
книги / Процессы обработки заготовок В. А. Бахвалов. Слесарная обработка
.pdf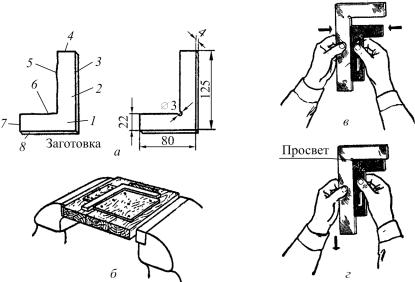
Рис. 61. Опиливание угольника: а – заготовка и эскиз угольника;
б– крепление заготовки угольника; в, г – проверка качества опиливания
–заменяют деревянный брусок нагубниками, зажимают угольник и последовательно опиливают ребра угольника под углом 90о; для обеспечения точности обработки сначала следует обработать ребро 3 до получения прямого угла между этим ребром и поверхностями 1 и 2 угольника, затем в такой же последовательности обработатьребро8, проверяяотносительно ребра3 угольником;
–в вершине внутреннего угла сверлят отверстие диаметром 3 мм, а затем ножовкой делают к нему прорезь шириной 1 мм для выхода инструмента;
–опиливают последовательно ребра 5 и 6 под углом 90о, выдерживая при этом параллельность ребра 5 с ребром 3 и ребра 6
сребром 8, добиваясь, чтобы внутренний угол между ребрами 5 и 6 и наружный угол между ребрами 3 и 8 были прямыми;
–опиливают последовательно торцы 4 и 7, выдерживая размеры по чертежу;
–удаляют заусенцы, полируют все ребра и поверхности угольника.
71
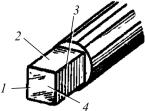
Приведенная выше последовательность обработки угольника обеспечивает заданную плоскостность каждой поверхности угольника и перпендикулярность ребер между собой и по отношению к поверхностям угольника (см. рис. 61, в, г).
Опиливание квадрата на конце стержня начинают с опиливания грани 1 (рис. 62), затем параллельно ей опиливают грань 3. Грань 2 опиливают под углом 90о к грани 1 и 3. Грань 4 опиливают в размер к грани 2. Размер проверяют штангенциркулем.
Опиливание цилиндрических загото-
вок производят в следующей последовательности. Цилиндрический стержень I (рис. 63) сначала опиливают на квадрат II (в размер сторон квадрата
должен войти припуск на последующую обработку). Затем у квадрата опиливают углы и получают восьмигранник III, из которого путем опиливания углов получают шестнадцатигранник IV и т.д. В процессе дальнейшей обработки получают цилиндрический стержень требуемого диаметра.
Опиливание вогнутых поверхностей начинают с разметки заготовки. Основную часть материала обычно удаляют выпиливанием ножовкой, придав впадине в заготовке форму треугольника (рис. 64, а), или высверливанием.
Затем напильником опиливают грани и спиливают выступы полукруглым или круглым драчевым напильником до разметочной риски. Профиль сечения круглого или полукруглого напильника выбирают таким образом, чтобы его радиус был несколько меньше, чем радиус опиливаемой поверхности заготовки.
Не доходя 0,3–0,5 мм до разметочной риски, драчевый напильник заменяют личным. Правильность формы опиливаемой поверхности проверяют по шаблону на просвет, а перпендикулярность опиленной поверхности торцу заготовки проверяют угольником.
72
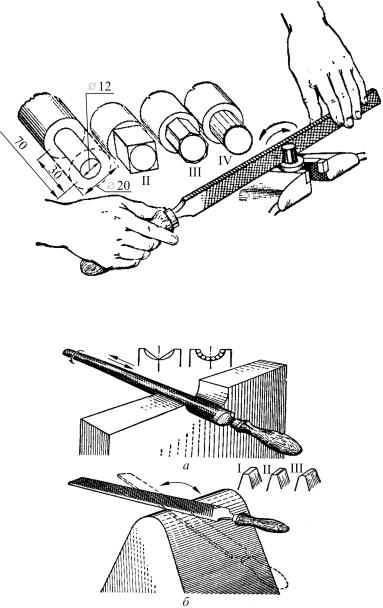
Рис. 63. Опиливание цилиндрических заготовок: I – цилиндр; II – квадрат; III – восьмигранник; IV – многогранник
Рис. 64. Опиливание поверхностей: а – вогнутых; б – выпуклых
73
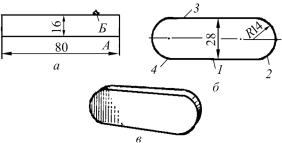
Опиливание выпуклыхповерхностей представлено нарис. 64, б.
После разметки ножовкой срезают углы заготовки, и заготовка принимает форму пирамиды (I). Затем драчевым напильником снимают слой материала, не доходя 0,8–1,0 мм до разметочной риски (II), после чего личным напильником снимают оставшийся слой материала с заготовки в размер до разметочной риски (III).
Призматические шпонки (рис. 65) изготавливают, выполняя следующие операции:
– размечают на стальной полосе и отрезают ножовкой заготовку нужной для изготовления шпонки длины;
Рис. 65. Изготовление шпонки: а – заготовка;
б– разметка; в – готовая шпонка
–опиливают начисто плоскость А, затем размечают и опиливают поверхности 1 и 2;
–размечают поверхности 3 и 4 согласно чертежу;
–опиливают поверхности 3 и 4;
–подгоняют опиливанием шпонку к соответствующему шпоночному пазу;
–шпонка должна легко входить в шпоночный паз (без нажима), садиться плотно, без зазора;
–поверхность Б опиливают по высоте, выдерживая заданный размер.
Опиливание тонких пластинок обычными приемами нецеле-
сообразно, так как при рабочем ходе напильника пластинка изгибается и возникают завалы. Не рекомендуется для опиливания
74
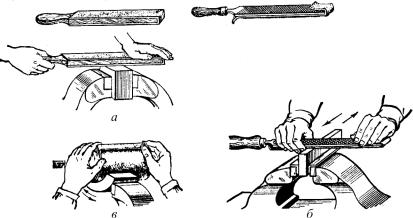
тонких пластинок зажимать их между двумя деревянными брусками, поскольку при этом насечка напильника быстро забивается древесной и металлической стружкой и напильник приходится часто чистить, что резко снижает производительность опиливания. С целью повышения производительности труда при опиливании тонких пластин целесообразно склепывать до 10–12 пластинок в пакет. Можно обойтись без склепывания пластинок в пакеты, а использовать раздвижные рамки, плоскопараллельные наметки, кондукторы и т.п. Приемы опиливания пластинок в пакете (рамках, наметках, кондукторах) те же, что при опиливании плитки с широкими ребрами.
Выбор способа отделки поверхностей заготовки после опи-
ливания зависит от материала заготовки, требований к чистоте обработки, размеров заготовки, формы поверхности и припуска, который обычно составляет 0,05–0,3 мм.
Рис. 66. Отделка (зачистка) опиленной поверхности:
а– шлифовальной шкуркой; б – напильником со шкуркой;
в– зачистка вогнутой поверхности шкуркой, навернутой на оправку
Втех случаях, когда требуется высокая точность обработки, поверхности после опиливания подвергают финишной отделке
75
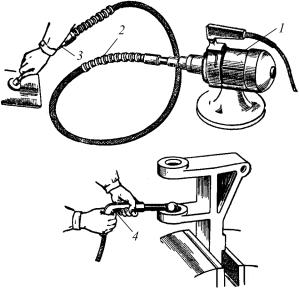
бархатными напильниками, шлифовальной (абразивной или алмазной) шкуркой и шлифовальными (абразивными или алмазными) брусками (рис. 66).
4.4.Механизация опиловочных работ
Сцелью повышения производительности труда и культуры производства опиловочные работы подвергают механизации путем применения ручных электрических и пневматических опиловочных инструментов и опиловочных машинок и станков.
Механизированные ручные опиловочные машинки с прямым напильником не получили широкого применения. Механизиро-
ванные опиловочные машинки с вращающимся опиловочным ин-
струментом типа мелких фрез диаметром 1,5–25 мм, шлифовальных головок диаметром 10–50 мм и шлифовальных кругов диаметром до 150 мм (рис. 67) используют достаточно широко.
Рис. 67. Механизированная опиловочная машинка с электроприводом: 1 – электродвигатель; 2 – гибкий вал;
3 – патрон с опиловочным инструментом; 4 – угловая державка
76
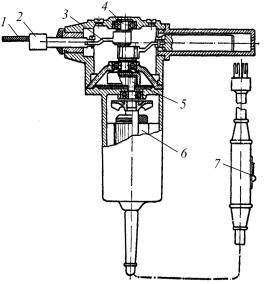
Механизированная опиловочная машинка, работающая от трехфазного двигателя 1, имеет шпиндель, к которому крепится гибкий вал 2 спатроном3 для закрепленияопиловочного инструмента.
Механизированные ручные напильники с электрическим и пневматическим приводом предназначены для различных видов опиловочных работ. Механизированный напильник с электрическим приводом (рис. 68) работает следующим образом. Нажимом на кнопку пуска 7 включают электродвигатель 6. Вращение ротора электродвигателя через зубчатую передачу 5 передается коленчатому валу 4, кривошипная шейка которого сопряжена с шатуном 3. При вращении вала шатун получает возвратно-поступательное движение, которое передается через шток напильнику 1, закрепленному в патроне 2. Длина хода напильника равна 10–12 мм, число двойных ходов напильника составляет 1200–1500 в минуту.
Рис. 68. Механизированный напильник с электрическим приводом: 1 – напильник; 2 – патрон; 3 – шатун; 4 – коленчатый вал; 5 – зубчатая передача; 6 – электродвигатель, 7 – кнопка пуска
77
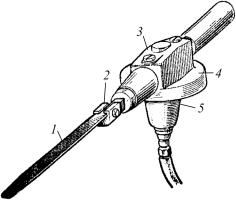
Применение механизированного электрического напильника повышает производительность труда в 4–5 раз по сравнению с работой напильником вручную.
Механизированный напильник с пневматическим приводом
(рис. 69) имеет двигатель ротационного типа, работающий от сжатого воздуха, подаваемого от цеховой сети сжатого воздуха или от автономного компрессора под давлением 5–6 атмосфер. Механизированный напильник состоит из рабочего инструмента 1, головки (патрона) 2 для его закрепления, преобразователя движения 3, редуктора 4 и двигателя 5.
Рис. 69. Механизированный напильник с пневматическим приводом: 1 – инструмент; 2 – головка (патрон); 3 – преобразователь движения; 4 – редуктор; 5 – двигатель
Длина хода напильника равна 10–12 мм, число двойных ходов напильника составляет 1200–1500 в минуту. Применение механизированных напильников с пневматическим приводом повышает производительность опиливания в 3–5 раз по сравнению с опиливанием, осуществляемым вручную.
Опиловочные станки производят с возвратно-поступательным и вращательным движением инструмента. Однако опиловочные станки применяют крайне редко, так как работа на этих станках
78
обеспечивает меньшую производительность и экономически менее выгодна, чем обработка на токарных, фрезерных и шлифовальных станках.
Наиболее частыми видами брака при опиливании (ручном и механизированном) являются:
–неровности поверхности (горбы) посередине и завалы краев заготовки как результат неумения пользоваться напильником;
–вмятины или повреждения поверхности заготовки в результате ее неправильного зажима в тисках;
–неточность размеров опиленной заготовки вследствие неправильной разметки, удаления слишком большого или слишком малого слоя материала, а также погрешностей измерения или неточности мерительного инструмента;
–задиры, царапины на опиленной поверхности, возникающие в результате небрежной работы и неправильно выбранного напильника.
Контрольные вопросы
1.Чем следует руководствоваться при выборе напильника при обработке разных материалов?
2.Когда следует применять алмазные надфили?
3.Когда применяют дисковые напильники?
79
5.РАСПИЛИВАНИЕ И ПРИПАСОВКА ЗАГОТОВОК
5.1.Общие сведения о распиливании и припасовке
Распиливанием называют обработку отверстий опиливанием с целью придать им заданную чертежом форму.
Припасовкой называют пригонку одной детали к другой детали, точно обработанной по чертежу. Обе детали после припасовки должны сопрягаться без зазора.
Ручное распиливание, пригонка и припасовка являются очень трудоемкими операциями, которые выполняют при слесар- но-сборочных и ремонтных работах, а также при окончательной (финишной) обработке деталей полученных штамповкой.
5.2. Распиливание
Прежде чем начать распиливание, производят разметку, кернение, сверление по накерненным точкам и вырубают проймы, образованные сверлением.
Распиливание в заготовке воротка производят после разметки квадрата и сверления отверстия по центру квадрата (рис. 70, а). Диаметр отверстия должен быть на 0,5–0,7 мм меньше стороны квадрата. В просверленном отверстии пропиливают четыре угла квадратным напильником, не доходя 0,5–0,7 мм до разметочных рисок. Затем распиливают отверстие до разметочных рисок в следующей последовательности: вначале распиливают поверхности 1 и 3, а затем поверхности 2 и 4 и производят подгонку отверстия по метчику так, чтобы он входил в отверстие на глубину 2–3 мм. Дальнейшую обработку сторон отверстия производят до тех пор, пока квадратная головка метчика легко, но плотно будет входить в отверстие квадратного сечения(рис. 70, б).
Распиливание в заготовке трехгранного отверстия произ-
водят после разметки, кернения и сверления по центру треугольника отверстия, стороны которого не касаются разметочных ри-
сок (рис. 71, а).
80