
книги / Методы оценки трещиностойкости конструкционных материалов
..pdfА
Рис. 108. Схема нагружения образца с трещиной с записью диаграммы разрушения нагрузка — стрела прогиба.
Полученные экспериментальные данные обработаны и представ лены точками на рис. 51. Из рисунка видно, что результаты экспе риментальных исследований подтверждают достоверность анали тической зависимости, изображенной линией, в широком диапа зоне относительной глубины трещины е.
Экспериментальной проверке подвергали также установлен ную в гл. III аналитическую зависимость (II 1.90) величины внеш него нагружения Р от безразмерного параметра е при постоянной величине стрелы прогиба h. Для этого необходимо было в процессе испытания на изгиб образцов с трещинами записывать диаграмму нагрузка Р — стрела прогиба h. С этой целью испытательная ма шина УМ-5А была оборудована (рис. 108) тензорезисторным дат чиком нагрузки 2, датчиком перемещения 2 и двухкоординатным самописцем ПДС-021М (3). Датчик нагрузки представлял собой кольцевой упругий элемент с наклеенными по мостовой схеме про волочными преобразователями. Питание моста осуществлялось от блока питания 4 напряжением 6 в, а разбаланс моста подавался на вход самописца (ось у).
Прогиб образца измеряли с помощью двухконсольного датчика перемещения, который устанавливали на линии действия нагруз ки между нижней поверхностью образца 5 и призмой 6, установ ленной между опорами на траверсе машины. Сигнал с моста дат чика перемещения подавался на второй вход самописца (ось х).
Балки датчика изготовлены из термически обработанной стали 65Г, что обеспечивало хорошую линейность в необходимом интер вале измеряемого перемещения. Неизменность положения датчика
в процессе испытания относи тельно деформируемого образца обеспечивало измерение прогиба с достаточной точностью.
Установку образца на опо ры 7 проводили с помощью фик сатора 8 и выточек в роликах 9 опор, что обеспечивало цент ровку образцов в двух плоскос тях.
Испытательная установка предварительно была опробова на на правильность показаний измеряемых величин. Для это го гладкий цилиндрический об разец подвергали трехточечно му изгибу с записью диаграм-
мы Р — h. Полученные экспериментальные данные Р и h сопоставлены с соответствующими расчетными данными. Результаты проверки представлены на рис. 109, где сплошная линия — рас четные значения, а точки — экспериментальные данные.
Эксперименты проводили на образцах из стали 40Х, закаленные и отпущенные при температуре 200° С, а также в состоянии по ставки. Подготовленные по описанному способу образцы с тре щинами устанавливали на опоры, закрепляли, с небольшой пред варительной деформацией, датчик перемещения и, нагружая обра зец, записывали диаграмму Р — h. Такие эксперименты проводили на образцах с различной относительной глубиной трещины и раз ными диаметрами D K с постоянным отношением 2L/DK = 10.
Для установления достоверности полученных результатов на образцах с различной глубиной трещины, а также с целью исклю чения возможного влияния термической обработки были проведены эксперименты с разной относительной глубиной трещины е на одном и том же образце двух различных диаметров D K = И мм и D K = 22 мм. Для этого после получения первоначальной коль цевой трещины ех образец подвергали нагружению в пределах упругой деформации, записывая диаграмму Р — h. После этого первоначальна^ трещина закрашивалась специальной краской, используемой в красочной дефектоскопии [150]. Затем усталост ным нагружением кругового изгиба (см. гл. VI) продвигали тре щину на определенную глубину е2 <1 ех и снова записывали диаграм му Р — h для образца с глубиной трещины е2 и т. д. В результате такой методики удавалось записать по 2—3 диаграммы на одном образце с различной глубиной трещины. На рис. 110 изображены такие диаграммы для двух глубин трещин ег и е2, на которых ука заны значения разрушающей нагрузки Р \^, Рг^ и величины стрелы прогиба 1, соответственно.
Располагая значением величины прогиба h при заданных Р ,
Рис. |
110. |
Диаграммы разрушения |
Рис. 111. Зависимость F2от е. Сплош |
||||
при изгибе |
цилиндрических |
образ |
ная |
линия — аналитическая |
зави |
||
цов |
с D K = |
11 мм и 2 L = |
100 мм |
симость, построенная |
по формуле |
||
для |
различных глубин кольцевых |
(III. 91), точки — экспериментальные |
|||||
трещин (сталь 40Х, закалка, отпуск |
данные, полученные на образцах из |
||||||
при 2006 С). |
|
стали |
40Х (закалка, |
отпуск |
при |
||
|
|
|
|
200° С). |
|
|
|
2L, |
Д, Е, v, можно определить величину F2 (е) (см. гл. III) |
для |
|||||
соответствующих значений е по формуле |
|
|
= (VIIU5>
где |х — модуль сдвига.
Как видно из рис. 111, экспериментальные данные хорошо под тверждают аналитическую зависимость. При этом данные, полу ченные на разных образцах с одной кольцевой трещиной и несколь кими кольцевыми трещинами на одном образце, хорошо согласуют
ся между собой.
Таким образом, теоретические средства для обработки экспери мента, найденные в гл. III, получили экспериментальное под тверждение и могут быть использованы в дальнейшем при исследо вании усталостного разрушения.
3. Образцы и оборудование для проведения усталостных испытаний
В параграфе 1 настоящей главы приведены некоторые типы образцов и схемы их нагружения, которые приме няются при исследовании усталостного разрушения конструк ционных материалов. Каждая из этих схем имеет свои преиму щества и недостатки. Так, схемы, представленные на рис. 98—
100, могут быть применены для исследования тойколистовых ма териалов. В противном случае требуется мощное испытательное оборудование и, кроме того, возникают методические трудности при создании исходных усталостных трещин.
При использовании указанных схем для исследования усталост ного разрушения пластичных материалов имеет место течение ма териала в захватах. С целью устранения этого явления прибегают к изготовлению образцов сложной формы, увеличивая размеры по толщине или ширине в захватной части.
Аналогичное явление наблюдается также при использовании образцов в виде пластины с центральной трещиной (см. рис. 99) и образца-диска с центральной трещиной (см. рис. 100). При про ведении испытаний на таких образцах необходимо изготавливать специальные захваты для крепления образцов или специальные образцы с утолщениями в области отверстий для приложения на грузки.
Группа силовых схем (см. рис. 101—105) используется для исследования усталостного разрушения материалов большой тол щины и непригодна для исследования тонколистовых материа лов из-за потери устойчивости формы образца при его испы-
.тании.
Отдельные формы образцов сложны в изготовлении. Так, при изготовлении прямоугольного образца с боковой трещиной (см. рис. 102) возникают определенные трудности при изготовлении бокового надреза, особенно для образцов большой ширины, а так же при подготовке вершины концентратора. Эта операция требует изготовления специального режущего инструмента. Аналогичные недостатки имеет также образец клиновидной формы (см. рис.104). Кроме того, сложная форма такого образца вызывает дополнитель ную затрату времени на его изготовление.
Прц исследовании влияния режимов термической обработки на усталостные характеристики материала также встречаются значительные трудности для реализации отдельных схем нагру жения. Не всегда у исследователя имеются нагревательные печи необходимых размеров, чтобы провести термическую обработку партии образцов — пластин или дисков — больших размеров. Неизбежным в процессе закалки таких образцов является короб ление, что затрудняет дальнейшее их использование.
Для реализации каждой из упомянутых выше схем необходи мы пульсирующие установки определенной мощности, соответст вующие приспособления для крепления и нагружения образцов, а также измерительные устройства для фиксирования величины нагружения, изменяющейся длины трещины, податливости испыту емого образца. Так, для силовой схемы по испытанию прямоуголь ных образцов (см. рис. 102) с боковой трещиной требуются специ альные захваты для обеспечения жесткого крепления торцовых поверхностей образца. Вместе с тем для испытания образцов даже среднем ширины при соблюдении условий необходимы установки
довольно большой мощности. Это также имеет место и в случае испытания других образцов (см., например, рис. 98, б), когда их нагружение осуществляется равномерной нагрузкой а по всему сечению.
Определенными преимуществами обладает силовая схема кру гового изгиба цилиндрического образца с внешней кольцевой трещиной. Такой образец легко изготовить, нарезать на нем кру говой концентратор, провести термическую обработку, шлифов ку. Одним из главных преимуществ данного образца является то, что для образования кольцевой трещины не требуется мощного дорогостоящего оборудования. Любой токарный станок средней мощности с успехом может быть применен для образования трещин,, а также для проведения усталостных испытаний.
Выбор размера образца обусловливается различными фактора ми. Главную роль при этом играет трещиностойкость материала. Если исследованию подлежит материал после термической обра ботки на высокую прочность и твердость, когда обычно материал обладает пониженной трещиностойкостыо, то достаточно изгото вить образцы относительно малых размеров. В таком случае для образования трещин и проведения испытаний могут быть приме нены малые токарные станки. Кроме того, размер образца в каж дом конкретном случае определяется мощностью имеющейся уста новки.
Цилиндрические образцы диаметром D0 и длиной 2Ь0 изготов ляют из имеющегося ассортимента материала. Размеры образца выбираются такими, чтобы сохранялось отношение 2L0/DK>> 10 (см. рис. 50), учитывая при этом возможности установки, на ко торой будут проводиться испытания. На образцах нарезают кольцевой концентратор диаметром DK^ 0,8 D0. Конфигурация концентратора (его глубина, угол раскрытия, радиус кривизны у основания) определяется возможностями имеющегося инстру мента для обработки материалов (резцы, шлифовальные круги и т. п.). Желательно получать концентратор максимальной остро ты (р <; 0,1), чтобы облегчить в дальнейшем процесс образования исходной усталостной трещины. Это касается и угла концентра тора, который должен быть не более 60°.
Нагружение образца в процессе образования усталостной тре щины, а также при дальнейших усталостных испытаниях осущест вляют приспособлением, позволяющим нагружать вращающийся образец и контролировать нагрузку, при которой происходит процесс усталостного испытания. Один из возможных вариантов такого приспособления описан ранее (см. параграф 2 гл. VI, рис. 44, 46). Такое приспособление должно надежно закрепляться в установке (например, в суппорте токарного станка), поддержи вать постоянство заданной стрелы прогиба. Датчик нагрузки должен обеспечивать линейность показаний в исследуемом ин тервале интенсивностей нагружения данного образца. Желатель но иметь набор датчиков нагрузки, обеспечивающих различный
уровень интенсивности напряжений и необходимую при этом чув ствительность для определенного диапазона диаметров испытуе мых образцов.
В процессе экспериментов на образцах из материала относитель но небольшой твердости наблюдается вминание подшипников нагружающего приспособления в материал образца, что крайне нежелательно при контроле глубины трещины по изменению на грузки при постоянной стреле прогиба. Для устранения этого уве личивают отношение 2L0/Z)K, что приводит к уменьшению величины изгибающего усилия при необходимой интенсивности нагружения. Кроме того, с целью уменьшения вминания подшипников в мате риал образца изгиб осуществляют четырехточечным нагружением (см. рис. 43, б). Общий вид приспособления с приставкой для конт роля нагрузки, а также сменная вилка для реализации четырех точечного нагружения показаны на‘ рис. 45, 46.
Если образцы подвергают термической обработке, то ее про водят перед образованием трещины. При этом необходимо соблю дать все рекомендации, чтобы получить однородную структуру по всему сечению образца. Подготовленный образец закрепляют в центрах установки, предварительно проверив состояние их конус ных поверхностей. Если на последних обнаружен локальный из нос, что может повлиять на концентричность создаваемой усталост ной трещины, его устраняют шлифовкой.
Для измерения глубины кольцевой трещины в процессе испы таний могут быть использованы приборы, основанные на электро магнитном методе контроля. Применение электромагнитных при боров в этом случае обеспечивает преимущества по сравнению с приборами контроля, основанными на других методах, как, например, ультразвуковом или методе измерения електросопротивления. Основные преимущества электромагнитных приборов состоят в возможности бесконтактного контроля и высокой ско рости контроля, что является важным при данных испытаниях. Электромагнитные дефектоскопы позволяют измерять глубину кольцевой трещины в ферромагнитных и пеферромагнитных об разцах начиная с 0,1—0,2 мм до 5—7 мм [22, 75]. При этом испы тания необходимо проводить на образцах, в которых снят концент ратор и не создается наклеп металла около берегов трещины. Соблюдение таких условий обеспечивает измерения с точностью 5—7%.
Для проведения исследований целесообразно применять элект ромагнитные приборы универсального типа, имеющие широкий диапазон рабочих частот. Это обеспечивает контроль различных металлов и сплавов, как ферромагнитных, так и неферромагнит ных. В частности, для измерения глубины кольцевой трещины ис пользовали [106] универсальный электромагнитный дефектоскоп типа ДУЭТ [132], разработанный в Физико-механическом институ те АН УССР и предназначенный для решения подобный задач. Существенное значение для проведения исследований имеет выбор
Рис. 112. Схема контроля глубины кольцевой трещины с помощью электро магнитного преобразователя в процессе испытания (а) и зависимость выход ного сигнала дефектоскопа от глубины трещины (б).
типа электромагнитного преобразователя и частоты его возбужде ния. Более подробно эти вопросы рассмотрены в работе [106]. На рис. 112, а приведена схема испытания с применением электро магнитного контроля глубины кольцевой трещины. Преобразова тели дефектоскопа устанавливают над трещиной образца 1 с за зором 0,5—1,0 мм и подключают к измерительному прибору 2. Катушки возбуждения 3 преобразователя создают электромагнит ное поле, которое распространяется в образце. Увеличение глу бины трещины приводит к искажениям этого поля, что обнаружи вают с помощью специальной системы измерительных катушек 4. Сигнал, пропорциональный глубине кольцевой трещины, с дефекто скопа подают на многоканальный быстродействующий самопи сец 5, на который одновременно поступает сигнал от датчика на грузки.
На рис. 112, б представлена зависимость выходного сигнала
а |
х |
^ |
D« ~ d |
дефектоскопа |
от глубины |
— ^— кольцевой трещины для |
|
образцов из стали 40Х (закалка, отпуск при 400° С) диаметром DK = |
|||
= |
15 мм. Для разных материалов эта зависимость в значительном |
интервале глубины трещины обычно носит линейный характер. При этом требуется тарировка прибора по контрольным образцам.
4. Методика проведения эксперимента на усталость
Эксперимент начинают с определения трещцностоикости лштериала К\с статическим (см. гл. VI) или цикли ческим методами (теоретическая основа циклического метода изложена в параграфе 5 настоящей главы).
Для определения характеристики К ic циклическим методом поступают следующим образом. В цилиндрическом образце создают
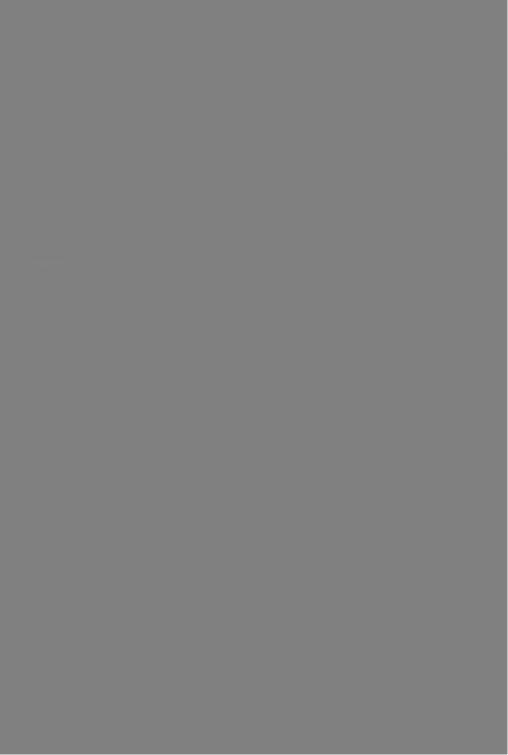
начального концентратора, т. е. до величины DK, и приступают к исследованию усталостного разрушения материала. Первое продвижение трещины осуществляют до глубины « 0 , 7 DH (см. рис. ИЗ, а) при постоянной величине стрелы прогиба и началь ной нагрузке
0,0126а , К б ; £ 1с, (VIII.27)
фиксируя количество циклов нагружения Л^.
Аналогично осуществляется второе продвижение усталостной
трещины до глубины d2 « |
0,6 D Kпри нагрузке |
|
Р 2« |
0,0226А , К б ; К ie |
(VIII.28) |
исоответственно фиксируется количество циклов нагружения N2. •Третье продвижение усталостной трещины и фиксацию соот
ветствующего числа циклов нагружения N3проводили при началь ной нагрузке
Р3« |
0,02210* K A ,fffc |
(VIII.29) |
до глубины трещины d3 « |
0,4 Z)K. |
|
Величина нагрузки Pi при каждом продвижении усталостной трещины выбирается из соображений обеспечения ранее приве денного диапазона интенсивности нагружения.
После составления программы приступают к испытанию образ ца на усталость. Для этого устанавливают подготовленный обра зец в центрах токарного станка и нагружают его по силовой схе ме, указанной на рис. 43, а. Подготовленным здесь считается образец, термообработанный и отшлифованный как по внешнему диаметру, так и по концентратору. Далее при величине стрелы прогиба h0, соответствующей первоначальному нагружению Р0, образуют усталостную трещину до глубины d0, после чего снимают с образца слой материала на глубину первоначального концентра тора до диаметра DK. Затем приступают к усталостному продви жению трещины согласно намеченной программе.
Важным моментом в методическом плане при проведении экспе римента является контроль глубины усталостной трещины. Один из способов такого контроля описан в параграфе 3 данной главы.
Другой из возможных способов заключается в следующем. При распространении трещины поперечное сечение образца умень шается, в результате чего уменьшается жесткость образца. В про цессе эксперимента при постоянной величине стрелы прогиба датчик воспринимает изменение жесткости в виде спада нагрузки, которая фиксируется измерительным прибором 9 (см. рис. 43). Кроме того, в параграфе 4 гл. III установлена аналитическая зави симость (II 1.90) величины Р изгибающего усилия от величины стре лы прогиба /г, достоверность которой подтверждена (см. параграф 2 данной главы) результатами экспериментальных исследований в широком диапазоне относительной глубины трещины и при раз личной величине стрелы прогиба. На основании сказанного в каж дом конкретном случае при данной величине стрелы прогиба по
изменению нагрузки, выбранной для реализации составленной программы испытаний, и размерам образца можно ориентировочно определить величину подрастания усталостной трещины. Это под растание трещины фиксируют для того, чтобы можно было ориенти ровочно осуществить три продвижения усталостной трещины.
Фиксирование трещины может быть также осуществлено с по мощью красок, применяющихся в дефектоскопии, либо чередова нием различной интенсивности нагружения вращающегося образ ца. Так, после первого продвижения трещины при данной интен сивности нагружения уменьшают нагрузку и вращают образец при значительно меньшей интенсивности. Уменьшение интенсив
ности нагружения вызывает изменение характера |
разрушения |
в' микрообъемах вершины трещины, что приводит |
к изменению |
рельефа поверхности разрушения.. Последнее проявляется на по верхности излома в виде круга, четко фиксирующего величину пер вого подрастания трещины Д/. Далее образец нагружают согласно программе и эксперимент повторяется.
После того как осуществлено три продвижения усталостной трещины, образец снимают с установки и разрушают. Затем на разрушенных поверхностях уточняют величину каждого продви
жения усталостной трещины d0l |
d2, d3 и вносят коррективы в |
|||
интенсивность нагружения X. Полученные в процессе эксперимента |
||||
величины hm, dm, |
Nm (т = 1, 2, 3) подставляют |
в |
уравнения |
|
(IV.77) — (IV.79) и |
определяют |
коэффициенты Ai |
(i |
-= 1, 2, 3). |
|
5. Обработка результатов эксперимента |
|||
|
и построение |
|
|
|
|
диаграмм усталостного |
|
|
|
|
разрушения |
|
|
|
% |
Для проведения эксперимента по исследо |
ванию усталостного распространения трещины на стадии ее докритического роста необходимо в первую очередь (как указывалось выше) составить программу проведения эксперимента. Это воз можно только тогда, когда известно значение характеристики трещиностойкости исследуемого материала К 1с. Зная величину К ic, определяют такие размеры образца и трещины, а также величины внешнего нагружения Pi при каждом продвижении усталостной трещины, которые обеспечивали бы выполнение условий автомо дельности зоны^предразрушения (IV.81), (IV.82) и равномерное распределение по исследуемому интервалу усталости заданных при каждом продвижении трещины значений интенсивности напря жений в окрестности ее контура. Поэтому нахождение характе ристики трещиностойкости материала K ic необходимо считать составной частью методики исследования усталостного распрост ранения трещины на стадии ее докритичёского роста.
Определение характеристики K\Q можно осуществлять стати ческим методом, описанным в гл. VI. Однако при эксперименталь