
- •ИЗДАНИЕ ВТОРОЕ, ПЕРЕРАБОТАННОЕ И ДОПОЛНЕННОЕ
- •ОСНОВНЫЕ СХЕМЫ ПРОИЗВОДСТВА ГАЗА ДЛЯ СИНТЕЗА АММИАКА
- •ОСНОВЫ ПРОЦЕССОВ ОЧИСТКИ ГАЗОВ
- •Циркуляционные процессы
- •ОЧИСТКА ПРИРОДНОГО ГАЗА ОТ ВЫСШИХ УГЛЕВОДОРОДОВ
- •АБСОРБЦИОННЫЕ МЕТОДЫ ОЧИСТКИ ГАЗОВ ОТ ДВУОКИСИ УГЛЕРОДА И СЕРНИСТЫХ СОЕДИНЕНИЙ
- •Примеры расчета абсорберов МЭА-очистки
- •Катализаторы
- •Кинетика и механизм процесса гидрирования
- •Аппаратурно-технологическое оформление процесса
- •АБСОРБЦИОННЫЕ СПОСОБЫ ОЧИСТКИ ГАЗОВ ОТ СЕРНИСТЫХ СОЕДИНЕНИЙ
- •ОЧИСТКА ГАЗОВ ОТ ОКИСИ УГЛЕРОДА
- •КАТАЛИТИЧЕСКИЕ И АДСОРБЦИОННЫЕ МЕТОДЫ УДАЛЕНИЯ ИЗ СИНТЕЗ-ГАЗА КИСЛОРОДСОДЕРЖАЩИХ СОЕДИНЕНИИ
- •Катализаторы
- •Аппаратурно-технологическое оформление
- •Катализаторы
- •2. ТОНКАЯ ОЧИСТКА ОТ ДВУОКИСИ УГЛЕРОДА МЕТОДОМ АДСОРБЦИИ
- •ОЧИСТКА ГАЗОВ ОТ ОКИСИ АЗОТА И АЦЕТИЛЕНА
- •2. СПОСОБ ОЧИСТКИ ОТ ОКИСИ АЗОТА И АЦЕТИЛЕНА МЕТОДОМ КАТАЛИТИЧЕСКОГО ГИДРИРОВАНИЯ
- •АБСОРБЦИОННЫЕ МЕТОДЫ ОЧИСТКИ ГАЗОВ ОТ АЦЕТИЛЕНА
- •Очистка пирогаза от сажи
гидрируется легче, чем 1,2-дигидротиофен, а последний — легче тиофена. Способность индивидуальных соединений серы к реакции гидрирования увеличивается в следующей последовательности: тио фен, меркаптаны жирного ряда, сероуглерод, меркаптаны бензоль ного ряда, сероокись углерода.
Для процесса гидрирования сероорганических соединений водо родом необходимо присутствие И 2 в очищаемом газе, а при очистке путем взаимодействия с водяным паром — присутствие в газе водя ного пара. Водород, как известно, часто входит в состав технологи ческих газов, дозировка его не представляет трудностей. В схемах
Рис. V-7. Изменение равновесных кон стант гидрирования некоторых серо органических соединений в зависимости от температуры:
1 — диметилдисульфид; 2 — тиофен; з — диэтилсульфид; 4 — тетрагидротиофен; 5 — метилмеркаптан; 6 — фснилмеркаптан.
синтеза аммиака к очищаемому газу можно добавлять не чистый водород, а азотноводородную смесь.
Очистку, основанную на взаимодействии сероорганических со единений с водяным паром, обычно совмещают с конверсией окиси углерода. Процесс ведут на таких же катализаторах, что и конвер сию СО. В связи с широким применением природного газа как техно логического сырья для синтеза аммиака этот метод сероочистки используется очень редко.
Катализаторы
Наиболее распространенными для процесса гидрирования серо органических соединений являются катализаторы на основе железа, кобальта, никеля, молибдена, меди, цинка [1, 10, 67—72]. Из вестны также катализаторы на основе благородных металлов [73, 74]. Как отдельный класс можно рассматривать катализаторы на ос нове модибдатов и тиомолибдатов [64]. Анализ литературных данных показывает, что наибольшей активностью обладают катализаторы на основе металлов VIII группы периодической системы.
Состав катализаторов гидрирования и, следовательно, их актив ность и другие свойства определяются содержанием в реакцион ной смеси сернистых соединений и водорода. Все катализаторы, независимо от их исходного состава, в процессе очистки сульфи дируются в результате взаимодействия присутствующих в газе сернистых соединений с компонентами катализатора. \ При этом
образуются |
такие |
сульфиды, как |
FeS, |
FeS2, NiS, |
Ni3S2, Co9S8, |
|
CoS, Co6S9 |
и др. |
В ряде |
случаев |
сера |
растворяется |
в сульфидах |
металлов с |
образованием |
пиротинов [75]. |
|
Растворениая сера играет важную роль в каталитическом про цессе. Установлено, что активность катализаторов зависит от нали чия в них сульфидов или растворенной серы. Поэтому для получе ния высокоактивных катализаторов при отсутствии в газе серово дорода или сероуглерода рекомендуется специально (хотя бы частило) сульфидировать катализаторы этими газами при темпе ратуре 300—450 °С [1, 76—79]. Особенно большое значение имеет операция предварительного сульфидирования катализаторов, кото рые Используют при гидрировании тиофенов. В ряде случаев про мышленностью выпускаются сульфидированные или частично суль фидированные катализаторы. При протекании реакции гидрирова ния На сульфидах в газе образуется сероводород, в присутствии которого полностью завершается сульфидирование катализатора. В связи с этим в первый период очистки катализаторы гидрирования поглощают практически всю содержащуюся в очищаемом газе серу.
Процесс сульфидирования обратим: при изменении в реакцион ной Смеси соотношения водорода и сернистых соединений из ката лизаторов может выделяться сера. Состав катализатора определяется условиями равновесия систем Me—S—Н 2 или MeO—S—Н 2.
В работах [1, 80] показано, что активный катализатор содержит сульфид кобальта Co9S8 и сульфид молибдена MoS2, концентрация которых составляет 1—4%. Оставшаяся непросульфидированная окись кобальта, по-видимому, предотвращает спекание кристал литов сульфида молибдена и способствует увеличению активной поверхности фазы сульфида молибдена.; На это указывают данные, полученные в работе [80],— дисульфид молибдена, образующийся при сульфидировании катализатора, обладает повышенной дисперс ностью (45 • 10"10 м) по сравнению с полученным из окисла (70 X
X 10" м).
Катализаторы гидролиза сернистых соединений аналогичны катализаторам процесса конверсии в тех случаях, когда очистка совмещается с конверсией окиси углерода. В качестве главного компонента они содержат окись железа. Предложены катализаторы
Нна другой основе [81—83].
Впромышленности наибольшее распространение для процессов
гидрирования получили кобальтмолибденовые и никельмолибдеяовые катализаторы. Это наносные катализаторы. Они содержат, как правило, до 5% СоО и 15% Мо03 и до 10% NiO и 10% Мо03 соответственно. В качестве носителя наибольшее распространение получила активная окись алюминия. Возможны также алюмоси ликатные носители. Катализаторы выпускают как в таблетироканном, так и в формованном виде.
Процесс гидрирования проводится обычно при температуре 300—400 °С, объемной скорости 1000—5000 ч '1 и давлении 0,98 X X 105—39,2• 105 Па (1—40 кгс/см2). Для гидрирования дозируется
2 0 Заказ 14G0 |
3 0 5 |
от 1—2 до 10% водорода. В газе, являющемся источником водорода, не должно содержаться более 5% окислов углерода. Это связано с тем, что последние на катализаторах могут гидрироваться до ме тана, в результате чего увеличивается расход водорода и возрастает температура. Было установлено [84], что если в очищаемом газе присутствуют предельные углеводороды и низшие олефины, то они не оказывают влияния на гидрирование и в процессе участия не при нимают. У
Условия конверсии сернистых соединений в производствах аммиака аналогичны условиям проведения процесса конверсии окиси углерода на железохромовом катализаторе: температура
300—500 °С, |
объемная скорость 300—3000 ч” 1, давление 0,98 X |
X 10ь—39,2 |
• 105 Па (1—40 кгс/см2). |
При очистке коксового газа гидрирование сероорганических соединений протекает труднее, так как его компоненты оказывают влияние на степень гидрирования.
При работе с промышленными газами, в частности с коксовым,, часто наблюдается зауглероживание катализаторов в результате присутствия в газах значительного количества примесей и проте кания побочных реакций. Выделение углерода не происходит лишь при очистке .природного газа.
В связи с тем, что в промышленных газах содержание влаги обычно превышает содержание сернистых соединений, можно счи тать, что наряду с гидрированием частично протекает и конверсия сероорганических соединений.
Кинетика и механизм процесса гидрирования
Исследованию механизма гидрирования* сероорганических со единений на различных катализаторах посвящено много работ. Процесс гидрирования достаточно сложен. Предполагается, что он протекает через ряд промежуточных стадий с образованием побоч ных продуктов. Авторы [85], исследовавшие гидрирование суль фидов и дисульфидов в синтез-газе на катализаторах — окислах Fe, Ni, Со, Mn, Cd, Cr, Mo, V, Al, Mg, показали, что первоначально происходит гидрирование до меркаптана; который затем превра щается в сероводород./В работе [86] исследовано гидрирование метилмеркаптана и тиофена над алюмокобальтмолйбденовым катали затором в интервале температур 200—260 °С. Показано, что реакция гидрирования метилмеркаптана протекает в двух направлениях: 1) гидрирование с образованием метана и сероводорода, 2) диспро порционирование с образованием диметилсульфида и сероводорода.
Максимальная конверсия в метан получена |
над катализатором |
с соотношением атомов кобальта и молибдена 1 |
3, конверсия на та |
ком катализаторе в диметил сульфид минимальна. Тиофен раз
лагается при более |
высокой температуре, |
образуя |
бутан, |
бутены |
и сероводород. Методом изотопного обмена |
[87] над |
MoS2 |
и W Sa |
|
при гидрировании |
этилмеркаптапа было установлено, что |
помимо |
указанных выше двух стадий протекает еще и гидрогенолиз с обра зованием этилена и сероводорода. Этот механизм подтвержден для
промышленного |
алюмокобальтмолибденового и цинкал1рминиево го |
||
катализаторов |
[24]. Однако авторы отмечают, что образование |
||
диэтилсульфида |
протекает |
лишь в незначительной |
степени. |
В работе [88] описан |
механизм гидрирования |
сероуглерода |
и тиофена, изученный с помощью метода меченых атомов на железо хромовом катализаторе. Показано, что каталитически активными к гидрированию сероорганических соединений являются те места решетки, в которых находится растворенная сера (твердый раствор). Первая стадия процесса — восстановление катализатора. Последу ющие стадии включают расщепление органической серосодержащей молекулы с образованием элементарной серы, а затем внедрение этой серы в восстановленные участки катализатора.
Ф. П. Ивановский, В. А. Донцова, Г. С. Бескова [89] исследовали кинетику гидрирования CS2 на сульфидах железа, кобальта и никеля при 220—400 °С и содержании сероуглерода в газе от 1 до 5%. Они получили следующее кинетическое уравнение:
W= kPct
где w — скорость реакции; к — константа скорости; /?CSa — парциальное да вление CS2.
Энергии активации реакций на всех сульфидах близки между собой. На сульфидах кобальта и никеля скорость реакции на по рядок выше, чем на сульфиде железа. Авторы предполагают, что механизм гидрирования на всех трех сульфидах идентичен и носит окислительно-восстановительный характер.
Первый порядок по серосодержащим соединениям (этилмеркаптан, тиофен, сероуглерод) и водороду был получен при их гид
рировании |
в н-гептане на кобальтмолибденовом катализаторе [90]. |
|
Энергия активации при этом равна —20,9 |
кДж/моль (—5 ккал/моль). |
|
В работе, |
выполненной фирмой ICI |
[1], также был получен |
близкий к единице порядок реакции гидрирования по серосодер жащему соединению.1Во всех случаях скорость сероочистки воз растает с увеличением парциального давления водорода. Ско рость гидрирования зависит также от характера углеводородов, присутствующих в очищаемом газе и оказывающих ингибирующее воздействие на процесс. Ингибирующий эффект снижается с умень шением молекулярной массы углеводорода и достигает минимальной
величины для |
метана — 0,05. |
Скорость |
сероочистки возрастает |
с увеличением |
общего давления |
в системе |
в степени от 0,5 до 0,6. |
Аппаратурно-технологическое оформление процесса
В настоящее время коксовый и водяной газы с высоким содер жанием сернистых соединений все меньше используют как химиче ское сырье для производства водорода, аммиака, метанола и др.
Поэтому в настоящей книге схемы очистки коксового и водяного газов не приведены [91].
При очистке природного газа от органических сернистых соеди нений стадию гидрирования применяют в сочетании с адсорбцион ным методом [64, 92]. Контактный аппарат либо устанавливают первым по ходу газа, либо располагают между двумя адсорберами. На рис. V-8 приведена принципиальная схема серооочистки природ ного газа в производстве аммиака с использованием стадии гидри рования сероорганических соединений.
Рис. V-8. Принципиальная схема сероочистки природного газа от органических сернистых соединений:
1 — огневой подогреватель; 2 — контактный аппарат.
Природный газ, содержащий до 40 мг/м3 органических серни
стых |
соединений и |
20 мг/м3 |
сероводорода, сжатый до |
давления |
39,2 |
• 10б—44,1-Ю 5 Па (40—45 кгс/см2), нагревается до температуры |
|||
400 °С. Для нагрева |
в данной |
схеме используют огневой |
подогре |
ватель i , в котором сжигается топливный природный газ. Установка такого подогревателя позволяет осуществлять пуск и налаживание процесса сероочистки независимо от работы всей системы. Перед поступлением природного газа в подогреватель к нему примешивают водород в виде азот-водородной смеси в количестве до 15% (от объема природного газа). В контактном аппарате 2 на алюмокобальтмолибденовом катализаторе при температуре 400 °С и объемной скорости 1000—2000 ч"1 происходит превращение серооргапических соеди нений в сероводород. После аппарата гидрирования газ направляют в адсорбер. Содержание органических сернистых соединений после гидрирования не превышает 1 мг/м3. Контактный аппарат может быть полочного и радиального типа. Конструкции полочного и радиального аппаратов подробно описаны в главе VIII. \[
Каталитическое окисление сероорганических соединений
Метод основан на каталитическом взаимодействии сероорганиче ских соединений с кислородом и образовании легкоудаляемых кислородных соединений серы. Применение этого способа в азотной промышленности осложняется необходимостью дозировки кислорода
иотсутствием высокоселективиых катализаторов для очистки газов-
вприсутствии водорода. Последнее связано с тем, что водород ре агирует с кислородом с высокой скоростью на большинстве катализа
торов [2, 93—95]. В азотной промышленности этот метод пока не нашел применения.
ТОНКАЯ ОЧИСТКА ГАЗОВ ОТ СЕРООРГАНИЧЕСКИХ СОЕДИНЕНИЙ НА АКТИВНЫХ ХЕМОСОРБЕНТАХ
Одним из методов очистки газов от серосодержащих примесей является хемосорбция, основанная на непосредственном связы вании сероорганических соединений при 200—400 °С твердыми по глотителями. Принципиальная схема процесса состоит из двух стадий: нагревания газа и поглощения серы. Тепло газа может быть использовано при его дальнейшей переработке. Для приготовления поглотителей используются окислы цинка, железа, меди.
Очистка поглотителями на основе окиси цинка
Поглощение сероорганических соединений окисыо цинка может быть описано следующими уравнениями:
2ZnO + CS2 = 2ZnS + С02 |
(V ДО) |
* ZnO + СОS = ZnS + С02 |
(V ,ll) |
ZnO + C2H5SH = ZnS + С2И5ОН |
(V ,12) |
ZnO + C2H5SH = ZnS + C2H4+ HoO |
(V,13) |
В табл. V-5 приведены ;значения констант равновесия [17\ реакций (V,10)—(V,12). Термодинамические данные, использо ванные для расчета, взяты из работ [96, 97].
Таблица V-5. Константы равновесия реакций (V, 10) — (V,12) поглощения сероорганических соединений окисыо цинка
|
|
|
Константы |
|
|
Температура, °С |
|
|
|
|
K IM |
|
K t o |
К г г |
|
||
200 |
6,0 • 1019 |
9,9 • 108 |
|
||
300 |
1,1 |
- 1016 |
1,25-107 |
3,63'102 |
|
400 |
2,7 |
• 1013 |
5,8 • |
105 |
7,4 . 102 |
500 |
8,0 |
- ЮН |
6,0 * |
104 |
10,3 • 102 |
600 |
1,0 - 101° |
1,0-104 |
18,6 • 102 |
Термодинамические расчеты показывают, что реакции поглоще ния сероорганических соединений окисью цинка при 400—450 °С практически необратимы, следовательно, возможна полная очистка газа от этих соединений. Как окись цинка, так и продукт реакции —
сульфид цинка |
в восстановительной атмосфере очищаемого газа |
при температуре |
до 400—500 °С вполне стабильны. Термическая |
диссоциация ZnO и ZnS в указанной области температур не на
блюдается (так, при |
400 °С |
константа равновесия диссоциации |
||||
окиси |
цинка |
составляет 10“ 22, а |
константа |
диссоциации ZnS — |
||
40“ 16 |
[98]). |
газы |
почти |
всегда |
содержат |
двуокись углерода, |
Очищаемые |
однако взаимодействие ее с окисью цинка не происходит, так как уже при 200 °С равновесное давление £ 0 2 над углекислым цинком составляет 21,6-105 Па (22 кгс/см2).
В условиях очистки нежелательны реакции восстановления окиси цинка и сульфида цинка компонентами очищенного газа.
Значения констант равновесия этих реакций (от 1,5 • 10“11 до 3,4 X X 10“ 7) и экспериментальные данные подтверждают, что восстано вления ZnO и ZnS в указанном интервале температур не происходит.
Разработанный [18] на основе окиси цинка поглотитель ГИАП-10 не требует предварительной подготовки (восстановления, актива ции и др.). На его сероемкость не влияет содержание соединений серы в газе. Полнота очистки зависит лишь от характера этих со единений. Сероводород, сероокись углерода, сероуглерод и мер каптаны практически полностью удаляются поглотителем ГИАП-10; хуже поглощаются тиофен и органические сульфиды.
Для протекания процесса очистки |
не обязательно присутствие |
водорода в газе, поэтому поглотитель |
пригоден для очистки угле |
водородных газов, не содержащих водорода. При наличии же его |
|
в газах возможна более тонкая, очистка за счет гидрирования высших |
органических соединений серы.
v В процессе очистки коксового газа поглотителем ГИАП-10 при 400 °С и объемной скорости 1000 ч '1 удаляется 92—98% сероорга нических соединений (тиофен плохо удаляется из коксового газа этим методом). Одновременно в указанных условиях происходит очистка газа от ацетилена и кислорода.
Если применять поглотитель ГИАП-10 для очистки водяного газ'а, то достигается степень очистки, близкая к 100%, причем про цесс можно проводить при более низкой температуре (300—350 °С). Это объясняется тем, что органическая сера в водяном газе почти целиком состоит из сероокиси углерода, более реакционноспособной, чем другие сероорганические соединения.
Применение поглотителя ГИАП-10 для очистки природного и попутных газов от сернистых соединений показало, что присут ствие в газе гомологов метана не сказывается на работе поглотителя [18]. При 400 °С достигается тонкая очистка газа (остаточное со держание этилмеркаптана менее 1 мг/м3). При этом не наблюдается заметного изменения состава газа по основным компонентам, а также
повышенного отложения углерода в поглотителе. Дисульфиды поглотителем не сорбируются.
Очистку природного газа осуществляют при давлении 19,6 X X 105—49,0- 10б Па (20—50 кгс/см2). Повышение давления в этих:, пределах не оказывает заметного влияния на степень очистки газа.
В процессе очистки природного и попутных газов нет необхо димости в предварительной конверсии этилмеркаптана в серово дород. Однако при наличии в газах более тяжелых меркаптанов, целесообразно сочетать поглощение на окиси цинка с гидрированием сероорганических соединений.
Применение поглотителей на основе окиси цинка наиболее ра ционально для очистки газов с невысоким содержанием серы, при этом отпадает необходимость регенерации отработанного поглоти теле.
'При очистке газа с высоким содержанием соединений серы отра ботанный поглотитель ГИАП-10 можно регенерировать и исполь зовать повторно без выгрузки из очистного аппарата. Регенерация поглотителя заключается в окислении сульфида цинка кислородом при 500—550 °С. В связи с тем, что процесс регенерации экзотермичен, а перегрев поглотителя.приводит к снижению его активности,, для регенерации следует использовать смесь инертного газа (азота) с воздухом (начальная концентрация кислорода в смеси 0,5%), чтобы скорость выделения серы соответствовала образованию не бо лее 1-10" 2 кгс/м3 газа. Объемная скорость дутья при регенерации 1000-2000 ч"1.
Сероемкость поглотителя после регенерации снижается на '2— 3%. Степень очистки газа регенерированным поглотителем такая жег как свежим.
Установлено, что при нагревании поглотителя выше 500—550 °С понижается его активность, что связано с изменением структуры окиси цийка: уменьшением дисперсности, пористости и удельной поверхности поглотителя.
Разработан низкотемпературный поглотитель ГИАП-10-2 на ос нове окиси цинка с активирующей добавкой окиси меди [26, 27]. Окись меди, полученную прокаливанием основной углекислой меди при 260—280 °С, добавляют [10% (масс.)] на стадии смешения окиси цинка с водой и графитом перед таблетированием. Это по зволяет снизить температуру процесса очистки до 280—300 °С, что уменьшает возможность зауглероживания поглотителя при очистке газов с повышенным содержанием тяжелых углеводородов. По глотитель ГИАП-10-2 предварительно восстанавливают азотоводо родной смесью [27].
Описан способ приготовления модифицированного .катализатора 482-Gu, применяемого на первой стадии очистки газов от серни стых соединений [13] (меркаптанов, сероуглерода, сероокиси угле рода, сероводорода). Отмечено, что этот катализатор имеет доста точно высокую активность и сохраняет механическую прочность при рабочих температурах сероочистки. Приведены сравнительные
характеристики катализаторов 481-Си и 482-Си, полученные в период их промышленных испытаний. Показаны преимущества первого катализатора [99, 100].
За рубежом разработаны и выпускаются в промышленном мас штабе катализаторы на основе активной окиси цинка: G-72 (фирма Gerdler); 29-1; 29-2 и 32-4 (фирма ICI); G-7-1 (фирма GGI); B-ZnO (фирма BASF); ZnO (фирма ONIA) и др. [1, 10, 101, 102]. Харак теристика указанных катализаторов и их некоторые физико-хими ческие и адсорбционные свойства приведены в табл. V-6. Для срав нения здесь же помещены данные по отечественным поглотителям ГИАП-10 и ГИАП-10-2 на основе окиси цинка.
Таблица V-6. Характеристика * катализаторов на основе окиси цинка
Катализаторы (и фир |
Форма и размеры |
мы-производители) |
частиц, мм |
ГИАП-10 (промышл.) |
Таблетки |
|
d — 5 |
|
/г = 3 |
Насыпная плотность, КГ/М* |
Пористость, % |
Удельная поверхность М*/г |
1,6-103 |
55,0 |
32,8 |
►3 _
О о
X®
ЙО
О
с
а х CJ
24,5
ГИАП-10 |
(лаборат.) |
То |
же |
1,5-103 |
39,7 |
50,0 |
31,4 |
|
ГИАП-10-2 (лаборат.) |
» |
2,1-103 |
36,9 |
45,0 |
19,6 (при |
|||
29—2 (ICI, |
Англия) |
Таблетки |
1,9-103 |
30,3 |
35,7 |
250° С) |
||
|
|
|
d = 5 |
|
|
|
20,7 (при |
|
32—4 (ICI, |
Англия) |
h = 5 |
1,2 - 103 |
43,3 |
34,9 |
250° С) |
||
Шарики |
20,2 |
|||||||
ZnO (ONIA, |
Фран |
d = 3 |
1,5-103 |
39,5 |
35,6 |
18,0 |
||
Таблетки |
||||||||
ция) |
|
|
d = |
10 |
|
|
|
|
ZnO+ 2% М о+ 1 % Си |
/г = |
5 |
1,4 • 103 |
37,4 |
|
24,9 |
||
Таблетки |
|
|||||||
(ONIA, |
Франция) |
d = 6 |
|
|
|
|
||
О—7 2 -С |
(Gerdler, |
h = 5 |
1,2-103 |
58,6 |
|
|
||
Шарики |
35,6 |
21,4 |
||||||
США) |
|
|
d - 2 - 3 |
1,44 • Юз |
44,8 |
18,7 |
26,3 |
|
В —ZnO (BASF, ФРГ) |
Формованные |
|||||||
|
|
|
d = 4 |
|
|
|
|
|
ZnO (Чехословакия) |
Л = 5—10 |
1,7-103 |
36,7 |
32,9 |
18,8 |
|||
Таблетки |
||||||||
|
|
|
d = |
10 |
|
|
|
|
N —741 (Nikki, Япо |
Л — 10 |
1,1-103 |
55,3 |
29,2 |
30,2 |
|||
Таблетки |
||||||||
ния) |
|
|
d = 5 |
|
|
|
|
|
|
|
|
h = 4 |
|
|
|
|
* Характеристики получены в результате испытаний, проведенных в ГИАП.
Имеются указания [102], что обработка окиси цинка бикарбо натом 1 аммония повышает сорбционную способность поглоти теля.
Изучена [103] возможность получения активной окиси цинка из металлического цинка длц приготовления; поглотителей сернистых соединений (ГИАП-10 и ГИАП-10-2).
Приведены исследования [104] с целью нахождения таких доба вок к окиси цинка, которые позволили бы очищать газ от соединений серы, не сорбируемых поглотителем ГИАП-10. Приготовлены цин ковые' поглотители с различным содержанием окиси хрома [5, 8,
Рис. V-9. Схема очистки газа на ZnO в сочетании с гидрированием серооргани ческих соединений:
1, 2 — адсорберы с поглотителем; 3 — аппарат гидрирования с кобальтмолибденовым катали затором; 4 — сепаратор; 5 — компрессор.
10, 15 и 20% (масс.)]', железа и алюминия [до 1% (масс.)]. Погло тители с добавками испытаны при температуре 400 °С и объемной скорости 1000 ч"1. Показано, что введение в поглотитель на основе окиси цинка до 1% железа или алюминиц и до 5% окиси хрома позволяет получить более высокую, чем на поглотителе ГИАП-10, степень очистки газа от сернистых соединений.
На опытно-промышленных установках [93] изучена очистка природного газа от сернистых соединений по трех- и двухступен чатой схемам с использованием алюмокобальтмолибдеиового ката
лизатора и цинкмедного |
поглотителя ГИАП-10-2 при температуре |
|||||
320—390 °С, давлении 14,7 • 105—19,6 • 105 |
Па (15—20 кгс/см2) и вы |
|||||
сокой |
скорости |
подачи |
газа. |
Содержание сернистых |
соединений |
|
в очищаемом газе снижено |
с 1,5* 10“ в—8,9 • 10“ 6 до |
0,2 • 10“ ®— |
||||
0,0 кг/bi3 (в пересчете на серу). |
|
|
||||
На рис. V-9 представлена принципиальная двухступенчатая |
||||||
схема |
очистки |
природного |
газа от |
органических |
сернистых |
^соединений с использованием методов гидрирования и поглощением образовавшегося сероводорода на окиси цинка.
Поглотительную очистку рекомендуется проводить в двух по следовательно работающих аппаратах, что позволяет полностью использовать емкость поглотителя по сере и обеспечивает высокую степень очистки газа. Когда снизится степень очистки или пре кратится поглощение серы в первом по ходу газа аппарате, его отключают. Второй аппарат ставят в положение первого и после довательно с ним включают аппарат со свежим поглотителем.
Моделирование процесса поглощения сернистых соединений твердыми поглотителями
Моделирование процесса поглощения сернистых соединений стро жится на общем для гетерогенных процессов подходе, изложенном в гл. VIII применительно к каталитической конверсии окиси угле рода. В отличие от каталитических процессов существенной осо бенностью поглощения является специфически присущая ему неста-
ционарность, связанная |
с исчерпыванием вещества поглотителя |
во времени. |
|
Это создает большие |
трудности при математическом описании |
и расчете гетерогенного поглощение, усугубляемые к тому же отсут ствием необходимого экспериментального материала. Совсем недавно -Фурмером Ю. В. и Колбасовым А. М. получены данные о характере поглощения сероводорода таблетками окиси цинка [105].
На рис. V-10, а показана фотография среза таблетки окиси цинка после выдерживания ее в потоке сероводорода, меченого ^радиоактивной серой, в течение 20 ч.
На фотографии отчетливо видна граница, разделяющая таблетку на области ZnS (светлая на рисунке) и не участвовавшей в реакции ZnO. На рис. V-10, б показано распределение серы по диаметру таблетки, полученное методом электронной бомбардировки.
Здесь также видно резкое разграничение между отработанной и чистой от серы областями таблетки. Из этих данных можно сде лать следующие выводы: а) скорость поглощения лимитируется
диффузией сероводорода через |
химически |
инертную |
область |
ZnS, |
б) на поверхности чистой ZnO |
в весьма |
узкой зоне |
таблетки |
про |
текает чрезвычайно быстрая химическая реакция (УД), в) концен трация II2S на границе между отработанной и чистой областями таблетки из-за практической необратимости реакции близка к нулю.
Так же, как и в главе VIII, рассмотрим последовательные стадии поглощения сернистых соединений окисью цинка.
Скорость химической реакции. Поскольку химическая реакция протекает на поверхности чистой окиси цинка, концентрация по следней остается постоянной и, следовательно, кинетическое уравне ние имеет вид:
1/.’ = А-сп |
(V ,14) |
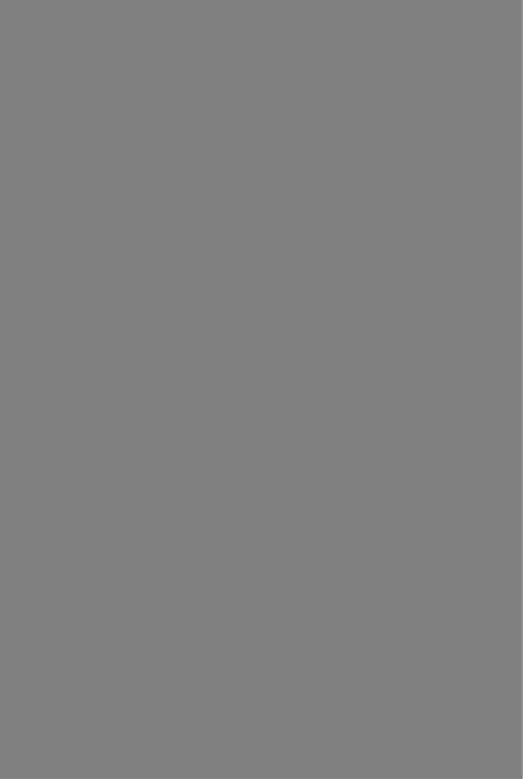
Условие протекания процесса на поверхности зерна определяется подводом вещества из внешнего потока
P (co o - cs) = - £ [ g r a d c ] s (V»1G)
где Р — коэффициент массоотдачи; с8 — концентрация сероводорода на поверх ности зерна поглотителя; — концентрация сероводорода в ядре потока.
Внешняя диффузия определяет подвод вещества к поверхности только в начальный промежуток времени, пока еще не образовался слой сульфида цинка. В дальнейшем процесс лимитируется внутридиффузионной стадией, поэтому Соо В общем случае концен трация в ядре потока — функция времени, т. е. Соо = с (*>•
Условие на внутренней границе слоя сернистого цинка
с= О
Впростейшем случае (сферическое зерно) задача сводится к ре шению дифференциального уравнения
дс |
= D ( |
|
|
д*с\ |
(V, 17) |
|
dt |
Or |
_ L i |
|
|||
V r |
|
* дdrу |
|
|||
с граничными условиями |
|
|
|
|
|
|
t=r-0 |
|
|
|
|
|
|
t> 0 г= R |
~ D^ |
|
H |
Cco-^s) |
||
|
|
dr |
|
|
|
|
|
c= 0 |
|
|
|
|
|
Здесь г* — положение |
границы |
между |
|
областями ZnS и ZnO |
внутри зерна. Эта задача отличается от традиционных задач мате матической физики тем, что значение г* является функцией времени.
Однако в первом приближении можно получить решение, до пуская, что процесс проходит через серию стационарных состояний при каждом значении г*, т. е. принимая dc/dt = 0. Рассмотрим изменение процесса во времени. Пусть отработанная зона зерна за время dt продвинулась на dr. Тогда прореагировало 4я (r*)2y/Midr молей окиси цинка (где у — кажущаяся плотность таблетки, кг/м3, Mi — мольная масса окиси цинка). За это же время прореагировало / Р* X 4я (г*)2 X РТ 0/22,4Р0Г dt молей сероводорода. Приравняв про
реагировавшие |
количества, получим: |
|
|
|||||
|
|
|
|
|
|
- Л Т З - d l ^ - J — dr |
||
или |
|
|
|
|
|
22АР0Т |
М1 |
|
|
|
|
|
dt |
\Р0Т-22А / |
дс \- 1 |
л- |
|
|
|
|
|
|
||||
|
|
|
|
|
|
P T 0MiD V dr J r* |
|
|
Значение |
производной |
(dcldr)r* находим |
из решения уравнения |
|||||
д2с!дг2 + |
2dclrdr = |
0 в указанных выше граничных условиях. В ре |
||||||
зультате |
имеем: |
|
|
|
|
|
||
|
t |
|
Яу |
22,4Р0Т |
|
(V.18) |
||
где у = |
|
Ш1Ссор |
РТ0 |
[( |
|
|
||
г*/Л. |
|
|
|
|
|
|
Уравнение (V,18) устанавливает приближенную связь между положением границы отработанной зоны таблетки и временем. Из уравнения легко можно получить зависимость сероемкости
таблетки от времени контакта |
с очищаемым газом. При pi? |
D, |
что возможно в практических условиях, уравнение упрощается |
||
и принимает вид: |
22АР0Т |
|
В2у |
|
|
* “ врртмх |
РТ о [ I — г/2 ( 3 — 21/)] |
(V .19) |
При у = 0 граница достигает центра зерна, |
зерно полностью отра |
|||
батывается. Время полной отработки |
зерна |
равно |
||
|
В*у |
22АР0Т |
(У, 20) |
|
^ - |
‘ |
РТ0 |
||
|
||||
Применение полых зерен. |
Мы видели, что количество вещества, |
поглощаемое, в единицу времени таблеткой окиси цинка, пропор ционально поверхности границы раздела между отработанной и не отработанной зонами таблетки. Эта поверхность с течением времени уменьшается и наблюдаемая скорость реакции убывает, стремясь в пределе (при t = tn) к нулю. Одновременно понижается интен сивность использования единицы объема слоя поглотителя и его средняя сероемкость, так как проскок сернистых соединений через слой очистной массы наблюдается прежде, чем вступит в реакцию окись цинка вблизи центра таблеток. Увеличить степень исполь зования окиси цинка, повысить среднюю сероемкость слоя возможно, применяя полые таблетки, например кольцевидные.
Для шарообразной таблетки, внутренняя полость которой со общается с окружающей средой через отверстия на полюсах, время
полной |
отработки |
составит |
27 |
/ а 2 —1 \з / |
|
|
|||||
|
|
|
|
/?2у |
|
22APQT Г |
а2- 1 \ - | |
(V ,21) |
|||
|
|
|
tп — l |
|
>т0 L1 - 4 |
U 3- w |
V |
*3- l / J |
|||
|
|
|
|
-6£>CooMi |
|
||||||
|
|
|
|
РТ о |
|
|
|
|
|
||
г д е |
а = |
R /Вт, |
— |
р а д и у с в н у т р е н н е й |
п о л о с т и , |
м . |
|
|
|||
|
Объем |
вещества, |
в среднем |
реагирующий за |
единицу времени |
||||||
в |
м3/с, |
в |
сплошной |
таблетке |
составляет |
|
|
|
|||
|
|
|
|
|
|
m = |
8 n i ? Z ) c 00 |
|
|
|
а средний объем вещества, реагирующий в единицу времени в еди
нице |
объема слоя из сплошных |
таблеток (в с-1) равен |
|||
|
|
rt_6DCoo(l- e ) |
|
|
|
|
|
8 |
Д2 |
|
|
г д е е — п о р и с т о с т ь ( с в о б о д н ы й |
объем) |
слоя |
|
|
|
Те |
же величины для полых |
таблеток |
|
соответственно равны |
|
|
8 л R \ D C Q |
|
аз —1 |
|
|
|
772” |
27 |
/ а 2 — 1 \ 2 |
/ |
а 2 — 1 \ |
|
|
~ 4 \ а 3 — 1 ) |
V 1 _ «3 - l / |
||
|
6 D Coc> (1 + е ) |
|
аз—1 |
||
|
Н2 |
|
|
|
|
Отношение g j g характеризует эффективность слоя, состоящего из полых таблеток, по сравнению со слоем из сплошных таблеток,
показывая, |
во сколько раз |
возрастает |
средняя скорость реакции |
||
на единицу |
объема |
слоя: |
|
|
|
|
gl |
|
fl3 _ l |
|
(V ,22) |
|
g ~ |
г |
27 / а 2 —1 \2 Л л2— 1 \ "1 |
||
|
|
||||
|
|
а31_1— |
4 (.а3 — 1 / |
\ 1 а3— 1 / J |
|
Соотношение (V,22) имеет экстремум, которому соответствует оптимальный размер внутренней полости. При i ? i = 0 , 5 отношение g j g = 2,96, т. е. наблюдаемая средняя скорость реакции для слоя из полых таблеток почти в три раза выше, чем для слоя из сплошных таблеток. ,
Процесс в малом объеме слоя. Если в единице объема слоя заклю чено п таблеток, то количество вещества, реагирующего в единице объема слоя за единицу времени, будет равно
g = — D [grad c]s Fn |
(V,23) |
где F — поверхность одной таблетки, м2. |
|
Градиент концентрации сероводорода на поверхности |
таблетки |
([grad с] S) должен быть найден из решения уравнения типа (V,15). Величину Fn = FIV (1—е) (где V — объем таблетки, м3) находят из результатов замеров таблеток и определений кажущейся и на сыпной плотности поглотителя.
Процесс во всем объеме аппарата. Уравнение переноса вещества в слре поглотителя в общем виде выглядит следующим образом:
grad c-{-g = D* Ac |
(V,24) |
dt
Первый член этого уравнения выражает увеличение концентрации вещества в свободном объеме слоя, второй — количество вещества, переносимое потоком, третий — количество поглощаемого вещества. Правая часть уравнения характеризует перемешивание в результате случайных неравномерностей в слое, приводящих к диффузионному размытию профиля концентраций с коэффициентом эффективной диффузии /)*. Уравнение (V,24) достаточно сложно для решения
в общем |
виде. Кроме |
того, неизвестно |
распределение |
скорости и |
||
в слое поглотителя, которое зависит |
от |
того, |
какова |
конструкция |
||
входных |
и выходных |
устройств в |
аппарате. |
В настоящее время |
не существует достаточно простых и точных описаний распределения скоростей потока в зернистом слое.
|
В простейшем виде задача |
нахождения профиля |
концентраций |
в |
слое поглотителя сводится |
к решению уравнения |
|
|
- £ + « * - £ ■ + * = о |
(V.25) |
|
|
dt |
дх |
|
с |
граничными условиями |
|
|
t^O х = 0 с = с0
представляющими собой математическое выражение того, что после пуска аппарата на входе в слой поддерживается концентрация с0, которая вообще может изменяться во времени.
Несмотря на то что из-за сложного вида функции g не удается получить аналитическое решение уравнения (V,25), однако из его анализа можно сделать некоторые важные выводы. Характеристи ческая система
d t/ 1 dx/vx = — dc/g
приводит к характеристическому уравнению
t —х/их — to
которое показывает, что решение будет функцией двучлена t—yllvx (где у — безразмерная координата, а I — длина слоя поглотителя). Это означает, что при постоянном объеме поглотителя величина l!vx остается постоянной, поэтому в определенных пределах можно выбирать любые конфигурации слоя, а следовательно, и разнообраз ные конструкции аппаратов.
Аппаратура для сероочистки на поглотителях
Выше показано, что разнообразие конструкций аппаратуры для сероочистки на поглотителях в значительной мере обусловлено необходимостью исключения значительного продольного перемеши вания в слое.
Чтобы устранить продольное перемешивание, требуются следу ющие условия: поток очищаемого газа на входе в слой поглотителя должен равномерно распределяться; поглотитель не должен содер жать пыли и мелочи (поэтому его рассеивают перед загрузкой в ап парат); слой поглотителя должен быть равномерно уложен в аппарате (разравнивают при загрузке); теплоизоляция аппарата должна быть надежной; на распределение потока в слое поглотителя не должно влиять выходное устройство. Если указанные требования выполнены, то для данного процесса можно использовать любые типы аппаратов, описанные в главе VIII применительно к конвер сии окиси углерода с водяным паром.
Для аппаратуры сероочистки справедливы все замечания, из ложенные в главе VIII. Здесь же рассмотрим влияние температурных напряжений на зернистый слой (в гл. VIII о нем только упомянуто). Рассчитаем усилия на слой, которые возникают, например, при охлаждении аппарата. При нагревании аппарата вследствие разли чия в коэффициентах расширения слой поглотителя оседает, при последующем охлаждении и сжатии корпуса слой выпучивается лишь частично, поэтому на него и действуют со, стороны корпуса сжимающие усилия.
Если аппарат охлаждается на At °С, то удлинение (в м) окруж ности корпуса составит
где D — диаметр аппарата, м; а х — коэффициент линейного расширения ме талла корпуса, м/(°С-м); а 2 — коэффициент объемного расширения зернистого слоя, м3/(°С-м3).
Относительное удлинение е = blnD = [а*—а 2/3] At вызывает напряжение в металле, характеризующееся модулем упругости
а=^гЕ
Сдругой стороны, из расчетов тонкостенных сосудов величина
напряжения определяется по уравнению
a = PD/2h
где Р — давление, Па; h — толщина стенки, м.
Приравнивая уравнения, определим давление, которое стенки аппарата оказывают на зернистый слой:
р__ 2&tEh (ах—а 2/3)
(V ,26)
D
Для радиального аппарата, где зернистый слой расположен между коаксиальными перфорированными цилиндрами (централь ной трубой и наружной обечайкой корзины), уравнение (V,26) приобретает вид:
D_ 2 (1 — ср) А/ (D — d) Eh (<Xi — а 2/3)
£2 |
(V,27) |
где d — диаметр центральной трубы, м; ф — доля свободного |
сечения перфо |
рации. |
|
Как видно, давление на слой катализатора при охлаждении его в радиальном аппарате меньше, чем в полочном.
По формулам (V,26) и (V,27) рассчитывают максимальные нагрузки без учета вспучивания и разрушения части зерен. Рас четы показывают, что при охлаждении аппарата на 100 °С сжима ющее усилие на зернистый слой в аппарате диаметром 3,8 м может достигать 0,98* МПа (10 кгс/см2) и для сравнения укажем, что давление на дно аппарата слоя высотой 10 м составляет лишь 1,58 X X 106 Па (1,6 кгс/см2).
Такие усилия оказывают разрущающее воздействие на таблетки катализатора. Хотя рассчитанные усилия на слой меньше, чем сообщаемые в паспорте данные о прочности поглотителя или ката лизатора, следует учитывать, что условия в зернистом слое сильно отличаются от условий, при которых проводятся стандартные испы тания на прочность партий катализаторов или поглотителей на катализаторных фабриках.
При стандартных испытаниях определяют главным образом усилия на раздавливание (предел прочности при сжатии), а в усло виях эксплуатации таблетки в слое разрушаются путем раскалы вания и смятия острых краев, что приводит к появлению пыли
и мелочЯТаким образом, для поддержания хорошего состояния зернистого слоя особенно важно соблюдение стабильного технологи ческого режима, исключение многократных остановок и охлаждения аппаратуры.
Очистка железосодовой поглотительной массой
Для топкой очистки водяного газа в качестве поглотителя сероорганических соединений применяют железосодовую массу, при готовленную на основе активной окиси железа с добавлением 30% соды [5, 66, 107].
Ниже приведена общая характеристика поглотительной массы [1, Ю, 108]:
Размеры зерен, мм . |
5 -1 5 |
|
Общая пористость, % . . . |
Около 50 |
|
Насыпная плотность, кг/м3 |
0,71 • Ю3— |
|
Примерный состав, % |
0,73 • Юз |
|
4 1 -44 |
||
Fe20 3 |
||
Na2C03 |
30 |
|
А120 3 |
1,8 |
|
SiOa |
2,6 |
|
CaO |
2,0—2.5 |
|
тю2 |
3,4 |
|
S |
. Отсутству |
|
|
ет |
Железосодовый поглотитель обеспечивает высокую степень очи стки газа (до 1—2 мг/м3 остаточной серы) и наиболее часто приме няется на промышленных установках синтеза бензина.
Очистку железосодовым поглотителем проводят при 150—250 °С и объемной скорости 100—200 ч"1. Для успешного ведения про цесса оадстки в газе необходимо поддерживать определенную кон центрацию кислорода (0,2—0,3%). Железосодовая масса поглощает сероокись углерода, сероуглерод, меркаптаны (тиофен не погло щается). При этом образуются сульфаты, сульфиды и элементарная сера, одновременно выделяется углерод [109]. Поглотитель чувстви телен к присутствию в газе примесей, способных окисляться и полимеризоваться. Даже небольшое содержание таких примесей снижает степень очистки газа и уменьшает срок службы поглотителя.
При очистке водяного газа сероемкость поглотителя [110] соста вляет 6_-9% (масс.), но чаще не более 3—4% (масс.). Учитывая малую сероемкость железосодового поглотителя и невозможность его регенерации, целесообразно применять этот метод для очистки гавов с невысоким содержанием органической серы.
ТиНОная схема промышленной установки для тонкой очистки газов от органических сернистых соединений поглотительным ме тодом Изображена на рис. V-11.
21 3^кя8 1460 |
3 3 1 |
Исходный газ поступает в теплообменник для предварительпого подогрева газом, выходящим из первой очистной башни. В трубчатом огневом подогревателе газ нагревается до требуемой температуры и последовательно проходит все очистные башни. По мере насыщения
заз |
газ |
Рис. V-11. Принципиальная схема промышленной установки для тонкой очи стки газов от сероорганических соединений поглотительным методом:
1 — трубчатый огневой -подогреватель; 2 — башни с жслезощелочной массой; з — тепло обменник.
и |
дезактивации поглотителя температура в башнях повышается |
от |
150 до 260 °С. После этого второй аппарат включают первым |
по ходу газа, а в первой башне заменяют отработанный поглотитель.
Очистка на активированном угле
На применении активированного угля основаны два способа очист ки: адсорбционный и окислительный, преимущество которых заклю чается в том, что для их проведения не требуется подогрев газа [66]. Адсорбционный способ заключается в обратимой адсорбции сернистых соединений из газа с последующей их десорбцией (для регенерации угля), осуществляемой путем пропускания пара при 120-— 150 °С. Легче других адсорбируются тиофен, сероуглерод, плохо адсорбируются сероокись углерода, дисульфиды.
В литературе [111—115] подробно описано применение активи рованного угля для удаления соединений серы из синтез-газа и опи-
Таблица V-7. Очистка технологических газов активированным углем
|
Содержание серы, мг/м* |
Степень |
|
Газ |
|
после адсор |
очистки, |
|
до адсорбера |
°/ |
|
|
|
бера |
|
Б ы т о в о й |
192 |
100 |
50 |
(светиль |
|||
ный) |
|
|
|
Воздушный |
244 |
161 |
3 3 |
Водяной |
119 |
116 |
0 |
сана технология процесса очистки активированным углем. Резуль таты опытов по очистке различных технологических газов [115] активированным углем приведены в табл. V-7.
Высокая степень очистки коксового газа от сероорганических соединений может быть достигнута комбинированием адсорбционного метода с очисткой от сероокиси углерода (например, каталитиче ским или поглотительным методом).
Возможность практически полного удаления тиофена является преимуществом адсорбционного способа. Одновременно с соединени ями серы удаляются остатки тяжелых углеводородов (нафталина, бензольных углеводородов и др.), затрудняющих адсорбцию серо содержащих примесей.
В работе [115] для адсорбционной очистки газа рекомендуется гранулированный активированный уголь марки АР-3. Показано, что коксовый газ может быть очищен от тиофепа и сероуглерода (степень очистки от сероорганических соединений 75—80%) с одно временным удалением углеводородов, кипящих при температуре выше 40 °С.
Предложены два варианта адсорбционной очистки коксового газа [37]:
сокращенный цикл — процесс адсорбции продолжается до про скока сероуглерода. При этом достигается полная очистка газа от высших углеводородов и на 80% — от сероорганических примесей (в сумме). Емкость активированного угля по углеводородам соста вляет 6—7% и по сере — 0,6% массы угля;
удлиненный цикл — процесс адсорбции продолжается до про скока тяжелых углеводородов. Достигается полная очистка от угле водородов и тиофена и выводится только одна треть общего коли чества сероорганических соединений. Емкость активированного угля по углеводородам увеличивается до 12% массы угля.
Выбор того или другого варианта определяется схемой дальней шей очистки газа. Расход пара на регенерацию угля по сокращен ному режиму на 70% больше, чем по удлиненному.
Обработка угля водяным паром при 120—150 °С обеспечивает его регенерацию, однако от цикла к циклу емкость угля постепенно снижается вследствие накопления на его поверхности продуктов осмоления и полимеризации. В присутствии сероводорода в кок совом газе количество недесорбируемых веществ на угле увеличи вается. Во избежание преждевременного загрязнения угля и его частой замены коксовый газ необходимо предварительно очищать от сероводорода [115].
Изучено {116] влияние температуры, влажности и состава га зовой смеси на разложение сероуглерода на активированном угле марки APT с целью подбора оптимальных параметров процесса адсорбции и десорбции при очистке воздуха от CS2.
Активированный уголь был применен для очистки коксового [117], природного [118] и генераторного газов [119] под давлением 19,6-105—29,4» 10б Па (20—30 кгс/см2). По опубликованным данным,
содержание сероорганических соединений снижалось от 35— 45 мг до нескольких долей миллиграмма в 1 м8 газа; сероемкость угля составляла 0,2—0,3%.
Для удаления меркаптана и сероокиси углерода из природного газа предложено использовать активированный уголь с добавками металлов (никель, железо) [120, 121] или окислов металлов [10, 122], нанесенных на уголь. Для очистки природного газа'были испытаны активированные угли отечественного производства [123] и определена их динамическая и статическая активность (результаты испытаний представлены в табл. V-8).
Таблица V.8. Характеристика активированных углей
Показатели |
|
Марки углей |
|
||
СКТ |
CKT-2 |
С |
АР-3 |
||
|
|||||
Плотность, кг/м3 |
|
|
|
|
|
насыпная |
460 |
470 |
400 |
530 |
|
кажущаяся |
700 |
— |
600 |
900 |
|
истинная |
1980 |
— |
1900 |
2000 |
|
Удельная поверхность, м2/г |
1400 |
993 |
576 |
890 |
|
Статическая активность по |
20,3 |
10,7 |
3,8 |
36.6 |
|
меркаптану, мг/г |
|
|
|
|
Установлено, что кроме меркаптанов активированный уголь адсорбирует тяжелые углеводороды (газовый бензин), следовательно, адсорбционная установка может быть использована для одновремен ного удаления этих компонентов из природного газа. Регенерация отработанного угля может осуществляться продувкой при 200— 300 °С очищенным природным газом, а также острым перегретым паром. Показано, что емкость угля, насыщенного меркаптаном, восстанавливается на 60% при многократной регенерации, что позволяет его эффективно использовать [121].
Принципиальная особенность окислительного метода состоит в том, что сероорганические соединения подвергаются окислению
на |
поверхности активированного |
угля в присутствии кислорода |
и |
аммиака и продукты окисления |
задерживаются углем [17, 66, |
125]. Для протекания процесса необходимо, чтобы газ содержал 0,1% кислорода и двухили трехкратное количество (к содержанию серы) аммиака. Эффективность окислительного процесса выше, чем адсорб ционного. Однако химия, скому превращению на активированном угле при обычной температуре подвергается лишь сероокись угле рода, но не сероуглерод и тиофен. Следовательно, этот метод может дать высокую степень очистки водяного газа, но непригоден [126] для очистки коксового газа.
Сероемкость промышленных активированных углей АР-3 и АГ составляет 8—10%. Наибольшей сероемкостыо обладает специально
разработанный К-уголь, получаемый парогазовой активацией Тощих кузнецких углей [126]. Его сероемкость равна примерно 12% при насыпной плотности 540—550 кг/м8; прочность при истирании К-угля 90%.
Существенное влияние на окислительную сорбцию активирован ным углем оказывает относительная влажность очищаемого газа. Каждый вид угля характеризуется резко выраженным оптимумом влажности очищаемого газа. Для К-угля рекомендуется влажность очищаемого газа в пределах 50—60%.
При окислительном способе очистки линейная скорость газа должна быть не выше 0,1 м/с (считая на общее сечение аппарата), объемная скорость — 200—250 ч~ г.
Для увеличения степени насыщения угля серой рекомендуется двухили трехступенчатая схема очистки с отключением на регене рацию адсорбера первой ступени. Насыщенный серой уголь Можно регенерировать перегретым паром при 350—400 °С.
Для очистки от сероорганических соединений можно применять активированный уголь, пропитанный химически активными вещест вами, главным образом окислителями и щелочами. Так, для очистки от сероокиси углерода [37] предложен активированный уголь, про питанный щелочью (10% от массы угля). В этом случае нет необходи мости добавлять к очищаемому газу аммиак. Однако регенерация и повторное использование угля затрудняется, поскольку щелочь, добавляемая к углю, в процессе очистки полностью превращается в сульфат и оседает на адсорбенте.
Кроме того, по-видимому, нельзя нанести на активированный уголь достаточно большой слой твердой щелочи или окислителя без изменения пористой структуры угля. Поэтому в процессе очи стки газа от сернистых соединений методом окисления на активиро ванном угле наиболее целесообразно применять газообразные реа генты — кислород и аммиак.
Очистка на синтетических цеолитах
Вкачестве адсорбентов для тонкой очистки газов от серооргани ческих соединений могут быть эффективно использованы синтетиче ские цеолиты — молекулярные сита [45, 49].
Адсорбционные свойства цеолитов и области их использования подробно описаны в главе И.
ВСоветском Союзе проведены работы по применению цеолитов для обессеривания крекинг-бензинов, очистки изобутилена, алканов С4—С5 и других углеводородных газов [44, 48, 53]. Очистка цеоли
тами позволяет снизить содержание серы в пропане до 1-10” 4%. Для сероочистки могут быть использованы цеолиты типа СаА и типа X. Применение последних дает возможность удалять из газа цикли ческие сернистые соединения.
Запатентованы способы удаления сероводорода из пропана, серо водорода и меркаптана из природного газа на цеолитах марки X [60, 127].
Существенным преимуществом синтетических цеолитов является их способность адсорбировать тиофен в значительных [15—20% (масс.)] количествах [128, 129].
Показана возможность применения отечественных синтетических цеолитов NaX и СаА для очистки природного газа от сернистых соединений [50]. Наилучшим адсорбентом является синтетический цеолит NaX (рис. V-12). Полная адсорбционная емкость его по этилмеркаптану при 25 °С составляет 0,19 кг/кг, но сероводороду 0,17 кг/кг. Установлено, что очистка метана от сероводорода и этилмеркаптана на цеолите NaX позволяет получить газ, практически
свободный |
от |
сернистых |
соединений. |
|
|
|
|
|
|
|
|
|
|
||||
Ниже приведены данные, характеризующие этот способ очистки: |
|||||||||||||||||
Содержание |
серы |
(C2H5SH) |
в |
исходном газе, |
16 • 10-6—20 • 10-6 |
|
|||||||||||
к г /м з ............................................. |
|
очистки, |
Па |
|
|
|
|
|
|
||||||||
Давление процесса |
|
|
|
|
|
|
13,7 • 105— |
|
|
||||||||
|
|
|
|
|
|
|
|
|
|
|
|
19,6.105 |
|
|
|
||
Температура адсорбции, |
°С |
|
|
|
|
|
|
(14—20 кгс/см2) |
|
|
|||||||
|
|
|
|
|
|
|
25 |
|
|
|
|||||||
Объемная скорость, ч-1 |
........................................ |
|
|
|
|
|
|
|
1000 |
|
|
|
|||||
Адсорбционная емкость по C2H5SH в указан |
|
|
|
|
0,15 |
||||||||||||
ных условиях, к г / к г ........................................... |
|
|
|
|
|
|
|
|
250—280 |
|
|||||||
Пробег адсорбента до проскока, ч |
|
|
|
|
|
|
|
|
|||||||||
|
|
|
|
|
|
При |
этих |
условиях |
на |
1 т |
|||||||
|
70 |
|
20 |
30 |
цеолита |
марки NaX за один |
цикл |
||||||||||
|
|
|
|
|
|
можно |
очистить 500 000 м3 |
газа. |
|||||||||
|
|
|
|
|
|
Проверялась |
[130] |
степень |
|||||||||
|
|
|
|
|
|
очистки |
природного |
газа на оте |
|||||||||
|
|
|
|
|
|
чественных |
цеолитах |
NaX |
и СаА |
||||||||
|
|
|
|
|
|
от одоранта, |
содержащего наряду |
||||||||||
|
|
|
|
|
|
с этилмеркаптаном |
примеси |
бо |
|||||||||
|
|
|
|
|
|
лее тяжелых |
|
сернистых |
соеди |
||||||||
|
|
|
|
|
|
нений. |
|
|
|
|
|
|
|
|
|
||
|
|
|
|
|
|
Активность |
цеолита |
СаА |
по |
||||||||
|
|
|
|
|
|
этилмеркадтану |
составила |
1,0 X |
|||||||||
|
|
|
|
|
|
Х10"3 — 1,5 • 10“ 3 кг/кг |
(в |
пере |
|||||||||
|
|
|
|
|
|
счете |
|
на серу), |
т. е. |
на 25—30% |
|||||||
|
|
|
|
|
|
ниже, чем цеолита NaX, примене |
|||||||||||
|
|
|
|
|
|
ние которого |
наиболее |
целесооб |
|||||||||
Парциальное давление СдН5S Н }Па |
разно |
в этих |
условиях. |
|
|
|
|||||||||||
Очистка |
на |
молекулярных си |
|||||||||||||||
Рис. V-12. Адсорбционная емкость |
тах |
(цеолиты |
типа |
X) |
наиболее |
||||||||||||
эффективна |
при относительно |
не |
|||||||||||||||
различных |
адсорбентов |
при 25 °С: |
|||||||||||||||
1 — уголь СКТ; 2 — цеолит |
NaX; |
2 — |
высоком |
содержании |
в |
жидкости |
|||||||||||
цеолит СаА; 4 — цеолит NaA; |
5 — цеолит |
или |
газе |
сернистых |
соединений. |
||||||||||||
|
СаХ. |
|
|
|
При |
высоком |
|
содержании |
серы |
||||||||
|
|
|
|
|
|
|
рационально комбинировать адсорбцию с осушкой на молекулярных ситах [131].
Регенерация цеолитов. Разработано несколько вариантов реге нерации цеолитов, при которых активность цеолита NaX по отно
шению к меркаптанам сохраняется практически постоянной на про тяжении большого числа адсорбционно-десорбционных .циклов [132]. В работе [50] предложено проводить регенерацию цеолитов потоком азота или очищенного природного газа при 350 °С. Скорость газа при десорбции 0,01—0,03 м3/(м2-с). Расход десорбирующего газа составляет 6—8% объема очищенного газа.
И* В промышленных условиях температуру десорбции поддержи вают па 100—200 °С выше температуры адсорбции [44]. В качестве теплоносителей и одновременно десорбирующих агентов используют сухой воздух, азот, метан [133]. Предложены различные способы интенсификации этого процесса, например путем создания электро магнитного поля в слое цеолита при продувке горячим газом; в этом случае адсорбер должен быть выполнен из неэлектропроводного материала и снабжен внутри металлической арматурой.
Предложен также способ регенерации цеолитов промывкой растворителем, например раствором CS2—SC12 (1 1), с последу ющей продувкой газом для удаления растворителя [135].
ЛИТЕРА ТУРА
1.В кн.: Справочное руководство по катализаторам для производства аммиака и водорода. Л., «Химия», 1973, с. 65—69.
2. Коуль А. А ., Ризенфелъд Ф. С. Очистка газа. М., «Недра», 1968. 392 с.
3.Справочник азотчика. Т. 1. Под ред. Н. А. Симулина. М., «Химия», 1967, с. 214-293.
4.Андреев Ф. А. и др. Технология связанного азота. М., «Химия», 1974. 500 с.
5.Егоров Н. Н., Дмитриев М. М., Зыков Д . Д . Очистка от серы коксоваль
ного и других горючих газов. М., Металлургиздат, 1950. 238 с.
6.Литвиненко М. С. Очистка коксового газа от сероводорода. М., Металлургиздат, 1959. 307 с.
7.Англ. пат. 1274457 (1972).
8. Маркичев Н. А. и др., «Труды Ивановского ХТИ», 1970, № 12, с. 74—77.
9.Маркичев Н. А. и др., «Труды Ивановского ХТИ», 1972, № 15, с. 25—28.
10.Томас Ч. В кн.: Промышленные каталитические процессы и эффективные катализаторы. Пер. с англ. Под ред. А. М. Рубинштейна. М., «Мир», 1973,
с. 175—180.
11. Рябинин А. И., Лазарева Е. А ., ЖПХ, 1972, т. 45, № 7, с. 1636—1637. 12. Гаврилов А. Я ., «Труды ИГИ АН СССР», 1972, т. 28, № 2, с. 167—170.
13.Пат. ФРГ 1470587 (1972).
14.Пат. США 3572293 (1972).
15.* Англ. пат. 901609 (1958); 902140 (1959); 902138 (1962); 953868 (1964).
16.Пат. ФРГ 1166968 (1964).
17.Зелъвенский Я . Д . Докторская диссертация. М., МХТИ им. Д. И. Менде леева, 1963.
18.Зелъвенский Я. Д ., Герчикова С. Ю., «Труды ГИАП», 1953, вып. 2, с. 132—
159; |
1954, вып. 4, с. 127—178; 1956, вып. 5, с. 211—239; выл. 6, с. 165— |
||
184; |
1960, -вып. И , |
с. 129—148. |
с. 51. |
19. Зелъвенский Я . Д ., |
Авт. свид. № 85834; Бголл. изобр., 1950, № 7, |
||
20. Поезд Д . Ф., Силин |
Н. Г., «Нефтепереработка и нефтехимия», 1970, |
№ 5, |
с. 33—35.
21.Тагинцев Б . Г . и др., «Труды ГИАП», 1971, вып. 10, с. 134—140.
22.Зелъвенский Я . Д ., Герчикова С. Ю., «Труды ГИАП», 1960, вып. 11, с. 129— 148.
23.Ян. пат. 19681 (1970).
24.Данциг Г. А ., Воронцова Н .Ф . В кн.: Каталитическая конверсия угле водородов. Киев, «Наукова думка», 1974, с. 133—138.
25.Тагипцев Б . Г., Харьковская Е. Я ., Штейнберг Б. И ., «Труды ГИАП», 1971, вып. 10, с. 128—133.
26.Харьковская Е. Я ., Зельвенский Я . Д ., Пронина Р . Я ., Авт. свид. № 197519; Изобр., Пром. Образцы. Товарн. знаки, 1967, № 13.
27. Харьковская Е. Я ., Зельвенский Я. Д ., Пронина Р. Я ., Хим. пром., 1968,
№7, с. 3 4 -3 6 .
28.Англ. пат. 878493 (1958); 86931 (1961).
29.Франц, пат. 1128668 (1957).
30.Яп. пат. 34401, 39081 (1971).
31.Пат. СРР 53965 (1971).
32.Англ. пат. 1273738, 1276659 (1972).
33.Пат. ВНР 157032 (1970).
34.Зельвенский Я. Д ., Волков А . Я., «Труды ГИАП», 1953, вып. 1, с. 131—158.
35.Зельвенский Я. Д . В кн.: Гетерогенный катализ в химической промышлен ности. М., Госхимиздат, 1955, с. 399—405.
36.Зельвенский Я . Д . В кн.: Процессы и аппараты химической технологии. Под ред. А. Г. Касаткина. М., Госхимиздат, 1953, с. 110—116.
37.Зельвенский Я . Д ., Соколов В . Я., «Труды ГИАП», 1961, вып. 12, с. 175— 181.
38.Суханов М. В ., «Кокс и химия», 1971, № И , с. 59, 60.
39. Зельвенский Я . Д ., Шахова С. Ф., Дедова И, В., «Труды ГИАП», 1959, вып. 9, с. 316, 339.
40.Гаврилов В. С., Ларин Я., «Обмен опытом в азотной промышленности», 1962, № 6, с. 10, 11.
41.Жданов С. Я ., Изв. АН СССР. Сер. Орг. хим., 1965, № 6, с. 950—953.
42.Дубинин М. М ., Изв. АН СССР. ОХН, 1961, № 7, с. 1183—1191.
43.Barer Я. М ., Brit. Chem. Eng., 1959, № 5, р. 267—279.
44.Мирский Я . Я., Митрофанов М. Г ., ДорогочинЬкий А . Я., Новые адсор бенты — молекулярные сита. Грозный, Чечено-Ингушское книжное изда тельство, 1964. 108 с.
45.Синтетические цеолиты и их применение в СССР и за рубежом. Обзоры по отдельным производствам в химической промышленности. Вып. 4. М., изд. НИИТЭхим, 1971. 41 с.
46.Синтетические цеолиты. Под ред. М. М. Дубинина. М., изд. АН СССР,
1962. 286 с.
47. Николина В. А ., Неймарк Я . Я., Пионтковская М . А . , Усп. хим., I960,
т. 29, № 9, с. 1088—1191.
48.Агафонов А . В. и др.у Хим. пром., 1961, т. 7, с. 470—474.
49.Соколов В. А ., орочешников Я . Я., Молекулярные сита и их применение- М., «Химия», 1964. 156 с.
50. |
Харьковская Я. Я ., Зельвенский Я . Д ., Хим. пром., 1966, № 4, с\ 28—32. |
|
51. |
Щеглова М. Я ., Азотная пром., 1970, № 3, с. 14—16. |
|
52. |
Trenel Я ., Erdol-Erdgas-Z., 1969, Bd. 85, № 9, S. 363—365. |
|
53. |
Кельцев Я . Я., Газ. пром., 1963, |
№ 9, с. 52—56. |
54. |
Beach Я., Can. Oil a. Gas J., 1962, v. 15, № 7, р. 41—46. |
|
55. |
Clark Я. / . , Oil a. Gas J., 1959, |
v. 57, № 27, p. 120—124. |
56.Пат. США 3144307 (1960).
57.Haines Я ., Weilingeh / ., Petrol. Ref., 1961, v. 40, № 4, p. 123, 124.
58.Воронцова Я. Я., Газ. пром., 1972, № 1, с. 45—46.
59.Meditsch / . , Custil V., Eng. е. quimica, 1960, v. 12, № 1, p. 10—18.
60.Пат. США 3078640 (1963).
61. Stormont Я ., Gas liquefatti, 1963, v. 9, JST®4, p. 30—34.
62.Бельг. пат. 623543 (1963); 629431 (1964).
63.Wilby F. F., Gas. J., 1969, № 7 - 8 , p. 300—306.
64.Schmidt / . , Verfahren der Gasaufbereitung. Leipzig, УЕВ Deutscher Verlag fur Grundstoffindustrie, 1970. 508 S.
65.Авдеева А. Я., Газовая сера. M.—Л., Госхимиздат, 1950. 108 с.
66.Зельвенский Я. Д ., Хим. наука и пром., 1956, т. 1, № 6, с. 654—660.
67.Бельг. пат. 726803 (1969).
68.Пат. США 3496117 (1970); 3627674 (1971).
69.Англ. пат. 1221051 (1971).
70.Франц, пат. 1594411 (1970); 2130204 (1972).
71. |
Свинухов А . Г. |
и др., Пром. и сан. очистка газов, 1972, № 3, с. 22—26. |
||
72. |
Павелко В. 3., |
«Нефтепереработка и нефтехимия», 1972, |
№ 7, с. 33—35. |
|
73. |
Sommers Я ., Last W ., «Erdol und Kohle», 1971, Bd. 24, |
№ |
9, S. 578—581. |
|
74. |
Лилейкина T. H. и др., «Труды ГИАП», 1971, вып. 10, |
с. 83—90. |
75.Людковская Б. Г ., Бескова Г . С., «Труды ГИАП», 1969, вып. 24, с. 30—36.
76.Namba Seitara е. а., «Коге кагаку дзасси» (J. Chem. Soc. Japan, Ind. Chem. Sec.), 1970, v. 73, № 2, p. 272 -276.
77.Франц, пат. 1466905 (1967).
78.Пат. ФРГ 1279661, 1280224 (1968).
79.Голл. пат. 6818025 (1969).
80.Донцова В. А ., Барабанщикова Я . Ф., Людковская Б . Г ., Хим. пром., 1967, № 7, с. 515 -517 .
81.Штейнберг Б. И. и др., Авт. свид. № 256730; Изобр., Пром. Образцы.
Товарн. знаки, 1969, № 35, с. 19; Тюрин Я . Я ., Павелко Б . 3 ., Авт. свид.
№246485; Изобр., Пром. Образцы. Товарн. знаки, 1969, № 21, с. 19.
82.Франц, пат. 1550440 (1968).
83.Медоев Б . С., Афанасьев Ю. М., Тибилов С. Г., «Химия и технология топ лив и масел», 1971, № 8, с. 15—17.
84.Донцова В. А ., Герасимова А . В., Барабанщикова Я . Ф., Хим. пром., 1969,
№2, с. 154.
85.Копо К ., Ogoro Я ., Inaba Т., «Коге кагаку дзасси» (J. Chem. Soc. Japan, Ind. Chem. Sec.), 1958, v. 61, № 11, p. 1461—1469; 1961, v. 64, № 3, p. 525— 538; 631—635; № 5, p. 888—892.
86.«Коге кагаку дзасси», (J. Chem. Soc. Japan, Ind. Chem. Sec.), 1971, v. 74,
№7, p. 1313—1316.
87.Киран Я ., Кемболл Я ., «Кинетика и катализ», 1966, т§ 7, № 2, с. 375, 376.
88. Ивановский Ф. Я ., Кальварская Р . С., Бескова Г. С., ЖФХ, 1956, |
т. 30, |
№ 8, с. 1860—1866; № 10, с. 2353—2355; № 11, с. 2555—2559; |
№ 12, |
с. 2740—2746.
89.Ивановский Ф. Я ., Донцова В . А ., Бескова Г . С., ЖФХ, 1959, т. 33, № 11,
с. 2569_2579.
90.Ghoshal S. е. а., «Technology», 1965, v. 2, № 4, р. 211—216; 1966, v. 3, № 1, р. 3—7, № 3, р. 126—130.
91.Семенова Т. А. и др., Очистка технологических газов. М., «Химия», 1969. 392 с.
92.Шемякин Я . Е ., Тагинцев Б. Г ., «Труды ГИАП», 1972, вып. 14, с. 55—65.
93.Франц, пат. 1426719 (1966).
94.Пат. ФРГ 1040170, 1042171 (1959); 1263702 (1968).
95.Яп. пат. 11005 (1971).
96.В кн.: Краткий справочник физико-химических величин. Под ред. Е. Я. Мель никова. М., «Химия», 1967, с. 44, 45.
97.Айвазов Б. В ., Петров С. М., В кн.: Физико-химические константы серо-
органических соединений. М., « Х и м и я » , 1964, с. 200, 201.
98.Герасимов Я . Я ., Крестников А. Я ., Шахов А. С., В кн.: Химическая тер модинамика в цветной металлургии. М., Металлургиздат, 1960, т. 1, с. 150, 151; т. 2, с. 30, 31.
99.Варфоломеев Д. Ф., Егоров Е. А ., Тюрин В. В., «Нефтепереработка и нефте химия», 1970, № 5, с. 28—33.
100.Боброва Л. А. и др., Хим. пром., 1973, № 2, с. 123, 124.
101.Andrew S ., Wyrwas W ., «Chemik», 1970, v. 23, № 2, p. 39—43.
102.Garlet R ., Pupko S ., Mem. Sect. Chim. Minerale, 1957, p. 749—753; C. A., 1960, v. 54, № 9, p. 8402.
103. |
Тагинцев Б. Г ., |
Пронина |
P. Я ., |
Савинова Г. Я ., |
Азотная |
пром., |
1971, |
104. |
№ 2, с. 5—7. |
Пронина |
Р. Я ., |
Шемякин Я. Е ., |
Азотная |
пром., |
1972, |
Тагинцев Б. Г., |
|||||||
105. |
№ 3, с. 5 - 8 . |
|
|
др., «Труды ГИАП» 1977, вып. 43, |
|||
Бруй О. Я ., Фурмер Ю. В. и |
|||||||
|
с. 18—21. |
|
|
|
|
|
|
106.Кузнецов И . Д ., ЖПХ, 1954, т. 28, № 1, с. 5—11.
107.Зельвенский Я . Д ., Хим. пром., 1951, № 7, с. 209—212.
108. Sands А ., Wainright Я ., Schmidt L., Ind. Eng. Chem., 1948, v. 40, № 4,
р.607 -611 .
109.Башкиров А. Я ., Барабанов Я. Л ., ДАН СССР, 1955, т. 104, № 3, с. 415— 417.
110.Шполянский М. А ., Нефт. хоз., 1952, т. 30, № 4, с. 52—57.
111.Белоцерковский Т., Левит Р ., Хим. волокна, 1962, № 2, с. 40—43.
112. |
Зелесков И . Ф., Колесников Э. И., |
Хим. |
волокна, |
1964, № 2, с. 57—62. |
113. |
Uno Kadzuo, Chem. Factory, 1963, |
v. 7, |
№ 10, |
p. 41—47. |
114.Livingston Y ., Hidrocarb. Proc., 1971, v. 50, № 1, p. 126—130.
115.Зельвенский Я . Д ., Грузинцева А. Я ., «Труды ГИАП», 1954, вып. 3, с. 109— 138; 1956, вып. 5, с. 193—210.
116. Лазарев В . Я ., Костриков В. Я ., Пром. и сан. очистка газов, 1971, № 6,
с.8—11.
117.Пат. США 3116970 (1964).
118.Somer Т . G., Brit. Chem. Eng., 1963, v. 8, № 7, p. 466—470.
119. Lee G., Leslie / ., Rodekohr Я ., Petrol. Ref., 1963, v. 42, № 9, p. 125—131.
120.Пат. ФРГ 1054071 (1961).
121.Пат. США 2930673 (1960).
122.Томас Дж., Томас У. Гетерогенный катализ. Пер. с англ. Под ред. А. М. Ру бинштейна. М., «Мир», 1969. 452 с.
123. Зельвенский Я. Д ., Струнина А . Я., «Труды ГИАП», 1968, вып. 20, с. 21 — 36.
124.Струнина А. В. и др., «Труды ГИАП», 1971, вып. 10, с. 73—82, с. 269— 271.
125.Пат. ФРГ 1144692 (1963).
126.Зельвенский Я . Д ., Грузинцева А. Я ., «Труды ГИАП», 1953, вып. 1, с. 159— 201.
127.Пат. США 3078641 (1963).
128.Виноградова В. С., Кофман Л. С. В кн.: Синтетические цеолиты. М., изд. АН СССР, 1962, с. 99—102.
129.Киселев А. В ., Элътеков Ю. А ., Семенова В . Я ., В кн.: Синтетические цеолиты. М., изд. АН СССР, 1962, с. 218—224.
130.Тагинцев Б . Г. и др., Азотная пром., 1971, № 1, с. 5—14.
131.Thomas Т. Я., Clark Е. L., Oil a. Gas J., 1967, v. 65, № 12, р. 112—116.
132. Кофман Л. С., Виноградов В. С., Изв. АН СССР, Сер. Орг. хим., 1965,
№ 6, с. 375—382.
133.Боброва Л. Я ., «Химия и технология топлив и масел», 1964, № 2, с. 18—24.
134.Васильев С. 3. и др., Авт. свид. №253030 (1968); Изобр., Пром* Образцы* Товарн. знаки, 1969, № 30, с. 24.
135.Пат. США 3450629 (1969).