
книги / Процессы обработки заготовок В. А. Бахвалов. Слесарная обработка
.pdf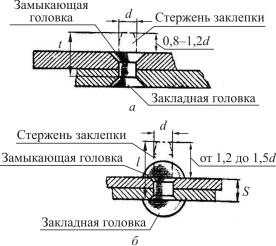
Количество, диаметр и длину заклепки выбирают в зависимости от толщины соединяемых листов и формы замыкающей головки заклепки.
Длину части заклепки для образования потайной головки (рис. 115, а) рассчитывают по формуле
l = S + (0,8…1,2)d,
где l – длина стержня заклепки, мм; S – толщина склепываемых листов, мм; d – диаметр заклепки, мм.
Длину части стержня заклепки для образования замыкающей полукруглойголовки (рис. 115, б) рассчитываютпоформуле
l = S + (1,2…1,5)d.
Рис. 115. Элементы заклепки: а – с потайной головкой; б – с полукруглой головкой
Расстояние от центра заклепки до края листа должно быть не менее 2,5 мм. В зависимости от диаметра заклепки отверстия выполняют согласно данным табл. 7.
131
Таблица 7
Диаметр отверстий под заклепки в зависимости от диаметра заклепок
Диаметр заклепки, мм |
2,0 |
2,3 |
2,6 |
3,0 |
3,5 |
4,0 |
5,0 |
6,0 |
7,0 |
8,0 |
Диаметр отверстия, мм |
2,1 |
2,4 |
2,7 |
3,1 |
3,6 |
4,1 |
5,2 |
6,2 |
7,2 |
8,2 |
Существуют два вида клепки:
–с двусторонним подходом, когда имеется свободный доступ как к замыкающей, так и к закладной головкам;
–с односторонним подходом, когда доступ к замыкающей головке невозможен.
В связи с этим различают два метода клепки: открытый (прямой) и закрытый (обратный).
Прямой метод клепки характеризуется тем, что удары молотком наносят по стержню заклепки со стороны вновь образуемой замыкающей головки.
Клепку прямым методом начинают со сверления отверстий по заклепку (рис. 116, а). Затем в отверстие вводят снизу стержень заклепки и под закладную головку ставят массивную поддержку 2 (рис. 116, б).
Склепываемые листы осаживают (уплотняют) при помощи натяжки 1, которую устанавливают так, чтобы выступающий конец стержня заклепки вошел в ее отверстие. Ударом молотка по вершине натяжки осаждают листы и таким образом устраняют зазор между листами. После этого расклепывают стержень заклепки. Поскольку при расклепывании материал листов упрочняется, стремятся к возможно меньшему числу ударов молотком. Поэтому сначала несколькими ударами молотка осаживают стержень заклепки (рис. 116, в), затем боковыми ударами молотка придают полученной головке заклепки необходимую форму (рис. 116, г), после чего обжимкой окончательно оформляют замыкающую головку (рис. 116, д).
132
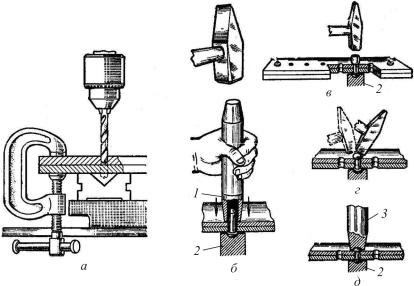
Рис. 116. Процесс клепки прямым методом: а – сверление отверстия; б – осаживание склепываемых листов при помощи натяжки; в – осаживание стержня заклепки; г – придание формы замыкающей головке при помощи молотка; д – окончательное формирование замыкающей головки при помощи обжимки; 1 – натяжка; 2 – поддержка; 3 – обжимка
При выполнении шва с потайными головками под закладную головку устанавливают плоскую поддержку. Молотком ударяют точно по оси заклепки. Во избежание образования неровностей клепку выполняют не подряд, а через два-три отверстия, начиная с крайних.
Обратный метод клепки характеризуется тем, что удары молотком наносят по закладной головке. Обратный метод применяют при затрудненном доступе к замыкающей головке. При клепке по этому методу стержень заклепки вводят сверху (рис. 117, а), поддержку ставят по стержень. Молотком ударяют по закладной головке через оправку (рис. 117, б), формируя при помощи поддержки замыкающую головку. Качество соединения, выполненного по этому способу, несколько хуже, чемпо прямомуметоду клепки.
133
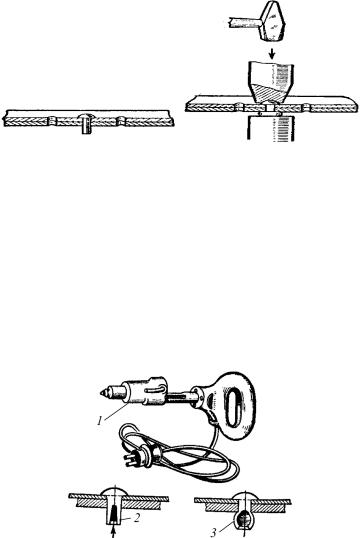
а |
б |
Рис. 117. Процесс клепки обратным методом: а – вставка заклепки в отверстие; б – оформление замыкающей головки
Клепка взрывными заклепками заключается в том, что в от-
верстие вставляют заклепку 2 (рис. 118), в свободном конце стержня которой имеется камера, заполненная взрывчатым веществом. Легким ударом молотка заклепку осаживают. Затем на закладную головку заклепки накладывают наконечник электрического нагревателя 1. В течение 2–3 секунд заклепка нагревается, и при температуре 130–160 оС заряд взрывается, при этом конец стержня сильно расширяется, образуя замыкающую головку 3.
Рис. 118. Клепка взрывными заклепками: 1 – электрический нагреватель; 2 – заклепка до взрыва; 3 – заклепка после взрыва
Клепка трубчатыми заклепками заключается в том, что в от-
верстие устанавливают заклепку 1 (рис. 119, а) с полым стержнем
134
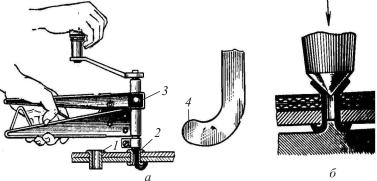
(пистоном), затем специальным инструментом – пистонницей 3 – заклепку осаживают, подтягивают склепываемые заготовки (листы) и расклепывают заклепку 2. Качество клепки (развальцовки) свободного конца стержня для образования замыкающей головки зависит от конструкции, формы и размеров крючка 4 пистонницы, который подбираетсяпоразмерамзакладнойголовки, атакжеотсилынажима.
Более просто заготовки (листы) пустотелыми заклепками склепывают следующим образом: в отверстие вставляют трубчатую заклепку, упирают в поддержку и раздают концы заклепки ударами молотка по кернеру (рис. 119, б).
Рис. 119. Клепка трубчатыми заклепками: а – рабочий момент; б – раздача концов заклепки кернером; 1 – заклепка; 2 – расклепанная заклепка; 3 – пистонница; 4 – крючок
Клепаные швы не бывают полностью герметичными, что связано с наличием неровностей и шероховатостей на склепанных листах, вследствие чего в шве остаются воздушные прослойки и каналы, через которые могут проходить жидкость или газ. Для абсолютной плотности и непроницаемости клепанного шва стыки клепанных швов и головки заклепок уплотняют зачеканиванием.
На рис. 120, а показана схема работы одним острокромочным чеканом. При этом способе выбивают канавку, и материал (металл, сплав) отжимается к нижнему листу, заполняя зазор (если таковой существует) и усиливая контакт склепанных листов.
135
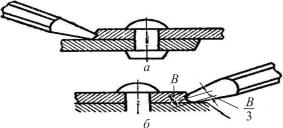
Существенным недостатком этого способа является то, что при работе требуется очень большая аккуратность и внимательность, возникает опасность повреждения нижнего листа, а ширина уплотнения небольшая.
Зачеканивание двумя чеканами с тупыми кромками (рис. 120, б) производят в два прохода. Первый проход производят чеканом с закругленным бойком, а второй проход – чеканом с плоским бойком, которым окончательно уплотняют отжатый к нижнему листу материал. Этот способ имеет ряд преимуществ перед обработкой острокромочным чеканом:
–уплотнение материала получается более глубоким, что обеспечивает высокую плотность шва;
–применение чекана с тупой кромкой вызывает меньшую концентрацию напряжений у кромки шва, чем исключается возможность поврежденияповерхностинижнеголистаострыминструментом.
Рис. 120. Способы чеканки:
а – одним чеканом; б – двумя чеканами
Закладные и замыкающие головки заклепок чеканят закругленным по контуру головки чеканом. Сначала удаляют заусенцы по контуру головки, а затем уплотняют материал заклепки по контуру головки.
Следует иметь в виду, что чеканка обеспечивает уплотнение заклепочного шва, если толщина листовой стали более 4 мм. При толщине листа менее 4 мм чеканку швов не производят, а шов уплотняют парусиновой прокладкой, пропитанной свинцовым суриком на натуральной олифе.
136
10.4. Виды и причины брака при клепке
Виды и причины брака клепанных соединений приведены в табл. 8.
|
Таблица 8 |
|
|
Вид брака |
Причина брака |
Смещение замыкающей головки |
Смещен или неровно обрезан |
|
торец стержня |
Прогиб материала |
Диаметр отверстия мал |
Смещение обеих головок заклепок |
Отверстие просверлено косо |
Изгиб замыкающей головки |
Длинный стержень заклепки; |
|
поддержка установлена не по оси |
|
заклепки |
Расклепывание стержня между |
Клепка произведенапринеприжатых |
листами |
листах |
Подсечка (зарубка) головки |
Обжимка при отделке головки косо |
|
поставлена |
Недотянутая головка |
Неплотнаяосадказакладнойголовки |
|
при клепке |
Мала замыкающая головка |
Недостаточна длина выступающей |
|
части стержня заклепки |
Неплотное прилегание |
Перекос обжимки |
замыкающей головки |
|
Рваные края головки |
Плохое качество металла заклепки |
Контрольные вопросы
1.Какие существуют способы клепки?
2.Как выбирают заклепки по длине, диаметру, материалу?
3.Как выполняют и чем отличаются клепка прямым и обратным методами?
4.Какие основные причины брака при клепке, меры его предупреждения и способы исправления?
137
11.ШАБРЕНИЕ
11.1.Сущность и назначение шабрения
Шабрением называют операцию по снятию (соскабливанию) с поверхностей деталей машин очень тонких слоев металла (сплава) специальным режущим инструментом – шабером.
Целью шабрения является обеспечение плотного прилегания сопрягаемых поверхностей, герметичности (непроницаемости) соединения и создание специфического макрорельефа поверхности, обеспечивающего удержание масляной пленки и повышающего износостойкость поверхности.
Шабрение применяют в станкостроении и инструментальном производстве в качестве окончательной (финишной) обработки незакаленных поверхностей и в качестве ремонтной операции.
Применение шабрения можно объяснить особыми качествами обработанной поверхности, которые состоят в следующем:
–в отличие от шлифованной или притертой поверхности, шаброванная поверхность более износостойка, потому что не имеет прижогов, трещин или шаржированных в нее остатков абразивных зерен, ускоряющих процесс износасопрягаемых поверхностей;
–шаброванная поверхность лучше смачивается и дольше сохраняет смазывающие вещества благодаря наличию так называемой разбивки этой поверхности на отдельные «карманы» – впадины (ложбинки), что также повышает ее износостойкость и снижает величину коэффициента трения;
–шаброванная поверхность позволяет использовать простой
инаиболее доступный метод оценки ее качества по числу контактных пятен на единицу площади.
В результате шабрения повышаются износостойкость и смачиваемость шабреной поверхности смазочными веществами.
Шабрение можно выполнять с помощью шабера вручную или механическим способом.
Первый способ требует большой затраты времени при высокой квалификации исполнителя, но обеспечивает высокую точ-
138
ность и качество обработанной поверхности, а именно ручное шабрение дает возможность получить точность от 0,003 до 0,01 мм. За один проход шабером снимается слой металла (сплава) тол-
щиной 0,003–0,07 мм.
Второй способ осуществляется с помощью специальных станков, на которых шабер получает возвратно-поступательное движение. При этом способе требуется меньше времени, однако качество обработки снижается.
Шабрению предшествует чистовая обработка резанием лезвийным инструментом.
Припуск под шабрение составляет в зависимости от размера обрабатываемой поверхности от 0,1 до 0,5 мм.
11.2. Инструменты для шабрения
Дляшабренияприменяютспециальныеинструменты– шаберы. Шаберы – это металлические стержни различной формы
с режущими кромками на конце (рис. 121).
Изготавливают шаберы из инструментальных углеродистых сталей У10 (У10А) или У12 (У12А). Режущую часть шабера закаливают до твердости HRC 58–64.
По форме режущей части шаберы подразделяют на плоские, трехгранные, фасонные; по числу режущих граней (концов) – на односторонние и двусторонние; по конструкции – на цельные и со вставными режущими пластинами.
Плоские шаберы применяют для шабрения плоских поверхностей – открытых пазов, канавок и т.п.
По числу режущих граней плоские шаберы могут быть односторонними (см. рис. 121, а) и двусторонними (см. рис. 121, в). Рациональной является выпуклая форма лезвия, очерченная дугой радиусом 30–40 мм для получистового шабрения и 40–55 мм для чистового шабрения.
Плоские шаберы изготавливают с прямыми (см. рис. 121, а) и изогнутыми (см. рис. 121, б) концами. Открытые плоскости шабрят шаберами с прямыми концами; стенки пазов, канавок и
139

смежных плоскостей, а также мягкие цветные металлы и сплавы на основе алюминия, меди, цинка, баббита и т.п. шабрят шаберами с отогнутыми концами.
Рис. 121. Видынеразборныхшаберов: а– плоскийодностороннийшабер;
б– шаберсизогнутымконцом; в– плоскийдвустороннийшабер;
г– трехичетырехгранныешаберы; д– углызаточкишаберов
Двусторонний плоский шабер (см. рис. 121, в) благодаря наличию двух режущих концов имеет больший срок службы.
Трехгранные шаберы (см. рис. 121, г) применяют для шабрения вогнутых и цилиндрических поверхностей. Как правило,
140