
книги / Цилиндрические зубчатые колеса
..pdf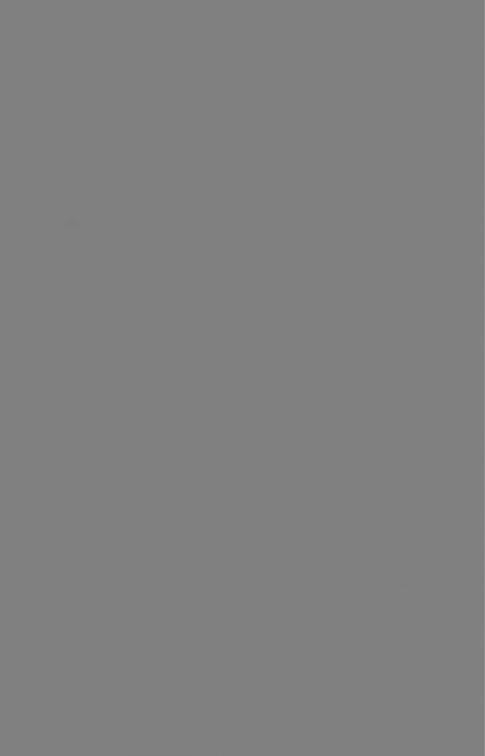
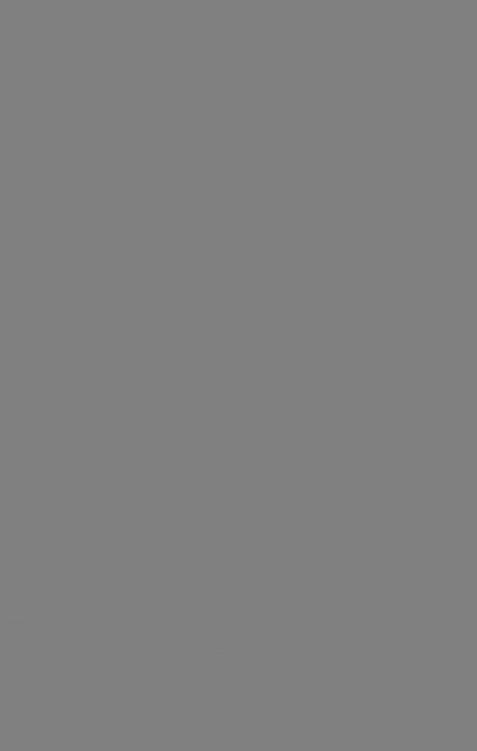
Глава 2
Материалы, получение заготовок, термическая обработка
2.1. Материал для изготовления зубчатых колес
Зубья колес должны обладать достаточно высокими прочностью, твердостью, способностью сопротивляться истиранию и другими свойствами, обеспечивающими надежную работу зубчатой передачи при наименьших ее габаритах и массе.
Материал для изготовления зубчатых колес выбирается в зависи мости от назначения и условий эксплуатации, передаваемых нагру зок, скоростей вращения и т.п. При выборе материала необходимо учитывать его низкую стоимость, хорошую обрабатываемость реза нием, минимальное коробление при термообработке, высокую проч ность, долговечность работы и повышенную стойкость к износу.
В передачах часто применяют колеса из стального литья, сопря гаемые с коваными шестернями. Для изготовления литых колес при меняют стали 50Л, 40ГЛ, ХГСЛ, ХН2Л и др. Литые зубчатые колеса обычно подвергают нормализации и длительному отпуску для сня тия внутренних напряжений.
Для изготовления венцов зубчатых колес, работающих при малых скоростях и небольших усилиях, применяют серый чугун марки СЧ20, СЧЗО и др. В ряде случаев изготовления червячных колес при меняется бронза БР. ОФ 10-1, БР. АЖ 9-4 и др.
Основная масса зубчатых колес, применяемых в автомобилях, трак торах, самолетах, станках и других силовых агрегатах, где лимитирую щим фактором является прочность зубьев (сопротивление на изгиб, стойкость поверхности профиля зубьев против усталостного разруше ния —- питгинга и изнашивание зубьев), изготавливается из стали.
Выбором марки стали определяется весь процесс изготовления зубчатого колеса (штамповка, термообработка, режимы механичес кой и химико-термической обработки). Сталь должна обеспечивать
наилучшие значения эксплуатационных характеристик, высокую технологичность и экономическую целесообразность.
Для производства зубчатых колес могут применяться углеродные ста ли — 40, 45, 50; углеродистые стали пониженной прокаливаемости — 55ПП. Однако эти стали не находят широкого применения в условиях крупносерийного и массового производства вследствие большого короб ления в процессе термообработки и сравнительно низкой прочности. Для повышения прочности и износостойкости в стали добавляют один или несколько легирующих элементов. Одним из наиболее универсальных и широкоприменяемых легирующих элементов является хром. Он уси ливает действие углерода, повышает твердость, стойкость к износу, рас ширяет предел упругости, увеличивает прочность на разрыв и прокаливаемость. Введение никеля увеличивает ударную вязкость, предел упру гости и прочность стали на разрыв. Прочная и вязкая поверхность никелевых сталей обеспечивает высокую стойкость к усталости и изно су. Молибден увеличивает прокаливаемость сталей и оказывает значи тельное влияние на уменьшение твердости сталей при температурах от пуска. Титан размельчает зерно, но обрабатываемость ухудшается.
Обрабатываемость различных материалов зависит от их химичес кого состава и механических свойств. Чем тверже сталь данной мар ки, тем хуже она обрабатывается, тем быстрее изнашивается режу щий инструмент. При введении легирующих элементов (например, хрома) обрабатываемость стали ухудшается даже при сохранении твердости. Стали с малым содержанием углерода (например, 20Х) и некоторые другие (например, 35ХМ) вследствие вязкости обладают худшей обрабатываемостью по шероховатости поверхности.
В настоящее время для цементуемых зубчатых колес применяют ся стали с содержанием углерода 0,12-0,25%. Наиболее широко ис пользуются следующие стали: хромистые (15Х, 20Х); хромомарганце вые с титаном (18ХГТ, 25ХГТ), с бором (20ХГР, 27ХГР), с никелем (14ХГН, 19ХГН) и с молибденом (25ХГМ); хромоникелевые (12ХНЗА, 20ХНЗА, 12Х2Н4А, 20Х2Н4А); хромоникелевые с бором (20ХНР), с молибденом (20ХНМ, 20ХН2М) и с вольфрамом (18Х2Н4ВА); хромо марганцевоникелевые с титаном (15ХГНТА, 15ХГН2ТА), с бором (20ХГНР), с молибденом (20ХГНМ), с титаном и бором (20ГНТР) и с молибденом и титаном (25ХГНМТ).
Для изготовления зубчатых колес, подвергаемых нитроцемента ции, обычно применяют стали с содержанием углерода 0,3-0,45%, например 30Х, 45Х, 30ХМ, 35ХМ, 38ХМА. Следует отметить, что для этой цели используются также стали с более низким содержанием углерода, т.е. цементуемые, например 18ХГТ, 25ХГМ и др.
На прочность и долговечность зубчатых колес большое влияние оказывает качество используемых сталей и, прежде всего, содержа ние таких примесей, как сера, фосфор, мышьяк, кислород, азот, во дород, а также однородность химического состава и структуры [9].
Впоследнее годы все чаще предпринимаются попытки замены стальных зубчатых колес на колеса из высокопрочного чугуна.
Высокопрочный чугун — это чугун, в котором углерод в значи тельной степени или полностью находится в свободном состоянии в форме шаровидного графита. Выплавляется с присадкой небольшого количества магния или церия. Имеет значительно более высокую прочность при растяжении и изгибе.
Впромышленности применяется несколько марок высокопрочно го чугуна, из которых для изготовления таких ответственных деталей, как зубчатые колеса, могут быть использованы ВЧ 60, ВЧ 45, ВЧ 40, различающиеся, главным образом, структурой металлической основы. Механические свойства этих чугунов приведены в таблице 8 [7].
Для чугуна с шаровидным графитом принципиально возможны два вида термической обработки, применяемые для стали.
Опыт работы Минского автозавода по изготовлению из высоко прочного чугуна главной пары автомобиля МАЗ-5551 показывает, что для высокопрочного чугуна с химическим составом (% шах): С 2,8-3,2; Si 1,7-2,4; Мп 0,3-0,7; Ni 0,25; Си 0,2; S до 0,03; Р до 0,01; ос таточный Mg до 0,03 режим термообработки должен быть следую щим: нагрев до температуры 950°С, выдержка 1час, быстрое охлаж дение до температуры 320°С и выдержка при этой температуре 2 часа, охлаждение на воздухе и промывка, дробеочистка дробью 0,3-0,5 в течение 15 мин. [8].
Таблица 8. Механические свойства высокопрочных чугунов
|
Предел |
Условный |
Относитель |
Ударная |
|
|
|
предел |
|
||||
|
прочности при |
ное |
|
|||
Марка |
текучести при |
вязкость, |
Твердость, |
|||
растяжении, |
растяжении, |
удлинение, |
Нм/см2 |
|||
чугуна |
МПа |
% |
НВ |
|||
МПа |
|
|||||
|
|
|
|
|
||
|
|
не менее |
|
|
||
ВЧ 60 |
600 |
420 |
2,0 |
15 |
197-269 |
|
ВЧ 45 |
450 |
330 |
5,0 |
20 |
170-207 |
|
ВЧ 40 |
400 |
300 |
10,0 |
30 |
156-197 |
2.2. Методы получения заготовок
Выбор метода получения заготовки для зубчатого колеса зависит от формы и размеров детали, ее назначения, материала, объемов про изводства. В основе выбора метода получения заготовки должна ле жать как экономичность самого метода, так и стоимость последую щей механической обработки. Для получения максимального коэф фициента использования металла, учитывая весь технологический процесс изготовления зубчатого колеса, необходимо выбирать такой метод получения заготовки, который максимально приблизит ее форму и размеры к готовому изделию. Уменьшение припусков под механическую обработку обеспечивает исключение черновых опера ций, таких, как точение, зубофрезерование, применение более вы соких режимов резания, т.е., в конечном итоге, повышение произ водительности обработки и качества зубчатого колеса.
Для изготовления заготовок зубчатых колес в условиях крупносе рийного и массового производства применяются малоотходные ме тоды, к которым относятся: поперечно-клиновая прокатка ступен чатых валов, горячая высадка на многопозиционных автоматах, хо лодная штамповка, вырубка, горячее накатывание.
В мелкосерийном производстве заготовки зубчатых колес получа ют другими методами — отрезкой, ковкой, горячей штамповкой по типовой технологии: очистка металла от поверхностных дефектов, разрезка на мерные части, нагрев заготовки, осадка и штамповка за готовки за несколько рабочих ходов, пробивка отверстия у колесдисков, обрезка облоя, термообработка.
Традиционным методом получения заготовок зубчатых колес яв ляется литье. Чтобы максимально приблизить форму и размеры за готовки к готовой детали применяют некоторые специальные мето ды литья: в кокиль, под давлением, по выплавляемым моделям.
Литье в кокиль — применяют для изготовления заготовок прямо зубых цилиндрических колес, зубчатых секторов. Отливки получают путем разливания жидкого металла в кокили, изготавливаемые из стали или графита. Литейный материал — чугун с шаровидным или пластинчатым графитом, медь, медные сплавы.
Литье под давлением применяют для изготовления заготовок зуб чатых колес из цветных металлов. В этом случае жидкий металл под высоким давлением и при высокой скорости заливается в закален ные стальные формы. Этим методом можно изготавливать заготов ки с зубом внешнего и внутреннего зацепления.
Литье по выплавляемым моделям применяется для изготовления за
готовок и зубчатых колес сложной формы из стали и цветных метал лов. Литье выполняют по высокоточным керамическим моделям, которые соответствуют контуру получаемой заготовки. Этот метод изготовления обеспечивает высокую точность: большинство повер хностей заготовки не требуют механической обработки.
Поперечно-клиновая прокатка производится круглыми роликами или плоскими плашками и применяется для изготовления заготовок шестерен-валов ступенчатой формы. На периферии роликов распо ложены клиновые копиры, которые во время вращения постепенно внедряются в заготовку и формируют необходимый профиль. Заго товка полностью обрабатывается за один оборот роликов. Припуск на механическую обработку снижается примерно в 2 раза. Произво дительность прокатных станов конструкции ВНИИметмаш состав ляет 360-900 шт/час.
Горячая высадка применяется для изготовления дисковых загото вок. Выполняется на многопозиционных автоматах. Процесс полно стью автоматизирован. Суть процесса: горячекатаные прутки непре рывно подаются в индуктор, где происходит нагрев до температуры ковки. Далее нагретые прутки подаются в горизонтальный автомат для горячей штамповки, затем от прутка отрезается мерная заготов ка и подается к матрицам. На различных позициях автомата произ водится последовательно: осадка заготовки, предварительное и окон чательное формообразование и прошивка отверстия. Формообразо вание производится в закрытых штампах, поэтому заготовки не имеют штамповочных уклонов и заусенцев.
Холодная объемная штамповка. Этим методом можно получать за готовки зубчатых колес, как с прямым зубом, так и без него. Метод отличается высокой производительностью и высоким коэффициен том использования металла. Холодной обработкой рекомендуется изготавливать детали из стали с содержанием углерода 0,15-0,4%. При более высоком содержании углерода снижается период стойко сти инструмента. В этом случае рекомендуется применять полугорячую штамповку, которая производится при температуре 500-700°С.
Вырубка используется для изготовления плоских деталей из стали, меди, алюминия и их сплавов. Вырубка — высокопроизводительный метод, позволяющий за один рабочий цикл изготовить несколько деталей сложной геометрической формы. Зубчатые колеса, изготов ленные вырубкой, дальнейшей механической обработке не подвер гаются. Точность таких колес невысока и соответствует 10-11 степе ни по ГОСТ 1643-81. Модуль вырубаемых зубчатых колес принято выбирать приблизительно равным 60% толщины материала.
Метод порошковой металлургии. При этом методе зубчатые колеса спекаются из порошковых смесей в закрытых штампах. Материалом служат железные порошки с добавлением порошков легирующих элементов — никеля, хрома, молибдена и др. Процесс изготовления складывается из трех этапов: точного взвешивания порошка и изостатического сухого прессования в мягких оболочках; спекания при высокой температуре, после которого получается заготовка; оконча тельной горячей штамповки, после которой получается готовая де таль.
Спекание в печах производится при температуре 1150-1350°С. При горячем прессовании производится вторичный подогрев до тем пературы 800-1100°С. Охлаждение детали происходит в защитном газе. Сегодня имеются автоматические установки для получения зуб чатых колес из порошка, полностью исключающие ручные опера ции. В специальную автоматическую установку с одного конца по дается порошковая металлическая смесь, а с другого конца выходит готовая деталь, обладающая всеми геометрическими и физико-меха ническими свойствами, присущими аналогичным деталям, изготов ленным из стальной заготовки другими методами. Время спекания в автоматических установках 3-5мин. вместо 20-30, затрачиваемых в обычных печах.
Если не требуется высокая точность зубьев, то после спекания дополнительной обработке колеса не подвергают. Если необходима высокая точность, то предусматривают небольшой припуск на зубьях для последующей чистовой обработки.
Метод порошковой металлургии используется для получения зуб чатых колес масляных насосов, коробок передач, садовых тракторов. Метод очень экономичен: при изготовлении 1т заготовок из метал лического порошка экономится 2т стального проката.
Горячее накатывание зубьев. Для горячего накатывания зубьев ци линдрических зубчатых колес, применяют два метода: с осевой и ра диальной подачей. Методом с осевой подачей накатывают зубья ци линдрических колес диаметром до 200мм с модулем до 4мм. При этом методе зубья накатывают на длинных штангах, а затем разреза ют на отдельные колеса. С радиальной подачей накатывают отдель ные заготовки с модулем выше 4мм. Метод и оборудование разрабо таны ВНИИметмашем и с успехом используются на ряде машино строительных предприятий. Схема накатывания на зубонакатном стане мод. ЗПС-350 представлены на рис.34.
Поковка 5, изготовленная на механическом ковочном прессе, ус танавливается в зажимное приспособление и закрепляется между
Рис.34. Схема горячего накатывания цилинрических зубчатых колес.
двумя стаканами 6 и 7. Для лучшего заполнения зубьев у заготовки перед накатыванием должна быть специальная форма — небольшая вогнутость на периферии (глубиной 1,5-2мм), а торец венца должен быть выполнен конусным под углом 3-5°
Нагрев поковки под накатывание осуществляется в зоне накаты вания токами высокой частоты до температуры 1100-1150°С. Нака тывание производится в два этапа: сначала гладкими роликами 1 и 9, имеющими реборды, калибруют штампованную поковку по на ружной поверхности и ширине зубчатого венца до требуемых разме ров под накатку зубьев. Наружная поверхность заготовки получает вогнутую форму. Затем заготовку в зажатом состоянии вместе с ин дуктором перемещают в положение для накатывания зубчатого вен ца. После вторичного подогрева начинается процесс накатывания зубьев зубчатыми накатниками 2 и 8. Когда головки с накатниками достигают механического упора, процесс накатывания заканчивает ся, накатники отходят в исходное положение, накатанное зубчатое колесо освобождается для выгрузки.
Гладкий и зубчатый накатники с ребордами собраны в единый узел на втулке 3 и стянуты гайкой 4. Реборды служат для ограниче ния течения металла поковки в осевом направлении.
Размеры и форму заготовки под накатывание рассчитывают, а за тем практически корректируют таким образом, чтобы объем метал ла, вытесненный из впадин, был равен объему металла, необходимо му для заполнения вершин зубьев.
Горячее накатывание зубьев не обеспечивает достаточной точно сти зубчатых колес, поэтому после него требуется дополнительная механическая обработка зубьев. По опыту АМО «ЗИЛ» зубчатые ко
леса с параметрами z=46; т=6мм, b=70, р =16°7' имеют следующую точность: радиальное биение 0,8-1,0мм, колебание длины общей нормали 0,5-0,7мм, припуск на сторону 1,5-2,0мм. Стойкость зубча тых накатников 2,5-3,0 тыс. заготовок. Время цикла накатывания составляет 2,4мин. [10].
2.3. Термическая обработка зубчатых колес
Стальные зубчатые колеса после механической обработки под вергаются различным видам термической обработки.
Если термической обработке подвергается все колесо, то ее назы вают объемной. Объемная термообработка включает в себя закалку при температурах нагрева 790-920°С с последующим отпуском при темпе ратурах 300-690°С в зависимости от марки обрабатываемой стали.
Охлаждающая среда при закалке — вода или масло, при отпуске — воздух. Интервал получаемой при объемной обработке твердости находится в пределах НВ 170-477, в зависимости от марки стали и применяемых режимов термообработки. Объемная закалка с более высокой твердостью зубьев (свыше HRC 40) применяется редко, т.к. при этом наблюдается разброс значений по пределу усталости, низ кая ударная вязкость, что снижает надежность работы передачи. Кроме того, при высокой твердости весьма сложно исправление ме ханической обработкой деформации, возникающей при закалке зуб чатых колес. Основные параметры для объемной закалки и отпуска зубчатых колес можно найти в справочниках (например, [38]).
Объемной закалке подвергаются зубчатые колеса, выполненные из углеродных сталей — 35,40,45, 50, сталей с добавлением хрома, крем ня, марганца, алюминия — 40Х, 45Х, 40ХС, 35Г2, 50Г2, 35ХГ2, 38ХА, 35ХГСА, 35СГ, 40ХС, 40ХН, с добавлением других легирующих эле ментов - 35ХГСА, 38ХМЮА, 45ХНМФА, 45ХНМ, ЗОХГНЗА и др.
Термическая объемная обработка обеспечивает, как правило, из менение свойств металла по всему объему изделия. Однако в ряде случаев требуется изменить физико-механические свойства только поверхностного слоя без изменения его химического состава, а так же структуры и свойств сердцевины детали. В этом случае применя ется поверхностная закалка деталей, которая производится путем на грева и быстрого охлаждения только поверхности зубьев. При повер хностной закалке производят индукционный нагрев токами высокой частоты (ТВЧ) или газовым пламенем.
Газопламенная закалка производится при нагреве поверхности пла