
книги / Химия диэлектриков
..pdfмного экономичнее и безопаснее, чем любой органический растворитель при полимеризации в растворе.
Поскольку вся масса мономера разделена на микроблоки (капли), легко контролировать длину цепей и можно получить высокомолекулярный продукт с узким молекулярно-массовым распределением.
Полимеризация протекает почти всегда на 100 %, т. е. мономер расходуется полностью и не загрязняет полимер, который образуется с высоким выходом.
Полимер получается в виде гранул. Его легко отделить от воды фильтрованием, а остатки ПАВ и защитных коллоидов смываются с поверхности гранул чистой водой. Промытые и высушенные полимерные гранулы перерабатывают в изделия экструзией, литьем под давлением или растворяют для получения лаков и клеев.
Суспензионную радикальную полимеризацию используют для получения гранул полистирола, которые перерабатываются в пенополистирол (пенопласт). Этим же способом получают полисти- рол-дивинилбензольные гранулы для изготовления ионообменных смол и гранулы поливинилацетата для переработки в поливиниловый спирт.
4.1.4. Эмульсионная полимеризация
Мономер, как и в предыдущем способе, диспергируют в воде, но не до отдельных капель, а до однородной эмульсии. Эмульсию стабилизируют эмульгаторами: ПАВ, защитными коллоидами, буферными растворами.
Поскольку поверхностно-активные вещества берутся в количе- ствах, превышающих критическую концентрацию мицеллообразования, они находятся в системе в мицеллярной форме. Добавляемый в систему мономер солюбилизируется в ядрах мицелл. Если мономер частично растворим в воде, то водный раствор эмульгатора содержит некоторое количество молекул мономера. Можно также допустить, что очень небольшая часть мономера находится в системе в виде мелких капелек, как при суспензионной полимеризации. Таким образом, эмульсия является сложной комплексной системой, в которой водный молекулярный раствор эмульгатора является дисперсионной средой, а дисперсную фазу образуют мицел-
61
лы ПАВ с солюбилизированным мономером и мелкие мономерные капли.
Как правило, в эмульсионной полимеризации используют водорастворимые инициаторы типа персульфатов или гидропероксидов. Поскольку инициатор водорастворим, а мономер нерастворим или очень мало растворим в воде, трудно представить, что молекулы инициатора попадут в капли мономера. Следовательно, полимеризация внутри этих капель маловероятна.
Напротив, полярная поверхность мицелл хорошо адсорбирует молекулы инициатора. Полимеризация легко инициируется на поверхности мицелл и распространяется далее вглубь ядер мицелл. По мере расходования мономера в мицеллу диффундируют новые мономерные молекулы из водного раствора и из отдельных мономерных капель до полного их исчерпания. Полимерная молекула продолжает свой рост, пока в мицеллу не попадет другой радикал
èне оборвет цепь. Такое бывает нечасто, поэтому полимеризация идет обычно до полного исчерпания мономера. При этом получаются макромолекулы с очень большой молекулярной массой. Эти молекулы объединяются в более крупные агрегаты, на поверхности которых адсорбируются молекулы ПАВ из мицелл и из раствора. Такие агрегаты адсорбируют и молекулы мономера, набухая в нем
èувеличивая свои размеры и рыхлость клубка. Это только способствует проникновению в клубок новых молекул мономера, и полимеризация идет все дальше и дальше.
Âрезультате образуются мелкие частички полимера, стабилизированные слоем эмульгатора и равномерно распределенные в водной фазе. Эту молочно-белую коллоидную систему называют латексом. По окончании реакции латекс готов к употреблению. Его используют или в качестве адгезива, или как водоэмульсионную краску.
Полимер можно выделить из латекса путем коагуляции. Коагуляцию проводят электролитами, высушиванием или вымораживанием.
Описанная схема полностью выполнима, только если инициатор абсолютно нерастворим в мономере, а мономер совершенно нерастворим в воде. В действительности механизм эмульсионной полимеризации сложнее и меняется от системы к системе. В зависимости от растворимости мономера, инициатора и эмульгатора, от
62
их соотношения и концентрации в системе процесс полимеризации может протекать и в растворенном в воде мономере, и на границе раздела вода — мономерная капля, и внутри мономерных капель. Конечный результат тем не менее во всех случаях будет одинаков — образуется латекс, т. е. мелкодисперсные частицы полимера, стабилизированные слоем молекул ПАВ на их поверхности.
Эмульсионная полимеризация — самый распространенный в промышленности способ. По этому способу полимеризуют винилхлорид, бутадиен, хлоропрен, акрилаты и метакрилаты.
Преимущества способа. Легко регулировать теплоперенос в системе. Полимеризация идет в мицелле, в маленькой частице с большой удельной поверхностью. Поэтому очень высока скорость реакции в ядре мицеллы.
Число растущих цепей в мицелле ограничено, не увеличивается
èне уменьшается во времени, а мономер извне поступает регулярно
èв неограниченном количестве. Поэтому в каждой мицелле полу- чается мало, но очень больших и одинаковых по размерам макромолекул.
Образующийся латекс является готовым товарным продуктом. Серьезным недостатком эмульсионной полимеризации является загрязнение полимера остатками эмульгаторов и электролитов,
что значительно ухудшает диэлектрические свойства продукта.
4.1.5. Твердофазная и газофазная полимеризация
Хотя основным видом полимеризации в промышленности являются жидкофазные процессы, иногда полимеризацию проводят в твердой или газовой фазе.
Если мономер представляет собой неплавкое и нерастворимое термически нестойкое твердое вещество, он может быть заполимеризован только в твердой фазе. Твердофазная полимеризация представляет наибольшие трудности для роста цепи. Кроме того, чтобы исключить термическое разложение мономера (а иногда и полимера), реакцию обычно проводят при низких температурах, а следовательно, возможно только фотоили радиационное инициирование. Скорость реакции в этих условиях крайне низкая.
Примером твердофазной полимеризации может служить радиационное сшивание триоксана в полиформальдегид:
63
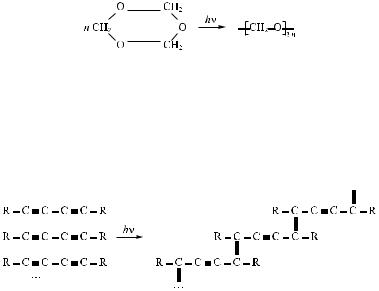
В результате полимеризации получается волокнообразный полимер с высокой механической прочностью и стойкостью к истиранию. В отличие от мономера, он устойчив при температуре до 80 °С и выдерживает кратковременный нагрев до 120 °С.
При фотополимеризации твердых диацетиленов получаются высококристалличные электропроводные полимеры:
Газофазную полимеризацию используют крайне редко, в основном из-за очень плохого отвода тепла. В качестве примера назовем полимеризацию этилена на катализаторе Циглера — Натта.
Хлорид титана и триэтилалюминий смешивают в среде пентана
èраспыляют смесь в колонне с насадкой. Пентан испаряется, а катализатор оседает на внутренней поверхности колонны и на насадке в виде тонкой пудры.
Âколонну при температуре от комнатной до 70–80 °С под небольшим давлением (4–5 ат) подают газообразный этилен. Соприкасаясь с катализатором, этилен полимеризуется. Образующийся полимер собирают со дна колонны в виде легкого пушистого порошка.
Получаемый таким путем полиэтилен низкого давления (ПЭНД) является стереорегулярным кристаллическим полимером с молекулярной массой от 100 тысяч до миллиона. По эксплуатационным характеристикам он превосходит полиэтилен высокого давления (ПЭВД), но является более дорогим и несколько быстрее стареет.
Главным недостатком процесса является его огнеопасность
èнеобходимость очистки полимера от твердого катализатора.
64
4.2. Способы проведения процессов поликонденсации
4.2.1. Поликонденсация в расплаве
Этот способ применяют, когда один из мономеров представляет собой твердое вещество и не разлагается при плавлении. Второй мономер (в случае гетерополиконденсации) растворяют в расплаве первого.
Температуры, при которых проводят поликонденсацию в расплаве, достаточно высоки, поэтому процесс проводят в инертной атмосфере азота или углекислого газа, чтобы предотвратить деструкцию получаемого полимера.
Часто реакцию проводят при пониженном давлении, что облег- чает удаление выделяющегося низкомолекулярного продукта. Но даже в таких условиях на окончательном этапе реакции вязкость системы сильно возрастает, что создает трудности для отвода низкомолекулярных продуктов.
Существует еще одно осложнение: полимер получается в виде расплава, и его надо удалять из реактора горячим и немедленно, ина- че он застынет прямо в реакторе. Обычно горячий полимерный расплав сразу направляют на переработку методом экструзии или литья.
Достоинством метода является отсутствие необходимости удаления из полимера растворителя и регенерации последнего.
Поликонденсацией в расплаве в промышленности получают полигексаметиленадипамид (анид или найлон 6,6) из гексаметилендиамина и адипиновой кислоты и лавсан из диметилового эфира терефталевой кислоты и этиленгликоля. Выбор в этом процессе диметилового эфира терефталевой кислоты взамен самой кислоты связан с тем, что диметилтерефталат плавится при более низкой температуре (140 °С, а не 425 °С как кислота) и хорошо растворим в этиленгликоле в отличие от самой терефталевой кислоты.
4.2.2. Поликонденсация в растворе
В этом методе исходные мономеры перед проведением процесса растворяют в инертном растворителе, а сам процесс проводят при 20–50 °С.
Преимущества метода — более низкая по сравнению с поликонденсацией в расплаве температура реакции, облегченный тепло-
65
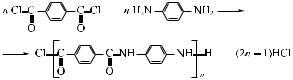
и массообмен. Растворитель может служить улавливающим агентом для выделяющихся низкомолекулярных продуктов, что облег- чает их удаление из реакционной массы.
Недостатки метода. Растворитель уменьшает вероятность роста цепи. Это снижает скорость реакции и молекулярную массу образующегося полимера.
Поликонденсацией в растворе получают большинство жидких полиэфирных смол на основе гликолей и непредельных дикарбоновых кислот. В качестве растворителя берут высококипящие ароматические углеводороды. С образующейся в ходе реакции водой они образуют азеотропные смеси, которые легко отгоняются от конеч- ного продукта.
4.2.3. Поликонденсация на границе раздела фаз
При этом способе реакция протекает на границе двух несмешивающихся фаз: водной и органической. Реагенты должны содержать очень активные функциональные группы, которые быстро реагируют даже при комнатной температуре. Типичный пример — синтез ароматического полиамида из хлорангидрида терефталевой кислоты и пара-фенилендиамина:
Ароматический диамин растворяют в воде, а хлорангидрид кислоты — в хлороформе или четыреххлористом углероде. При сливании этих несмешивающихся растворов молекулы диамина диффундируют в органический слой, реагируют с хлорангидридом и образуют полимер, который нерастворим ни в одной из двух жидкостей и выпадает в осадок в виде пленки на границе двух жидких фаз. Эту пленку непрерывно удаляют, освобождая межфазную поверхность для взаимодействия новых молекул мономеров. Хлористый водород растворяется в воде и с ней отделяется.
66
В промышленных условиях два раствора сливают при очень сильном перемешивании. При этом несмешивающиеся жидкости дробятся на капли, на поверхности которых и образуется полимерная пленка. За счет соударения капель их поверхность постоянно обновляется, поэтому процесс поликонденсации идет с высокой скоростью до полного исчерпания мономеров.
5. СРЕДНЯЯ МОЛЕКУЛЯРНАЯ МАССА ПОЛИМЕРОВ
Как мы знаем, молекулярные массы полимеров огромны. Так молекулярная масса ДНК — около 2 миллиардов, а молекулы водорода — всего 2. Зададимся вопросом: одинаков ли смысл термина «молекулярная масса» в этих двух случаях?
Любое низкомолекулярное вещество имеет определенную молекулярную массу независимо от того, из каких веществ и каким путем оно было получено. Так, молекулярная масса ацетона равна 58. Если анализ дал значение не 58, а 60, то это не ацетон, а другое вещество, возможно, уксусная кислота. Иными словами, молекулярная масса низкомолекулярных веществ есть их характерный признак, неизменная справочная величина.
Другое дело — полимеры. Они содержат молекулы разных размеров, поэтому молекулярная масса полимера есть некая средняя величина — средняя не только для данного вида полимера, но даже для данного образца, полученного в ходе одного синтеза.
Для этилена характерно строго определенное строение молекулы и строго определенная молекулярная масса. Однако полимеризация этилена приводит к образованию неопределенной структуры –(CH2–CH2)n–, где степень полимеризации n зависит от многих условий роста каждой конкретной цепи.
Поскольку обрыв цепи является случайным событием, то и степень полимеризации тоже величина достаточно случайная. В одном образце полиэтилена могут соседствовать такие цепи:
–(CH2–CH2)500–, Ì = 14000; –(CH2–CH2)550–, Ì = 15400; –(CH2–CH2)600–, Ì = 16800.
Три молекулы имеют разную степень полимеризации, разные размеры и разную молекулярную массу, но все они принадлежат полиэтилену. Поэтому молекулярная масса этого образца полиэтилена может рассматриваться только статистически, как некая усредненная величина. А поскольку способов усреднения может быть применено
68
несколько, для одного и того же образца полимера могут быть вычислены несколько различных значений молекулярной массы.
Для полимеров принято определять среднечисловую Mn и среднемассовую Mw молекулярную массу. Это две наиболее распространенные величины, получаемые экспериментально по соответствующим методикам. Рассмотрим их вначале на простом примере.
Представим образец полимера, который состоит из молекул только трех видов: с молекулярными массами 20000, 40000
è60000 у. е. соответственно. Предположим, что в образце полимера содержится 100 молекул первого вида, 200 молекул второго вида
è300 молекул третьего вида.
Рассчитаем среднюю молекулярную массу полимера, считая, что вклад каждого вида молекул в среднюю молекулярную массу пропорционален числу молекул данного вида. Иначе говоря, рас- считаем среднечисловую молекулярную массу Mn.
Составим таблицу:
|
|
Молекулярная масса |
|
Вид молекул |
Число молекул |
(масса одной молеку- |
Общая масса, у. е. |
|
|
ëû), ó. å. |
|
I |
100 |
20000 |
2000000 |
II |
200 |
40000 |
8000000 |
III |
300 |
60000 |
18000000 |
Итого |
600 |
– |
28000000 |
Общее число молекул в полимере — 600; число молекул I вида — 100;
числовая доля молекул I вида (от общего числа молекул) — 100/600 = 1/6;
вклад молекул первого вида в Mn — (1/6)·Ì = (1/6)·20000 = = 3333,3.
Аналогично считаем для молекул второго и третьего вида: Число молекул второго вида — 200;
числовая доля молекул II вида — 200/600 = 1/3;
вклад молекул второго вида в Mn — (1/3)·Ì = (1/3)·40000 = = 13333,3;
число молекул третьего вида — 300;
69
числовая доля молекул третьего вида — 300/600 = 1/2;
вклад молекул третьего вида в Mn — (1/2)·Ì = (1/2)·60000 = = 30000,0.
Сумма вкладов каждого вида молекул и даст среднечисловую молекулярную массу:
Mn = 3333,3 + 13333,3 + 30000 = 46666,6.
Среднемассовую молекулярную массу этого образца полимера рассчитаем, исходя из предположения, что вклад каждого вида молекул в Mw пропорционален не числу молекул, а их молекулярной массе.
Общая молекулярная масса всех молекул — 28000000; масса молекул первого вида — 2000000;
массовая доля молекул первого вида — 2000000/28000000 = = 1/14 = 0,071.
Аналогично рассчитанные массовые доли молекул второго и третьего вида составляют 0,286 и 0,643.
Вклады каждого вида молекул в среднюю молекулярную массу равны произведению массовой доли молекул на их молекулярную массу:
Вклад молекул первого вида = 0,071·20000 = 1420,0. Вклад молекул второго вида = 0,286·40000 = 11440,0. Вклад молекул третьего вида = 0,643·60000 = 38580,0.
Сумма вкладов каждого вида молекул даст среднемассовую молекулярную массу:
Mw = 1420,0 + 11440,0 + 38580,0 = 51440,0.
Итак, для одного и того же образца полимера мы нашли два зна- чения средней молекулярной массы, причем Mn существенно меньше, чем Mw.
Для всех синтетических полимеров среднечисловая молекулярная масса всегда меньше, чем среднемассовая, Mn Mw. Если эти значения равны, то это значит, что образец мономолекулярен, т. е. все входящие в него молекулы имеют одинаковую степень полимеризации и одинаковую молекулярную массу. На практике такого никогда не бывает.
Существуют и другие способы выражения молекулярной массы полимеров, связанные с экспериментальными методами изуче-
70