
книги / Функционально-стоимостный анализ (кейсы - примеры, задания, тесты)
..pdf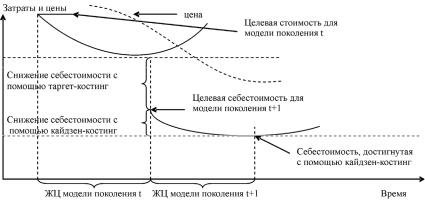
ния и разработки, а затем – уже на стадии производства – будет постепенно снижаться в соответствии стак называемой «кайдзен-задачей». Жизненный цикл модели поколения t + 1 закончится тогда, когда будет достигнута точка минимальной себестоимости, после которой себестоимость может только повышаться. Далее весь процесс повторится, толькоужедляследующеймоделипоколенияt + 2 ит.д.
Наличие небольшой разницы (в пределах 3–5 %)между расчетной (после завершения проектирования) и целевой себестоимостью продукта не является препятствием для принятия решения о производстве. Возникшая разница является отправной точкой для определения «кайдзен-задачи», т.е. целевого снижения отдельных статей затрат и себестоимости в целом в процессе производства.
Для наглядности рассмотрим влияние систем «таргет-кос- тинг» и «кайдзен-костинг» на кривые затрат и цен (рис. 7).
«Кайдзен-задача» может быть общей и подразделяться на конкретные задачи как для отдельных заводов, так и для более мелких подразделений (цехов, сборочных линий и т.д.). Сотрудники японских компаний стремятся, чтобы достигнутый вследствие снижения себестоимости результат был равен или превышал обозначенные в «кайдзен-задаче» целевые показатели, что является основанием для дополнительного и существенного вознаграждения (рис. 8).
Рис. 7. Влияние систем «таргет-костинг» и «кайдзен-костинг» на кривые затрат и цен
91
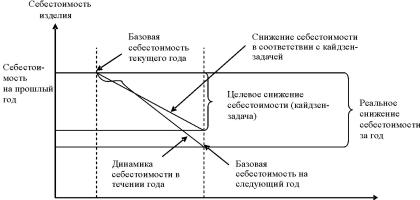
Рис. 8. Механизм снижения себестоимости в соответствии с кайдзен-задачей
Одним из наиболее ярких примеров работы системы «кайдзен» (непрерывного усовершенствования) является опыт компании Toyota. Система управления затратами в компании Toyota, изображенная на рис. 9, позволяет организованно и целенаправленно осуществлять политику снижения себестоимости, рационально инвестировать денежные средства в новые продукты, координировать действия множества людей, вовлеченных в производственный процесс, и совместными действиями добиваться достижения поставленных целей.
Все члены большой команды Toyota активно участвуют в выдвижении идей и предложений, позволяющих улучшить производственный процесс. Они также постоянно учатся быть внимательными к непродуктивным потерям, выявляют те затраты материалов, усилий и времени, которые не приносят пользы, и оперативно устраняют их. В последнее время члены команды Toyota были ориентированы на выдвижение полезных предложений в плане снижения вредного воздействия автомобилей на окружающую среду. Каждый год тысячи членов компании вносят реальный вклад в улучшение качества и экономию средств, делают производство простым, безопасным и чистым.
92
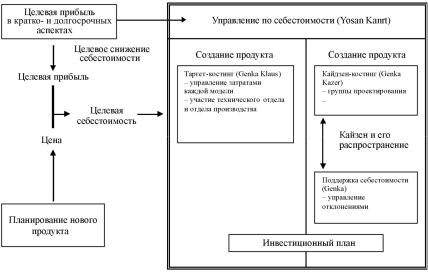
Рис. 9. Система управления затратами в компании Toyota
Например, известно, что в Toyota двигатели всегда строго проверяются, а охладители, используемые после испытания образцов, всегда заменяются – после первого же использования. Рабочими было предложено вставлять в охладительную систему специальный фильтр, предохраняющий от возможного засорения. Теперь Toyota экономит несколько тонн хладагента ежегодно, многократно его используя.
Другой пример, касающийся приближения производственных линий к потребностям человека. В период 1987–1991 гг. в японской автомобильной промышленности начали широко употреблять понятие «дружественная сборочная линия» (human friendly assembly line) и активно внедрять «серебряный конвейер», на котором могли работать даже пожилые рабочие, что привело к значительному росту уровня автоматизации заводов.
В это же время компания Toyota проводила радикальную реорганизацию систем управления производством и людскими ресурсами. Программа реконструкции коснулась многих заводов и сбо-
93
рочных линий. Например, сборочная линия на заводе Toyota Kyushu в результате реформ была разделена на 11 функциональных сегментов. Было решено ввести пятиминутные промежутки (буферы) между двумя сегментами, чтобы в случае поломки в пределах одного сегмента остальные продолжали работать. Оказалось, что производительность линии не уменьшилась, так как потери времени в случае поломки почти всегда «поглощались» буфером, а вся линия уже не останавливалась, как это было раньше. Теперь же рабочие трудились с гораздо меньшим напряжением и намного реже оставались на своем рабочем месте сверхурочно (до введения новой структуры сборочной линии это было обычной практикой). Таким образом, сборочная линия начинала приобретать характер «дружественной», что позволило успешно решать «кайдзен-задачи», связанные со снижением переменных затрат (сокращение почасовой оплаты за сверхурочный труд, которая значительно выше обычной).
Постановка и выполнение кайдзен-задачи – длительный процесс, тесно связанный с процессом бизнес-планирования в корпорации и ее подразделениях. Например, производители запасных частей к автомобилям каждый год изучают и пересматривают среднесрочные планы (3–5 лет), бизнес-планы и планы прибыли на следующий год. Эта процедура выполняется плановым отделом, которому активно помогает отдел управления затратами. В декабре, после получения годовых планов производства от своего клиента (автомобильной компании), производители запчастей начинают формировать свой собственный годовой бюджет. Довольно часто планы производства требуют тщательного изучения и неоднократно пересматриваются. Когда окончательный вариант плана производства клиента согласован и утвержден, отдел продаж компаниипроизводителя запчастей разрабатывает план производства для своей фирмы, в соответствии с которым далее каждый отдел калькулирует собственные плановые затраты. Например, если технический отдел собирается в следующем году приобрести новое оборудование, он должен оценить затраты, связанные с такой покупкой, в том числе затраты на амортизацию оборудования, и отобразить их в ра-
94
бочей калькуляции. Калькуляции, составленные всеми отделами компании, должны быть завершены за два-три месяца до начала следующего отчетного года, который для японских компаний начинается обычно 1 апреля. Далее отделом управления затратами оцениваются общие плановые затраты и составляется плановый отчет о прибылях и убытках. Показатели этого отчета сравниваются с показателями целевой прибыли, после чего определяется разница между этими показателями, которая и становится основой кайдзензадачи на следующий год.
Значения целевого снижения затрат определяются по целому списку статей затрат (в основном переменных), таких как прямые материальные затраты, прямые затраты на оплату труда (почасовая оплата) и т.д. Постоянные же затраты группируются отдельно по каждому подразделению фирмы, после чего на основании показателей кайдзен-задачи и бюджетов постоянных затрат составляется годовой бюджет. С начала отчетной даты в японских компаниях вступает в силу новый бюджет и включается механизм деятельности «кайдзен» я на уровне групп сотрудников (кружков качества, проектных групп) и отдельных рабочих, вносящих свою лепту в улучшение бизнес-процессов. На протяжении отчетного года сотрудниками отдела управления затратами ежемесячно проводится проверка того, достигнуты ли промежуточные цели снижения переменных затрат, указанные в кайдзен-задаче, и выполняются ли бюджеты постоянных затрат:
Однако необходимо заметить, что ни таргет-костинг, ни кайдзен-костинг никоим образом с западными методами калькулирования затрат не пересекаются. Например, «стандарт-костинг» (нормативный учет) используется в основном для регулирования затрат и оценки результативности, а таргет-костинг и кайдзенкостинг являются инструментами снижения затрат, и их относят скорее к области стратегического управления затратами, чем к сфере производственного учета.
Во многих странах очень подробно разрабатываются практические подходы к реализации идей постоянного улучшения. Кон-
95
цепция постоянного улучшения декларирована в МС ИСО серии 9000:200, где указываются наиболее важные положения по ее реализации. В МС ИСО 9004:2000 наряду с тем, что процесс постоянного улучшения должен использоваться как инструмент для улучшения внутренней эффективности и результативности, а также для удовлетворения потребителей и заинтересованных сторон, в приложении описана методология постоянного улучшения. В соответствии с этой методологией существует два фундаментальных подхода к действиям по улучшению:
а) крупные «прорывные» проекты в улучшении качества, так называемыеKayrio, ведущиекпересмотру существующихпроцессов;
б) пошаговое постоянное улучшение, проводимое обычными рабочими группами в пределах существующих процессов.
Выделяют также десять ключевых критериев, которые являются важным фундаментом, необходимым для создания и поддержания постоянного улучшения:
•конкретные обязательства высшего руководства и его активное участие в деятельности организации, в том числе в области постоянного улучшения;
•эффективное руководство и конкретные обязательства, демонстрируемые руководителями на всех уровнях;
•нацеленность на потребности заинтересованных сторон;
•объединение деятельности по постоянному улучшению
встратегические цели во всей организации, за ее пределами и на всех уровнях;
•установление культуры для постоянного улучшения, способствующей новаторству и творчеству;
•нацеленность на процессы, особенно на процессы, критические для качества;
•нацеленность на работу с персоналом по четырем направлениям: участие персонала в работе по постоянному улучшению, делегирование полномочий, групповая работа и создание групп по постоянному улучшению, обучение и повышение квалификации;
96
•стандартизация достижений в рамках документированной системы менеджмента качества;
•создание системы измерений и обратной связи;
•извлечение уроков из результата постоянного улучшения.
Структурирование функций качества (СФК)
Методическое обеспечение ФСА включает набор разнообраз-
ных методов, позволяющих анализировать функции, выявлять зоны сосредоточения затрат, ставить и решать задачи повышения потребительской стоимости, т.е. конкурентоспособности. В большинстве рассматриваемых методик по ФСА действует принцип соответствия степени значимости затратам и уровню качества их реализации, т.е. определяются значимость каждой функции объекта в сравнении с другими функциями, фактические затраты на осуществление этих функций и уровень качества их выполнения. Затем происходит сопоставление значимости функций с затратами на их реализацию и уровнем качества их осуществления. Этот прием позволяет дать экономическую оценку существующему и предлагаемым вариантам анализируемого объекта, выявить «дефектные зоны».
Метод структурирования (развертывания) функций качества направлен на решение той же задачи, что и ФСА, – повышение конкурентоспособности. Главная идея СФК (РФК) – перевод оценок качества продукций с позиции потребителя в ее технические характеристики. Но сделать это можно, используя методы формулирования функций, разработанные в ФСА.
Рассмотрим, например, такую понятную всем продукцию, как стиральный порошок. С позиции ФСА главная функция стирального порошка – удалять загрязнения с белья. С качеством реализации этой функции связаны, например, такие характеристики, как диапазон тканей, для которых может быть использован данный порошок, время удаления загрязнения (при заданном режиме стирки), удельный расход порошка и т.д. Кроме того, в ФСА предусмотрено формулирование вредных функций. Так, стиральный порошок может разрушать ткань, изменять ее цвет, разрушать детали стиральной машины, загрязнять окружающую среду, оказывать при контакте вредное воздействие на
97
человека. Для этих функций также можно указать конкретные техническиехарактеристики, влияющиенаихвыполнение.
Технические характеристики могут изменяться в широких пределах. Соответственно будет изменяться степень реализации перечисленных функций, а значит, и качество продукции.
Что желает потребитель, выбирая стиральный порошок? Естественно, чтобы стиральный порошок отстирывал любое белье, возможно лучше, быстрее и при минимальном расходе, не портил белье, был безвреден во всех отношениях и стоил как можно меньше. Добиться наилучших характеристик, т.е. идеального качества, невозможно. Тем не менее для того чтобы потребитель предпочел продукцию вашей компании продукции конкурентов, необходимо ее постоянно совершенствовать. Следует понять, какие характеристики стирального порошка требуется изменить и на какую величину, а также в какую цену необходимо при этом уложиться.
Для решения таких задач необходимо установить зависимость между уровнем качества продукции и конкурентоспособной ценой
иполучить крайне важную информацию:
–какие на данном этапе характеристики продукции наиболее выгодно совершенствовать;
–насколько необходимо изменить характеристики, чтобы получить конкурентное преимущество;
–какая при этом будет конкурентоспособная цена продукции.
Получив эту информацию, можно поставить конкретные задачи перед конкретными специалистами. Правильно же поставленные задачи во многом предопределяют успех дела.
Итак, наиболее перспективной для создания новых инновационных продуктов является стратегия, основанная на методе струк-
турирования функции качества (Function Quality DepioyBent),ши-
роко используемая в Японии, а в последнее время и в США. Этот метод позволяет понять механизм реализации самой перспективной и конкурентоспособной на мировом рынке маркетинговой стратегии – повышения качества продукции при снижении ее цены. Этот метод позволяет максимально точно и полно довести «голос потре-
98
бителя» до разработчиков новой продукции, резко уменьшить сроки разработки и количество доработок на стадии производства и риск ее невостребованности. В этом убеждает анализ деятельности японских и американских автомобильных корпораций – Honda выпускает новый автомобиль каждые два года, Toyota –каждые три, а Ford – каждые пять лет.
Основная задача любой компании – поставить на рынок раньше других более качественный и дешевый товар. Эта маркетинговая стратегия реализуется в Японии через систему СФК. При этом стратегия маркетинга или «точки продаж» сохраняются в процессе движения изделия от маркетинга к разработке и далее к производству
иреализации, системно выявляя и ставя под контроль все важные факторы, необходимые для получения желаемого результата.
Многие компании США в последние годы разрабатывали свои философии качества. Философию компании нельзя скопировать. Ее необходимо разработать таким образом, чтобы она отражала культуру данной компании и долговременные цели управления. Если она разработана именно с этих позиций, ее можно структурировать по вертикали и по горизонтали, охватывая всю компанию, изменяя мышлениевсехсотрудниковчерезполитикууправленияипрактику работы.
Подход к качеству в компаниях Японии и США различен. В японских компаниях «голос покупателя» управляет всеми видами деятельности, в то время как в компаниях США превалирует «голос исполнителя или инженера». Более того, по сравнению с компаниями США, японские компании концентрируются в основном на том, что больше всего нравится потребителю. Компании США, напротив, уделяют больше внимания определению того, что больше всего не нравится потребителю. Поэтому японцы больше сил вкладывают
впланирование качества на начальном этапе разработки изделия,
вто время как компании США больше внимания уделяют решению проблем по мере их появления на последующих этапах разработки
ипроизводства.
Метод СФК впервые стал использоваться на судоверфи вг. Кобэ, принадлежащей машиностроительной корпорации Mitsubisi Ltd в1972 г., чтозатемполучилоначалоегораспространениявЯпонии.
99
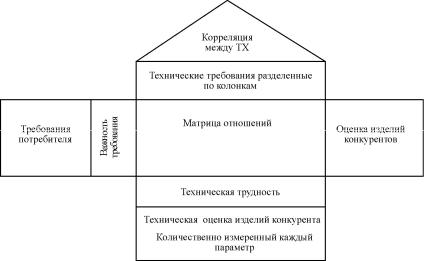
Метод СФК использует графический подход и связан с построением так называемого «дома качества». Проведение СФК включает несколько этапов (рис. 10):
1.Определение требований потребителей (ТП) – «голос клиента», при этом клиент не всегда четко может сформулировать свои требования. Обычно он говорит: «Быстрее, меньше, легче, другой цвет».
2.Расположение по приоритетам требований потребителей (с помощью статистического анализа требований клиентов).
3.Перевод требований потребителей в технические требования, т.е. в такие требования, которые можно измерять.
4.Построение матрицы отношений: цель матрицы состоит
втом, чтобы связать технические характеристики (ТХ) и требования потребителей.
5.Анализ изделий конкурента.
6.Оценка относительной технической трудности для достижения каждой технической характеристики.
Рис. 10. Общая схема представления всех стадий СФК
100