
книги / Цилиндрические зубчатые колеса
..pdfменем с высокой, около 3100°С, температурой, образующимся при горении ацетилена и кислорода при соотношении кислорода и газа 1:1,3. Охлаждение после нагрева производится с помощью душа из воды или эмульсии, а также погружением в масло. Глубина термооб работанного слоя при различных показателях процесса составляет 1,3-3,Омм. Преимуществом метода газопламенной закалки является простота и универсальность применяемого оборудования. Основной недостаток — трудность получения оптимальной температуры нагре ва без специальных малоинерционных устройств, обеспечивающих автоматическое регулирование температуры.
Наиболее совершенным методом поверхностной закалки являет ся закалка с использованием ТВЧ. Изделие при этом помещается в ин дукторе, через который пропускается ток высокой частоты от 103 до 106 Гц. Вследствие этого в поверхностных слоях изделия индуктиру ются вихревые токи, посредством которых производится быстрый нагрев наружной зоны детали. После нагрева производится охлаж дение душем водой или эмульсией. В некоторых случаях нагретое изделие погружается в бак с маслом.
При заданной толщине слоя режим нагрева определяется часто той тока, подводимой удельной мощностью и длительностью нагре ва. Вследствие высокой скорости нагрева (200-600°С/с) и небольшой продолжительности выдержки при закалке ТВЧ оптимальная темпе ратура нагрева на 100-150°С выше, чем при обычной закалке.
В результате закалки ТВЧ значительно повышается твердость, износостойкость и усталостная прочность. Однако в зубчатых ко лесах повышение усталостной прочности достигается только в том случае, если применяемый метод закалки обеспечивает обработку поверхности зуба по контуру с обязательной закалкой переходной поверхности у корня зуба, являющейся наиболее опасной зоной в колесе.
Основная масса зубчатых колес, используемых в тяжелонагруженных и высокоскоростных агрегатах, проходит химико-термическую об работку. При химико-термической обработке производится измене ние химического состава поверхностного слоя изделий в результате диффузии в сталь различных элементов из внешней среды. После насыщения производится закалка и низкий отпуск.
Из множества процессов химико-термической обработки наибо лее существенное значение для колес имеют газовая цементация, а также нитроцементация (газовое цианирование).
Цементация — это процесс насыщения поверхности углеродом. В результате последующей термической обработки получают повыше
ние твердости и износостойкости, а также повышение усталостной прочности и контактной выносливости.
Газовая цементация — производится в шахтных печах и в печах не прерывного действия, муфельных и безмуфельных. Газовая смесь получается непосредственно в рабочем пространстве. Температура прогрева 930-950°С. Время выдержки зависит от необходимой глуби ны слоя. Например, при глубине слоя 1,0-1,3 мм время выдержки 7- 9 часов в шахтных печах и 8-10 часов в печах непрерывного действия.
Цементация может также производиться в твердом или жидком карбюризаторах. Твердый карбюризатор — это смесь древесного угля или каменноугольного полукокса с углекислыми солями бария и кальция. Температура прогрева 880-980°С (преимущественно 930°С). Время выдержки для получения слоя 0,8-1,2 мм от 6,5 до 10 часов. Жидкий карбюризатор — это смесь расплавленных солей NaCN, ВаС12, NaCl. Температура прогрева 850-950°С. Время выдержки для получения слоя 0,8-1,3 мм от 2 до 4 часов.
Нитроцементация — это процесс одновременного насыщения по верхности углеродом и азотом с целью повышения твердости, изно состойкости и сопротивления усталости. Процесс происходит в сме си цементирующего газа и аммиака при температуре прогрева 820860°С. Время выдержки для получения слоя 0,8-1,0 мм от 4 до 5 часов.
Для зубчатых колес наиболее ответственного назначения приме няется другой вид химико-термической обработки — азотирование.
Азотирование — это насыщение поверхности азотом с целью повыше ния твердости, износостойкости и предела усталости. Процесс азоти рования производится в шахтных печах в среде аммиака. Зубчатые ко леса перед азотированием подвергаются, как правило, предварительно му улучшению и полной механической обработке. При различных видах азотирования температура прогрева составляет от 480 до 600°С. Аммиак при этой температуре распадается на азот и водород. Азот со единяется с некоторыми легирующими элементами, образуя нитриды, имеющие высокую твердость. Длительность процесса для получения глубины слоя 0,4-0,7 мм составляет от 10до 25 часов. Достигаемая твер дость поверхности при указанных температурах до HV 600.
Азотированию подвергаются высоколегированные стали с содер жанием Cr, Al, Mo, V, W, типа 38ХМЮА, 18Х2Н4ВА.
Применяемые стали и методы химико-термической обработки должны обеспечить соблюдение следующих основных требований:
• Глубина слоя должна быть в пределах 0,25-0,35 от половины толщины зуба при концентрации углерода на поверхности 0,8- 1,0% и при поверхностной твердости HRC 59-63;
•Структура слоя — мелкоигольчатый мартенсит с небольшими изолированными участками остаточного аустенита. Недопус тимы выделения карбидов в форме сетки в цементованном слое и массивные включения карбонитридов в нитроцементованном слое;
•Структура сердцевины — малоуглеродистый мартенсит или бейнит без выделений структурно свободного феррита.
2.4.Деформации и их причины
Впроцессе проведения термической или химико-термической обработки зубчатых колес всегда происходят изменения их основных поверхностей: появляется овальность и конусообразность отверстий, отклонение от плоскостности опорного торца, возникает биение шеек относительно центров, а также происходит деформация зубь ев. Каждое из перечисленных отклонений само по себе влияет на окончательную точность зубчатого венца, однако возможна дефор мация зубьев и без существенного изменения остальных параметров зубчатого колеса.
Вцилиндрических зубчатых колесах деформация зуба в процес се термообработки оказывает влияние на эвольвентный профиль и угол наклона зуба косозубых колес. Степень влияния зависит от вида термической обработки. Максимальные поводки дает объемная за калка, меньшие — химико-термическая обработка. Наименьшие де формации происходят в процессе азотирования. Опыт проверки хи мико-термической обработки зубчатых колес в автомобильной про мышленности (в частности, на АМО «ЗИЛ» и АО «ГАЗ») показывает, что при цементации угол профиля зуба увеличивается в зависимос ти от модуля и глубины слоя цементации, а угол наклона линии зуба косозубых колес уменьшается, т.е. зуб как бы выпрямляется. По дан ным, приведенным в работе [10], отклонения эвольвентного профи ля и хода винтовой линии зуба при цементации следующие:
Модуль, мм |
1,5-2,0 |
2,0-4,0 |
|
4,0-6,5 |
|
Отклонение профиля, мкм |
5-7,6 |
7,6-20 |
|
20-25 |
|
Наклон зуба, град. |
|
5-10 |
10-20 |
20-30 |
30-40 |
Погрешность хода винтовой линии, мкм |
5-7,6 |
7,6-13 |
13-18 |
18-25 |
Приведенные величины отклонения эвольвентного профиля и угла спирали при цементации могут меняться в зависимости от ма-
териала, вида термической обработки, формы и размера зубчатого колеса.
Деформация и коробление зубчатых колес в процессе их химико термической обработки обуславливается целым рядом фактором. Среди них особо следует отметить такие, как температура и время нагрева, длительность насыщения деталей углеродом и азотом, со став насыщающей атмосферы, температура закалки, температура за калочного масла. Поскольку колебания этих факторов носят случай ный характер, то и деформации, вызываемые ими, нестабильны.
Немаловажное влияние на возникновение деформаций оказыва ют: укладка деталей на поддонах, состав печных атмосфер, охлажда ющая способность закалочных устройств, конструктивные и тепло технические особенности печей и агрегатов.
В связи с тем, что термическая или химико-термическая обработ ка во многих случаях является заключительным этапом в общем про цессе изготовления зубчатых колес, принято считать, что основной причиной нестабильной и повышенной деформации является несо вершенство прежде всего этих процессов. Это связано с тем, что на этом этапе технологического процесса изготовления зубчатого коле са происходит большая часть общей деформации и именно на этой стадии проявляется ее нестабильность.
Глава 3
Методы и способы образования поверхности зубьев
Подавляющее большинство методов зубообработки характеризу ется кинематическими процессами, сводящимися к взаимному обка тыванию зубообрабатывающего инструмента относительно обраба тываемой заготовки. При обработке зубчатых колес различают три метода образования поверхности зубьев [30]:
•метод копирования, в котором контактные линии между повер хностью инструмента совпадают с плоским сечением произво дящей поверхности инструмента. Этот метод обычно сочета ется с индивидуальным делением, но может быть осуществлен
ибез деления, например, при одновременной обработке зубо долбежными головками всех зубьев колеса.
•метод огибания (бесцентроидного огибания) с индивидуальным делением, при котором профиль нарезаемых зубьев получается как огибающая различных положений производящей поверх ности инструмента. На этой поверхности лежат режущие кромки, но в процессе нарезания центроиды на инструменте
инарезаемом колесе отсутствуют. Метод применяется при на резании косозубых колес и червяков фасонными фрезами; со четается с индивидуальным делением.
•метод обката — частный случай огибания (метод центроидного огибания), при котором центроиды инструмента и нареза емого колеса катятся друг по другу без скольжения. Профиль нарезаемых зубьев получается в процессе обработки как оги бающая различных положений производящей поверхности инструмента, которая образуется режущими кромками инст румента. Различают две разновидности: метод принужденно го обката, осуществляемый при обработке колес гребенками, червячными фрезами, долбяками, червячным шлифовальным кругом, и метод свободного обката, используемый при обра ботке колес шеверами, притирами, хонами и др.
5 Заказ 4583
3.1. Формообразование методом копирования
При обработке методом копирования применяется фасонный ин струмент, профиль которого точно копируется на впадине между зу бьями. Этот метод предусматривает последовательное фрезерование каждой впадины, т.е. после обработки одной впадины заготовка по ворачивается на один шаг и производится фрезерование следующей впадины. Для осуществления обработки методом копирования ис пользуются либо специальные зубофрезерные станки, либо универ сально-фрезерные станки с делительной головкой.
Основным недостатком зубонарезания методом копирования явля ется необходимость использования большого количества инструментов для обработки колес одного модуля, но с разным числом зубьев. Эвольвентный профиль зависит от числа зубьев колеса, т.е. у зубчатых колес одного и того же модуля, но с разным числом зубьев профили зубьев неодинаковы. Поэтому теоретически для каждого модуля и числа зубьев необходима отдельная фреза. На практике нарезание зубчатых колес в условном диапазоне чисел зубьев производится одним инструментом, что неизбежно приводит к снижению точности профиля зубьев.
Поскольку при методе копирования фасонные поверхности зуба образуются профилем фрезы, необходимо в процессе переточки ин струмента сохранять точность заданного профиля. С этой целью зад няя поверхность зубьев фрезы обрабатывается по кривой линии (затылуется). Эта кривая представляет собой архимедову спираль, обес печивающую постоянство величины заднего угла и, как следствие, сохранение профиля зуба при переточках.
К способам обработки цилиндрических зубчатых колес по мето ду копирования относятся:
•фрезерование зубьев дисковыми модульными фрезами;
•фрезерование зубьев пальцевыми модульными фрезами;
•контурное долбление зубьев многорезцовыми головками;
•протягивание зубьев осевыми протяжками;
•шлифование зубьев фасонным кругом.
3.1.1.Фрезерование зубьев дисковыми и пальцевыми
модульными фрезами
Этот способ малопроизводительный, поэтому применяется, в ос новном, при изготовлении запасных частей в ремонтном деле и при изготовлении небольших партий зубчатых колес, к точности которых
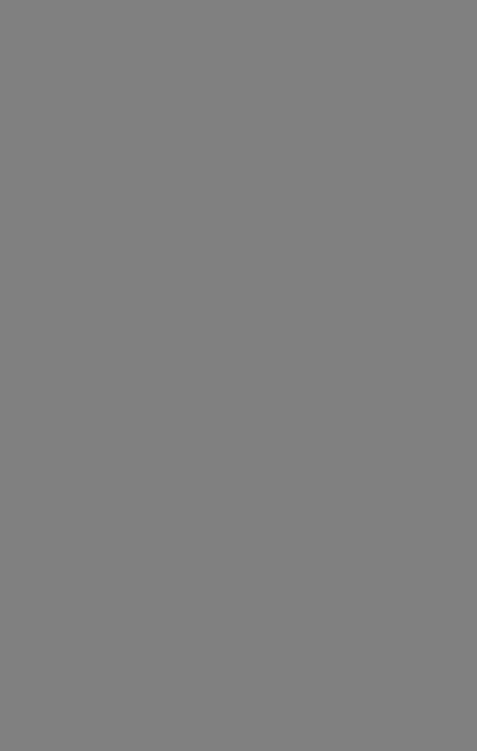
Таблица 9. Комплекты дисковых модульных колес
|
Число зубьев колес, |
|
Число зубьев колес, |
|||
Номер |
нарезаемых комплектом |
Номер |
нарезаемых комплектом |
|||
с числом фрез |
с числом фрез |
|||||
фрезы |
фрезы |
|||||
|
|
|
|
|||
|
8 |
15 |
|
8 |
15 |
|
1 |
12-13 |
12 |
5 |
26-34 |
26-29 |
|
1 1/2 |
|
13 |
5 1/2 |
|
30-34 |
|
2 |
14-16 |
14 |
6 |
35-54 |
35-41 |
|
2 1/2 |
- |
15-16 |
6 1/2 |
- |
42-54 |
|
3 |
17-20 |
17-18 |
7 |
55-134 |
55-79 |
|
3 1/2 |
|
19-20 |
7 1/2 |
|
80-134 |
|
4 |
21-25 |
21-22 |
8 |
135 — рейка |
135 — рейка |
|
4 1/2 |
|
23-25 |
|
|
|
Таблица 10 - Значение коэффициента кр
Р°
■S
5 |
10 |
15 |
20 |
25 |
30 |
35 |
40 |
45 |
1,011 |
1,045 |
1,104 |
1,193 |
1,323 |
1,505 |
1,756 |
2,119 |
2,64 |
Таблица 11. Основные размеры, мм, дисковых модульных фрез по ОСТ 2И41-14-87
т 0 |
|
d |
zo |
в |
1-1,0375 |
50 |
19 |
14 |
4-5,5 |
1,5-1,75 |
55 |
22 |
14 |
6-7 |
2-2,25 |
63 |
22 |
12 |
8-8,5 |
2,5-2,75 |
70 |
22 |
12 |
9,5-10,5 |
3-3,75 |
80 |
27 |
12 |
11,5-14 |
4-4,5 |
90 |
27 |
12 |
15-16,5 |
5-5,5 |
100 |
27 |
12 |
18-20 |
6-7 |
110 |
32 |
10 |
21,5-24 |
8-9 |
125 |
32 |
10 |
28-31 |
10-11 |
140 |
40 |
10 |
34-37 |
12-14 |
160 |
40 |
10 |
41-47 |
16 |
180 |
50 |
10 |
53 |
В таблице 9 указаны числа зубьев, нарезаемые каждой фрезой, входящей в комплект.
Комплект из 8 фрез не рекомендуется применять для колес с мо дулем выше 8 мм.
Фрезу для нарезания косозубого колеса выбирают по приведен ному числу зубьев Znp , определяемому по формуле
где р — угол наклона зуба нарезаемого колеса; z — число нарезанных зубьев;
кр — коэффициент, определяемый по таблице 10.
Основные размеры дисковых модульных фрез приведены в табл. 11.
Стандартные дисковые модульные фрезы выполняются затылованными. Переточка производится по передней поверхности. Пере дний угол у черновых фрез обычно принимают равным 8-10° У чи стовых фрез, снимающих небольшую стружку, идут на некоторое ухудшение условий резания и принимают его равным 0° Этим обес печивается более высокая точность профиля.
Для повышения производительности, особенно при обработке крупномодульных зубчатых колес, нарезание можно производить набором из двух или трех дисковых модульных фрез по схеме, при веденной на рис.36.
Расстояние между фрезами, соответствующее шагу нарезаемого колеса, устанавливается с помощью промежуточных колец.
Дисковые модульные фрезы изготавливают из быстрорежущей стали с твердостью рабочей поверхности HRC 61-64. В целях эконо мии быстрорежущей стали применяют сборные дисковые модульные фрезы со вставными ножами (рис.37, табл. 12). Сборные фрезы нор мализованы для модулей от 8 до 30мм.
Для чернового нарезания зубьев колес средних и крупных моду лей рекомендуется применять
а |
а |
острозаточенные фрезы с пере |
|
Т |
Р |
менным направлением зубьев |
|
(рис.38, табл. 13). |
|||
|
|
||
|
' g |
Фрезы такого типа имеют кли |
|
а# |
новидные правые и левые ножи с |
||
|
углом наклона 2°30' в радиаль |
||
|
w |
ном и 5° в поперечном направле |
|
|
ниях. Фрезы затачиваются по |
||
Рис.36. Фрезерование зубьев набо |
задним поверхностям, что по |
||
ром дисковых фрез: а) тремя фреза |
зволяет резко увеличить зад |
||
ми; б) двумя фрезами. |
|
ние углы по сравнению с затыло- |
Рис.37. Сборная модульная дисковая фреза: 1 — корпус фрезы; 2 — зубья; 3 — штифты.
Таблица 12. Основные размеры сборных модульных дисковых фрез со вставными ножами
Модуль фрезы, мм
8
10
12
14
16
18
20
22
24
26
28
30
Наружный диаметр фрезы, мм
180
195
220
220
240
270
Припуск по |
Диаметр отверстия |
толщине зуба, мм |
под оправку, мм |
1,0
1,2
1.3
1.3
1.3
1.3
60
1.4
1.5
1.7
1.8
1,9
2,0
ванными фрезами. Чередование правых и левых резцов обеспечива ет передний угол 10° на боковых и наружных режущих кромках. На боковых режущих кромках выполняют стружкоделительные канав ки. По мере стачивания резцы можно выдвигать на шаг рифлений.