
книги / Цилиндрические зубчатые колеса
..pdfРис.38. Дисковая модульная острозаточенная фреза.
Таблица 13. Размеры дисковых модульных острозаточенных фрез
ш |
D |
Е>, |
в |
н |
h |
А |
т |
8-10 |
180 |
170 |
25 |
30 |
10 |
12 |
7 |
12-14 |
195 |
183 |
37 |
40 |
15 |
18 |
10 |
16-18 |
225 |
201 |
48 |
50 |
20 |
24 |
12 |
20-22 |
240 |
224 |
57 |
58 |
25 |
30 |
14 |
24-26 |
260 |
240 |
67 |
68 |
30 |
36 |
16 |
28-30 |
290 |
268 |
75 |
78 |
35 |
42 |
17 . |
Допускается 5-6 повторных заточек резцов. Резцы затачиваются окончательно в собранном виде в корпусе фрезы. Профиль зубьев фрезы прямолинейный.
Рекомендуется работать комплектом из двух дисковых острозато ченных фрез.
Для чернового нарезания зубьев колес средних и крупных моду лей могут быть рекомендованы сборные дисковые модульные твер досплавные фрезы. При использовании твердосплавных дисковых фрез на специальных станках (ЕЗ-28, ЕЗ-11) достигается повышение
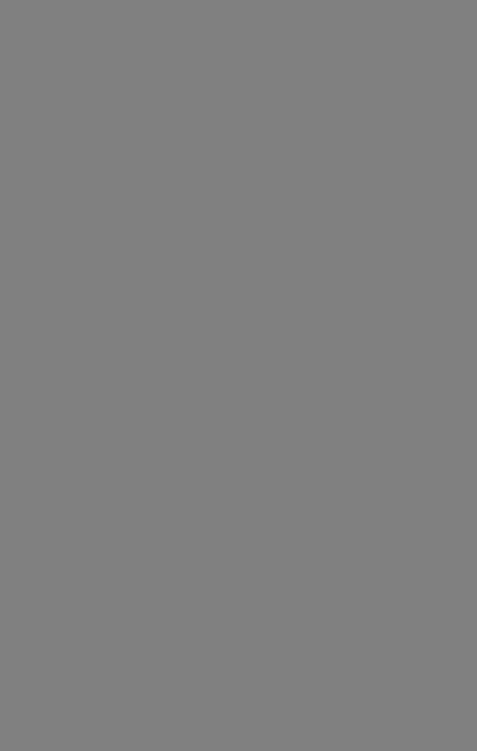
При окончательном нарезании зубчатых колес для каждого модуля применяют комплект из 15 чистовых фрез. Каждым номером фрезы нарезается зубчатое колесо с числом зубьев 12, 13, 14, 15-16, 17-18, 1920, 21-22, 23-25, 26-29, 30-34, 35-51,42-54, 55-79, 80-134, 185 и более.
Размеры пальцевых модульных фрез приведены в таблице 14.
Таблица 14. Основные размеры пальцевых модульных фрез, мм
Z к
19-22
30-41
80 и более
19-22
30-41
80 и более
19-22
30-41
80 и более
19-22
30-41
80 и более
19-22
30-41
80 и более
19-22
30-41
80 и более
19-22
30-41
80 и более
19-22
30-41
80 и более
19-22
30-41
80 и более
М |
D |
d |
ч, |
S |
П |
L |
1 |
|
|
65 |
|
50 |
|
|
|
||
|
мзо |
40 |
22 |
105 |
47 |
|||
20 |
60 |
46 |
||||||
М24 |
32 |
42 |
||||||
|
52 |
41 |
|
|
||||
|
|
|
|
|
|
|||
|
80 |
МЗО |
40 |
55 |
|
|
47 |
|
22 |
65 |
50 |
20 |
110 |
||||
М24 |
32 |
42 |
||||||
|
60 |
46 |
|
|
||||
|
|
|
|
|
|
|||
|
85 |
М36 |
50 |
65 |
26 |
|
58 |
|
25 |
75 |
60 |
22 |
125 |
||||
МЗО |
40 |
47 |
||||||
|
65 |
50 |
20 |
|
||||
|
|
|
|
|
||||
|
95 |
М36 |
50 |
65 |
26 |
135 |
58 |
|
28 |
85 |
|||||||
МЗО |
40 |
60 |
22 |
120 |
47 |
|||
|
85 |
|||||||
|
|
|
|
|
|
|
||
|
105 |
М42 |
|
80 |
28 |
150 |
58 |
|
32 |
95 |
50 |
70 |
|||||
М36 |
26 |
|||||||
|
85 |
|
65 |
|
|
|||
|
|
|
|
|
|
|||
|
120 |
М42 |
50 |
80 |
28 |
160 |
58 |
|
36 |
105 |
|||||||
М36 |
75 |
26 |
||||||
|
95 |
|
|
|
||||
|
|
|
|
|
|
|
||
|
130 |
М42 |
|
80 |
28 |
170 |
58 |
|
40 |
120 |
50 |
||||||
|
105 |
|
|
|
|
|
|
|
|
150 |
М56 |
|
|
|
190 |
80 |
|
45 |
130 |
90 |
90 |
33 |
||||
М48 |
70 |
|||||||
|
120 |
|
|
|
|
|||
|
|
|
|
|
|
|
||
|
170 |
М64 |
|
|
35 |
210 |
82 |
|
50 |
150 |
М50 |
100 |
100 |
||||
70 |
||||||||
|
130 |
М48 |
|
|
|
|
||
|
|
|
|
|
|
н
13
11 51
13
58
11
15
65
13
15
13 73
15 82
15 91
25 100
23
115
19
23
230
19
Пальцевыми модульными фрезами нарезают зубчатые колеса с прямыми, винтовыми и шевронными зубьями. Пальцевые фрезы ра ботают в тяжелых условиях, т.к. из-за консольного крепления инст румента усилия подачи вызывает большой изгибающий момент.
Для чернового нарезания могут быть рекомендованы высокопро изводительные острозаточенные черновые пальцевые модульные фрезы конструкции ЦНИИТМАШ [23, 38] (рис.40).
Профиль этих фрез представляет собой ломаную линию. Их зата чивают по задней поверхности на универсально-заточных станках. Имеются конструкции пальцевых фрез, зубья которых оснащены напайными пластинами из твердого сплава.
Нарезание зубчатых колес еди ничным делением производится на специальных станках с верти кальной или горизонтальной осью изделия, а также на некоторых моделях универсальных зуборез ных станков, имеющих механиз мы единичного деления. Фрезер ные станки с делительной го ловкой используются только в отсутствии специальных зубо фрезерных станков. Технические характеристики станков для ра боты дисковыми и пальцевыми модульными фрезами представ лены в справочной литературе (например, [23, 38]).
Рис.40. Острозаточенная пальцевая фреза конструкции ЦНИИТМАШ.
3.1.2. Контурное долбление зубьев многорезцовыми головками (способ «Shear speed»)
Способ «Shear speed» разработан фирмой Michigan Tool и пред назначен для одновременного долбления всех зубьев венца. Этим вы сокопроизводительным способом можно обрабатывать наружные и внутренние, закрытые и открытые зубчатые венцы прямозубых ци линдрических колес, зубчатые муфты и шлицы.
Режущим инструментом является резцовая головка с расположен ными радиально выдвижными затылованными резцами. Число рез цов в головке соответствует числу впадин обрабатываемого колеса. Форма режущей кромки резцов соответствует форме впадин. Для каждого обрабатываемого зубчатого колеса в соответствии с его мо дулем и количеством зубьев изготавливается специальная головка. Поскольку изготовление многорезцовых головок и самих фасонных резцов — процесс трудоемкий и дорогостоящий, указанный способ
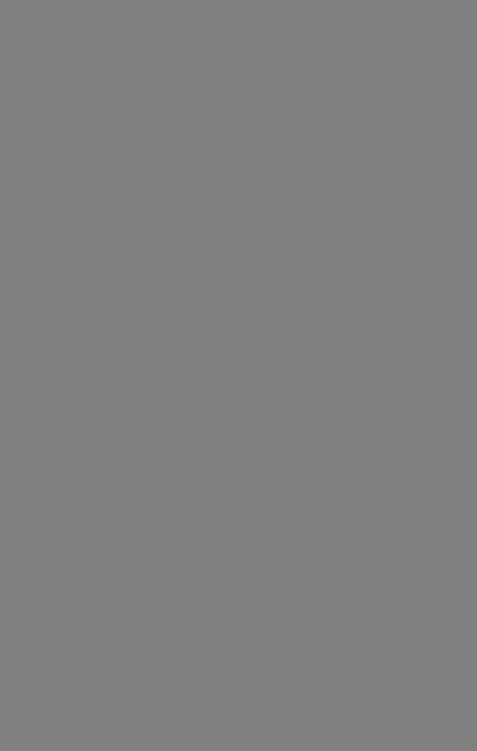
целесообразно применять в массовом и крупносерийном производ стве. Обычно контурное долбление используется для получистового нарезания зубьев под шевингование или для чистовой обработки колес 7-8 степени точности по ГОСТ 1643-81.
Головка состоит из двух стальных дисков 1 и 2 (рис.41б). В ниж нем диске сделаны пазы для резцов, число которых равно числу зу бьев нарезаемого колеса. Нарезаемое колесо 1 закрепляется на вер хнем конце подвижного штосселя 2 (рис.41а), расположенного под многорезцовой головкой, и получает возвратно-поступательное дви жение в вертикальной плоскости. Резцы 3, установленные в непод вижной головке, после каждого рабочего хода заготовки получают перемещение в радиальном направлении.
При обработке силы резания, действующие на резцы, передают ся через нижний диск на неподвижный шток станка. Таким образом, корпус головки разгружен от сил резания и служит только для на правления и перемещения резцов. Резцы получают движение пода чи к оси колеса от конусов 4 и 5, опускающихся на определенную величину после каждого двойного хода заготовки. Подача в процес се обработки колеса переменна: в начале работы она больше (до 0,4 мм/дв.ход), в конце меньше (до 0,025 мм/дв.ход).
Для избежания трения резцов об обработанную поверхность при обратном ходе штосселя перед ходом заготовки вниз резцы разводятся на 0,5мм при помощи конуса отвода 5, взаимодействующего с внутрен ней поверхностью хвостовиков резцов. Резцы взаимозаменяемы и ус танавливаются на скользящей посадке. Они профилируются как фасон ный инструмент, не изменяющий своего профиля при переточках.
Многорезцовыми головками можно нарезать колеса с модулем от 2 до 10,5мм. Фирма изготавливает шесть моделей станков для обра ботки зубчатых колес с наружным диаметром 25-508 мм.
Несмотря на невысокую скорость резания — от 3 до 10 м/мин производительность обработки в 8-10 раз превышает альтернатив ную обработку на зубофрезерных и зубодолбежных станках.
Резцы затачиваются на плоскошлифовальном станке: все резцы шлифуют одновременно по передней грани. Форма профиля резца сохраняется весь срок службы.
3.1.3. Протягивание зубьев осевыми протяжками
Процесс формообразования наружных и особенно внутренних зуб чатых и шлицевых венцов способом осевого протягивания широко применяется в условиях крупносерийного и массового производства.
Протягивание выполняется на вертикальных и горизонтальных протяжных станках и является высокопроизводительным процессом, обеспечивающим довольно высокую точность.
При обработке протягиванием решающее значение для результа тов работы имеет инструмент, его конструкция и качество изготов ления. Протяжка является сложным и точным инструментом, кото рый выполняет также функции подачи станка. Процесс резания при протягивании усложняется вследствие необходимости размещения стружки в ограниченном пространстве впадины зуба.
В связи с этим обработку эвольвентных зубьев, а также шлицев — эвольвентных, прямобочных и трапецеидальных ведут по следую щим схемам резания:
•профильно-генераторная схема. Заключается в том, что срезание припуска производится зубьями, имеющими переменный про филь, постепенно переходящий от прямолинейной или круг лой формы к заданному профилю на изделии;
•групповая (прогрессивная) схема. Отличается тем, что металл сре зается не кольцевыми слоями по всему профилю, а разделяется на части так, что каждый зуб срезает металл только с части профиля. И так последовательно, пока не будет снят металл со всего профиля.
В зависимости отделительного диаметра и длины протягиваемых зубьев протяжки проектируются либо одинарными, либо комплек том из двух или более единиц. Для получения высокой точности и необходимого класса шероховатости поверхности протяжки выпол няются комбинированными — с цилиндрическим и зубчатым про филями. Пример такой протяжки представлен на рис.42.
Если обработку приходится вести комплектом из двух и более протяжек, то на последней протяжке комплекта предусматривают несколько круглых зубьев, оставляя для них небольшую часть при пуска по внутреннему диаметру зубчатого венца. Это обеспечивает соосность внутреннего и наружного диаметров отверстия. Протяги ванием можно обрабатывать внутренние венцы с делительным диа метром до 400 мм.
Обычно протягивание зубчатых колес внутреннего зацепления не обеспечивает высокого качества, поэтому для изготовления прямо зубых и косозубых колес внутреннего зацепления автоматических коробок передач автомобилей метод протягивания был усовершен ствован.
Фирма National Broach изготавливает такие колеса специальны ми протяжками до окончательного размера из целой заготовки за
Рис.42. Образец протяжки для внутреннего зубчатого венца.
один ход заготовки. Протяжка состоит из двух секций: черновой и чистовой. Чистовая секция съемная, плавающая, типа гильзы. Ее зу бья имеют эвольвентную форму на всей высоте. Чистовая секция производит окончательную обработку профиля зуба колеса, образо ванного черновой частью протяжки. Такая протяжка обеспечивает точный и стабильный размер зуба.
Наружные зубья цилиндрических зубчатых колес могут протяги ваться одновременно по всей окружности охватывающей протяжкой, которая может быть изготовлена цельной из одной заготовки или сборной из отдельных реек.
Фирмой National Broach разработан также высокопроизводитель ный процесс протягивания точных эвольвентных зубчатых колес с внешним зацеплением протяжками чашечного типа с внутренними зубьями. Процесс обработки заключается в проталкивании целой за готовки через протяжку за один ход. Чашечная протяжка монтиру ется над обрабатываемой деталью. Деталь устанавливается на длин ной колонке, а чашечная протяжка подается вниз на деталь с помо щью гидроцилиндра.
Кольцеобразная чашечная протяжка состоит из держателя и от дельных точно шлифованных стальных колец, закрепленных шпон кой, внутренние зубья которых индивидуально затылованы. Чашеч ная протяжка представляет собой зубчатое колесо с внутренними затылованными зубьями. Кольца затачивают по торцовой поверхности с последующим шлифованием внутренней поверхности. Этот метод обработки обеспечивает высокую точность по шагу и профилю зуба (около 0,005 мм). Производительность протяжных станков-автома тов 240-300 дет/час [40].
Важнейшими достоинствами зуборезных протяжек являются: большой срок службы, длительное сохранение точности и большое количество переточек.
3.1.4. Шлифование зубьев фасонным кругом.
Обработка производится на специальных зубошлифовальных стан ках, где в качестве инструмента используется профильный круг (рис.43).
Зубошлифование можно производить двумя способами: одним шли фовальным кругом, фасонный профиль которого образуется с помо щью механизма правки с эвольвентными копирами, имеющими про филь, соответствующий форме обрабатываемых впадин зубьев и двумя шлифовальными кругами, фасонный профиль на каждом из которых образуется алмазами механизма правки, воспроизводящими эвольвен-
тный профиль без применения фасонных копиров. Правка круга производится несколько раз за цикл обработки одного колеса.
В процессе обработки прямо зубых колес профилированный круг перемещается вдоль оси ко леса и за каждой ход полностью профилирует обе стороны одной впадины. После выхода круга из зацепления с колесом последнее поворачивается на угол, соответ
ствующий одному шагу. После полного оборота колеса круг подается в радиальном направлении и цикл повторяется.
При шлифовании косозубых колес схема обработки изменяется. Круг поворачивается на угол наклона зуба р, при продольном пере мещении круга вдоль оси колеса оно получает доворот на угол со, оп ределяемый в зависимости от угла наклона зубьев шестерни.
При шлифовании профильным кругом контакте зубьями проис ходит по всему периметру впадины. Из-за снятия большого количе ства металла вероятность появления прижогов на обрабатываемых зубьях увеличивается. Поэтому режимы шлифования профильным кругом подбираются особенно тщательно.
В связи с тем, что форма и положение рабочей поверхности круга зависят от параметров шлифуемого зубчатого колеса, станки с профиль ным кругом целесообразно применять в условиях крупносерийного и массового производства. Производительность таких станков высока. Получаемая точность зубчатых колес — 6 степень по ГОСТ 1643-81.
Модели и технические характеристики оборудования, работаю щего профильным кругом, представлены в [38].
3.2. Формообразование методом обката
Сущность метода обката состоит в том, что в процессе нарезания зубьев воспроизводится зацепление сопряженных деталей зубчатой пары, из которых одна деталь является заготовкой нарезаемого ко леса, а другая — режущим инструментом. Физический смысл мето да поясним на простом примере. Пусть задан какой-то криволиней ный профиль (рис.44).
Проведя к нему ряд касательных 1,2, 3... этот профиль можно рас-