
книги / Функционально-стоимостный анализ (кейсы - примеры, задания, тесты)
..pdfбыть «развернуты», т.е. систематизированным образом преобразованы в количественные требования, и контролироваться на всех этапах проекта. Напротив, те характеристики, которые не критичны для удовлетворения потребительских нужд и не дают существенных «точек продаж», для которых не трудно достичь целевых значений, – не включаются в процесс структурирования.
Когда плановая матрица потребительских требований заполнена, переходят к матрице структурирования характеристик конечного продукта, т.е. ко второму ключевому документу СФК. В этой матрице контролируемые характеристики проектируемого продукта переносят нас с верхнего уровня, характеризующего изделие (например, автомобиль) в целом, на уровень функциональных подсистем, узлов и составляющих их компонентов (рис. 19).
На этой фазе процесса структурирования как потребительские требования, так и контролируемые характеристики конечного продукта рассматриваются более подробно. Вначале определяются характеристики подсистем и составляющих их узлов (компонентов), оказывающие влияние на контролируемые характеристики конечного продукта. Затем заполняется матрица, которая наглядно показывает степень взаимосвязи характеристик подсистем и компонентов и изделия в целом. Это позволяет выделить наиболее значимые, «критические» параметры и характеристики подсистем и узлов. Такие «критические» параметры и характеристики подсистем предстоит «структурировать» на следующих этапах. Результатом такого структурирования является создание условий для обеспечения таких значений характеристик, подсистем и компонентов, которые необходимы для достижения требуемых свойств изделия в целом.
Матрица структурирования компонентов (рис. 20) расширяет список компонентов, влияющих на характеристики подсистем и изделия в целом, а также перечень параметров указанных компонентов. Значения этих параметров определяют способность достижения целевых характеристик готового изделия. Критические параметры компонентов затем «развертываются» с помощью плана процесса – третьего важного документа системы СФК.
111
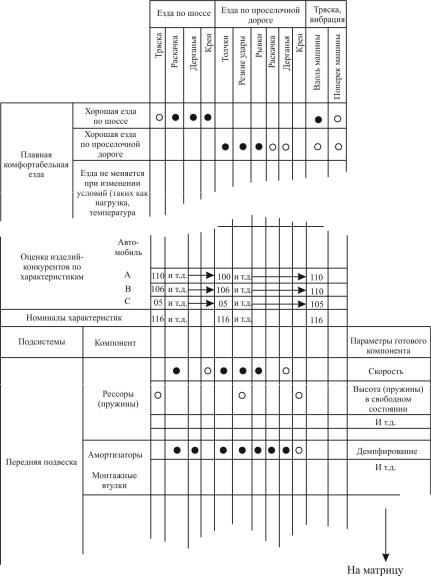
Рис. 19. Матрица структурирования требований к изделию в целом, требований к его функциональныи подсистемам
112
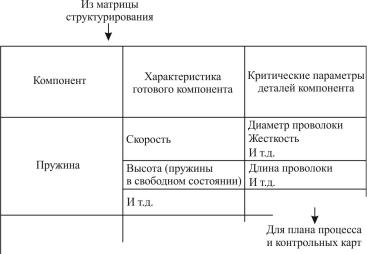
Рис. 20. Матрица структурирования компонентов функциональных подсистем
План процесса устанавливает связи между операциями процесса, используемого для производства компонента, параметрами компонента и составляющими его деталями. Для обозначения силы связи используются те же символы, что и в предшествующих матрицах.
На этой фазе структурирования производится выделение операций в составе процесса производства, которые в решающей степени определяют значения важных параметров готового компонента. Если важная характеристика критического компонента изделия (например, диаметр пружины, прочность, качество поверхности и т.п.) формируется или существенно изменяется в процессе выполнения данной операции, она начинает рассматриваться как подлежащая контролю. Знания и опыт позволяют определить те параметры, которые необходимо контролировать на данной операции для того, чтобы обеспечить достижение необходимых свойств готового компонента, т.е. определяются «контрольные точки».
Перечень «контрольных точек» и контролируемых параметров составляет исходную информацию для разработки стратегии
113
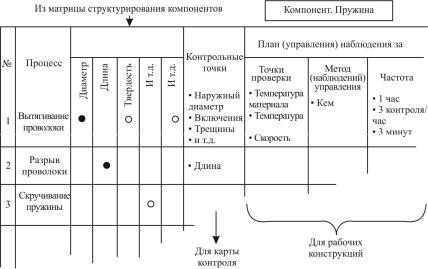
и плана обеспечения качества изделий (рис. 21). Они задают подход
кконцентрации внимания и ресурсов на формировании и контроле таких параметров компонентов и процессов их производства, которые определяют способность изделия удовлетворять потребительские требования.
Рис. 21. План обеспечения качества в процессе производства
Чтобы добиться целевых значений параметров компонентов в процессе проведения технологической операции процесса (например, температура, давление и пр.), эти параметры фиксируются отдельно как «точки проверки». Информация о контрольных точках и точках проверки является исходной для разработки карты контроля качества.
Карта контроля качества (рис. 22) включает в себя: блок – схему процесса, точки контроля, а также характеристики используемых методов контроля (объем и частоту выборок,, методы анализа результатов и выработки решений по управлению процессом) для каждой из перечисленной точек контроля.
114
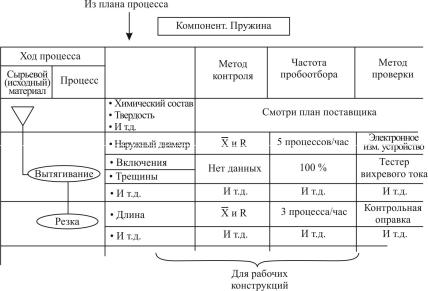
Рис. 22. Карта контроля качества процесса производства компонента
Итак, в результате структурирования были определены способы контроля ключевых деталей и узлов, а также точки и методы контроля и мониторинга наиболее важных параметров компонентов и процессов их создания. Выделение критических контролируемых параметров имеет принципиальное значение для того, чтобы обеспечить характеристики компонентов и узлов, наиболее тесно связанных
судовлетворением потребительских предпочтений.
Всвою очередь информация, получаемая на данной стадии процесса структурирования, используется с целью разработки рабочих инструкций для исполнителей технологических и контрольных операций. Рабочие инструкции по технологическим и контрольным операциям – четвертый и последний документ по СФК. Он определяет требования к исполнителям, вытекающие из выделенных ранее контрольных точек и точек проверки, зафиксированных в плане процессов и карте контроля качества. В инструкциях по технологическим операциям необходимо предусмотреть варианты действий
115
для возможных ситуаций, возникающих в процессе производства. Этот документ четко диктует оператору способы реализации операции, обеспечивающие достижение требуемого уровня качества. Так, например, для оператора на сборочной линии в таких инструкциях должны быть указаны:
–требования, предъявляемые к используемым деталям;
–инструменты, используемые в процессе операции;
–контроль параметров компонентов и параметров операции. В технологической и контрольной карте должно быть указа-
но, как выполнение (невыполнение) этих требований может повлиять на контролируемые параметры компонента и конечного продукта. Таким образом, каждый оператор осведомлен о связи между выполняемой им работой и степенью удовлетворенности потребителя продукцией компании.
Система СФК применялась фирмой Toyota с 1977 г., причем до этого четыре года было затрачено на обучение и подготовку персонала. В период времени с января 1977 г. по апрель 1984 г. в отделении производства кузовов освоено производство четырех типов автомобилей. Принимая 1977 г. за точку отсчета, компания сообщила о сокращении на 20 % стартовых затрат на внедрение нового типа автомобиля, в октябре 1979 г.; к октябрю 1982 г. – на 38 % и суммарное сокращение затрат на 61% к апрелю 1984 г. За этот же период длительность цикла конструкторской разработки изделия – время вывода продукта на рынок – было сокращено на 1/3, при соответствующем повышении качества благодаря сокращению числа конструкторских изменений.
В настоящее время все поставщики компании Toyota применяют СФК. Компания «Аисин Варнер», которая обеспечивает поставку 98 %коробок передач для компании Toyota, сообщает, что СФК помогла сократить количество конструкторских изменений в период технологической разработки изделия на половину. Общий эффект СФК заключается в сокращении времени разработки и общей длительности цикла разработки и освоения производства наполовину. Тем самым достигается сокращение длительности времени выхода на рынок новых марок автомобилей.
116
Внедрение СФК требует большого объема работ на ранних этапах планирования. СФК также усложняет внесение изменений после того, как проект принят к разработке, потому что в этом случае придется изменять все элементы системы, внутренне связанные между собой. Система может также оказаться слишком сложной
сточки зрения администрирования: Как наладить коммуникацию между участвующими в работе подразделениями, обеспечить согласованность их решений? Кто будет следить за документами на протяжении всего цикла конструкторской разработки? Как внести изменения в документы СФК, если эти изменения инициируются во время разработки технологии и подготовки производства?
Несмотря на все эти потенциальные трудности, СФК предоставляет множество преимуществ. Эта система приводится в движение потребителем. Она позволяет установить связь между требованиями потребителей, техническими характеристиками изделия, параметрами его функциональных подсистем и их компонентов на всех этапах разработки. СФК также обеспечивает средства перевода потребительских требований в совокупность контролируемых характеристик и требований к методам реализации технологических операций. Эта система формирует непрерывный информационный поток, гарантирующий, что все элементы производственной системы подчинены потребительским требованиям.
Система СФК предполагает использование командного подхода к организации работ. Она позволяет объединить, скоординировать действия различных функциональных служб, помогает им
лучше понять требования потребителя и друг друга и совместно находить средства удовлетворения этих требований.
Пример
Вкачестве примера будем использовать прибор для изготовления ледяного чая (рис. 23). Необходимо улучшить данный прибор
спомощью СФК.
Принцип действия прибора следующий: в специальную корзинку добавляется заварка, затем в резервуар наливается холодная вода, включается машина. Вода в резервуаре нагревается с помощью технической спирали. Горячая вода просачивается через за-
117
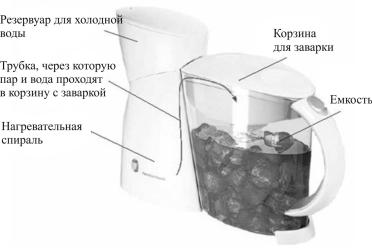
варку, и чай капает вниз в специальную емкость. Когда чай готов, добавляется сахар, лимон и лед в емкость с чаем и все смешивается.
Рис. 23. Составные элементы прибора для изготовления ледяного чая
Определяем требования клиента, важность каждого из них, технические характеристики изделия, основываясь на техническом анализе проекта. Кроме того, устанавливаем корреляцию между требованием клиента и техническими параметрами, а также отмечаем стрелками вверх положительную корреляцию, а стрелками вниз – отрицательную (рис. 24).
Примечания:
1.Корреляция между требованиями потребителей и техническими характеристиками оцениваем по шкале 9, 5, 3; 9 –высокая корреляция, 5 –средняя, 3 –слабая. Пустая ячейка означает, что корреляция является незначительной (может быть выбрана и другая шкала оценивания корреляции).
2.Стрелки помогают понять, что необходимо максимизировать для получения идеального проекта, а что нужно минимизировать.
3.Оценка относительной важности требований клиента получена из результата опроса.
118
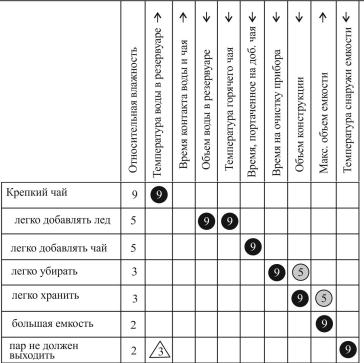
Рис. 24. Корреляция между требованиями клиента и техническими характеристиками
Теперь переходим к следующим этапам: анализ изделий конкурентов, рассмотрение возможностей изменения некоторых модулей изделия для улучшения их технических характеристик (рис. 25). Числовую оценку трудности улучшения технических характеристик должны производить инженеры, которые отвечают за проектирования данного модуля. Они должны консультироваться друг у друга, чтобы стандартизировать свои оценки.
Примечания:
1. Оценка технической трудности назначается экспертами
вотносительных числах.
2.Праваясторона«дома» показывает, чтохорошоуконкурентов.
119
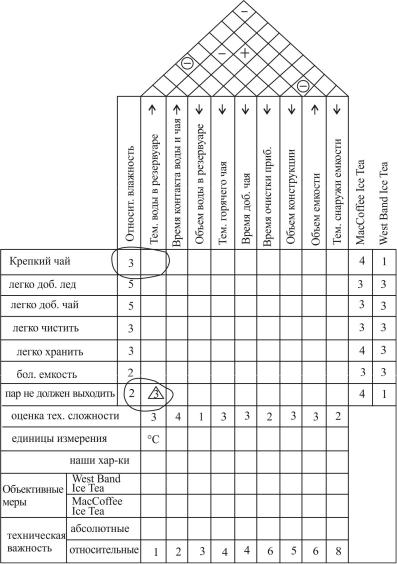
Рис. 25. Оценка технической трудности
120