
книги / Строительная механика и расчеты композитных конструкций на прочность
..pdfРассмотрим, как реализуется прочность в конструкции, где присутствует не одно волокно, а их система — пучок волокон. Каждое волокно в пучке имеет свои дефекты. У одного волокна они больше, у другого — меньше. Поставим вопрос о том, какую нагрузку выдержит пучок. На простом примере покажем, что прочность пучка волокон зависит не только от средней прочнос ти волокон, но и от параметра вариации прочности волокон, т. е. от разброса прочности волокон.
Возьмем 10 волокон. Пусть первое волокно может выдержать нагрузку 1 единицу (безразмерная величина) силы, второе — 2,...
десятое — 10 единиц силы (рис. 1.10). Средняя прочность воло
кон будет (1 + |
10)/2 = (9 + 2)/2 = |
= (5 + 6)/2 = 5,5 единиц |
силы. Волокон |
10, но очевидно ли, что разрушающая нагрузка |
будет равна 55 единиц силы? Это ошибочный результат. В этом примере рассуждать нужно с учетом механизма разрушения. Рас смотрим этот путь рассуждения.
Рис. 1.10. К определению прочности пучка волокон
Задаем на пучок нагрузку 10 единиц силы. Имеем 10 волокон, на каждое волокно будет приходиться 1 единица силы. В этом случае первое волокно порвется. Остается 9 волокон.
Задаем на пучок нагрузку 18 единиц силы, в пучке 9 волокон, на каждое волокно приходится 2 единицы силы, и второе волокно порвется, останется 8 волокон. Задаем на пучок нагрузку 24 еди ницы силы, волокон 8, на каждое приходится по 3 единицы силы, тогда порвется третье волокно и останется 7 волокон. При на грузке 28 единиц силы на 7 волокон порвется четвертое волокно.
При нагрузке 30 единиц силы разорвется пятое волокно, а за ним и все остальные. Этот процесс последовательного разрушения условно показан на рис. 1.11, где я. соответствует числу разор ванных волокон.
Возьмем другой пучок. Пусть каждое из 5 первых волокон может выдержать по 5 единиц силы, а остальные 5 волокон — по 6 единиц силы. Средняя прочность волокна останется той же самой — 5,5. Однако и такой пучок не выдержит нагрузку 55 единиц силы. В самом деле, при нагрузке 50 единиц силы разру шатся первые 5 волокон. Оставшиеся 5 волокон не смогут вы держать нагрузку 50 единиц силы (так как 5 х 6 < 50) и также разрушатся. Итак, рассматриваемый пучок выдержит 50 единиц силы. Пучок вьщержит 55 единиц силы только в том случае, если средняя прочность волокна равна 5,5 и прочность каждого во локна равна средней прочности (т. е. 5,5 единиц силы).
Из рассмотренных простых примеров можно сделать три важ ных вывода. Во-первых, прочность пучка волокон зависит не только от средней прочности волокон, но и от величины разбро са прочностных характеристик отдельных волокон, т. е. от каче ства, технологии, культуры производства. Во-вторых, разруше ние первых волокон в пучке может не приводить к разрушению всего пучка. В-третьих, слабые прослойки между волокнами обес печивают независимость разрушения волокон. Если бы имелась идеальная адгезионная прочность прослоек (например, для стек ловолокон — стеклянная матрица), то трещина, не встречая со противления, распространялась бы от первого разрушенного во локна по всем остальным.
Рассмотрим типовую картину разрушения однонаправленно го слоя КМ (ОКМ) с полимерной хрупкой матрицей при растя-
жении. Пусть в матрице образовалась поперечная трещина. Она начала распространяться поперек ОКМ (рис. 1.12) и приблизи лась к волокну. Если адгезионная прочность волокна и матрицы большая, то трещина не пойдет вдоль волокна, а окружит его. Трещина тормозится перед волокном, как перед преградой. Кон центрация напряжений в кончике трещины уменьшится. Нужно увеличить напряжения, чтобы трещину продвинуть дальше в мат рицу и, наконец, в волокно (рис. 1.12, а).
Если адгезионная прочность мала, то трещина образуется на поверхности раздела, пойдет вдоль волокна (рис. 1.12, б) и будет искать слабое место в волокне. В этом месте трещина окружает волокно, волокно вытягивается из матрицы, образуется мостик из волокна (рис. 1.12, в), и волокно рвется.
Таким образом, можно установить, что при разрушении ОКМ энергия расходуется на:
1)пластическое деформирование матрицы;
2)образование новых поверхностей в матрице;
3)разрушение волокон;
4)отслаивание матрицы от волокон;
5)вытягивание волокон из матрицы;
6)упругую энергию деформирования волокна.
Сумма этих энергетических затрат обеспечивает большую ра боту разрушения, что дает хорошую грещиностойкость КМ. На пример, работа разрушения стекла примерно равна 10 дж/м2;
Рис. 1.12. Схемы разрушения ОКМ
смолы — 102дж/м2; стеклопластика — 105 дж/м2, что примерно в два раза больше, чем у хороших сталей и титановых сплавов.
Итак, мы отметили сильные положительные стороны ОКМ. Теперь поговорим о слабых их сторонах. В качестве основных недостатков ОКМ следует отметить низкую прочность в направ лении поперек волокон, а также низкую прочность на сдвиг в плоскости слоя.
При проектировании силовых конструкций необходимо уме ло управлять структурой КМ и проектировать материал под заданную систему нагрузок. Проиллюстрируем это на простом примере. Возьмем тонкостенный стержень кругового сечения (трубку). При нагружении трубки осевой растягивающей си лой Р (рис. 1.13, а) очевидно, что рационально в отношении минимальной массы армировать трубку волокнами, ориентиро ванными вдоль продольной оси.
При нагружении трубки внутренним давлением р (рис. 1.13, б) рационально располагать волокна в окружном направлении (коль цевая намотка). При закручивании трубки крутящим моментом Мкр (рис. 1.13, в) рационально применять спиральную намотку с
углами укладки волокон ±45* |
В этом случае волокна с укладкой |
|
+45° будут растянуты, а волокна с укладкой —45* сжаты. |
||
а |
б |
в |
|
Р |
|
(р= 0°
Рис. 1.13. Варианты нагружения тонкостенного стержня кругово го сечения:
а —осевое растяжение; б— внутреннее давление; в — кручение
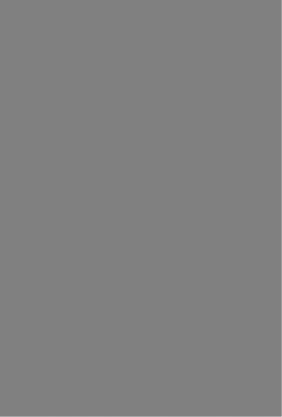
маций е2 в КМ связан с трешинообразованием в матрице). При достижении Щ происходит разрушение ОКМ. В случае сдвига ОКМ в плоскости слоя деформирование развивается линейно упруго вплоть до достижения предела прочности т,2. Дальнейшее деформирование происходит при постоянных напряжениях сдвига и также связано с трешинообразованием в матрице.
Специфика расчета многослойных конструкций из КМ зак лючается в следующем. Зная жесткостные характеристики во локна и матрицы, определяются те же свойства отдельного слоя, т. е. жесткости на растяжение вдоль волокон, поперек волокон и на сдвиг (если известны паспортные характеристики ОКМ, то лучше в расчете использовать их). Поскольку слой может ле жать под некоторым углом к осям системы координат, связан ной с конструкцией, жесткостные характеристики нужно пере считать, ориентируясь на систему координат конструкции, т. е. сделать «разворот». После обработки одного слоя переходят к другому и суммируют жесткости. При решении задачи статики определяют деформации в осях конструкции, далее «разворачи вают» эти деформации в системы координат слоев и анализиру ют, что происходит в каждом слое. Если решение задачи статики проводят с учетом трешинообразования, то нагрузку приклады вают частями (порциями) и на каждом этапе нагружения кор ректируют жесткостные характеристики слоев, учитывая трещинообразование.
Кроме решения задач статики, при проектировании конст рукций из КМ решают также задачи динамики, когда внешние силы переменны по времени, или определяют собственные час тоты конструкции. При проектировании тонкостенных элемен тов, работающих на сжатие или сдвиг, приходится решать задачи устойчивости.
Однако, хотя вопросы расчета играют важную роль, кроме них в процессе конструирования приходится решать много дру гих задач. В общих чертах дать определение конструированию можно следующим образом. Конструирование — это важнейший этап в разработке и создании изделий из КМ, в процессе которо го определяются конструктивные параметры, обеспечивающие выполнение эксплуатационных и технологических требований. В качестве основной особенности конструкций из КМ следует отметить то, что совместно с конструированием элемента осуще ствляется проектирование материала, и уже на этих этапах необ ходимо думать о методах изготовления. Современные методы
изготовления изделий из КМ достаточно технологичны. Учет специфики методов изготовления и сборки изделий из КМ мо жет обеспечить меньшую трудоемкость по сравнению с трудоем костью изготовления аналогов из изотропных материалов.
Процесс конструирования — сложный итерационный про цесс. Условно основные этапы конструирования показаны на схеме, изображенной на рис. 1.15.
Все этапы взаимосвязаны и при необходимости в процессе конструирования возможны корректировка, уточнение или до полнительная доработка на любом из них. Дадим краткие ком ментарии к основным этапам конструирования.
Впроцессах сборки, транспортировки, хранения, испытания
иэксплуатации изделия на него действуют различные комбина ции внешних воздействий. В передовых отраслях техники (хими ческом и криогенном машиностроении, судостроении, автомобиль ной промышленности, строительстве и др.) в проектах характеры величины нагрузок, как правило, регламентированы и определя ются отраслевыми нормами прочности. Эти нормы основаны на опыте производства и эксплуатации конструкций данного типа,
атакже на экспериментальных и теоретических исследованиях. Такие системы нагрузок называют типовыми расчетными случа ями нагружения.
Совершенство конструкции (технологичность, материалоем
кость и др.) во многом зависит от правильного выбора силовой схемы. Она формируется набором конструктивных элементов,
---------- ' 1 ' -------- |
--------2 --------- |
------ 3 ------ |
Анализ режимов |
Выбор |
Выбор |
эксплуатации |
силовой схемы |
< -> материалов |
и нагрузок |
|
|
------------------4 ----------------- |
=— | |
------ 5 ------ |
Определение основных |
|
Расчеты на |
конструктивных параметров |
прочность |
|
______________ ГТ\------- |
* -------- |
|
Конструкторско-технологическая |
|
|
отработка |
|
|
Рис. 1.15. Основные этапы конструирования
обеспечивающих прочность и геометрическую неизменяемость объекта под действием внешних нагрузок.
Универсальных рекомендаций по выбору силовых схем не существует. На практике приходится анализировать различные конструктивные варианты. Из общих соображений относитель но рациональных силовых схем можно отметить следующие.
Рациональной силовой схемой при статических нагрузках является такая, в которой действующие силы замыкаются на бо лее коротком участке (рис. 1.16). Как правило, конструктивное решение силовой схемы, в которой больше элементов работают на растяжение, лучше схемы, в которой больше сжатых элемен тов, так как сжатые элементы могут терять устойчивость, а на пряжения потери устойчивости меньше предела прочности мате риала на сжатие.
з — > Щ ,
Рис. 1.16. Передача силы:
а — кратчайшим путем, стержень работает на растяжение; б — стержень работает на растяжение и изгиб; в — наличие эксцентриситета е и сочленении стержней прииоднт к допол нительному изгибу
Однако если предел прочности материала на растяжение на много меньше, чем предел прочности на сжатие (например, бе тон, кирпичная кладка), то ситуация будет другой. На рис. 1.17 показаны два варианта постановки раскосов в ферме.
В варианте а длинные стержни-раскосы работают на растя жение, а в варианте б — на сжатие, поэтому конструкция вариан та а будет обладать меньшей массой, так как плошадь попереч ного сечения раскоса будет меньше, чем в варианте б.
Рис. 1.17. Варианты постановки раскосов:
а — раскосы растянуты; б — раскосы сжаты
Весьма ответственным этапом в конструировании является выбор материалов. Здесь необходимо сформулировать требова ния к механическим, теплофизическим, химическим и др. харак теристикам КМ и предусмотреть их совместимость. Выбор ис ходных материалов, включая и тип армирующих элементов (нить, жгут, ткань), влияет на параметры конструкции, технологию про цесса, на массу и стоимость изделия, его долговечность.
Непосредственный этап определения основных конструктив ных параметров взаимосвязан с расчетами, которые прогнозиру ют поведение конструкции в процессе эксплуатации. Расчетные схемы определяются силовой схемой, расчетными случаями на гружения и идеализацией конструкции (ее представлением в виде набора стержней, пластин, оболочек). Основные конструктив ные параметры (структура КМ) определяются на этапе проекти ровочного расчета с использованием приближенных методов по одной или нескольким расчетным схемам.
Расчеты проводятся на прочность, жесткость, устойчивость, колебания, температурные воздействия и др. Расчетные нагрузки задаются как Рр = Р3 ■/ где Рр — расчетная разрушающая нагруз ка; Р3 — эксплуатационная нагрузка; / — коэффициент безопас ности ( / > 1,0). Следует отметить, что для конструкций из КМ коэффициентом / нужно учитывать не только возможные отсут ствия данных о точных значениях эксплуатационных нагрузок, погрешности расчетных схем, но и разброс механических харак теристик КМ. Другой особенностью расчетов конструкций из КМ является назначение допускаемых напряжений в материале. Если ориентироваться на напряжения в матрице, то уровень реализа ции материала будет низким. Назначать допускаемые напряже ния по разрушающим напряжениям в волокнах опасно, так как механизм поведения КМ с разрушенным связующим изучен пока еще недостаточно полно. В практике проектировочных расчетов допускаемые напряжения [ст] для ОКМ часто принимают равны ми 2/3 о„ где с?! — предел прочности ОКМ вдоль направления армирования.
Определение рациональных конструктивных параметров изде лия формулируется как задача нелинейного программирования: поиск экстремума целевой функции осуществляется при задан ных ограничениях в виде равенств и (или) неравенств. В качестве целевой функции выступает, как правило, стоимость изделия. Ограничения формулируются условиями прочности, жесткости, устойчивости, технологичности и др.
Проиллюстрировать такую формулировку задачи о выборе ра циональных параметров можно на следующем простом примере.
Пример 1.1
►Для трехслойной панели, нагруженной сжимающими рас пределенными силами (рис. 1.18) требуется определить рацио нальные значения толщины несущего слоя И и заполнителя Н. Заданными считаются: / — длина панели; д — распределенная погонная сила; Е — модуль упругости несущего слоя; Е3 — мо дуль упругости слоя заполнителя; О — модуль поперечного сдви га для заполнителя; [о] — допускаемое напряжение для мате риала несущего слоя; к «: Я; / » 1; р, <; — удельные массы материалов несущего слоя и заполнителя. В качестве целевой функции примем погонную массу панели. Заполнитель будем считать легким.
Рис. 1.18. Расчетная схема трехслойной панели
Сформулируем ограничения.
I. Ограничение по прочности несущего слоя (рис. 1.19)
9 <[а]-2А;
или
г -| |
Рис. 1.19. Определение огра- |
^ М |
ничения по прочности |