
книги / Процессы обработки заготовок В. А. Бахвалов. Слесарная обработка
.pdf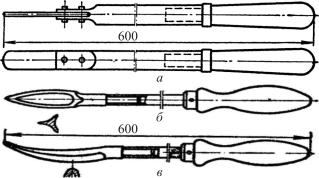
трехгранные шаберы изготовляют односторонними. Они имеют длину 350–450 мм.
Для облегчения заточки трехгранный шабер имеет желобки, образующие режущие кромки с углом заострения 60о.
Составные шаберы значительно легче целых шаберов тех же размеров.
По форме режущей части их подразделяют на плоские, трехгранные прямые и трехгранные изогнутые (рис. 122, а–в).
Рис. 122. Составные шаберы: а – плоский; б – трехгранный прямой; в – трехгранный изогнутый
Такие шаберы при работе пружинят, что повышает чувствительность рук слесаря-шабровщика и способствует увеличению точности шабрения.
Опытные слесари-шабровщики достаточно часто применяют разработанные ими шаберы иных конструкций, основные из которых приведены ниже.
Шабер с радиусной заточной (рис. 123) благодаря плавности и легкости проникновения в металл (сплав) значительно облегчает шабрение, так как требует приложения меньших усилий, чем при шабрении плоским шабером. Для предварительного шабрения радиус заточки составляет 30–40 мм, а для окончательного шабрения – 40–55 мм.
141

Рис. 123. Составной шабер с радиусной заточкой
На рис. 124 представлена конструкция универсального шабера со сменными режущими пластинами. Он состоит из корпуса 3, держателя 2, рукоятки 5, зажимного винта 4, сменной режущей пластины 1, выполненной из быстрорежущей стали или твердого сплава. Пластина вставляется в держатель, зажимается винтом при вращении ручки шабера по направлению часовой стрелке (для снятия пластины ручку вращают против часовой стрелки).
Рис. 124. Шабер со сменными режущими пластинами
Усовершенствованный шабер со сменными режущими пластинами состоит из трех частей: державки, деревянной рукоятки и сменной режущей пластины (рис. 125). Сменная режущая пластина с хвостовиком типа «ласточкин хвост» вставлена в паз державки, что обеспечивает надежность ее крепления.
Рис. 125. Шабер со сменными режущими пластинами
142
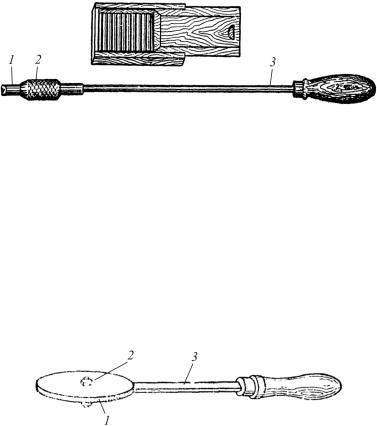
На рис. 126 показана конструкция одного из наиболее совершенных шаберов. Он состоит из сменной режущей пластины 1, зажимного патрона 2 и стержня 3.
Рис. 126. Шабер с зажимным патроном
Режущие пластинки таких шаберов изготавливают размером 3 16 50 мм из закаленной инструментальной углеродистой стали У12 (У12А), а стержень – из стали 45.
При работе по твердому металлу (сплаву), например для работы по белому чугуну, применяют режущие пластины из твердого сплава, например ВК6 или Т15К6. Замену затупленной режущей пластины производят путем поворота стержня (рукоятки), так как губка зажимной части патрона соединена с корпусом шарнирно. Такая конструкция шабера позволяет применять комплект режущих пластин, заточенных под разными углами.
Рис. 127. Дисковый шабер:
1 – режущий диск; 2 – гайка; 3 – державка
Дисковый шабер (рис. 127), как правило, применяют для шабрения широких плоскостей. Режущая часть 1 представляет собой диск из закаленной стали, закрепленный гайкой 2 на державке 3. Диск диаметром 50–60 мм, толщиной 3–4 мм затачивают
143

на кругло-шлифовальном станке. По мере затупления при шабрении его поворачивают на некоторый угол и работают острым (незатупившимся) участком. Таким образом, используют весь режущий диск шабера, что значительно экономит время на заточку и повышает производительность труда.
Фасонный шабер (рис. 128) представляет собой набор сменных режущих пластин из закаленной инструментальной углеродистой или быстрорежущей стали 1, закрепленных на стержне 2 с рукояткой 3. Эти шаберы предназначены для шабрения в труднодоступных местах – впадин, замкнутых контуров, желобков, канавок и других фасонных поверхностей. Торцовые грани режущих пластин затачивают в соответствии с формой обрабатываемых поверхностей.
Рис. 128. Фасонный шабер: 1 – набор режущих пластин; 2 – стержень; 3 – рукоятка
Рис. 129. Шаберы-кольца и их заточка:
1 – шлифовальный круг; 2 – доводочный диск
144
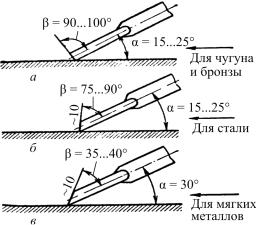
Шаберы-кольца из изношенных наружных колец конических роликовых подшипников затачивают на шлифовальном круге 1 (рис. 129) и доводят его торец на мелкозернистом шлифовальном круге 2.
Шаберы-кольца обеспечивают значительное повышение производительностипо сравнениюс трехграннымишаберами.
11.3. Заточка и доводка плоских шаберов
Достаточно часто величину угла β режущей части шабера принимают равной 90о в связи с тем, что при установке шабера под углом α = 15…25о угол резания δ = 105…125о. Такая геометрия шабера обеспечивает наиболее легкое снятие металла (сплава), так как шабер излишне не врезается в обрабатываемую поверхность.
Однако в ряде случаев целесообразно величину углов заточки шабера выбирать в зависимости от характера работы, твердости обрабатываемого металла (сплава) и формы шабера.
На рис. 130 показана заточка шабера для обработки чугуна и бронзы (рис. 130, а), стали (рис. 130, б) и мягких металлов
(рис. 130, в).
Рис. 130. Геометрия заточки шаберов для обработки: а – чугуна и бронзы; б – стали; в – мягких (цветных) металлов и сплавов
145
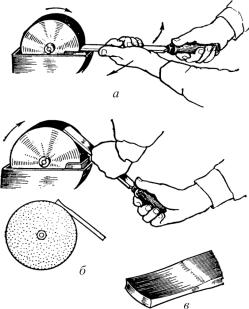
Заточка шабера под углом 35–40о (рис. 130, в) для чернового шабрения, предложенная В.С. Горбуновым и Н.И. Пахновым, позволяет увеличить толщину стружки до 0,1 мм вместо 0,01 мм.
Последовательность заточки плоских шаберов приведена на рис. 131.
Затупленные плоские шаберы затачивают на заточном станке с применением СОТС на корундовом шлифовальном круге зернистостью менее 60 и твердостью СМ1–СМ3 в следующем порядке: шабер берут правой рукой за рукоятку, а левой рукой охватывают его как можно ближе к рабочему концу.
Рис. 131. Заточка плоского шабера: а – торца режущей пластины; б – боковой поверхности режущей пластины; в – вид режущей кромки пластины после заточки
Опираясь плоской поверхностью шабера на подручник, плавно подводят торцовый конец шабера к шлифовальному кругу. При этом положение шабера должно быть строго горизон-
146
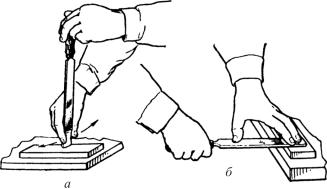
тальным, а ось шабера должна совпадать с центром шлифовального круга (см. рис. 131, а). Плавным движением правой руки, не отнимая конца шабера от шлифовального круга, делают небольшие горизонтальные движения для образования на торцовой части шабера криволинейной режущей кромки. Большую кривизну придают шаберу для точного шабрения, меньшую – для предварительного шабрения (см. рис. 131, в). Заточка широкой грани шабера показана на рис. 131, б.
После заточки на режущем лезвии шабера обычно остаются заусенцы и неровности, которые необходимо удалить. С целью повышения режущих свойств шабера его лезвие после заточки доводят (правят), причем так, чтобы на нем нельзя было бы обнаружить под лупой (увеличение 2,5 раза) заусенцы и неровности, которые снижают качество шабрения.
Шабер доводят на шлифовальных (абразивных или алмазных) мелкозернистых брусках (рис. 132).
Рис. 132. Доводка (заправка) шабера на шлифовальном бруске: а – по торцовой поверхности; б – по боковой поверхности
Поверхность бруска смазывают тонким слоем машинного масла, например масла индустриального И-20А. Шлифовальный брусок во время доводки помещают на деревянную неподвижную прокладку, в которой вырезано гнездо по размеру бруска. Вместо
147
шлифовального бруска можно применять ровную чугунную плиту с нанесенным на ее поверхность свободным абразивом мелкой фракции или пастой ГОИ (Государственного оптического института). При доводке торцовую часть шабера устанавливают на шлифовальном бруске (см. рис. 132, а), тремя пальцами левой руки шабер удерживают за рукоятку, слегка прижимая его к шлифовальному бруску, а правой рукой, удерживающей двумя пальцами конец шабера, совершают колебательные движения.
После доводки торцовой части шабера правят его плоскости (участки широких граней, прилегающие к торцу). Двумя руками, удерживая шабер в горизонтальном положении на шлифовальном бруске (см. рис. 132, б), делают движения вдоль режущих кромок. Для точного шабрения и окончательной доводки режущей части шабера(получениязеркальнойповерхности) применяютпастыГОИ.
Заточку режущих пластин из твердого сплава производят на заточном шлифовальном круге из зеленого карбида кремния. Доводку пластин из твердого сплава доводят на чугунной плите, покрытой мелкозернистым свободным абразивом или с нанесенной пастой ГОИ.
Повторно шабер доводят сразу, как только почувствуют небольшое увеличение усилия шабрения в следствии затупления шабера. Периодичность доводки зависит от характера шабрения и от обрабатываемого материала. В среднем шабер доводят 4–6 раз в течение рабочей смены.
11.4. Основные приемы шабрения
Перед шабрением обрабатываемую поверхность очищают, промывают, протирают, затем на нее наносят краску.
Краски для шабрения. После подготовки поверхности к шабрению выявляют неровности путем окрашивания поверхности краской. Краска для шабрения представляет собой смесь машинного масла, например масла индустриального И-20А, с лазурью и реже с суриком и ультрамарином (синька), которые, в отличие от лазури, плохо смешиваются с маслом и нечетко видны на детали.
148
Лазурь можно заменить сажей, замешанной на смеси автола с керосином. Краску измельчают так, чтобы между пальцами не ощущалось зерен. Затем краску насыпают в баночку (металлическую или стеклянную) и вливают туда масло. Количество масла в смеси должно быть таким, чтобы краска имела консистенцию пасты, но не была жидкой, так как излишек масла будет расплываться по контрольной плите и проверяемая поверхность при наложении ее на плиту вся покроется краской.
Окрашивание поверхности (рис. 133, а–г). Краску наносят на поверхность плиты тампоном (см. рис. 133, а) из чистых льняных тряпок, сложенных в нескольких слоев. Удобно наносит краску также мешочком, изготовленным из чистого полотна (холста), в который накладывают краску. Мешочек и тампоны в паузах между окрашиваниями кладут в чистую стеклянную посуду или в жестяную баночку. Перед окрашиванием с поверхности детали удаляют стружку и грязь волосяной щеткой или чистой тряпкой, деталь осторожно накладывают на поверхность плиты и медленно передвигают. Для достижения равномерного износа плиты необходимо использовать всю ее поверхность.
После двух-трех круговых движений по плите (см. рис. 133, б) деталь осторожно снимают. На хорошо подготовленных поверхностях краска ложится равномерно по всей поверхности (см. рис. 133, в), на плохо подготовленных поверхностях краска ляжет неравномерно. В небольших углублениях краска будет скапливаться, а в местах белее углубленных ее вообще не будет. Так возникают белые пятна – наиболее углубленные места, не покрытые краской; темные пятна – наименее углубленные, в них скопилась краска; серые пятна– наиболеевыступающие, нанихкраскаложитсятонкимслоем.
При определении неровностей тяжелых деталей, не снимаемых с места, закрепленный поверочный инструмент – плиту (см. рис. 133, г) или линейку – перемещают по контролируемым поверхностям.
Легкие изделия (детали) при шабрении устанавливают на слесарном верстаке, акрупные и тяжелые– накозлах, стендах ит.п.
149
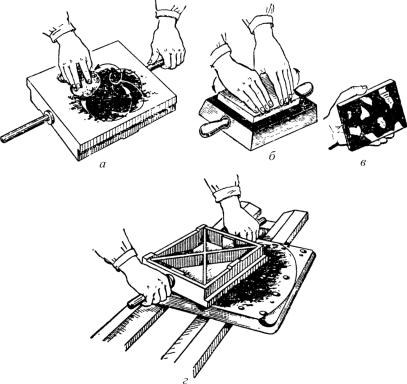
Рис. 133. Окрашивание поверхности при шабрении:
а– окрашивание плиты; б – перемещение детали по плите;
в– окрашенная деталь; г – перемещение плиты по детали
Процесс шабрения заключается в постепенном снятии материала с выступающих участков (серых пятен).
Шабер держат правой рукой за рукоятку, а левой рукой нажимают на его конец (рис. 134, а). По отношению к обрабатываемой поверхности шабер устанавливают под углом 25–30о. Материал снимают скоблением. Рабочим ходом при шабрении является движение вперед, т.е. от себя (рис. 134, а), а при работе плоским шабером с отогнутым вниз концом – движение назад, т.е. на себя (рис. 134, б). При холостом ходе шабер приподнимают.
150