
книги / Механика промышленных роботов и манипуляторов с электроприводом
..pdfВсе четыре электромеханических привода звеньев выполнены одинако во. Каждый привод содержит электродвигатель 7 типа ПЯ 250Ф, волновой редуктор 76, датчик положения 10 типа ППК-15, тахогенератор 3 типа ТГП-3 (рис. 3.12). Вращение к валу датчика от вала двигателя передается с помощью зубчато-ременной передачи; в нее входит шкив 2 (z = 28), установленный на входном валу редуктора, шкив 9 (z=45), установленный на валу датчика, и зубчатый ремень 8 (модуль 1 мм). Тахогенератор смон тирован на крышке двигателя и соединяется с ротором при помощи муфты.
Волновой редуктор выполнен следующим образом. Ведущий вал 5 сое диняется с валом двигателя при помощи шпонки 4 и другим концом опира ется на подшипник 14 на выходном валу 13. На входном валу с радиальным зазором установлен эллиптический кулачок 18 генератора волн, соединен ный с валом компенсирующей муфтой 17. Таким образом обеспечивается самоустановка генератора волн в процессе работы. На кулачке имеется гибкий подшипник 6, взаимодействующий с гибким колесом 15 (d= 80 мм, z = 205, т = 0,4 мм), находящимся в зацеплении в двух зонах с жестким колесом 7 (z = 207), неподвижно закрепленным в корпусе 12. Ведомым
является гибкое колесо 15; оно |
|
|
соединено с выходным валом |
|
|
13, который установлен в под |
|
|
шипниках 77 в корпусе 12. |
|
|
Рука манипулятора снабже |
|
|
на механизмом уравновешива |
|
|
ния статических моментов от |
|
|
веса звеньев. Уравновешивание |
|
|
производится с помощью пру |
|
|
жин, закрепленных на поворот |
|
|
ной платф орм е. Пружины |
|
|
посредством цепей и звездочек |
|
|
соединены с приводными кри |
|
|
вошипами плеча и предплечья. |
|
|
Уравновешивание моментов от 4 |
|
|
веса звеньев производится |
|
|
практически постоянной силой, |
|
|
создаваемой пружинным меха |
|
|
низмом на всем диапазоне пере |
|
|
мещения звена. Рабочее усилие |
|
|
пружины регулируется путем |
|У T * i |
|
ее предварительного поджатия |
||
из расчета уравновешивания |
||
наибольшего статического мо |
7 |
\ |
мента, создаваемого весом |
2 |
1 |
звеньев. Поджатие должно |
Рис. 3.13. Схема робота "AsealRB-ô" |
быть таким, чтобы не наблюдалось самопроизвольное движение звеньев. Электромеханический робот “AseaIRB-б" шведской фирмы по своему
строению близок к рассмотренному выше роботу ТУР-10, но отличается от него выполнением приводных модулей. Робот применяется для таких тех нологических операций, как сварка, окраска, снятие заусенцев и т.д. Он имеет антропоморфную схему, компоновка его узлов показана на рис. 3.13.
Техническая характеристика робота “AseaIRB-6” Число степеней подвижности 5 Переносные степени подвижности:
поворот платформы q\, град (град/с) 340(95) поворот плеча q2, град 80
поворот предплечья #3, град 65 Ориентирующие степени подвижности:
качание $4, град (град/с) 180(115) ротация q5, град (град/с) 360(195)
Грузоподъемность, кг 6 Точность позиционирования, мм 0,2
Тип управляющего устройства—позиционно-контурное Масса манипулятора, кг 125
Поворот руки вокруг вертикальной оси осуществляется от двигателя 1 через безлюфтовую волновую передачу 2, выходное звено которой связано с поворотной платформой 19. На платформе шарнирно закреплен мотор-ре дуктор 3 и параллелограммный механизм передачи движения к предплечью 10. Этот механизм состоит из двух кривошипов 5 и 8 и двух тяг 7, 14. Нижний кривошип с помощью шариковинтовой передачи 4 связан с выход ным валом мотор-редуктора; верхний кривошип связан с предплечьем 10.
Наклон плеча 14 обеспечивается мотор-редуктором 18, движение кото рого через шариковинтовую передачу сообщается кривошипу /б, жестко соединенному с плечом 14. Для разгрузки привода плеча предназначен дебаланс 6.
Механизмы ориентирующих степеней подвижности состоят из двух мо тор-редукторов 15, установленных соосно с плечевым шарниром системы тяг 13, 12, кривошипов 17, 9, 11, образующих параллелограммные транс ляторы (их два и они расположены по обеим сторонам плеча и предплечья). Качание кисти осуществляется непосредственно от кривошипа 11, а рота ция — от кривошипа параллельного транслятора через систему конических зубчатых колес.
Робот имеет антропоморфную схему (подъем и опускание рабочего ор гана происходит по вертикали и горизонтали) и работает в цилиндрической системе координат. Это обеспечивается за счет соответствующего управле ния двигателями плеча и предплечья; пересчет требуемых скоростей про исходит автоматически в управляющем устройстве.
Движение звеньев по всем степеням подвижности контролируется дат чиками положений. Измерительная система построена на фазоаналоговом принципе: разность фаз между сигналами датчиков и заданным сигналом преобразуется в аналоговый сигнал, управляющий сервосистемой. Управ ляющее устройство робота может работать в трех режимах: отточки к точке..
Рис. 3.14. Схема манипулятора робота 4‘Ршпа-560"
точно, от точки к точке грубо, от точки к точке линейно. При оснащении рабочего органа сенсорным устройством робот может работать в режиме поиска неориентированных предметов.
Универсальный промышленный робот РМ-01 (аналог робота “Puma560", выпускающегося с 1978 г.) предназначен для выполнения основных технологических и вспомогательных операций. Он имеет развитую кине матику, систему управления на базе микропроцессоров, хорошо приспособ лен для работы с системами технического зрения и другими средствами очувствления. Способ^управления роботом—контурно-позиционный, спо соб программирования — аналитический и обучением.
В состав робота входят манипулятор, устройство управления “Сфера36" с выносным пультом обучения. Манипулятор, построенный по антропо морфной схеме, вклю чает корпус, поворотную колонну, плечо, предплечье, кисть (рис. 3.14).
Техническая характеристика робота РМ-01 Число степеней подвижности 6
Максимальная скорость перемещения по степеням подвижности«м/с 0,5 Грузоподъемность, кг 2,5 Точность позиционирования, мм 0,1 Масса общая, кг 342 Масса манипулятора, кг 62
Кинематическая схема манипулятора представлена на рис. 3.15. Элект родвигатели приводов размещены на звеньях, это упрощает передачи и
повышает точность, но увеличивает перемещаемую массу. Двигатели—по стоянного тока, напряжение питания — 220 В, общая потребляемая мощ ность — не более 1200 Вт. Каждый двигатель снабжен датчиками положения и скорости, а также электромагнитным тормозом, служащим для фиксации положения звеньев при отключенном двигателе.
В приводах переносных степеней подвижности и q3 использованы рядовые зубчатые передачи, в приводе координат q2 — планетарный меха низм с ведущим сателлитом. Передаточные отношения ÏJ = 60, i2 = 50, z3 = =30. Движения всех переносных степеней подвижности кинематически не зависимы.
Оригинальное устройство имеет приводная система кисти. Все три дви гателя М4, М5, М б размещены на предплечье манипулятора. При работе
двигателя М4 поворачивается корпус кисти, увлекая за собой концы транс миссионных валов, соединяющих двигатели М5 и Мб с кистью. При этом оси валов образуют скрещивающиеся прямые. Для того чтобы это оказалось возможным, на трансмиссионных валах приводов имеются компенсацион ные муфты, способные легко изгибаться, но при этом передавать крутящий момент. Конструктивно компенсационная муфта представляет втулку в виде толстостенной трубы. Встенках втулки выполнены сквозные винтовые пазы, таким образом она фактически превращена в винтовую пружину с прямоугольным сечением витка. Размер сечения в радиальном направле нии превосходит размер в осевом, что обеспечивает компенсационной муф те повышенную податливость на растяжение — сжатие, а следовательно, на изгиб, и повышенную жесткость на кручение.
Конструктивные особенности манипулятора обеспечивают ему при за данной грузоподъемности высокую точность на протяжении всего периода эксплуатации. Наработка на отказ робота составляет 500 ч, средний срок службы — не менее 10 лет.
Схема манипулятора с размещением приводов на звеньях позволяет свести к минимуму длину кинематических цепей. Привод каждого звена содержит не более двух зубчатых передач, высокая точность которых и наличие механизма выборки люфтов обеспечивают высокую точность пе редачи движения в целом. Для уменьшения погрешности кинематических цепей, вызванной деформацией скручивания валов, наиболее нагружен ные детали выполняются в виде труб большого диаметра.
Монококковая конструкция узлов манипулятора, при которой корпус ные детали воспринимают основную нагрузку, обеспечивает высокую жес ткость манипулятора при минимальном весе. В поперечном сечении корпусные детали узлов манипулятора имеют форму прямоугольника. По мере удаления от шарнира площадь сечения уменьшается, что приближает звено к балке равного сопротивления. Все это обеспечивает рациональное использование несущей способности корпуса и снижение его массы.
Подшипниковые опрры всех валов максимально разнесены в пределах габаритов звеньев манипулятора, что обеспечивает повышение жесткости конструкции, уменьшение реакции в опорах и снижение влияния деформа ций и зазоров. При этом используются подшипники больших диаметров, но более легких серий, что необходимо для повышения их несущей способно сти, плавности вращения, долговечности.
Все зубчатые колеса, непосредственно связанные с перемещаемыми звеньями, имеют максимально возможные диаметры в пределах габаритов корпусов. Это позволяет уменьшить усилия в зацеплении, а следовательно, снизить деформирование зубьев и его влияние на угловое положение звена в целом.
Кроме описанных мер облегчения конструкции, в манипуляторе осуще ствлено рациональное размещение масс.Центры масс звеньев прибли-
жены к осям вращения. Для этого узлы приводных механизмов располага ются по обе стороны от шарнира, причем более массивные части и электро двигатели — на коротком плече. Таким образом, конструкция звена оказывается полностью или частично статически уравновешенной, что сни жает мощность двигателя, необходимую для преодоления статической на грузки. Для уменьшения моментов инерции массивные узлы размещаются как можно ближе к оси вращения.
В целом конструкция манипулятора весьма совершенна. Многие приня тые решения являются эталонными для большого числа роботов последних лет разработки.
3.4. Рабочие органы манипуляторов
Рабочий орган — это составная часть исполнительного устройства мани пулятора для непосредственного выполнения технологической операции и (или) вспомогательных переходов. К рабочим органам относятся сварочные клещи, окрасочный пистолет, сборочный инструмент, захватное устройст во. Расширение области применения роботов во многих случаях тормозится отсутствием соответствующих рабочих органов.
Рабочий орган находится на конце кинематической цепи и поэтому в наибольшей мере подвержен агрессивному воздействию среды. Он посто янно контактирует с окружающими предметами и более подвержен опас ности повреждения. Рабочий орган максимально должен соответствовать условиям работы. Часто он оснащается датчиками и специальными приво дами. Он связан с роботом механическими, энергетическими, информаци онными связями, а также оснащается системами подачи материалов (сварочной электродной проволоки, охлаждающих веществ, воздуха и газа, смазочного материала, жидкости для окраски и распыления) к месту рабо ты. Все это позволяет рассматривать рабочий орган как отдельную подси стему робота, от совершенства которой во многом зависит эффективность использования робота.
Рабочие органы могут быть разделены на два вида: технологические инструменты и захватные устройства. Технологические инструменты ис пользуются для выполнения роботом специальных технологических про цессов. Захватные устройства предназначены для захватывания объектов манипулирования и надежного их удержания в процессе изменения про странственного положения.
Одна из наиболее важных областей использования роботов — монтаж и сборка изделий в машиностроении. Известно, что около 40 % трудоемкости изготовления машины приходится на сборочные работы. Внастоящее время роботы применяются для монтажа валов, колец, осей, корпусов, установки прокладок, монтажа резьбовых соединений, сборки подшипниковых узлов.
Сборка — это получение конечного изделия путем соединения несколь ких деталей. При этом внутренние связи между различными частями изде
лия могут иметь от 0 до 5 степеней подвижности. -7уу Монтажом называется разновидность сборки, ког да изделие может быть разобрано на составляю щие его отдельные детали без повреждения.
Наиболее распространенной операцией монта жа является операция вставки цилиндрического пальца во втулку. При ее осуществлении важная роль отводится зрению и осязанию.Наибольшая точность позиционирования, достигаемая челове ком с помощью его органов чувств, — 0,2—0,5 мм. Для соединения деталей, допуск на которые зна чительно меньше, человек инстинктивно совер шает поисковые движения, наклоняя и перемещая деталь относительно оси монтажа.
Автоматическое выполнение роботом сборочных операций может про изводиться по схеме разомкнутой системы управления или по замкнутой схеме с обратными связями. В первом случае предъявляются повышенные требования к жесткости и точности робота, поэтому он может оказаться дорогим и неэффективным средством. При этой схеме робот используется в том случае, когда зазоры в соединении достаточно велики. При управлении с обратными связями от робота требуются более низкие точностные харак теристики, компенсация же неточности достигается за счет наличия у него адаптивных свойств. Роботы снабжаются силомоментаыми датчиками, по сигналам которых производится корректировка их движений. Это случай активной корректировки. Пример устройства с пассивной корректировкой (самокорректировкой) представлен на рис. 3.16. Конструкция состоит из трех параллельных стержней, шарнирно присоединенных к основаниям. Они обеспечивают поступательное перемещение основания, так как пред ставляют пространственный аналог шарнирного параллелограмма. Конст рукция, составленная из трех стержней с пересекающимися осями, является аналогом шарнирного четырехзвенника с мгновенным центром вращения шатуна в точке пересечения осей стержней — точке О. При этом обеспечивается сферическое движение вокруг точки О с наибольшей амп литудой. При выполнении поисковых движений в зоне контакта фасок пальца и отверстия происходит самокорректировка положения пальца по отверстию. С помощью такого устройства за несколько долей секунды осу ществляется соединение двух деталей с зазором в сотые доли миллиметра:
Помимо своих основных функций захватывания и удержания объекта манипулирования рабочий орган адаптивного робота используется для оп ределения расположения объекта и самого робота, контроля формы и раз меров объекта. С этой целью рабочий орган снабжается датчиками силомоментного или контактного очувствления.
Силомоментное очувствление необходимо для измерения сил и момен-
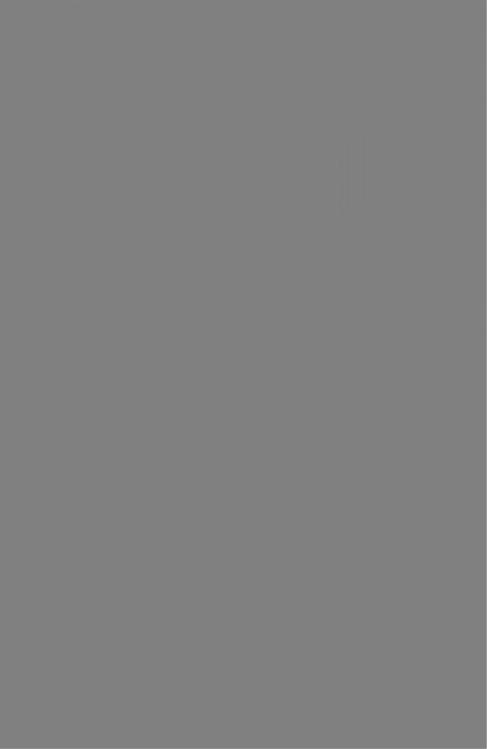
лей, таких как, например, наполненные стеклянные колбы, весьма эффек тивно использование датчика проскальзывания. По формируемому им сиг налу можно установить такое усилие зажима, при котором предмет не выскальзывает из захвата, но и не разрушается. Чувствительные элементы тактильных датчиков выполняются в форме пластин и покрывают всю внешнюю поверхность губок захвата. Они выполняются на основе тензорезисторных, пьезоэлектрических, электромагнитных, емкостных и магни тоупругих преобразователей, в них могут также применяться различные микровыключатели, струйные пневматические элементы, электропрово дящие полимеры и углеродные волокна.
3.5. Схемы и конструкции захватных устройств
Наиболее совершенное захватное устройство создано природой — это кисть руки человека. Однако копирование такого образца требует создания механической системы с 32 степенями подвижности, с огромным числом датчиков положения, усилий, давления и т.п. В результате может быть получена громоздкая и дорогостоящая конструкция.
Захватные устройства роботов могут быть универсального или специ ального типа. Наиболее предпочтительна разработка захватных устройств, предназначенных для выполнения конкретных функций. Универсальность захватных устройств достигается за счет применения набора таких органов. Они выполняются быстросъемными, поэтому их можно менять автомати чески в соответствии с получаемыми роботом заданиями, подобно тому, как происходит смена инструмента в обрабатывающих центрах.
При выполнении транспортных и загрузочных движений основными функциями захватного устройства являются захват и удержание детали, а также точное ее базирование относительно захватного устройства.
Выбор захватного устройства определяется массой объекта манипулиро вания и его физическими и геометрическими свойствами: жесткостью, спо собностью к деформированию, формой и структурой (например, наличием полостей), габаритами. Кроме того, следует принимать во внимание по ложение и ориентацию детали в начальной и конечной позициях, наличие поверхностей для захвата, возможность сохранения положения детали от носительно рабочих поверхностей, действующие силы (силы инерции, дав ления), состояние внешней среды (температура, влажность).
Среди перечисленных факторов наиболее существенную роль играют геометрические характеристики объекта манипулирования. По этим при знакам следует выделить следующие группы: плоские детали, полученные штамповкой, резкой, литьем; детали в форме тел вращения, полученные в результате механической обработки, литья, прессования; объемные детали произвольной формы; упаковочные коробки и контейнеры; изделия изме няемой формы (кабели, шланги, резиновые ленты, пленки).
Многочисленность факторов, влияющих на эффективность работы за-
а |
5 |
в |
Рис. 3.18. Схемы двухпальцевых схватов
хватного устройства, приводит к чрезвычайно большому разнообразию конструктивных решений. В то же время имеются общие обязательные требования ко всем захватным устройствам: надежность зажима и удержа ния, точность фиксирования положения объекта в захватном устройстве, недопустимость повреждения объекта.
Захватные устройства бывают следующих типов: механические (схва ты), вакуумные, с эластичными камерами, электромагнитные.
Простейшим захватным устройством является двухпальцевый схват, работающий по принципу клещевого зажима. На рис. 3.18,а, б, в представ лены три основные схемы двухпальцевых схватов: несимметричный схват с поступательным перемещением губок; симметричный схват; симметрич ный схват с поворотом губок. Несимметричный схват прост по конструк ции, однако вызывает смещение первоначального положения детали. Форма губок двухпальцевых схватов обеспечивает центрирование деталей и улучшает условия их удержания.
Трехпальцевые схваты обладают большей универсальностью, являются самоцентрирующимися, однако их конструкция намного сложнее. В зави симости от формы предметов могут применяться схваты с большим числом пальцев, а также схваты с пальцами, приспосабливающимися к форме предметов. Существует принципиальная разница между зацеплением при удержании предмета кончиками пальцев и захватыванием. Высокий коэф фициент трения кожи на кончиках пальцев человека позволяет удерживать тяжелые предметы при малых усилиях зажатия. Существуют некоторые виды пластиков и резины с аналогичными свойствами.
Приводные механические захватные устройства включают привод, ме ханизм зажима и захватывающие элементы — губки схвата. По виду ис пользуемого привода схваты подразделяются на электромеханические, пневматические и гидравлические; по виду механизмов зажима — на ры чажные, зубчатые, кулачковые. Схваты также различаются формой и ма териалом губок. В целях приспособления схватов к различной форме деталей губки делаются легкосъемными. Впроцессе механической обработ ки деталей часто изменяется форма поверхности удержания, поэтому робот снабжается сменными схватами или сменными губками.
В качестве приводного двигателя в схватах чаще всего используется пневмопривод в виде пневмоцилиндра двухили одностороннего действия;