сбросом давления и отдувкой; |
б — регенерация |
с применением нагрева; |
1 — абсорбер; 2 |
— насос; з — десорбер (регенератор); 4 — холодильник; 5 — теплообмен |
||
|
ник; в — кипятильник; |
7 — конденсатор. |
|
в абсорбере |
1 растворенным газом |
(извлекаемой |
примесью), посту |
пает в десорбер (регенератор) 3, где происходит обратный процесс — выделение растворенного газа, после чего абсорбент поступает вновь на абсорбцию.
Десорбция осуществляется за счет сдвига равновесия газ — жидкость в сторону уменьшения растворимости газа. Это достигается одним из следующих способов (или их сочетанием):
1 ) |
снижением общего давления до атмосферного или более низ |
кого; |
|
2 ) снижением парциального давления газа над раствором, что достигается отдувкой газа каким-либо другим газом либо отдувкой парами абсорбента (например, при его кипении);
3) повышением температуры, чток в подавляющем большинстве практически важных случаев приводит к снижению растворимости. Исключением является абсорбция аргона и метана жидким амми аком. Растворимость газов в данном случае увеличивается при повышении температуры, поэтому десорбцию проводят при охла ждении аммиака.
Преимуществами циркуляционных методов являются снижение расхода абсорбента (восполняются только его потери), возмож ность выделения в чистом виде хорошо растворимых газов. Однако при этом возрастает расход энергии и усложняется аппаратурно технологическое оформление процесса.
Примеры циркуляционных процессов весьма разнообразны. К ним относятся, в частности, большинство процессов очистки газов от двуокиси углерода и очистка газа от окиси углерода медноаммиач ными растворами.
Технологические схемы циркуляционных процессов включают кроме абсорбера и десорбера разнообразное оборудование, причем число десорберов может достигать 3—4. Это вызвано либо необхо димостью селективного выделения различных газов за счет посте пенного сброса давления или постепенного нагрева, либо необхо димостью глубокой регенерации. Соответственно могут применяться более сложные циклы абсорбента, частичная рециркуляция газовых потоков, что часто необходимо для полного разделения смесей.
Если регенерация абсорбента производится при нагревании, в схему включается оборудование для подвода тепла к системе (кипя тильники), для его отвода от системы (холодильники, конденсаторы), для рекуперации тепла (теплообменники). Ряд усложнений схемы вызывается необходимостью снижения энергии на процесс (рис. Н-4, б).
Технологическое оформление циркуляционных процессов сильно зависит от физико-химических особенностей процесса.
Так, при физической абсорбции относительно малая раствори мость и близкая к линейной зависимость ее от давления приводят к необходимости проводить абсорбцию под давлением. Чем выше давление, тем экономичнее процессы физической абсорбции. По этой же причине десорбцию выгоднее вести не при нагревании, а пу тем сброса давления (или отдувкой).
Ввиду относительно малой растворимости газов расход электро энергии на циркуляции абсорбента при физической абсорбции сравнительно велик. Он снижается при проведении физической абсорбции при пониженных температурах. Характерным примером такого процесса"является очистка газа от С 02 и других примесей холодным метанолом (см. гл. IV).
При циркуляционном процессе физической абсорбции трудно достичь тонкой очистки, так как наличие даже небольшого
количества растворенного газа в регенерированном растворе при водит к существенному увеличению его давления над раствором.
Для процессов физической абсорбции характерна сравнительно малая селективность растворителя по отношению к извлекаемому газу. Это приводит либо к потерям малорастворимого газа (и соот ветственно к загрязнению им хорошо растворимого газа), либо к необходимости усложнять технологическую схему.
Вследствие линейной зависимости растворимости газа от его давления при физической абсорбции количество циркулирующей жидкости в этом случае теоретически не зависит от концентрации извлекаемого компонента в исходном газе, так как с увеличением количества извлекаемого газа возрастает его парциальное давление, а следовательно, и поглотительная способность раствора. Повыше ние концентрации примеси приводит к увеличению высоты абсор бера либо (при заданной высоте) к незначительному возрастанию циркуляции раствора. Поэтому при физической абсорбции возможна рециркуляция газовых потоков после промежуточной десорбции с подачей их вновь в абсорбер.
Особенности технологического оформления процессов физической абсорбции* иллюстрируются на примере процесса водной очистки от СО2 (см. гл. IV).
Для химической абсорбции характерны следующие особенности: 1 ) возможность абсорбции при низком парциальном давлении извлекаемого газа вследствие более высокой поглотительной способ
ности раствора; 2 ) относительно низкая циркуляция раствора и соответственно
малый расход электроэнергии;
3)регенерация, как правило, путем нагревания (либо в сочетании со сбросом давления) вследствие резкого уменьшения растворимости
сростом температуры, при этом относительно велик расход тепла на десорбцию;
4)поскольку регенерация проводится часто при кипении абсор бента, его пары играют роль десорбирующего агента;
5)достижение весьма тонкой очистки;
6 ) более высокая селективность абсорбента и, следовательно, отсутствие рециркуляции газовых потоков;
7) возрастание коррозии и протекание побочных реакций, что обусловлено применением повышенных температур и щелочных реагентов — сильных и слабых электролитов;
8) возрастание расхода энергии при увеличении количества извлекаемого компонента.
Таким образом, в целом технологическое оформление процесса физической абсорбции проще, чем процесса хемосорбции. При повы шенных давлениях, пониженных температурах и грубой очистке физическая абсорбция потребляет меньше энергии. В этих случаях она является предпочтительной.
При высоком парциальном давлении примеси и в случае необ ходимости тонкой очистки целесообразно применять двухступенча
тые схемы, включающие физическую абсорбцию в первой ступени (грубая очистка) с регенерацией абсорбента путем снижения давле ния и хемосорбцию во второй ступени. Применяются и трехступен чатые схемы очистки, например в схемах производства аммиака с применением глубокого охлаждения. В качестве третьей ступени очистки от СО2 используется, например, тонкая очистка раство рами NaOH.
Технологические схемы циркуляционных процессов весьма раз нообразны. Так, в стадии абсорбции, кроме схем, показанных на рис. Н-5 и И-6 , используются и другие. Могут применяться схемы абсорбции с двумя и большим числом потоков абсорбента. Обычно верхний поток охлаждают до более низкой температуры или глубже регенерируют. Такие схемы позволяют в ряде случаев добиться более тонкой очистки и одновременно сократить расход энергии на регенерацию, сократить циркуляцию абсорбента, упростить схему (заменив двухступенчатую очистку одноступенчатой). Применяются схемы абсорбции с отводом тепла абсорбции (неадиабатическая абсорбция), что способствует увеличению поглотительной способности абсорбента.
В стадии регенерации, так же как и в стадии абсорбции, при меняются схемы с разделенными потоками абсорбента, позволяющие снизить расход тепла (см. гл. IV).
АБСОРБЕНТЫ ДЛЯ ОЧИСТКИ ГАЗОВ
К физико-химическим свойствам абсорбентов, применяемых для очистки газов, предъявляется ряд требований.
Абсорбционная емкость растворителя. Решающим свойством растворителя являются растворимость в нем основного извлека емого компонента и её зависимость от температуры и давления. От растворимости зависят все главные показатели процесса: циркуля ция абсорбента, расход тепла на десорбцию газа, расход электро энергии, условия регенерации (десорбции), габариты аппаратов.
Селективность растворителя характеризуется отношением между растворимостями извлекаемого газа а 2 и наиболее близкого к нему по растворимости a i компонента очищаемого газа (при одинаковых температурах,и парциальных давлениях):
|
С= |
« , / « ! . = Кф, i/Кф, 2 |
( 11, 22) |
где |
С — коэффициент селективности; Кф, i — коэффициент |
растворимости ме |
|
нее |
растворимого компонента |
1, |
|
От селективности растворителя зависят потери менее раствори мого газа при абсорбции, возможность полного разделения смеси, особенности технологической схемы и ряд расходных коэффициентов.
Давление насыщенных паров. При температуре абсорбции давле ние паров должно быть невелико во избежание потерь растворителя, а температура кипения растворителя соответственно достаточно велика. Промывка газов водой (или другие способы улавливания
паров и брызг) необходима почти во всех случаях, но при высоком давлении насыщенных паров она связана с усложнением схемы, расходом тепла на отгонку воды из рабочего раствора (или на ректи фикацию промывных вод). Требования к давлению насыщенных паров растворителя зависят от давления, при котором проводится абсорб ция, от его концентрации (если растворитель используется в виде водного раствора).
В некоторых случаях возможно применение весьма летучих абсорбентов (водные растворы аммиака, метанол). Это бывает оправ дано только при понижении температуры абсорбции или повышении давления, особенно в сочетании с конкретной схемой производства. Так, абсорбция холодным метанолом проводится при —50 °С (см. гл. IV), а очищенный газ поступает в блок глубокого охлаждения. В ряде случаев при очистке газа от микропримесей растворами, содержащими аммиак, очищенный газ поступает на синтез аммиака.
Температура кипения в значительной мере определяется требо ваниями к давлению насыщенных паров растворителя, поэтому оптимальная температура кипения абсорбента должна быть выше
150°С.
Вряде случаев, особенно при хемосорбции, очень высокая тем пература кипения абсорбента, т. е. чрезмерно малое давление'насы щенных паров, нежелательна. При накоплении в рабочем растворе примесей (продуктов побочных реакций, примесей, попавших с очи щаемым газом) целесообразна разгонка (ректификация) абсорбента.
Чрезмерно высокая температура кипения растворителя приводит к необходимости либо сильно повышать температуру разгонки, либо проводить ее в условиях глубокого вакуума.
Практически широкое распространение получили растворители, температура кипения которых 170—200 °С и давление насыщенных паров при 30 °С до 13,33 Па (0,1 мм рт. ст.).
Температуру плавления необходимо учитывать при выборе тем пературы абсорбции и условий хранения абсорбента. Смеси раство рителей (в том числе водные растворы) имеют более низкую темпе ратуру плавления, что позволяет использовать растворители с высокой температурой плавления.
Плотность обычно мало сказывается на возможности применения абсорбента, однако при прочих равных условиях желательно исполь зовать абсорбенты меньшей плотности.
Вязкость влияет на скорость тепло- и массопер'едачи и соответ ственно на габариты аппаратов и расход электроэнергии при пере качивании раствора. Поэтому при прочих равных условиях исполь зуются абсорбенты минимальной вязкости.
Термохимическая устойчивость. В условиях циклических абсорб
ционных |
процессов продолжительность |
пребывания |
абсорбента |
в системе |
очень велика. Полный обмен |
растворителя |
происходит |
в течение 6—18 мес. (в зависимости от потерь). В связи с этим к термо химической устойчивости абсорбента предъявляются высокие тре бования, поэтому при выборе абсорбента необходимо учитывать
даже весьма медленно протекающие побочные реакции (взаимодей ствие с компонентами исходного газа, гидролиз и др.).
К другим требованиям, предъявляемым к абсорбентам, относятся низкая коррозионная активность и невысокая стоимость.
ОСНОВЫ ТЕХНОЛОГИЧЕСКОГО РАСЧЕТА И ТЕРМОДИНАМИЧЕСКОЙ ОПТИМИЗАЦИИ АБСОРБЦИОННЫХ
ПРОЦЕССОВ
При расчете абсорбционного процесса обычно задают параметры очищаемого газа (давление, температуру, состав) и требования к очищенному газу.
Технологический расчет выполняется методом последовательного приближения. На первом этапе расчета используются только данные материального и энергетического баланса и данные о термодинами ческом равновесии. При этом сведения о кинетике и данные об аппа ратурном оформлении входят в расчет лишь в самом общем виде
(например, в виде допущений о |
возможной степени |
приближения |
|
к равновесию). |
|
|
|
На первом |
этапе приближенно определяются |
следующие |
|
данные: |
|
|
|
количество |
циркулирующего |
раствора; • температурный режим |
работы абсорбера (и давление в нем, если оно не задано);фавновесная линия абсорбера;» рабочая линия абсорбера; •число теоретических тарелок; расход электроэнергии на циркуляцию раствора; необ ходимая степень регенерации, давление, температура и число сту пеней регенерации; равновесная и рабочая линия в регенераторах и число теоретических тарелок; схема циркуляции раствора и схема газовых потоков;,степень очистки газа, потери полезных компонен тов, степень чистоты извлекаемого газа; режим работы теплообмен ной аппаратуры; расход тепла на регенерацию;.потери абсорбента с отходящими газовыми потоками.
Далее на втором этапе производится расчет массо- и теплообмен ной аппаратуры, включающий выбор типа аппаратов, гидродинами ческий расчет, расчет кинетики процессов и габаритов аппаратов.
На третьем этапе, в зависимости от результатов расчета на первщх двух этапах, уточняются технологические параметры. По существу третий этап — это оптимизация технологического режима, техноло гической схемы и аппаратурного оформления процесса с целью определения условий, обеспечивающий минимум приведенных затрат.
Если при первоначальном расчете энергетические затраты суще ственно превышают капитальные и другие виды затрат, то в первую очередь исследуют возможность снижения энергетических затрат. Аналогично поступают, когда определяющими являются какие-либо другие виды затрат. Для этого, целесообразно провести термодина мический анализ процесса [15, 16] с целью определения степени его термодинамического совершенства, источников потерь, возможностей
их устранения и основных направлений усовершенствования процесса. Термодинамический анализ проводят в следующем по рядке.
1.Расчет эксергетического к. п. д. [15, 16], характеризующего общие затраты работоспособной энергии на единицу полезной произ веденной работы.
2.Анализ потерь эксергии в отдельных аппаратах, т. е. опре деление узлов, в которых необратимость наиболее велика и усовер шенствование которых может дать наибольший эффект.
3.Классификация видов потерь по способам их снижения и опре деление максимально возможного эффекта в каждом случае.
В абсорбционных процессах все потери можно разделить на следующие категории:
1) потери, устранимые при изменении технологического режима;
2) потери, устранимые при изменении габаритов, гидродинами ческих и кинетических характеристик аппаратов;
3)потери, устранимые при изменении технологической схемы процесса;
4)потери, устранимые при замене состава или вида абсорбента;
5)потери, неизбежные при абсорбционном процессе.
При оптимизации процесса с применением способов пп. 2—4 производится повторный расчет процесса и аппаратуры.
ТЕХНОЛОГИЧЕСКИЙ РАСЧЕТ АБСОРБЦИОННЫХ ПРОЦЕССОВ
Технологический расчет разомкнутого процесса абсорбции сво дится к расчету абсорбера.
При необратимой химической реакции (когда равновесное давле
ние растворенного |
газа «над раствором Р 2 = 0 ) минимальную цир |
|||
куляцию (расход) |
абсорбента |
Дмин |
определяют из |
стехиометриче |
ского уравнения химической |
реакции. Реальная |
величина L = |
||
= \ £ МИ/,Пн.а (здесь |
т)н. а — степень |
приближения |
к равновесию |
|
внизу абсорбера, зависящая от кинетики процесса). |
|
Температурный режим абсорбера в общем случае необходимо рассчитывать по энтальпийному балансу. На повышение температуры в абсорбере может влиять не только теплота абсорбции извлекаемого газа, но и конденсация паров из газа. В простейшем случае уц2о ^ ^ 0 , а температура исходного газа равна температуре раствора на входе в абсорбер. Тогда при адиабатической абсорбции (отсутствие тепловых потерь и отвода тепла из абсорбера)
|
LC At = G2 АН |
( И , 23) |
где L — количество циркулирующего абсорбента; |
С — средняя теплоемкость; |
|
At = |
t\i. а — *и. а — разность температур абсорбента на выходе из абсорбера |
|
(tn. а) |
и на входе в абсорбер (tB. a)\G2 — количество извлекаемого газа; АН — |
|
теплота абсорбции (если tn. а > *D. а, то АН £ > 0)» |
|
|
Так как |
|
G2= LA X = L |
—я?2, в) |
(П .24) |
где я2,н и х2, tj — концентрации извлекаемого компонента на |
выходе и входе |
|
в абсорбер, |
|
|
то вместо уравнения (11,23) можно записать |
|
|
М = |
ЛЯ Ах |
(11,25) |
^ ---- |
Расход энергии на циркуляцию абсорбента определяют по урав нению:
I d Hg |
|
L dH |
|
|
|
/тт |
осч |
(в Дж) илиЛГ= |
367300-0,65 |
(в к В т -4) |
( |
’ 6) |
|||
где L — объем раствора, м3; d — плотность, кг/м3; |
Я = |
iOP + |
h\ Р — избы |
||||
точное давление в аппарате, кгс/см2; h — высота абсорбера, м; g — |
ускорение |
||||||
свободного падении, g = 9,81 м/с2. |
|
|
|
|
|
|
|
Количество рекуперируемой |
энергии в |
агрегате |
мотор — на |
||||
сос — турбина (в кВт-ч) |
|
|
|
|
|
|
|
hd (ЮР — К) 0,83 |
или |
8,15Ld (ЮР —h) 10& (в |
Дж) |
|
|
||
N p ^ — '-— 30 7 зоо-------- ’ |
|
|
В общем случае (физическая абсорбция или обратимая хими ческая реакция), когда равновесное давление Р*2 =£ 0 , величину Lm определяют из уравнения материального баланса (11,24):
т |
____ |
(11.27) |
•Ьмин — * |
|
|
Х2, п~!~ХЪ*в |
|
|
И |
|
|
^г.н^н . a |
x 2t в |
(11.28) |
|
где Х2 , н—растворимость газа 2 в абсорбенте при температуре и парциальном давлении Я2, н извлекаемого газа на входе в абсорбер.
Эту растворимость находят из равновесных данных. Величина Р 2>н = Ру2,н (здесь Р — давление в абсорбере; z/2iH — концентра ция извлекаемого компонента газа на входе в абсорбер, или точнее в газе, находящемся в контакте с раствором, выходящим из абсор бера).
Температура внизу абсорбера зависит от величины a;2tH. В общем случае растворимость газа 2 рассчитывают методом последователь
ного приближения [приближенный расчет |
из предположения, |
|
что tH= |
затем расчет tHпо уравнению (11,25), расчет уточненной |
величины x2tfi и т. д. ].
Равновесная линия абсорбера (зависимость у2 от х2 при перемен ной температуре, соответствующей профилю изменения температуры по высоте абсорбера) строится следующим образом. По уравнению (11,25), или более точно по полному балансу энтальпий, находят зависимость температуры раствора от концентрации х2. Затем по равновесным данным для каждой величины х2 и t находят значе ние Р\ и yl = РУР (где Р — давление в абсорбере).
Соотношение жидкость газ L1G в абсорбере, где G — общее количество газа на входе в абсорбер, можно найти следующим обра зом. С учетом того, что
|
G2— Gy2%н |
GBy 2, в |
|
(11.29) |
||
Здесь GB— количество |
очищенного |
газа, |
равно G Ga, поэтому |
|||
|
|
G (у2, н |
У2»в) |
|
(11.30) |
|
|
(72“ |
1 -1 /2 , В |
|
|||
Следовательно |
|
|
||||
|
G (у2»н |
У2* в) |
|
|||
|
|
|
||||
и |
|
(1 |
У2*в) (^2»Н Х2* в) |
|
||
__ ______У2, н У2* В_____ |
|
|||||
L |
(11,31) |
|||||
G |
(1 |
У2чв) (Х2*В Х2»в) |
||||
|
При разомкнутых процессах обычно x2tB ^ 0, при циркуляционных процессах x2tB ^ x2tP (концентрация газа в регенерированном рас творе).
При физической абсорбции x2tP |
х2,„, |
поэтому, |
учитывая, |
||
что x*2tH = Р 2,Н1КФ, получим (при у 2 |
,в = |
0) |
|
|
|
G2K<b = |
Су2.н#Ф |
__ |
G/Гф |
Gm |
|
■^2»нЛн. а |
РУ2* н'Пн. а |
|
-^Лн. а |
Лн. а |
’ |
где т = 1/2 , н/яг, н — константа фазового равновесия для условий низа абсор бера (или в точке вывода насыщенного раствора из абсорбера).
В большинстве процессов физической абсорбции величина Кф мало зависит от состава раствора и давления, поэтому
L/G = Кг/(РЦн. а) |
(11,33) |
т. е. объем циркуляции физического абсорбента не зависит от коли чества извлекаемого газа и определяется значениями коэффициента Генри и давления абсорбции. Следовательно, расход энергии на единицу объема извлекаемого газа тем меньше, чем больше его концентрация в смеси. В этом заключается преимущество физической абсорбции.
При химической абсорбции вместо Кф (или КТ) используется
величина Кх = |
P 2/z2» возрастающая с увеличением х2. Циркуляция |
|||
хемосорбента |
возрастает при увеличении |
концентрации |
примеси |
|
в очищаемом газе. |
|
|
|
|
Минимальная концентрация примеси y2tB в очищенном газе |
||||
определяется равновесным давлением двуокиси углерода |
„ |
над |
||
регенерированным раствором, поступающим |
на абсорбцию, а |
сле |
довательно, и условиями десорбции. Таким образом, минимальное парциальное давление примеси в очищенном газе
в==^>2, В = |
P y2t в = |
К.г, В^г» р |
(II,34) |
где Кгьв — коэффициент Геири для |
условий |
верха абсорбера, |
^ |
При равновесии внизу десорбера
#2. Р= |
Х2, Р = |
-^2»р/-^Г,р |
(11,35) |
где Р 2, р — парциальное давление |
газа |
над регенерированным раствором на |
выходе из десорбера; К г, р — коэффициент Генри для условий низа десорбера.
Тогда
_ |
^ 2. р |
Кг, П |
(11,36) |
2/2,в - |
р |
К г р |
Если температура в верхней части абсорбера и нижней части десорбера одинакова, то К г,в = Кг,? и
У2.в = Р 2,т>/Р |
(И,37) |
Так, если десорбция проводится при |
атмосферном давлении |
без нагрева, вакуумирования и без отдува каким-либо газом (т. е.
Р 2,р равно |
общему давлению в десорбере), то для того |
чтобы кон |
центрация |
примеси в очищенном газе составляла 4%, давление |
|
в абсорбере |
должно быть выше 2,45 МПа (25 кгс/см2). |
|
В тех случаях, когда десорбция проводится при нагревании, уравнение (11,36) с учетом зависимости коэффициента Генри от температуры [см. уравнение (1 1 ,6 )] примет вид:
, |
, * |
, |
Я2,р |
ДЯ |
/ 1 |
1 \ |
(11,38) |
lg2/2, B ^lg2/2, B - t e |
р |
2,3 R |
\* Т В |
Т р ) |
|||
где Тъ — температура |
газа на |
выходе из |
абсорбера; |
Гр — температура рас |
|||
твора на выходе из десорбера* |
|
|
|
|
|
|
Уравнение (11,38) позволяет при заданных степени очистки, темпе ратуре и давлении в абсорбере выбрать давление и температуру регенерации. Практически концентрация примеси в очищенном газе
выше в |
T)aiaT)Hip раз |
(здесь т]в,а — степень |
приближения |
к равно |
|
весию |
в |
верхней части абсорбера; г)„, р — степень приближения |
|||
к равновесию в нижней части десорбера). |
|
|
|||
При |
физической |
абсорбции величина |
г|н> а может |
достигать |
70—80%, при хемосорбции она сильно зависит от скорости хими ческой реакции. При тонкой очистке желательно, чтобы г|в>а ^ ОД, т. е. чтобы y l t в ^ 0,lz/2tB. В этом случае движущая сила процесса абсорбции практически не зависит от равновесного давления в верх ней части абсорбера. Степень приближения к равновесию в нижней части десорбера обычно выше, чем в абсорбере, особенно при повы шенной температуре. Поэтому можно принимать т]„,р = 0,8—1.
Количество менее растворимого газа (компонент 1), поглощаемое в абсорбере, зависит, как было указано выше, от его селективности. Чем выше коэффициент селективности, тем меньше потери очища емого газа и соответственно степень загрязнения извлекаемого компонента 2 менее растворимым компонентом 1 .
Количество растворителя, подаваемого на абсорбцию, опре деляется уравнением (11,32), поэтому максимальное количество менее растворимого компонента 6?lfP, которое может содержаться
в насыщенном растворе, выходящем из абсорбера, равно (при усло вии достижения равновесия по компоненту 1 )
GKГ, 2 ^ 1 |
_ |
@У1 |
Кг, о |
(II,39) |
GltP = x1L = рт1н^ К г 1 |
- |
% а |
Kr i |
где 2/i — максимальная концентрация в газе менее растворимого компонента.
Доля б менее растворимого компонента, уносимого с абсорбентом вследствие растворения, составит по отношению к общему его коли честву
Р |
Кг, 2У1____ I _ |
I |
I |
У\ |
(11,40) |
|
@Уън |
Кг,ll/i* н Ли» а |
С Ли. а |
1/1 . и |
|||
|
||||||
где у ъ н ~ концентрация |
менее растворимого |
компонента в газе в нижней |
||||
части абсорбера. |
|
|
|
|
|
Таким образом, если y t ^ у lt н (когда величина у2мала) и т) ->■ 1, то § = 1/С. Величина 1/С характеризует возможную потерю менее растворимого компонента с хорошо растворимым компонентом. Соответственно она позволяет рассчитать степень загрязнения извле каемого газа, а также оценить целесообразность и необходимость усложнения технологической схемы для снижения потерь менее растворимого компонента.
Если на абсорбцию подается очень большой избыток раствори теля по сравнению с необходимым по равновесию (т. е. величина г)„,а мала), потеря менее растворимого газа (например, водорода) возрастает. Кроме того, существенное влияние на эффективность селективного разделения газов оказывает различие в скорости абсорбции газов.
Когда селективность растворителя недостаточна, то для умень шения потерь разделяемых газов и получения их в чистом виде используется промежуточная десорбция с рециркуляцией десорби рованных газов. Однако это связано с дополнительным расходом электроэнергии и усложнением технологической схемы. Рециркуля ция газов промежуточной десорбции целесообразна лишь при физи ческой абсорбции, когда изменение парциального давления газов не оказывает существенного влияния на соотношение жидкость — газ.
Обычно хемосорбенты являются более селективными; при этом чем ниже давление абсорбции, тем выше селективность.
Селективная абсорбция может также осуществляться за счет различия в скоростях абсорбции. В этом случае селективное извле чение одного из компонентов возможно, например, вследствие боль шой скорости химического взаимодействия или каталитического ускорения одной из реакций.
Существуют и другие варианты. В частности, когда скорость абсорбции одного из компонентов газовой смеси лимитируется скоростью диффузии в жидкой фазе, а другого — скоростью диф фузии в газовой фазе, для селективного извлечения одного из ком
понентов подбирают такой аппарат и такие условия абсорбции, при которых интенсифицируется диффузия только в одной из фаз (подробнее см. главу VI). Селективное разделение газов при абсорб ции более подробно рассмотрено в главах IV и X.
Технологический режим (давление и температуру) промежуточной десорбции выбирают таким образом, чтобы обеспечить полную десорбцию меиее растворимого компонента (водорода и др.) при минимальной десорбции хорошо растворимого компонента. Оче видно, что десорбция компонента 2 не будет происходить, если давле ние в промежуточном десорбере равно парциальному давлению компонента 2 над насыщенным раствором (при отсутствии отдувки).
Если температура в промежуточном десорбере равна |
температуре |
в абсорбере, то давление в нем Рп д = Р 2%„"П, а- |
Практически |
оно должно быть ниже, чтобы обеспечить дополнительную движущую силу десорбции менее растворимого газа 1 за счет отдувки его де сорбирующимся компонентом 2 .
Аналогичный эффект достигается при некотором повышении температуры и промежуточном десорбере. Распространенный способ промёжуточйой десорбции заключается в отдувке из раствора рас творенного компонента 1 чистым компонентом 2 (возвращаемым после десорбции его в следующем десорбере), либо каким-либо дру гим газом.
Аналогично достигается десорбция компонента 2 в следующем десорбере, если расчет показывает, что десорбция сбросом давления и нагреванием [уравнение (11,38)] недостаточна для обеспечения нужной степени#очистки газа. Кроме того, при повышении темпе ратуры увеличивается давление насыщенный паров растворителя, которые начинают играть роль отдувочного агента.
При расчете десорбции парами растворителя используют зави симость температуры кипения абсорбента от содержания в нем
растворенного газа х2 при |
заданном давлении в |
регенераторе. Эту |
||
зависимость находят после |
построения графика |
функции Робщ = |
||
= Р1 + Рпар от |
х2 при различных температурах с последующим |
|||
снятием с |
этих |
графиков изобар Т — х2 при Р0бщ = const. Кон |
||
центрация |
x2tfl |
может быть либо задана условиями очистки в аб |
сорбере (см. выше), либо (если достигнута достаточная движущая сила в верхней части абсорбера) найдена после оптимизации про цесса по расходу энергии (см. главу IV), а также условиями терми ческой устойчивости растворителя.
Зная концентрацию x2tH и температуру в нижней части регене ратора, определяют давление в регенераторе. При заданном давлении в регенераторе в простейшей схеме регенерации температура вверху регенератора равна температуре кипения насыщенного раствора на входе в регенератор, т. е. определяется по тем же графикам зави симости Т от #2. Практически эта температура может быть несколько выше, причем от того, на сколько реальная температура вверху регенератора выше температуры кипения при х2 „#а, зависит движу щая сила десорбции вверху регенератора.
4 Саказ 1Л6о |
49 |
Важным |
фактором, влияющим на выбор режима |
регенерации* |
в частности |
его давления, является флегмовое число |
Ф = -Р^арАРг* |
От величины Ф вверху регенератора зависит расход тепла на созда ние отдувочного пара. Величина Ф необходима при расчете нагрузки по парогазовой смеси по высоте регенератора (т. е. при расчете егодиаметра и т. д.).
Равновесное флегмовое число
р
Ф* — пар (f, xt )
Р* (/, *,)
Г2
__р*
*2 (U хщ)
Р*
(11,41>
*2 (t, хг)
может быть найдено из равновесных данных. Практически Ф Ф Ф* и при заданном давлении в регенераторе зависит только от темпе ратуры
^пар (О
(П,42)
Р Р"“ Р пар (О
Расход тепла на регенерацию слагается из расхода тепла на покрытие теплоты десорбции, на нагрев растворителя и на его испа рение. Количество паров, уходящих через верх регенератора
Gnap = G20 2l8 = G2 - p - ^ V — |
( И . 4 3 > |
Если термическая устойчивость растворителя и степень очистки
вабсорбере позволяют варьировать в некотором интервале давление
врегенераторе, то его выбирают, исходя из соображений экономии энергии (минимум расхода тепла). При этом важно изменение Ф* при увеличений давления (а следовательно, и температуры). Вели
чина dO*/dt > О (т. е. флегмовое число возрастает при повыше нии температуры), если давление растворенного газа над раствором увеличивается медленнее, чем давление паров растворителя, или (что равносильно) если теплота десорбции газа меньше теплоты испарения растворителя. При обратной зависимости выгодно повы шать температуру, а следовательно, и давление регенераций (не смотря на кажущееся противоречие, так как снижение давления формально облегчает десорбцию). Однако в этом случае повышение температуры без увеличения давления приводит к росту Ф и расхода тепла, а следовательно, может привести (при ограниченном расходе тепла) и к ухудшению регенерации растворителя.
Равновесная линия в регенераторе строится аналогично равно
весной линии абсорбера по |
известной зависимости у* = P S ^ .^ /P p |
||
от х 2, причем значение PJ |
принимается при температуре, |
равной |
|
температуре кипения раствора при данном х2. Подробно |
расчет |
||
регенерации паром, в частности расчет расхода |
тепла, рассмотрен |
||
в главе IV. |
|
|
|
При регенерации отдувкой газом количество |
отдувочного |
агента |
в верхней части десорбера определяют аналогично количеству отдувочных паров:
J-ОТД- |
(11,44) |
Количество отдувочцого газа (или пара) G0TA, необходимое ддя де сорбции, можно определить по уравнению, аналогичному уравнению (1 1 ,33), исходя из условий равновесия в верхней части десорбера
G? _ |
Р р |
(11,45) |
|
L |
K rr\Q, р |
||
|
где Gp = G2t р + £ 0тд — количество газа, выходящего через верх десорбера’ равное сумме количества газа, десорбируемого в данном десорбере G2t р, и отдувочного агента £ 0тд’, т]в. р—степень достижения равновесия в верхней части десорбера.
Расход электроэнергии на отдувку равен для N в кВт*ч
^ = 0,123(?отд lg (P i/^ 2)
где бготд — в м3; Р х и Р 2 — давление внизу и вверху десорбера.
Из уравнений (11,32) и (11,45) следует, что при одинаковых тем пературах абсорбера и десорбера, т. е. при одинаковых значениях Кг
и Кф
G2,р~Ь £ОТД |
_ ____________ |
|
G2>р |
Р 2>н^н. аЛв. р |
|
6отд=С2,р ( > 2.н%Р;лв.Р - 1) = |
<?2>р |
(и,46) |
Следовательно, чем выше давление в абсорбере, концентрация при меси в очищаемом газе и степень приближения к равновесию в аб сорбере, тем меньше Сготд.
Если при расчете по уравнению (11,46) величина Сохд ^ 0, то отдувочный агент необходим лишь для сдвига равновесия в нижней части десорбера.
Наиболее сложным случаем является десорбция нескольких газов при нагревании. В этом случае десорбция каждого из компо нентов облегчается Наличием других компонентов, выполняющих функцию десорбирующих агентов. В результате температура де сорбции ниже (или степень десорбции выше), чем при десорбции одного растворенного газа. Это наблюдается, например, при аб сорбции сероводорода и органических сернистых соединений раз личными растворителями из газов, содержащих двуокись углерода. В извлечении двуокиси углерода нет необходимости, однако нали чие СО2 в растворе облегчает десорбцию сернистых соединений и позволяет соответственно увеличить степень очистки газа от сер нистых соединений.
Приведенные соотношения основаны на расчете условий равно весия на концах аппаратов. Однако при криволинейных равно весных и рабочих линиях возможны случаи, когда процесс
лимитируется равновесием в средней части абсорбера или регенера тора. Для расчета соотношений жидкость — газ в таких процессах ис пользуется более сложная методика, основанная на анализе приведен ных выше соотношений по всей высоте аппарата (см. гл. IV). Если вы численное для какого-либо сечения аппарата минимальное соотно шение LIG в абсорбере и Gp/L в регенераторе окажется больше вели чины, найденной расчетом по равновесию на концах аппаратов, то в последующих расчетах следует пользоваться большей вели чиной.
Окончательной проверкой принципиальной работоспособности процесса является построение наряду с равновесной также и рабочей линии процесса. Расчет этих кривых, а также определение числа теоретических тарелок являются последним этапом перед расчетом аппаратов и последующей оптимизацией процесса в целом.
Уравнение рабочей линии является уравнением материально теплового баланса процесса. Для любого сечения аппарата соблю дается условие:
d (Lx) = d (Gy)
где L п G — количества газа и жидкости;- х и у — концентрации извлекаемого компонента в газовой и жидкой фазах.
Следовательно
L dx + х dL = G dy + у dG
отсюда
Поскольку dG = — dL, то получаем
dy |
_ |
L |
dG |
dx |
~ |
G |
Gdx (* + 0 ) |
В частном случае, когда dG/dx и dLldx малы, dyldx = LIG, т. e. рабочая линия в координатах у — х является прямой линией. Однако в общем случае рабочая линия представляет собой кривую. Это характерно при большом количестве извлекаемого компонента в аб сорбере и для регенератора (где dG/dx может быть большим).
При построении рабочей линии абсорбера в простейшем случае расчет ведут по уравнению материального баланса для каждого участка L {хвых — xBX) = G (узх — z/Bblx), в котором известны, на пример, величины L, G, увх, хвых. Задаваясь величиной хЬХ1 можно получить значение увых.
При расчете рабочей линии при совместном массо- и теплообмене (например, в регенераторе с отдувкой парами) расчет рабочей линии усложняется тем, что^ объем парогазовой смеси сильно зависит от тепла, поглощаемого на каждом участке. При этом приходится решать совместно уравнения теплового и материального баланса
ивводить некоторые дополнительные допущения (см. главу IV). Обычно расчет ведут снизу вверх, задаваясь расходом жидкости,
концентрацией х2,р и количеством тепла, подведенного к системе
(а следовательно, и количеством парогазовой смеси в нижнем сечении регенератора), затем по тепловому балансу участка (с произвольно выбранной величиной х2) рассчитывают количество парогазовой смеси на выходе из этого участка.
Результаты построения рабочей и равновесной линий позволяют судить о возможных направлениях усовершенствования процесса. Так, малое число теоретических тарелок (большая движущая сила) указывает на то, что аппараты могут быть небольшой высоты. Однако это же свидетельствует о необратимости процесса (высокий расход энергии). Более детальный анализ позволяет найти пути снижения расхода энергии.
КИНЕТИКА ФИЗИЧЕСКОЙ АБСОРБЦИИ
При расчете кинетики процесса физической абсорбции 'обычно используют уравнение массопередачи:
i = K va (у—у*) |
(II ,47) |
Для расчета количества поглощенного компонента у надо знать коэффициент массопередачи К г, поверхность контакта а и движущую силу у — у*. В уравнении (11,47) К г отнесен к концентрации компо нента в газе и измеряется в кмоль/(м2 *ч*кмоль/м3) или м/ч; вели чина а выражена в м2/м3, концентрации у и у* — в кмоль/м3 (у — фактическая концентрация передаваемого компонента в газе; у* — концентрация компонента в газе, равновесная с составом жидкой фазы).
Коэффициент массопередачи К т и количество передаваемого вещества / могут быть выражены через коэффициенты массоотдачи
|
1 |
__ _1 _ , _т_ |
(11,48) |
|
|
К т |
Рг |
Рж |
|
|
|
|||
/ = Рга (у — ур) = Ржа (*р—я) |
(И ,49) |
|||
где ур и Хр — концентрации |
передаваемого |
компонента на границе |
раздела |
|
фаз, соответственно в газе и |
жидкости, кмоль/м3. |
|
Указанные концентрации связаны между собой через константу фазового равновесия /гг, выраженную в м3 жидкости на м3 газа
Ур = тхр |
(П,50) |
Из уравнения (11,48) следует, что общее сопротивление массопередаче 1 1КГ представляет собой сумму сопротивлений в газовой (1 /рг) и жидкой (т/рж) фазах. Доля фазовых сопротивлений в общем сопро тивлении массопередаче зависит от кинетических коэффициентов рг и’рж; большое влияние оказывает также^константа фазового равно весия. При уменьшении т (т. е. при увеличении растворимости) доля сопротивления в газовой фазе возрастает.
Как видно цз уравнений (11,47)—(11,49), для их практического использования нужны значения рг, рж, а. Теоретический расчет коэффициентов массоотдачи, основанный на решении уравнения
конвективной диффузии, возможен лишь для простых случаев дви жения жидкости. Поэтому на практике приходится либо обращаться к эмпирическим данным (подробные практические рекомендации по расчету коэффициентов К г, рг, рж даны в работе [17]), либо исполь зовать полуэмпирический аппарат теории подобия [17, 18]. В пос леднем случае обычно представляют зависимость критерия Нуссельта от определяющих критериев Рейнольдса, Прандтля и др. и симплек сов геометрического подобия в виде степенной функции.
Поскольку для некоторых массообменных аппаратов определе ние поверхности контакта связано с большими трудностями, реко мендуется пользоваться объемными коэффициентами массопередачи или массоотдачи (К^а, рга, ржа), имеющими размерность ч-1.
В реальных массообменных аппаратах процесс проводят при высокой турбулизации фаз с целью обеспечения высокой скорости массопередачи. В общем случае перенос вещества в каждой из фаз осуществляется благодаря молекулярной и турбулентной диффузии, причем скорость диффузии подчиняется закону Фика
(П,51)
где с — концентрация диффундирующего компонента, кмоль/м3; D — коэффи циент молекулярной или турбулентной диффузии, м2/с; х — расстояние, м.
При турбулентном движении перенос вещества за счет молеку лярной диффузии невелик по сравнению с переносом вещества за счет турбулентных пульсаций и направленного движения фазы. Однако картина резко изменяется в непосредственной близости к границе раздела, где значение молекулярной диффузии становится исклю чительно важным.
Согласно современным представлениям [19], вблизи границы раздела существует пограничный диффузионный слой, в котором и происходит резкое изменение концентрации. В пограничном диф фузионном слое перенос вещества осуществляется за счет молекуляр ной диффузии и конвекции; обычно считают, что роль турбулентной диффузии в диффузионном слое пренебрежимо мала и становится заметной и даже преобладающей за его пределами, а именно в вязком пограничном слое. В жидкостях толщина пограничного диффузион ного слоя намного меньше толщины вязкого пограничного слоя. Указанные представления позволяют записать уравнение конвек тивной диффузии в диффузионном пограничном слое в следующем виде:
dcildt — D[ diu grad с/— w grad с/—/Хим |
(11,52) |
где w — скорость потока, в общем случае зависит от поперечной координаты у; /хим — расход компонентов с* на химическую реакцию.
Если ограничиться следующими условиями: одномерное движе ние по продольной координате х; диффузия только по поперечной координате у; процесс стационарный (dcldt = 0) и наличие только
физической абсорбции (/хим = 0), то уравнение (11,52) существенно упрощается
02с |
дс |
(11,53) |
D |
д х |
|
|
|
Скорость потока оказывает большое влияние на толщину погра ничного диффузирнного слоя. Зависимость коэффициента массоотдачи от скорости соответствующей фазы обычно представляют в виде степенной функции; показатель степени в зависимости от типа
аппарата |
и гидродинамического режима изменяется в интервале |
от 0,3 до |
1. |
Коэффициент молекулярной диффузии влияет на коэффициент массоотдачи; по теоретическим данным для жидкой фазы показатель степени в зависимости от р ~ D n равен 0,5, для газовой фазы — 0,67. Экспериментальные данные хорошо согласуются с теорией [19]. Исключение составляет случай, когда в жидкости в непосредственной близости к границе раздела развивается поверхностная конвекция. В таких условиях влияние коэффициента молекулярной диффузии уменьшается вплоть до полной независимости рж от Ъж [2 0 ].
Влияние вязкости на коэффициент массоотдачи можно устано вить из анализа критериальных уравнений и экспериментальных данных. Для каждой из фаз коэффициент массоотдачи обратно про порционален вязкости в степени, близкой к 0,5.
Поверхностное натяжение не влияет на коэффициент массоот дачи рж в условиях ламинарного течения жидкости. При турбу лентном течении рж обратно пропорционален поверхностному натя жению в степени около 1/ 3 [21]. При добавлении поверхностно активных веществ могут наблюдаться локальные изменения поверх ностного натяжения и, как следствие, поверхностная конвекция и увеличение скорости массопередачи. Изменение величины а в на правлении движения жидкости также способствует образованию конвективных токов вблизи поверхности [22]. В ряде случаев, наоборот, при добавлении ПАВ изменяется структура поверхно стного слоя таким образом, что коэффициент массоотдачи рж умень шается.
При изменении температуры меняются физические свойства и соответственно величины рг и рж. Как правило, коэффициенты массоотдачи возрастают при увеличении температуры. Поскольку константа фазового равновесия с повышением температуры также увеличивается, то температурная зависимость коэффициента массо передачи определяется главным образом температурной зависи мостью тп!рж.
Давление не влияет па коэффициент массоотдачи в жидкой фазе. Коэффициент молекулярной диффузии в газовой фазе, а следова тельно, и величина рг уменьшаются с повышением давления; соот ветственно снижается и коэффициент массопередачи.
КИНЕТИЧЕСКИЙ РАСЧЕТ АБСОРБЕРОВ
При расчете абсорберов обычно задаются количеством газа, его давлением и температурой, начальной и конечной концентрацией извлекаемого компонента в газе. Начальная концентрация извле каемого компонента в жидкости также бывает задана; для установок с регенерацией поглотителя ее определяют, исходя из оптимального режима работы регенератора (десорбера). Конечную концентрацию поглотителя принимают максимально возможной; при этом учиты вают условия равновесия, коррозионную активность и др.
Обычно степень приближения к равновесию на входе газа в противоточный абсорбер т|и а, которую оценивают как отношение равновесного давления компонента к его парциальному давлению в газе, не превышает 80%. По уравнениям материального баланса (11,27), (11,31) и (11,33) рассчитывают количества передаваемого компонента и поглотителя. Для кинетического расчета абсорбера необходимо знать уравнение рабочей линии. В общем случае рабочая линия является кривой. Если пренебречь изменением объема фаз
по |
высоте аппарата (L/G — const), то уравнение рабочей |
линии |
сводится к уравнению прямой линии: |
|
|
|
У — Ух— L J G (а?! — х) |
(11,54) |
|
Для процессов абсорбции рабочая линия располагается выше |
|
равновесной, причем отношение тангенсов угла наклона |
рабочей |
|
и |
равновесной линий соответствует абсорбционному фактору А = |
|
= |
wm/mwr. На диаграмме у — х при фиксированном составе жидкой |
фазы х отрезок ординаты между рабочей и равновесной линией равен движущей силе массопередачи у — у*.
В дифференциальной форме уравнение рабочей линии имеет вид:
Г |
1 |
( |
d L |
dG |
\ ~ ] |
(11,55) |
d y / d x = L/C l i + |
— |
[ х |
- |
- у — |
) J |
Аппараты с непрерывным контактом фаз
Расчет рабочей высоты Н (или объема) |
аппарата |
проводят или |
с использованием уравнения массопередачи, |
в которое вводит сред |
|
няя движущая сила процесса Дср |
|
|
7 = wrS {у\. —у2) = Кта Дср |
(И ,56) |
|
или непосредственно по уравнению |
|
|
JI = N olhor |
|
(11,57) |
где TVor и h0r — соответственно число единиц переноса и высота единицы пере носа, отпесенные к концентрации компонента в газовой фазе; S — поперечное сечение абсорбера, м2; шг — приведенная скорость газа, м/ч.
Высота единицы переноса hor характеризует интенсивность массообмена в аппарате, будучи связана с коэффициентом массопередачи соотношением
Wr
h°r = -K ZT |
(!Ь58) |
Число единиц переноса Nor определяет степень извлечения ком понента. Если пренебречь изменением объема газа по высоте аппа рата и считать величину К г постоянной, то
_ |
Vi |
_dy__ |
К гаН |
|
|
Г |
(11,59) |
||||
' |
J |
|
У—У* |
Wr |
|
|
|
||||
|
Уш |
|
|
|
Величина iVor связана со средней движущей силой соотношением
Nor = ~JACp 2 |
(II.60) |
Из уравнения (11,60) следует, что число единиц переноса есть безразмерная величина, определяемая отношением изменения кон центраций (от у ± до у 2) к средней движущей силе. Для объема аб сорбера, в котором изменение концентрации равно средней движу щей силе, величину Nor можно считать равной единице. Движущая сила и число единиц переноса могут быть выражены через состав жидкой фазы. Числа единиц переноса Nor и Nomсвязаны между собой соотношением
N or = A N ож |
(11,61) |
где А — массообменный (абсорбционный) фактор, |
равный |
А = и>ж/(тшг) |
(11,62) |
Если расчет ведут по уравнению массоотдачи, то, например, для газовой фазы число единиц переноса Nr следует выразить через коэффициент массоотдачи рг и концентрацию на границе раздела у р:
|
dy |
Era# |
(11,63) |
|
|
У“ Ур |
wr |
||
|
|
|||
Числа единиц переноса Norj Nr и |
связаны между собой на |
|||
основе аддитивности фазовых сопротивлений |
|
|||
1 |
1 . |
1 |
(11,64) |
|
N or |
Nr + |
ANm |
||
|
При изменении состава жидкой фазы от х2до хх и соответственна состава газовой фазы от ух до у %определение Nor сводится к вычис лению интеграла из уравнения (11,59). Для этой цели строят график зависимости подынтегральной функции 1 /(у — у*) от у и находят площадь, ограниченную построенной кривой, осью абсцисс и орди натами, соответствующими значениям у± и у 2. Найденная площадь (с учетом масштаба) есть число единиц переноса Nor. Тогда средняя движущая сила будет равна
Аср — |
У1 — У2 |
Уг —Уа |
(11,65) |
N ог |
dy |
||
|
|
|
|
|
|
I У —У* |
|
Число единиц переноса может быть найдено и методом численного интегрирования, когда на диаграмме у — х отрезок ординаты между Ух и У2 разбивают на несколько равных участков. В простейшем слу чае при разбивке на два участка Nor следует рассчитывать по фор муле
No |
У1 — У2 |
(П,66) |
( ^ г + т + 4 г) |
где Дх, А и Д2 - движущие силы, соответствующие начальному, промежуточ ному и конечному значению у.
При линейной равновесной зависимости среднюю движущую силу можно рассчитывать аналитически
(г/1 —yt) — (^а—Уа) |
(11,67) |
|
Аср — |
у\ |
|
Уг |
|
|
2,3 lg |
|
|
У2—У2
При заметном отклонении равновесной зависимости от линейной
использование |
среднелогарифмической |
движущей |
силы |
приводит |
||||||||
к значительной |
ошибке. В |
этом случае рекомендуется |
разбивать |
|||||||||
2,5 |
|
|
|
общий |
интервал |
изменения |
кон |
|||||
|
|
|
центраций |
на |
отдельные участки, |
|||||||
|
|
|
|
|||||||||
|
X1 |
l i y |
/ |
для каждого из которых определя |
||||||||
h5 |
ют число единиц переноса. |
То же |
||||||||||
|
|
|
рекомендуется |
и |
в случае |
значи |
||||||
с* |
|
а |
|
|||||||||
|
|
тельной криволинейности |
рабочей |
|||||||||
ta |
|
|
||||||||||
*0,5 |
|
|
|
линии. |
|
|
метод |
[17] |
расчета |
|||
|
|
|
Описанный |
|||||||||
|
|
3,0 |
чо |
абсорберов |
достаточно точен, если |
|||||||
|
|
процесс можно рассматривать как |
||||||||||
- 0,5 |
!/Л |
_ L |
|
изотермический, |
а |
коэффициент |
||||||
|
|
|
|
массопередачи |
постоянным. |
Эти |
||||||
Рис. II-7. Зависимость констант |
а, |
условия, как |
правило, |
выполня |
||||||||
6 , с, d, g, h от абсорбционного фак |
ются |
при |
физической абсорбции, |
|||||||||
тора А по данным |
[24]. |
|
так как теплота |
растворения сра |
||||||||
ские свойства жидкости и газа |
внительно |
невелика, |
|
а |
физиче |
|||||||
несущественно изменяются по вы |
||||||||||||
соте аппарата. |
|
|
|
|
|
|
|
|
|
|
|
|
Влияние продольного перемешивания фаз на эффективность |
||||||||||||
массопередачи. В реальных условиях в аппаратах имеет место |
про |
дольное перемешивание потоков газа и жидкости, приводящее к вы равниванию концентраций по высоте массообменного устройства и, следовательно, к уменьшению движущей силы процесса.
Предложены [23 — 25] упрощеппые методы расчета, позволяющие оценить снижение эффективности протнвоточного абсорбера в зависимости от величины Вог и Вож. По методу Миякп и Вермелепа [23] спачала определяют фиктив ное число единиц переноса N 0r, ф, т. е. рассчитанное по движущей силе для истин ного противотока при фактическом его отсутствии. Рассчитанная по величине ЛУог,ф с помощью известных уравнении для истпппого противотока высота ан-
парата будет заниженной. Поэтому нужно определить истинное число единиц, переноса, используя уравнение
1 |
1 |
1 |
(1 1 ,68)- |
N ог, ф |
ЛГог |
“Ь N. |
|
|
|
or, D |
|
где N or D —число единиц переноса, учитывающее влияние продольного пере мешивания и определяемое из соотношения (для А Ф 1)
|
|
N or, D |
|
|
|
Ф -f- В о ж , прив |
(11,69)* |
|
Приведенный критерий Боденштейна |
В о ж ,прив является функцией |
|
||||||
|
|
Вог = |
wrff |
и Вож = |
|
|
||
|
|
vrD r |
|
|
||||
|
|
1 |
|
|
1/А |
___ 1 __ |
(11,70> |
|
|
|
Вож» прив |
|
/г В О г + |
/ ж В о л |
|||
где |
vr и |
иж — газосодержание |
и |
количество |
удерживаемой жидкости, |
мэ/м3;_ |
||
Dr |
и £ ж — эффективный коэффициент |
продольного перемешивания в газе к- |
||||||
жидкости, |
м2/ч; Н — высота |
аппарата, м. |
|
|
||||
|
Поправочные множители Ф, /г и / ж представляют собой следующие эмпири |
|||||||
ческие функции: |
|
|
|
6,8(1М)-о.в |
|
|||
|
|
, |
|
Лог + |
|
|||
|
|
/ г |
-^ог + |
6 ,8 (1М)-1.5 |
|
|||
|
|
|
|
^ог + |
6,8(1М )-0.5 |
|
||
|
|
/ ж = |
^ ог+6,8(1М )0,5 |
|
||||
|
|
|
|
|
|
0.05________ |
|
|
|
|
|
|
(НА .JV0r)0-6B o ^ « pHB |
|
|||
|
Поскольку в уравнения (11,68)—(11,70) величина N or входит в неявном виде», |
расчет ведут методом последовательных приближений. Найденное в результатарасчета отношение N 0r/N0Tt фпоказывает, во сколько раз должна быть увеличена
высота аппарата, рассчитанная по величине Л^ог.ф. |
потоков, |
|
По |
методу Слейчера [24] влияние продольного перемешивания |
|
учитывают с помощью уравнения: |
|
|
= |
вогВож {вогВож+ЛГог [аВог+Ь В ож+ с / В о гВож —d V Вог+ |
Вож+ |
|
+ £ (Вог— Вож) e-ftwor]} |
(Ц,71) |
Зависимость коэффициентов д, 5 , с, d, g и h от абсорбционного фактора пред ставлена на рис. II.7.
Аппараты со ступенчатым контактом фаз
Число тарелок в массообменном аппарате зависит от организации потоков газа и жидкости, абсорбционного фактораг заданной степени извлечения компонента и эффективности массообмена одной та релки. В табл. II.3 приведены формулы [26], позволяющие рассчи тать число тарелок.
Схема^вижения |
Расчет через состав |
Расчет через состав |
|
потоков газа |
|||
газовой фазы |
жидкой фазы |
||
и жидкости |
|||
|
|
||
Противоток |
|
|
|
П ерекрестный |
|
1|){1п [1 + ( 4 - 1 ) Д ж ] } - 1 |
|
ток |
|
|
П р и м е ч а н и е . В таблице приняты следующие обозначения:
1 —а—ег
|
£= 1п А |
(1—а) Л —ег ’ |
|
|
||
|
^ = In |
* |
&Аеж . |
|
|
|
a=vllvi, |
|
!-Э 8ж |
’ |
|
|
|
f>=*2/(xa —*х); |
|
|
||||
e r = |
(l/i— V*)/z/i; |
вж = (х2— х , ) / х 2; |
|
|
||
^/i и г/.—состав газа в нижнем |
и верхнем |
сечении |
аппарата; |
xt |
и х2—-состав жидкости |
|
в нижнем и верхнем сечении аппарата; у2 и —составы газа |
и |
жидкости, равновесные |
по отношению к составам соответственно х2 и у и
В формулы, приведенные в табл. И-З, входят коэффициент извле чения для тарелки ф и коэффициент обогащения для тарелки Е. Коэффициенты извлечения для п-ой тарелки по газу и жидкости при противотоке определяются следующим образом (нумерация тарелок по ходу газа):
Уп— Уп+1
фг — |
* |
(11,72) |
|
Уп - У п +1 |
|
ф ж — |
хп--- ХП+1 |
( П . 7 3 ) |
* |
Хп ХП+1
В табл. II-4 приведены формулы [26], рекомендуемые для рас чета фг и фж тарелок при противотоке в зависимости от режима движения жидкости и газа, абсорбционного фактора и числа единиц переноса.
Формулы, приведенные в табл. Н-4, могут быть использованы и при расчете коэффициента извлечения в аппаратах с непрерывным контактом фаз.
При перекрестном токе коэффициент обогащения по газу (или коэффициент полезного действия по Мерфри [17]) следует рассчиты вать по уравнению [26]
Е г = |
Кц/А + Вож/2) е-1 ah е ехр ( - |
Вож/2) + |
|
Уп — Уп |
|
|
-г ch 6 ехр ( — Вож/2) — 1] |
(11,75) |
Таблица II-4.
Режимы движения газа и жидкости
Полное |
вытеснение |
|
газа |
и жидкости |
|
Полное |
перемеш ива |
|
ние газа и жидкости |
||
Полное |
вытеснение |
|
газа и полное пе |
||
ремешивание ж ид |
||
кости |
|
|
Полное |
перемеш ива |
|
ние |
газа и |
полное |
вытеснение |
ж идко |
|
сти |
|
|
Коэффициенты извлечения по газу и жидкости для тарелки при противотоке
|
ФГ |
Фж |
. 1 — ехр (1/А — 1) N 0r |
1 — ехр ( А — 1) No-ж |
|
А — exp (1/А — 1) N 0r |
1 — Л ехр (А — 1) N ож |
|
|
A N0r |
Nож |
A (i + |
N 0r) + N or |
1 + (1 + Л)ЛГ0ж |
. |
1 — ехрЛ^ог |
1 — ехрЛЛ^ож |
1 — (1 + Л)ехрЛГ0Г |
1 — (1-(-Л )ехр4Л С 0Ж |
|
1—ехр (Nor/ А) |
1 — expiVoiK |
|
А — (1 + 4 ) ехр (Nor/А) |
А — (1 + А) ех р Nож |
П р и м е ч а н и е . Между коэффициентами извлечения <рг и <рж существует соотно шение
фг *=эА<рж |
(11,74) |
где
ч / |
Вож , В°ж |
, |
ЛГ |
ч |
е= у |
ч\—д-Н ----4— > |
Л — 1 — exp (—N0T) |
||
При полном перемешивании жидкости (Вож = |
0) величина Ег = |
|||
= rj. При полном |
вытеснении жидкости *(Вож = |
оо) |
||
|
Ег = А [ехр (г)/Л) — 1] |
|
(11,76) |
Сравнение различных способов абсорбции показывает, что при одинаковых значениях числа единиц переноса и абсорбционного фактора наибольший коэффициент извлечения достигается при противотоке, наименьший — при полном перемешивании жидкости и газа. Различие возрастает с уменьшением значения абсорбционного фактора А.
При противотоке минимальный расход абсорбента рассчитывают по формуле [17]:
(L/G) mjn=™<p |
(11,77) |
Поскольку <р <J1, то из (11,77) видно, что минимальный расход абсорбента достигается при А <] 1. При этом необходима бесконечно большая поверхность контакта фаз: на диаграмме у — х этот слу чай соответствует соприкосновению рабочей линии и линии равнове сия (движущая сила процесса минимальная).
При заметном отклонении рабочей и равновесной линии от ли нейной зависимости расчет (L/G)min можно также вести по формуле
(II, 77), но лишь для отдельных участков аппарата. Тогда мини мальное значение LIG [для аппарата] часто определяется по (L/G)min, найденному для «критического» сечения, расположенного в средней части аппарата.
ТЕОРЕТИЧЕСКИЕ ОСНОВЫ КИНЕТИКИ АБСОРБЦИИ, ОСЛОЖНЕННОЙ ХИМИЧЕСКОЙ РЕАКЦИЕЙ
При протекании в жидкой фазе химической реакции абсорбиру емый компонент полностью или частично связывается в химическое соединение. Градиент концентраций у поверхности раздела увели чивается. Скорость поглощения возрастает по сравнению со скоро стью поглощения при физической абсорбции. Обычно [13, 14, 17, 27—29] увеличение скорости поглощения в хемосорбционном про цессе учитывают путем введения в уравнение массоотдачи в жидкой фазе коэффициента ускорения х, показывающего, во сколько раз при химической абсорбции возрастает коэффициент массоотдачи по сравнению с коэффициентом массоотдачи при физической абсорб ции (при одинаковой движущей силе, равной движущей силе про цесса хемосорбции)
7— |
(Ар — Аж) — Ржа (Ар |
Аж) |
(11,78) |
||
где Рж — коэффициент массоотдачи |
в жидкой |
фазе при хемосорбции; Ар я |
|||
А ж — концентрация передаваемого |
компонента |
соответственно на |
границе |
||
раздела и в основной массе жидкости. |
|
|
|
||
Коэффициент массоотдачи |
Рж связан |
с |
коэффициентом |
массо- |
|
передачи при хемосорбции К'г следующим соотношением: |
|
||||
|
l/X '^ l/P r+ ^ j/Рж |
|
<п ’79) |
где nij — константа фазового равновесия для физической абсорбции с поправ кой на ионную силу раствора»
На коэффициент массоотдачи Рж оказывает прямое или косвенное влияние целый ряд гидродинамических, физико-химических и гео метрических факторов. В зависимости от условий ведения: процесса и его аппаратурного оформления относительная роль этих факторов
существенно |
изменяется. |
|
|
|
Расчет скорости поглощения j при абсорбции, сопровождаемой |
||||
химической |
реакцией типа |
А + тгВ |
Е + |
F произвольного по |
рядка а по |
абсорбируемому |
компоненту А, |
порядка р (0; 1; 2) по |
хемосорбенту В и первого порядка по каждому из продуктов реак ции Е и F, рекомендуется вести по приближенному уравнению [29]:
|
|
м |
(Кх+ ТУВж) |
Уг |
7 = Ржа |
|
К 2е~г |
||
(1 |
—л) |
мвж |
(Ар А >к) |
|
|
(Х2+Т\ГВЖ) т г Ь ” * |
Этим уравнением можно воспользоваться, если известны коэффициент массоотдачи при физической абсорбции рж, удельная поверхность контакта фаз а, движущая сила процесса Ар — А ж п безразмерный коэффициент ускорения х (равный выражению в фигурных скобках). В уравнении (11,80) М = В ж!пАр\
А ---- Лр/Лж; Z= (К 1 — К 2) х/и>ж = (ЛГ, — К 2) 4 /я .Д Л/р^; |
В ж —концентра- |
|
ция свободного хемосорбента в основной массе |
жидкости |
(в кмоль/м3); К х |
и Кг — корпи характеристического уравнения, |
равные |
|
К ъ а= - N J 2 ± V ( N XI2 ) ^ - N 2N |
(11,81) |
(значения, коэффициентов N , N x и N 2 даны в табл. П-5); ЕЖ1 Рж — концентра ции продуктов реакции в осповной массе жидкости (в кмоль/м3); гп и го — кон станта скорости прямой и обратной реакции, п — стехиометрический коэффи циент.
Таблица Л-5. Значения коэффициентов в характеристическом уравнении (11,81)
Значе |
|
|
|
|
|
|
|
ния |
N |
|
|
Ni |
N* |
|
|
Р |
|
|
|
|
|
|
|
0 |
Гр |
~ ~ |
(2#ж |
пЕж-|- n'Fm) -Ь |
- п г пЛ « + |
^ Х |
|
п |
|||||||
|
|
|
|
X {Вж-\-пВжЕж.-\-пВжЕж-\- |
|||
|
|
|
|
|
|||
|
|
|
|
|
+ n2B x Fж) + ВЖЬ |
||
1 |
Гр |
|
ПГпА9 + ' Т Х |
^ ( В * т + п В жЕж + |
|||
п |
|
||||||
|
|
|
|
||||
|
|
X (2Вж+ пЕж-f- nFж) + Ь |
-{-пВжРж-\-п2ЕжРж} -\-ВжЬ |
||||
2 |
Гр _ |
~ |
(2 # ж + |
пЕж-\-пРж)-\-Ь |
*“ (Вж4~ пВжЕж+ пВжрж + |
||
п |
|||||||
|
|
|
|
|
|
||
|
— пгпА* |
|
|
|
+ п2ЕжР |
-]- ВЖЬ |
П р и м е ч а н и е . Ь = -а ^ 1
Расчет коэффициента ускорения и скорости абсорбции может быть выпол нен для произвольного сочетания концентраций реагентов при условии, что \К2\ > | К х |. Результаты расчета по уравнению (11,80) хорошо согласуются с результатами решения системы уравнений конвективной диффузии, получен ными [30] с помощью ЭВМ. Коэффициент ускорения х зависит от скорости химической реакции и степени турбулизации жидкости. В предельных случаях возможны существенные упрощения. В табл. II-6 приведены уравнения, реко мендуемые для расчета коэффициентов ускорения в конкретных технологиче ских процессах.
При больших значениях параметра я (большая величина константы равно весия химической реакции) уравнение (11,80) описывает кинетику абсорбции, осложненной необратимой реакцией [31]. Химическая реакция протекает в реакционно-диффузионной зоне, непосредственно примыкающей к поверх ности раздела.
Коэффициент ускорения х при необратимой реакции можно рассчитать как по уравнению (1 1 ,84), приведенному в табл. П-6 , так п с помощью более точного уравнения [32]
2 { м / е +i)
(11,90)
1 -|-1 Л + 4 {M VQIR?
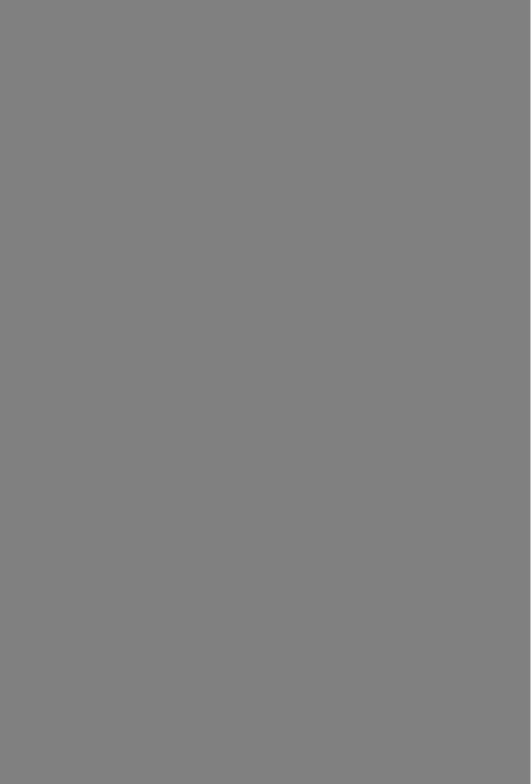
Гидродинамический |
Характеристика |
Пример процесса |
режим |
химической кинетики |
Произвольной ин Скорость реакции произ Поглощение С02 водными тенсивности вольная растворами поташа (п =
= 2 , а = Р = 1 )
Слабо или умеренно |
Скорость обратной реакции |
Поглощение |
С02 |
водными |
||||||||
развитый |
сравнительно невелика |
растворами |
моноэтанол- |
|||||||||
|
|
|
|
|
|
|
амина при |
высоких |
сте |
|||
|
|
|
|
|
|
|
пенях карбонизации {п = |
|||||
|
|
|
|
|
|
|
= 2, а = Р= 1) |
|
|
|
||
То же |
|
Необратимая реакция |
пер |
Поглощение |
С02 |
водными |
||||||
|
|
вого |
порядка |
по |
хемо |
растворами |
моноэтанол- |
|||||
|
|
сорбенту |
|
|
|
амина |
при |
умеренных |
||||
|
|
|
|
|
|
|
степенях |
карбонизации |
||||
Слабо развитый |
|
|
|
|
|
(л = 2 , а = Р — 1 ) |
|
|
||||
Мгновенная |
необратимая |
Поглощение |
NH3 |
серной |
||||||||
|
|
реакция |
|
Лж^ 0 ; |
к и с л о т о й |
(/г = 1 / 2 ; |
а = |
|||||
|
|
Вж |
А к, крит) |
|
|
= (3 = 1 ); поглощение H2S |
||||||
|
|
|
|
водным раствором диэта |
||||||||
|
|
|
|
|
|
|
||||||
|
|
|
|
|
|
|
ноламина |
при |
высоком |
|||
|
|
|
|
|
|
|
содержании |
H2S |
в |
газе |
||
|
|
|
|
|
|
|
(и = а = р = |
1 ) |
|
|
|
|
Умеренно или силь |
Мгновенная |
необратимая |
Поглощение серного анги |
|||||||||
но развитый |
реакция |
на поверхности |
дрида серной^кислотои |
|||||||||
|
|
ЖИДКОСТИ (Вж^Вж. Крит) 1 |
|
|
|
|
|
|
||||
|
|
сопротивление |
в газовой |
|
|
|
|
|
|
|||
Умеренно |
развитый |
фазе |
|
|
|
|
Поглощение С02 |
раствором |
||||
Необратимая реакция пер |
||||||||||||
|
|
вого |
или |
второго поряд |
NaOH |
(при избытке |
ще |
|||||
|
|
ка по хемосорбенту при |
лочи) |
(п = 2 , a = P = i) |
||||||||
|
|
избытке |
хемосорбента |
|
|
|
|
|
|
|||
|
|
(М > 5 Д ; |
Лж ~ 0 ) |
|
|
|
|
|
|
|
||
То же |
|
Необратимая реакция ну |
Поглощение кислорода вод |
|||||||||
|
|
левого порядка по |
хемо |
ным раствором сульфита |
||||||||
|
|
сорбенту |
|
|
|
в присутствии соли |
меди |
|||||
|
|
|
|
|
|
|
(п = 2 , a = 1 ч-2 , Р = 0) |
|||||
» |
|
Необратимая реакция |
вто |
|
— |
|
|
|
||||
|
|
рого |
порядка |
по |
хемо |
|
|
|
|
|
|
|
|
|
сорбенту |
|
|
|
|
|
|
|
|
|
|
» |
|
Реакция существенно обра |
|
— |
|
|
|
|||||
|
|
тима |
|
|
|
|
|
|
|
|
|
|
5 Заказ |
1460 |
|
|
|
|
|
|
|
|
|
|
65 |
Из (11,90) следует, что коэффициент ускорения является функцией кинетиче ского Л, стехиометрического М и диффузионного 0 параметров
|
R —r f a _j_i rnBmDAAv |
^ |
АГ = Лж/лАр |
|
Q= DBIDA |
Для расчета х при необратимой реакции (при D в *=^ВА) можно пользоваться
также графиком зависимости к от R и М [17]. В области значений Л, значи тельно превышающих М (по Рамму [17] Л > 5Л/), х не зависит от Л и опреде ляется по уравнению (11,85). В таких условиях достигается максимальное зна чение х, уже не зависящее от гп; эта область называется областью протекания очень быстрой (мгновенной) необратимой химической реакции в жидкой фазе. Скорость абсорбции зависит главным образом от гидродинамических условии и рассчитывается по уравнению
;' = Рж“ (1 -\-M Vo) Ар |
(11,91) |
которое применяется при условии, что Лж <С.ВЖ. крКритическую концентрацию хемосорбента В ж. кр определяют из уравнения
в ж, кр— Q |
li_ |
л = - .nL, |
(11,92) |
Рж |
Г 6°Рж |
|
|
При В ж ^ Лж. Кр реакция также протекает мгновенно, |
но уже на поверх |
ности раздела фаз, поэтому все сопротивление массопередаче оказывается со
средоточенным |
в газовой фазе. |
В области |
значений Л/, бблыпих по сравнению с Л (по Рамму [17] М > |
•> 5Л), величина х не зависит от М и х « Л. Тогда
( и ’ 9 3 >
Такой случай соответствует умеренно быстрым и средним скоростям необра тимой химической реакции; процесс не зависит от гидродинамических условии. Область работы может быть названа областью протекания реакции кажущегося суммарного порядка а, так как концентрация свободного хемосорбента, зна чительно превышающая концентрацию абсорбируемого компонента (Лж А р), практически не изменяется вблизи поверхности раздела фаз.
Приведенные выше теоретические уравнения хемосорбции получены в пред положении, что если имеет место вторая (последовательная) реакция, где расхо
дуется вторая молекула хемосорбента (я = 2 ), то |
она |
протекает мгновенно. |
Это наблюдается, например, при взаимодействии |
С 02 |
с моноэтаноламином. |
Если же промежуточное вещество существует относительно долго, зависимость х от Л проходит через максимум [33].
Экспериментальная проверка теоретических уравнений необратимой хемо сорбции проведена [14, 28, 34—39] на примерах поглощения С 02 водными рас творами NaOH, КОН, NH4OH, МЭА, ДЭА в аппаратах с фиксированной по верхностью раздела (в широком диапазоне значений М и Л).
Удовлетворительное соответствие найденной опытным путем и теоретиче ски рассчитанной скорости абсорбции позволяет рекомендовать уравнение (11,90) для инженерной практики.
При расчете коэффициентов ускорения процесса абсорбции, осложненной
обратимой химической реакцией, следует использовать уравнения (11,82), (11,83) и (11,89), приведенные в табл. П-6 . Значения функции
|
|
Yz |
|
|
о |
могут быть взяты из |
работ [17, |
34]. |
' С увеличением |
обратимости |
химической реакции уменьшается скорость |
взаимодействия абсорбируемого компонента и хемосорбента и возрастает глу бина проникновения абсорбируемого компонента. Химическая реакция выходит за пределы пограничного реакционно-диффузионного слоя и охватывает всю массу жидкости. Для массопередачи с обратимой реакцией характерно такое состояние, когда А ж заметно больше нуля и существенно зависит от количества жидкости в аппарате уж. В зависимости от степени турбулизации жидкости, константы равновесия К и иж можно рассматривать две предельные области: диффузионную (отношение А Ж/А р незначительно) и кинетическую (Аж/А р ^ 1 ).
Аналитическое определение состава основной массы жидкости (особенно Аж) связано часто с большими трудностями. Поэтому для практических расчетов уравнение массоотдачи следует рассматри вать совместно с другими уравнениями (уравнение скорости химиче ской реакции в основной массе жидкости, уравнение закона дейст вующих масс и др.).
При протекании сравнительно медленной химической реакции концентрация абсорбируемого компонента в жидкости Ажможет значительно превышать равновесную концентрацию А ж, что на блюдается, например, при поглощении С 02 растворами поташа или моноэтаноламина при высоких степенях карбонизации [14, 29, 40]. Поэтому скорость поглощения следует рассчитывать по уравнению (II, 80), подставляя фактическую движущую силу Ар — Аж, соот ветствующую истинному градиенту концентраций у границы раздела фаз, а не Ар — А ж. В этом случае можно использовать значения Рж> рассчитанные теоретически или определенные с помощью теории
подобия. Применяют также экспериментальные методы определе ния Рж.
При соизмеримости фазовых сопротивлений величину Ар опреде ляют совместным решением уравнения массоотдачи в жидкой фазе
(II, 78) и уравнения |
|
/ = Рг® {Аг — mj^p) |
(11,94) |
где Ат — концентрация передаваемого компонента в газе, кмоль/м3.
В химической и газовой промышленности широко распространена одновременная хемосорбция двух компонентов газа. Теория кине тики необратимой двухкомпонентной хемосорбции подробно рас смотрена в работах [41—43].
Для использования теоретических уравнений хемосорбции не обходимо знать значения ряда параметров. Хотя в настоящее время нет достаточно полных данных для расчета некоторых из них, теория хемосорбции позволяет во многих случаях установить ка чественное и полуколичественное влияние того или иного фактора
на скорость поглощения. Для таких важных технологических про цессов, как, например, абсорбция СО2 моноэтаноламином, селектив ная абсорбция СО2 и H 2S растворами МЭА и ДЭА и другие, уже имеются достаточно точные-методы расчета, подтвержденные опытом работы промышленных аппаратов.
Литературные данные об экспериментальных значениях рж можно использовать только в том случае, если хемосорбция не сопрово ждается поверхностной конвекцией (или если коэффициент массоотдачи рж определен при одновременном с физической абсорбцией протекании хемосорбции [44]). Сущность поверхностной конвекции заключается в возникновении и развитии в непосредственной бли зости к поверхности раздела фаз конвективных токов, значительно ускоряющих процесс как физической абсорбции, так и хемосорб ции.
Одной из причин возникновения конвективных токов являются продольные градиенты поверхностного натяжения, а также гра диенты плотности, появляющиеся при протекании хемосорбции. Явление поверхностной конвекции было обнаружено [20, 22, 37—39] при поглощении С 02 водными растворами МЭА, ДЭА и др. Поверх ностная конвекция наблюдается в пленочных и насадочных аппара тах [20], в ламинарных струях жидкости [42]; в барботажных ап паратах ее влияние на массопередачу сравнительно невелико. Из сказанного выше следует, что коэффициент физической массоотдачи рж должен быть определен при протекании хемосорбционного
процесса, |
т. е. в идентичных гидродинамических |
условиях. Если |
объектом |
исследования является поглощение С 02 |
хемосорбентом, |
то величину рж удобно определять по методу [36, 37], заключающе муся в десорбции N 20 из раствора хемосорбента. Поскольку коэф фициенты диффузии N 20 и СО2 близки, то близки между собой и
Рж, N*0 и Рж, С02-
Ускорение массопередачи за счет поверхностной конвекции Р необходимо учитывать при подборе новых хемосорбентов. Протека ние химическЪй реакции оказывает существенное влияние на динамическое поверхностное натяжение, т. е. на поверхностное натя жение, измеренное непосредственно при протекании химической реакции.
Динамическое поверхностное натяжение можно определить мето дом горизонтальной колеблющейся, струи жидкости [45, 46]. Путем обработки опытных данных установлено, что ускорение Р скорости массопередачи за счет поверхностной конвекции можно оценивать в зависимости от продольного градиента динамического поверхност ного натяжения с помощью уравнения:
Р = 1 + 0,282 (Д оди н /А *)8'2 |
(11,05) |
С помощью теоретических уравнений хемосорбции можно опре делить влияние различных факторов на кинетику поглощения.
Скорость жидкости влияет на коэффициент массопередачи через коэффициент массоотдачи рж. Величина рж, а также К'г (при условии,
что сопротивлением в газовой фазе можно пренебречь) пропорцио нальна скорости жидкоЛги в степени га, причем максимальное зна чение га достигается в области мгновенной химической реакции. При переходе в область реакции псевдопервого порядка влияние скоро
сти |
уменьшается |
(га->■ 0). |
Экспериментальные |
|
данные |
[47—50] |
|||||||||||||||||
подтверждают |
теоретические предпо |
|
|
|
|
|
|
|
|
|
|||||||||||||
сылки. |
|
|
|
|
|
|
|
|
|
|
|
|
|
|
|
|
|
|
|
||||
|
Влияние скорости газа на К'г про |
|
|
|
|
|
|
|
|
|
|||||||||||||
является |
при |
заметном |
|
увеличении |
|
|
|
|
|
|
|
|
|
||||||||||
сопротивления |
процессу |
массопере- |
|
|
|
|
|
|
|
|
|
||||||||||||
дачи |
|
в |
газовой |
фазе; |
доля сопро |
|
|
|
|
|
|
|
|
|
|||||||||
тивления |
в |
газовой фазе возрастает |
|
|
|
|
|
|
|
|
|
||||||||||||
при повышении давления. Скорость |
|
|
|
|
|
|
|
|
|
||||||||||||||
газа может оказывать заметное вли |
|
|
|
|
|
|
|
|
|
||||||||||||||
яние на поверхность контакта фаз, |
|
|
|
|
|
|
|
|
|
||||||||||||||
что нередко выражается в сильной |
|
|
|
|
|
|
|
|
|
||||||||||||||
зависимости объемного коэффициента |
|
|
|
|
|
|
|
|
|
||||||||||||||
массопередачи |
К'га от |
скорости |
га |
|
|
|
|
|
|
|
|
|
|||||||||||
за, |
как, |
например, в насадочных ко |
|
|
|
|
|
|
|
|
|
||||||||||||
лоннах в режиме додвисания или в |
|
|
|
|
|
|
|
|
|
||||||||||||||
условиях |
барботажа |
особенно |
при |
|
|
|
|
|
|
|
|
|
|||||||||||
малых скоростях |
газа. |
|
|
|
|
|
|
|
|
|
|
|
|
|
|
||||||||
|
Парциальное |
давление |
компо |
Рис. II-8 . Зависимость скорости |
|||||||||||||||||||
нента |
в |
соответствии |
с |
теоретиче |
|||||||||||||||||||
абсорбции |
СОо |
водным |
раство |
||||||||||||||||||||
скими |
уравнениями необратимой хе |
ром МЭА |
(3 кмоль/м3) от темпе |
||||||||||||||||||||
мосорбции влияет на Рж и К'г только |
ратуры |
(данные |
|
Аксельрода |
и |
||||||||||||||||||
в |
области |
мгновенной |
|
химической |
Морозова для пленочной колонны |
||||||||||||||||||
реакции. |
При |
М > |
1 |
величина |
Рж |
диаметром |
0,0185 |
м |
и |
высотой |
|||||||||||||
|
|
|
1 м): |
|
|
|
|||||||||||||||||
обратно |
пропорциональна |
парци |
1 — степень |
карбонизации |
0,11 моль/ |
||||||||||||||||||
альному |
давлению (при отсутствии |
моль; |
2 — степень |
|
карбонизации |
||||||||||||||||||
0,24 моль/моль; з — степень карбони |
|||||||||||||||||||||||
поверхностной конвекции). При |
раз |
зации |
0,41 моль/моль. |
|
|||||||||||||||||||
витой поверхностной конвекции, ин |
|
|
|
|
|
|
|
|
|
||||||||||||||
тенсивность которой, |
как |
указывалось выше, |
увеличивается с |
по |
|||||||||||||||||||
вышением |
парциального |
давления |
компонента |
А Г1 |
зависимость |
||||||||||||||||||
Рж от А т проявляется слабее. |
В |
переходной |
области |
|
влияние пар |
||||||||||||||||||
циального |
давления |
постепенно |
уменьшается |
и сводится к нулю в |
|||||||||||||||||||
области |
реакции псевдопервого порядка, что согласуется с опыт |
||||||||||||||||||||||
ными данными |
[47, 48, 50, 51]. |
|
|
|
|
|
|
|
|
|
|
|
|||||||||||
|
Концентрация |
свободного хемосорбента Вж влияет на |
Рж |
как |
|||||||||||||||||||
в |
области |
мгновенной |
химической |
реакции |
(причем |
если |
М » |
1 , |
|||||||||||||||
то |
|
рж ~ |
Вж), так и в области реакции псевдопервого порядка, |
||||||||||||||||||||
где |
Рж |
Вж*. |
|
|
повышении концентрации |
хемосорбента |
ве |
||||||||||||||||
|
При |
значительном |
личина Рж, а следовательно, и К'г уменьшается, что объясняется воз растанием вязкости раствора и уменьшением эффекта поверхност ной конвекции. От концентрации хемЪсорбента зависит также ионная сила раствора и, следовательно, константа фазового равнове сия
Температура влияет на коэффициент массоотдачи |3ж и движу щую силу процесса. С повышением температуры увеличивается ко эффициент массоотдачи. В области мгновенной химической реакции
это объясняется возрастанием Рж и уменьшением Ар |
[уравнение |
|
(II, 91)]; |
в области реакции псевдопервого порядка |
увеличение |
Рж можно |
объяснить заметным ростом значений гп и D А [см. урав |
|
нение (II, |
93)]. |
сила про |
С повышением температуры уменьшается движущая |
цесса; при высоких температурах процесс поглощения уже нельзя рассматривать как необратимый. В некотором интервале температур увеличение коэффициента массопередачи может опережать умень шение движущей силы процесса. При этом скорость абсорбции возрастает при повышении температуры (рис. II-8).
КИНЕТИЧЕСКИЙ РАСЧЕТ АБСОРБЕРОВ ДЛЯ ПРОЦЕССОВ С ХИМИЧЕСКОЙ РЕАКЦИЕЙ
В отличие от физической абсорбции при хемосорбции заметно изменяется по высоте аппарата не только движущая сила, но и ко эффициент массопередачи, поэтому ранее описанные методы расчетов абсорберов не могут быть рекомендованы.
В настоящее время методику расчета абсорберов с необратимой химической реакцией можно считать разработанной достаточно полно [32]. При сравнительно небольшом изменении температуры по высоте аппарата процесс можно рассматривать как изотермиче ский.
Распределение концентраций У = |
А г/А Гг1 и X = В ж1ВЖу2по высоте аппа |
||
рата I = |
х/Н, а следовательно, и степень извлечения компонента определяются |
||
общим числом единиц переноса N'0T, абсорбционным фактором а = |
|||
стехиометрическим параметром |
|
||
|
М 0= |
Вж, 2mj |
|
|
пАг, 1 * |
||
|
|
||
и числом |
Боденштейна для газовой |
|
|
|
ВОг |
wrH |
|
|
vrD r |
||
и жидкой |
фазы |
||
и>жН |
|||
|
Вож |
||
|
»жОж |
где А т— текущая концентрация компонента в основной массе газа, кмоль/м3, х — текущая продольная координата, м; Н — высота абсорбера, м; wr п шж— приведенные скорости газа и жидкости, м/ч; vr и иж— газосодержание и коли чество удерживаемой жидкости; D r и — эффективные коэффициенты про дольного перемешивания в газе и жидкости, м2/ч; В ж — текущая концентрация активной части хемосорбента в основной массе раствора, кмоль/м3. Индексы «1 » и «2 » относятся соответственно к нижнему и верхнему сечению аб сорбера. В качестве ключевого компонента жидкой фазы используется хемо сорбент В. Концентрации остальных компонентов легко определяются с помощью уравнений материального баланса и констант равновесия.
Решение исходной системы нелинейных дифференциальных урав нений при произвольном соотношении диффузионных сопротивле ний в обеих фазах при условии, что коэффициент массоотдачи Рж определяется по уравнению (II, 90), было получено [32] с помощью ЭВМ М-220. При этом можно рассчитать высоту абсорбера для за данной степени извлечения
и заданной величины BMt 2 в л1рбой области необратимой хемосорб ции. Можно также определить степень извлечения при заданной высоте абсорбера. Решение позволяет быстро и достаточно точно провести анализ зависимости кинетики абсорбции от целого ряда параметров. Аналитические решения [32] могут быть рекомендо ваны для частных случаев абсорбции.
Например, для области мгновенной химической реакции при условии, что Вог = Вож ->• оо, такое решение имеет вид
1
(1--ir)y+M'o/0 (l f ^ - )
где
|
|
/В |
|
|
|
1 |
|
|
Ъ = - |
1 |
1 * 0 — Q B / D A |
|
|
N |
aN» |
При Вог оо, |
Вож -> 0 уравнение имеет вид |
||
~ |
( N r + |
<*ЛГЖ) |
In- |
Безразмерные параметры М о и Л о связаны с параметрами М х и R x для ниж него сечения абсорбера и параметрами М 2 и Л2 для его верхнего сечения сле дующими соотношениями:
Д 2 = /?0 R ^ R Q V X I Af1 = Af0X1 М а = Mo/Ya
Результаты численного решения удовлетворительно согласуются с данными опытно-промышленных испытаний насадочных абсорберов.
Расчет кинетики двухкомпонентнои хемосорбции следует проводить по ана логичной методике [43, 52], однако система исходных дифференциальных урав нений дополняется еще одним уравнением для второго компонента газа.
Если сопротивление массопередаче для первого из компонентов полностью контролируется диффузионным сопротивлением в газовой фазе, а второго — сопротивлением в обеих фазах, то селективность извлечения первого компо нента по сравнению со вторым может быть определена по уравнению
Кс = In (1 —q>i) _ |
N r, 1 |
N r |
(11,90) |
In ( 1 Ф2) |
Nr, 2 |
/2 |
|
N Ж , 2^0» 2a 2^ cp |
|
где А'с — коэффициент селективности; Х Ср = (1 + X J /2 — безразмерная кон центрация активной части хемосорбента (средняя по высоте аппарата).
Число единиц переноса JVr,i, необходимое для обеспечения заданной сте пени извлечения ф2, рассчитывается по уравнению
N г,1 = —In (! — Ф1)
Рекомендованный метод расчета массопередачи с необратимой химической реакцией может быть использован для аппаратов как с непрерывным, так и со ступенчатым контактом фаз. Во втором случае расчет следует вести последовательно от тарелки к тарелке, начиная с нижней. Для каждой тарелки определяют степень извле чения, достигаемую при высоте барботажного слоя, найдепной гидродинамическим расчетом. При расчете известна величина ^4Г, i> значением Вж2 задаются. Зная М о и R о, находят ср и А г%2 при I. = = 1 и рассчитывают величину ВЖг2 из уравнения материального баланса. Если найденное значение Вжt 2 отличается от заданного, расчет повторяют до их сходимости. После этого определяют пара метры следующей тарелки.
Расчет числа тарелок в аппарате продолжают до тех пор, пока
определенная концентрация компонента на выходе |
с n-й тарелки |
не будет меньше заданной концентрации на выходе |
из абсорбера. |
Расчет противоточных абсорберов с обратимой химической реак цией разработан только для предельных гидродинамических режи мов. Так, при полном перемешивании жидкости расчет следует ве сти по уравнению (II, 80) на конечные концентрации всех компонен тов в жидкости. Если предположить идеальное вытеснение потоков газа и жидкости, то расчет ведут последовательно, разбивая весь диапазон концентрации (от начальной до конечной) на ряд интерва лов. При расчете скорости абсорбции используют средние для дан
ного интервала |
значения концентраций. |
I |
ОСНОВЫ А П П А Р А Т У Р Н О Г О О Ф О Р М Л Е Н И Я |
|
Насадочные абсорберы |
Для очистки технологических газов большое распространение получили как в отечественной промышленности, так и за рубежом
массообмейн ые аппараты |
с нерегулярной (засыпанной навалом) на |
|
садкой [17, 18, 53, 54]. |
Такие аппараты обеспечивают |
высокую |
надежность эксплуатации |
в широком диапазоне нагрузок |
по газу |
и жидкости, что важно для агрегатов большой единичной мощности. За последние годы эксплуатационные показатели абсорберов с нерегулярной насадкой значительно повышены. Это достигнуто
за счет применения новых эффективных насадочных устройств, су щественного уменьшения отрицательного влияния поперечной не равномерности, ведения процесса в интенсивном гидродинамиче ском режиме работы, использования математических методов расчета (с применением ЭВМ) кинетики абсорбционных и хемосорбционных процессов. В настоящее время на Славянском керамическом комби
нате налажено промышленное производство седловидной насадки типа Инталокс и новой керамической насадки, разработанной ГИАП и НИИэмальхиммаш; один из заводов пластмасс выпускает кольца Палля из полипропилена.
Гидродинамические характеристики насадок заметно зависят от технологии и качества изготовления. Данные зарубежных ис следований [55—57] седловидных и кольцевых насадок весьма противоречивы; некоторые сообщения [58, 59] носят, по-видимому, рекламный характер. В табл. И-7 приведены, по данным [17, 60], характеристики отечественных керамических насадок, а также сталь ных и пластмассовых колец Палля.
Таблица II-7. Характеристики насадок
Насадка |
|
*Размер,мм |
Геометриче поверхская ность,a Q м*/м* |
Свободный объем,м*/м3 |
Эквивалент диаметр,ный м |
|
|
|
|
|
|
||
Седла типа |
Инталокс* |
|
\ |
|
|
0,0134 |
|
25 |
230 |
0,77 |
|||
|
|
|
44Г |
130 |
0,77 |
0,0237 |
Седла Берля |
|
50 |
10 0 |
0,81 |
0,0324 |
|
|
25 |
235 |
0,74 |
0,0126 |
||
Кольца Палля из поли |
50 |
1 1 2 |
0,86 |
0,0307 |
||
пропилена |
|
|
|
|
|
|
Насадка |
ГИАП |
и |
50 |
106 |
0,79 |
0,0298 |
НИИэмальхиммаш** |
|
|
|
|
|
|
Кольца Рашига |
|
25 |
190 |
0.605 |
0,01275 - |
|
Кольца Палля стальные |
50 |
93 |
0,74 |
0,0318 |
||
35 |
170 |
0,9 |
0 .0 2 1 |
|||
|
|
|
50 |
108 |
0,9 |
0,033 |
Число в 1 м*
76 600
14000
9400
70 000
6800
7400
50 600
5530
18 200
6400
Насыпная плотность, кг/м3
575
550
505
840
10 0
475
890
580
455
415
*В качестве размера седловидных насадок принято среднеарифметическ длины, ширины и высоты насадки.
**Данные Л. В. Алекперовой и А. В. Струниной
Сопротивление насадок (кроме стальных колец Палля) рекомен дуется рассчитывать по эмпирическому уравнению
АР/Н = Л0ш®Ют Re* |
(11,97) |
где АР/Н — сопротивление 1 м высоты насадочного слоя, кгс/м3; — при веденная скорость газа, м/с; Иеж — число Рейнольдса для жидкости.
Значения коэффициентов А0 и/тгдля различных насадок приве дены ниже в табл. II-8 . Уравнение (II, 97) следует при&енять при использовании жидкостей, вязкость которых не сильно отличается от вязкости воды.
При числе Рейнольдса для газа Rer > 500 режим прохождения газа через слой нерегулярной насадки автомоделей и коэффициент
сопротивления g не зависит от Rer. Для сухих седловидных насадок g = 2,6, для колец Палля g = 3, для колец Радшга g = 4,5. В пле ночном режиме сопротивление седел и колец Палля, а также насадки ГИАП и НИИэмальхиммаш меньше сопротивления колец Рапшга в 1,65—5 раз. Разница в сопротивлении уменьшается при увеличе нии размера насадки и возрастает при повышении плотности оро шения.
Преимущества седловидной насадки и колец Палля обусло влены тем, что при их использовании в значительной степени ис ключается возможность экранирования насадочных элементов, а следовательно, и создания застойных зон. Более равномерная по сравнению с кольцами Рапшга порозность уменьшает возможность каналообразования. По опытным данным [60], седловидная насадка и кольца Палля могут работать при более высоких предельных нагрузках но сравнению с кольцами Рашига. Преимущества ука занных насадок перед кольцами Рашига особенно очевидны при увеличении плотности орошения, что делает их перспективными
для процессов очистки под повышенным давлением. |
|
||||||||
Скорость газа |
wo (в м/с), соответствующую началу режима под |
||||||||
писания и захлебывания, можно |
рассчитать с помощью уравнения |
||||||||
|
( |
wl a0 |
уг |
„оде |
|
|
|
|
(11,98) |
|
h \ |
ge3 |
Уж Г'Ж h - W ' W ' |
|
|||||
|
|
|
|||||||
Таблица Ц-8. Значения коэффициентов А о, тпь Ь и с |
|
||||||||
|
|
в уравнениях |
(И,97) |
и (11,98) |
|
|
|
||
|
|
|
|
А о |
|
Начало режимаL |
Начало режима |
||
|
я |
|
|
|
подвисания |
захлебываыид |
|||
|
|
|
|
|
■ |
|
|
|
|
Насадка |
я |
(при |
|
|
|
|
|
||
а |
|
771 • 101 |
|
|
|
||||
|
V |
ДР/Лг |
(при А Р //1 |
Ъ |
|
Ь |
|
||
|
я |
в |
|
в Па/м) |
|
|
|
||
|
со |
|
|
|
|
|
|
||
|
се |
кге/м* |
|
|
|
|
|
|
|
|
А |
|
|
|
|
|
|
|
|
Седла Инта- |
25 |
20,4 |
20 0 0 0 0 0 |
1,80 |
-0 ,3 3 |
1,04 |
0,142 |
1,48 |
|
локс |
44 |
1 2 ,1 |
|
1190000 |
1,29 |
-0 ,4 9 |
1,04 |
0,085 |
1,59 |
|
|
||||||||
Седла Берля |
50 |
10 ,0 |
98070 |
0,747 |
—0,58 |
1,04 |
0,02 |
1,62 |
|
25 |
23,5 |
2310000 |
1,53 |
—0,33 |
1,04 |
0,142 |
1,48 |
||
Кольца Палля |
50 |
9,5 |
|
932000 |
0,944 |
-0 ,4 9 |
1,04 |
— |
— |
из полипропи |
|
|
|
|
|
|
|
|
|
лена |
|
|
|
834000 |
|
-0,274 |
1,16 |
|
|
Насадка ГИАП |
50 |
8,5 |
|
|
|
|
|||
и НИИэмаль |
|
|
|
|
|
|
|
|
|
химмаш |
|
|
|
|
|
|
1,04 |
—0,02 |
1,62 |
Кольца Раши |
25 |
60,3 |
|
5920000 |
2,96 |
—0,55 |
|||
га |
50 |
15,1 |
|
1480000 |
0,79 |
- 0,68 |
1,04 |
—0,02 |
1,62 |
Кольца Палля |
|
||||||||
35 |
— |
|
— |
— |
—0,073 |
1,75 |
0 ,0 2 2 |
1,75 |
|
стальные |
50 |
— |
|
— |
— |
—0,073 |
1,75 |
0 ,0 2 2 |
1,75 |
|
|
где L/G — отношение весовых нагрузок по жидкости и газу; уг/уж — отношение удельных весов газа и жидкости; р,ж!— вязкость жидкости, сП; g = 9,81 м/с2; 8 — свободный объем сухой насадки; а о — удельная геометрическая поверх ность насадки, м2/м3.
Значения коэффициентов Ъ и с приведены в табл. Н-8 и могут быть рекомендованы для расчета, если в качестве жидкой фазы
используется вода. |
|
|
-1,7 |
|
|
|
|
|
|
• |
||||||
|
Для водного |
раствора |
|
|
|
|
|
|
||||||||
|
|
|
|
|
|
|
|
|
|
|||||||
МЭА концентрацией |
2— |
|
1,6 |
|
|
|
|
|
X'* |
|
||||||
3 кмоль/м3 предельные на |
- |
|
|
|
|
/ |
|
|
||||||||
грузки на 10—15% |
ниже. |
-1,5 |
|
|
|
X/ |
|
|
||||||||
|
|
|
|
|
|
|||||||||||
Экспериментальные |
дан |
|
|
|
/ |
/ |
|
|||||||||
ные но предельным нагруз |
|
|
|
|
|
|
|
|||||||||
|
|
|
|
' |
/ |
у А |
|
|
||||||||
кам приведены на рис. И-9. |
|
|
|
|
г 0~ |
— |
||||||||||
|
Эффективность |
массо- |
|
|
|
* |
/ |
|
|
У |
|
|||||
обмена |
на седловидных |
|
|
|
|
|
|
|
|
|||||||
насадках, |
насадке ГИАП |
|
|
/ |
А |
|
|
/ |
/ \ I |
|
||||||
и |
НИИэмальхиммаш |
и |
|
|
> |
|
|
|
|
|
|
|||||
кольцах Палля [60, 61] не |
|
|
|
|
|
|
□ |
i |
|
|||||||
менее |
чем на 20 % при со |
|
|
|
|
|
|
|
1 |
/ |
||||||
поставимых условиях пре |
|
|
|
|
|
|
|
• - |
||||||||
|
|
|
|
|
|
|
х - |
2 |
||||||||
вышает эффективность мас- |
- |
1,0 |
0 > |
1 |
|
|
|
|||||||||
|
|
|
V - 3 |
|||||||||||||
сообмена на керамических |
|
|
|
|
|
|
|
□ - |
4 |
|||||||
кольцах |
Рашига, |
причем |
|
|
|
|
|
|
|
А - 5 |
||||||
-0,9 |
А |
|
|
|
|
о - |
6 ----- |
|||||||||
эта разница увеличивается |
|
|
|
|
|
|
/V - 7 |
|||||||||
с |
ростом |
высоты насадоч |
- 0,8 |
|
0,6 |
|
0,8 |
_____ L...... |
||||||||
ного слоя. |
|
|
|
|
|
|
|
|
/,0 |
|||||||
|
Отечественные |
седла |
|
|
|
(L/G)"4Tr/ r J /S |
|
|||||||||
типа |
Инталокс, |
насадка |
Рис. II-9. |
Корреляция даппых |
по скорости |
|||||||||||
ГИАП |
и |
НИИэмальхим |
||||||||||||||
газа |
в точках |
подвисания |
жидкости [60]: |
|||||||||||||
маш и |
кольца Палля |
ус |
||||||||||||||
1 — кольца |
Рашига 25 мм; |
2 — кольца |
Рашига |
|||||||||||||
пешно |
применяются |
при |
50 мм; |
з — кольца |
Палля 50 мм; |
4 — седла Берля |
||||||||||
производстве аммиака (ста |
25 мм; |
5 — седла типа |
Инталокс |
25 мм; 6 — седла |
||||||||||||
типа Инталокс 44 мм; 7 —седла типа Инталокс 50 мм. |
||||||||||||||||
дия очистки МЭА при ат |
|
|
|
|
|
|
|
|
|
|||||||
мосферном и избыточном давлении), |
а также |
в производстве тех |
||||||||||||||
нического |
азота |
(извлечение |
С 02 |
из топочных газов). |
|
|
|
Полуэмпирические методы расчета коэффициентов массоотдачп при физи ческой абсорбции в аппаратах с нерегулярной насадкой достаточно подробно изложены в монографии [17]. Коэффициент массоотдачп в газовой фазе рг ре комендуется рассчитывать по уравнению, предложенному в работе [62]
где |
|
Nur = 0,407Rejy55Pr|!’33 |
(11,99) |
|
wrds |
|
|
Рг^э: |
Vr |
||
Nur = D |
А , г |
Reг = ■ evr |
Ргг = |
|
|
'А , г |
Массоотдачу в жидкой фазе при физической абсорбции рассчитывают с помощью уравнения [63]
Nu* = 0,0021Re®'76Pr®'5 |
(И,100) |
M v» |
v |
Иеж — |
4^ж |
Уж |
|
Nil* = |
D A |
|
РГж = DA |
||
В уравнениях (11,99) |
п |
(11,100) |
коэффициенты |
молекулярной диффузии |
D л г»D а выражены в м2/ч, кинематическая вязкость v — в м2/ч, приведенная
скорость газа и жидкости — в м/ч, е — свободный объем насадки, м8/м3. Коэффи циент массоотдачи 0Ж в уравнении (11,99) является истинным, так как он отнесеп к единице эффективной поверхности лЭф| в уравнении (1 1 ,1 0 0 ) коэффициент массоотдачи рж условно отнесен к единице геометрической поверхности насадки во» поэтому для определения объемного коэффициента массоотдачи нужно умно жить рж на а0. Истинный коэффициент массоотдачи, отнесенный к единице эффективной поверхности а^ , будет выше и равен
Рж,ист — Рж а |
(11,101) |
В насадочных аппаратах эффективная поверхность |
контакта |
аэф в значительной степени зависит от плотности орошения, разме ров насадки и области протекания химической реакции. Не вся геометрическая поверхность насадки а0 является смоченной и не вся смоченная поверхность асм может быть эффективна. Величина а^/а0 характеризует степень использования поверхности насадки.
Рекомендации |
[64—66] по практическому использованию величины |
||||
аЭф/а0 приведены в табл. Н-9. |
|
|
|
||
|
Таблица Н- 9. Эффективная поверхность контакта фаз |
||||
в насадочных аппаратах, работающих в пленочном режиме |
|||||
|
|
|
|
N |
>/°0 |
Насадка |
Размер, мм |
а см/а 0 |
физическая аб |
хемосорбция в |
|
сорбция и хемо |
|||||
|
|
|
|
сорбция в обла |
области протека |
|
|
|
|
сти протекания |
ния реакции |
|
|
|
|
псевдопервого |
|
|
|
|
|
мгновенной ре |
|
|
|
|
|
порядка |
|
|
|
|
|
акции |
|
\ |
|
|
|
|
|
Седла |
Б'ерля |
25 |
0,81 |
0,5 |
0.7 |
Седла типа |
|
|
|
|
|
Инталокс |
25 |
0,77 |
0,5 |
0,7 |
|
|
|
44 |
0,87 |
0,8 |
0,8 |
Кольца |
Палля |
50 |
> 0 ,9 |
0,8 |
0,8 |
50 |
0,81 |
0,8 |
0,8 |
||
Кольца |
Рашига |
25 |
0,5 |
0,4 |
0,5 |
|
|
50 |
0,95 |
0,8 |
0,8 |
Приведенные выше уравнения для расчета рж и рг не учитывают влияние поверхностной конвекции. Приближенно поправочный ко эффициент (фактор интенсивности поверхностной конвекции), учи тывающий увеличение рж при хемосорбции, можно рассчитывать по опытным данным [67], полученным на дисковой колонне, т. е.
вгидродинамических условиях, близких к гидродинамическим усло виям в колоннах с нерегулярной насадкой.
При переходе из пленочного гидродинамического режима работы
врежим подвисания эффективность массообмена заметно увеличи
вается [68], особенно для насадок сравнительно небольшого размера. Одной из главных причин уменьшения эффективности работы абсорберов большого диаметра является значительная поперечная неравномерность [69] потоков газа и жидкости. Так, даже при равномерной порозности насадочного слоя наблюдается растекание жидкости к стенкам абсорбера. Если укладка насадки такова, что порозность возрастает от центра аппарата к его периферии, то доля жидкости, проходящая вблизи стенок, значительно увеличивается [70]. При заметном повышении скорости газа и особенно при пере ходе в режим подвисания следует ожидать уменьшение поперечной неравномерности жидкости. На практике главной причиной по перечной неравномерности является недостаточно хорошее первона чальное распределение газа и жидкости по сечению аппарата. В при менении к моноэтаноламиновому абсорберу этот вопрос был подробно
освещен в работах [53, 71, 72].
Для снижения поперечной неравномерности при очистке техно логических газов (особенно для процесса очистки под давлением) применяются тарелки — распределители жидкости. Тарелка пред ставляет собой плиту с отверстиями для стока жидкости и колпач ками для прохода газа. Для ввода жидкости служит пучок перфори рованных труб, проложенных между газовыми патрубками. Такое устройство компактно и не нарушает равномерность газового по тока.
Равномерность раздачи жидкости из коллектора по трубам до стигается уменьшением диаметра труб от центра к периферии, рав номерность расхода вдоль этих труб — переменным шагом между отверстиями равного диаметра. Методика расчета равномерности подачи жидкости перфорированными трубами приведена в работе [73]. Уровень жидкости над сливными отверстиями должен быть достаточно большим, чтобы снизить влияние перекоса плиты на рас пределение жидкости. Зазор между зонтом и патрубком газового колпака следует выбирать таким образом, чтобы коэффициент гид равлического сопротивления практически не зависел от его величины.
В литературе приводятся опытные данные по эффективным ко эффициентам продольного перемешивания жидкости и газа в наса дочных аппаратах [68, 74—83], но в ограниченном интервале пара метров. В целом можно считать, что при правильном первичном распределении влияние продольного перемешивания жидкости в на садке на эффективность массообмена невелико. Так, по данным [78], коэффициент Dx изменяется в пределах от 50 до 120 см2/с при уве личении плотности орошения от 10 до 40м 3/(м2*ч); при расчете по данным [80] величина Ижне превышает 150 см2/с для условий ра боты промышленных абсорберов очистки МЭА при атмосферном давлении.
Эффективный коэффициент продольного перемешивания в газо вой фазе DT для сухой насадки можно рассчитать по теоретической формуле:
|
« |
wrdHас |
|
|
|
|
|
|
|
|
|
||
|
Рег= - ^ З Г ~ |
21 |
|
|
|
|
|
|
|
|
|||
В орошаемой насадке значение коэффициента Dr выше. |
При |
||||||||||||
ближенная |
величина Dr для |
условий работы промышленных |
наса- |
||||||||||
Газ |
Г |
|
дочиых аппаратов составляет при |
||||||||||
|
мерно |
100—500 см2/с. |
При |
таких |
|||||||||
|
|
|
|||||||||||
|
|
|
значениях/),, величина Вог, харак |
||||||||||
|
|
|
теризующая |
степень |
|
продольного |
|||||||
|
|
|
перемешивания; высока, |
что гово |
|||||||||
|
|
|
рит об отсутствии влияния на эф |
||||||||||
|
|
|
фективность |
абсорбции |
продоль |
||||||||
|
|
|
ного перемешивания газа. Однако |
||||||||||
|
|
|
в некоторых |
случаях |
(например, |
||||||||
|
|
|
при малой скорости |
газа и очень |
|||||||||
|
|
|
высокой |
плотности |
орошения) |
от |
|||||||
|
|
|
рицательное |
влияние |
продольного |
||||||||
|
|
|
перемешивания следует учитывать, |
||||||||||
|
|
|
особенно, |
если |
^требуется |
обеспе |
|||||||
|
|
|
чить высокий коэффициент извле |
||||||||||
|
|
|
чения. |
|
|
|
|
|
|
|
|
|
|
|
|
|
Для |
аппаратов |
с |
регулярной |
|||||||
|
|
|
(упорядоченной) |
насадкой |
харак |
||||||||
|
|
|
терны |
отсутствие |
существенных |
||||||||
|
|
|
местных |
сопротивлений |
и |
значи |
|||||||
Рис. 11-10. Абсорбер с частично за |
тельный |
свободный |
объем. |
Это |
|||||||||
обусловливает |
высокую |
пропуск |
|||||||||||
топленной |
насадкой для поглоще |
||||||||||||
ния С 02 из конвертированного газа |
ную способность при сравнительно |
||||||||||||
водным раствором МЭА: |
|
низком |
сопротивлении. |
Из |
раз |
||||||||
1 *— верхняя зона аппарата; 2 — нижняя |
личных типов регулярной насадки |
||||||||||||
зона аппарата; 3—газораспределитель; 4— |
наиболее |
распространена плоско |
|||||||||||
распределитель жидкости; 5, б — днфма- |
|||||||||||||
нометры ДМПК-100. |
|
параллельная |
насадка |
[17, |
84, |
||||||||
|
|
|
85]. |
|
|
|
|
|
|
|
|
|
Подробные методы расчета эффективности массообмена в аппа ратах с упорядоченной насадкой приведены в монографиях [17, 85]; рекомендуемые уравнения можно считать достаточно надежными, если обеспечено тщательное распределение газа и жидкости по по перечному сечению абсорбера. Как отмечалось выше, хемосорбция в аппаратах пленочного типа протекает в условиях резко выражен ного эффекта поверхностной конвекции в жидкой фазе. При этом возрастает интенсивность массопередачи и в ряде случаев коэффи циенты массоотдачи рж при пленочном режиме и при барботаже ста новятся соизмеримыми.
Если по условиям технологического процесса в абсорбере не обходимо иметь значительное количество жидкости, т. е. увеличить
ее время пребывания в аппарате, целесообразно использовать наса дочные аппараты, работающие в режиме частичного затопления, или иначе абсорберы с регулируемым запасом жидкости. Если в нижней части абсорбера протекают сравнительно медленные хи мические реакции, то эту нижнюю (затопленную) зону аппарата можно рассматривать как химический реактор барботажного типа, секционированный по высоте насадочными элементами. Секциони рование позволяет значительно снизить отрицательное влияние продольного перемешивания жидкости.
Принципиальная схема устройства абсорбера и регулирования высоты затопления показана на рис. 11-10. Дифференциальным ма нометром ДМПК-100 измеряется сопротивление АР а - б с л о я на
садки между точками А и Б . Вторичный прибор пневматически свя зан с клапаном на линии выходящего из абсорбера раствора. Со противление слоя, соответствующее заданной высоте затопления, устанавливают с помощью вторичного прибора. Высота затопления Н и высота слоя светлой жидкости h0 связаны между собой соотно шением
уж
h o = — Н = ижН
где иж и иж — количество удерживаемой жидкости, м3 на 1 м3 соответственно аппарата и газожидкостного слоя; е — свободный объем сухой насадки, м3/м3 аппарата.
Величина |
А0уж близка |
к сопротивлению АРа-бч |
поскольку |
для насадок |
промышленных |
размеров сопротивление |
при трении |
в затопленной части насадки и сопротивление незатопленной части насадки невелики по сравнению с сопротивлением столба жидкости высотой Ао (уж — удельный вес жидкости, кгс/м3). Таким образом, АР а - б й0уж. Следовательно, по показаниям дифманометра мож
но рассчитать высоту газожидкостного слоя Н, если известна вели чина ижили газосодержание ср = 1 — иж.
Газосодержание ср рассчитывают по уравнению:
(Р= т [ 1 +<Ро(1 - с - ? г ) ] ~ 1 ^ т [ 1 +,Р»(1 - с ^ г ) ] а“ фв (ПЛ02)
Газосодержание непроточного слоя сро определяется [8 6] по уравнению, близкому к уравнению Айзенбуда и Дильмана [87] для газосодержания свободного (без насадки) барботажного слоя
Фоио = а — ехр |
■(-Sr)*;/Yr)0’2 |
(11,103) |
|
/ |
wr \<М |
|
|
t |
+ 0,01 \ |
еи>п / (Y*/Yr) ° - 75 |
] |
где ал—~1 для керамических насадок и 1,092 для пластмассовых колец Палля; wn — скорость свободного всплывания пузыря, равная примерно 0,25 м/с; и о — коэффицпент^стесненностп.
Коэффициент и0 рассчитывают по формуле
|
|
и0 = |
1 - Д 2 //^ |
(11,104) |
||
где R — средний радиус пузыря, определенный по данным работы |
[8 8 ]; До — |
|||||
эквивалентный радиус насадки. |
|
|
|
|
||
Коэффициент |
с |
в уравнении (II, 102) равен |
|
|||
|
|
с — |
|
И>ж |
спред |
|
|
|
^ж , пред |
|
|||
причем 0 ==£ С sg |
Спред, а |
у |
|
|||
|
|
|
|
|||
|
|
|
|
(ф |
|
|
|
|
СПреД |
|
(и>ж/ ^ г) пред |
|
|
При лредельном |
|
режиме (режим |
захлебывания) газосодержанне |
|||
можно рассчитать |
по формуле |
ф пред = Фо72- |
|
Указанный метод расчета ф основан на представлении о том, что в затопленной насадке действуют два механизма удерживания жидкости; естественный (за счет трения жидкости о насадку и газо вый поток) и искусственный (за счет подпора на выходе жидкости из аппарата). Предельные нагрузки для колонн с частично затоплен
|
|
|
ной насадкой [68] опреде |
|||||||
|
|
|
ляются на основе тех же |
|||||||
|
|
|
закономерностей, что и для |
|||||||
|
|
|
обычных |
насадочных |
ко |
|||||
|
|
|
лонн, и, следовательно, мо |
|||||||
|
|
|
гут |
быть |
рассчитаны |
по |
||||
|
|
|
уравнению (И, 98). |
|
||||||
|
|
|
|
Для абсорбера с частич |
||||||
|
|
|
но |
затопленной |
насадкой |
|||||
|
|
|
ступенчатый |
распредели |
||||||
Рис. 11-11. |
Зависимость |
объемного коэффи |
тель |
[89] |
газа, |
который |
||||
циента массоотдачи (Зжа |
от скорости газа в |
представляет |
собой плиту |
|||||||
колонне с высоким барботажным слоем [плот |
с |
отверстиями |
(первая |
|||||||
ность |
орошения 54 м3/(м2 *ч)]. |
|||||||||
ступень |
распределения). |
|||||||||
|
|
|
||||||||
В плиту вварены трубы различной длины |
(последующие |
ступени). |
Число ступеней выбирается произвольно, обычно имеются 3—4 сту пени. Разметка отверстий и труб каждой ступени выполняется по равномерным сеткам, при совмещедии которых образуется также равномерная, но более частая сетка. Для протока жидкости служат специальные трубьг. Газ поступает под плиту, где образуется газовая подушка, высота которой пропорциональна сопротивлению распре делителя. При малых расходах газ выходит через отверстия. При увеличении нагрузки сопротивление отверстий повышается и жидкость вытесняется через трубы (ступени). При понижении уровня жидкости последовательно высвобождаются концы труб. Свободное сечение для прохода газа увеличивается. При использовании в зоне затопления насадки из пластмассы необходима прижимная или ограничительная решетка.
На рис. И -И приведены данные по эффективности массообмена в барботажном слое, относящиеся к плотности орошения L = 54 м/ч.
Зависимость объемного коэффициента массоотдачи ржа от ско рости газа получена при обработке данных различных исследовате лей для свободного (без насадки) барботажного слоя. При секциони ровании с помощью насадки эффективность массообмена увеличи вается, особенно для насадки мелких размеров. Для крупных наса док (50 мм и более) увеличение ржа по сравнению с свободным барботажным слоем сравнительно невелико, поэтому для промышлен ных абсорберов с затопленной насадкой можно использовать данные рис. Н-11. Влияние плотности орошения на объемный коэффициент массоотдачи можно учесть с помощью зависимости
Ржа~ £0,6
Тарельчатые абсорберы
Основным преимуществом тарелок провального типа является высокая пропускная способность по газу й простота конструкции. Диапазон устойчивой работы тарелок провального типа, соответст вующий равномерному гидродинамическому режиму [17], меньше, чем у насадочных аппаратов. Равномерный режим работы характе ризуется сравнительно небольшой зависимостью сопротивления та релки АР и высоты газожидкостного слоя от скорости газа. При значительном увеличении скорости газа сопротивление резко воз растает (режим захлебывания). Однако на тарелках с большим сво бодным сечением (примерно больше 2 2 %) даже при значительном увеличении скорости газа сопротивление тарелки незначительно
иравномерно повышается.
Всоответствии с рекомендациями [90, 91], гидродинамический расчет та релок провального типа можно вести в следующей последовательности. Зада
ются статическим давлением барботажного слоя А Р 2 (обычно 25—50 кгс/м2) и рассчитывают скорость газа в отверстиях или щелях тарелки
(11,105)
где о — поверхностное натяжение, кгс/м; а — ширина щели или радиус от верстия, м; уг — удельный вес газа, кгс/м3.
Коэффициент сопротивления £ рекомендуется принять равным двум (с не которым запасом). Коэффициент Р характеризует [90, 92] соотношение между средним статическим давлением барботажного слоя и локальным статическим давлением, вызывающим стекание яшдкостп через отверстия; величину р рассчи тывают по уравнению
р = 1Д1 (у г/у ж )0’11» |
(11,106) |
Долю свободного сечения т, занятую стекающей жидкостью, рассчитывают по уравнению
3/ |
1 |
|
V(L/G)2 Уг/уж~^2 |
(11,107) |
|
v(L/G)2 \гАуж £^2 |
|
6 Заказ 14Ь0 |
81 |
В |
уравнении (11,107) величина LIG — отношение |
весовых |
расходов |
жидкости |
|
и |
газа; р, — коэффициент истечения жидкости |
из |
отверстия, близкий к 0,62. |
||
|
После расчета wp задаются свободным сечением тарелки Fc. Практически |
||||
используются тарелки провального типа со |
свободным |
сечением |
10—30%. |
||
|
Рассчитывают приведенную скорость газа и?г и диаметр аппарата, а затем |
||||
высоту барботажного слоя Н п |
|
|
|
|
|
|
Н п = АР21уп |
|
|
|
(11,108) |
где уп = (1 — <р)уж, а газосодержание ср можно приближенно принять равным
0,6- 0,8.
В литературе имеются [17, 93, 94] более точные методы расчета ср. Так, по данным [94], величина <р зависит от критерия Фруда Fr = wr/gho
<p = 0,58Fr0.i |
(1Ы09) |
где ho — высота светлой жидкости на тарелке, м.
После определения геометрических характеристик тарелки рассчитывают диапазон устойчивой работы абсорбера. Скорость газа w3l соответствующая
верхнему пределу работы, может быть найдена с помощью |
корреляции [95] |
|||
Jf3_ _YD_ |
- I /"_ Y r _ |
11,6 ( L /G ) - 0 .2 28 |
(IU 10) |
|
Fс Уж |
У Увозд |
|||
|
|
где ув — удельный вес воды.
Практически рабочую скорость газа рекомендуется принимать равной 0,7— 0,9 предельной скорости газа w3.
Верхний предел устойчивой работы можно рассчитать также п© уравнению
------2 _ |
JL . „оде = В е-4 (L/C)'/«OV/v*)1/. |
( 11,111) |
gdsnFt |
УжРж |
|
причем В = 10. Уравнение (11,111) следует считать менее точным, чем уравнение (1 1 ,1 1 0 ); как правило, при расчете по уравнению (1 1 ,1 1 1 ) получают заниженные значения w3. Скорость газа, соответствующую нижнему пределу работы, следует рассчитывать по уравнению (11,111) при В = 2,95.
Общее сопротивление тарелки рассчитывают по уравнению:
Ь Р = T T F |
( т г ) 8 i d b p |
11 _ т <1 —Р)] + 2<т/« (1 - Р ) |
(11.112) |
||||
Для расчета удельной поверхности контакта фаз а (в м2/м3) на тарелках |
|||||||
провального типа можно рекомендовать следующие уравнения: |
|
||||||
для водных растворов электролитов |
|
|
|
|
|||
aft0 =5R e“0 ,2sFr0'2We-°>e (" ^ " ) |
0 ’ * 5 |
(11.113) |
|||||
для органических |
жидкостей |
|
|
|
|
||
|
яле |
|
/ |
\ “0.43 |
/ Vr \ “ 0,25 |
(11.114) |
|
aho = 6,4Re“°’2 5Fг®»2We- 0 »e |
|
|
V v t ) |
||||
В уравнениях (11,113) |
и |
(11,114) |
|
|
|
|
|
|
wrh0 |
ehо |
|
|
|
||
Be г — |
vr |
Fr: |
We = |
y*hl |
|
||
|
|
|
|
|
|
|
где ho — высота светлой жидкости на тарелке.
Предложенные уравнения применяются для расчета колонн диаметром более 120 мм и при /ю > 20 мм, vB — вязкость воды при 20 °С.
Коэффициенты массоотдачи Рг и рж, отнесенные к фактической поверх ности контакта фаз, можно рассчитать с помощью уравнений [94]:
Nur = 0,12Re®,7Pr®’ 5 (<*„/<*„,1)0'5 |
(11.115) |
Nu* = 1 .2 Re^7PrS; 5 (d„/dn>1)o.b |
(11.116) |
где
Здесь dn — средний поверхностно-объемный диаметр пузырьков, равен бер/а, a dn, г = 4 мм. Точность приведенных уравнений ±20% .
Уравнения (11,115) и (11,116) применяются для расчета эффективности массопередачи и на ситчатых тарелках.
Данные [97] свидетельствуют о весьма интенсивном перемешива нии жидкости на тарелках провального типа (значения Вож малы). Однако в ряде случаев, например при обработке опытных данных,
отсутствие учета влияния продольного |
перемешивания жидкости |
не только искажает абсолютное Значение |
коэффициента массоотдачи, |
но и может привести к неверной зависимости коэффициента массоот дачи от ряда определяющих параметров (скорость жидкости и др.). Практически аппараты с тарелками провального типа рассчиты вают исходя из условия полного перемешивания жидкости, т. е. с некоторым запасом. Для газовой фазы принимают схему идеаль ного вытеснения.
Ситчатые тарелки имеют отверстия (иногда щели) обычно разме ром от 2 до 10 мм, через которые проходит газ. Уровень жидкости на тарелке поддерживалот с помощью переливного устройства.
Методика гидравлического расчета ситчатых тарелок основана на том, что при заданном свободном сечении тарелки рассчитывают нижний предел скорости газа, соответствующий отсутствию провала жидкости через отверстия, и верхний предел (захлебывание вслед ствие переполнения переливного устройства). В результате расчета определяют рабочую скорость газа, сопротивление тарелок и рас стояние между ними.
В соответствии с рекомендациями [98, 99], гидравлический расчет ситча тых тарелок можно вести в такой последовательности. Выбирают длину сливной перегородки b (обычно величина 6/Z), где D — диаметр аппарата, составляет 0,6—0,8). При известном расходе жидкости L рассчитывают напряженность слива ЫЬ. Принимают высоту сливной перегородки z1 и рассчитывают гидра влический градиент жидкости по длине тарелки:
Ah — [(1 — иж) Zi -f- / |
hi] уж |
(П.И7) |
где уж — количество жидкости в газожидкостном слое [87], м3/м3:
иж= ехр |
(I III18) |
В этом уравнении шп — скорость свободного всплывания пузыря. Уравнение (11,118) рекомендуется для расчета при высоте слоя более 50 мм; при меньшей высоте рассчитанные значения шж следует умножить на поправочные коэффи
циенты [87]. |
|
|
|
|
|
|
|
Напор слоя небарботируемой жидкости у сливной перегородки определяют |
|||||
по |
формуле |
________ |
|
|
||
где |
т — коэффициент расхода, равный 6400; |
для |
ЫЬ ^ 1 0 |
м3/(м*ч). |
||
|
Зная гидравлический |
градиент Д н а х о д я т |
скорость |
газа в отверстиях |
||
wон» соответствующую началу равномерной |
работы тарелки: |
|||||
|
|
u’o«=°-6 7 / o |
^ |
r |
|
<п -120> |
Фактическая скорость газа в отверстиях должна быть выше найденного значе ния Won, т. е. должно выполняться условие w0 > шон. При заданном свободном сечении тарелки можно рассчитать приведенную скорость газа и при известном расходе газа — диаметр аппарата. Если условие wQ> wOH не выполнено, та^ редка будет работать в неравномерном режиме. Для обеспечения равномерной работы необходимо изменить геометрические характеристики тарелки. Чтобы уменьшить величину ш0н» уменьшают свободное сечение или значение ъъ либо увеличивают Ь.
Гидравлическое сопротивление ситчатой тарелки ДРТ складывается иэ со противления сухой тарелки ДРХ, статического давления столба жидкости ДР 2 и сопротивления ДР3, обусловленного действием сил поверхностного натяжения.
Для расчета статического давления служит уравнение |
|
b P 2 = ( v x * l-\ -¥ v iiih 1) y x |
( 11,121) |
Сопротивление ДР х рассчитывают по уравнению |
|
ДР Х« Б - ^ |
(11.122) |
(где £ = 1,7—2), а сопротивление ДР3 — по уравнению: |
|
ДРз = - р - |
(11,123) |
(*ъкв |
|
Далее выбирают тип переливного устройства. Высоту подпорной |
перегородки |
/ z 2 рассчитывают по уравнению
z2 = 4ЛКр+ Л
Величину а = z 2 — s (где s — высота щели) принимают равной 5—10 Критическую глубину потока жидкости ЛКр* рассчитывают по уравнению
K V= Y (ЫЬ)* Y
Значение коэффициента А зависит от конструкции переливного устройства. Если переливное устройство имеет вид прямого кармана [98, 99], А = 1,34.
Средпяя по тарелке высота барботажного слоя будет равна
АРо |
|
IIП — Уж^ж |
(П.124) |
В общем случае расстояние между тарелками / должно*удовлетворять усло виям
1 ^ Н 0- 2 г |
(11,125) |
1 ^ Н п |
(11,126) |
Кроме того, нужно учитывать унос жидкости, поэтому расстояние |
между |
тарелками может быть увеличено по сравнению с величинами /, определяемыми
неравенствами |
(11,125) |
и |
(11,126). |
|
|
|
|
Высота светлой жидкости Н о в переливном устройстве будет равна |
|||||
|
|
|
|
Д Р Т+ Д Р Ж . |
(11,127) |
|
|
|
|
# 0 = ----- J — |
~ + h 0+ b h |
||
где |
ДРЖ—" местное сопротивление, |
обусловленное протеканием |
жидкости |
|||
через щель из |
переливного |
кармана на тарелку. |
|
|||
|
Обычно скорость жидкости, отнесенную к площади переливного устройства, |
|||||
принимают равной не |
более 0,25 м/с. |
|
|
|||
ния |
Изложенные выше рекомендации по определению межтарелочного расстоя |
|||||
справедливы, если |
в переливном |
устройстве течет жидкость, |
свободная |
от пузырей газа. Если жидкость увлекает в переливное устройство значитель ное количество газа или она склонна к устойчивому ценообразованию, расстоя ние между тарелками следует увеличить в 1,5—2 раза по сравнению с расчетным.
Одной из модификаций аппаратов с ситчатыми тарелками являются пенные аппараты [1 0 0 , 1 0 1 ], в которых пена через переливную перегородку перетекает с подпором. Переливное устройство обычно размещается снаружи аппарата, для слива жидкости служит прямоугольное отверстие в стенке аппарата. За счет создания подпора жидкости, увеличивается высота слоя на тарелке. При малых расходах .жидкости пенный аппарат работает со свободным сливом. Свободное сечение тарелок в пенных аппаратах обычно составляет 15—25% (иногда более 30%), т. е. значительно выше, чем в обычных ситчатых тарелках. Соответственно выше и скорость газа. В пенных аппаратах доля жидкости, проваливающаяся через отверстия, может быть весьма значительной (особенно при высоких слоях газожидкостного слоя); такое устройство работает как комбинированная пере- точно-провальная тарелка.
Поверхность контакта фаз на ситчатых тарелках, детально исследованную |
|
в работе [94], можно рассчитать по уравнению |
|
afco = 0,65Fr<>,2We-o.e(pO,3 / Vw \J 0»25 |
(11,128) |
Обозначения те же, что и в уравнении (11,114). |
фазах можно- |
Для расчета коэффициентов массоотдачи в газовой и жидкой |
пользоваться соответственно уравнениями (11,115) и (11,116). Можно применять-
также уравнения, предложенные в |
работе [1 0 2 ]: |
|
||
Nur = 2.5Re°-72We-o.25pr°.6 |
(11,129) |
|||
Рж-4 — 1 ,2 2 ftJ*13 ( |
1^,ф ) |
|
(11,130)- |
|
В уравнении (11,129) в критериях |
|
|
|
|
Р г ^ х |
|
|
Ы7ГХ |
|
N ur= D A |
г и |
Rer“ |
v r |
|
в качестве характерного линейного' размера введена капиллярная постоянная
х = |
V о / у ж; величина А |
— поверхность контакта фаз, отнесенная к 1 ма пло |
|
щади |
тарелки, |
А = 6 Лоф/с/п (1 — ф); dn = 6 ф/а — средний диаметр пузыря; |
|
критерий We = |
х2/ho2. |
ho следует брать в мм, а рж выражено в м/ч. |
|
В уравнении (11,130) |
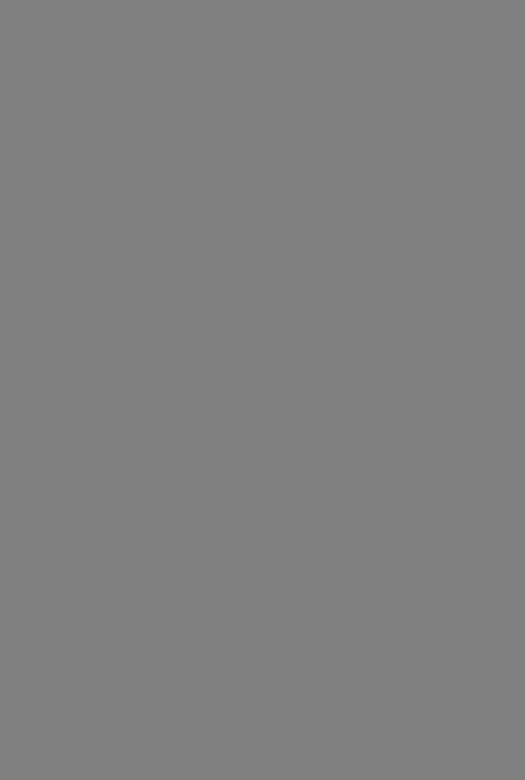
Уравнения |
Характер адсорбции |
Ленгмюра [104, 105]
е - |
КР |
w |
1+ КР |
Брунаусра, Эммета, Теллера (БЭТ) [105]
hC
а ~ ат ( 1 — Л)[1+Л (СЧ-1)1
h ~ P / P g
Фаулера и Гуггенгейма [105]
К ( 1 - 0 )
Киселева [105]
ге
Я( 1 - О ) ( 1 + 'п 0 )
Фрэндлиха [104]
е = КР ехр -££■
т
Темкина [104]
0 - J ^ l n (КР)
Дубинина [109]
Мономолекулярная; энергия абсорбции не изменяется с заполнением поверх ности
Полимолекулярная на непористых сор бентах; энергия взаимодействия меж ду молекулами адсорбата невелика
Мономолекулярная с учетом сил при тяжения между молекулами адсор бата; энергия адсорбции возрастает с заполнением поверхности по линей ному закону
То же, по логарифмическому закону
Хемосорбция; энергия адсорбции умень шается с заполнением поверхности, по логарифмическому закону
То же, по линейному закону. Приме няется в области средних заполнений поверхности
Физическая адсорбция на мелкопори стых адсорбентах первого структур ного типа
То же, на крупнопористых адсорбентах vвторого структурного типа
О б о з н а ч е н и я: а—количество поглощенного вещества, моль/г; ат—то же, соответствующее плотному заполнению мопослоя,
моль/г; Р —давление, мм рт. ст.;
PQ—давление насыщенного пара при данной температуре г
ммрт. ст.;
©= а/от — степень заполнения поверхности;
К, тп, С, -В WQt w j, А —константы, специфические для каждого уравнения;
Р—коэффициент афинности, равный отношению парахоров адсорбента и стандартного вещества (бензола);
о*—мольный объем ожиженного пара адсорбата при данной температуре, сма/моль.
для извлечения из газов летучих веществ при парциальном давле нии, близком к давлению насыщенного пара [103].
^Наконец, изотерма типа г характерна для мелкопористых сор бентов с вторичной пористой структурой, образованной добавками связующих веществ, что приводит к появлению на графике капил лярно-конденсационной области. Примером таких адсорбентов являются некоторые гранулированные цеолиты.
Изотермы адсорбции описываются уравнениями [104, 105], наи более известные из которых помещены в табл. И -1 0 .
ДИНАМИКА АДСОРБЦИИ
В этом разделе приведены закономерности, наблюдаемые при наиболее распространенном способе адсорбционной очистки и раз делении газов — продувке газа через покоящийся слой гранули рованного адсорбента. При этом процесс очистки или разделения газовой смеси подчиняется специфическим законам динамики ад сорбции [106, 107]. Для характеристики динамики адсорбции важно, является ли изотерма выпуклой, линейной или вогнутой.
При продувке газа через слой сорбента в газовой и твердой фа зах образуется концентрационное поле поглощаемого вещества; движение точек поля происходит в соответствии с уравнением Викке;
w
и= 1 + / »
где и — скорость движения данной концентрационной точки вдоль слоя сор бента, м/с; w — скорость газа в слое, м/с; /' (с) = da/dc (причем а = / (с) — уравнение изотермы); с — концентрация адсорбата в газовой фазе.
Для |
выпуклой |
(к оси ординат) изотермы при с2 > сх функция |
Т (ci) > |
V (сг)- Это |
означает, что точки, соответствующие меньшим |
концентрациям, движутся вдоль слоя сорбента медленнее, чем точки с большими концентрациями. Последние как б& догоняют и погло щают малые концентрации, так что через определенный промежуток времени в концентрационном поле должна установиться единствен ная концентрация поглощаемого вещества, равная начальной. Об разуется сорбционный фронт, перемещающийся в .слое параллельно самому себе, что приводит к послойной отработке сорбента. В общем случае под воздействием различных возмущающих факторов (на пример, неравномерной скорости газа по сечению аппарата) сорб ционный фронт диффузно размывается на каком-то участке слоя. При этом концентрация адсорбата в газовой фазе распределяется от с0 до С/. Величина с{ называется концентрацией проскока и фак тически является наименьшей концентрацией поглощаемого веще ства, аналитически определяемой па выходе из слоя сорбента.
Вследствие диффузного размывания сорбционного фронта ад сорбент отрабатывается не полностью и характеризуется некоторой динамической активностью, равной количеству поглощенного ве щества до появления за слоем концентрации проскока ct-. Динамиче ская активность сорбента всегда меньше его равновесной активности,
соответствующей количеству поглощенного вещества после появле ния за слоем начальной концентрации адсорбата с0.
Скорость движения сформировавшегося сорбционного фронта описывается балансовым уравнением:
W C0
и = ----- :-----
а0+ с0
где д0 — равновесная активность сорбента, моль/см3.
Зависимость между временем защитного действия слоя t и его дли ной L устанавливает уравнение Шилова
t = kL—т
где t — время защитного действия слоя сорбента, исчисляемое от момента подачи газовой смеси до появления за слоем проскоковой концентрации сор бируемого вещества; к = 1 /и — коэффициент защитного действия; т — потеря времени защитного действия вследствие диффузного размытия сорбционного фронта.
Уравнение Шилова, ранее известное как эмпирическое, в настоя щее время получило теоретическую интерпретацию в виде решения дифференциальных уравнений адсорбции [106].
В случае линейной и вогнутой изотерм при действии размыва ющих факторов не образуется стационарного адсорбционного фронта, поэтому уравнение Шилова здесь не применимо. При вогнутой изо терме динамику адсорбции приближенно мояшо оцисать уравнением Викке; для*'линейной изотермы известны другие теоретические ре шения [106].
ПРОМЫШЛЕННЫЕ АДСОРБЕНТЫ
В настоящее время промышленность производит разнообразные типы адсорбентов, обладающих различной пористой структурой и разными свойствами поверхности — активированные угли, сили кагели, синтетические цеолиты и др. Это позволяет для каждогоконкретного случая подобрать высокоселективный сорбент, который обеспечивает очистку газового потока с мдлыми потерями целевого продукта. Для адсорбционной очистки газов применяют главным образом пористые адсорбенты: активированный уголь, силикагель, цеолиты, отличающиеся высокой адсорбционной активностью и сравнительно легко регенерируемые.
Активированный уголь представляет собой сорбент' губчатой структуры, состоящий в основном из углерода [107, 108]. Его струк тура характеризуется наличием пор трех разновидностей: диаметром от нескольких ангстрем (микропоры) до нескольких микрометров (макропоры); между этими пределами находятся поры переходных размеров.
В соответствии с размерами пор различают три структурных типа активированных углей. К первому типу относятся угли с микропорами, эффективный радиус которых менее 16-10~10 м. Объем микропор в таких углях от 0,20 до 0,60 см3/г.
Второй структурный тип отличается развитой сетью макропор; размеры их от 5 • 10~5 до 2 • 10"4 см. Объем этих пор достигает 0,5 см3/г,
я удельная |
поверхность |
сорбента 1,3 м2/г. |
В углях |
смешанного |
структурного типа имеются поры обеих |
разновидностей, а также поры переходных размеров о эффектив ными радиусами от 40 до 200*10"8 см. У специальных образцов углей объем переходных пор может достигать 0,85 см3/г.
Адсорбция веществ на активированном угле при обычной тем пературе обусловлена дисперсиоппымй силами, причем высокая адсорбционная активность угля объясняется резким повышением адсорбционного потецдиала в микропорах. Поэтому для очистки газов при малых парциальных давлениях примесей применяют угли первого структурного типа (так называемые газовые угли).
Угли смешанного и второго структурного типов (так называемые рекуперационные) используют для адсорбции летучих веществ, когда парциальное давление адсорбата близко к давлению его насы щенных паров. Высокая активность этих углей обусловлена ка пиллярной конденсацией поглощаемого вещества в переходных порах и макропорах.
Самые широкопористые угли применяют для осветления раство ров. Для каждого конкретного процесса можно подобрать опреде ленный тип активированного угля (табл. И-ll). При этом необ ходимо учитывать, что угли с меньшими значениями константы В в уравнении Дубинина (см. табл. Н-10) обладают более высокой ад сорбционной активностью в области малых давлений, но труднее поддаются регенерации.
Силикагель представляет собой гель ангидрида кремневой ки слоты. Это сорбент с высокоразвитой пористой структурой; скелет геля состоит из мельчайших шарообразных частиц S i0 2. Поверх ность скелета силикагеля покрыта гидроксильными группами, что •оказывает существенное влияние на его адсорбционные свойства [111—114]. Силикагель легко адсорбирует полярные вещества, а также соединения, образующие с гидроксильными ионами водород ную связь; причем сорбционная активность силикагеля умень шается по мере дегидратации поверхности.
Неполярные вещества адсорбируются в основном за счет диспер сионного взаимодействия на мелкопористых силикагелях, для ко торых характерно увеличение адсорбционного потенциала в тонких лорах. При этом влияние химического состояния поверхности геля на адсорбцию практически несущественно, по становится заметным, если неполярное вещество адсорбируется широкопористым силика гелем.
При практическом применении силикагелей большое значение имеет температурный режим регенерации [115—119]. Химическое состояние поверхности силикагеля, обусловливающее его высокую адсорбционную активность по отношению к полярным веществам, сохраняется только при сравнительно низкой температуре (до 200 °С), если десорбция проводится сухим газом. Регенерация при более
Мари,
БАУ
ТАУ
КАУ
КАД-1
КАД- 1 1
АГ
АГ-2
АГ-3
СКТ
АР-3 APT
ОУК ОУК кисл.
|
Характеристика |
W0, см3/г |
|
В - 10е, к-- |
|
Угли газового типа |
|
|
|
Березовый |
уголь пароводяной актива- |
0,238 |
|
0,617 |
ции |
|
0,266 |
|
0,773 |
Торфяной уголь пароводяной актива- |
|
|||
ции |
|
0,379 |
|
0,779, |
Косточковый уголь пароводяной акти- |
|
|||
вации |
|
0,217 |
|
0,166 |
Полукокс длиннопламенного угля па- |
|
|||
роводяной активации (1 -я активация) |
0,276 |
|
0,876. |
|
То же (2-я активация) |
|
|||
Антрацитовый гранулированный уголь |
0,312 |
|
1,17 |
|
пароводяной активации |
0,330 |
|
0,950 |
|
На основе слабоспекаемого угля паро |
|
|||
водяной |
активации |
0,230 |
|
0,820 |
На основе |
полукокса длиннопламен |
|
||
ного угля пароводяной активации |
0,560 |
|
0,860* |
|
На основе торфа сернистокалиевой ак |
|
|||
тивации |
|
|
|
|
|
Угли рекуперационного типа |
|
|
|
|
I |
0,301 |
I |
0,900 |
|
| |
0,495 |
1 |
0,670 |
Осветляющие угли W*, см^/г, А»103, К - 1 |
|
|
||
|
_ |
0,652 |
|
1,92 |
|
— |
а,614 |
|
1,67 |
высокой температуре приводит к необратимым изменениям пористой структуры и поверхности сорбента, причем тонкопористые силикагели более чувствительны к повышению температуры, чем широкопористые.
При продолжительности десорбции поглощенных веществ нагре тым влажным газом или водяным паром также наблюдается сниже ние адсорбционной активности, в основном из-за уменьшения удель ной поверхности сорбента, тогда как его химическое состояние изме няется мало. Поэтому регенерация силикагелей проводится в более мягких условиях, чем регенерация активных углей.
Изотермы адсорбции полярных веществ на широкопористых силикагелях могут быть описаны известными уравнениями для непористых или широкопористых адсорбентов [12 0 ], адсорбцию неполярных веществ можно рассчитать по уравнению Дубинина для адсорбентов второго структурного типа [1 2 1 ].
Для описания изотерм адсорбции на тонкопористых силикагелях во многих случаях применимо уравнение Дубинина для сорбентов первого структурного типа. Проявление электростатических и ин-
.Аукционных взаимодействий, образование водородных связей обычно сказывается в увеличении опытных значений коэффициентов афинности по сравнению с теоретически вычисленными вели чинами.
Цеолиты —■алюмосиликатные адсорбенты кристаллической струк туры. В решетке цеолита часть ионов Si4+ заменена ионамн А13+ , вследствие чего решетка обладает некоторым избыточным отрица тельным зарядом, компенсируемым различными катионами. Эта особенность строения сорбента позволяет синтезировать цеолиты разнообразных форм, характеризующиеся различным соотношением ионов кремния и алюминия, количеством и зарядом катионов и от личающиеся типом кристаллической решетки.
Наибольшее значение приобрели цеолиты типов А и X, свойства которых описаны в работах [122—130]. Характерной особенностью их является наличие больших полостей (пустот) между элементами, образующими кристаллическую решетку. Внутри элементов имеются малые полости. В большие полости ведут окна. Молекулы, размер которых меньше размеров окон, проникают в полости кристалличеокой структуры и адсорбируются цеолитом.
С другой стороны, на сорбцию различных молекул, критические размеры которых меньше эффективных диаметров входных окон, существенно влияют размер, заряд, количество и расположение ка тионов (Са2+, Na+ и т. д.), компенсирующих отрицательный заряд решетки. Это связано с изменением объёма адсорбционного про странства и электрического поля в больших полостях цеолита.
Цеолиты проявляют различную чувствительность к термической обработке; Так, кальциевый цеолит теряет адсорбционные свойства лишь при 800 °С, натриевый. — при 700 °С, литиевый — при 640 °С.
По термической устойчивости цеолиты образуют следующий ряд: СаА > КА > NaA > LiA >> NH 4A. Термостабильность цеолитов уменьшается после обработки их водяным паром. Например, цеолит NaA разрушается при 500 °С, практически он устойчив лишь до 200 °С.
Размер кристаллов синтетических цеолитов измеряется в микро метрах, поэтому в практических условиях цеолиты применяют в гра нулированном виде с добавкой различных связующих веществ. В та ком виде цеолит приобретает вторичную пористую структуру. Сле дует указать, что связующие добавки иногда могут проявлять себя
как катализаторы побочных процессов |
при адсорбции, например |
полимеризации некоторых углеводородов |
[131]. |
Цеолиты — типичные мелкопористые сорбенты и, в соответствии |
|
с классификацией Дубинина [1 2 1 ], должны быть отнесены к сор |
бентам первого структурного типа^Лоэтому для расчета изотерм абсорбции неполярных веществ можно применять соответствующее уравнение Дубинина.
Это подтверждается многочисленными экспериментальными дан ными, полученными при изучении адсорбции на цеолитах [131 — 135].
Уравнение для адсорбентов первого структурного типа может быть использовано и для условий адсорбции полярных веществ (например, воды) или веществ, молекулы которых обладают боль шим квадрупольным моментом (например, азот) [122—129, 137]. Однако при этом наблюдается увеличение экспериментальных ко эффициентов афинности по сравнению с их теоретическими значе ниями.
ПРЕИМУЩЕСТВА ^НЕДОСТАТКИ АДСОРБЦИОННЫХ МЕТОДОВ
К преимуществам адсорбционных методов относится высокая поглотительная "способность адсорбентов, особенно при цизких пар циальных давлениях извлекаемых компонентов, что позволяет об рабатывать относительно малым количеством сорбента огромные объемы газов и достигать при этом высокой степени очистки. В слу чае применения твердого сорбента отпадает опасность загрязнения технологического газа вторичными примесями.
Недостатки адсорбционных методов, препятствующие их широ кому внедрению в промышленность, заключаются в периодичности процесса очистки, высокой стоимости регенерации адсорбентов и сравнительно низкой эффективности аппаратуры. Организация непрерывных процессов (адсорбция в движущихся слоях) связана с конструктивными и техническими трудностями. Существенным недостатком пористых сорбентов является снижение их адсорб ционной активности в процессе эксплуатаций, особенно при очистке многокомпонентных смесей.
В производстве аммиака адсорбция применяется главным обра зом для тонкой очистки технологических газов от сернистых соеди нений и двуокиси углерода, а также для очистки ацетилена., полу чаемого пиролизом углеводородов.
3. ОСНОВЫ КАТАЛИТИЧЕСКИХ МЕТОДОВ ОЧИСТКИ
Каталитические методы очистки газов основаны на взаимодейст вии удаляемых веществ с одним из компонентов, присутствующим в очищаемом газе,-или со специально добавляемым в смесь веществом на твердых катализаторах. К таким методам применимы общие за кономерности гетерогенно-каталитических процессов.
Действие катализаторов сводится к многократному промежуточ ному химическому взаимодействию катализатора с реагирующими соединениями, в результате которого образуются промежуточные вещества, распадающиеся в определенных условиях на целевой продукт и регенерированный катализатор [136—138]. Благодаря такому постадийному пути реакции увеличивается скорость дости жения равновесия, термодинамически возможного, но трудно до стижимого в отсутствие катализатора. Таким образом, очевидно, что активность катализатора определяется его химическим составом.
Явления адсорбции в гетерогенном катализе изучены и описаны в литературе [138—141].
Скорость каталитических процессов выражают общепринятым для всех химических реакций уравнением
W = K C \C \ . .
где W — скорость реакции; Cv С2 и т. д. — концентрации веществ, участву ющих в реакции (для реакций, протекающих в газовой смеси, они, как правило, заменяются соответствующими парциальными давлениями); К — константа скорости реакции; а, b — порядок реакции по соответствующему компоненту.
Зависимость константы скорости реакции от температуры опи сывается законом Аррениуса:
K = ze-E/RT
где Т — абсолютная температура; R — универсальная газовая постоянная; Е — энергия активации; z — предэкспоненциальный множитель.
Величины Е и z — постоянные, характерные для данной химичесской реакции и катализатора.
Каталитические процессы могут замедляться образующимися продуктами реакции. В этом случае в уравнение скорости реакции следует вводить значения концентрации продуктов реакции в сте пени со знаком минус. Торможение каталитических процессов про дуктами реакции может объясняться двумя причинами. Одной из них является адсорбция продуктов реакции поверхностью катали затора, что уменьшает ее рабочую часть.
Для обратимых реакций возможен совершенно иной механизм торможения образующимися продуктами [139]. В результате проте кания наряду с прямым целевым процессом обратного продукт реакции находится в равновесии с адсорбированными и присут ствующими в газе исходными компонентами реакции. Это приводит к увеличению на поверхности катализатора концентрации адсор бированного компонента и к снижению содержания целевого про дукта в газовой фазе, т. е. к замедлению скорости его образования.
В промышленных условиях об активности катализаторов судят по количеству продукта, получаемого с единицы объема катализа тора, или по максимально допустимой объемной скорости, при ко торой обеспечивается требуемая степень превращения.
Каталитическая очистка применяется главным образом при небольшой концентрации удаляемого компонента в исходном газе; содержание этого компонента после очистки снижается на несколько порядков. Очень часто процесс протекает при большом избытке другого компонента реакции, концентрация которого после катали тической очистки практически не меняется. В связи с этим при проведении очистки большое значение приобретают процессы диф фузии, тесным образом связанные с пористой структурой катализа торов. Таким образом, пористая структура является одной из важ нейших характеристик катализаторов. Она определяется удельной
поверхностью, пористостью, размером пор и распределением их по радиусу.
Вопросы теории диффузионного торможения при каталитиче ских процессах рассмотрены в ряде научных статей и монографий [152—159]. Различают три основные области протекания каталити ческих процессов: кинетическую, внешнедиффузионную и внутридиффузионную и соответствующие переходные области.
В кинетической области скорость процесса определяется только скоростью химического превращения, а в диффузионных областях она лимитируется скоростью подвода реагирующих веществ к внеш ней или внутренней поверхности катализатора и соответственно скоростью отвода продуктов реакции. При очистке газов реакции протекают главным образом в диффузионных областях.
Количественно скорость реакции, протекающей во внешнедиф фузионной области, определяется законом Фика и выражается уравнением скорости реакции первого порядка. Для уменьшения внешнедиффузионного торможения необходимо увеличивать ли нейную скорость газового потока через слой катализатора.
Явления внутридиффузионного торможения связаны с пористой структурой катализаторов. Следует различать два типа диффузии — молекулярную и кнудсеновскую. Первый тип диффузии характерен для крупных пор, размеры которых превышают среднюю длину свободного пробега молекул. Поскольку длина свободного пробега обратно пропорциональна давлению, то чем больше давление, тем меньше скорость диффузии, т. е. тем труднее молекулам достигнуть внутренней поверхности катализатора.
Кнудсеновская диффузия протекает в тонких порах, причем коэффициент диффузии снижается прямо пропорционально умень шению диаметра капилляра. Особое значение этот тип диффузии имеет для процессов, проходящих при низких давлениях, а под давлением около 29,4 МПа (300 кгс/см2) она становится заметной лишь в порах размером порядка 1 0 '7 см.
При сопоставлении скоростей химического превращения и диф фузии реагирующих веществ внутри зерен катализатора было сде лано заключение [149, 159, 160] об оптимальной пористой структуре катализатора. Для медленнопротекающих реакций, когда скорость диффузионного переноса значительно превышает скорость химиче ского превращения, выгоден катализатор с тонкопористой структу рой. Для быстрых реакций, когда скорость химического превраще ния в глубине зерен заметно ниже, чем на их внешней поверхно сти, наиболее выгодньР катализаторы с размером пор, близким к средней длине свободного пробега реагирующих молекул (при атмосферном давлении — порядка 10' 5 см, при 29,4 МПа — около
1 0 ' 7 см).
Особенно эффективен в данном случае катализатор неоднородной структуры с крупными порами, превышающими длину свободного пробега, к стенкам которых примыкают короткие тонкие капилляры, отличающиеся большой поверхностью. В таких условиях скорость
реакции увеличивается в 1 0 — 100 раз по сравнению со скоростью процесса на катализаторе с однородной пористой структурой. При высоких давлениях, когда даже в самых тонких порах коэффи циент диффузии не зависит от их размера, наличие крупных пор не дает положительного эффекта и оптимальной является однородная тонкопористая структура.
Создание катализатора с оптимальной пористой структурой — весьма сложная задача, легче всего она может быть решена на ран них стадиях его приготовления. Явление внутридиффузионного торможения приводит к тому, что не весь объем зерна катализатора участвует в реакции. Толщина работающего слоя может быть опре делена путем сопоставления удельных каталитических активностей в кинетической и диффузионной областях. В условиях промышлен ной эксплуатации катализаторов чаще всего используется не более 20—40% объема зерна катализатора. Из этого следует, что для сни жения влияния внутридиффузионного торможения необходимо уве личивать геометрическую поверхность катализаторов. Наиболее простым способом такого увеличения является уменьшение размеров зерна катализатора. Однако это приводит к возрастанию сопроти вления слоя катализатора, так как оно обратно пропорционально доле свободного объема в третьей степени.
В последнее время все шире стали применяться катализаторы в виде полых цилиндров, фигурных кусочков, монолитов по типу пчелиных сот и т. д. Кроме того, ведутся работы по созданию контакт ных аппаратов с малым гидравлическим сопротивлением, например реакторы с радиальным ходом газа.
Наряду с активностью и пористой структурой промышленных катализаторов к важнейшим их свойствам относятся стабильность, селективность, или избирательность действия, прочность, насыпная плотность. Стабильность катализаторов определяется устойчивостью к длительному воздействию температуры (при которой проводится процесс), а также компонентов газовой смеси, отравляющих катали затор.
Под прочностью катализаторов обычно подразумевают раздавли вающее усилие по торцу или по образующей гранулы, отнесенное к единице площади поперечного сечения гранулы. Реже прочность характеризуется степенью истираемости кусочков катализатора. Оба показателя влияют на срок службы катализаторов. Избиратель ность действия катализаторов характеризуется массовым соотно шением между целевым и побочным продуктами. Основные характе ристики катализаторов определяются их химическим составом и спо собом приготовления и, следовательно, закладываются при их про изводстве [149]. Однако сохранение высокого качества катализатора на протяжении всего периода эксплуатации достигается только в ре зультате соблюдения всех необходимых норм его эксплуатации. Са мый высококачественный катализатор может быть выведен из строя в течение короткого времени из-за парушения требуемых правил обращения с катализатором. Для каждого промышленного катали-
затора существуют определенные требования транспортирования, загрузки, восстановления и пассивации, а также его эксплуатации.
Протекание побочных реакций при очистке газа нежелательно, так как это усложняет технологическую схему процессов. Насыпная плотность зависит от химического состава и условий формирования катализатора. Эта величина учитывается при расчете контактных аппаратов.
Большинство катализаторов подвергается восстановлению, которое осуществляется при приготовлении катализаторов или непосредствен но в контактных аппаратах. Процесс восстановления оказывает боль шое влияние на формирование активной поверхности катализатора.
В последние годы все более широко используются каталитические методы очистки промышленных газов, поэтому большинство иссле дований посвящено созданию новых и усовершенствованию уже суще ствующих катализаторов. Предвидение каталитического действия имеет такой же смысл, что и предсказание скорости химических реакций, но более сложно из-за участия в процессах дополнительного компонента — катализатора. Поэтому приемы подбора катализа торов весьма разнообразны и основаны на эмпирических или полуэмпирических методах [149—151] с использованием эксперименталь ных данных о взаимодействии реагирующих веществ с катализато ром (энергия и энтропия хемосорбции, состав и строение продуктов поверхностного взаимодействия, полярность образующихся связей и т. д.). Перспективность этого пути обусловлена прогрессом в обла сти физических методов исследования хемосорбции и катализа.
К основным недостаткам каталитических методов очистки отно сятся следующие:
образование в.результате каталитической реакции новых веществ, которые удаляют из газа путем их химического связывания, мето дами адсорбции или абсорбции. В результате из-за необходимости дополнительного удаления продуктов реакции часто снижается эффект очистки. Поэтому при разработке каталитических методов следует предусмотреть, чтобы образующиеся вещества легко выво дились из системы;
участие целевого продукта в каталитических реакциях процесса очистки (например, водород при очистке азотоводородной смеси).
Основное достоинство каталитических способов — возможность достижения высокой степени очистки [152, 153]. Предел чистоты газа, который может быть достигнут при каталитическом методе, определяется условием химического равновесия протекающей реак ции при данных температуре и давлении. В большинстве случаев константы равновесия реакций, на которых основаны методы катали тической очистки газов в производстве аммиака, очень велики (дан ные по равновесию приведены в главах, где рассматриваются про цессы очистки газов от отдельных примесей). При температурах 100— 500 °С процессы можно рассматривать как практически необратимые, что дает возможность получать газ с низким остаточным содержа нием примесей.
7 Заказ 1460 |
97 |
1.Криневский И. Р. Фазовые равновесия в растворах при высоких давлениях. М., Госхимиздат, 1952. 169 с.
2.Hildebrand J. Я ., Scott R. L. The Solubility of Nonelectrolyses. New Jercey,
|
Reinhold Publ. Corp., |
1950. |
440 p |
Idem. Regular Solutions. New |
Jercey, |
||||||||
3. |
Prentice-Hall, |
1962. |
180 p. |
|
П ., |
Хим. пром., 1962, № |
9, с. 29— 33 |
||||||
Лейтес |
И. |
Л ., |
Ивановский Ф. |
||||||||||
4. |
Лейтес |
И . |
Л ., |
Ивановский Ф. |
П ., |
ЖФХ, 1965, т. 39, № |
6 , с. 1511 |
||||||
5. |
Wilhelm |
Е., Battino R., |
J. |
Chem. |
Thermodyn., 1971, |
v. 3, |
p .761 —768; |
||||||
|
Chem. Rev., 1973, v. 73, № 1, p. 1—9; Seglor J. Я ., Battino i?., J. Ph\s. |
||||||||||||
|
Chem., |
1958, |
v. 62, |
p. 334—342. * |
|
|
v. 61, p. 1078—1084. |
|
|
||||
6 . Clever H . L., Battino |
Я ., J. Phys. Chem., 1957, |
|
|
||||||||||
7. |
Pierotti R. A ., J. Phys. Chem., 1963. v. 67, p. 1840; 1965, |
v. 69, p. 281—285. |
|||||||||||
8 . Кузнецова E. M., ЖФХ, 1973, T . 47, |
№ |
1, c. 231—233. |
|
1973, |
т. 7. |
||||||||
9. |
Лейтес И. Л., |
Сергеева Л . В., Теорет. |
основы |
хим. технол., |
№ 5, с. 691—697.
10.Рид Р.у Шервуд Т. Свойства газов и жидкостей. Пер. с англ. Под ред.
В.Б. Когана. Л., «Химия», 1971. 702 с.
11.Справочник по растворимости. Т. 1, кн. 1 и 2. Под ред. В. В. Кафарова, М., «Химия», 1969. 3012 с.
12.Клямер С . Д . , Газ. пром., 1971, № 9, с. 38—45.
13.Acmapuma Дж. Массопередачи с химической реакцией. Пер. с англ. Под ред. Л. А. Серафимова. Л., «Химия», 1971. 224 с.
14.Данквертс П . В. Газожидкостные реакции. Пер. с англ. Под ред. И. А. Гиль-
денблата. М., «Химия», 1973. 296 с.
45.Лейтес Я . Л. и др. Теорет. основы хим. технол., 1972, т. 6 , № 1, с. 29—36;
Лейтес И. Л ., Карпова Ю. Г., Бродянский В. М ., Теорет основы хим.
технол., |
1973, |
т. 7, № |
1, с. 231—233; Лейтес И. Л ., |
Дымов В . Я., Кар |
пова Ю. |
Г., |
Теорет. |
основы хим. технол., 1976, |
т. 10, № 5, с. 678— |
690. |
|
|
|
|
16.Бродянский В. М ., Эксергетический метод термодинамического анализа. М., «Энергия», 1973. 296 с.
17.Рамм В . М . Абсорбция газов. Изд. 2-е. М., «Химия», 1976. 655 с.
18.Касаткин А. Г. Основные процессы и аппараты химической технологии. Изд. 9-е. М., «Химия», 1973. 750 с.
19.Левин В . Г. Физико-химическая гидродинамика. Изд. 2-е. М., Физматгиз, 1959. 669 с.
20.Аксельрод Ю. В ., Дильман В . В ., Фурмер Ю. В ., Теорет. основы хим.
технол., 1971, т. 5, № 5, с. 676—683.
21. Гильденблат И. А ., Родионов А. И,, Демченко Б . Я ., ДАН СССР, 1971,
т.198, № 6 , с. 1389-1392.
22.Дильман В. В ., Аксельрод Ю. В., Хуторянский Ф. М., Хим. пром., 1976,
№9, с. 693 -695 .
23. Miyachi Г., Vermeulen Г., Ind. Eng. Chem., Fundament., 1963, v. 2, № 2,
p. 113—126.
24.Sleicher С. A ., A. I. Ch. E. Journal, 1959, v. 5, № 2, p. 145—149.
25.Danckwerts P. F., Chem. Eng. Sci., 1953, v. 2, № 1, p. 1—13.
26. |
Дильман В. В ., |
Теорет. основы хим. |
технол., 1967, т. |
1, № 1, с. 100—104. |
27. |
Van Krevelen D. |
W., Hoftijzer P . / . , |
Rec. trav. chim., |
1948, v. 67, № 9/10, |
p. 563—586.
28.Кишиневский M . X ., Теорет. основы хим. технол., 1967, т. 1, № 6 , с. 759— 775.
29.Аксельрод Ю. В ., Дильман В. В ., Юдину, Л . А ., Теорет. основы хим. тех
нол., 1973, т. 1\ № 3, с. 3 2 0 -327 .
30.Secor В. Л/., Beutler / . А ., А. I. Ch. Е. Journal, 1967, v. 13, № 2, р. 365— 373.
31. Кишиневский М. X ., ЖПХ, 1954, т. 27, № 4, с. 450—454.
32.Аксельрод Ю. В ., Дильман В. В ., Вайнберг А. М ., Теорет* основы хим* технол., 1970, т. 4, № 6 , с. 845—852.
33. |
Brian P. L. Г., Beaverstock M. C., Chem. Eng. Sci., 1965, v. 20, N° 1 , p. 4 7 — |
|
56. |
34. |
Кишиневский M. X ., Армаш A. C.y ЖПХ, 1966, T . 39, № 7, c. 1487—1492. |
35.Кишиневский M. X ., Корниенко T. C., Попа T. Af., Теорет. основы хим. технол., 1970, т. 4, № 5, с. 671—678.
36.Фурмер Ю. В ., Аксельрод 10. В ., Дилъман В. В ., Теорет. основы хим. тех нол., 1971, т. 5, № 1, с. 134—136.
37.Аксельрод Ю. В ., Дилъман В. В ., Фурмер Ю. В ., Теорет. основы хим. тех нол., 1973, т. 7, № 5, с. 683—689.
38. |
Фурмер Ю . В., |
Аксельрод Ю. В ., Дилъман В. В ., |
ЖПХ, |
1973, т. 46, |
№ 7, |
39. |
с. 1508-1511. |
Vivian J . Е ., Matiatos D. С., А. |
I. Ch. |
Е. Journal, |
1967, |
Brian Р. L . 7\, |
v. 13, № 1, р. 28—36.
40.Danckwerts Р . F., McNeil К . A/., Trans. Inst. Chem. Eng. (L.), 1967, v. 45, № 1, p. T 32-T 49.
41.Шкляр P. JI., Аксельрод Ю. В., Соколинский Ю. А ., Теорет. основы хим. технол., 197В, т. 10, № 4, с. 531—539.
42.Шкляр Р . Кандидатская диссертация. М., МХТИ, 1973.
43.Аксельрод Ю. В ., Дилъман В . 5 ., Труды ГИАП, 1971, вып. 10, с. 187—205.
44.Гильденблат И. А ., Теорет. основы хим. технол., 1968, т. 2, N° 4, с. 637— 638.
45.Хутпоряпский Ф. М. и др., Коллоид, журн.,. 1974, т. 36, № 4, с. 814—817.
46.Хуторянский Ф. Af., Аксельрод Ю. 5 ., Дилъман В . В ., ЖПХ, 1975, т. 48, N° 1, с. 72—77.
47. Шнеерсон A. JI., Лейбу ш А. Г., ЖПХ, 1946, т. 19, N° 9, с. 869—879.
48.Ellis J . Е., Trans. Inst. Chem. Eng., 1960, v. 38, N2 4, p. 216—224.
49.Teller A - Ford H. E ., Ind. Eng. Chem., 1958, v. 50, N2 8 , p. 1201—1206.
50. Morris D. B ., Watkins S . В ., Brit. Chem. Eng., 1957, v. 2, N2 2, p. 79—8 6 .
51.Лозин M. E ., Tapam Э. Я ., Марариу И ., Изв. вузов. Химия и хим. технол., 1964, т- 7, N2 2, с. 240-245.
52. |
Шкляр Р • |
Аксельрод Ю. В ., Хим. пром., 1972, |
N2 3, с. 198—202. |
||
53. |
С е м е н о в а Т. А. и |
др. Очистка технологических газов. М., |
«Химия», 1969, |
||
54. |
392 с. |
Л. В ., |
Кандидатская диссертация. М., |
ГИАП, |
1975. |
А л е к п е р о в а |
55.Leva A/*» Tower Packing and Packed Tower Design. Ed. 2nd. Akron (Ohio), US Stoneware CO., 1953. 232 p.
56. Teutsch T., «Chemie Ingenieur Technik», 1964, Bd. 36, N2 5, S. 496—503.
57.Kast «Chemie Ingenieur Technik», 1964, Bd. 36, N2 5, S. 464—468.
58.Field J - A. , Chem. Proc. Eng., 1959, v. 40,*N2 9, p. 310—311.
59.Chem. Eng. Progr., 1958, v. 54, N2 1, p. 83.
60. АлекпеРооа Л. В ., Аксельрод Ю. В ., Дилъман В. В ., Хим. пром., 1974, N2 5, с- 380-384.
61.Дильмвн В- В-, Алекперова Л. В ., Аксельрод Ю. В. В кЬ.: III Всесоюзная конференДия по теории и практике ректификации. Часть 2 . Северодонецк,
62. |
1973, |
с• 136—140. |
Рамм В. М ., ЖПХ, |
1960, т. 33, |
|||
Жавор0нков Н. М ., Гильденблат И . А ., |
|||||||
63. |
N2 8 , * 1790-1800. |
|
N2 |
7, с. 203—210. |
|||
Касат1*ин А. -Г., |
Ципарис И. Н. , Хим. пром., 1952, |
||||||
64. |
Danckverts Р • Рч |
А. I. Ch. Е. Journal, 1955, v. 1, N2 4, |
р. 456—463. |
||||
65. |
НоШЫТ Р • 1ч Van Krevelen D. W., Trans. Inst. Chem. |
Eng., |
1954, v. 32, |
||||
|
№ 1, p- 30—67. |
|
|
Газ. пром., |
1968, т. 13, |
||
6 6 . АкселъР0^ В). В ., Дилъман В. В ., Алекперова Л. В ., |
|||||||
67. |
N2 8 , С- 37—39. |
|
|
|
1971. |
|
|
Фурмер Ю. В., Кандидатская диссертация. М., ГИАП, |
|
||||||
6 8 . КафарОв В. В. |
Основы массопередачи. |
ИзД. 2-е. |
М., |
«Высшая школа», |
|||
69. |
1972. |
А94 с* |
|
|
|
|
|
Розен A- Af., Аксельрод Л. С., Дилъман В. В., Теорет. основы хим. технол., |
|||||||
70 |
1967, |
1» № 4, |
с. 446—458. |
основы хим. технол., |
1973, т. 7, |
||
Кабаков М. И ., |
Дилъман В. В., Теорет. |
||||||
|
N2 4, |
(/* 539—549; N2 6 , с. 815—824. |
|
|
|
|
71.Тительман Л. Я ., Дин Вэй, Аксельрод Ю. В., «Химическое и нефтяное машиностроение», 1970, № 6 , с. 15—16.
72.Аксельрод 10. В ., Дильман В. В., Алекперова Л. В., «Труды ГИАП», 1971, вып. 6 , с. 261—262.
73.Дильман В. В ., Сергеев С. П ., Генкин В . С., Тео'рет. основы хим. технол., 1971, т. 5, № 4, с. 564—571; Инж. физ. журнал, 1974, т. 27, № 4, с. 588— 595.
74. |
Аксельрод Ю. В ., |
Дильман В . Б ., |
Орлов Ю . А ., Хим. пром., |
1967, |
№ |
4, |
||||
|
с. 291—294; в кн.: Химия и технология азотных удобрений. Процессы и аппа |
|||||||||
75. |
раты (информационное сообщение). М., изд. ОНТИ, 1969, с. 10—19. |
|
|
|||||||
De Maria |
F., White R . Б ., A. I. Cn. E. Journal, 1960, v. 6 , № 3, p. 473—481. |
|||||||||
76. |
McHenry |
K. W., |
Wilhelm R. H., A. I. Ch. E. Journal, |
1957, |
v. 3, |
№ |
1, |
|||
77. |
p. 83—91. |
Potter О. Б., |
Trans. |
Inst. Ghem. Eng., 1965, |
v. 43, |
№ |
1, |
|||
Sinclair R. I., |
||||||||||
|
p. 3—9; |
Gray |
R. / ., Prados |
J. W., |
A. I. Ch. E. Journal, |
1963, |
v. 9, |
№ |
2, |
|
78. |
р. 211-216. |
|
|
|
|
1968, т. 41, № |
И, |
|||
Дильман В. В ., Аксельрод 10. В ., Жиляева Т. А ., ЖПХ, |
||||||||||
79. |
с. 2488-2494. |
|
|
|
|
1966, |
v. 5, |
№ |
1, |
|
£ater F. Е ., Levenspiel О., Ind. Eng. Chem., Fundament., |
||||||||||
80. |
p. 8 6 -9 2 . |
|
E ., Kawabe A ., |
Chem. Eng. (Japan), |
1959, |
v. 23, |
№ |
2, |
||
Otake T K u n u g i t a |
р. 81 -85; 1962, v. 26, № 7, p. 800—806.
81.Смыслов M. H., Балле Б. ikf., Теорет. основы хим. технол., 1970, т. 4, № 6 ,
с.932-933.
82.Терловская Т. Б., Кац ,М. Б ., Генин Л . С. В кн.: III Всесоюзная конфе ренция по теории и практике ректификации. Часть 2. Северодонецк, 1973,
с.181-184.
83.Кафаров В. В ., Шестопалов В. В ., ЖПХ, 1964, т. 37, № 11, с. 2461—2468.
84. Малюсов В. А ., Жаворонков Н . М ., Малофеев Н. А ., Хим. пром., 1962,
№7, с. 519—529.
85.Олевский В. М., Ручинский В. Б., Ректификация термически нестойких продуктов. М., «Химия», 1972. 200 с.
8 6 . |
Тительман Л. И ., |
Дильман В . Б ., Аксельрод Ю. Б ., |
Хим. |
пром., |
1976, |
||||||||
87. |
№ 7, с. 533—535. |
|
|
|
|
|
|
4, |
с. 295—297. |
|
|
||
Айзенбуд М. Б ., Дильман В. Б ., Хим. пром., 1963, № |
1965, |
||||||||||||
8 8 . Вевиоровский М. М., Дильман Б. Б ., Айзенбуд М. Б ., |
Хим. |
пром., |
|||||||||||
89. |
№ 3, с. 204—206. |
Шульц Э. 3., |
Драчева Н. Н . |
Авт. |
свид. № 297368; |
||||||||
Тительман Л. И ., |
|||||||||||||
V |
Открытия. Изобр. Пром. образцы. Товарн. знаки, 1971, № 10. |
№ |
7, |
||||||||||
90. |
Сум-Шик Л. Б., |
Аэров |
М . Б., |
Быстрова |
Т. А ., |
Хим. |
пром., |
1962, |
|||||
91. |
с. 530—532. |
Аэров |
М . Э . , |
Быстрова |
Т. А . , |
Хим. |
пром., |
1963, |
№ |
1, |
|||
Сум-Шик Л. Б., |
|||||||||||||
92. |
с.,63—68. |
Даровских Б. Я ., |
Аэров |
М. Б., |
Хим. |
йром., |
1956, |
№ |
3, |
||||
Дильман В. Б ., |
с. 156—161.
93.Касаткин А. Г., Дытнерский 10. Я ., Попов Д . М ., Хим. пром., 1961, № 7,
с.482—491.
94.Родионов А. И. Докторская диссертация. М., МХТИ, 1969.
95.Балл Б. М., Аксельрод Ю. Б ., Сурков Б. Я . В кн.: Процессы химической технологии. Гидродинамика, тепло- и массопередача. Под ред. М. Е. Позина.
М.—Л., «Наука», 1965, с. 49—58.
96. Касаткин А. Б., Дытнерский Ю. Я ., Умаров С. Я ., Хим. пром., 1958,
№3, с. 166-173.
97.Дильман В. В., Сенькина Б. Б ., «Химия и технология топлив и масел», 1964, № 8 , с. 46—49.
98.Аксельрод Л . С., «Труды ВНИИКИмаш», 1956, вып. 1, с. 22—36.
99. Аксельрод Л. С., Дильман В. Б ., «Кислород», 1950, № 6 , с. 9—16; 1951,
№4, с. 2 0 -2 7 .
100.Позин М. Б. u dp. Пенный способ обработки газов и жидкостей. Л., Госхимиздат, 1955. 248 с.
101.Позип М. Д., Мухленов И. Л ., Тарат Э . Я . Пенные газоочистители, теплообменники и абсорберы. Л., Госхпмиздат, 1959. 123 с.
102.Соломаха R. П- Докторская диссертация. М., МИХМ/ 1969.
103.Киселев А , J ШФХ, 1949, т: 23, № 4, с. 452-459.
104.Трепнел В. Хемосорбция. Пер. с англ. Под ред. А. В. Киселева. М., Издатинлит, 1958. 326 с.
105.Курс физической химии. Под ред. Я. И. Герасимова. Т. 2. М., Госхпмиздат, 1973. 623 е.
106.Рачинский В. В. Введение в общую теорию динамики сорбции и хромато графии. М., «Наука», 1964. 137 с.
107.Дубинин Jlf0 М. Физико-химические основы сорбционной техники. М., изд. ОНТй ГИАП, 1935, 537 с.
108.Кржиль Фч Исследование и оценка технических адсорбционных веществ. Киев, 1933 369 с.
109.Дубинин М. М., ЖПХ, 1961, т. 34, № 2, с. 291-299.
110. Дубинин М. М., Заверина Е. Д., ЖПХ, 1961, т. 34, № 1, с. 113—129.
111.Киселев А. В ., Коллоид, журн., 1936, т. 2, с. 17—23.
112.Киселев А. В ., ДАН СССР, 1954, т. 38, с. 427—434.
ИЗ. Щербаков К. Д. В кн.: Поверхностные химические соединения и их роль
в явления* адсорбции. М., изд^ МГУ, 1957, с. 175—179.
114.Киселев А. В. и др., ЖФХ, 1945, т. 19, с. 83—87.
115. |
Боресков |
Г. К • и др., ДАН СССР, |
1948, т. 62, с. 649—652. |
|
|
|||||
116. |
Неймарк Л. Е., Шейнфайн Р. Ю., Укр. хим. журн., 1949, т. 14, с. 24—30. |
|||||||||
117. |
Shapiro |
Kolthoff М., J. Am. Chem. Soc., |
1950, v. 79, p. 776—782. |
|||||||
118. |
Nordstand |
R. H., |
Van Kreger W. E ., |
Ries |
H. E-, |
J. Phys. |
Coll. |
Chem., |
||
119. |
1951, v. 55, p. 621-638. |
|
|
|
|
|
|
|
||
Никитин Ю. С. |
В кн.: Поверхностные химические соединения и их роль |
|||||||||
120. |
в явления* адсорбции. М., изд. МГУ, 1957, с. 170—175. |
|
|
|||||||
Дубинин |
М. М ., Зуев А. Г ., ДАН |
СССР, 1949, т. 64, с. 209—214. |
т. 23, |
|||||||
121. |
Дубинин |
М. М., |
Заверина Е. Д ., |
Тимофеев Д . Я ., |
ЖПХ, |
1949, |
||||
122. |
№ 10, с. 1129—1136. |
ОХН, 1961, № 7, |
с. 1183—1191. |
|
||||||
Дубинин |
М. М.,Изв. АН СССР, |
№ 8 , |
||||||||
123. |
Дубинин |
М. М ., Заверина Е . Д. |
и др., |
Изв. АН СССР, ОХН, |
1961, |
с. 1380—1387.
124.Дубинин М. М., Жуковская В . Г., Мурдмаа К. О., Изв. АН СССР, ОХН, 1962, № 6 , с. 960—968.
125.Дубинин М. М., Жуковская Е . Г ., Мурдмаа К. О., Изв. АН СССР, ОХН, 1962, № 5, с. 760—769.
126. |
Дубинин |
М. М. и др. Изв. |
АН |
СССР, ОХН, 1962, № 12, с. 2121—2129. |
|||
127. |
Дубинин |
М. М.,Изв. АН СССР, |
ОХН, 1964, |
№ 2, с. 209—215. |
|||
128. |
Дубинин |
М. М. и |
др., Изв. |
АН |
СССР, ОХН, |
1964, № 9, |
с. 1565—1573. |
129. |
Дубинин |
М. М. и |
др., Изв. |
АН |
СССР, ОХН, |
1964, № 9, |
с. 1573—1580. |
130.Дубинин М. М. и др.., Изв. АН СССР. Сер. хим., 1965, № 10, с. 1731— 1739.
131.Кофман Л. С., Виноградова В. С., Изв. АН СССР. Сер. хим., 1965, № 6 ,
с.975 -984.
132.Липкинд Б. А. и др. В кн.: Синтетические цеолиты. М., изд. АН СССР,
1962, с. 191-193.
133.Дубинин М . М ., Жукова 3 . А ., Келъцев Н . В. Там же, с. 7—12.
134.Иру Я ., Грубнер О., Раллек Н. Там же, с. 129—134.
135.Беринг Б. Я. и др., ДАН СССР, 1960, т. 131, с. 865—867.
136.Боресков Г. К . Катализ. Ч. I, II. Новосибирск, «Наука», 1971. 267 с.
137.Сокольский Д. В ., Друзь В. А . Теория гетерогенного катализа (Введение). Алма-Ата, «Наука», 1968. 390 с.
138.Ашмор Я. Катализ и ингибирование химических реакций. Пер. с англ. Под ред. А. М. Рубинштейна. М., «Мир», 1966. 504 с.
139. Темкин М . Я . и др., ЖФХ, 1939, т. 13, № 7, с. 851—867; 1941, т. 15,
№3, с. 296—332.
140.Темкин М. Я ., «Кинетика и катализ», 1967, т. 8 , № 5, с. 1005—1019; ЖФХ, 1957, т. 31, № 1 , с. 3—26.
141.Киперман С. Л . Введение в кинетику гетерогенных каталитических реак ций. М., «Наука», 1964. 607 с.
142.Боресков Г. К . В кн.: Проблемы кинетики и катализа. Т. 6 . М*, изд. АН СССР, 1949, с. 404—425.
143.Боресков Г . Я ., Хим. пром., 1947, № 8 , с. 1—6; № 9, с. 5—11.
144.Ройтер В, А. В кн.: Проблемы кинетики и катализа. М., изд. АН СССР,
1949, с. 357—362; «Кинетика и катализ», 1962, т. 3, № 4, с. 602.
145. |
Иоффе И. # . , Писмен Л . Н . |
Инженерная химия гетерогенного катализа. |
|||
146. |
М., «Химия», 1965. 456 с. |
|
|
||
Шервуд Т. Я ., Теорет, основы хим. техпол., 1967, т. 1, № 1, с. 17—30. |
|||||
147. |
Боресков |
Г. Я., В кн.: Пористая структура катализаторов и процессы пере |
|||
|
носа в гетерогенном катализе. Под |
ред. Г. К. Борескова. Новосибирск, |
|||
148. |
«Наука», |
1970, |
с. 5—15. |
О. А ., |
Бесков В . 67., Хим. пром., 1967, № 9, |
Слинъко |
М . Т7., |
Малиновская |
с.641-646.
149.Технология катализаторов. Под ред. И. П. Мухленова. Л ., «Химия», 1974. 325 с.
150.Научные основы подбора катализаторов гетерогенных каталитических реакций. М., «Наука», 1966. 245 с.
151.Селвуд Л . , Берелл Р ., Эейшенс Р. В кн.: Новые методы изучения гетеро генного катализа. Пер. с франц. Под ред. А. А. Баландина. М., Издатинлит, 1963. 104 с.
152.Боресков Г . Я ., «Кинетика и катализ», 1962, т. 3, № 5, с. 633—642.
153.Власенко В . М . Каталитическая очистка газов. Киев, «Техшка», 1973. 199 с.